Machine Plastic Metal Parts
Machine Plastic metal parts are crucial in making all sorts of things we use daily. Imagine a tool that can quickly shape melted plastic into the exact part you need. That's what these molds do! They team up with special machines to heat up and press plastic, then pop it into a mold to harden into the desired shape.
These molds are usually made from strong stuff like steel or aluminum, which means they can make really detailed and tricky parts. Whether it's something small you use at home or a big part for a car, these molds can handle it all.
Creating these molds starts on a computer. Designers use software to draw up 3D pictures of the parts they want to make, and then figure out how to build a mold for them. Once the design is ready, skilled workers use fancy machines to carve out the mold just right.
One awesome thing about using these molds is how fast they work. The machines can churn out thousands of pieces every hour, perfect for making lots of stuff quickly.
They're also super flexible. Need a simple piece or something with lots of curves and angles? No problem! These molds can do it all, which is why they're used in so many different fields like cars, gadgets, and everyday items.
Of course, getting started with these molds isn't cheap. Making them takes time and money, but the payoff is huge. They let manufacturers make top-notch parts faster and cheaper than old-fashioned ways.
In a nutshell, plastic metal parts have transformed manufacturing. They've made production quicker, better, and more affordable. As factories grow and evolve, having these molds will keep helping makers stay ahead in today's fast-paced world.
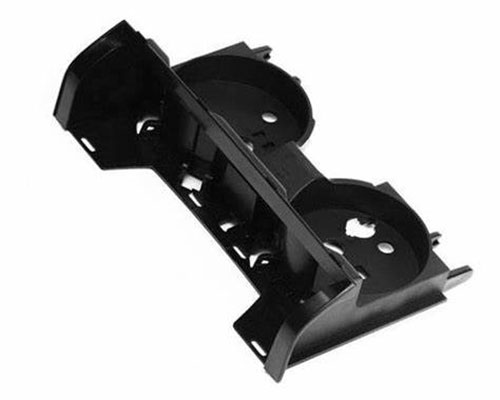
Machine Parts
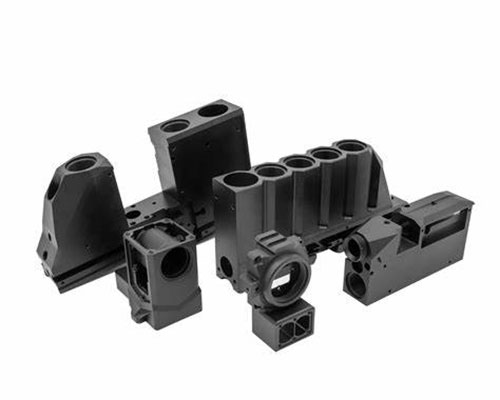
Machine Parts
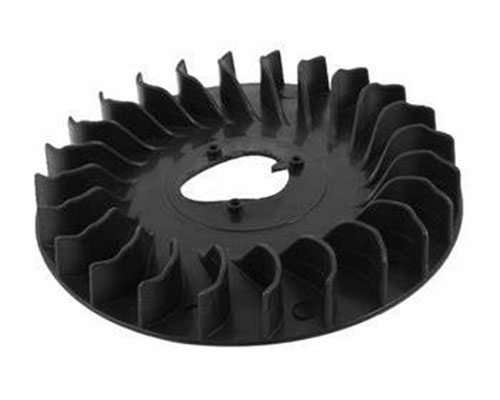
Machine Products
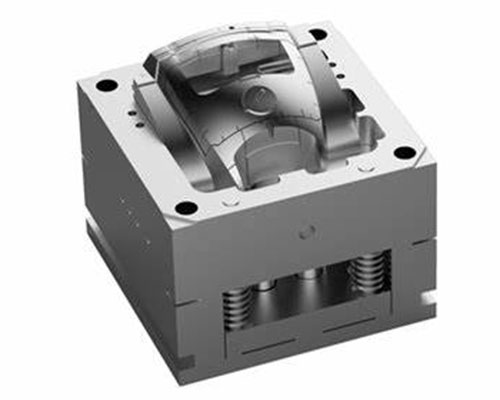
Machine Parts Mould
Machine Plastic Metal Parts Making Service
Be good at product structure optimization and greatly reduce the cost of Plastic Metal Parts custom solutions
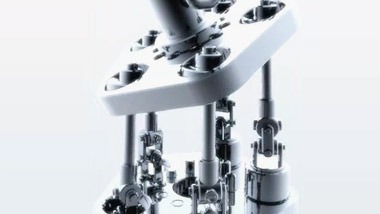
Part Design
Appearance and structural design
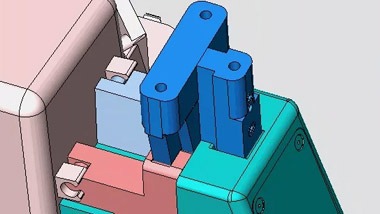
Mold Making
Design, DFM confirmation
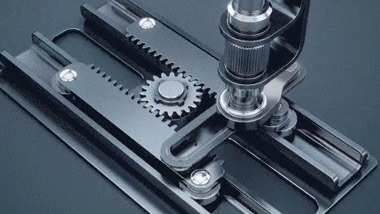
Product Production
Imported, high-speed equipment

Product Assembly
Incoming materials, inspection and assembly
Plastic Metal Parts are used in the Machine industry
The machine industry is a big part of modern manufacturing, making all sorts of components for different industries. In this field, plastic metal parts are super important because they help manufacturers make high-quality parts quickly, efficiently, and at a lower cost.
These plastic metal parts are used to create everything from small gears and valves to large mechanical parts. They are usually made from tough materials like steel or aluminum, ensuring that each part is precise and consistent.
Creating these parts starts with computer-aided design (CAD) software. This tool lets manufacturers design 3D models of the parts they need and then figure out how to make them. Once the design is ready, the parts are produced using advanced techniques like CNC machining.
One great thing about plastic metal parts is that they can be made really fast. Machines can produce thousands of parts every hour, which is perfect for industries that need lots of parts quickly. This speed helps keep up with the constant changes in the market as new products come out.
Another plus is their flexibility. Machines need parts in various shapes and sizes, and plastic metal parts can be customized to fit specific needs. This allows manufacturers to offer unique features that set their products apart from competitors.
Of course, making these parts does require a significant investment upfront. The cost of creating the initial setup can be high, and it takes some time to get everything ready. But the benefits, like faster production and lower costs compared to traditional methods, make it worth it.
Overall, plastic metal parts are essential in the machine industry. They help revolutionize the way machines are made, making them more accessible and affordable for consumers. As the machine industry keeps growing, these parts will continue to be crucial for staying competitive in this fast-paced market.
FAQ About Machine Plastic Metal Parts
What materials are commonly used in manufacturing machine plastic metal parts?
In making these parts, we often use a mix of materials to get the best of both worlds. Plastics like ABS or polycarbonate are popular for their lightweight and cost-effective nature. Metals such as aluminum or stainless steel add strength and durability. Sometimes, we even combine them to create hybrid parts that leverage the benefits of each material.
How do you ensure the quality of machine plastic metal parts during production?
Quality is our top priority. We start by using high-grade raw materials and precise molds. During production, we conduct regular inspections at various stages to catch any issues early. After manufacturing, each part undergoes rigorous testing, including stress tests and dimensional checks, to make sure they meet our strict standards.
Can machine plastic metal parts be customized for specific applications?
Absolutely! Customization is one of our strengths. Whether it's a unique size, shape, or material composition, we can tailor the parts to fit your exact needs. Our engineering team works closely with clients to understand their requirements and then designs and manufactures parts that perfectly match the specifications.
What are the advantages of using machine plastic metal parts over traditional materials?
These parts offer several benefits. They are usually lighter, which can reduce overall weight and improve efficiency. They are also resistant to corrosion and wear, which means they last longer. Plus, they can be produced more quickly and cost-effectively than some traditional materials.
Are machine plastic metal parts environmentally friendly?
Yes, they can be. We offer options made from recyclable or biodegradable plastics. Additionally, using metals like aluminum, which is highly recyclable, helps minimize environmental impact. We also strive to reduce waste and energy consumption in our manufacturing processes.
How durable are machine plastic metal parts?
Durability varies depending on the specific materials and design, but generally, these parts are quite robust. Plastics provide excellent resistance to impact and chemicals, while metals add structural strength. Together, they create parts that can withstand harsh conditions and heavy use.
What industries commonly use machine plastic metal parts?
These versatile parts are used across many industries. Automotive companies use them for lightweight components and improved fuel efficiency. In electronics, they help with heat dissipation and electromagnetic interference shielding. Even in medical devices, they are valued for their biocompatibility and strength.
How do you handle the shipping and logistics of machine plastic metal parts?
We take great care in packaging to ensure the parts arrive in perfect condition. Depending on the destination and urgency, we use various shipping methods, from standard ground transport to air freight. We also work with reliable logistics partners to track shipments and ensure timely delivery.
Can you provide samples of machine plastic metal parts before bulk production?
Yes, we can. Providing samples is a standard part of our process. This allows you to test the parts and make sure they meet your expectations before committing to a larger order. It’s a great way to ensure everything is perfect before full-scale production begins.
What kind of maintenance is required for machine plastic metal parts?
Maintenance is relatively minimal, thanks to the durable materials used. For plastic parts, occasional cleaning to remove dirt and debris is usually sufficient. Metal parts might need periodic rust prevention treatments, especially if exposed to moisture. Overall, these parts are designed to be low-maintenance and long-lasting.