Gear Plastic Metal Parts
Ever wondered about those super-durable plastic metal parts we use all the time? They're made with special tools called gear injection molds. These molds are crafted from top-notch steel or aluminum alloys, built to handle the intense heat and pressure of the injection molding process.
These molds can create all sorts of gears—like spur gears, helical gears, bevel gears, and worm gears. They're incredibly precise, so manufacturers can get gears in just the right size and shape they need.
Not only are these molds precise, but they're also built to last. With proper care, they can churn out millions of high-quality gears over their lifetime, making them essential in manufacturing.
So, what makes a great gear injection mold? First, it starts with the design. Then, the materials used matter a lot. Lastly, the precision and accuracy during the injection molding process are crucial. To keep them working perfectly, skilled technicians need to regularly check and maintain these molds.
In short, gear injection molds are vital for making high-quality, durable plastic metal parts. Their precision and longevity make them perfect for creating complex components that need to be just right every time.
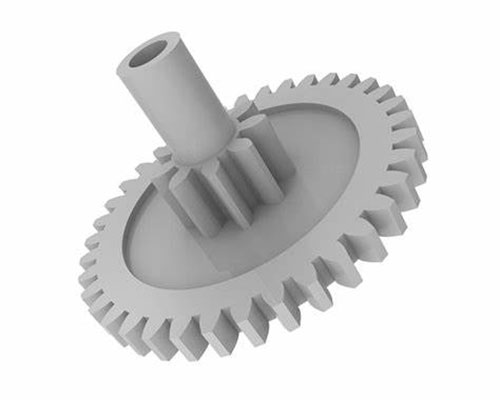
Gear Parts
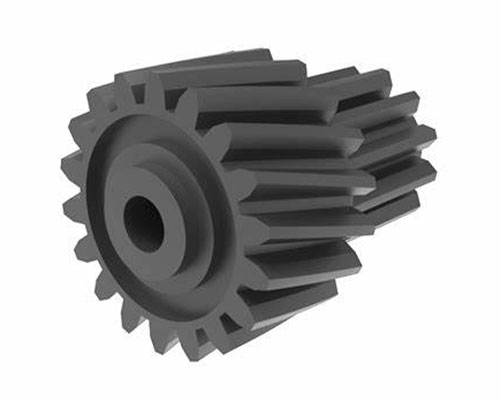
Gear Parts
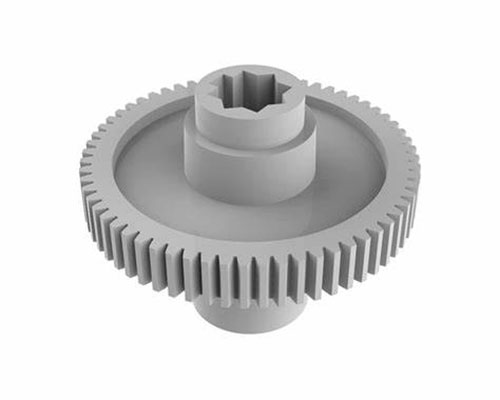
Gear Products
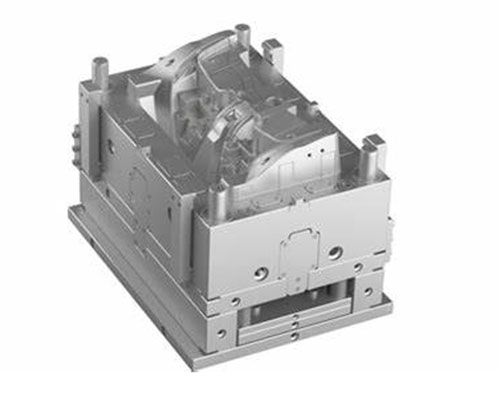
Gear Parts Mould
Gear Plastic Metal Parts Making Service
Be good at product structure optimization and greatly reduce the cost of Plastic Metal Parts custom solutions
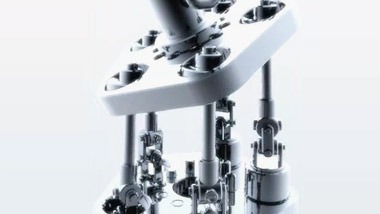
Part Design
Appearance and structural design
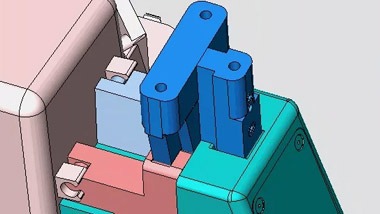
Mold Making
Design, DFM confirmation
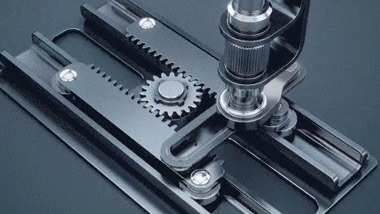
Product Production
Imported, high-speed equipment

Product Assembly
Incoming materials, inspection and assembly
Plastic Metal Parts are used in the Gear industry
The plastic metal parts industry is a key player in manufacturing, with applications ranging from small consumer electronics to large industrial machinery. These parts are essential for various mechanical uses, and their production demands precision and accuracy. One way to achieve this is through injection molding technology.
Injection molding involves injecting molten material, like plastic or metal, into a mold cavity. Once the material cools and solidifies, it forms a solid object that can be removed from the mold. This process allows for creating complex shapes and designs with high accuracy and consistency.
In the plastic metal parts industry, injection molding is used to make different types of gears, such as spur gears, helical gears, bevel gears, and worm gears. These gears are vital in various mechanical applications, from consumer electronics to automotive transmission systems.
One major benefit of using injection molding in this industry is its ability to produce high-quality gears with consistent size and shape. This consistency is crucial for ensuring compatibility between gears and existing mechanical systems, as well as providing reliable performance levels.
Another advantage is the capability to create gears with intricate shapes and designs. This is particularly important for the plastic metal parts industry because precise engineering is needed to ensure optimal performance.
To make high-quality injection molds, manufacturers use advanced software and design tools to create detailed 3D models of the molds. Then, these models are used to create mold cavities using advanced CNC machining technology, ensuring the mold's accuracy.
Once the molds are ready, they are typically used in high-speed injection molding processes to quickly and efficiently produce large quantities of gears. This process involves heating plastic or metal materials to their melting point and then injecting them into the mold cavity under high pressure. After cooling and solidifying, the finished gear is removed from the mold.
Overall, injection molding is a vital technology for the plastic metal parts industry. It enables manufacturers to produce high-quality gears with consistent size and shape. By employing advanced manufacturing techniques and processes, manufacturers can ensure their gears meet the highest performance and durability standards.
FAQ About Gear Plastic Metal Parts
What are gear plastic metal parts used for?
Gear plastic metal parts are commonly used in various industries for their versatility and durability. They are ideal for applications requiring lightweight yet strong components, such as automotive transmissions, machinery gears, and electronic devices. These parts offer excellent wear resistance and can handle high loads while reducing noise and vibration. By combining the properties of both plastic and metal, these gears provide a cost-effective solution that enhances performance and longevity.
How do gear plastic metal parts compare to traditional metal gears?
Gear plastic metal parts have several advantages over traditional metal gears. For starters, they are much lighter, which is crucial in industries where weight reduction leads to better fuel efficiency and performance. Additionally, plastic gears tend to be quieter and cause less wear on mating metal parts, extending the lifespan of the entire system. However, they might not be suitable for extremely high-temperature environments or heavy-duty industrial applications where metal's strength is paramount. Overall, the choice between plastic and metal gears depends on the specific requirements of the application.
Are gear plastic metal parts more cost-effective than all-metal gears?
Yes, gear plastic metal parts can often be more cost-effective compared to all-metal gears. The manufacturing process for plastic parts is generally less expensive due to lower material costs and simpler production methods like injection molding. This makes them an attractive option for large-scale production runs. Furthermore, the reduced weight of plastic components can lead to significant savings in transportation and handling costs. Despite being cheaper, these parts don't necessarily compromise on quality, making them a smart economical choice for many applications.
Can gear plastic metal parts withstand extreme temperatures?
While gear plastic metal parts are quite durable, their ability to withstand extreme temperatures varies depending on the specific type of plastic used. Some high-performance plastics can endure temperatures ranging from -50°C to 150°C without significant degradation. However, they might not match the thermal stability of certain metals under very high heat. For applications involving extreme temperatures, it's essential to select the right type of plastic and possibly incorporate heat-resistant additives. Generally, these parts perform admirably within their specified temperature ranges but should be chosen carefully for high-temperature environments.
Do gear plastic metal parts require special maintenance?
Maintenance for gear plastic metal parts is relatively straightforward but does require some attention to ensure longevity. Regular cleaning to remove dirt and debris is important, as these can cause abrasion and wear over time. Lubrication might also be necessary, especially in high-load or high-speed applications, to reduce friction and wear. It's advisable to check for any signs of wear periodically and replace parts as needed to prevent unexpected failures. Proper maintenance can significantly extend the life of these gears and keep them operating smoothly.
Are gear plastic metal parts recyclable?
Absolutely, gear plastic metal parts are recyclable, provided they are made from recyclable materials. Plastics used in these parts can often be reprocessed through mechanical recycling, where they are shredded, melted, and reformed into new products. Metal components can also be recycled using standard metallurgical processes. Recycling these parts not only helps in reducing waste but also conserves raw materials and energy. It’s always a good idea to check the recycling guidelines specific to the type of plastic and metal used in your gears to ensure proper disposal and recycling.
How do you choose the right material for gear plastic metal parts?
Choosing the right material for gear plastic metal parts involves considering several factors, including load capacity, operating environment, and cost. Common materials include nylon, polycarbonate, and acetal, each offering unique properties. Nylon is known for its toughness and flexibility, making it suitable for applications with shock absorption needs. Polycarbonate provides high impact resistance and clarity, ideal for visible components. Acetal offers low friction and high strength, perfect for precision gears. Assessing the specific requirements of your application will help you select the most appropriate material.
Can gear plastic metal parts be custom-made?
Yes, gear plastic metal parts can definitely be custom-made to fit specific requirements. Many manufacturers specialize in creating bespoke components tailored to exact specifications, whether it’s a unique size, shape, or material composition. Customization allows for optimal performance and integration into existing systems. Working closely with a manufacturer can help ensure that the gears meet all necessary standards and perform as intended. This flexibility makes plastic metal gears a versatile option for specialized applications.
Are there any common issues with gear plastic metal parts?
While gear plastic metal parts are generally reliable, they can face some common issues. One potential problem is deformation under high loads or at elevated temperatures, which can affect performance. Wear and tear over time can also be a concern, particularly if the gears are not properly maintained. Another issue is the potential for brittleness in some plastic types when exposed to cold temperatures. To mitigate these issues, it’s important to select the right material for the job and ensure proper design and maintenance practices are followed.
What are the environmental benefits of gear plastic metal parts?
Gear plastic metal parts offer several environmental benefits. Firstly, they are often lighter, which can reduce the overall energy consumption of vehicles and machinery during operation. Secondly, many plastics used in these parts are recyclable, which helps in reducing waste and conserving resources. Additionally, producing plastic parts generally requires less energy compared to metal parts, further lowering the carbon footprint. By choosing eco-friendly materials and recycling options, manufacturers can significantly minimize the environmental impact of these components.