Construction Plastic Metal Parts
Plastic metal parts are super important in construction. They help make lots of different things we need. These parts are made using special molds and machines that melt plastic and shape it under high pressure.
Here's what makes these molds special:
- Strong Materials: They're usually made of really good steel or aluminum, so they last a long time.
- Super Precise: They make parts that fit perfectly for the construction industry.
- Can Make Many Parts: From tiny connectors to big pipes and valves, they can do it all.
How they make these parts:
- Design First: Using computer software, they design the part and then the mold.
- Machining: The mold is made with special machines called CNC.
Why they're great:
- Fast Production: Can make thousands of parts an hour, which is perfect for construction needs.
- High Quality: Parts are very accurate and safe.
- Efficient: Saves time and money compared to old methods.
But there are some challenges:
- Cost: Making the mold can be expensive and take a long time.
- Environment: Plastic waste can be bad for the environment.
Looking ahead: Even with these problems, plastic metal parts are still crucial. New designs and better recycling could make them even better. Future tech like 3D printing might make them even more precise and eco-friendly.
In short, plastic metal parts are key in construction. As things change, they'll keep helping manufacturers stay ahead.
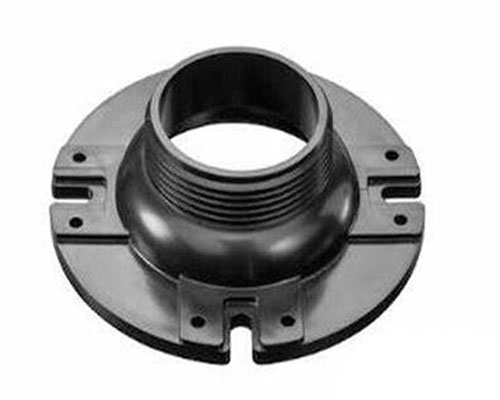
Construction Parts
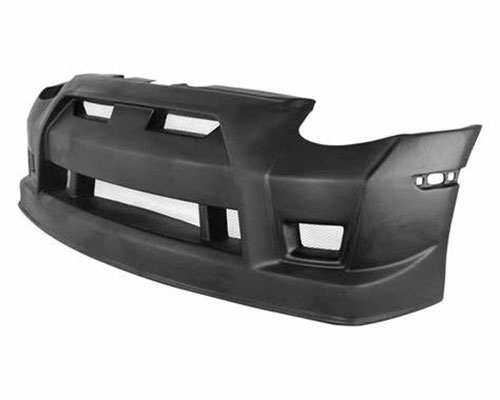
Construction Parts
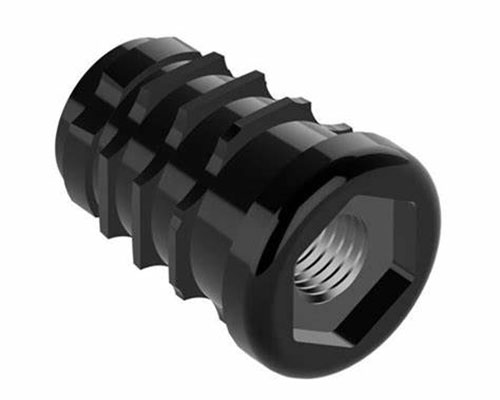
Construction Products
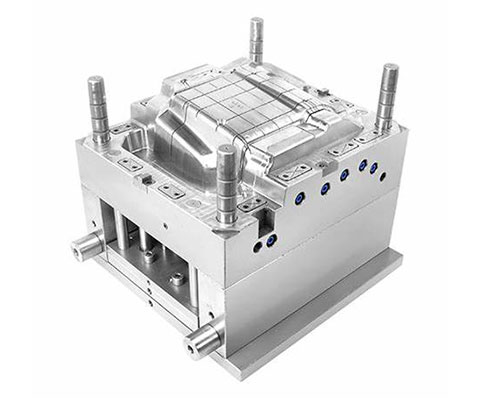
Construction Parts Mould
Construction Plastic Metal Parts Making Service
Be good at product structure optimization and greatly reduce the cost of Plastic Metal Parts custom solutions
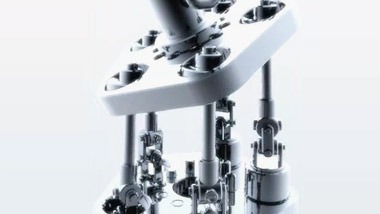
Part Design
Appearance and structural design
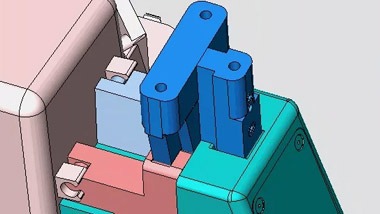
Mold Making
Design, DFM confirmation
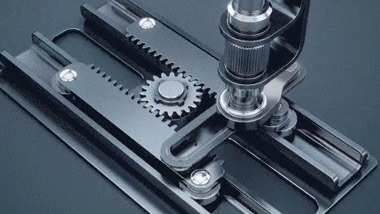
Product Production
Imported, high-speed equipment

Product Assembly
Incoming materials, inspection and assembly
Plastic Metal Parts are used in the Construction industry
The construction industry really leans on plastic metal parts for a lot of stuff, like insulation and roofing. These days, injection molding is super important because it quickly makes lots of high-quality parts.
Here's why injection molding rocks in construction:
- Big Batch Production: It lets us make tons of parts fast, which is awesome when you need a lot for big projects.
- Fancy Precision: With machines doing the work, every part is exactly the same, meeting all the strict rules for safety and performance.
- All Shapes and Sizes: Whether you need tiny connectors or huge pipes, injection molding can handle it.
Now, about those molds:
- Strong Materials: They're usually made from tough steel or aluminum to deal with the heat and pressure during molding.
- Custom Made: You can tweak the molds to get just the right part for any job on a construction site.
But there are some tricky parts too:
- Material Mix-Up: Different building materials need special ways of molding, so you need to know your stuff.
Overall, injection molding has totally changed how we do construction by making top-notch parts easier and cheaper to get. It's made everything more efficient and saved money. As the construction world keeps growing, injection molds will keep being key for staying ahead in this ever-changing market.
FAQ About Construction Plastic Metal Parts
What types of plastic and metal parts are commonly used in construction?
In construction, we often use a variety of plastic and metal parts. Plastics like PVC, polycarbonate, and nylon are popular for their durability and resistance to weather. Metals such as steel, aluminum, and stainless steel are favored for their strength and longevity. Each material has its unique benefits, making them suitable for different applications in construction projects.
How do you ensure the quality of plastic and metal parts in construction?
Ensuring quality involves several steps. First, we conduct rigorous testing on all materials before they are used. This includes checking for strength, durability, and resistance to environmental factors. We also work closely with suppliers who adhere to strict quality standards. Additionally, regular inspections during the manufacturing process help catch any defects early on. By following these practices, we can maintain high-quality parts for construction projects.
What are the advantages of using plastic parts over metal ones in construction?
Plastic parts have several advantages. They are generally lighter, which makes handling and installation easier. Plastics are also resistant to corrosion, which is great for outdoor use. Moreover, they can be molded into complex shapes, offering more design flexibility. These benefits make plastic parts a cost-effective and versatile choice for many construction applications.
Are there any downsides to using plastic parts in construction?
While plastic parts have many benefits, they also have some drawbacks. For instance, they may not be as strong as metal parts, especially under high stress or extreme temperatures. Plastics can also degrade over time when exposed to UV light or certain chemicals. Therefore, it's important to choose the right type of plastic for each specific application to avoid these issues.
How can I determine if plastic or metal parts are better for my construction project?
To decide between plastic and metal parts, consider the specific needs of your project. Think about factors like load requirements, exposure to the elements, and budget constraints. For example, if you need something lightweight and resistant to rust, plastic might be the way to go. If you require high strength and durability, metal could be the better option. Consulting with an engineer can also help you make an informed decision.
What maintenance do plastic and metal parts require?
Maintenance varies depending on the material. Plastic parts generally require less upkeep; occasional cleaning and inspection for wear are usually sufficient. Metal parts, on the other hand, may need more attention. They should be regularly checked for rust and corrosion, and protective coatings might be necessary. Proper maintenance ensures both types of parts last longer and perform better.
Can plastic and metal parts be recycled or reused in construction?
Yes, many plastic and metal parts can be recycled or reused. Recycling helps reduce waste and conserve resources. Some companies specialize in collecting and processing these materials for reuse in new products. Before disposing of any part, check if it can be recycled or repurposed. This not only benefits the environment but can also save money in the long run.
How do temperature changes affect plastic and metal parts in construction?
Temperature changes can impact both plastic and metal parts differently. Plastics can become brittle in cold weather and may expand or contract with temperature fluctuations. Metals, while more stable, can also expand and contract, potentially causing issues with fit and function. It's important to choose materials that can withstand the typical temperature range of your project's location to minimize these effects.
Are there any safety concerns when using plastic and metal parts in construction?
Safety is always a priority in construction. While both plastic and metal parts are generally safe, there are some considerations. For example, certain plastics can release harmful fumes when heated. Metals, if not properly treated, can rust or corrode, posing risks. Always follow safety guidelines and use appropriate personal protective equipment when handling these materials. Proper installation and regular inspections further ensure safety.
Where can I find reliable suppliers for construction plastic and metal parts?
Finding reliable suppliers is crucial for getting quality materials. Start by looking for suppliers with good reputations and positive reviews. You can also ask for recommendations from industry contacts or visit trade shows to meet potential suppliers in person. Make sure to check their certifications and ask about their quality control processes. Building a good relationship with a trustworthy supplier can make a big difference in the success of your projects.