Peek Kunststoffteile Materialien
Polyether ether ketone, or PEEK, injection molding is a pretty amazing way to make high-quality plastic parts. This method lets us create parts that are super strong and durable.
PEEK is a special type of plastic known for its incredible strength, stiffness, and ability to withstand heat, chemicals, and wear and tear. It's like the ultimate all-rounder in the world of materials.
Here’s how it works: First, we melt down the raw PEEK material in a heated barrel. Once it's melted, we inject it under high pressure into a carefully designed mold. The molten PEEK fills the mold and then cools down, taking on the exact shape we want. It's like magic, but backed by science!
This process is incredibly precise, allowing us to make complex shapes with very tight tolerances. It’s like having a Swiss watchmaker’s precision for every part we produce. That’s why it’s perfect for industries like aerospace, automotive, medical, and oil and gas. These sectors need really complex parts, and PEEK injection molding delivers.
And there’s more! PEEK injection molding is also used to make components for high-performance applications such as pumps, valves, and electrical connectors. These parts are the unsung heroes of our daily lives, working tirelessly behind the scenes to keep everything running smoothly.
So, the next time you use a product that relies on these high-performance plastic parts, remember the incredible process that made it possible. PEEK injection molding isn’t just a manufacturing technique; it’s a testament to human ingenuity and innovation.
Peek Plastic Parts Making Service
Be good at product structure optimization and greatly reduce the cost of Plastic Parts Materials
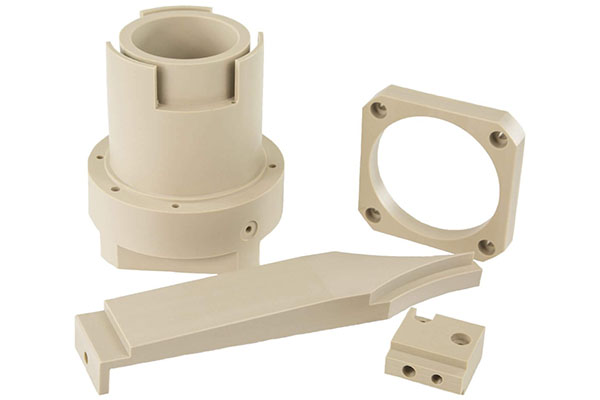
Teil Design
Auftritt und Strukturdesign
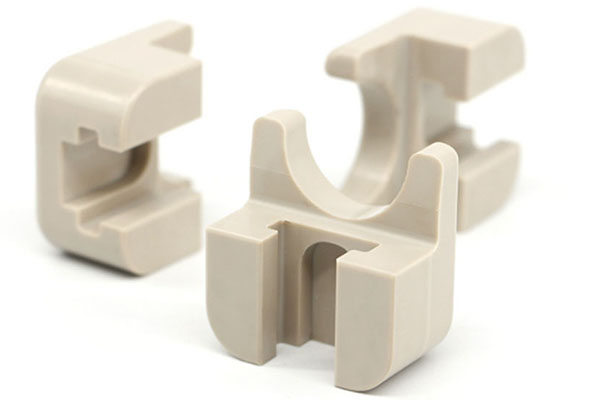
Formenbau
Design, Bestätigung der Fertigungsfähigkeit
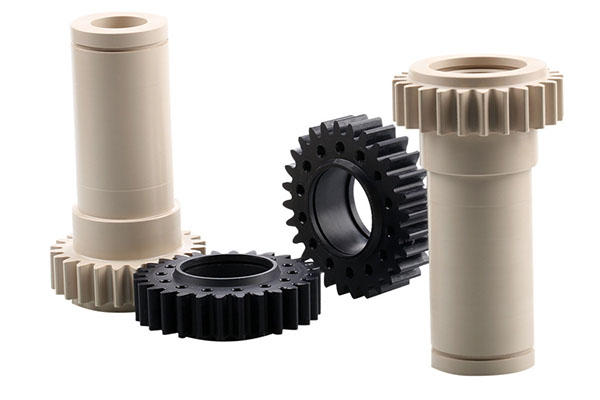
Produktion
Imported, high-speed equipment
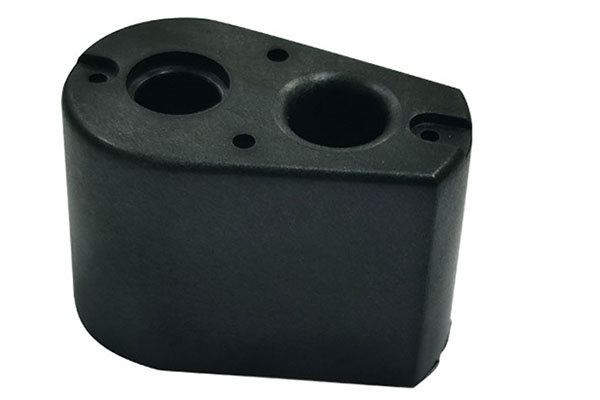
Produktmontage
Einlaufende Materialien, Inspektion und Montage
Exploring the Benefits and Applications of PEEK Plastic Parts Materials
Polyether ether ketone, or PEEK for short, is a superstar in the world of plastic parts. It's tough, stands up to heat, and doesn't mess around with chemicals, making it perfect for all kinds of heavy-duty jobs. Whether you're in the business of building machines that can take a beating or crafting medical gear that needs to be sterilized but still strong, PEEK has got your back.
Let's break down why PEEK is so awesome:
Toughness: This material can handle serious stress without breaking a sweat. It's like the superhero of plastics when it comes to taking on weight and wear.
Heat Resistance: Up to 260°C (500°F), no problemo! PEEK stays cool under pressure, making it great for things that get hot, like engines or cooking appliances.
Chemical Resistance: Strong acids? Harsh bases? No biggie. PEEK laughs in the face of corrosive stuff, which means it lasts longer in rough conditions.
Lightweight & Smooth: Light as a feather but strong as an ox, PEEK also glides smoothly, reducing friction and wear. This means parts move better and last longer.
Easy to Work With: You can shape PEEK into almost anything using injection molding or other methods. It's like Play-Doh for engineers, but way stronger.
Where does PEEK shine? Well, just about everywhere:
- Sky High: In aerospace, PEEK makes parts that keep planes and rockets flying safely.
- Health Hero: Medical devices benefit from PEEK's strength and biocompatibility.
- Oil Country: Down in the oil fields, PEEK components withstand extreme conditions.
- Road Warriors: Automotive applications love PEEK for its strength and resistance to car chemicals.
In short, PEEK injection molding materials are like the Swiss Army knife of the manufacturing world. They're versatile, durable, and make life easier for engineers and designers alike. By choosing PEEK, you're not just getting a part; you're getting peace of mind knowing it'll perform well and last a long time.