5 Axis Machining Service
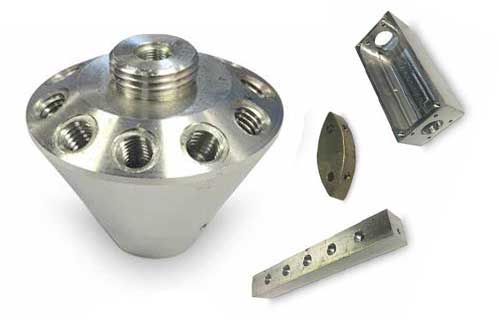
Custom Precision Part 5 Axis CNC Machining Services
With the use of sophisticated CNC machining technology, 5-axis machining services can concurrently cut and shape a workpiece in five separate directions. When constructing intricate structures and designs, the five axes of motion—X, Y, Z, A, and B—allow for increased accuracy, speed, and flexibility. This service is perfect for producing parts for the automotive, aerospace, and medical industries. Faster production speeds, increased precision, and the capacity to produce intricate forms and designs that are challenging or impossible to do with conventional machining techniques are some advantages of 5-axis machining.
Advantages of 5 Axis CNC Machining
One advantage of 5-axis CNC machining is its capacity to produce intricate pieces with increased accuracy and precision. By cutting and shaping the workpiece in numerous directions at once, it cuts down on production time by eliminating the need for different setups and tools.
Complex geometries and shapes that are challenging or impossible to accomplish with conventional machining techniques can also be created with 5-axis CNC machining. Furthermore, it lowers the possibility of mistakes and irregularities by offering more flexibility and control throughout the milling process. All things considered, 5-axis CNC machining is a very sophisticated and effective way to make items.
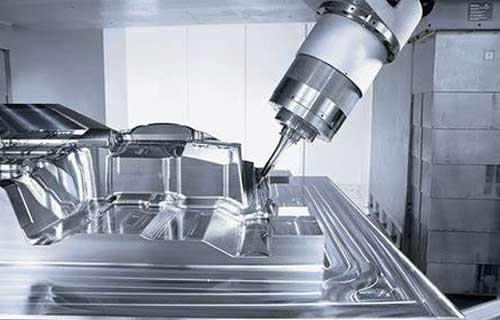
5 Axis CNC Machining Tolerances
Tolerances that can be achieved with 5 Axis CNC Machining:
- Positional tolerance: +/- 0.0002 inches
- Angular tolerance: +/- 0.05 degrees
- Surface finish: up to 16 microinches
- Circularity tolerance: 0.0001 inches
- Concentricity tolerance: 0.0002 inches
- Parallelism tolerance: 0.0002 inches
- Perpendicularity tolerance: 0.0002 inches
- Symmetry tolerance: 0.0002 inches
Factors that can affect tolerances in 5 Axis CNC Machining:
- Type of material being machined
- Complexity of the design
- Cutting tool geometry and quality
- Machine accuracy and repeatability
- Environmental factors, such as temperature and humidity
Importance of tolerances in 5 Axis CNC Machining:
- Achieving tight tolerances is crucial in industries such as aerospace and medical, where precision and accuracy are of utmost importance
- Tolerances ensure that parts and components fit and function correctly, reducing the risk of errors or failures
- Consistent tolerances improve the overall quality and reliability of the final product.
Materials for Custom 5 Axis CNC Machining
Metals For 5 Axis CNC Machining
- Aluminum alloys (e.g. 6061, 7075)
- Stainless steel (e.g. 304, 316)
- Titanium alloys (e.g. Ti6Al4V)
- Nickel alloys (e.g. Inconel 718)
- Copper alloys (e.g. brass, bronze)
- Magnesium alloys (e.g. AZ31B)
Plastics For 5 Axis CNC Machining
- Acetal (e.g. Delrin)
- Nylon (e.g. Nylon 6/6)
- Polycarbonate (e.g. Lexan)
- Acrylic (e.g. Plexiglass)
- PVC
- PEEK
Composites For 5 Axis CNC Machining
- Carbon fiber reinforced polymer (CFRP)
- Glass fiber reinforced polymer (GFRP)
- Kevlar reinforced polymer
- Ceramic matrix composites (CMC)
Other materials For 5 Axis CNC Machining
- Wood
- Foam
- Rubber
- Ceramics
Factors to choose materials for 5 Axis CNC Machining
- Material properties, such as strength, hardness, and thermal conductivity
- Machinability of the material
- Cost and availability of the material
- Environmental factors, such as temperature and humidity
- Desired surface finish and tolerances of the final product.
Surface Finishes for 5 Axis CNC Machining
Anodized Finish For 5 Axis CNC Machining
An electrochemical process called anodizing leaves a thin layer of oxide on a material's surface. A range of finishes, such as matte, satin, and gloss finishes, can be produced by the procedure. Anodizing is frequently applied in protective or decorative contexts.
Mirror Finish For 5 Axis CNC Machining
This is the smoothest surface that 5-axis CNC machining can produce. High reflectivity and an extremely low roughness average (Ra), usually less than 0.1 microns, are its defining characteristics. In high-end applications where surface quality and aesthetics are crucial, this surface finish is frequently utilized.
Satin Finish For 5 Axis CNC Machining
Although this surface is not as flawless as a mirror finish, it nevertheless has a low Ra value—between 0.1 and 0.4 microns, on average. It is frequently utilized for functional or ornamental purposes and has a gentle, brushed appearance.
Matte Finish For 5 Axis CNC Machining
Ra values for this finish are typically between 0.4 and 1.6 microns, which is greater than for a satin finish. It looks tougher and is frequently utilized in functional applications where a textured or non-slip surface is necessary.
Bead Blast Finish For 5 Axis CNC Machining
The surface is blasted at a high speed with tiny beads or particles to produce this polish. It yields a consistent matte surface, often with a Ra value of 3.2 microns, that is relatively high. When a textured surface is needed for utilitarian purposes, it is frequently utilized.
Polished Finish For 5 Axis CNC Machining
Abrasive materials are used in polishing to give a material's surface a glossy, smooth finish. A matte surface with a low Ra-value can be as high-gloss as a mirror finish after polishing. They are frequently employed in ornamental applications where a high sheen or gloss is needed.
Brushed Finish For 5 Axis CNC Machining
Brushing is the process of applying an abrasive pad or wire brush to a material's surface to create a textured, linear pattern. The appearance of brushed finishes can vary from smooth and glossy to rugged and earthy. When a distinctive texture or pattern is required in decorative applications, they are frequently utilized.
Sandblasted Finish For 5 Axis CNC Machining
Sandblasting is the process of applying high pressure air or water to a material's surface in order to blast it with sand or other abrasive particles. A textured matte surface with a comparatively high Ra value is produced by this method. In functional applications where a textured or non-slip surface is required, sandblasting is frequently employed.
Powder Coated Finish For 5 Axis CNC Machining
To generate a strong, protective surface, powder coating entails dusting a material with dry powder and baking it in an oven. Matte to glossy finishes are available for powder coating, which can be applied to both practical and decorative surfaces.
Applications of 5 Axis Machining
5-axis machining is a highly advanced manufacturing technology that utilizes a computer numerical control (CNC) machine to move a cutting tool along five axes simultaneously. The industrial sector has undergone a revolution because to this technology, which makes it possible to produce incredibly complicated and detailed parts quickly and precisely. The automotive, aerospace, and medical industries are just a few of the industries in which 5-axis machining finds application.
In the aerospace industry, 5-axis machining is used to produce highly complex parts such as turbine blades, engine components, and structural components. With the ability to manipulate the cutting tool in multiple directions, 5-axis machining allows for the production of parts with extremely tight tolerances and complex geometry.
In the medical industry, 5-axis machining is used to produce highly precise and complex medical devices such as surgical instruments and implants. 5-axis machining is a very precise and accurate process that is well-suited for producing intricate medical equipment that necessitates precise and accurate results.
In the automotive industry, 5-axis machining is used to produce engine components, suspension components, and other parts that require high precision and accuracy. High-performance automobile parts may be produced with 5-axis machining thanks to its ability to produce parts with intricate geometries and tight tolerances.
A very sophisticated production technique that is revolutionizing the manufacturing industry is five-axis machining. Overall, its applications are diverse. Due to the unprecedented precision and accuracy provided by five axis machining, it is a key technology for the production of complex products in industries such as automotive, aerospace, and medical.
Simultaneous 5 Axis Machining or 3+2 Axis Machining
Simultaneous 5-axis machining and 3+2-axis machining are advanced manufacturing techniques used to produce complex parts. In simultaneous 5-axis machining, the cutting tool moves along five axes simultaneously, allowing the production of parts with complex geometries and close tolerances. This technique is particularly useful for the aerospace and medical industries, which require complex parts with precise geometries.
On the other hand, 3+2-axis machining is a technique in which the cutting tool moves along three axes while the workpiece is tilted along two additional axes. This technique is ideal for producing parts with complex features on the sides of the workpiece. It is particularly useful in the production of automotive parts, mold making, and other industries that require complex geometries.
Both simultaneous 5-axis machining and 3+2-axis machining are highly advanced manufacturing techniques used to produce parts with high precision and accuracy. They are essential in modern manufacturing and have revolutionized the production of complex parts.
Why Choose Our 5 Axis CNC Machining Service
Our 5-axis CNC machining service is a reliable and high-quality solution for producing complex and intricate parts with a high level of precision and accuracy. There are several reasons why you should choose our service:
Highly skilled technicians: Our team of highly skilled technicians has extensive experience in 5-axis CNC machining and is dedicated to producing parts that meet or exceed customer expectations.
State-of-the-art equipment: We use the latest 5-axis CNC machining technology and equipment, ensuring that we can produce parts with a high level of precision and accuracy.
Fast turnaround times: Our streamlined processes and efficient production methods allow us to offer fast turnaround times without compromising on quality.
Competitive pricing: We offer competitive pricing without compromising on the quality of our services, ensuring that our customers receive the best value for their investment.
Customized solutions: We work closely with our customers to understand their unique requirements and offer customized solutions that meet their specific needs.
Overall, our 5-axis CNC machining service is a reliable and high-quality solution for producing complex and intricate parts. Our commitment to quality, efficiency, and customer satisfaction makes us the ideal partner for your 5-axis CNC machining needs.
5-Axis CNC Machining FAQ
What is 5-axis CNC machining?
5-axis CNC machining is a manufacturing technique that uses a computer numerical control (CNC) machine to move cutting tools along five axes simultaneously to produce complex and detailed parts.
5-axis CNC machining is an advanced manufacturing process used in the machining industry. CNC stands for computer numerical control and refers to the method of controlling machine tools through computer programming instructions. In 5-axis CNC machining, the cutting tool can move along five different axes simultaneously, allowing for more complex and intricate machining operations.
Traditional 3-axis CNC machines can move the tool along three linear axes (X, Y, and Z). These machines are capable of creating 3D shapes and performing various operations such as milling, drilling, and cutting, but have limitations when it comes to certain complex geometries and angles.
On the other hand, 5-axis CNC machines have two additional rotary axes, commonly referred to as the A-axis and the B-axis. The A-axis is a rotary axis that rotates around the X-axis, and the B-axis is a rotary axis that rotates around the Y-axis. These rotary motions enable the cutting tool to approach the workpiece from a variety of angles and directions, enabling it to access hard-to-reach areas and create more complex shapes with fewer tool changes.
Overall, 5-axis CNC machining is a sophisticated technology that is capable of creating complex parts with high precision and efficiency.
How is 5-axis CNC machining different from other machining techniques?
5-axis CNC machining is different from other machining techniques because it allows for the manipulation of the cutting tool in multiple directions simultaneously, which allows for the production of complex geometries and tight tolerances.
5-axis CNC machining is different from other machining techniques primarily because of its ability to move the cutting tool along five different axes simultaneously. Let's explore the key differences between 5-axis CNC machining and other common machining techniques:
- Number of axes: The fundamental difference lies in the number of axes controlled by the machine. Traditional 3-axis CNC machining can move the cutting tool along three linear axes (X, Y, and Z), whereas 4-axis machining adds an additional rotational axis (usually around the Z-axis). 5-axis CNC machining, as the name suggests, incorporates two additional rotary axes (A and B) in addition to the three linear axes.
- Flexibility and complexity: 5-axis CNC machining offers unparalleled flexibility and versatility compared to other techniques. It can handle highly complex geometries and contours that would be challenging or impossible to achieve using 3-axis or 4-axis machines. This ability is especially beneficial for manufacturing intricate parts and components in industries like aerospace and medical.
- Tool access: 5-axis CNC machines allow the cutting tool to approach the workpiece from various angles, including undercuts and sidewalls. This unrestricted tool access enables efficient machining of complex shapes without requiring multiple setups or repositioning of the workpiece, which can be time-consuming in other machining techniques.
- Setup time: Setting up a 5-axis CNC machine might be more complex and time-consuming than a 3-axis or 4-axis machine due to the additional axes and associated calibration. However, the increased setup time is offset by the reduction in overall machining time, as 5-axis machines can perform multiple operations in one setup.
- Precision and accuracy: 5-axis CNC machining offers enhanced precision and accuracy due to its ability to approach the workpiece from different angles, reducing the chance of errors caused by fixture setups. This is particularly critical for high-tolerance applications and parts with strict dimensional requirements.
- Cost: 5-axis CNC machines are generally more expensive than their 3-axis and 4-axis counterparts due to the added complexity and sophistication of the machine. However, the advantages it brings in terms of efficiency, reduced labor costs, and increased capabilities can make it a cost-effective choice for certain industries and applications.
In summary, 5-axis CNC machining stands out for its ability to handle complex geometries, increased precision, and reduced setup time. While it may not be necessary for every machining task, it provides a significant advantage for industries that require intricate and precise parts. Other machining techniques, like 3-axis and 4-axis CNC machining, still have their place in manufacturing and are well-suited for simpler and less complex applications.
What are the benefits of 5-axis CNC machining?
The benefits of 5-axis CNC machining include the ability to produce complex parts with a high level of precision and accuracy, reduced production time and costs, and the ability to work with a wide range of materials.
5-axis CNC machining offers a range of benefits that make it a preferred choice for various industries and applications. Here are the key advantages of 5-axis CNC machining:
Complex geometries: 5-axis machines can create intricate and complex geometries that would be challenging or impossible to achieve with conventional 3-axis or 4-axis machining. The ability to move the cutting tool along five axes enables the machining of undercuts, overhangs, and compound angles with ease.
Reduced setup time: Unlike traditional machining techniques that may require multiple setups to access different angles, 5-axis CNC machining can often complete a part in a single setup. This reduces overall setup time, streamlining the manufacturing process and increasing productivity.
Enhanced precision and accuracy: The continuous and unrestricted tool movement in 5-axis machining ensures higher precision and accuracy. The cutting tool can maintain its optimal orientation throughout the machining process, resulting in parts with tighter tolerances and better surface finishes.
Improved surface finish: With the ability to approach the workpiece from multiple angles, 5-axis machining can achieve smoother surface finishes. This is particularly advantageous for parts that require a high-quality finish, such as components used in aerospace or medical applications.
Efficiency and productivity: 5-axis CNC machining can significantly reduce cycle times and increase efficiency due to its ability to perform multiple operations in one setup. It minimizes manual intervention and tool changes, leading to faster production and reduced lead times.
Reduced tool wear and tear: The continuous tool paths and optimized cutting angles in 5-axis machining help reduce tool wear and extend the life of cutting tools. This lowers tooling costs and ensures consistent performance over extended periods.
Versatility: 5-axis CNC machines can handle a wide range of parts and materials, making them suitable for diverse industries, including aerospace, automotive, medical, and mold making. The flexibility of 5-axis machining allows for a broader scope of manufacturing capabilities.
Design freedom: Manufacturers have more design freedom when using 5-axis CNC machining. The added axes enable them to create innovative and unique parts without compromising on manufacturability.
Elimination of manual errors: The precision of computer-controlled 5-axis machines minimizes the risk of manual errors and ensures consistent part quality, reducing scrap rates and material waste.
Cost-effectiveness: Although 5-axis CNC machines are more expensive than 3-axis or 4-axis machines, their benefits in terms of increased efficiency, reduced labor costs, and improved part quality can lead to long-term cost savings, especially for complex and high-tolerance components.
In summary, 5-axis CNC machining offers numerous advantages that contribute to improved productivity, accuracy, and flexibility in manufacturing, making it an ideal choice for industries that demand intricate and complex components.
What industries benefit from 5-axis CNC machining?
Industries that benefit from 5-axis CNC machining include aerospace, medical, automotive, and more.
5-axis CNC machining benefits a wide range of industries, particularly those that require the production of complex and highly precise components. Some of the key industries that benefit from 5-axis CNC machining include:
Aerospace: The aerospace industry often deals with intricate and high-tolerance parts, such as turbine blades, impellers, and engine components. 5-axis CNC machining enables the production of these complex parts with greater efficiency and precision, meeting the industry's stringent requirements.
Automotive: In the automotive sector, 5-axis CNC machining is used to manufacture complex molds, tooling, and prototypes. Additionally, it allows the production of lightweight and intricate components for performance vehicles and advanced systems.
Medical: The medical industry benefits from 5-axis CNC machining for the fabrication of precision medical instruments, orthopedic implants, dental components, and other intricate medical devices.
Defense and Military: The defense sector often requires the production of specialized and intricate parts for various applications, including aerospace and military equipment. 5-axis CNC machining enables the production of these complex components with high accuracy.
Mold Making: In mold making industries, 5-axis CNC machining is used to create complex molds for plastic injection molding, die casting, and other manufacturing processes. The technology allows for smoother and more efficient machining of intricate mold cavities.
Prototyping and Rapid Manufacturing: 5-axis CNC machining is valuable in rapid prototyping and low-volume manufacturing. It enables designers and engineers to quickly produce functional prototypes and small batches of parts with complex geometries.
Marine and Shipbuilding: Shipbuilders use 5-axis CNC machining to manufacture intricate components for shipbuilding, such as propellers, turbine blades, and ship structures.
Energy and Power Generation: The energy industry employs 5-axis CNC machining for producing complex components used in turbines, generators, and other power generation equipment.
Tool and Die Manufacturing: In tool and die manufacturing, 5-axis CNC machining allows the production of intricate cutting tools and dies with higher precision and surface finish.
Art and Sculpture: Artists and sculptors use 5-axis CNC machines to create intricate and detailed sculptures and art pieces with various materials.
Overall, any industry that requires high-precision, complex, and customized components can benefit from 5-axis CNC machining. Its versatility and capability to produce intricate shapes and features make it an essential technology in modern manufacturing processes across multiple sectors.
What types of materials can be used in 5-axis CNC machining?
A wide range of materials can be used in 5-axis CNC machining, including metals, plastics, composites, and more.
5-axis CNC machining is versatile and can work with a wide range of materials, including metals, plastics, composites, and even certain types of wood. The specific materials that can be used in 5-axis CNC machining depend on the machine's capabilities, cutting tools, and the overall setup. Here are some common materials that are compatible with 5-axis CNC machining:
Metals:
- Aluminum: A popular material due to its lightweight, high strength-to-weight ratio, and good machinability.
- Stainless Steel: Used for its corrosion resistance and mechanical properties, commonly found in medical and aerospace components.
- Titanium: Known for its high strength, low weight, and biocompatibility, used in aerospace and medical applications.
- Brass and Copper: Often used for decorative and electrical components due to their excellent conductivity.
- Steel: A broad category that includes various grades suitable for different industrial applications.
Plastics:
- Acrylic (PMMA): Used for its optical clarity and easy machinability in producing signage, displays, and transparent components.
- ABS (Acrylonitrile Butadiene Styrene): A widely used thermoplastic with good impact resistance, commonly found in automotive and consumer goods.
- Nylon: Known for its strength, toughness, and wear resistance, used in various mechanical components.
- PEEK (Polyether Ether Ketone): A high-performance thermoplastic used in aerospace, medical, and engineering applications due to its excellent mechanical properties and resistance to chemicals and heat.
Composites:
- Carbon Fiber Reinforced Polymer (CFRP): Lightweight and strong composite material used in aerospace, automotive, and sporting goods industries.
- Glass Fiber Reinforced Polymer (GFRP): Offers good strength and durability and is used in various structural applications.
Wood:
- Hardwoods (e.g., Oak, Maple, Walnut): Used for producing wooden prototypes, custom furniture, and decorative objects.
- Medium Density Fiberboard (MDF): A wood composite often used for rapid prototyping and making tooling patterns.
Other Materials:
- Foam: Used for creating molds, patterns, and architectural models.
- Wax: Utilized in investment casting processes to create patterns for metal parts.
It's important to note that the specific suitability of a material for 5-axis CNC machining depends on factors like the machine's rigidity, spindle power, cutting tools, and the intricacy of the part being machined. Some materials may require specialized cutting tools or machining strategies to achieve optimal results.
Before starting any machining project, it is essential to consult with a knowledgeable CNC programmer or machining expert to ensure the material chosen is compatible with the 5-axis CNC machine and suitable for the desired application.
What is the maximum size of parts that can be produced using 5-axis CNC machining?
The maximum size of a part that can be produced using 5-axis CNC machining depends on the size of the CNC machine being used, but it can range from small parts to large, complex parts.
The maximum size of a part that can be produced using 5-axis CNC machining depends on several factors, including the specific capabilities of the CNC machine, the size of the machining envelope, and the type of workholding available. Typically, 5-axis CNC machines come in a variety of sizes to accommodate a variety of part sizes.
For smaller 5-axis CNC machines, the maximum part size may be limited to the following dimensions:
X-axis travel: Typically from a few inches (e.g., 10-12 inches) to a few feet (e.g., 4-6 feet).
Y-axis travel: Similar to the X-axis, ranging from a few inches to a few feet.
Z-axis travel: Typically in the range of a few inches to a few feet.
On the other hand, larger, industrial-grade 5-axis CNC machines can handle larger parts, such as:
X-axis travel: A few feet to tens of feet.
Y-axis travel: A few feet to tens of feet.
Z-axis travel: A few feet to a few yards.
The overall work envelope, or the space in which the machine can operate, is an important consideration when determining the maximum part size. Some machines may have rotary tables or other features that allow for larger part sizes or longer workpieces.
It is critical to match the size of the part to the capabilities of the machine to ensure that the part can be fully machined within the available work envelope. For very large parts that exceed the capacity of a specific 5-axis CNC machine, manufacturers may choose alternative machining methods or larger, specialized equipment.
When planning to produce large parts using 5-axis CNC machining, it is recommended to consult with a machining expert or CNC machine manufacturer to determine the appropriate machine size and work envelope to meet specific project requirements.
What level of precision can be achieved with 5-axis CNC machining?
A high level of precision can be achieved with 5-axis CNC machining, with tolerances as tight as ±0.0005 inches.
5-axis CNC machining is capable of achieving a high level of precision, allowing for the production of intricate and complex parts with tight tolerances. The precision that can be achieved with 5-axis CNC machining depends on several factors, including the machine's design and construction, the quality of the cutting tools, the rigidity of the setup, and the skill of the CNC programmer and operator.
In general, 5-axis CNC machines can achieve tolerances in the range of:
- +/- 0.005 mm to +/- 0.025 mm (0.0002 inches to 0.001 inches) for dimensions in the range of a few millimeters to a few centimeters.
- +/- 0.025 mm to +/- 0.1 mm (0.001 inches to 0.004 inches) for larger dimensions, ranging from a few centimeters to several meters.
It's important to note that achieving high precision in 5-axis CNC machining requires careful consideration of various factors, such as:
Machine Calibration: Regular calibration of the machine is essential to ensure accuracy and repeatability in the machining process.
Cutting Tools: Using high-quality cutting tools with sharp edges and proper coatings can significantly impact the precision of the machining process.
Fixture and Workholding: A rigid and stable fixture is crucial to prevent movement or vibration during machining, which can affect the accuracy of the final part.
Cutting Parameters: Optimal cutting parameters, such as cutting speed, feed rate, and depth of cut, must be carefully selected to achieve the desired precision.
Tool Path Strategies: Advanced tool path strategies and CAM software can optimize the cutting paths to minimize tool deflection and produce smoother surface finishes.
Material Properties: Understanding the material being machined and its behavior under cutting forces is essential to control dimensional accuracy.
Achieving high precision in 5-axis CNC machining allows for the production of parts used in critical applications, such as aerospace, medical devices, and precision engineering components. However, it's important to keep in mind that achieving tighter tolerances may increase machining time and cost, as it requires more careful and precise control of the entire process.
What is the cost of 5-axis CNC machining compared to other machining techniques?
The cost of 5-axis CNC machining depends on various factors such as the complexity of the part, the type of material used, and the quantity produced, but it is generally competitive with other machining techniques.
The cost of 5-axis CNC machining compared to other machining techniques can vary significantly and is influenced by several factors. While 5-axis CNC machining offers numerous advantages, it generally comes at a higher initial cost compared to traditional 3-axis or 4-axis machining. Here are some key factors that can impact the cost of 5-axis CNC machining:
Machine Cost: 5-axis CNC machines are more complex and sophisticated machines, often with additional axes and capabilities. As a result, they are generally more expensive to purchase and maintain than 3-axis or 4-axis machines.
Tooling Cost: 5-axis machining may require specialized tooling, including rotary cutters and other accessories, which can be more costly than standard tooling used in traditional machining.
Setup Time: While 5-axis machining can reduce setup time by allowing multiple operations in one setup, the initial setup for 5-axis machining may be more involved and time-consuming compared to simpler machining techniques.
Programming Complexity: The programming for 5-axis CNC machining can be more complex and may require skilled programmers, which could lead to higher programming costs.
Part Complexity: If the part design requires the use of 5-axis machining to achieve specific features or geometries, the cost may be justified by the ability to produce the part efficiently and accurately.
Production Volume: For high-volume production of relatively simple parts, traditional 3-axis or 4-axis machining may be more cost-effective. 5-axis CNC machining is often more advantageous for low-volume or complex part production.
Material Cost: The choice of material can impact the overall cost, but this factor is applicable to both 5-axis and other machining techniques.
It's important to note that the cost-effectiveness of 5-axis CNC machining depends on the specific requirements of the project and the benefits it provides. While 5-axis machining may have a higher initial cost, it can often lead to cost savings in the long run due to increased efficiency, reduced labor costs, and improved part quality. Additionally, the ability to produce complex parts in one setup can reduce overall production time and increase throughput.
Ultimately, the decision to use 5-axis CNC machining or other machining techniques depends on the complexity of the parts, production volume, budget considerations, and the desired level of precision and quality. Consulting with experienced machining professionals and analyzing the specific requirements of the project can help determine the most cost-effective approach for a given application.
How long does it take to produce parts using 5-axis CNC machining?
The production time for parts using 5-axis CNC machining depends on the complexity of the part, the type of material used, and the quantity produced, but it is generally faster than other machining techniques.
The time it takes to produce parts using 5-axis CNC machining can vary significantly depending on various factors, including the complexity of the part, the material being machined, the machining strategy, the machine's capabilities, and the desired level of precision. Here are some key factors that influence the production time:
Part Complexity: Parts with intricate geometries and complex features will generally take longer to machine than simpler parts. 5-axis CNC machining excels at producing complex shapes efficiently, but the intricacy of the part design can still impact the overall production time.
Material Type: Different materials have different machinability characteristics. Some materials, like aluminum and plastics, are generally easier to machine and may take less time compared to harder materials like titanium or stainless steel.
Tool Selection and Cutting Parameters: The choice of cutting tools and cutting parameters, such as cutting speed and feed rate, can significantly impact machining time. Proper tool selection and optimization of cutting parameters can reduce cycle times.
Machining Strategy: The choice of machining strategy, such as roughing and finishing passes, can affect the time it takes to produce the part. Advanced CAM software can optimize tool paths to minimize machining time.
Machine Capability: The specific capabilities of the 5-axis CNC machine, including spindle speed, acceleration, and rigidity, can impact machining time. More powerful and rigid machines can often achieve higher material removal rates, reducing cycle times.
Production Volume: The production volume of parts can influence the overall time. Producing multiple parts in one setup can be more time-efficient than producing them individually.
Setup Time: The initial setup time for 5-axis CNC machining may be longer than traditional machining due to the complexity of the machine and the need for precise calibration. However, once set up, 5-axis machines can reduce the need for repositioning and tool changes, potentially saving time for multi-sided machining.
It's challenging to provide an exact estimate of the production time without specific details about the part and machining process. In some cases, 5-axis CNC machining can significantly reduce production time compared to other machining techniques, especially for complex parts that would require multiple setups in traditional machining.
To determine the expected production time, it's best to consult with experienced CNC programmers and machinists who can analyze the part design, material, and machining requirements to provide accurate time estimates. Additionally, modern CAM software can simulate the machining process and provide estimated cycle times for better planning and optimization.
How do you ensure the quality of parts produced using 5-axis CNC machining?
Quality control measures such as inspection and testing are used to ensure the quality of parts produced using 5-axis CNC machining.
Ensuring the quality of parts produced using 5-axis CNC machining involves a combination of careful planning, proper machine setup, effective programming, and thorough inspection. Here are some key steps and best practices to ensure the quality of the machined parts:
Design Review: Begin by reviewing the part design to identify potential challenges and critical features that require precise machining. Work with the design team to ensure that the design is manufacturable and suitable for 5-axis CNC machining.
Material Selection: Choose appropriate materials with the required mechanical properties for the intended application. Ensure that the selected material is compatible with the 5-axis CNC machine and the cutting tools being used.
Machine Calibration: Regularly calibrate the 5-axis CNC machine to maintain its accuracy and repeatability. Ensure that all axes are correctly aligned and calibrated to avoid errors in machining.
Cutting Tools and Toolpath Optimization: Select high-quality cutting tools that are suitable for the material and geometry of the part. Optimize the tool paths using advanced CAM software to reduce cutting forces, minimize tool deflection, and achieve the desired surface finish.
Workholding and Fixturing: Use proper workholding techniques and fixtures to secure the workpiece firmly during machining. A rigid setup minimizes vibration and ensures consistent machining results.
Programming and Simulation: Thoroughly program the CNC machine using accurate CAD/CAM software. Utilize simulation tools to verify the tool paths and identify any potential collisions or errors before running the actual machining process.
Inspection and Quality Control: Perform regular in-process inspections to verify the dimensions and features of the machined part. Use precision measuring instruments like calipers, micrometers, and CMM (Coordinate Measuring Machine) for accurate measurements.
Surface Finish and Deburring: Pay attention to the surface finish of the machined part. Properly deburr and remove sharp edges to meet the required quality standards.
Process Documentation: Maintain detailed records of the machining process, including setup parameters, tooling information, and inspection results. This documentation aids in traceability and facilitates corrective actions if needed.
Continuous Improvement: Continuously monitor and analyze the machining process to identify areas for improvement. Implement corrective actions and refine processes to enhance overall quality and productivity.
Operator Training: Ensure that the CNC machine operators are well-trained and experienced in 5-axis machining. Skilled operators can respond to challenges effectively and make adjustments as needed during the machining process.
By implementing these steps and adhering to best practices, manufacturers can ensure the consistent quality of parts produced using 5-axis CNC machining. Emphasizing quality control throughout the entire production process helps deliver precision parts that meet or exceed customer expectations.
What is the difference between simultaneous 5-axis machining and 3+2 axis machining?
Simultaneous 5-axis machining and 3+2 axis machining are two different techniques used in 5-axis CNC machining. Simultaneous 5-axis machining involves the cutting tool moving along five axes simultaneously, while 3+2 axis machining involves the cutting tool moving along three axes while the workpiece is tilted along two additional axes.
Simultaneous 5-axis machining and 3+2 axis machining are two different strategies used in 5-axis CNC machining, each with its own advantages and applications. Let's explore the key differences between these two machining techniques:
Simultaneous 5-Axis Machining:
- In simultaneous 5-axis machining, the cutting tool can move along all five axes (X, Y, Z, A, and B) simultaneously during the machining process.
- This means the tool can approach the workpiece from any angle and orientation, allowing for continuous and smooth tool paths, especially when machining complex 3D geometries and sculptured surfaces.
- Simultaneous 5-axis machining is ideal for parts with intricate curves, undercuts, and compound angles, as it can efficiently machine these features without the need for multiple setups or repositioning the workpiece.
- The ability to machine complex parts in one setup improves accuracy and reduces cycle times, making it suitable for industries like aerospace, automotive, and medical where high-precision components are required.
3+2 Axis Machining:
- 3+2 axis machining, also known as positional 5-axis machining, is a technique where the cutting tool is limited to three linear axes (X, Y, and Z) for the main cutting motion, while the remaining two rotational axes (A and B) are locked or fixed at specific angles.
- The tool is repositioned and locked into a new orientation at each step or "index" before the cutting process starts, effectively machining the part from different directions but not moving all axes simultaneously during cutting.
- While 3+2 axis machining cannot follow complex tool paths like simultaneous 5-axis machining, it allows for more stable cutting conditions as the tool is only cutting along three linear axes at a time.
- 3+2 axis machining is suitable for parts with features that can be accessed from specific angles without the need for complex tool movements. It is often used for roughing, finishing, and secondary operations on parts that don't require full 5-axis simultaneous motion.
- This technique is popular for machining complex parts while maintaining better tool control and rigidity compared to traditional 3-axis machining.
In summary, simultaneous 5-axis machining and 3+2 axis machining are two different approaches used in 5-axis CNC machining. Simultaneous 5-axis machining allows for continuous and complex tool paths, making it ideal for intricate parts, while 3+2 axis machining provides more stability and control for parts that can be machined from specific orientations without the need for full 5-axis simultaneous motion. The choice between these techniques depends on the specific requirements of the part being machined and the desired level of complexity and precision.
Can 5-axis CNC machining be used for prototyping and small production runs?
Yes, 5-axis CNC machining can be used for prototyping and small production runs, as well as large-scale production runs.
5-axis CNC machining can be used for both prototyping and small production runs. While 5-axis CNC machines are often associated with high-end and complex manufacturing, they are also versatile enough to accommodate low-volume production and rapid prototyping.
Here's how 5-axis CNC machining is beneficial for prototyping and small production runs:
Rapid Prototyping: 5-axis CNC machining allows for the quick production of functional prototypes with complex geometries. The ability to machine parts from multiple angles and orientations in one setup facilitates the creation of intricate designs without the need for specialized tooling or multiple operations.
Reduced Setup Time: 5-axis machining can reduce setup time compared to traditional machining methods. The ability to machine complex parts in a single setup eliminates the need for repositioning the workpiece and reduces the time spent on fixture changes.
Flexibility and Iteration: For prototyping, design changes and iterations are common. 5-axis CNC machining allows for easy adjustments to the machining program, enabling rapid testing and modification of the design.
Shorter Lead Times: The efficiency of 5-axis CNC machining can result in shorter lead times for both prototypes and small production runs. This is especially beneficial for getting products to market quickly and meeting tight project timelines.
High Precision: 5-axis CNC machining ensures high precision and accuracy, crucial for prototyping and small production runs that require parts with tight tolerances and intricate details.
Material Versatility: 5-axis CNC machines can work with a wide range of materials, including metals, plastics, composites, and wood, providing flexibility in material selection for prototypes and production runs.
Cost-Effectiveness: While 5-axis CNC machining may have higher initial setup costs, it can be cost-effective for low-volume production, as it reduces labor time and manual interventions compared to traditional machining methods.
Multi-Axis Features: For parts that require complex features, such as undercuts or compound angles, 5-axis CNC machining is often the most efficient and accurate method for production.
As with any manufacturing process, it is essential to consider factors like part complexity, material choice, and budget constraints when deciding to use 5-axis CNC machining for prototyping and small production runs. Working with an experienced CNC machining service provider can help ensure that the most appropriate machining technique is chosen to meet the specific requirements of the project.
Why use 5 axis machining?
5-axis machining has many advantages that make it a top choice for a variety of industries and applications. Here are some key reasons to use 5-axis machining:
Complex Geometries: 5-axis machining allows the production of parts with complex geometries that are difficult or impossible to achieve with traditional 3-axis or 4-axis machining. Additional axes give the cutting tool access to multiple angles and orientations, facilitating the machining of undercuts, overhangs and compound angles.
Single-setup efficiency: 5-axis machining reduces the need for multiple setups because it can machine parts from multiple sides in one setup. This significantly improves efficiency, reduces processing time, and minimizes the chance of introducing errors during workpiece repositioning.
Precision and Accuracy: Continuous tool paths in five-axis machining allow for greater precision and accuracy. The cutting tool maintains its optimal orientation, resulting in tighter tolerances and better surface finish on machined parts.
Reduced tool wear: 5-axis machining allows for optimized tool paths, minimizing unnecessary tool engagement and reducing tool wear. This results in longer tool life and lower tool costs.
Versatility: 5-axis CNC machines can process a wide range of materials, including metals, plastics, composites, and wood, making them suitable for a wide range of industries and applications.
Improved surface finish: The ability to approach the workpiece from different angles and directions results in a smoother surface finish on the machined part.
Reduced production time: 5-axis machining can reduce overall production time by combining multiple machining operations into a single setup. This not only saves time but also increases throughput and productivity.
Design freedom: Manufacturers have more design freedom when using 5-axis machining because it can produce parts with complex features without compromising manufacturability.
Cost-effectiveness in small batch production: Although 5-axis machines have a higher initial cost, they are cost-effective in small batch production due to reduced labor time and increased efficiency.
Complex toolpaths: 5-axis machining allows for complex toolpaths that can optimize material removal, improve surface finish, and reduce machining time, making it a valuable technology for parts with challenging geometries.
Overall, 5-axis machining is chosen because of its ability to produce complex parts with high precision, efficiency, and versatility. Its advantages make it an important technology for industries such as aerospace, automotive, medical, and mold making that require complex and precise components.