Smart Device Plastic Metal Parts
Imagine holding a brand new smartphone in your hand. Where did the smooth exterior, precise buttons, and almost invisible tiny connectors come from? The answer lies in those inconspicuous plastic metal parts. These parts are like the hands of a magician, capable of turning a pile of plastic and metal into an indispensable part of the smart devices we rely on in our daily lives.
Let me tell you a little story. Once, I visited a factory specializing in the production of smartphones, where the machines roared incessantly. What impressed me the most were the precision plastic metal parts. The workers told me that these parts are made of high-quality materials and every detail is carefully designed and calculated to ensure the accuracy and consistency of the final product.
You might be curious, how are these parts manufactured? In fact, they are supported by complex computer-aided design (CAD) software. Designers draw every detail of the part on the computer and then turn it into reality through precise mechanical equipment. This technology not only improves production efficiency but also greatly reduces costs, enabling smart devices to appear in our lives at a more affordable price.
Moreover, these parts are very flexible. Whether it's phone cases, buttons, or connectors, as long as the corresponding design drawings are provided, they can produce parts that meet the requirements. This means that every smartphone manufacturer can customize unique parts based on their design philosophy to make their products stand out in the market.
Overall, plastic metal parts are a miracle in modern manufacturing. Without them, our smartphones, smartwatches, and other smart devices would not be so popular and convenient. With the continuous advancement of technology, the demand for these high-precision parts will only increase. Next time you hold a smart device, think about the unsung heroes behind it – plastic metal parts, which are the cornerstone of all these wonderful experiences.
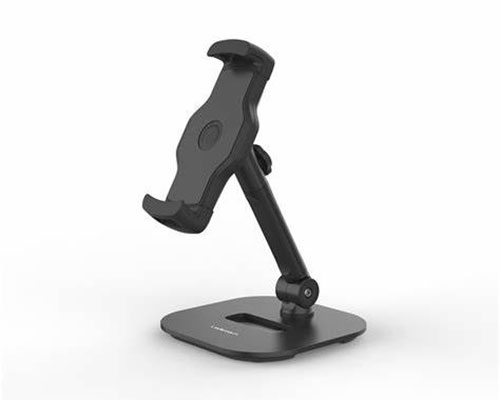
Smart Device Parts
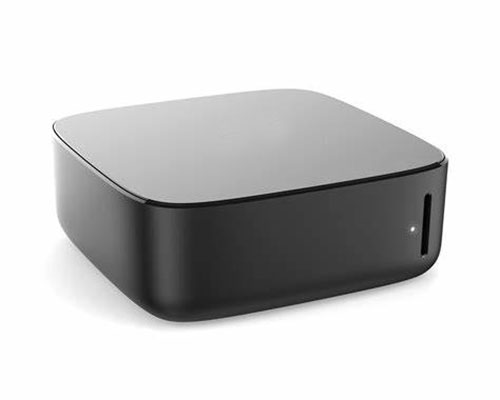
Smart Device Parts
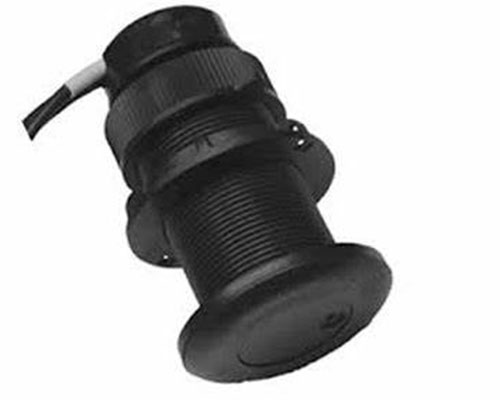
Smart Device Product
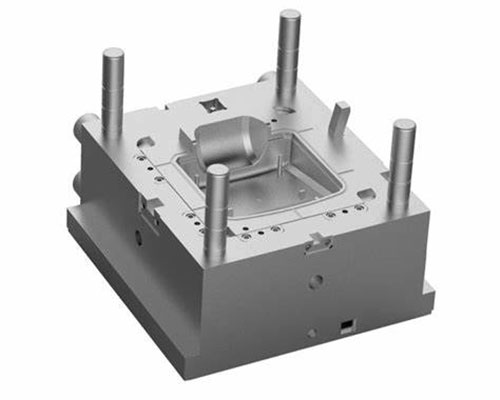
Smart Device Parts Mould
Smart Device Plastic Metal Parts Making Service
Be good at product structure optimization and greatly reduce the cost of Plastic Metal Parts custom solutions
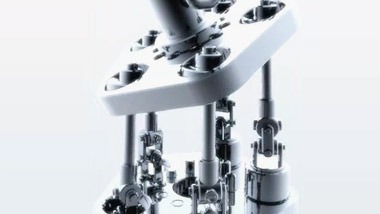
Part Design
Appearance and structural design
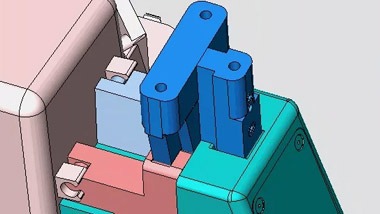
Mold Making
Design, DFM confirmation
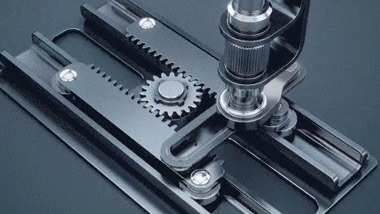
Product Production
Imported, high-speed equipment

Product Assembly
Incoming materials, inspection and assembly
Plastic Metal Parts are used in the Smart Device industry
In recent years, the smart device industry has really taken off, with gadgets like smartphones and smartwatches becoming everyday essentials. These devices are packed with tiny, precise parts, all made possible thanks to plastic metal parts.
Plastic metal parts are the backbone of smart devices, forming everything from shells to buttons and connectors. These parts are crafted using top-notch materials and cutting-edge techniques to ensure they're both accurate and consistent. This is super important because even a tiny mistake can mess up how these devices work.
The journey of making plastic metal parts starts with special design software. This software helps makers create 3D models of the parts they need and then design molds to make those parts. Once the design is ready, the mold is made using fancy machines and expert skills.
One big plus of plastic metal parts is that they can be made quickly and in large quantities. This is crucial in the fast-paced world of smart devices where new models pop up all the time. Plastic metal parts let manufacturers produce components faster than old-school methods, saving money and speeding up production.
Another great thing about plastic metal parts is their flexibility. Smart devices come in all shapes and sizes, each needing different parts. Plastic metal parts can be customized for each device, helping manufacturers stand out from the crowd.
Of course, getting started with plastic metal parts requires a fair bit of investment. Making a mold can be expensive and time-consuming. But the benefits far outweigh the costs. They allow manufacturers to make high-quality parts faster and cheaper than ever before.
In short, plastic metal parts are a game-changer for the smart device industry. They've revolutionized how these gadgets are made, making them more affordable and accessible. As the smart device industry keeps growing, plastic metal parts will remain a vital tool for manufacturers looking to stay ahead in this ever-evolving market.
FAQ About Smart Device Plastic Metal Parts
What are the most common materials used for smart device plastic and metal parts?
Smart devices often use a variety of materials, with plastics and metals being the most popular. Plastics like ABS (Acrylonitrile Butadiene Styrene) and polycarbonate are frequently chosen for their durability and lightweight properties. Metals such as aluminum and stainless steel are preferred for their strength and sleek appearance. These materials offer a good balance of functionality and aesthetics, making them ideal for various components in smart devices.
How do I choose between plastic and metal parts for my smart device?
Choosing between plastic and metal depends on several factors. If weight is a concern, plastic might be the better option since it's generally lighter. However, if you need more durability and a premium feel, metal could be the way to go. Additionally, consider the cost; plastic is usually cheaper to manufacture compared to metal. Think about what features are most important for your device and make your choice accordingly.
Are there any environmental concerns with using plastic and metal in smart devices?
Yes, environmental concerns are significant when it comes to using plastic and metal in smart devices. Plastics can take hundreds of years to decompose, leading to long-term pollution issues. On the other hand, metals like aluminum can be recycled infinitely without losing quality, which makes them more eco-friendly. It’s essential to consider the lifecycle of these materials and opt for sustainable practices whenever possible.
Can plastic and metal parts be recycled?
Absolutely! Both plastic and metal parts can be recycled, but the processes differ. Plastics need to be sorted by type before recycling, which can be more complex. Metals, especially aluminum, can be recycled repeatedly without losing quality. Recycling these materials helps reduce waste and conserve natural resources, so it's great that they can be reused.
How do temperature changes affect plastic and metal parts in smart devices?
Temperature changes can impact both plastic and metal parts differently. Plastics can become brittle or warp under extreme temperatures, while metals can expand or contract slightly but usually maintain their integrity better. It's crucial to design smart devices with materials that can withstand typical environmental conditions to ensure longevity and performance.
What are the manufacturing costs associated with plastic and metal parts?
Manufacturing costs vary significantly between plastic and metal parts. Injection molding of plastic is generally less expensive and faster, making it a cost-effective option for large production runs. Metal parts, on the other hand, often require more complex processes like CNC machining or casting, which can drive up costs. Balancing budget and material properties is key when deciding which to use.
How do plastic and metal parts compare in terms of weight?
When it comes to weight, plastic parts have a clear advantage. They are generally much lighter than metal parts, which can be a significant factor in portable smart devices. This lighter weight can enhance user experience by making the device easier to handle. However, if strength and durability are top priorities, metal might be worth the extra heft.
Do plastic or metal parts provide better thermal management for smart devices?
Metal parts typically offer better thermal management due to their higher thermal conductivity. This means they can dissipate heat more effectively, which is crucial for maintaining optimal performance of electronic components. Plastic, while not as efficient in heat dissipation, still has its place in areas where thermal management is less critical.
Are there any new advancements in the materials used for smart device parts?
Yes, there are always advancements in materials science. For instance, composite materials that combine plastics with other substances like carbon fibers are becoming more popular. These materials offer improved strength and reduced weight compared to traditional plastics. Additionally, there are biodegradable plastics that address some of the environmental concerns associated with conventional plastics. Keeping an eye on these innovations can lead to better design choices.
How do the finishing processes differ for plastic and metal parts?
The finishing processes for plastic and metal parts vary quite a bit. Plastic parts often undergo painting, coating, or plating to achieve the desired look and feel. Metal parts can be polished, anodized, or coated as well, but the techniques are different due to the nature of the material. Each finishing process has its own set of advantages and challenges, so it’s important to choose the right one based on the final product’s requirements.