The seemingly simple dichotomy of core and cavity in injection molding belies a complex interplay of material science, thermodynamics, and precision engineering. Far from being merely "parts" of a mold, the core and cavity represent the very crucible of transformation, where molten polymer transitions from a chaotic fluid state to a precisely defined solid form. Their interaction dictates not only the fidelity of the final product but also the economic viability and lifespan of the entire molding operation. from mold7.
The conventional understanding – that the core forms the shape and the cavity contains the molten plastic – is an oversimplification. A more nuanced perspective reveals a dynamic relationship. The core, typically crafted from hardened steel or specialized alloys capable of enduring immense thermal and mechanical stress, acts as a negative imprint, defining the internal geometries and features of the molded part. The cavity, while seemingly passive, plays a crucial role in controlling heat transfer, influencing the cooling rate, and consequently, the final crystallinity and mechanical properties of the molded component. The design of the cavity, therefore, is not merely a matter of accommodating the molten material; it is a sophisticated manipulation of thermal gradients to achieve optimal part quality.
The selection of materials extends beyond simple strength considerations. Thermal conductivity, coefficient of thermal expansion, and resistance to chemical degradation all play critical roles in determining the longevity and performance of the mold. The choice between steel, aluminum, beryllium copper, or even specialized polymers for the cavity, for example, will significantly impact cycle times, dimensional stability, and the overall cost-effectiveness of the operation. Further complicating the matter is the intricate design of the cooling channels, often involving complex geometries and strategically placed manifolds to ensure uniform cooling and minimize warping or sink marks. This necessitates sophisticated computational fluid dynamics (CFD) simulations to optimize cooling efficiency and minimize energy consumption.
Beyond the initial design, the operational realities introduce further layers of complexity. Mold wear, far from being a simple matter of abrasion, involves a complex interplay of erosion, corrosion, and even micro-cracking induced by thermal cycling. This wear is not uniform; localized stress concentrations can lead to premature failure in critical areas, necessitating predictive maintenance strategies and potentially the implementation of advanced surface treatments to enhance durability. Similarly, clogging is not simply a matter of solidified plastic; it can involve the accumulation of degradation products, the formation of weld lines, or even the entrapment of air bubbles, each requiring specific preventative measures and remediation techniques. The continuous monitoring and analysis of process parameters, coupled with advanced diagnostic tools, are essential for maintaining optimal performance and preventing catastrophic failures.
In conclusion, the core and cavity of an injection mold are far more than simple components; they are the heart of a complex system, demanding a deep understanding of materials science, thermodynamics, and manufacturing engineering to ensure both the quality of the final product and the long-term viability of the production process. The seemingly straightforward initial concept gives way to a multifaceted challenge requiring continuous optimization and adaptation.
The seemingly mundane injection molding process hinges on a complex interplay between core and cavity—two components whose precise geometries dictate the final form of the plastic part. Far from simple shapes, these elements represent a sophisticated engineering challenge, demanding meticulous design and robust materials to withstand the extreme pressures and temperatures inherent in the process.
The core, residing within the cavity, defines the internal architecture of the molded piece. Its design isn't merely about creating holes; it encompasses the precise rendering of intricate internal features—threads, undercuts, internal channels—each demanding a nuanced understanding of material flow and potential for stress concentration. Manufacturing tolerances must be razor-sharp; microscopic deviations can result in catastrophic failure or unacceptable dimensional inaccuracies.
The cavity, conversely, dictates the external contours of the final product. This isn't simply about replicating a surface; it's about managing the complex interplay of surface tension, cooling rates, and material shrinkage. The cavity's design must account for subtle variations in material behavior, anticipating shrinkage and warping to ensure dimensional stability and aesthetic perfection. The seemingly insignificant draft angles, for instance, are crucial for efficient part ejection, preventing damage to both the part and the mold itself.
The materials themselves are far from ordinary. High-grade tool steels and specialized alloys, chosen for their exceptional wear resistance and thermal stability, are subjected to intense cyclical loading. The selection process is critical, balancing cost with the required lifespan and the ability to withstand the corrosive effects of molten polymers. Even the surface treatments applied to these materials—nitriding, hard chrome plating—play a significant role in extending the mold's operational life.
The injection process itself is a dynamic event, a carefully orchestrated ballet of molten polymer flow, pressure gradients, and thermal transfer. The design of the runner system, the gate locations, and the cooling channels are all intimately linked to the core and cavity geometries, influencing the final part's quality and structural integrity. Defects such as sink marks, weld lines, and warping, often subtle yet devastating, are direct consequences of imperfections in this intricate interplay.
The design of the core and cavity is therefore not merely a matter of CAD modeling; it requires a deep understanding of materials science, fluid dynamics, and heat transfer. The expertise of mold engineers is paramount, their knowledge shaping not only the final product but also the economic viability of the entire manufacturing process. A poorly designed mold can lead to costly downtime, scrap parts, and ultimately, a compromised product. The core and cavity, therefore, are not just components; they are the heart of the injection molding process, their precision defining the success or failure of the entire enterprise.
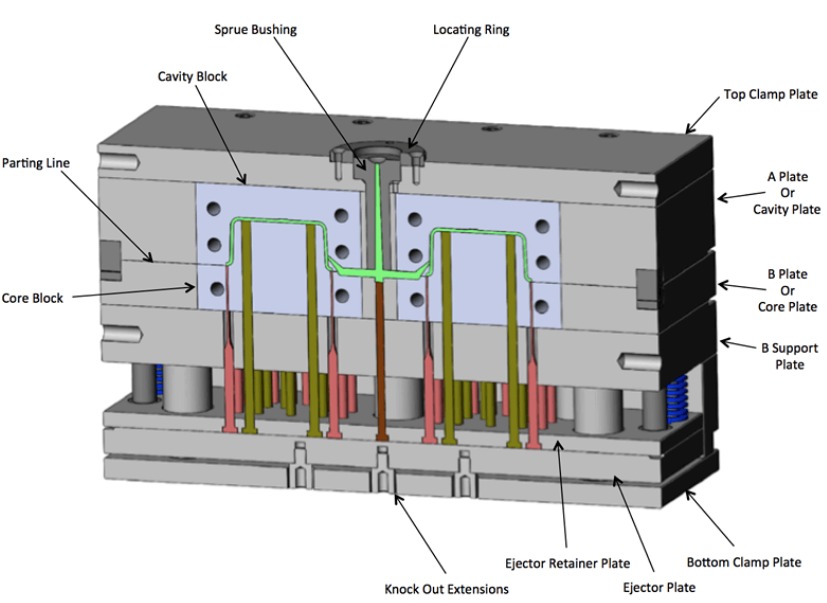
What is Injection Mold Core and Cavity?
The core and cavity are the backbone of an injection mold, shaping and sizing the final product. The core, or male part, fits snugly into the cavity, which is the female part surrounding it. Both parts are typically crafted from tough steel or alloys that can handle high heat and pressure.
Getting the core and cavity to fit just right is key. They need to match up perfectly, leaving only a tiny gap for the molten plastic to flow in and fill every nook and cranny. Once the plastic cools down and solidifies, the mold opens, and out pops the finished item.
Injection molding works by melting plastic and then forcing it into the mold under intense pressure. The mold's design has to be strong enough to withstand these extreme conditions, ensuring the final product comes out just as needed.
In essence, the core and cavity are vital parts of the injection mold, teaming up to create the desired shape and size. Made from resilient materials, they ensure the molten plastic fills the mold completely. When the plastic hardens, the mold opens, releasing the end product.
What are the Functions of Injection Mold Core and Cavity?
The core and cavity have several functions in the injection molding process, such as:
- Forming the shape and size of the molded part. The core and cavity determine the geometry, dimensions, and features of the molded part. They also affect the appearance, strength, and functionality of the part.
- Controlling the flow and cooling of the molten plastic. The core and cavity influence the flow rate, pressure, temperature, and direction of the molten plastic in the mold. They also affect the cooling rate, shrinkage, warpage, and crystallization of the plastic.
- Providing support and alignment for the mold components. The core and cavity provide structural support for other mold components such as runners, gates, vents, ejector pins, etc. They also ensure proper alignment and fit between the mold halves.
How to Design Injection Mold Core and Cavity?
The core and cavity are the two main components of an injection mold. The core is the part that forms the internal shape of the molded part, while the cavity is the part that forms the external shape. The core and cavity are usually made of steel or aluminum and are machined to fit together precisely. The design of the core and cavity depends on several factors, such as the type of material to be molded, the shape and size of the part, the molding process parameters, and the quality requirements.
Some of the main steps involved in designing the core and cavity are:
- Analyze the part geometry and identify the parting line, which is the line where the core and cavity separate during mold opening.
- Determine the number and location of the gates, which are the openings where the molten material enters the mold cavity.
- Select the type and size of the runners, which are the channels that connect the gates to the sprue, which is the main inlet of the mold.
- Choose the type and size of the ejector pins, which are the devices that push the molded part out of the core after cooling.
- Design the cooling system, which consists of water or oil channels that circulate around the core and cavity to control their temperature and prevent warping or shrinkage of the molded part.
- Add any other features or accessories that are needed for the mold function, such as vents, slides, lifters, inserts, etc.
The design of the core and cavity should ensure that:
- The mold can fill uniformly and completely without defects such as short shots, flash, weld lines, sink marks, etc.
- The mold can open and close smoothly without excessive force or wear.
- The mold can eject the part easily without damage or deformation.
- The mold can withstand the high pressure and temperature of the molding process without cracking or distortion.
- The mold can produce parts that meet the specifications and quality standards.
The design of the core and cavity is a complex and critical task that requires a lot of experience and knowledge. It is advisable to use computer-aided design (CAD) software and simulation tools to optimize the design and verify its feasibility before manufacturing. A well-designed core and cavity can improve the efficiency and profitability of injection molding.
What are the Common Problems of Injection Mold Core and Cavity?
The injection mold core and cavity are the two main components of the mold, which shape plastic parts during the injection molding process. The core is the male component that forms the internal features of the part, while the cavity is the female component that forms the external features of the part. The core and cavity are designed to fit precisely together, leaving a small gap between them where the molten plastic flows and solidifies.
However, there are some common problems that can affect the quality and functionality of the injection molded parts due to defects in the core and cavity design or manufacturing. Some of these problems are:
- Flash: Flash is the excess plastic material that escapes from the mold and forms thin projections along the parting line or around inserts. Flash can occur due to excessive injection pressure, poor clamping force, worn or damaged mold surfaces, or improper venting of the mold.
- Short shot: Short shot is the incomplete filling of the mold cavity, resulting in a part that is smaller than intended or missing some features. Short shot can occur due to insufficient injection pressure, low melt temperature, inadequate venting, or obstructions in the runner system.
- Sink marks: Sink marks are depressions or dimples on the surface of the part, caused by shrinkage of the plastic material as it cools. Sink marks can occur due to thick or uneven wall sections, insufficient cooling time, high injection pressure, or low packing pressure.
- Warping: Warping is the distortion or deformation of the part shape, caused by uneven shrinkage or residual stresses in the plastic material. Warping can occur due to non-uniform wall thickness, different cooling rates, high injection speed, or improper orientation of fibers or fillers in the material.
- Ejector marks: Ejector marks are indentations or scratches on the surface of the part, caused by the action of the ejector pins that push the part out of the mold. Ejector marks can occur due to excessive ejection force, misaligned or damaged ejector pins, or rough or dirty mold surfaces.
To prevent or minimize these problems, it is important to design and manufacture the core and cavity with high accuracy and precision, taking into account factors such as material properties, mold temperature, injection pressure, cooling time, and ejection system. Additionally, regular inspection and maintenance of the mold are essential to ensure its optimal performance and longevity.
How to Prevent and Solve Injection Mold Core and Cavity Problems?
The insidious nature of injection mold core and cavity defects—manifest as flash, short shots, sink marks, warping, and dimensional inconsistencies—demands a rigorous, multifaceted approach to prevention and remediation. Mere adherence to "best practices" is insufficient; a profound understanding of material science, thermal dynamics, and precision engineering is paramount.
Optimal core and cavity design transcends the simplistic application of draft angles. Precise calculations, informed by finite element analysis (FEA) and considering the viscoelastic properties of the injected polymer under extreme pressure and temperature gradients, are crucial for minimizing ejection forces and preventing premature wear. Material selection extends beyond rudimentary considerations of hardness and thermal conductivity. The interplay of coefficient of thermal expansion (CTE) mismatch between core, cavity, and the molded part itself, coupled with the potential for stress corrosion cracking, necessitates a sophisticated materials engineering approach. High-performance alloys, specialized steels, and even advanced ceramic composites may be required, their selection dictated by the specific polymeric material and the desired production cycle.
Surface treatments are not merely cosmetic enhancements. Advanced techniques like plasma nitriding, electroless nickel plating, and diamond-like carbon (DLC) coatings offer tailored solutions for wear resistance, lubricity, and corrosion protection, each impacting mold longevity and part quality in unique ways. Their selection demands a detailed analysis of the specific challenges posed by the molding process and the material being processed.
Precise alignment and fit are not simply achieved through rudimentary machining. Laser interferometry and advanced metrology techniques are essential for ensuring sub-micron tolerances, minimizing the potential for flash and dimensional inaccuracies. The integration of sophisticated clamping systems and precision guiding mechanisms is crucial for maintaining this alignment throughout the mold's operational lifespan.
Cooling channel design is far from trivial. Computational fluid dynamics (CFD) simulations are indispensable for optimizing coolant flow, ensuring uniform temperature distribution, and preventing thermal stresses that lead to warping or sink marks. The selection of cooling media and the incorporation of advanced cooling technologies, such as micro-channels or conformal cooling, can significantly impact cycle times and part quality.
Preventative maintenance transcends routine cleaning and lubrication. Regular, non-destructive testing (NDT) employing techniques like ultrasonic inspection and dye penetrant testing is essential for early detection of micro-cracks and other defects before they escalate into catastrophic failures. Predictive maintenance strategies, utilizing data analytics from sensor integration within the mold, offer the potential for proactive intervention, minimizing downtime and maximizing production efficiency.
In conclusion, mastering the complexities of injection mold core and cavity technology demands a holistic approach, integrating advanced design principles, sophisticated materials science, precision manufacturing techniques, and proactive maintenance strategies. Only through such a rigorous commitment can injection molders consistently produce high-quality products and maintain a competitive edge in a demanding market.