DLP 3D Printing Service for Creative Projects
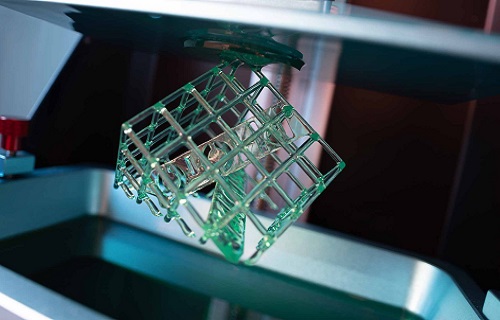
Unlock Endless Possibilities with Our Premium DLP 3D Printing Service
Let our cutting-edge DLP (Digital Light Processing) 3D printing services enhance your creative vision, where precision and detail intertwine, unlocking new possibilities. Trusted by industry leaders and passionate enthusiasts, our advanced DLP technology provides unparalleled print quality that will surely exceed your wildest expectations.
Unleash the true potential of your design with a printing resolution of up to 25 microns, allowing you to turn the most complex creations into reality with astonishing clarity and delicate details. Whether you are prototyping new products, designing custom artworks, or exploring the infinite possibilities of additive manufacturing, our DLP 3D printing services are the gateway to unleash your creative talents.
Our professional 3D printing team supports you and guides you through every step, ensuring that the project is executed with the utmost care and attention. From material selection to post-processing, we work closely with you to ensure that your vision is achieved with precision and perfection.
How DLP 3D Print Works
The Principle Behind DLP 3D Printing Technology
DLP (Digital Light Processing) is a cutting-edge rapid prototyping technology that solidifies photosensitive polymer liquid layer by layer using a projector, enabling the creation of intricate 3D printed objects. The process begins with slicing software that divides the 3D model into a series of individual layer images, which are then displayed by the projector.
Each image layer is cured through a photopolymerization reaction in areas where the resin layer is extremely thin, forming a single solid layer of the part. After each layer is cured, the build platform moves down by one layer, and the projector displays the next layer image, continuing this cycle for subsequent layers.
This iterative process allows the printing to be completed directly, resulting in not only high forming accuracy but also very fast printing speeds. The DLP technology's ability to rapidly cure each layer through precise light projection is the key to its superior print quality and efficiency. This makes it an ideal choice for creating detailed and complex 3D models efficiently.
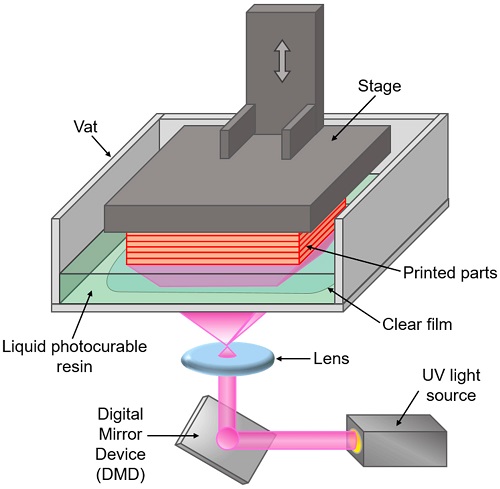
DLP Design Guidelines and Capabilities
Our basic guidelines for stereolithography include important design considerations to help improve part manufacturability, enhance cosmetic appearance, and reduce overall production time.
Max Part Size | 192*108*200mm | 7.56*4.25* 7.87 in. |
Layer Thickness | 50 microns | 0.00197 in. |
Minimum Feature Size | 0.05mm | 0.00197 in. |
DLP Tolerances | For well-designed parts, tolerances of +/0.012 in. (0.30mm) plus +/- 0.002 in./in.(0.002mm/mm) for each additional inch can typically be achieved. Note that tolerances may change depending on part geometry. |
Advantage of DLP 3D Print
● DLP 3D printing has a wide range of printable materials available, offering versatility for a diverse set of applications.
● The printing resolution of DLP 3D printers is much higher compared to other technologies, resulting in parts with a smoother surface finish.
● The working process of DLP 3D printing involves projecting and curing an entire layer at once. By utilizing light to solidify the resin, the whole layer is formed simultaneously, which can significantly improve the overall printing speed.
● The future application space for DLP 3D printing is even greater, as the technology continues to evolve and unlock new possibilities for rapid prototyping, small-scale production, and complex part fabrication.
DLP Printed Parts Application
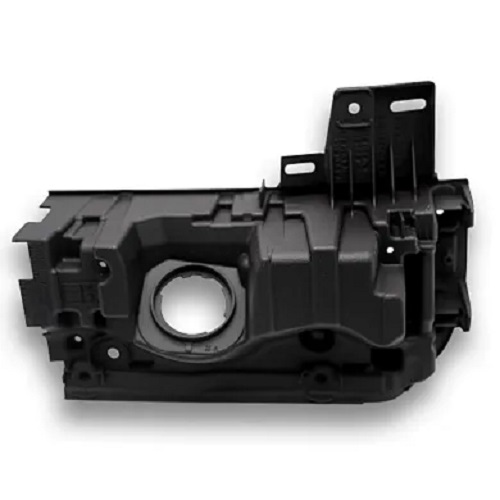
Car 3d Model Engine Cover
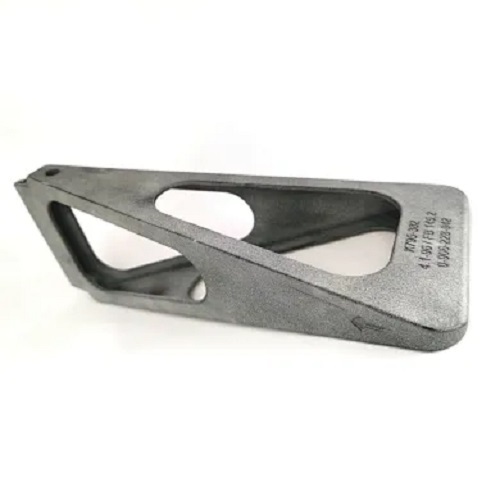
Jet Fusion Functional Parts
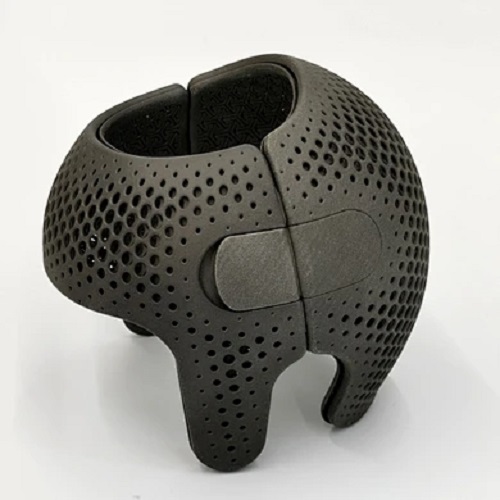
High Strength Nylon Head Orthopedics
DLP 3D printing equipment
As a professional 3D printing company, we boast an extensive fleet of 50 SLA resin 3D printers, complemented by 6 advanced SLS nylon 3D printers and metal 3D printers. Our diverse range of 3D printing materials ensures that we can meet the specific needs of any project, and our comprehensive post-processing capabilities guarantee high-quality finishes.
We offer a wide array of services including 3D printing, copying, and coloring, backed by a dedicated team specializing in model production. This team possesses exceptional display analysis and design capabilities, ensuring that your projects are handled with precision and creativity.
Our commitment to quality is underscored by a strict quality management system certification. With extensive experience spanning industries such as automobiles, home appliances, office equipment, building models, medical dentistry, jewelry, sculpture, ceramics, and more, we bring unparalleled expertise to every project. Whether you need rapid prototyping or custom manufacturing, our state-of-the-art facilities and skilled professionals are ready to elevate your creative visions to reality.
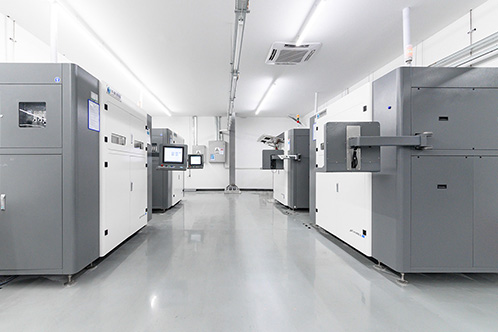
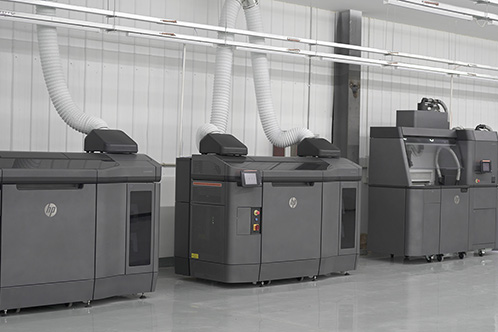
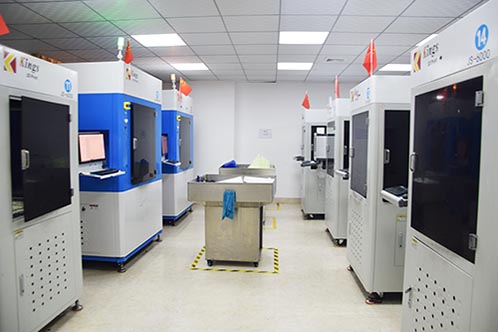
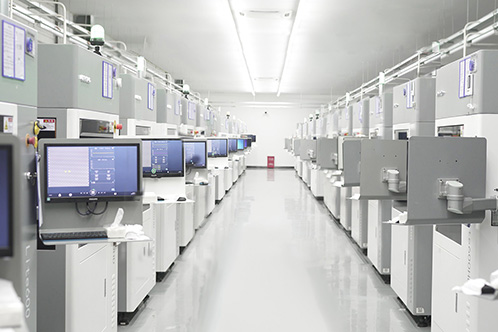
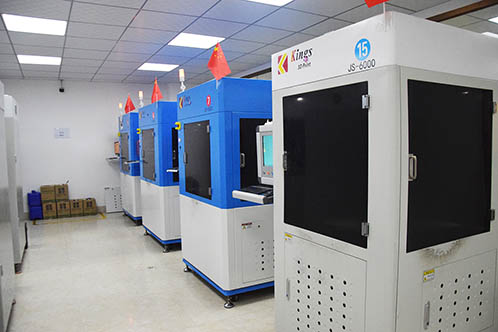
DLP 3D Printing FAQ
What is DLP 3D Printing and how does it work?
DLP (Digital Light Processing) 3D printing is a additive manufacturing technology that uses a digital light source, such as a projector or DLP chip, to selectively cure photopolymer resin layer-by-layer to create 3D objects.
What are the key advantages of DLP 3D printing?
DLP 3D printing offers high resolution, fast print speeds, and smooth surface finishes compared to other 3D printing technologies. It also has a wide range of compatible photopolymer materials.
What materials can be used with DLP 3D printers?
DLP 3D printers can work with a variety of photopolymer resins, including standard acrylics, engineering-grade resins, flexible rubbers, dental materials, and more. Material selection depends on the desired part properties.
What are the typical applications for DLP 3D printing?
Common DLP 3D printing applications include rapid prototyping, jewelry making, dental models, microfluidics, model making, and other projects requiring high-resolution, detailed parts.
What is the print resolution of DLP 3D printers?
DLP 3D printers can achieve print resolutions down to 25 microns or even finer, allowing for extremely detailed and precise 3D printed parts.
How fast are DLP 3D printers compared to other technologies?
DLP 3D printing is generally faster than other resin-based 3D printing methods, as it can cure an entire layer at once rather than a point-by-point process.
What are the post-processing steps for DLP 3D printed parts?
Parts typically require post-curing under UV light to fully harden the resin, as well as cleaning and support removal depending on the design.
Can DLP 3D printing be used for mass production?
While not as scalable as injection molding, DLP 3D printing can be a cost-effective solution for small-batch manufacturing and bridge production.
What are the limitations or drawbacks of DLP 3D printing?
Limitations include part size constraints, the need for support structures, and the limited color options compared to FDM or SLA printing.
How does the cost of DLP 3D printing compare to other 3D printing methods?
DLP 3D printing can have higher upfront equipment costs but lower per-part costs, making it economical for high-resolution, low-volume applications.