Auto Plastic Metal Parts
Our company specializes in making high-quality plastic metal parts for cars. We design, develop, and manufacture these parts to meet the needs of the auto industry. Over 90% of car parts are made using molds, including ours which use both cold and hot working processes as well as plastic molding. On average, it takes about 1500 molds to build a single car, with nearly 1000 of those being stamping dies and more than 200 internal components.
We're dedicated to creating top-notch plastic metal parts for the automotive sector. As the demand for these parts grows globally, we ensure our customers get excellent quality, fair prices, and quick delivery times. Our range includes essential car parts like bumpers, lights, and doors. With years of experience in this field, we've honed our skills to perfection, offering reliable and efficient services every time.
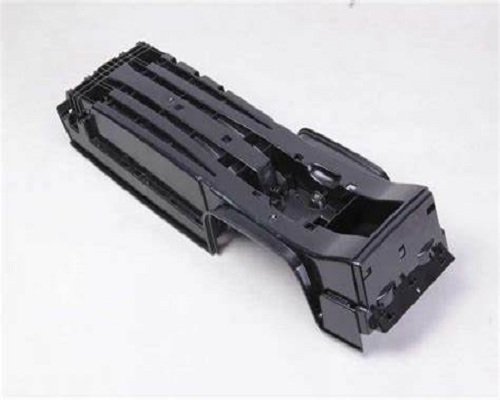
Auto Parts
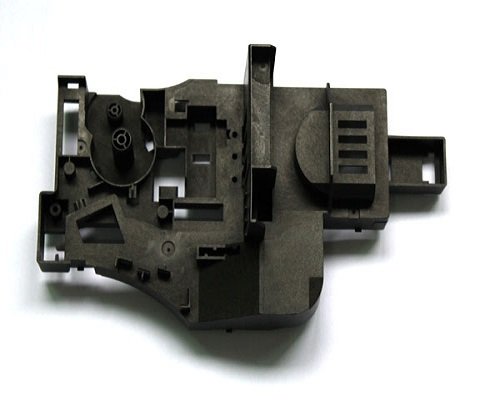
Automotive Parts
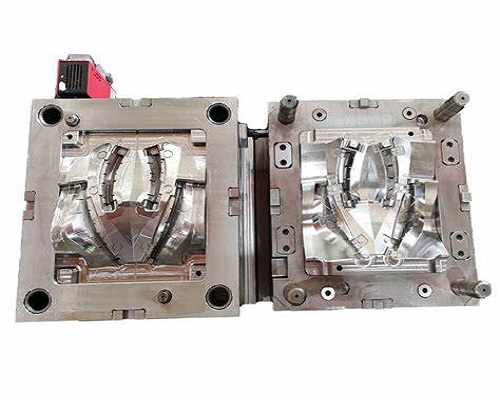
Automobile Parts Mold
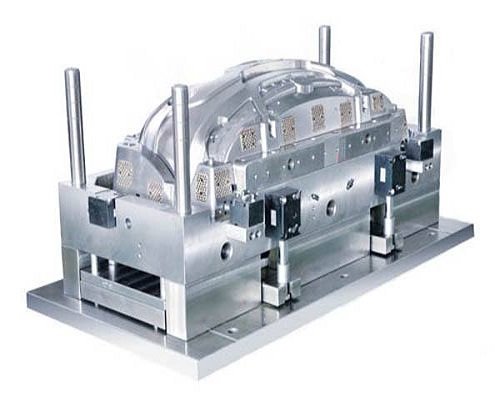
Auto Parts Mould
Auto Plastic Metal Parts Making Service
Be good at product structure optimization and greatly reduce the cost of Plastic Metal Parts custom solutions
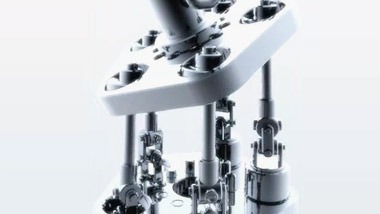
Part Design
Appearance and structural design
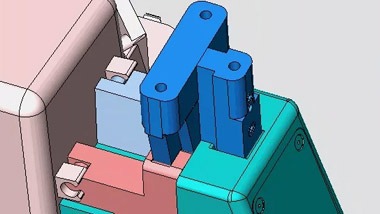
Mold Making
Design, DFM confirmation

Product Assembly
Incoming materials, inspection and assembly
Plastic Metal Parts are used in the automotive industry
Plastic metal parts are super important in making lots of things, especially in cars. These parts help make sure everything works just right.
In the car world, we use these plastic metal bits for all sorts of stuff, like dashboards, door handles, engine covers, and even big body panels. They're usually made from strong steel or aluminum to handle the heat and pressure when they're made.
One cool thing about using these parts is that they make everything really accurate and the same every time. Since each part is made specifically for its job, it fits perfectly and works as expected when put together.
Another great thing is that they speed up production a lot. Once the mold is ready, making the parts is quick and you can get tons of them fast. This is super helpful in the car industry where deadlines are tight and demand is high.
These plastic metal parts are also really flexible. You can use them to make anything from tiny inside pieces to huge outside panels. That makes them perfect for the car industry where different models need different parts.
But, there are some tough parts too. Making these custom molds can be expensive, which is hard on smaller companies. Also, the molds need regular care because the high heat and pressure can wear them out over time. If not taken care of, this can mess up the final product. So, keeping the molds in good shape is important but can take time and money.
Even with these challenges, plastic metal parts are still key in the car industry. Their precision, speed, and versatility make them ideal for creating all kinds of parts. As the automotive industry keeps changing and improving, these parts will keep being crucial in making high-quality components that are vital for modern vehicles.
FAQ about Automotive Plastic Metal Parts
What are Automotive Plastic Metal Parts?
Automotive plastic and metal parts refer to components used in vehicles that are made from either plastic or metal materials. These parts can include everything from the body panels and bumpers to engine components and interior trim. The choice between plastic and metal depends on factors like weight, durability, cost, and the specific function of the part.
Why are plastic parts used in automobiles?
Plastic parts are favored in automotive manufacturing due to their lightweight nature, which helps improve fuel efficiency. Additionally, plastics can be molded into complex shapes more easily than metals, allowing for greater design flexibility. They also tend to be more corrosion-resistant and can absorb impact better, enhancing safety.
Are metal parts stronger than plastic parts?
Generally, metal parts are stronger and more durable than plastic parts. However, advancements in plastic technology have led to the development of high-performance plastics that can rival metals in certain applications. The choice between metal and plastic often comes down to the specific requirements of the part and its intended use.
Can plastic parts replace metal parts in cars?
Yes, plastic parts can replace metal parts in many areas of a car. For instance, plastic is commonly used for bumpers, dashboards, and even some engine components. The key advantage is that plastic parts are lighter and can be designed to meet the required strength and durability standards.
How do you maintain plastic and metal parts in a vehicle?
Maintenance for plastic and metal parts differs slightly. Metal parts may require regular checks for rust and corrosion, and they might need lubrication to ensure smooth operation. Plastic parts generally require less maintenance but should be kept clean and protected from harsh chemicals that could cause degradation.
Are there any environmental concerns with using plastic parts in automobiles?
Yes, there are environmental concerns related to the use of plastic parts. Plastics are not biodegradable and can contribute to pollution if not properly recycled. However, many automotive manufacturers are working on solutions, such as using recycled plastics and developing biodegradable alternatives to mitigate these issues.
Do plastic parts affect the resale value of a car?
The impact of plastic parts on a car's resale value can vary. High-quality plastic components that are well-maintained can actually enhance the vehicle's appearance and functionality, potentially increasing its resale value. Conversely, cheap or poorly maintained plastic parts might detract from the car's overall appeal.
What are the cost implications of using plastic versus metal parts?
Plastic parts are generally less expensive to produce than metal parts, primarily because plastic is cheaper to manufacture and easier to mold into complex shapes. This can lead to cost savings in both production and assembly. However, the initial material cost is just one factor; the long-term durability and performance of the parts also play a crucial role.
How do temperature changes affect plastic and metal parts?
Temperature changes can significantly affect both plastic and metal parts. Metals expand and contract with temperature variations, which can lead to issues like warping or stress cracks if not managed properly. Plastics can become brittle in extremely cold temperatures and soft or warped in very hot conditions, posing potential risks for their structural integrity.
What innovations are being made in automotive plastic and metal parts?
Recent innovations include the development of composite materials that combine the best properties of both plastics and metals. There's also a growing focus on using recycled and sustainable materials to reduce environmental impact. Advances in 3D printing technology are enabling more customized and efficient manufacturing processes for both types of parts.