Ship Plastic Metal Parts
In the shipbuilding industry, plastic metal parts are like those unknown but indispensable craftsmen, precisely shaping various parts of ships. Imagine that from the propulsion system to the steering system, to the various components inside and outside the hull, these plastic and metal parts can be manufactured one by one, and each one is precise and error free.
Since the introduction of injection molding technology into the shipbuilding industry, the entire production process has been injected with new vitality. With the help of computer-aided design (CAD) software and precision machining technology, manufacturers can now easily create complex and intricate components. This technology also supports large-scale production, ensuring that the high demand for ship components is met.
One of the main advantages of using ship injection molds is that they can produce high-precision and highly consistent components. This is crucial in the maritime industry as all components must comply with strict safety standards to ensure the safety of crew and passengers. Injection molding technology enables manufacturers to create components that meet these standards, thereby reducing the risk of failure and improving overall safety.
Another advantage is that ship injection molds can use a variety of materials to manufacture components. Manufacturers can choose various plastics based on the specific needs of each component, such as polyethylene, polypropylene, polycarbonate, etc. This flexibility allows manufacturers to select the most ideal materials for each component.
Using injection molds to produce ship components can also reduce the demand for manual labor, thereby lowering costs and improving efficiency. Molds can produce high-precision and consistent components, avoiding expensive and time-consuming manual inspections and adjustments.
Although ship injection molds have many advantages, there are also some limitations. The initial cost of creating a mold can be high, especially for more complex designs. However, once the mold production is completed, they can produce components at a lower unit cost. In addition, this process may generate a large amount of plastic waste, which must be properly handled to reduce its impact on the environment.
In short, ship injection molds are key tools in the manufacturing process of ship components. They enable manufacturers to produce high-quality, high-precision, and highly consistent components, which is crucial for the maritime industry. With the continuous advancement of injection molding technology, manufacturers will continue to rely on this process to produce innovative and high-quality ship components to meet future needs.
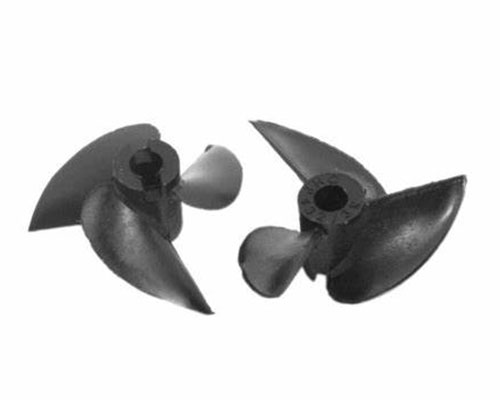
Ship Parts
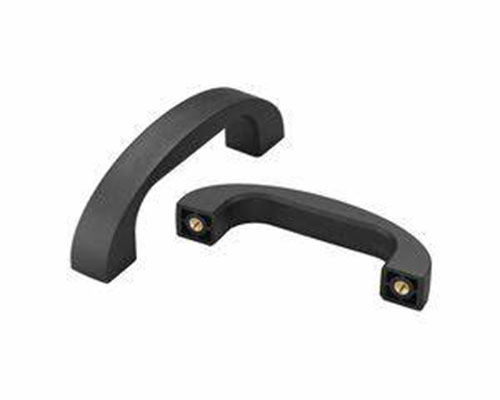
Ship Parts
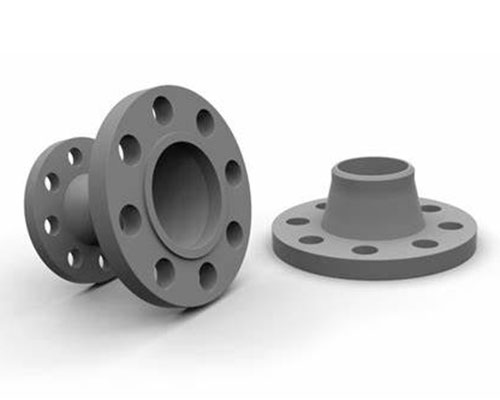
Ship Products
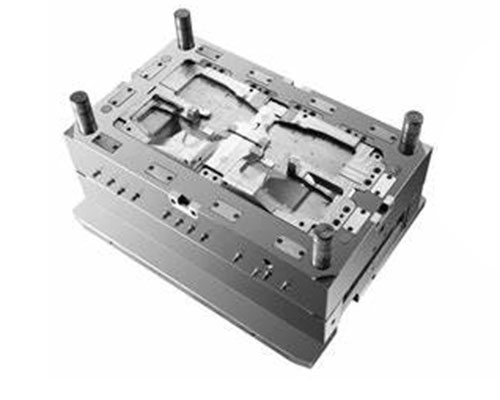
Ship Parts Mould
Ship Plastic Metal Parts Making Service
Be good at product structure optimization and greatly reduce the cost of Plastic Metal Parts custom solutions
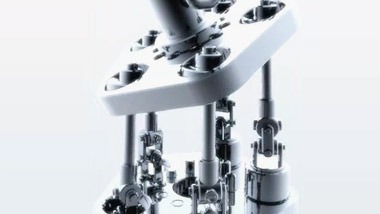
Part Design
Appearance and structural design
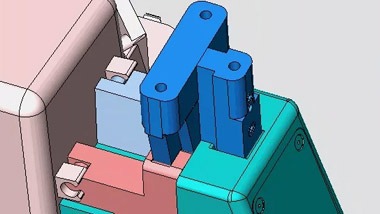
Mold Making
Design, DFM confirmation
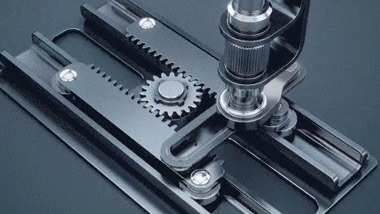
Product Production
Imported, high-speed equipment

Product Assembly
Incoming materials, inspection and assembly
Plastic Metal Parts are used in the Ship industry
In the shipbuilding biz, making top-notch, long-lasting parts is super important. These parts make sure everyone on board stays safe. Plastic metal parts play a big role in this because they help create complex pieces that are really strong and precise. Let's dive into how these parts are used.
First off, plastic metal parts are key for making system components like impellers, pumps, and other bits needed for moving the ship. This technology lets us make parts that can handle the tough marine conditions without breaking a sweat.
Steering systems also rely heavily on plastic metal parts. Things like rudder blades, steering columns, and control rods need to be spot-on perfect to keep ships navigating safely. Plastic metal parts ensure these crucial bits work just right every time.
Then there's the inside of the ship—think cabinets, seats, and furniture. These need to be tough, light, and resistant to saltwater and harsh sea environments. Plastic metal parts fit the bill perfectly, offering both design flexibility and cost savings.
Even the outside of the ship uses plastic metal parts, like hatches, ports, and other openings. These parts have to stand up to weather, waves, and rough conditions. Plastic metal parts deliver on all counts while giving designers more freedom and keeping costs down.
To sum it up, plastic metal parts are essential in shipbuilding. They help make high-quality, durable components that keep ships running smoothly and safely. As this tech keeps getting better, manufacturers will keep using it to make innovative, high-quality ship parts.
FAQ About Ship Plastic Metal Parts
What materials are commonly used in ship plastic metal parts?
Ship plastic metal parts are typically made from a combination of durable materials like stainless steel, aluminum, and various high-performance plastics such as polycarbonate or ABS. These materials are chosen for their strength, resistance to corrosion, and ability to withstand harsh marine environments. Stainless steel is often preferred for its excellent corrosion resistance, while aluminum is valued for its lightweight properties. High-performance plastics are used where weight reduction and chemical resistance are critical.
How do ship plastic metal parts contribute to the overall performance of a vessel?
Ship plastic metal parts play a crucial role in enhancing the performance and longevity of a vessel. They help reduce the overall weight of the ship, which can improve fuel efficiency and speed. Additionally, these parts offer superior resistance to rust and corrosion caused by saltwater exposure, ensuring that the vessel remains in optimal condition for longer periods. Their durability also means fewer repairs and maintenance, leading to cost savings over time.
Are there any eco-friendly options available for ship plastic metal parts?
Yes, there are several eco-friendly options available for ship plastic metal parts. Manufacturers are increasingly using recycled materials and sustainable production methods to create parts that have a lower environmental impact. For instance, some companies use recycled aluminum or bio-based plastics derived from renewable resources. These materials retain the necessary strength and durability while being more environmentally friendly. Additionally, advancements in coating technologies allow for longer-lasting protection without harmful chemicals.
What are the main challenges faced when manufacturing ship plastic metal parts?
Manufacturing ship plastic metal parts comes with several challenges. One major issue is ensuring the materials can withstand extreme weather conditions and constant exposure to saltwater. Corrosion resistance is a key concern, and achieving this without compromising on strength and durability requires advanced engineering solutions. Another challenge is maintaining quality control throughout the production process to ensure each part meets stringent safety standards. Finally, balancing cost-effectiveness with performance is always a consideration, as high-quality materials and advanced manufacturing techniques can be expensive.
How can I ensure the longevity of my ship's plastic metal parts?
To ensure the longevity of your ship's plastic metal parts, regular maintenance and inspections are essential. Make sure to clean the parts regularly to remove salt and other corrosive substances that can accumulate over time. Applying protective coatings or paints designed specifically for marine environments can also help prevent rust and corrosion. It's important to address any signs of damage promptly to prevent further deterioration. Additionally, storing spare parts properly when not in use can extend their lifespan significantly.
Can ship plastic metal parts be customized for specific vessels?
Absolutely! Many manufacturers offer customization options for ship plastic metal parts to meet the unique requirements of different vessels. Whether you need parts with specific dimensions, shapes, or performance characteristics, customization allows you to get exactly what you need. This flexibility is particularly useful for specialized ships or those operating in particularly harsh conditions. Customized parts can improve overall efficiency and performance, making them a worthwhile investment.
What role do ship plastic metal parts play in safety and compliance?
Ship plastic metal parts are integral to ensuring safety and compliance with maritime regulations. They must adhere to strict standards set by organizations like the International Maritime Organization (IMO) and the American Bureau of Shipping (ABS). These standards cover everything from material quality to design specifications, ensuring that parts can withstand the rigors of maritime operations. Compliance with these regulations is crucial not only for safety but also for avoiding legal issues and potential fines. Proper documentation and certification of the parts are also required during inspections.
How do advancements in technology affect the production of ship plastic metal parts?
Advancements in technology have greatly influenced the production of ship plastic metal parts. Modern manufacturing techniques such as 3D printing and CNC machining allow for more precise and efficient production processes. These technologies enable the creation of complex geometries that were previously difficult or impossible to achieve. Additionally, new materials with enhanced properties continue to emerge, offering better performance and longer lifespans. Automation and robotics also play a significant role in improving productivity and reducing human error during manufacturing.
What is the cost range for high-quality ship plastic metal parts?
The cost of high-quality ship plastic metal parts can vary widely depending on factors such as material type, complexity of design, and volume of production. Generally, stainless steel parts tend to be more expensive due to their superior corrosion resistance and durability. Aluminum parts are usually less costly but still offer good performance. High-performance plastics fall somewhere in between, depending on the specific type used. Customized parts will generally be more expensive than standard ones due to the additional engineering and manufacturing efforts involved. It's best to consult with suppliers directly to get accurate quotes based on your specific needs.
How can I find reliable suppliers for ship plastic metal parts?
Finding reliable suppliers for ship plastic metal parts involves doing thorough research and due diligence. Start by looking for suppliers with a proven track record in the maritime industry. Check their certifications and whether they comply with relevant safety and quality standards. Reading customer reviews and testimonials can provide valuable insights into their reliability and service quality. It's also a good idea to request samples or visit their facilities if possible to assess their capabilities firsthand. Building relationships with multiple suppliers can also help ensure a steady supply chain and better pricing options.