CNC Turning Service
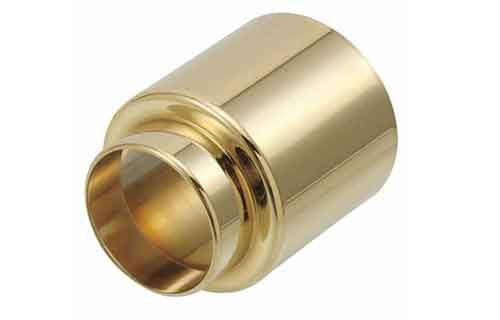
Custom Precision Part CNC Turning Service
Imagine you have a project on hand that requires precision CNC turning of parts, and time is tight with a limited budget. At this moment, Mold7 is like your personal assistant, always on standby. We have a vast network of over 11000 stores, including experts equipped with CNC lathes and turning centers. This means that no matter how specific your needs are, we can quickly match the most suitable resources.
When it comes to price and delivery time, we are equally confident. With a wide supplier network and efficient operational model, Mold7 is able to provide the most competitive conditions in the market. From rapid prototyping to mass production, we are able to respond flexibly and ensure high-quality output.
Do you want to give it a try? Just tell us your needs, and leave the rest to Mold7. Let's work together to turn your creativity into reality, efficiently and hassle free!
What is CNC Turning Service?
The Basics Of CNC Lathes
A CNC lathe machine, also called live tooling lathes, is ideal for cutting any symmetrical cylindrical or spherical parts. Characteristically, a lathe spins a workpiece on a vertical or horizontal axis, while a fixed shaping instrument moves around it on a more or less linear path. The act of cutting a workpiece on a CNC lathe is called turning.
How CNC Turning Works
CNC lathes use a subtractive method to create the desired shape. With the G-Code created, a blank bar of stock material is loaded into the chuck of the lathe's spindle. The chuck holds the workpiece in place while the spindle spins. When the spindle is up to speed, a stationary cutting tool is brought into contact with the workpiece to remove material until the desired geometry is achieved.
There are many operations that can be performed on a live tooling lathe, including facing, threading, knurling, drilling, boring, reaming, and taper turning. Different operations require tool changes and can increase cost and set-up time.
When all machining operations are completed, the part is cut from the stock for further post-processing. The CNC lathe is then ready to repeat the operation with little-to-no set-up time in between.
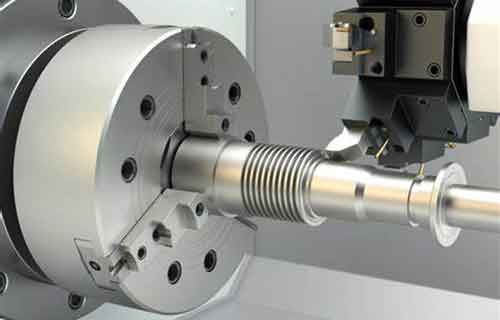
CNC Turning Materials
CNC Turning Aluminum
Aluminum 5052,
Aluminum 7075,
Aluminum 7075-T6,
Aluminum 6063-T5,
Aluminum 7050-T7451,
Aluminum MIC-6,
Aluminum 6061-T6,
Aluminum 2024-T3
CNC Turning Brass/Bronze
Brass C360,
Brass 260,
C932 M07 Bearing Bronze
CNC Turning Copper
EPT Copper C110,
Copper 101
CNC Turning Plastics
ABS,
Acetal [Delrin],
Acrylic,
G-10 Garolite,
Nylon 6/6,
PEEK,
Polycarbonate,
PTFE [Teflon],
Polypropylene,
Ultra-High Molecular Weight, Polyethylene
CNC Turning Steel
Alloy Steel 4130,
Alloy Steel 4140,
ASTM A36,
Stainless Steel 15-5,
Stainless Steel 17-4,
Stainless Steel 18-8,
Stainless Steel 303,
Stainless Steel 304,
Stainless Steel 316/316L,
Stainless Steel 416,
Stainless Steel 420,
Steel 1018,
Steel A36
CNC Turning Titanium
Titanium Grade 2,
Titanium 6Al-4V
CNC Turning Zinc
Zinc Sheet Alloy 500
CNC Turning Tolearances
CNC Turning Distance Dimensions
For features of size (Length, width, height, diameter) and location (position, concentricity, symmetry) +/- 0.005”.
CNC Turning Orientation and Form Dimensions
0-12" +/- 0.005", Angularity 1/2 degree. For 24" and beyond please consult our Manufacturing Standards.
CNC Turning Edge Condition
Sharp edges will be broken and deburred by default. Critical edges that must be left sharp should be noted and specified on a print.
CNC Turning Surface Finishes
CNC Turning As-Milled
The finish option with the quickest turnaround. Parts are left with visible tool marks and potentially sharp edges and burrs, which can be removed upon request. Surface finish is comparable to 125 uin Ra finish.
CNC Turning Bead Blast
The part surface is left with a smooth, matte appearance.
CNC Turning Anodized (Type II Or Type III)
Type II creates a corrosion-resistant finish. Parts can be anodized in different colors—clear, black, red, and gold are most common—and is usually associated with aluminum.
Type III is thicker and creates a wear-resistant layer in addition to the corrosion resistance seen with Type II.
CNC Turning Powder Coat
This is a process where powdered paint is sprayed onto a part which is then baked in an oven. This creates a strong, wear- and corrosion-resistant layer that is more durable than standard painting methods. A wide variety of colors are available to create the desired aesthetic.
CNC Turning Custom Service
Don’t see the finish you need? Submit an RFQ and we’ll look into a finishing process for process for your custom lathe work.
Benefits Of CNC Turning Service
CNC lathes, like CNC milling machines, can easily achieve high repeatability settings, which makes them perform well in both rapid prototyping and mass production. Multi axis CNC turning centers and Swiss type lathes can complete multiple machining operations on one machine, which is undoubtedly an economical and efficient choice for complex geometric parts, avoiding the hassle of multiple machines or tool changes that traditional CNC milling machines may require.
CNC turning service is a process of producing precise and complex parts from metal or plastic materials using computer-controlled machines. CNC turning services have many advantages, such as:
-It can create high-precision and high-quality parts, reducing the need for manual adjustment or correction.
-It can handle large-scale production, saving time and money.
-It is suitable for different types of materials, shapes, and sizes, providing more flexibility and versatility.
-It can utilize advanced software and tools to design and optimize parts, improve performance and functionality.
In our company, we have the experience and expertise to provide the best CNC turning services. We have a skilled and well-trained technical team that can operate the latest CNC machines and software. Our quality control system ensures that every part meets your specifications and standards. Our customer service listens to your needs and provides customized solutions for you. Contact us immediately and let us show you the benefits of CNC turning services.
Imagine if you need to mass produce a complex metal part, a traditional lathe may require multiple steps and multiple setups to complete. However, with our CNC turning services, all of this can be done on one machine, greatly saving time and costs. And, thanks to our high precision and quality standards, you can rest assured that the final product will fully meet your expectations.
So, why not give our CNC turning service a try? Whether you need rapid prototyping or mass production, we can provide solutions that meet your needs. Contact us and let's create excellent products together!
CNC Turning Frequently Asked Questions
What is the role of cutting speed in CNC turning?
Cutting speed affects the rate at which material is removed and can impact the quality and accuracy of the finished part.
The cutting speed is one of the most important parameters in CNC turning. It affects the quality, accuracy, and efficiency of the machining process. Cutting speed is the linear velocity of the cutting tool relative to the workpiece surface. It is usually measured in meters per minute (m/min) or feet per minute (ft/min).
As a CNC turning service provider with years of experience and expertise, we know how to choose the optimal cutting speed for different materials, tools, and geometries. We use advanced software and equipment to monitor and control the cutting speed during the machining process. We also adjust the cutting speed according to the feedback from the sensors, the tool wear, and the surface finish requirements.
By selecting the appropriate cutting speed, we can achieve high-quality CNC turning results with minimal waste and cost. We can also reduce the heat generation, tool wear, and vibration that may affect the machining performance and accuracy. Cutting speed is a key factor that determines our CNC turning service quality and efficiency.
What is the role of feed rate in CNC turning?
Feed rate refers to the speed at which the cutting tool moves through the material and can impact the quality and accuracy of the finished part.
The feed rate is one of the most important parameters in CNC turning, as it affects the quality, accuracy and efficiency of the machining process. The feed rate is the speed at which the cutting tool moves along the workpiece, measured in millimeters per revolution (mm/rev) or inches per revolution (ipr).
As a CNC turning service provider with years of experience and expertise, we know how to choose the optimal feed rate for different materials, shapes and sizes of workpieces. We use advanced software and equipment to calculate and control the feed rate, taking into account factors such as tool geometry, cutting depth, spindle speed, surface finish and chip formation.
By selecting the right feed rate, we can ensure that our CNC turning service delivers high-quality products that meet or exceed our customers' expectations. We can also reduce tool wear and tear, minimize waste and scrap, and improve productivity and profitability. We are always ready to share our knowledge and skills with our customers, and help them achieve their goals with our CNC turning service.
What is the role of spindle speed in CNC turning?
Spindle speed determines the rotational speed of the workpiece and can impact the quality and accuracy of the finished part.
In CNC turning, the spindle speed plays a crucial role in determining the cutting performance, surface finish, tool life, and overall machining efficiency. The spindle speed refers to the rotational speed of the lathe's spindle, which holds the workpiece and rotates it during the turning process. Here's how the spindle speed impacts CNC turning:
1. Cutting Speed: The spindle speed directly influences the cutting speed of the tool as it interacts with the workpiece. Cutting speed is the relative velocity between the cutting tool's edge and the workpiece surface. Proper selection of spindle speed ensures that the cutting speed is within an optimal range, allowing for efficient material removal and reducing the risk of tool wear.
2. Surface Finish: The spindle speed affects the surface finish of the machined part. Higher spindle speeds generally result in a smoother surface finish because the tool's cutting edges engage the workpiece at a faster rate, leading to reduced chip thickness and less surface roughness.
3. Tool Life: The choice of spindle speed has a significant impact on tool life. Running the tool at excessively high speeds can cause accelerated wear and reduce tool life. On the other hand, too low a spindle speed might cause the cutting edges to rub against the material rather than effectively cutting it, leading to premature tool failure.
4. Chip Control: Proper spindle speed selection helps in achieving better chip control during turning. A balanced chip formation and evacuation process reduce the chances of chip jamming, which can cause machining issues and damage the workpiece or tool.
5. Material Removal Rate: The spindle speed, in combination with the feed rate (the rate at which the cutting tool advances into the workpiece), determines the material removal rate. Optimal spindle speed selection ensures that the material is removed efficiently without causing excessive tool wear or compromising the surface finish.
6. Machining Efficiency: The right spindle speed helps achieve optimal machining efficiency. It ensures that the cutting process is neither too slow, wasting time, nor too fast, risking tool damage. A well-chosen spindle speed contributes to maximizing productivity while maintaining quality.
7. Tool Selection: Different cutting tools and materials require specific spindle speeds to perform optimally. Choosing the appropriate spindle speed based on the material and tool type is crucial for achieving the desired machining results.
CNC turning machines allow for easy adjustments to the spindle speed, either manually or through programmed commands, based on the specific requirements of each machining operation. Machinists and programmers must carefully consider the material properties, tooling, and desired outcomes to select the most appropriate spindle speed for each turning task. A proper understanding and utilization of spindle speed can lead to efficient, precise, and cost-effective CNC turning operations.
What is the role of coolant in CNC turning?
Coolant helps to lubricate and cool the cutting tool, which can improve the quality and accuracy of the finished part.
Coolant plays a vital role in CNC turning and other machining processes. It refers to a lubricating and cooling fluid used during the cutting operation. Coolant is typically applied to the cutting zone to improve machining performance, extend tool life, and enhance the overall efficiency of the CNC turning process. Here are the key roles of coolant in CNC turning:
1. Heat Dissipation: One of the primary functions of coolant is to dissipate the heat generated during the cutting process. As the cutting tool interacts with the workpiece, friction and cutting forces generate heat at the tool-workpiece interface. Excessive heat can lead to tool wear, premature tool failure, and potential damage to the workpiece. Coolant helps to regulate the temperature, keeping it within acceptable limits and preserving the cutting tool's integrity.
2. Lubrication: Coolant acts as a lubricant between the cutting tool and the workpiece. This reduces friction, minimizing the wear and tear on the cutting tool. Proper lubrication also improves chip flow, which aids in chip evacuation from the cutting zone, preventing chip jamming and improving machining efficiency.
3. Chip Removal: Coolant helps in efficiently evacuating chips away from the cutting zone. It carries the chips away from the cutting area and out of the machine, preventing chip recutting and minimizing the risk of damage to the workpiece or tool.
4. Surface Finish: The use of coolant can improve the surface finish of the machined part. By reducing friction and heat, coolant helps in achieving smoother and more precise surface finishes on the workpiece.
5. Tool Life Extension: Coolant plays a significant role in extending the life of cutting tools. By reducing heat and friction, coolant minimizes tool wear and chipping, leading to longer tool life and reduced tool replacement costs.
6. Machining Accuracy: The cooling effect of the coolant helps maintain the dimensional accuracy of the workpiece. By controlling the temperature, the expansion and contraction of the workpiece are minimized, resulting in more consistent and precise machining.
7. Material Compatibility: Some materials are prone to work hardening or generating excessive heat during machining. Coolant selection can be tailored to the material being machined, helping to optimize the machining process for specific materials.
8. Swarf Management: Coolant aids in managing the swarf or chips generated during the turning process. Efficient swarf management prevents interference with the cutting process and ensures a cleaner work environment.
9. Tool Performance: For certain advanced machining operations, such as high-speed machining, using coolant becomes essential. It helps to enhance the overall performance and productivity of the machining process.
The specific type of coolant used in CNC turning (e.g., oil-based, water-based, emulsions) can vary depending on the material being machined, the cutting process, and other considerations. Proper coolant application, maintenance, and disposal are crucial for achieving optimal results and ensuring a safe and efficient CNC turning operation.
What is the role of fixturing in CNC turning?
Fixturing refers to the process of holding the workpiece in place to ensure accuracy and consistency during the turning process.
In CNC turning, fixturing plays a critical role in securely holding the workpiece in place during the machining process. Fixturing refers to the design and implementation of specialized fixtures or workholding devices that attach the workpiece to the lathe or CNC turning machine. The primary purposes and roles of fixturing in CNC turning are as follows:
1. Workpiece Stability: Fixturing ensures that the workpiece remains stable and firmly held in position throughout the turning operation. This stability is crucial to prevent vibrations, shifting, or movement of the workpiece, which could lead to inaccurate machining and poor surface finishes.
2. Precision and Accuracy: Proper fixturing is essential for achieving precise and accurate machining results. It helps align the workpiece with respect to the machine's cutting tool and ensures that the desired cutting paths are followed with minimal deviation.
3. Safety: Fixturing enhances safety during CNC turning. A securely fixed workpiece reduces the risk of workpiece ejection, minimizing the chance of accidents and injuries to the machine operator.
4. Consistency and Reproducibility: By using consistent and well-designed fixtures, CNC turning processes can be standardized, allowing for the repeatable and reproducible production of identical parts with consistent quality.
5. Accessibility for Machining: Fixturing should provide appropriate access to the workpiece for the cutting tool. It should not obstruct the tool's movement and should allow for efficient chip evacuation.
6. Material Efficiency: Properly designed fixtures help in optimizing material usage. By securely holding the workpiece in the correct orientation, fixtures can reduce material wastage during the machining process.
7. Minimizing Set-up Time: Well-designed fixturing can reduce set-up time, making it quicker and easier to load and position the workpiece accurately in the CNC turning machine.
8. Flexibility: Depending on the requirements, fixtures can be designed to accommodate a wide range of workpiece sizes, shapes, and materials. This flexibility allows for the machining of various parts without the need for extensive retooling.
9. Enhanced Machining Capabilities: Advanced fixtures can be equipped with features such as rotary indexing, allowing for multi-axis machining and the creation of complex geometries that would be challenging with standard fixturing.
10. Increased Productivity: Efficient and reliable fixturing contributes to increased productivity by reducing downtime due to rejections, minimizing setup times, and optimizing machining processes.
Properly designed fixturing is crucial to achieving the full potential of CNC turning machines. It ensures that the workpiece is securely held and properly oriented, allowing the cutting tools to produce precise, consistent, and high-quality components. The choice of fixturing method and design considerations depend on the specific requirements of each machining operation, the complexity of the workpiece, and the capabilities of the CNC turning machine.
How can CNC turning manufacturers ensure the quality of their parts?
Manufacturers can use quality control measures such as testing and inspection to ensure that their parts meet the required specifications for dimensional accuracy and surface finish.
Ensuring the quality of parts produced through CNC turning is crucial for CNC turning manufacturers to maintain customer satisfaction, meet industry standards, and uphold their reputation. To achieve this, manufacturers can implement various quality control measures throughout the CNC turning process. Here are some key steps to ensure the quality of CNC turned parts:
1. Robust Design and Programming: Start with a well-designed part and develop accurate CNC programs. CAD/CAM software can be used to create detailed designs and generate precise tool paths for CNC turning machines.
2. Material Inspection: Verify the quality of the raw materials before machining. Check for material properties, dimensions, and any defects that could affect the final part's quality.
3. Machine Calibration and Maintenance: Regularly calibrate CNC turning machines and ensure proper maintenance to keep them in optimal working condition. Accurate machine tools are essential for producing high-quality parts.
4. Proper Fixturing: Use appropriate and well-designed fixtures to securely hold the workpiece during machining. Proper fixturing ensures accurate positioning and stability, minimizing errors during CNC turning.
5. Tool Selection and Maintenance: Choose high-quality cutting tools suitable for the specific material and machining requirements. Regularly inspect and maintain the tools to ensure they are sharp and in good condition.
6. In-Process Inspection: Implement in-process inspections to check the dimensions, tolerances, and surface finish of parts during the CNC turning process. Automated measuring systems or manual inspection can be used for this purpose.
7. Statistical Process Control (SPC): Implement SPC techniques to monitor and control the CNC turning process. SPC involves collecting and analyzing data at various stages of production to identify and address any variations or deviations from the desired quality.
8. Post-Machining Inspection: Perform thorough inspections on finished parts to validate their dimensional accuracy, surface finish, and other critical characteristics. Use precision measuring tools like calipers, micrometers, and coordinate measuring machines (CMM) for this purpose.
9. Non-Destructive Testing (NDT): In certain industries or for critical parts, non-destructive testing methods such as X-ray, ultrasonic testing, or dye penetrant testing can be employed to detect hidden defects without damaging the part.
10. Documented Quality Procedures: Have well-documented quality procedures and work instructions to ensure consistency and standardization in the CNC turning process. This documentation serves as a reference for operators and quality control personnel.
11. Continuous Improvement: Encourage a culture of continuous improvement within the organization. Regularly review and analyze quality data to identify areas for enhancement and implement corrective actions as needed.
12. Compliance with Standards: Ensure that the CNC turning process complies with relevant industry standards and customer requirements.
By implementing these quality control measures, CNC turning manufacturers can consistently produce high-quality parts, reduce rejections, and build a reputation for reliability and precision. Quality assurance is an ongoing process, and a proactive approach to quality management is essential for long-term success in CNC turning manufacturing.
What is the role of tooling in CNC turning?
Tooling includes cutting tools, tool holders, and other components that are used to shape the workpiece during the CNC turning process.
Tooling plays a crucial role in CNC turning as it directly affects the machining process and the quality of the final product. Tooling refers to the cutting tools and accessories used in the CNC turning machine to remove material from the workpiece and shape it into the desired form. The role of tooling in CNC turning can be summarized as follows:
1. Material Removal: The primary role of tooling in CNC turning is to remove material from the workpiece. The cutting tool comes into contact with the workpiece, and the material is cut away to create the desired shape and dimensions.
2. Precision Machining: CNC turning relies on precise and accurate cutting tools to achieve the desired tolerances and surface finish. High-quality tooling ensures that the machining process produces parts with the required dimensions and meets the specified tolerances.
3. Tool Life and Durability: The choice of appropriate tooling materials and coatings directly impacts tool life and durability. High-quality tooling with wear-resistant coatings can withstand the stresses of CNC turning, resulting in longer tool life and reduced tool replacement costs.
4. Surface Finish: Tooling affects the surface finish of the machined part. Properly selected and maintained cutting tools can result in a smooth and high-quality surface finish on the workpiece.
5. Chip Control: The design and geometry of the cutting tool influence chip control during CNC turning. Efficient chip control helps in maintaining a clean cutting zone and preventing chip-related machining issues.
6. Material Compatibility: Different materials require specific tooling to ensure effective material removal and avoid excessive tool wear. Tooling should be selected based on the material properties of the workpiece to achieve optimal machining results.
7. Tool Selection for Different Operations: CNC turning involves various cutting operations, such as roughing, finishing, threading, and grooving. Different tools are used for each operation, and proper tool selection ensures the most efficient and accurate machining process.
8. Feeds and Speeds: Tooling, in combination with CNC programming, determines the appropriate cutting feeds and spindle speeds for optimal material removal rates and machining efficiency.
9. Tool Changing and Automation: CNC turning often involves multiple tools for different machining steps. Efficient tool-changing mechanisms and automation ensure smooth transitions between tooling, reducing downtime and increasing productivity.
10. Safety: Properly installed and secured tooling is essential for the safety of the machine operator and the integrity of the CNC turning process. Incorrectly installed or damaged tooling can pose safety risks and affect machining quality.
In summary, tooling is a fundamental aspect of CNC turning that significantly impacts the machining process, accuracy, surface finish, and overall efficiency. The selection, maintenance, and management of cutting tools are essential for achieving consistent, high-quality, and cost-effective production in CNC turning operations.
What is the role of the turret in CNC turning?
The turret holds multiple cutting tools and can be rotated to select the appropriate tool for the job.
The turret in CNC turning plays a pivotal role in the machining process, specifically in CNC lathes with multiple tool capabilities. The turret is a tool-holding mechanism located on the CNC lathe's cross-slide or saddle, and it allows for the rapid and automated interchange of cutting tools during the turning operation. The main roles of the turret in CNC turning are as follows:
1. Tool Storage and Organization: The turret serves as a tool storage and organization system. It can hold multiple cutting tools simultaneously, allowing for quick access to a variety of tools during the machining process without the need for manual tool changes.
2. Automatic Tool Changing: With a turret in place, CNC turning machines can perform automatic tool changes during the machining process. This automation reduces downtime between tool changes, increases productivity, and minimizes operator intervention.
3. Multiple Tool Capabilities: The turret's ability to accommodate several tools enables the CNC lathe to perform various machining operations without manual intervention. Different tools can be used for roughing, finishing, threading, grooving, and other tasks, enabling greater versatility in CNC turning.
4. Quick and Repeatable Tool Indexing: The turret's indexing mechanism ensures precise and repeatable positioning of the tools. This accuracy allows for consistent machining results and the ability to return to specific tools for different machining steps.
5. Increased Efficiency: The turret's rapid tool-changing capabilities enhance the overall efficiency of CNC turning operations. It reduces idle time and enables continuous machining with minimal interruptions.
6. Flexibility: CNC turning with a turret offers flexibility in tool selection, allowing operators to choose the most suitable tools for specific machining tasks and materials.
7. Tool Monitoring and Management: Some modern CNC lathes equipped with turrets may have built-in tool monitoring systems. These systems can detect tool wear and breakage, alerting the operator to take corrective actions or initiate tool replacement as needed.
8. Reduced Setup Time: By having multiple tools readily available on the turret, setup time is significantly reduced. Operators can quickly switch between tools for different machining requirements without physically changing the tools.
9. Improved Machining Accuracy: The turret's ability to accurately index tools and maintain their positions contributes to the overall precision and dimensional accuracy of CNC turning operations.
In summary, the turret is a critical component in CNC turning, especially for lathes with multiple tool capabilities. It enables the automatic and efficient interchange of cutting tools, providing versatility, improved productivity, and increased accuracy in the machining process. The turret's role in tool management and quick tool changing is central to optimizing the performance of CNC turning machines.
How does CNC turning compare to other machining processes in terms of speed and efficiency?
CNC turning can be faster and more efficient than other machining processes because it allows for greater precision and accuracy.
CNC turning, as a machining process, has its strengths and weaknesses compared to other machining processes. The speed and efficiency of CNC turning are influenced by various factors, including the type of material being machined, the complexity of the part, the cutting tools used, and the specific CNC machine's capabilities. Let's compare CNC turning with other common machining processes in terms of speed and efficiency:
1. CNC Milling vs. CNC Turning:
- Speed: CNC milling and CNC turning can have comparable speed depending on the specific application. CNC milling is well-suited for machining complex 3D shapes and multiple surfaces simultaneously, while CNC turning excels at cylindrical and rotational parts.
- Efficiency: CNC milling may have an advantage in efficiency for certain intricate parts, as it can remove material from multiple angles in a single setup. However, CNC turning is generally more efficient for producing rotational parts with fewer setups and tool changes.
2. CNC Turning vs. Grinding:
- Speed: In general, CNC turning is faster than grinding for the same material removal volume. Turning machines can remove material more rapidly due to the nature of the cutting process.
- Efficiency: CNC turning is more efficient for producing parts with rotational symmetry, such as shafts, pins, and bushings. Grinding, on the other hand, is preferred for achieving tight tolerances and excellent surface finishes, especially in hardened materials.
3. CNC Turning vs. Wire EDM (Electrical Discharge Machining):
- Speed: In terms of speed, CNC turning is typically faster than Wire EDM for the removal of large amounts of material. However, Wire EDM can be faster for cutting intricate shapes in hard materials.
- Efficiency: CNC turning is more efficient for producing rotational parts, especially when the volume of material removal is significant. Wire EDM is highly efficient for intricate and delicate parts, particularly in hard materials where conventional cutting processes may be challenging.
4. CNC Turning vs. Waterjet Cutting:
- Speed: CNC turning is generally faster than waterjet cutting, particularly for moderate to high material removal rates. Waterjet cutting is more suitable for softer materials and intricate shapes but may have slower cutting speeds.
- Efficiency: CNC turning is more efficient for producing rotational parts and parts with higher material removal rates. Waterjet cutting is highly efficient for cutting softer materials, composite materials, and materials that may be sensitive to thermal damage.
In conclusion, the speed and efficiency of CNC turning depend on the specific application and the characteristics of the part being machined. CNC turning excels in producing rotational parts and parts with moderate material removal rates. For more complex shapes, tight tolerances, and intricate features, other machining processes like CNC milling, grinding, Wire EDM, or waterjet cutting may offer better efficiency and accuracy. Choosing the most suitable machining process involves considering factors such as the material, part geometry, volume of production, and desired surface finish.
What is the role of G-code in CNC turning?
G-code is a programming language that is used to control CNC machines, including CNC turning machines.
G-code plays a fundamental role in CNC turning, as well as in other CNC (Computer Numerical Control) machining processes. G-code, short for "Geometric Code" or "G-programming language," is a set of instructions used to control the movements and actions of CNC machines. In CNC turning, G-code specifically guides the cutting tool's movements and controls the entire machining process. Here's the role of G-code in CNC turning:
1. Toolpath Control: G-code instructs the CNC turning machine on the specific toolpath that the cutting tool should follow during the machining operation. It defines the coordinates, direction, and depth of the cuts required to shape the workpiece accurately.
2. Spindle Speed and Feed Rate: G-code sets the spindle speed and feed rate during CNC turning. It controls the rotational speed of the lathe's spindle and the rate at which the cutting tool advances into the workpiece. These parameters are crucial for determining the cutting speed and material removal rate.
3. Tool Selection: G-code commands specify which tool from the turret or tool magazine should be used for a particular operation. This allows the CNC turning machine to automatically select the appropriate cutting tool for each part of the machining process.
4. Tool Compensation: G-code can include tool compensation instructions, such as tool radius or length compensation. These commands help adjust the tool's position to compensate for the tool's geometry, ensuring precise machining and accurate part dimensions.
5. Machining Parameters: G-code includes parameters such as spindle direction, coolant on/off, tool change commands, dwell time (pausing at a specific location), and rapid traverse (fast movement between cutting points). These parameters control the machine's behavior throughout the turning process.
6. Reproducibility: G-code ensures the reproducibility of CNC turning operations. Once a program is written, it can be used repeatedly to manufacture identical parts with consistent accuracy.
7. Controlling Multiple Axes: CNC turning machines can have multiple axes of motion. G-code allows the coordination and control of these axes to perform complex turning operations, such as threading, grooving, and contouring.
8. Error Handling and Safety: G-code includes error handling and safety codes to deal with unexpected situations, emergency stops, and fault conditions during CNC turning.
9. CAM Software Integration: CAM (Computer-Aided Manufacturing) software generates G-code based on the part's CAD (Computer-Aided Design) model. The CAM software interprets the part's design, creates the toolpath, and generates the G-code to drive the CNC turning machine.
In summary, G-code serves as the language that communicates instructions to the CNC turning machine. It controls the movements, tool selections, and machining parameters necessary to shape the workpiece accurately and efficiently. CNC turning operators use G-code to program the machine, and CNC turning manufacturers rely on it to produce precise and consistent parts according to the desired specifications.
What are some common applications of CNC turning?
CNC turning can be used in a variety of industries, including aerospace, automotive, and medical device manufacturing.
CNC turning is a versatile machining process used across various industries due to its ability to produce a wide range of cylindrical and rotational parts. Some common applications of CNC turning include:
1. Aerospace Components: CNC turning is widely used in the aerospace industry to produce components such as engine shafts, turbine disks, landing gear parts, and hydraulic fittings.
2. Automotive Parts: CNC turning is employed in the automotive sector for manufacturing parts like axles, drive shafts, pistons, brake rotors, and various engine components.
3. Medical Devices: CNC turning is utilized to create medical device components, including surgical instruments, implantable devices, and prosthetics.
4. Electronics: CNC turning is employed to produce electronic components like connectors, terminals, and housings for electronic devices.
5. Hydraulic and Pneumatic Components: CNC turning is used to manufacture valves, fittings, cylinders, and other components used in hydraulic and pneumatic systems.
6. Fluid Handling Components: CNC turning is applied to produce various components used in fluid handling systems, such as pumps, valves, and nozzles.
7. Sporting Goods: CNC turning is utilized in the production of sporting goods like golf club shafts, bicycle components, and fishing reel parts.
8. Plumbing and HVAC Components: CNC turning is employed to manufacture plumbing fittings, couplings, and HVAC components.
9. Tooling and Fixtures: CNC turning is used to create tooling and fixtures required for various machining and manufacturing processes.
10. Defense and Military Applications: CNC turning is used in the defense and military industries to produce components for weapons, ammunition, vehicles, and communication systems.
11. Construction Equipment: CNC turning is employed in the manufacturing of parts for construction equipment such as bulldozers, excavators, and loaders.
12. Precision Machinery: CNC turning is used to produce parts for various precision machinery and equipment, including industrial robots and machine tools.
CNC turning's ability to produce accurate and repeatable cylindrical parts with high efficiency makes it an essential machining process for a wide range of applications. It is particularly well-suited for producing components with rotational symmetry and various complex features. CNC turning continues to play a critical role in modern manufacturing, enabling the production of high-quality parts used in diverse industries around the world.
What is the role of the collet in CNC turning?
The collet holds the cutting tool in place and can be used to change out tools during the turning process.
The collet plays a crucial role in CNC turning as it serves as the primary workholding device for securing the workpiece in the lathe spindle. The collet is a specialized chuck that clamps onto the workpiece, holding it firmly in place during the turning process. Its role in CNC turning includes the following:
1. Workpiece Holding: The collet securely grips the workpiece, ensuring that it remains fixed and stable during the machining process. This is essential to prevent any movement or vibrations that could lead to inaccuracies in the machined part.
2. Accuracy and Precision: By firmly holding the workpiece, the collet helps maintain accuracy and precision in CNC turning. The workpiece's position and orientation are critical for achieving the desired dimensions and tolerances in the finished part.
3. Quick Workpiece Changes: Collets are designed for rapid workpiece changes. This allows for efficient setup and minimizes downtime between different machining operations, improving overall productivity.
4. Consistency and Repeatability: The collet's ability to consistently hold the workpiece in the same position ensures repeatability in CNC turning. This is particularly important for mass production, where identical parts need to be produced with consistent quality.
5. Improved Surface Finish: A securely held workpiece leads to improved stability during the cutting process, resulting in a better surface finish on the machined part.
6. Reduced Tool Wear: Proper collet gripping reduces the chances of workpiece slippage or chatter, which can lead to increased tool wear. A stable workpiece allows the cutting tools to engage with the material accurately, prolonging tool life.
7. Minimized Workpiece Distortion: The collet's even and uniform clamping force helps minimize workpiece distortion during machining, particularly when working with delicate or thin-walled components.
8. Size Range: Collets come in various sizes to accommodate different workpiece diameters. This versatility allows for the machining of a wide range of part sizes using the same lathe.
9. Automatic Loading Systems: In automated CNC turning setups, collets are often used with automatic loading and unloading systems, allowing for continuous production with minimal operator intervention.
10. Safety: Properly clamped workpieces enhance safety during CNC turning by reducing the risk of workpiece ejection and potential accidents.
In summary, the collet is a critical component in CNC turning, providing a secure and efficient workholding solution for the workpiece. Its ability to hold the workpiece firmly, while allowing for quick and repeatable changes, contributes to the accuracy, productivity, and overall success of CNC turning operations.
What are some common cutting strategies used in CNC turning?
Common strategies include roughing, finishing, and facing.
In CNC turning, various cutting strategies are employed to achieve different machining goals and optimize the efficiency and quality of the process. Some common cutting strategies used in CNC turning include:
1. Facing: Facing is a basic turning operation used to create a flat surface at the end of the workpiece. It involves removing material from the workpiece's outer diameter to create a smooth, perpendicular face.
2. Turning: Turning is the fundamental CNC turning operation used to remove material from the outer diameter of the workpiece. It creates cylindrical shapes and reduces the workpiece's diameter to the desired size.
3. Roughing: Roughing is the initial material removal stage of CNC turning. It involves removing larger amounts of material to quickly shape the workpiece roughly to the desired form before finishing operations.
4. Finishing: Finishing is the final stage of CNC turning, where the cutting tool removes small amounts of material to achieve the required surface finish and precise dimensions.
5. Grooving: Grooving is a CNC turning operation used to cut narrow, straight or contoured grooves on the workpiece's surface. It is commonly used for creating O-ring grooves, snap ring grooves, and similar features.
6. Threading: Threading is the process of cutting threads on the workpiece's outer surface. CNC turning machines can perform both internal and external threading operations.
7. Parting: Parting, also known as cut-off or slitting, is used to separate the workpiece from the remaining stock. It involves cutting through the workpiece's diameter to create two separate parts.
8. Taper Turning: Taper turning is a CNC turning operation used to create tapered surfaces on the workpiece. The cutting tool is programmed to move at an angle relative to the workpiece axis, producing the desired taper.
9. Boring: Boring is used to enlarge an existing hole or create internal features with high precision. It involves cutting the interior surface of the workpiece using a single-point cutting tool.
10. Profile Turning: Profile turning involves cutting complex shapes and contours on the workpiece's outer surface. It is used to create intricate features and detailed designs.
11. Form Turning: Form turning is used to generate specific geometric shapes on the workpiece, such as convex or concave surfaces. It utilizes specialized cutting tools with predetermined profiles.
12. Knurling: Knurling is a CNC turning operation used to create a textured pattern on the workpiece's surface for improved grip or aesthetics.
These are some of the common cutting strategies used in CNC turning. The choice of cutting strategy depends on the specific part design, material, and machining requirements. CNC programmers and machinists use their expertise to select the most appropriate cutting strategies to achieve the desired results efficiently and accurately.
How does CNC turning help to reduce waste and increase efficiency in manufacturing?
CNC turning allows for greater precision and accuracy, which reduces waste and increases efficiency in the manufacturing process.
CNC turning offers several ways to reduce waste and increase efficiency in manufacturing processes. By combining advanced technology, automation, and precise control, CNC turning provides numerous benefits that contribute to waste reduction and improved efficiency. Here's how CNC turning helps in these aspects:
1. Material Optimization: CNC turning machines are programmed to remove only the necessary amount of material from the workpiece. This minimizes material wastage and helps optimize material usage, reducing the overall cost of production.
2. Reproducibility and Consistency: CNC turning allows for the creation of standardized programs that can be used to produce identical parts with consistent quality. This reduces the risk of errors and rework, saving time and resources.
3. Faster Setups: CNC turning machines can be set up quickly and efficiently with the use of pre-programmed toolpaths and tool libraries. This reduces downtime between production runs, leading to increased productivity.
4. Reduced Manual Labor: CNC turning is largely automated, reducing the need for extensive manual labor. This decreases the chances of human errors and fatigue-related mistakes, leading to better machining accuracy and efficiency.
5. Continuous Operation: CNC turning machines can operate continuously, 24/7, with minimal operator intervention. This non-stop production capability maximizes the utilization of the machine and reduces idle time.
6. Tool Life Management: CNC turning allows for precise control of cutting parameters, such as spindle speed and feed rate. This helps in optimizing tool life, reducing tool wear, and minimizing the need for frequent tool changes.
7. Real-time Monitoring and Control: CNC turning machines can be equipped with sensors and monitoring systems that provide real-time data on tool wear, machining performance, and part quality. This information enables operators to make timely adjustments, enhancing efficiency and reducing scrap.
8. Rapid Prototyping: CNC turning facilitates rapid prototyping by quickly translating CAD designs into tangible parts. This speeds up the product development process and reduces the need for extensive manual prototyping and iterations.
9. Shorter Lead Times: With faster setups, continuous operation, and reduced manual intervention, CNC turning helps in shortening production lead times, enabling manufacturers to meet customer demands more efficiently.
10. Less Secondary Operations: CNC turning machines can be equipped with multiple tool stations and live tooling capabilities, reducing the need for secondary operations on other machines. This streamlines the production process and improves efficiency.
11. Waste Recycling: CNC turning's material optimization and reduced scrap generation also contribute to waste reduction and support environmentally-friendly manufacturing practices.
Overall, CNC turning's precision, automation, and advanced capabilities contribute significantly to reducing waste, improving efficiency, and enhancing the overall competitiveness of manufacturing operations. By adopting CNC turning technology, manufacturers can achieve higher productivity, lower production costs, and improved sustainability.
How can manufacturers ensure that their CNC turning machines are properly maintained and calibrated?
Regular maintenance and calibration are essential for ensuring that CNC turning machines are operating at peak performance. Manufacturers can implement a maintenance and calibration schedule to ensure that their machines are in optimal condition.
Proper maintenance and calibration of CNC turning machines are essential to ensure their optimal performance, accuracy, and longevity. Regular maintenance and calibration practices help prevent breakdowns, reduce downtime, and maintain consistent machining quality. Here are some steps manufacturers can take to ensure that their CNC turning machines are properly maintained and calibrated:
1. Establish a Maintenance Schedule: Create a comprehensive maintenance schedule that includes regular inspections, cleaning, lubrication, and adjustments for various components of the CNC turning machine. The frequency of maintenance tasks may vary based on machine usage, but a well-defined schedule ensures timely and consistent maintenance.
2. Follow Manufacturer's Guidelines: Refer to the CNC machine manufacturer's maintenance guidelines and recommendations. They usually provide specific instructions for routine maintenance, calibration procedures, and best practices to keep the machine in top condition.
3. Train Operators and Maintenance Staff: Ensure that operators and maintenance staff receive proper training on the CNC turning machine's maintenance and calibration procedures. Well-trained personnel can identify potential issues and perform maintenance tasks correctly.
4. Monitor Machine Performance: Implement a system to monitor the CNC turning machine's performance regularly. Keep track of factors such as tool life, cutting parameters, accuracy, and part quality. Monitoring helps identify any deviations or abnormalities that may require maintenance or calibration.
5. Keep the Machine Clean: Regularly clean the CNC turning machine, including the work area, chip collection systems, and tool holders. Proper cleaning reduces the risk of contamination, improves accuracy, and prolongs the life of machine components.
6. Lubrication: Follow the recommended lubrication schedule and use the correct lubricants for various components. Lubrication prevents excessive wear, reduces friction, and ensures smooth machine operation.
7. Check and Replace Worn Parts: Inspect machine components, such as belts, bearings, and ball screws, for signs of wear and tear. Replace any worn or damaged parts promptly to maintain machine performance.
8. Calibrate the Machine: Schedule regular calibration of critical machine components, such as spindle runout, axis alignment, and tool offsets. Calibration ensures accurate machining and prevents dimensional inaccuracies.
9. Utilize Diagnostics and Monitoring Systems: Many modern CNC turning machines come equipped with diagnostic and monitoring systems. Use these systems to track machine health, tool condition, and performance metrics.
10. Document Maintenance and Calibration Records: Keep detailed records of all maintenance and calibration activities performed on the CNC turning machine. These records provide a historical overview of the machine's maintenance history and can be helpful for troubleshooting and decision-making.
11. Respond to Abnormalities: If the machine exhibits unusual behavior or experiences issues, address them promptly. Investigate the root cause, and take corrective actions to prevent further problems.
By diligently following these maintenance and calibration practices, manufacturers can ensure that their CNC turning machines operate optimally, maintain high accuracy, and deliver consistent, high-quality machining results. Properly maintained machines also contribute to a safer work environment and extended machine life, ultimately leading to enhanced productivity and profitability.
FAQs List of CNC Turning Services
What is CNC turning?
CNC turning is a manufacturing process that uses computer-controlled machines to create cylindrical parts by removing material from a rotating workpiece.
CNC turning, also known as computer numerical control turning, is a machining process used to create cylindrical parts by removing material from a rotating workpiece. It is a form of subtractive manufacturing, where material is removed from the workpiece to achieve the desired shape and dimensions. CNC turning is performed on a CNC lathe, which is a computer-controlled machine tool equipped with cutting tools that move in a linear path along the workpiece to remove material.
In CNC turning, the workpiece is clamped in a chuck or collet, and the cutting tool is mounted on a tool holder that moves along the workpiece's axis. The CNC turning machine follows pre-programmed instructions, called G-codes, to control the movements and actions of the cutting tool. These instructions specify the tool's position, feed rate, depth of cut, and other parameters to achieve precise machining.
During CNC turning, the workpiece rotates at a constant speed while the cutting tool traverses along the length of the workpiece. The cutting tool removes material from the workpiece's outer diameter, creating cylindrical shapes, threads, grooves, chamfers, and other features.
CNC turning is widely used in various industries for producing components such as shafts, pins, bushings, flanges, and other rotational parts. It offers several advantages, including high precision, repeatability, and the ability to produce complex shapes. CNC turning is also highly efficient and suitable for both low-volume and high-volume production runs.
The CNC turning process is versatile and can be used with a wide range of materials, including metals, plastics, and composites. It provides manufacturers with the flexibility to produce custom parts with tight tolerances and excellent surface finishes, making it an essential technology in modern manufacturing.
What types of materials can be used in CNC turning?
Common materials include metals (such as aluminum, brass, and steel), plastics, and wood.
CNC turning is a versatile machining process that can be used with a wide range of materials. The choice of material depends on the specific application, part requirements, and the machining capabilities of the CNC turning machine. Some common types of materials used in CNC turning include:
1. Metals:
- Aluminum: Lightweight, corrosion-resistant, and widely used in various industries.
- Steel: Offers good strength, toughness, and machinability for a wide range of applications.
- Stainless Steel: Provides excellent corrosion resistance and is commonly used in the food, medical, and aerospace industries.
- Brass: Known for its excellent electrical and thermal conductivity, often used in electrical components and decorative parts.
- Copper: Offers high electrical and thermal conductivity and is used in electrical and plumbing applications.
- Titanium: Known for its high strength-to-weight ratio and corrosion resistance, used in aerospace and medical applications.
- Cast Iron: Provides good wear resistance and vibration damping, commonly used for machine components.
2. Plastics:
- Acrylic (PMMA): Transparent, lightweight, and commonly used in displays, signs, and optical components.
- Nylon (Polyamide): Durable, low-friction material used in various engineering applications.
- Delrin (Polyoxymethylene, POM): Low-friction, wear-resistant material used for gears, bearings, and precision components.
- Polyethylene (PE): Lightweight and chemical-resistant material used in various applications.
- Polycarbonate (PC): Impact-resistant and used in applications requiring transparency and durability.
3. Composites:
- Carbon Fiber Reinforced Composites: Lightweight and high-strength materials used in aerospace, automotive, and sporting goods industries.
- Fiberglass Reinforced Composites: Offers good strength-to-weight ratio and used in various applications.
4. Other Materials:
- Wood: CNC turning can be used for wood turning applications to create artistic or functional wooden components.
- Ceramics: CNC turning can be used with certain ceramics for specialized applications.
It's essential to consider the specific properties of each material when choosing the right material for CNC turning. Factors such as mechanical properties, thermal conductivity, chemical resistance, and cost will influence the material selection for a particular part or component. CNC turning machines are capable of working with a wide variety of materials, making it a versatile and adaptable process for manufacturing various parts across different industries.
What is the difference between CNC turning and CNC milling?
CNC turning involves creating cylindrical parts by removing material from a rotating workpiece, while CNC milling involves cutting away material to create a 3D shape.
CNC turning and CNC milling are two distinct machining processes, each offering unique capabilities and applications. While both are computer numerical control (CNC) processes, they differ in the type of machine and the way material is removed from the workpiece. Here are the main differences between CNC turning and CNC milling:
1. Machine Type:
- CNC Turning: In CNC turning, the machining is performed on a lathe, also known as a CNC lathe or turning center. The workpiece rotates while the cutting tool remains stationary or moves along the workpiece's axis to remove material. CNC turning is primarily used for cylindrical and rotational parts.
- CNC Milling: In CNC milling, the machining is performed on a milling machine, also known as a CNC mill or machining center. The cutting tool rotates and moves along multiple axes to remove material from the workpiece in various directions. CNC milling is suitable for machining complex 3D shapes and features on both flat and curved surfaces.
2. Machining Process:
- CNC Turning: CNC turning is a process of removing material from the outside diameter of the workpiece to create cylindrical shapes, threads, and other rotational features.
- CNC Milling: CNC milling is a process of removing material from the workpiece using rotating cutting tools that can move along the X, Y, and Z axes. It can produce various shapes, slots, holes, and 3D contours on the workpiece.
3. Part Geometry:
- CNC Turning: CNC turning is best suited for parts with rotational symmetry, such as shafts, pins, and bushings. It excels at producing parts that have a consistent circular cross-section.
- CNC Milling: CNC milling is ideal for parts with complex geometries, 3D features, and varying surface profiles. It can create pockets, slots, steps, chamfers, and other intricate shapes.
4. Tooling:
- CNC Turning: CNC turning uses single-point cutting tools mounted on the lathe's tool post or turret. These tools have a single cutting edge and remove material as the workpiece rotates.
- CNC Milling: CNC milling uses multi-point cutting tools, such as end mills or drills, that have multiple cutting edges. The tools can move in multiple directions and angles to achieve various cutting actions.
5. Workpiece Fixturing:
- CNC Turning: The workpiece is usually held in a chuck or collet and rotates about its axis during CNC turning.
- CNC Milling: The workpiece is securely clamped to the milling machine's table or fixture and can be moved in multiple directions during CNC milling.
In summary, CNC turning and CNC milling are different machining processes suited for specific applications. CNC turning is ideal for cylindrical parts and rotational features, while CNC milling is preferred for complex 3D shapes and various surface profiles. Manufacturers choose between CNC turning and CNC milling based on the part's design, material, and the required machining operations.
What types of parts can be created using CNC turning?
CNC turning is ideal for creating parts such as shafts, pins, and connectors.
CNC turning is a versatile machining process that can create a wide range of parts with varying complexities. It is well-suited for producing cylindrical and rotational components, as well as parts with features that can be machined along the axial direction of the workpiece. Some common types of parts that can be created using CNC turning include:
1. Shafts: CNC turning is commonly used to produce shafts of various lengths and diameters used in machinery, engines, and transmission systems.
2. Pins and Bushings: CNC turning can create precise pins and bushings used in mechanical assemblies and linkages.
3. Flanges: Flanges, used for joining pipes, valves, and other components, can be CNC turned with the required mounting holes and features.
4. Connectors and Fittings: CNC turning is used to manufacture connectors, couplings, and fittings used in plumbing, hydraulics, and pneumatics.
5. Fasteners: CNC turning can produce screws, bolts, nuts, and other types of fasteners used in various applications.
6. Pulleys and Gears: CNC turning is used to create pulleys and gears for mechanical power transmission systems.
7. Couplings: CNC turning can produce rigid and flexible couplings used for connecting rotating shafts in machines.
8. Automotive Parts: CNC turning is commonly used in the automotive industry to produce various engine and transmission components, such as crankshafts, camshafts, and drive shafts.
9. Medical Components: CNC turning is used to manufacture medical device components, including surgical instruments, implantable devices, and orthopedic implants.
10. Aerospace Parts: CNC turning is employed in the aerospace industry to produce components such as engine shafts, turbine disks, and landing gear parts.
11. Hydraulic and Pneumatic Components: CNC turning is used to create hydraulic and pneumatic components, including valves, pistons, and cylinders.
12. Electrical and Electronics Parts: CNC turning is used to produce electrical connectors, terminals, and housings for electronic devices.
13. Lighting Fixtures: CNC turning can be used to create various components for lighting fixtures, such as lamp holders and housings.
14. Custom Artistic Components: CNC turning can produce artistic and decorative components, such as artistic wood turnings and decorative metalwork.
These are just a few examples of the types of parts that can be created using CNC turning. The process offers precise and consistent results, making it a valuable technology for manufacturing a wide variety of components used in industries ranging from automotive and aerospace to medical, electronics, and beyond.
What is the role of CAD software in CNC turning?
CAD software is used to create a 3D model of the part that is then used to generate the toolpaths for the CNC turning machine.
Computer-Aided Design (CAD) software plays a crucial role in CNC turning as it serves as the starting point for creating the digital model of the part to be machined. CAD software is used to design the 2D or 3D model of the component, which is then used to generate the necessary instructions for the CNC turning machine. Here's the role of CAD software in CNC turning:
1. Part Design: CAD software allows engineers and designers to create the detailed digital model of the part they want to manufacture using CNC turning. The software provides a user-friendly interface to design complex geometries, define dimensions, and specify tolerances.
2. Precise Geometry: CAD software ensures that the part's geometry is accurately represented in the digital model. This precision is essential to achieve the desired dimensions and fit of the finished part.
3. Visualization and Simulation: CAD software provides a 3D visualization of the part, allowing designers to see the part from different angles and assess its aesthetics and functionality. Some advanced CAD software also enables simulation, which can help detect interferences and potential machining issues.
4. Design Iterations: CAD software allows designers to make changes and iterations to the part's design easily. This flexibility is invaluable in the design process, enabling engineers to optimize the part's performance and manufacturability.
5. Parametric Modeling: CAD software often supports parametric modeling, which allows designers to link dimensions and relationships between features. Changes to one parameter automatically update related features, streamlining the design process.
6. Exporting CAM Data: Once the part design is complete, the CAD software can export the model to Computer-Aided Manufacturing (CAM) software. The CAM software uses the CAD model to generate toolpaths and G-code instructions for the CNC turning machine.
7. Toolpath Generation: CAM software uses the CAD model's geometry to calculate the most efficient toolpaths for CNC turning. It determines the tool's movements, feeds, and speeds to achieve the desired machining result.
8. Post-Processing: CAM software generates machine-specific G-code based on the CNC turning machine's capabilities and configuration. This G-code provides the instructions necessary to control the machine during the turning process.
9. Design Reuse: CAD software enables the reuse of existing part designs, saving time and effort when manufacturing similar or modified components.
In summary, CAD software is an essential tool in CNC turning, as it serves as the foundation for part design and enables seamless integration with CAM software. The CAD-to-CAM workflow streamlines the manufacturing process, ensuring that the part design is accurately translated into the machining instructions for the CNC turning machine. The use of CAD software enhances precision, accelerates design iterations, and facilitates efficient production in CNC turning operations.
What is the role of CAM software in CNC turning?
CAM software is used to generate the toolpaths that tell the machine how to remove material from the workpiece to create the desired shape.
Computer-Aided Manufacturing (CAM) software plays a critical role in CNC turning as it bridges the gap between the part design created in CAD software and the actual machining process. CAM software takes the digital model of the part designed in CAD and generates the necessary toolpaths and instructions (G-code) that control the CNC turning machine. Here's the role of CAM software in CNC turning:
1. Toolpath Generation: The primary role of CAM software is to generate toolpaths that guide the cutting tool's movements during CNC turning. It calculates the most efficient toolpath based on the part's geometry, required features, and machining parameters.
2. Feeds and Speeds Calculation: CAM software determines the appropriate feeds (cutting speed) and speeds (rotational speed of the spindle) for the CNC turning process. It takes into account factors such as material type, tooling, cutting forces, and desired surface finish to optimize the machining parameters.
3. Material Removal Simulation: CAM software can simulate the material removal process to visualize how the cutting tool interacts with the workpiece. This simulation helps identify potential collisions, interferences, or areas that need additional attention in the machining process.
4. Tool Selection and Management: CAM software enables the selection of appropriate cutting tools based on the part's design and machining requirements. It also manages tool libraries, keeping track of tool wear, tool life, and tool changes during the production process.
5. Customization and Optimization: CAM software allows machinists to customize the machining process to suit specific requirements. They can adjust cutting strategies, choose different toolpaths, and optimize tool movements for maximum efficiency and accuracy.
6. Post-Processing: Once the toolpaths are generated, CAM software translates them into machine-readable G-code. The G-code contains precise instructions for the CNC turning machine, specifying the tool movements, spindle speed, feed rate, and other parameters required to machine the part.
7. Multi-Axis Machining: Advanced CAM software supports multi-axis machining, allowing CNC turning machines with additional axes (such as live tooling or sub-spindles) to perform complex operations and create intricate features.
8. Error Detection and Correction: CAM software includes features to detect potential errors in the toolpaths, such as collisions or overcuts. It provides options to adjust the toolpaths or optimize the cutting sequence to avoid machining issues.
9. Batch Processing: CAM software can optimize toolpaths and machining parameters for multiple parts in a batch, reducing setup time and enhancing production efficiency.
In summary, CAM software is instrumental in CNC turning as it takes the part design from CAD software and converts it into the detailed instructions needed for the CNC turning machine. By generating efficient toolpaths and handling machining parameters, CAM software optimizes the manufacturing process, ensuring accurate and consistent results during CNC turning operations.
What are some common cutting tools used in CNC turning?
Common cutting tools include drills, end mills, and boring tools.
In CNC turning, a variety of cutting tools are used to remove material from the workpiece and create the desired shape and features. These cutting tools are mounted on the tool turret or toolpost of the CNC lathe and are selected based on the material being machined, the required features, and the cutting conditions. Some common types of cutting tools used in CNC turning include:
1. Turning Inserts: These are the most common cutting tools used in CNC turning. Turning inserts are indexable cutting tools with multiple cutting edges. They come in various geometries and grades optimized for specific materials and cutting conditions.
2. Boring Bars: Boring bars are used to enlarge existing holes or create internal features with high precision. They are available in different lengths and configurations to accommodate various bore sizes and depths.
3. Grooving and Parting Tools: Grooving tools are used to cut narrow, straight or contoured grooves on the workpiece's surface. Parting tools, also known as cut-off tools, are used to separate the workpiece from the remaining stock by cutting through the diameter.
4. Threading Tools: Threading tools are used to cut threads on the workpiece's outer surface. They come in different profiles to create various thread types, such as internal and external threads.
5. Face Mills: Face mills are used for facing operations to create flat surfaces at the end of the workpiece. They remove material from the workpiece's outer diameter.
6. Drill Bits: In some cases, drill bits can be used for drilling holes in the workpiece on a CNC lathe with live tooling capabilities.
7. Live Tooling: CNC lathes equipped with live tooling allow for the use of rotating cutting tools, such as end mills or drills, to perform milling or drilling operations on the workpiece's outer surface.
8. Knurling Tools: Knurling tools are used to create textured patterns on the workpiece's surface for improved grip or decorative purposes.
9. Thread Mills: Thread mills are used for thread milling operations, creating internal and external threads using a helical cutting motion.
10. Center Drills: Center drills are used to create accurate starting holes for subsequent drilling operations.
It's important to select the appropriate cutting tools based on the specific material, part geometry, and machining requirements. CNC turning machines are designed to accommodate a variety of cutting tools and tool holders, offering flexibility to perform various operations efficiently and achieve the desired results.
What is the role of the lathe in CNC turning?
The lathe holds and rotates the workpiece while the cutting tool removes material to create the desired shape.
The lathe plays a central role in CNC turning as it is the primary machine used to perform the turning process. In CNC turning, the lathe is a computer-controlled machine tool that rotates the workpiece while a cutting tool removes material from the workpiece's outer diameter. The lathe's main functions and roles in CNC turning are as follows:
1. Rotating the Workpiece: The primary function of the lathe is to hold and rotate the workpiece. The workpiece is mounted on the lathe's spindle and rotates at a controlled speed. The rotation allows the cutting tool to remove material and shape the workpiece.
2. Holding and Clamping the Workpiece: The lathe provides a secure holding mechanism to clamp and immobilize the workpiece during the machining process. Workholding devices, such as chucks or collets, are used to grip the workpiece and ensure it remains stable during cutting.
3. Carrying the Cutting Tool: The lathe is equipped with a tool turret or toolpost that holds and positions the cutting tool. The tool turret allows for the use of multiple cutting tools, each with a specific function, which can be quickly and accurately positioned as needed.
4. Tool Feed and Control: The lathe's tool turret or toolpost can be moved along the workpiece's axis, controlling the depth of cut and feed rate of the cutting tool. This movement is precisely controlled by the CNC system based on the programmed toolpaths.
5. Generating Toolpaths: The CNC system within the lathe interprets the G-code program generated by the CAM software. It converts the instructions into specific tool movements and feed rates, effectively generating the toolpaths that the cutting tool follows to shape the workpiece.
6. Real-time Monitoring: Many modern CNC lathes come with sensors and monitoring systems that provide real-time data on tool wear, machining performance, and part quality. This information enables operators to make timely adjustments to maintain efficient and accurate machining.
7. Automation and Precision: The lathe's CNC system enables automation of the machining process, resulting in precise and consistent cuts. The computer-controlled movements ensure that each part is machined with the same accuracy, reducing variability and increasing productivity.
8. Multitasking Capabilities: Some CNC lathes are equipped with live tooling and additional spindles, allowing for multitasking capabilities. These machines can perform milling, drilling, and other operations in addition to turning, increasing their versatility.
In summary, the lathe is the core machine tool in CNC turning. It holds and rotates the workpiece, positions and moves the cutting tool, and interprets the CNC program to execute precise machining operations. CNC lathes have revolutionized the turning process, offering high precision, efficiency, and automation in the production of cylindrical and rotational parts.
What is the role of the chuck in CNC turning?
The chuck holds the workpiece in place while it rotates during the turning process.
The chuck is a crucial component in CNC turning, as it plays a fundamental role in securely holding and rotating the workpiece during the machining process. The chuck is a specialized clamping device mounted on the lathe's spindle, and it provides the means to firmly grip and position the workpiece. Here's the role of the chuck in CNC turning:
1. Workpiece Clamping: The primary role of the chuck is to securely clamp the workpiece. It provides a firm grip on the workpiece to prevent any movement or vibration during machining, ensuring accuracy and repeatability in the machined features.
2. Rotating the Workpiece: The chuck is mounted on the lathe's spindle, and it enables the rotation of the workpiece. The spindle, along with the chuck, rotates the workpiece at a controlled speed, allowing the cutting tool to remove material and shape the workpiece.
3. Accommodating Various Workpiece Sizes: Chucks come in different sizes and configurations to accommodate a wide range of workpiece sizes and shapes. They can be designed to hold small, delicate parts or large, heavy workpieces, making them versatile for various machining applications.
4. Quick and Easy Workpiece Loading: Chucks are designed to allow for quick and easy loading and unloading of the workpiece. This facilitates efficient setup and reduces downtime between machining operations.
5. Multiple Jaw Configurations: Some chucks have multiple jaws that can be adjusted to hold various workpiece shapes and diameters. The jaws can be moved inwards or outwards to securely grip the workpiece.
6. Precision and Repeatability: Chucks are manufactured to high precision to ensure consistent and repeatable clamping of the workpiece. This is critical for maintaining dimensional accuracy and uniformity in the machined parts.
7. Jaw Positioning: In CNC turning, the jaws of the chuck can be precisely positioned using the lathe's control system. This allows for quick and accurate centering of the workpiece, ensuring proper alignment with the cutting tool.
8. Expanding and Contracting: Some chucks, known as collet chucks, can expand and contract to hold different workpiece diameters without requiring jaw adjustments. Collet chucks are especially useful for small-diameter parts.
In summary, the chuck's primary role in CNC turning is to securely hold and rotate the workpiece, providing a stable and accurate setup for the machining process. Its precision and flexibility contribute to the overall efficiency and success of the CNC turning operation, allowing for the production of high-quality cylindrical and rotational parts.
What is the role of the tailstock in CNC turning?
The tailstock provides support to the workpiece during the turning process and can be used to hold cutting tools.
The tailstock is an essential component in CNC turning, serving multiple functions that contribute to the overall machining process. It is located on the opposite end of the lathe from the chuck and provides additional support to the workpiece during machining. The tailstock plays the following roles in CNC turning:
1. Workpiece Support: The primary role of the tailstock is to provide additional support to the workpiece, especially when machining long or slender parts. It helps to minimize deflection or bending of the workpiece due to the cutting forces, ensuring dimensional accuracy and surface finish.
2. Centering and Alignment: The tailstock is equipped with a center, known as the tailstock center or dead center, which can be precisely aligned with the center of the workpiece. This alignment ensures that the workpiece rotates concentrically with the lathe's spindle, resulting in accurate and centered machining.
3. Drilling and Boring Operations: The tailstock can be extended or retracted to accommodate various workpiece lengths. This feature allows the tailstock to be used for drilling and boring operations, where a stationary cutting tool is used to create holes or enlarge existing holes in the workpiece.
4. Counterbalancing: In some CNC turning applications, long workpieces may cause an imbalance in the machine's spindle due to their weight. The tailstock can be used to counterbalance the weight of the workpiece, reducing vibrations and enhancing machining stability.
5. Steady Rest Mounting: The tailstock can be used to support a steady rest, a specialized device used to stabilize and support long, slender workpieces during machining. The steady rest reduces workpiece deflection and ensures consistent machining results.
6. Taper Turning: The tailstock can be adjusted to create a slight taper on the workpiece if required for the specific part's design or application.
7. Lubrication: Some tailstocks are equipped with lubrication systems to reduce friction between the tailstock center and the workpiece, allowing for smooth rotation during machining.
8. Quick Release: Many modern CNC lathes have a quick-release mechanism for the tailstock, allowing for rapid positioning and removal of the tailstock when it is not needed.
The tailstock is a valuable feature in CNC turning, providing additional support, stability, and alignment for the workpiece during machining. Its use enhances machining precision and allows for a wider range of operations, making it a versatile tool in the CNC turning process.
What is the difference between a CNC lathe and a manual lathe?
A CNC lathe is controlled by a computer and can produce more complex parts with greater precision than a manual lathe.
The primary difference between a CNC lathe and a manual lathe lies in the method of operation and the level of automation they offer. Both machines are used for turning operations, but they differ significantly in terms of control, setup, and capabilities. Here are the key differences between a CNC lathe and a manual lathe:
1. Control and Operation:
- CNC Lathe: CNC stands for Computer Numerical Control. In a CNC lathe, the machining process is automated and controlled by a computer. The operator uses CAD/CAM software to create a digital model of the part and generate the toolpaths. The CNC machine then reads the G-code instructions and controls the movements of the cutting tool, spindle, and other machine functions automatically.
- Manual Lathe: A manual lathe, on the other hand, is operated entirely by the machinist. The operator manually adjusts the cutting tool's position, controls the spindle speed, and moves the cutting tool along the workpiece by hand using various manual controls and handwheels.
2. Programming and Setup:
- CNC Lathe: Programming a CNC lathe involves creating a part design using CAD software and generating the G-code program with CAM software. The setup also includes loading the workpiece, tools, and tool offsets, and defining the cutting parameters. Once set up, the CNC lathe can repeatedly produce identical parts with high accuracy and precision.
- Manual Lathe: In a manual lathe, the setup and operation are more labor-intensive. The machinist manually positions and secures the workpiece and tools, adjusts the cutting parameters, and manually operates the machine throughout the turning process. The process requires skill and experience to achieve consistent results.
3. Automation and Productivity:
- CNC Lathe: CNC lathes are highly automated, allowing for unattended operation and higher productivity. Once the program is set up, the machine can run continuously, producing parts with minimal operator intervention. CNC lathes can also perform complex machining operations and multitasking capabilities.
- Manual Lathe: Manual lathes are less automated, requiring continuous manual operation by the machinist. This makes them slower and less productive compared to CNC lathes, especially for high-volume production.
4. Complexity of Parts:
- CNC Lathe: CNC lathes are capable of machining complex parts with intricate geometries and features. The CNC control allows for precise tool positioning and movement, enabling the creation of more complex shapes and designs.
- Manual Lathe: Manual lathes are best suited for simpler parts with straightforward geometries. Creating intricate features or complex shapes is more challenging and time-consuming on a manual lathe.
In summary, a CNC lathe is a more advanced and automated machine that offers higher productivity, versatility, and the ability to produce complex parts with greater accuracy. A manual lathe, on the other hand, requires skilled operators, offers limited automation, and is best suited for simpler turning tasks. The choice between a CNC lathe and a manual lathe depends on the specific manufacturing needs, part complexity, and the level of automation required for the production process.
What is the role of the operator in CNC turning?
The operator is responsible for setting up the machine, selecting the appropriate tools, and monitoring the turning process.
The operator plays a crucial role in CNC turning despite the high level of automation provided by the CNC system. While much of the machining process is automated, the operator's involvement is essential to ensure the CNC turning machine operates efficiently, safely, and produces high-quality parts. Here are some key roles of the operator in CNC turning:
1. Program Setup: The operator is responsible for setting up the CNC lathe with the correct program. This involves loading the appropriate G-code program into the machine's control system, which defines the toolpaths, cutting parameters, and other instructions for the machining process.
2. Workpiece Setup: The operator loads the workpiece into the chuck or collet and ensures it is securely clamped and aligned with the lathe's spindle. Proper workpiece setup is critical to achieve accurate and consistent machining results.
3. Tooling Setup: The operator installs the cutting tools on the lathe's tool turret or toolpost. This includes selecting the right cutting tools, installing them correctly, and adjusting tool offsets to ensure accurate tool positioning.
4. Machine Calibration: The operator may perform periodic calibration and alignment checks on the machine to ensure it is operating within specified tolerances. This helps maintain the machine's accuracy and overall performance.
5. Monitoring and Inspection: The operator monitors the CNC turning process, observing the machine's operation, and ensuring everything is running smoothly. They may also inspect the machined parts for quality, dimensions, and surface finish.
6. Tool Changes and Maintenance: The operator may be responsible for tool changes during the machining process, especially in jobs requiring multiple tool setups. Additionally, they may perform routine tool maintenance, such as replacing worn or damaged tools.
7. Troubleshooting: In the event of tool breakage, program errors, or other issues, the operator is responsible for troubleshooting and resolving the problems to minimize downtime and maintain productivity.
8. Process Optimization: The operator can make adjustments to the cutting parameters, toolpaths, and other settings to optimize the machining process, improve efficiency, and achieve better part quality.
9. Safety Compliance: The operator ensures that safety protocols and procedures are followed during CNC turning operations, promoting a safe working environment for themselves and others.
10. Tool Life and Material Management: The operator keeps track of tool life and may be responsible for managing tool inventory. They may also manage material stock, ensuring an adequate supply for continuous production.
11. Machine Maintenance: While not all machine maintenance tasks are performed by the operator, they may be involved in routine cleaning, lubrication, and simple maintenance tasks to keep the CNC turning machine in good working condition.
In summary, the operator's role in CNC turning is critical for the overall success of the machining process. Their responsibilities include setup, monitoring, inspection, troubleshooting, and process optimization. By skilled and knowledgeable operators, CNC turning operations can run efficiently, producing high-quality parts with minimal downtime and waste.
How can CNC turning be used in the manufacturing of small parts?
CNC turning is ideal for creating small parts with high precision and accuracy.
CNC turning is well-suited for the manufacturing of small parts due to its precision, repeatability, and ability to efficiently produce high volumes of small components. The process is widely used in industries that require the production of small and intricate parts with tight tolerances. Here are some ways CNC turning can be effectively used in the manufacturing of small parts:
1. High Precision: CNC turning machines offer exceptional precision, allowing for accurate machining of small parts with tight tolerances. The computer-controlled movements of the cutting tool ensure consistent results, ensuring that each small part is produced to the exact specifications.
2. Automation and Efficiency: CNC turning is highly automated, which makes it ideal for mass production of small parts. Once the CNC program is set up, the machine can run continuously, producing identical parts with minimal operator intervention, resulting in high productivity.
3. Multitasking Capabilities: Some advanced CNC turning machines come with multitasking capabilities, which means they can perform multiple operations in a single setup. This enables the production of small parts with complex features without the need for additional machines or setups.
4. Material Versatility: CNC turning can be used with a wide range of materials, including metals, plastics, and composites. This versatility allows for the manufacturing of small parts for diverse industries and applications.
5. Quick Setup and Changeover: CNC turning machines allow for quick and straightforward setup and changeover between different part runs. This flexibility is advantageous when manufacturing small batches of various parts.
6. Consistency and Quality Control: CNC turning ensures consistent and repeatable results, critical for maintaining quality control in the production of small parts. It reduces variability and the likelihood of defects, ensuring that each part meets the required standards.
7. Reducing Waste: CNC turning is a subtractive manufacturing process, meaning it removes material to create the final part. This reduces material waste compared to other manufacturing methods like casting or molding.
8. Small Tooling Options: CNC turning machines can accommodate small cutting tools, enabling the creation of intricate features and fine details in small parts.
9. Secondary Operations: CNC turning can be combined with other machining processes like milling, drilling, and tapping to perform additional operations on small parts, further enhancing their complexity and functionality.
10. Scalability: CNC turning is scalable, allowing manufacturers to adjust production volumes based on demand. It is equally efficient for producing small quantities or large-scale production runs of small parts.
In summary, CNC turning is a versatile and efficient method for manufacturing small parts with high precision and consistency. Its automation, versatility, and capability to handle complex features make it an ideal choice for a wide range of industries requiring small and intricate components.
What are some common challenges in CNC turning?
Common challenges include tool wear, vibration, and chip removal.
CNC turning is a sophisticated machining process that offers numerous advantages, but it also comes with some challenges that manufacturers must address to ensure successful and efficient operations. Some common challenges in CNC turning include:
1. Tool Wear and Tool Life: Cutting tools used in CNC turning are subject to wear and degradation due to the high-speed cutting forces and friction. Managing tool wear and tool life is crucial to maintain part accuracy, surface finish, and reduce downtime for tool changes.
2. Chip Control: The chips generated during the turning process can cause problems if not effectively controlled. Improper chip evacuation can lead to chip jamming, tool damage, and affect the machining process's performance.
3. Part Deflection: When machining long or slender parts, the workpiece may experience deflection due to cutting forces, leading to inaccuracies in part dimensions and surface finish. Careful consideration of part support and tool positioning is necessary to minimize deflection.
4. Workpiece Material Selection: Different materials have distinct machining characteristics, and some materials, such as high-temperature alloys or hardened steels, can be challenging to machine. Selecting the appropriate cutting tools and cutting parameters for specific materials is crucial to achieve optimal results.
5. Programming Errors: CNC turning relies on accurate G-code programming. Programming errors can lead to tool collisions, incorrect toolpaths, and other machining issues. Thoroughly verifying the CNC program and performing simulations can help avoid costly mistakes.
6. Surface Finish: Achieving the desired surface finish can be challenging, especially when machining complex geometries or tough materials. Proper tool selection, cutting parameters, and toolpath strategies are essential to achieving the required surface quality.
7. Heat Management: The heat generated during the machining process can affect the tool's performance and lead to thermal expansion of the workpiece, affecting part accuracy. Effective heat management strategies, such as coolant usage and appropriate cutting speeds, are crucial.
8. Machining Complex Shapes: CNC turning is well-suited for rotational parts, but machining complex 3D shapes may require additional operations or alternative machining methods.
9. Setup Time and Changeovers: Setting up the CNC lathe for a new part or changing tools can take time and may impact production efficiency, particularly when dealing with small batch sizes or frequent job changes.
10. Multitasking Complexities: Some advanced CNC turning machines offer multitasking capabilities, which involve simultaneous turning, milling, and other operations. Managing these complex operations requires skilled programming and operator expertise.
11. Part Holding and Workholding: Securing and supporting the workpiece during machining is crucial for part accuracy and stability. Choosing the right workholding solutions for various part geometries is essential.
By understanding and addressing these challenges, manufacturers can optimize CNC turning operations, improve productivity, and achieve high-quality results in their manufacturing processes. Regular maintenance, skilled operators, and continuous process improvement contribute to overcoming these challenges and ensuring CNC turning success.