Aluminium Metal Parts Materials
Aluminum has a relatively light weight, low rebound during molding, high strength, close to or exceeding high-quality steel, good plasticity, and is easier to control than stainless steel when forming complex products. It has excellent conductivity, thermal conductivity, and corrosion resistance. Currently, the surface treatment processes for aluminum, such as anodizing, wire drawing, and sandblasting, are very mature, and aluminum is widely used in mobile phones.
According to the processing method, aluminum alloys can be divided into deformed aluminum alloys and cast aluminum alloys. The numbering of aluminum and aluminum alloys is mainly divided into eight series. The international grades (Represented by 4 Arabic numerals) are as follows:
1XXX represents pure aluminum series with over 99% purity, such as 1050 and 1100
2XXX represents the aluminum copper alloy series, such as 2014
3XXX represents the aluminum manganese alloy series, such as 3003
4XXX represents the aluminum silicon alloy series, such as 4032
5XXX represents the aluminum magnesium alloy series, such as 5052
6XXX represents the aluminum magnesium silicon alloy series, such as 6061 and 6063
7XXX represents the aluminum zinc alloy series, such as 7001
8XXX represents alloy systems other than those mentioned above
Aluminium Metal Parts Making Service
Be good at product structure optimization and greatly reduce the cost of Aluminium Metal Parts Materials
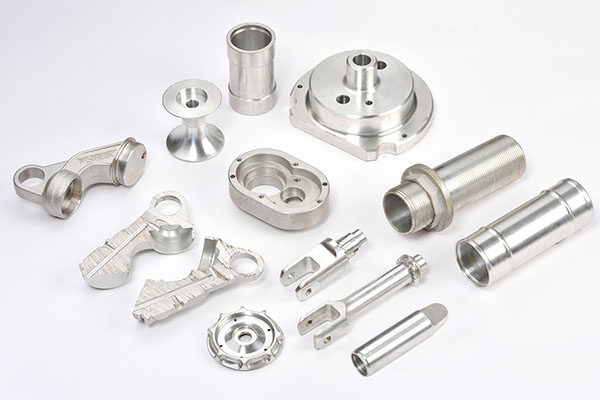
Part Design
Appearance and structural design
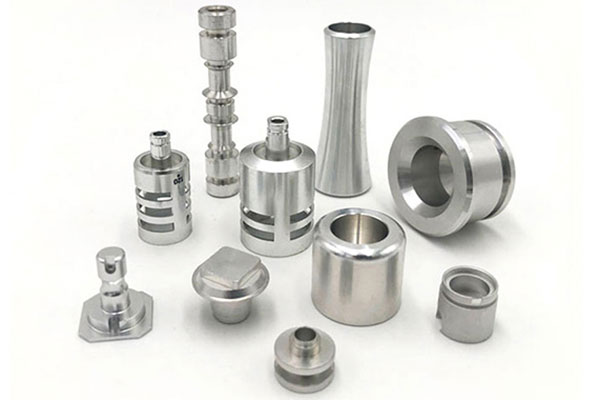
Mold Making
Design, DFM confirmation
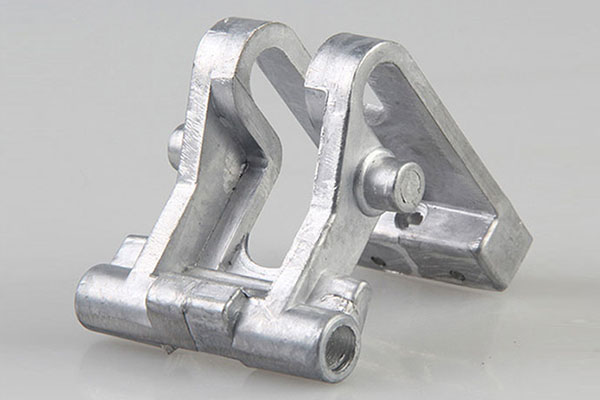
Product Production
Imported, high-speed equipment
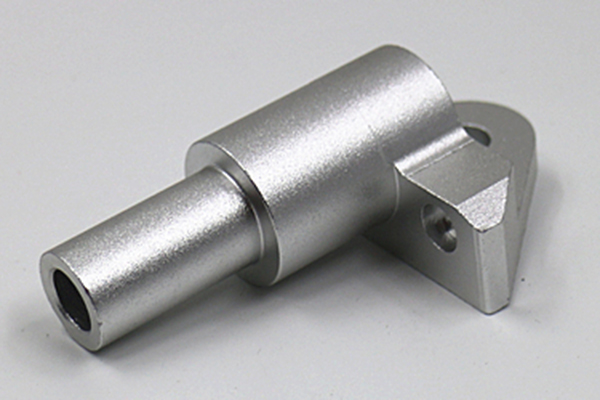
Product Assembly
Incoming materials, inspection and assembly
Model classification of Aluminium Metal Parts Materials
The 1000 series has the highest aluminum content among all series, with a purity of over 99.00%. The minimum aluminum content of the 1000 series aluminum plate is determined based on the last two Arabic numerals. For example, the last two Arabic numerals of the 1050 series are 50. According to international brand naming principles, the aluminum content must be above 99.5% to be a qualified product. The models include 1060, 1085, 1080, 1070, 1050, 1N30, 1100, 1200, 1N00,
The 1000 series aluminum has good formability and surface treatment, and its corrosion resistance is the best among aluminum alloys. Its strength is low, and the higher the purity, the lower its strength.
The commonly used ones on mobile phones are 1050, 1070, 1080, 1085, and 1100, which can be used for simple extrusion molding (without bending). Among them, 1050 and 1100 can be used for chemical sandblasting, smooth surface, matte surface, normal effect, with obvious material patterns and good coloring effect; 1080 and 1085 mirror aluminum are commonly used for bright text and matte effects, without obvious material patterns.
The aluminum materials of the 1000 series are relatively soft and mainly used for decorative or interior parts.
The characteristic is high hardness, but poor corrosion resistance, with the highest copper content, represented by the 2000 series aluminum alloys 2024, 2A16, and 2A02. The copper content of the 2000 series aluminum plate is around 3-5%. The models include 2011, 2014, 2017, 2024, 2117, 2018, 2218, 2618, 2219, 2025, and 2N01.
The 2000 series aluminum bars belong to aviation aluminum materials and are used as construction materials. Currently, they are not commonly used in conventional industries.
The 3000 series aluminum rod is mainly composed of manganese element. The 3000 series aluminum alloy mainly represents 3003, 3105, and 3A21. The content is between 1.0-1.5, making it a series with good rust prevention function. The models include 3003, 3203, 3004, 3104, 3005, and 3105.
Commonly used as tanks and cans for liquid products, construction processing parts, construction tools, various lighting components, as well as various pressure vessels and pipelines for sheet metal processing. Good formability, solubility, and corrosion resistance.
Usually, the silicon content is between 4.5-6.0%, and higher silicon content leads to relatively higher strength. The 4000 series aluminum rods are represented by 4A01, and the 4000 series aluminum plates belong to the series with higher silicon content. Good soup flow, minimal solidification shrinkage, belonging to building materials, mechanical parts, forging materials, welding materials; Low melting point, good corrosion resistance, and possessing characteristics of heat resistance and wear resistance. The models include 4032 and 4043.
The 5000 series aluminum rod belongs to the commonly used alloy aluminum plate series, with magnesium as the main element and a magnesium content between 3-5%. The 5000 series aluminum alloy represents the 5052, 5005, 5083, and 5A05 series. Also known as aluminum magnesium alloy. The main characteristics are low density, high tensile strength, and high elongation. The weight of aluminum magnesium alloy is lower than other series under the same area, and it is also widely used in conventional industry. The models include 5005, 5052, 5652, 5154, 5254, 5454, 5056, 5082, 5182, 5083, 5086, 5N01, and 5N02.
The most commonly used alloy on mobile phones is 5052, which is the most representative alloy with moderate strength. It has good corrosion resistance, solubility, and formability, especially high fatigue strength and excellent seawater resistance. It is commonly used to make products with high strength requirements, but its coloring effect is not ideal. It is suitable for sandblasting process and not suitable for chemical sandblasting, matte coating, etc. It is mainly formed by casting and not suitable for extrusion molding.
The 6000 series aluminum alloy represents 6061, which mainly contains magnesium and silicon elements, thus combining the advantages of the 4000 series and 5000 series. 6061 is a cold treated aluminum forging product suitable for applications with high requirements for corrosion resistance and oxidation resistance. Good usability, easy coating, and good processability. The models include 6061, 6N01, 6063, 6101, and 6151.
6061 and 6063 are commonly used on mobile phones, with 6061 having higher strength than 6063. By casting, it can produce complex structures and make components with buckles, such as battery covers.
Mainly containing zinc element, the 7000 series aluminum alloy represents 7075. Also belonging to the aviation series, it is an aluminum magnesium zinc copper alloy, a heat treatable alloy, and a superhard aluminum alloy with good wear resistance. At present, we mainly rely on imports, and our country's production technology still needs to be improved. The models include 7072, 7075, 7050, 7N01, and 7003.
The commonly used 8000 series aluminum alloy is 8011, which belongs to other series and is mostly used as aluminum foil. It is not commonly used in the production of aluminum bars.
Machining Process of Aluminium Metal Parts
There are many ways to produce and process aluminum parts. Firstly, we can produce aluminum parts through casting. Casting is a method of pouring molten aluminum into a mold, and then cooling and solidifying it into shape. This method is suitable for producing parts with complex shapes.
Secondly, we can also process aluminum parts through forging. Forging is the process of pressing and deforming aluminum materials heated to a certain temperature on a forging press to obtain the desired shape and size of the parts. Forging can improve the strength and toughness of aluminum parts.
In addition, we can also use cutting processing to manufacture aluminum parts. Cutting is the process of cutting, milling, drilling, and other operations on aluminum materials using cutting tools to obtain the desired shape and size of the parts. This method is suitable for producing parts with high precision requirements.
Finally, we can also connect aluminum parts through welding. Welding is a method of melting the contact surfaces of two or more aluminum parts and solidifying them together. Welding can be used to repair damaged parts or connect parts of different shapes together.
In general, there are various production and processing methods for aluminum parts, and suitable methods can be selected according to specific needs.
FAQ About Aluminium Metal Parts
You should consider aluminium parts because they offer a fantastic blend of strength and lightweight properties. This makes them ideal for applications where weight is a critical factor, such as in the automotive or aerospace industries. Aluminium is also highly resistant to corrosion, which means it can withstand harsh environmental conditions without deteriorating quickly. Additionally, its excellent thermal conductivity allows for efficient heat dissipation, which is crucial in many industrial applications. Another great advantage is that aluminium is fully recyclable, making it an eco-friendly choice. Its malleability also simplifies the manufacturing process, allowing for easy shaping and forming into various complex designs. Overall, these benefits make aluminium a top choice for a wide range of projects.
Ensuring the quality of our aluminium parts starts with selecting high-grade raw materials from trusted suppliers. We then use precision machining tools and equipment to achieve tight tolerances and smooth finishes. Throughout the manufacturing process, we conduct regular inspections and testing at different stages to catch any potential issues early on. Techniques like X-ray inspection and ultrasonic testing help us detect internal flaws without causing damage. Our skilled inspectors also perform visual checks to ensure each part meets both functional and aesthetic standards. We have a robust feedback loop where any identified problems are addressed promptly to continuously improve our processes. This comprehensive approach guarantees that every part we produce meets the highest quality standards.
Maintaining aluminium parts is pretty straightforward but essential for keeping them in good condition. Regular cleaning with mild soap and water is usually sufficient to remove dirt and debris. Avoid using abrasive cleaners or materials that could scratch the surface. For added protection, especially in harsh environments, consider applying a clear coat or sealant specifically designed for aluminium. This helps prevent oxidation and corrosion. Periodically inspect your parts for any signs of wear or damage, such as cracks or pitting, and address any issues immediately to prevent further deterioration. When not in use, store your aluminium parts in a dry, cool place away from direct sunlight and moisture. Following these simple steps will help extend the lifespan of your aluminium parts.
Absolutely! One of the great things about aluminium is how easily it can be customized. Whether you need a unique shape, size, or finish, we can tailor our manufacturing processes to meet your specific requirements. Our team works closely with clients to understand their needs and provide expert advice on design and material selection. We use advanced CNC machining, casting, and forging technologies to create parts with precise dimensions and intricate details. We also offer a range of surface treatments, such as anodizing, powder coating, or plating, to enhance the appearance and durability of the parts. Customization goes beyond just physical attributes; we also consider functional aspects like weight optimization and heat dissipation. With our comprehensive capabilities, we can deliver aluminium parts that perfectly fit your application.
Working with aluminium parts does come with its own set of challenges. One common issue is its softness compared to other metals, which makes it more prone to scratches and dents during handling and processing. To mitigate this, we take extra care in our workshop and use jigs and fixtures to protect the parts. Another challenge is its tendency to expand and contract more than other materials due to temperature changes, which can affect dimensional stability. We account for this by designing parts with appropriate tolerances and using thermal management strategies. Aluminium also has a natural oxide layer that can interfere with welding and bonding processes. To overcome this, we often remove the oxide layer before joining operations and use specialized techniques and materials. Despite these challenges, we have developed effective solutions to ensure the highest quality and performance of our aluminium parts.
The cost of aluminium parts can vary depending on several factors, including the complexity of the design, the volume of production, and the specific alloy used. Generally speaking, aluminium tends to be more expensive than some other common metals like steel due to its lower density and superior properties. However, when you factor in its lightweight nature and excellent strength-to-weight ratio, it often provides better value in terms of overall performance and efficiency. For example, in the automotive industry, using aluminium can lead to significant fuel savings over the vehicle's lifetime, which offsets the initial higher cost. Additionally, aluminium's recyclability can reduce long-term costs, as scrap aluminium holds its value well. We always strive to optimize our processes to offer competitive pricing while maintaining the highest standards of quality and service.