servicio de mecanizado de 5 axis
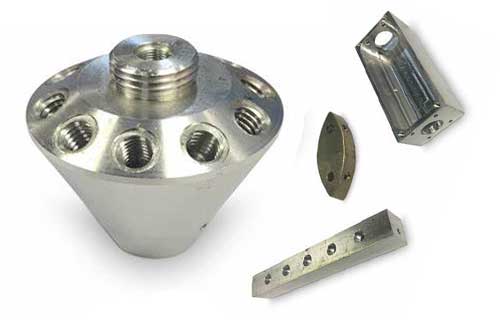
Servicio de mecanizado CNC de precisión de piezas personalizadas de 5 axis
With the use of sophisticated CNC machining technology, 5-axis machining services can concurrently cut and shape a workpiece in five separate directions. Al construir estructuras y diseños complejos, los cinco ejes de movimiento, X, Y, Z, A y B, permiten una mayor precisión, velocidad y flexibilidad. Este servicio es perfecto para producir piezas para los sectores automotriz, aeroespacial y médico. Las velocidades de producción más rápidas, la mayor precisión y la capacidad de producir formas y diseños complejos que son desafiantes o imposibles de realizar con las técnicas de mecanizado convencionales son algunas de las ventajas del mecanizado de 5 axis.
Ventajas del mecanizado CNC de 5 ejes
Una ventaja de Mecanizado CNC de 5 ejes es su capacidad para producir piezas complejas con mayor exactitud y precisión. Al cortar y dar forma a la pieza en numerosas direcciones a la vez, reduce el tiempo de producción al eliminar la necesidad de diferentes configuraciones y herramientas.
Las geometrías y formas complejas que son difíciles o imposibles de lograr con las técnicas de mecanizado convencionales también se pueden crear con Mecanizado CNC de 5 ejes. Furthermore, it lowers the possibility of mistakes and irregularities by offering more flexibility and control throughout the milling process. All things considered, 5-axis CNC machining is a very sophisticated and effective way to make items.
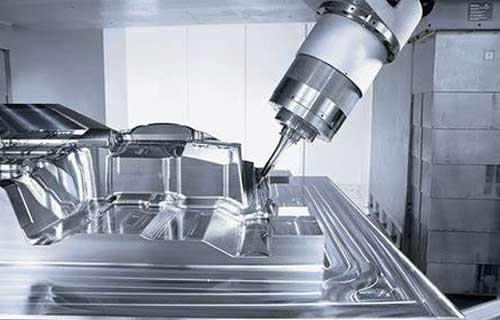
Tolerancias de mecanizado CNC de 5 ejes
Tolerancias que pueden alcanzarse con el mecanizado CNC de 5 ejes:
- Tolerancia posicional: +/- 0,0002 pulgadas
- Tolerancia angular: +/- 0,05 grados
- Surface finish: up to 16 microinches
- Tolerancia de circularidad: 0,0001 pulgadas
- Tolerancia de concentricidad: 0,0002 pulgadas
- Tolerancia de paralelismo: 0,0002 pulgadas
- Tolerancia de perpendicularidad: 0,0002 pulgadas
- Tolerancia de simetría: 0,0002 pulgadas
Factores que pueden afectar a las tolerancias en el mecanizado CNC de 5 ejes:
- Type of material being machined
- Complejidad del diseño
- Geometría y calidad de la herramienta de corte
- Machine accuracy and repeatability
- Factores ambientales, como la temperatura y la humedad
Importancia de las tolerancias en el mecanizado CNC de 5 ejes:
- Conseguir tolerancias estrechas es crucial en industrias como la aeroespacial y la médica, donde la precisión y la exactitud son de suma importancia.
- Las tolerancias garantizan que las piezas y componentes encajen y funcionen correctamente, reduciendo el riesgo de errores o fallos.
- Unas tolerancias constantes mejoran la calidad y fiabilidad generales del producto final.
Materiales para el mecanizado CNC de 5 ejes a medida
- Aluminum alloys (e.g. 6061, 7075)
- Stainless steel (e.g. 304, 316)
- Titanio alloys (e.g. Ti6Al4V)
- Níquel alloys (e.g. Inconel 718)
- Cobre alloys (e.g. brass, bronze)
- Aleaciones de magnesio (por ejemplo, AZ31B)
- Acetal (por ejemplo, Delrin)
- Nylon (por ejemplo, Nylon 6/6)
- Policarbonato (por ejemplo, Lexan)
- Acrílico (por ejemplo, plexiglás)
- PVC
- PEEK
- Polímero reforzado con fibra de carbono (CFRP)
- Polímero reforzado con fibra de vidrio (GFRP)
- Polímero reforzado con Kevlar
- Materiales compuestos de matriz cerámica (CMC)
- Madera
- Espuma
- Goma
- Cerámica
- Propiedades de los materiales, como resistencia, dureza y conductividad térmica.
- Maquinabilidad del material
- Cost and availability of the material
- Factores ambientales, como la temperatura y la humedad
- Acabado superficial deseado y tolerancias del producto final.
Acabados superficiales para el mecanizado CNC de 5 ejes
Un proceso electroquímico llamado anodizado deja una fina capa de óxido en la superficie de un material. Este procedimiento permite obtener una amplia gama de acabados, como mate, satinado y brillante. El anodizado se aplica con frecuencia en contextos protectores o decorativos.
Se trata de la superficie más lisa que puede producir el mecanizado CNC de 5 ejes. Sus características definitorias son una alta reflectividad y una rugosidad media (Ra) extremadamente baja, normalmente inferior a 0,1 micras. En aplicaciones de gama alta en las que la calidad de la superficie y la estética son cruciales, se utiliza con frecuencia este acabado superficial.
Aunque esta superficie no es tan perfecta como un acabado de espejo, tiene un valor Ra bajo: entre 0,1 y 0,4 micras de media. Se utiliza con frecuencia para fines funcionales u ornamentales y tiene un aspecto suave y cepillado.
Los valores Ra de este acabado suelen estar entre 0,4 y 1,6 micras, que es mayor que el de un acabado satinado. Tiene un aspecto más duro y se utiliza con frecuencia en aplicaciones funcionales en las que se necesita una superficie texturizada o antideslizante.
Para producir este pulido, la superficie se granalla a gran velocidad con pequeñas perlas o partículas. Se obtiene una superficie mate consistente, a menudo con un valor Ra de 3,2 micras, que es relativamente alto. Cuando se necesita una superficie texturada con fines utilitarios, se utiliza con frecuencia.
Los materiales abrasivos se utilizan en el pulido para dar a la superficie de un material un acabado liso y brillante. Una superficie mate con un valor Ra bajo puede ser tan brillante como un acabado de espejo después del pulido. Se emplean con frecuencia en aplicaciones ornamentales en las que se necesita un alto brillo o lustre.
El cepillado es el proceso de aplicar una almohadilla abrasiva o un cepillo de alambre a la superficie de un material para crear un patrón lineal texturizado. El aspecto de los acabados cepillados puede variar de liso y brillante a rugoso y terroso. Suelen utilizarse cuando se requiere una textura o un dibujo distintivos en aplicaciones decorativas.
El arenado es el proceso de aplicar aire o agua a alta presión a la superficie de un material para chorrearla con arena u otras partículas abrasivas. Este método produce una superficie mate texturada con un valor Ra comparativamente alto. En aplicaciones funcionales en las que se requiere una superficie texturizada o antideslizante, el chorro de arena se emplea con frecuencia.
Para generar una superficie resistente y protectora, el recubrimiento en polvo consiste en espolvorear un material con polvo seco y cocerlo en un horno. El recubrimiento en polvo puede tener acabados mates o brillantes, y puede aplicarse tanto a superficies prácticas como decorativas.
Aplicaciones del mecanizado en 5 ejes
El mecanizado en 5 ejes es una tecnología de fabricación muy avanzada que utiliza una máquina de control numérico por ordenador (CNC) para mover una herramienta de corte a lo largo de cinco ejes simultáneamente. El sector industrial ha experimentado una revolución gracias a esta tecnología, que permite fabricar piezas increíblemente complicadas y detalladas con rapidez y precisión. Las industrias automovilística, aeroespacial y médica son sólo algunos de los sectores en los que se aplica el mecanizado en 5 ejes.
In la industria aeroespacialEl mecanizado en 5 ejes se utiliza para fabricar piezas muy complejas, como álabes de turbinas, componentes de motores y componentes estructurales. Gracias a la posibilidad de manipular la herramienta de corte en varias direcciones, el mecanizado en 5 ejes permite fabricar piezas con tolerancias extremadamente estrechas y geometrías complejas.
In la industria médicaEl mecanizado en 5 ejes se utiliza para fabricar dispositivos médicos muy precisos y complejos, como instrumentos quirúrgicos e implantes. El mecanizado en 5 ejes es un proceso muy preciso y exacto que resulta idóneo para producir equipos médicos complejos que requieren resultados precisos y exactos.
En la industria del automóvilEl mecanizado en 5 ejes se utiliza para fabricar componentes de motor, componentes de suspensión y otras piezas que requieren gran precisión y exactitud. Las piezas de automóviles de alto rendimiento pueden fabricarse con mecanizado en 5 ejes gracias a su capacidad para producir piezas con geometrías intrincadas y tolerancias estrechas.
Una técnica de producción muy sofisticada que está revolucionando la industria manufacturera es el mecanizado en cinco ejes. En general, sus aplicaciones son diversas. Debido a la precisión y exactitud sin precedentes que proporciona el mecanizado en cinco ejes, es una tecnología clave para la fabricación de productos complejos en industrias como la automovilística, la aeroespacial y la médica.
Mecanizado simultáneo en 5 ejes o en 3+2 ejes
Simultánea Mecanizado en 5 ejes y mecanizado en 3+2 ejes son técnicas de fabricación avanzadas que se utilizan para producir piezas complejas. En el mecanizado simultáneo en 5 ejes, la herramienta de corte se desplaza por cinco ejes a la vez, lo que permite fabricar piezas con geometrías complejas y tolerancias estrechas. Esta técnica es especialmente útil para las industrias aeroespacial y médica, que requieren piezas complejas con geometrías precisas.
Por otro lado, Mecanizado en 3+2 ejes is a technique in which the cutting tool moves along three axes while the workpiece is tilted along two additional axes. This technique is ideal for producing parts with complex features on the sides of the workpiece. It is particularly useful in the production of automotive parts, mold making, and other industries that require complex geometries.
Ambos simultáneos Mecanizado en 5 ejes y mecanizado en 3+2 ejes son técnicas de fabricación muy avanzadas que se utilizan para producir piezas con gran precisión y exactitud. Son esenciales en la fabricación moderna y han revolucionado la producción de piezas complejas.
Por qué elegir nuestro servicio de mecanizado CNC de 5 ejes
Nuestra Servicio de mecanizado CNC de 5 ejes es una solución fiable y de alta calidad para producir piezas complejas e intrincadas con un alto nivel de precisión y exactitud. Hay varias razones por las que elegir nuestro servicio:
Técnicos altamente cualificados: Nuestro equipo de técnicos altamente cualificados cuenta con una amplia experiencia en el mecanizado CNC de 5 ejes y se dedica a producir piezas que cumplen o superan las expectativas del cliente.
Equipos de última generación: Utilizamos la última tecnología y equipos de mecanizado CNC de 5 ejes, lo que garantiza que podemos producir piezas con un alto nivel de precisión y exactitud.
Plazos de entrega rápidos: Nuestros procesos racionalizados y métodos de producción eficaces nos permiten ofrecer plazos de entrega rápidos sin comprometer la calidad.
Precios competitivos: Ofrecemos precios competitivos sin comprometer la calidad de nuestros servicios, garantizando que nuestros clientes reciban el mejor valor por su inversión.
Soluciones a medida: Trabajamos en estrecha colaboración con nuestros clientes para comprender sus requisitos exclusivos y ofrecerles soluciones personalizadas que satisfagan sus necesidades específicas.
En general, nuestro Servicio de mecanizado CNC de 5 ejes es una solución fiable y de alta calidad para producir piezas complejas e intrincadas. Nuestro compromiso con la calidad, la eficiencia y la satisfacción del cliente nos convierte en el socio ideal para sus necesidades de mecanizado CNC de 5 ejes.
Preguntas frecuentes sobre el mecanizado CNC de 5 ejes
El mecanizado CNC de 5 ejes es una técnica de fabricación que utiliza una máquina de control numérico por ordenador (CNC) para mover las herramientas de corte a lo largo de cinco ejes simultáneamente con el fin de producir piezas complejas y detalladas.
El mecanizado CNC de 5 ejes es un proceso de fabricación avanzado utilizado en la industria del mecanizado. CNC significa control numérico por ordenador y se refiere al método de control de máquinas herramienta mediante instrucciones de programación informática. En el mecanizado CNC de 5 ejes, la herramienta de corte puede moverse a lo largo de cinco ejes diferentes simultáneamente, lo que permite operaciones de mecanizado más complejas e intrincadas.
Traditional 3-axis CNC machines can move the tool along three linear axes (X, Y, and Z). These machines are capable of creating 3D shapes and performing various operations such as milling, drilling, and cutting, but have limitations when it comes to certain complex geometries and angles.
Por otro lado, las máquinas CNC de 5 ejes tienen dos ejes rotativos adicionales, comúnmente denominados eje A y eje B. El eje A es un eje rotativo que gira alrededor del eje X y el eje B es un eje rotativo que gira alrededor del eje Y. El eje A es un eje rotativo que gira alrededor del eje X, y el eje B es un eje rotativo que gira alrededor del eje Y. Gracias a estos movimientos giratorios, la herramienta de corte puede acercarse a la pieza desde distintos ángulos y direcciones, lo que le permite acceder a zonas de difícil acceso y crear formas más complejas con menos cambios de herramienta.
En general, el mecanizado CNC de 5 ejes es una tecnología sofisticada capaz de crear piezas complejas con gran precisión y eficacia.
El mecanizado CNC de 5 ejes se diferencia de otras técnicas de mecanizado porque permite manipular la herramienta de corte en varias direcciones simultáneamente, lo que permite producir geometrías complejas y tolerancias estrechas.
El mecanizado CNC de 5 ejes se diferencia de otras técnicas de mecanizado principalmente por su capacidad de mover la herramienta de corte a lo largo de cinco ejes diferentes simultáneamente. Analicemos las principales diferencias entre el mecanizado CNC de 5 ejes y otras técnicas de mecanizado habituales:
Número de ejes: La diferencia fundamental radica en el número de ejes controlados por la máquina. El mecanizado CNC tradicional de 3 ejes puede mover la herramienta de corte a lo largo de tres ejes lineales (X, Y y Z), mientras que el mecanizado de 4 ejes añade un eje de rotación adicional (normalmente alrededor del eje Z). El mecanizado CNC de 5 ejes, como su nombre indica, incorpora dos ejes de rotación adicionales (A y B) además de los tres ejes lineales.
Flexibilidad y complejidad: el mecanizado CNC de 5 ejes ofrece una flexibilidad y versatilidad inigualables en comparación con otras técnicas. Puede manejar geometrías y contornos muy complejos que serían difíciles o imposibles de conseguir con máquinas de 3 o 4 ejes. Esta capacidad es especialmente beneficiosa para la fabricación de piezas y componentes complejos en sectores como el aeroespacial y el médico.
Acceso a la herramienta: Las máquinas CNC de 5 ejes permiten que la herramienta de corte se acerque a la pieza de trabajo desde varios ángulos, incluidos los socavados y las paredes laterales. Este acceso sin restricciones a la herramienta permite un mecanizado eficaz de formas complejas sin necesidad de múltiples configuraciones o reposicionamiento de la pieza, lo que puede llevar mucho tiempo en otras técnicas de mecanizado.
Tiempo de configuración: La configuración de una máquina CNC de 5 ejes puede ser más compleja y requerir más tiempo que una máquina de 3 o 4 ejes debido a los ejes adicionales y a la calibración asociada. Sin embargo, el aumento del tiempo de preparación se compensa con la reducción del tiempo total de mecanizado, ya que las máquinas de 5 ejes pueden realizar varias operaciones en una sola preparación.
Precisión y exactitud: el mecanizado CNC de 5 ejes ofrece una mayor precisión y exactitud gracias a su capacidad para aproximarse a la pieza desde diferentes ángulos, lo que reduce la posibilidad de errores causados por la configuración de los dispositivos de fijación. Esto es especialmente importante para aplicaciones de alta tolerancia y piezas con requisitos dimensionales estrictos.
Cost: 5-axis CNC machines are generally more expensive than their 3-axis and 4-axis counterparts due to the added complexity and sophistication of the machine. However, the advantages it brings in terms of efficiency, reduced labor costs, and increased capabilities can make it a cost-effective choice for certain industries and applications.
En resumen, el mecanizado CNC de 5 ejes destaca por su capacidad para manejar geometrías complejas, mayor precisión y menor tiempo de preparación. Aunque puede no ser necesario para todas las tareas de mecanizado, proporciona una ventaja significativa para las industrias que requieren piezas intrincadas y precisas. Otras técnicas de mecanizado, como el mecanizado CNC de 3 y 4 ejes, siguen teniendo su lugar en la fabricación y son adecuadas para aplicaciones más sencillas y menos complejas.
Entre las ventajas del mecanizado CNC de 5 ejes se incluyen la capacidad de producir piezas complejas con un alto nivel de precisión y exactitud, la reducción del tiempo y los costes de producción y la posibilidad de trabajar con una amplia gama de materiales.
El mecanizado CNC de 5 ejes ofrece una serie de ventajas que lo convierten en la opción preferida para diversas industrias y aplicaciones. Estas son las principales ventajas del mecanizado CNC de 5 ejes:
Geometrías complejas: Las máquinas de 5 ejes pueden crear geometrías intrincadas y complejas que serían difíciles o imposibles de conseguir con el mecanizado convencional de 3 o 4 ejes. La capacidad de mover la herramienta de corte a lo largo de cinco ejes facilita el mecanizado de entalladuras, voladizos y ángulos compuestos.
Reducción del tiempo de preparación: A diferencia de las técnicas de mecanizado tradicionales que pueden requerir múltiples configuraciones para acceder a diferentes ángulos, el mecanizado CNC de 5 ejes a menudo puede completar una pieza en una sola configuración. Esto reduce el tiempo total de preparación, agilizando el proceso de fabricación y aumentando la productividad.
Mayor precisión y exactitud: El movimiento continuo y sin restricciones de la herramienta en el mecanizado de 5 ejes garantiza una mayor precisión y exactitud. La herramienta de corte puede mantener su orientación óptima durante todo el proceso de mecanizado, lo que da como resultado piezas con tolerancias más ajustadas y mejores acabados superficiales.
Mejor acabado superficial: Con la capacidad de abordar la pieza desde múltiples ángulos, el mecanizado en 5 ejes puede lograr acabados superficiales más suaves. Esto resulta especialmente ventajoso para piezas que requieren un acabado de alta calidad, como los componentes utilizados en aplicaciones aeroespaciales o médicas.
Eficacia y productividad: el mecanizado CNC de 5 ejes puede reducir considerablemente la duración de los ciclos y aumentar la eficacia gracias a su capacidad para realizar varias operaciones en una sola configuración. Minimiza la intervención manual y los cambios de herramienta, lo que agiliza la producción y reduce los plazos de entrega.
Reducción del desgaste de las herramientas: Las trayectorias continuas de las herramientas y los ángulos de corte optimizados en el mecanizado de 5 ejes ayudan a reducir el desgaste de las herramientas y a prolongar su vida útil. Esto reduce los costes de herramientas y garantiza un rendimiento constante durante periodos prolongados.
Versatilidad: Las máquinas CNC de 5 ejes pueden manipular una amplia gama de piezas y materiales, lo que las hace adecuadas para diversos sectores, como el aeroespacial, la automoción, el médico y la fabricación de moldes. La flexibilidad del mecanizado en 5 ejes permite ampliar las posibilidades de fabricación.
Libertad de diseño: Los fabricantes tienen más libertad de diseño cuando utilizan el mecanizado CNC de 5 ejes. Los ejes añadidos les permiten crear piezas innovadoras y únicas sin comprometer la fabricabilidad.
Eliminación de errores manuales: La precisión de las máquinas de 5 ejes controladas por ordenador minimiza el riesgo de errores manuales y garantiza una calidad constante de las piezas, reduciendo las tasas de rechazo y el desperdicio de material.
Rentabilidad: Aunque las máquinas CNC de 5 ejes son más caras que las de 3 o 4 ejes, sus ventajas en términos de mayor eficacia, reducción de los costes de mano de obra y mejora de la calidad de las piezas pueden suponer un ahorro de costes a largo plazo, especialmente en el caso de componentes complejos y de alta tolerancia.
En resumen, el mecanizado CNC de 5 ejes ofrece numerosas ventajas que contribuyen a mejorar la productividad, la precisión y la flexibilidad en la fabricación, por lo que es una opción ideal para las industrias que exigen componentes intrincados y complejos.
Entre las industrias que se benefician del mecanizado CNC de 5 ejes se incluyen la aeroespacial, la médica y la de automoción, entre otras.
El mecanizado CNC de 5 ejes beneficia a una amplia gama de industrias, en particular las que requieren la producción de componentes complejos y de alta precisión. Algunas de las industrias clave que se benefician del mecanizado CNC de 5 ejes son:
Industria aeroespacial: La industria aeroespacial trabaja a menudo con piezas complejas y de alta tolerancia, como álabes de turbina, impulsores y componentes de motor. El mecanizado CNC de 5 ejes permite producir estas piezas complejas con mayor eficiencia y precisión, cumpliendo los estrictos requisitos del sector.
Automotive: In the automotive sector, 5-axis CNC machining is used to manufacture complex molds, tooling, and prototypes. Additionally, it allows the production of lightweight and intricate components for performance vehicles and advanced systems.
Medicina: La industria médica se beneficia del mecanizado CNC de 5 ejes para la fabricación de instrumentos médicos de precisión, implantes ortopédicos, componentes dentales y otros dispositivos médicos complejos.
Defensa y militar: El sector de la defensa requiere a menudo la producción de piezas especializadas e intrincadas para diversas aplicaciones, incluidos los equipos aeroespaciales y militares. El mecanizado CNC de 5 ejes permite producir estos complejos componentes con gran precisión.
Mold Making: In mold making industries, 5-axis CNC machining is used to create complex molds for plastic injection molding, die casting, and other manufacturing processes. The technology allows for smoother and more efficient machining of intricate mold cavities.
Creación de prototipos y fabricación rápida: El mecanizado CNC de 5 ejes es valioso en la creación rápida de prototipos y la fabricación de bajo volumen. Permite a diseñadores e ingenieros producir rápidamente prototipos funcionales y pequeños lotes de piezas con geometrías complejas.
Marina y construcción naval: Los constructores navales utilizan el mecanizado CNC de 5 ejes para fabricar componentes intrincados para la construcción naval, como hélices, álabes de turbina y estructuras de buques.
Energía y generación de energía: La industria energética emplea el mecanizado CNC de 5 ejes para producir componentes complejos utilizados en turbinas, generadores y otros equipos de generación de energía.
Fabricación de herramientas y troqueles: En la fabricación de herramientas y troqueles, el mecanizado CNC de 5 ejes permite producir herramientas de corte y troqueles intrincados con mayor precisión y acabado superficial.
Arte y escultura: Artistas y escultores utilizan máquinas CNC de 5 ejes para crear intrincadas y detalladas esculturas y piezas de arte con diversos materiales.
En general, cualquier industria que requiera componentes de alta precisión, complejos y personalizados puede beneficiarse del mecanizado CNC de 5 ejes. Su versatilidad y capacidad para producir formas y características complejas lo convierten en una tecnología esencial en los procesos de fabricación modernos de múltiples sectores.
A wide range of materials can be used in 5-axis CNC machining, including metals, plastics, composites, and more.
5-axis CNC machining is versatile and can work with a wide range of materials, including metals, plastics, composites, and even certain types of wood. The specific materials that can be used in 5-axis CNC machining depend on the machine's capabilities, cutting tools, and the overall setup. Here are some common materials that are compatible with 5-axis CNC machining:
Metales:
- Aluminum: A popular material due to its lightweight, high strength-to-weight ratio, and good machinability.
- Acero inoxidable: Used for its corrosion resistance and mechanical properties, commonly found in medical and aerospace components.
- Titanio: Known for its high strength, low weight, and biocompatibility, used in aerospace and medical applications.
- Brass and Cobre: Often used for decorative and electrical components due to their excellent conductivity.
- Acero: Una amplia categoría que incluye varios grados adecuados para diferentes aplicaciones industriales.
Plásticos:
- Acrílico (PMMA): Se utiliza por su claridad óptica y fácil mecanización en la producción de señalización, expositores y componentes transparentes.
- ABS (acrilonitrilo butadieno estireno): Un termoplástico ampliamente utilizado con buena resistencia al impacto, que se encuentra comúnmente en automoción y bienes de consumo.
- Nylon: Conocido por su resistencia, dureza y resistencia al desgaste, se utiliza en diversos componentes mecánicos.
- PEEK (poliéter éter cetona): Termoplástico de alto rendimiento utilizado en aplicaciones aeroespaciales, médicas y de ingeniería por sus excelentes propiedades mecánicas y su resistencia a los productos químicos y al calor.
Compuestos:
- Polímero reforzado con fibra de carbono (CFRP): Material compuesto ligero y resistente utilizado en las industrias aeroespacial, automovilística y de artículos deportivos.
- Polímero reforzado con fibra de vidrio (GFRP): Ofrece buena resistencia y durabilidad y se utiliza en diversas aplicaciones estructurales.
Madera:
- Maderas duras (por ejemplo, roble, arce, nogal): Se utiliza para fabricar prototipos de madera, muebles a medida y objetos decorativos.
- Tablero de fibra de densidad media (MDF): Un compuesto de madera que se utiliza a menudo para la creación rápida de prototipos y la fabricación de patrones de herramientas.
Otros materiales:
- Espuma: Se utiliza para crear moldes, patrones y modelos arquitectónicos.
- Cera: Utilizada en procesos de fundición a la cera perdida para crear patrones para piezas metálicas.
Es importante tener en cuenta que la idoneidad específica de un material para el mecanizado CNC de 5 ejes depende de factores como la rigidez de la máquina, la potencia del husillo, las herramientas de corte y la complejidad de la pieza que se va a mecanizar. Algunos materiales pueden requerir herramientas de corte o estrategias de mecanizado especializadas para lograr resultados óptimos.
Antes de iniciar cualquier proyecto de mecanizado, es esencial consultar con un programador de CNC o un experto en mecanizado para asegurarse de que el material elegido es compatible con la máquina CNC de 5 ejes y adecuado para la aplicación deseada.
El tamaño máximo de una pieza que puede fabricarse utilizando el mecanizado CNC de 5 ejes depende del tamaño de la máquina CNC que se utilice, pero puede ir desde piezas pequeñas hasta piezas grandes y complejas.
El tamaño máximo de una pieza que puede fabricarse utilizando el mecanizado CNC de 5 ejes depende de varios factores, como las capacidades específicas de la máquina CNC, el tamaño de la zona de mecanizado y el tipo de portapiezas disponible. Normalmente, las máquinas CNC de 5 ejes están disponibles en varios tamaños para adaptarse a piezas de distintos tamaños.
Para máquinas CNC de 5 ejes más pequeñas, el tamaño máximo de la pieza puede limitarse a las siguientes dimensiones:
Recorrido del eje X: Típicamente de unas pocas pulgadas (por ejemplo, 10-12 pulgadas) a unos pocos pies (por ejemplo, 4-6 pies).
Recorrido del eje Y: Similar al eje X, oscilando entre unos centímetros y unos metros.
Recorrido del eje Z: Típicamente en el rango de unas pocas pulgadas a unos pocos pies.
Por otro lado, las máquinas CNC de 5 ejes industriales de mayor tamaño pueden manipular piezas más grandes, como:
Recorrido del eje X: De unos metros a decenas de metros.
Recorrido del eje Y: De unos metros a decenas de metros.
Recorrido del eje Z: De unos metros a unos metros.
El área de trabajo total, o el espacio en el que puede funcionar la máquina, es una consideración importante a la hora de determinar el tamaño máximo de la pieza. Algunas máquinas pueden tener mesas giratorias u otras características que permiten tamaños de pieza mayores o piezas más largas.
Es fundamental adaptar el tamaño de la pieza a las capacidades de la máquina para garantizar que la pieza pueda mecanizarse por completo dentro del espacio de trabajo disponible. En el caso de piezas muy grandes que superen la capacidad de una máquina CNC de 5 ejes específica, los fabricantes pueden optar por métodos de mecanizado alternativos o por equipos especializados de mayor tamaño.
Al planificar la producción de piezas grandes mediante mecanizado CNC de 5 ejes, se recomienda consultar con un experto en mecanizado o con un fabricante de máquinas CNC para determinar el tamaño de máquina y el área de trabajo adecuados para satisfacer los requisitos específicos del proyecto.
Con el mecanizado CNC de 5 ejes puede alcanzarse un alto nivel de precisión, con tolerancias tan ajustadas como ±0,0005 pulgadas.
El mecanizado CNC de 5 ejes es capaz de alcanzar un alto nivel de precisión, permitiendo la producción de piezas intrincadas y complejas con tolerancias estrechas. La precisión que puede alcanzarse con el mecanizado CNC de 5 ejes depende de varios factores, como el diseño y la construcción de la máquina, la calidad de las herramientas de corte, la rigidez de la configuración y la habilidad del programador y el operario del CNC.
En general, las máquinas CNC de 5 ejes pueden alcanzar tolerancias del orden de:
- +/- 0,005 mm a +/- 0,025 mm (0,0002 pulgadas a 0,001 pulgadas) para dimensiones comprendidas entre unos pocos milímetros y unos pocos centímetros.
- +/- 0,025 mm a +/- 0,1 mm (0,001 pulgadas a 0,004 pulgadas) para dimensiones mayores, desde unos pocos centímetros a varios metros.
Es importante tener en cuenta que para lograr una alta precisión en el mecanizado CNC de 5 ejes es necesario tener muy en cuenta diversos factores, como:
Calibración de la máquina: La calibración periódica de la máquina es esencial para garantizar la precisión y la repetibilidad en el proceso de mecanizado.
Herramientas de corte: El uso de herramientas de corte de alta calidad con bordes afilados y recubrimientos adecuados puede influir significativamente en la precisión del proceso de mecanizado.
Fijación y portapiezas: Una fijación rígida y estable es crucial para evitar movimientos o vibraciones durante el mecanizado, que pueden afectar a la precisión de la pieza final.
Parámetros de corte: Los parámetros de corte óptimos, como la velocidad de corte, el avance y la profundidad de corte, deben seleccionarse cuidadosamente para lograr la precisión deseada.
Estrategias de trayectoria de la herramienta: Las estrategias avanzadas de trayectoria de la herramienta y el software CAM pueden optimizar las trayectorias de corte para minimizar la desviación de la herramienta y producir acabados superficiales más suaves.
Propiedades del material: Comprender el material que se está mecanizando y su comportamiento bajo las fuerzas de corte es esencial para controlar la precisión dimensional.
Alcanzar una alta precisión en el mecanizado CNC de 5 ejes permite producir piezas utilizadas en aplicaciones críticas, como la industria aeroespacial, los dispositivos médicos y los componentes de ingeniería de precisión. Sin embargo, es importante tener en cuenta que conseguir tolerancias más ajustadas puede aumentar el tiempo y el coste del mecanizado, ya que requiere un control más cuidadoso y preciso de todo el proceso.
El coste del mecanizado CNC de 5 ejes depende de varios factores, como la complejidad de la pieza, el tipo de material utilizado y la cantidad producida, pero suele ser competitivo con otras técnicas de mecanizado.
El coste del mecanizado CNC de 5 ejes en comparación con otras técnicas de mecanizado puede variar significativamente y está influido por varios factores. Aunque el mecanizado CNC de 5 ejes ofrece numerosas ventajas, suele tener un coste inicial más elevado en comparación con el mecanizado tradicional de 3 o 4 ejes. A continuación se indican algunos factores clave que pueden influir en el coste del mecanizado CNC de 5 ejes:
Coste de la máquina: Las máquinas CNC de 5 ejes son máquinas más complejas y sofisticadas, a menudo con ejes y capacidades adicionales. En consecuencia, su adquisición y mantenimiento suelen ser más caros que los de las máquinas de 3 o 4 ejes.
Coste del utillaje: el mecanizado en 5 ejes puede requerir utillaje especializado, incluidas fresas rotativas y otros accesorios, que pueden ser más costosos que el utillaje estándar utilizado en el mecanizado tradicional.
Tiempo de preparación: Aunque el mecanizado en 5 ejes puede reducir el tiempo de preparación al permitir múltiples operaciones en una sola preparación, la preparación inicial para el mecanizado en 5 ejes puede ser más complicada y requerir más tiempo en comparación con técnicas de mecanizado más sencillas.
Complejidad de la programación: La programación para el mecanizado CNC de 5 ejes puede ser más compleja y puede requerir programadores cualificados, lo que podría conllevar mayores costes de programación.
Complejidad de la pieza: Si el diseño de la pieza requiere el uso del mecanizado en 5 ejes para conseguir características o geometrías específicas, el coste puede estar justificado por la capacidad de producir la pieza de forma eficaz y precisa.
Volumen de producción: Para la producción de grandes volúmenes de piezas relativamente sencillas, el mecanizado tradicional en 3 o 4 ejes puede resultar más rentable. El mecanizado CNC de 5 ejes suele ser más ventajoso para la producción de piezas complejas o de bajo volumen.
Coste del material: La elección del material puede repercutir en el coste global, pero este factor es aplicable tanto a las técnicas de mecanizado de 5 ejes como a otras.
Es importante tener en cuenta que la rentabilidad del mecanizado CNC de 5 ejes depende de los requisitos específicos del proyecto y de las ventajas que proporcione. Aunque el mecanizado en 5 ejes puede tener un coste inicial más elevado, a menudo puede suponer un ahorro de costes a largo plazo debido al aumento de la eficacia, la reducción de los costes de mano de obra y la mejora de la calidad de las piezas. Además, la capacidad de producir piezas complejas en una sola configuración puede reducir el tiempo total de producción y aumentar el rendimiento.
En última instancia, la decisión de utilizar el mecanizado CNC de 5 ejes u otras técnicas de mecanizado depende de la complejidad de las piezas, el volumen de producción, las consideraciones presupuestarias y el nivel deseado de precisión y calidad. Consultar con profesionales del mecanizado experimentados y analizar los requisitos específicos del proyecto puede ayudar a determinar el enfoque más rentable para una aplicación determinada.
El tiempo de producción de piezas mediante mecanizado CNC de 5 ejes depende de la complejidad de la pieza, el tipo de material utilizado y la cantidad producida, pero suele ser más rápido que otras técnicas de mecanizado.
El tiempo que se tarda en producir piezas utilizando el mecanizado CNC de 5 ejes puede variar significativamente en función de diversos factores, como la complejidad de la pieza, el material que se está mecanizando, la estrategia de mecanizado, las capacidades de la máquina y el nivel de precisión deseado. He aquí algunos factores clave que influyen en el tiempo de producción:
Complejidad de la pieza: Las piezas con geometrías intrincadas y características complejas suelen tardar más en mecanizarse que las piezas más sencillas. El mecanizado CNC de 5 ejes destaca en la producción eficiente de formas complejas, pero la complejidad del diseño de la pieza puede influir en el tiempo total de producción.
Tipo de material: Los distintos materiales tienen características de mecanización diferentes. Algunos materiales, como el aluminio y los plásticos, suelen ser más fáciles de mecanizar y pueden requerir menos tiempo en comparación con materiales más duros como el titanio o el acero inoxidable.
Selección de herramientas y parámetros de corte: La elección de las herramientas de corte y los parámetros de corte, como la velocidad de corte y el avance, pueden afectar significativamente al tiempo de mecanizado. La selección adecuada de la herramienta y la optimización de los parámetros de corte pueden reducir los tiempos de ciclo.
Estrategia de mecanizado: La elección de la estrategia de mecanizado, como las pasadas de desbaste y acabado, puede afectar al tiempo que se tarda en producir la pieza. El software CAM avanzado puede optimizar las trayectorias de las herramientas para minimizar el tiempo de mecanizado.
Capacidad de la máquina: Las capacidades específicas de la máquina CNC de 5 ejes, incluidas la velocidad del husillo, la aceleración y la rigidez, pueden influir en el tiempo de mecanizado. Las máquinas más potentes y rígidas suelen alcanzar mayores velocidades de arranque de material, lo que reduce los tiempos de ciclo.
Volumen de producción: El volumen de producción de piezas puede influir en el tiempo total. Producir varias piezas en una sola configuración puede ahorrar más tiempo que producirlas individualmente.
Tiempo de preparación: El tiempo de preparación inicial para el mecanizado CNC de 5 ejes puede ser mayor que el del mecanizado tradicional debido a la complejidad de la máquina y a la necesidad de una calibración precisa. Sin embargo, una vez configuradas, las máquinas de 5 ejes pueden reducir la necesidad de reposicionamiento y cambios de herramienta, lo que puede ahorrar tiempo en el mecanizado de varias caras.
Es difícil proporcionar una estimación exacta del tiempo de producción sin detalles específicos sobre la pieza y el proceso de mecanizado. En algunos casos, el mecanizado CNC de 5 ejes puede reducir significativamente el tiempo de producción en comparación con otras técnicas de mecanizado, especialmente para piezas complejas que requerirían múltiples configuraciones en el mecanizado tradicional.
Para determinar el tiempo de producción previsto, lo mejor es consultar con programadores CNC y maquinistas experimentados que puedan analizar el diseño de la pieza, el material y los requisitos de mecanizado para proporcionar estimaciones de tiempo precisas. Además, el software CAM moderno puede simular el proceso de mecanizado y proporcionar tiempos de ciclo estimados para una mejor planificación y optimización.
Las medidas de control de calidad, como la inspección y las pruebas, se utilizan para garantizar la calidad de las piezas producidas mediante mecanizado CNC de 5 ejes.
Garantizar la calidad de las piezas producidas mediante mecanizado CNC de 5 ejes implica una combinación de planificación cuidadosa, configuración adecuada de la máquina, programación eficaz e inspección minuciosa. A continuación se indican algunos pasos clave y las mejores prácticas para garantizar la calidad de las piezas mecanizadas:
Revisión del diseño: Comience revisando el diseño de la pieza para identificar posibles retos y características críticas que requieran un mecanizado preciso. Trabaje con el equipo de diseño para garantizar que el diseño se puede fabricar y es adecuado para el mecanizado CNC de 5 ejes.
Selección de materiales: Elegir los materiales adecuados con las propiedades mecánicas requeridas para la aplicación prevista. Asegúrese de que el material seleccionado es compatible con la máquina CNC de 5 ejes y las herramientas de corte utilizadas.
Calibración de la máquina: Calibre regularmente la máquina CNC de 5 ejes para mantener su precisión y repetibilidad. Asegúrese de que todos los ejes están correctamente alineados y calibrados para evitar errores en el mecanizado.
Herramientas de corte y optimización de la trayectoria de la herramienta: Seleccionar herramientas de corte de alta calidad que sean adecuadas para el material y la geometría de la pieza. Optimice las trayectorias de la herramienta mediante software CAM avanzado para reducir las fuerzas de corte, minimizar la desviación de la herramienta y lograr el acabado superficial deseado.
Sujeción y fijación: Utilice técnicas de sujeción de piezas y dispositivos de fijación adecuados para sujetar firmemente la pieza durante el mecanizado. Una configuración rígida minimiza las vibraciones y garantiza unos resultados de mecanizado uniformes.
Programación y simulación: Programe minuciosamente la máquina CNC utilizando un software CAD/CAM preciso. Utilice herramientas de simulación para verificar las trayectorias de la herramienta e identificar posibles colisiones o errores antes de ejecutar el proceso de mecanizado real.
Inspección y control de calidad: Realice inspecciones periódicas durante el proceso para verificar las dimensiones y características de la pieza mecanizada. Utilice instrumentos de medición de precisión como calibres, micrómetros y MMC (máquina de medición por coordenadas) para realizar mediciones precisas.
Acabado superficial y desbarbado: Preste atención al acabado superficial de la pieza mecanizada. Desbarbe y elimine correctamente los bordes afilados para cumplir los estándares de calidad exigidos.
Documentación del proceso: Mantener registros detallados del proceso de mecanizado, incluidos los parámetros de configuración, la información sobre las herramientas y los resultados de las inspecciones. Esta documentación ayuda a la trazabilidad y facilita las acciones correctivas en caso necesario.
Mejora continua: Supervisar y analizar continuamente el proceso de mecanizado para identificar áreas de mejora. Aplique medidas correctivas y perfeccione los procesos para mejorar la calidad y la productividad generales.
Formación de los operarios: Asegúrese de que los operarios de la máquina CNC están bien formados y tienen experiencia en el mecanizado de 5 ejes. Los operarios cualificados pueden responder a los retos con eficacia y realizar los ajustes necesarios durante el proceso de mecanizado.
Mediante la aplicación de estos pasos y la adhesión a las mejores prácticas, los fabricantes pueden garantizar la calidad constante de las piezas producidas utilizando el mecanizado CNC de 5 ejes. Hacer hincapié en el control de calidad a lo largo de todo el proceso de producción ayuda a entregar piezas de precisión que cumplen o superan las expectativas del cliente.
El mecanizado simultáneo de 5 ejes y el mecanizado de 3+2 ejes son dos técnicas diferentes utilizadas en el mecanizado CNC de 5 ejes. El mecanizado simultáneo de 5 ejes implica que la herramienta de corte se desplaza a lo largo de cinco ejes simultáneamente, mientras que el mecanizado de 3+2 ejes implica que la herramienta de corte se desplaza a lo largo de tres ejes mientras que la pieza se inclina a lo largo de dos ejes adicionales.
El mecanizado simultáneo de 5 ejes y el mecanizado de 3+2 ejes son dos estrategias diferentes utilizadas en el mecanizado CNC de 5 ejes, cada una con sus propias ventajas y aplicaciones. Analicemos las principales diferencias entre estas dos técnicas de mecanizado:
Mecanizado simultáneo en 5 ejes:
- En el mecanizado simultáneo de 5 ejes, la herramienta de corte puede moverse a lo largo de los cinco ejes (X, Y, Z, A y B) simultáneamente durante el proceso de mecanizado.
- Esto significa que la herramienta puede acercarse a la pieza de trabajo desde cualquier ángulo y orientación, lo que permite trayectorias continuas y suaves, especialmente al mecanizar geometrías 3D complejas y superficies esculpidas.
- El mecanizado simultáneo en 5 ejes es ideal para piezas con curvas intrincadas, socavados y ángulos compuestos, ya que puede mecanizar eficazmente estas características sin necesidad de configuraciones múltiples ni de reposicionar la pieza.
- La capacidad de mecanizar piezas complejas en una sola configuración mejora la precisión y reduce los tiempos de ciclo, lo que la hace idónea para sectores como el aeroespacial, la automoción y el médico, donde se requieren componentes de alta precisión.
Mecanizado en 3+2 ejes:
- El mecanizado de 3+2 ejes, también conocido como mecanizado posicional de 5 ejes, es una técnica en la que la herramienta de corte se limita a tres ejes lineales (X, Y y Z) para el movimiento de corte principal, mientras que los dos ejes de rotación restantes (A y B) se bloquean o fijan en ángulos específicos.
- La herramienta se reposiciona y se bloquea en una nueva orientación en cada paso o "índice" antes de que comience el proceso de corte, lo que permite mecanizar la pieza desde distintas direcciones pero sin mover todos los ejes simultáneamente durante el corte.
- Aunque el mecanizado de 3+2 ejes no puede seguir trayectorias de herramienta complejas como el mecanizado simultáneo de 5 ejes, permite unas condiciones de corte más estables, ya que la herramienta sólo corta a lo largo de tres ejes lineales a la vez.
- El mecanizado en 3+2 ejes es adecuado para piezas con características a las que se puede acceder desde ángulos específicos sin necesidad de movimientos complejos de la herramienta. Suele utilizarse para operaciones de desbaste, acabado y secundarias en piezas que no requieren un movimiento simultáneo completo de 5 ejes.
- Esta técnica es popular para mecanizar piezas complejas manteniendo un mejor control y rigidez de la herramienta en comparación con el mecanizado tradicional en 3 ejes.
En resumen, el mecanizado simultáneo de 5 ejes y el mecanizado de 3+2 ejes son dos enfoques diferentes utilizados en el mecanizado CNC de 5 ejes. El mecanizado simultáneo de 5 ejes permite trayectorias de herramienta continuas y complejas, por lo que es ideal para piezas intrincadas, mientras que el mecanizado de 3+2 ejes proporciona más estabilidad y control para piezas que pueden mecanizarse desde orientaciones específicas sin necesidad de un movimiento simultáneo completo de 5 ejes. La elección entre estas técnicas depende de los requisitos específicos de la pieza que se va a mecanizar y del nivel deseado de complejidad y precisión.
Sí, el mecanizado CNC de 5 ejes puede utilizarse para la creación de prototipos y pequeñas series de producción, así como para series de producción a gran escala.
El mecanizado CNC de 5 ejes puede utilizarse tanto para la creación de prototipos como para pequeñas series de producción. Aunque las máquinas CNC de 5 ejes suelen asociarse a la fabricación compleja y de gama alta, también son lo suficientemente versátiles como para adaptarse a la producción de bajo volumen y la creación rápida de prototipos.
A continuación se explica cómo el mecanizado CNC de 5 ejes resulta beneficioso para la creación de prototipos y pequeñas series de producción:
Creación rápida de prototipos: El mecanizado CNC de 5 ejes permite la producción rápida de prototipos funcionales con geometrías complejas. La capacidad de mecanizar piezas desde múltiples ángulos y orientaciones en una sola configuración facilita la creación de diseños intrincados sin necesidad de herramientas especializadas ni múltiples operaciones.
Reducción del tiempo de preparación: el mecanizado en 5 ejes puede reducir el tiempo de preparación en comparación con los métodos de mecanizado tradicionales. La capacidad de mecanizar piezas complejas en una sola configuración elimina la necesidad de reposicionar la pieza y reduce el tiempo dedicado a los cambios de utillaje.
Flexibilidad e iteración: En la creación de prototipos, los cambios de diseño y las iteraciones son habituales. El mecanizado CNC de 5 ejes permite ajustar fácilmente el programa de mecanizado, lo que permite probar y modificar rápidamente el diseño.
Plazos de entrega más cortos: La eficacia del mecanizado CNC de 5 ejes puede reducir los plazos de entrega tanto de prototipos como de pequeñas series de producción. Esto resulta especialmente beneficioso para lanzar productos al mercado con rapidez y cumplir plazos de entrega ajustados.
Alta precisión: el mecanizado CNC de 5 ejes garantiza una alta precisión y exactitud, lo que resulta crucial para la creación de prototipos y pequeñas series de producción que requieren piezas con tolerancias estrechas y detalles intrincados.
Versatilidad de materiales: las máquinas CNC de 5 ejes pueden trabajar con una amplia gama de materiales, incluidos metales, plásticos, materiales compuestos y madera, lo que proporciona flexibilidad en la selección de materiales para prototipos y series de producción.
Rentabilidad: Aunque el mecanizado CNC de 5 ejes puede tener unos costes de configuración iniciales más elevados, puede ser rentable para la producción de bajo volumen, ya que reduce el tiempo de mano de obra y las intervenciones manuales en comparación con los métodos de mecanizado tradicionales.
Características multieje: Para piezas que requieren características complejas, como socavados o ángulos compuestos, el mecanizado CNC de 5 ejes suele ser el método más eficaz y preciso para la producción.
Como en cualquier proceso de fabricación, es esencial tener en cuenta factores como la complejidad de la pieza, la elección del material y las limitaciones presupuestarias cuando se decide utilizar el mecanizado CNC de 5 ejes para la creación de prototipos y pequeñas series de producción. Trabajar con un proveedor de servicios de mecanizado CNC experimentado puede ayudar a garantizar que se elige la técnica de mecanizado más adecuada para satisfacer los requisitos específicos del proyecto.
El mecanizado en 5 ejes tiene muchas ventajas que lo convierten en la mejor opción para una gran variedad de industrias y aplicaciones. Estas son algunas de las principales razones para utilizar el mecanizado en 5 ejes:
Geometrías complejas: El mecanizado en 5 ejes permite fabricar piezas con geometrías complejas que son difíciles o imposibles de conseguir con el mecanizado tradicional en 3 o 4 ejes. Los ejes adicionales permiten a la herramienta de corte acceder a múltiples ángulos y orientaciones, lo que facilita el mecanizado de socavados, voladizos y ángulos compuestos.
Eficacia de una sola configuración: el mecanizado en 5 ejes reduce la necesidad de múltiples configuraciones, ya que puede mecanizar piezas desde varios lados en una sola configuración. Esto mejora significativamente la eficiencia, reduce el tiempo de procesamiento y minimiza la posibilidad de introducir errores durante el reposicionamiento de la pieza.
Precisión y exactitud: Las trayectorias continuas de la herramienta en el mecanizado de cinco ejes permiten una mayor precisión y exactitud. La herramienta de corte mantiene su orientación óptima, lo que se traduce en tolerancias más ajustadas y un mejor acabado superficial de las piezas mecanizadas.
Menor desgaste de la herramienta: El mecanizado en 5 ejes permite optimizar las trayectorias de las herramientas, lo que minimiza el acoplamiento innecesario de las herramientas y reduce su desgaste. Esto se traduce en una mayor vida útil de la herramienta y menores costes.
Versatilidad: las máquinas CNC de 5 ejes pueden procesar una amplia gama de materiales, incluidos metales, plásticos, materiales compuestos y madera, lo que las hace adecuadas para una gran variedad de industrias y aplicaciones.
Mejor acabado superficial: La posibilidad de acercarse a la pieza desde diferentes ángulos y direcciones da como resultado un acabado superficial más liso en la pieza mecanizada.
Reducción del tiempo de producción: el mecanizado en 5 ejes puede reducir el tiempo total de producción al combinar varias operaciones de mecanizado en una única configuración. Esto no solo ahorra tiempo, sino que también aumenta el rendimiento y la productividad.
Libertad de diseño: Los fabricantes tienen más libertad de diseño cuando utilizan el mecanizado en 5 ejes, ya que puede producir piezas con características complejas sin comprometer la fabricabilidad.
Rentabilidad en la producción de lotes pequeños: Aunque las máquinas de 5 ejes tienen un coste inicial más elevado, resultan rentables en la producción de lotes pequeños gracias a la reducción del tiempo de mano de obra y al aumento de la eficiencia.
Trayectorias de herramienta complejas: el mecanizado en 5 ejes permite realizar trayectorias de herramienta complejas que pueden optimizar la eliminación de material, mejorar el acabado superficial y reducir el tiempo de mecanizado, lo que la convierte en una tecnología valiosa para piezas con geometrías difíciles.
En general, se opta por el mecanizado en 5 ejes por su capacidad para producir piezas complejas con gran precisión, eficacia y versatilidad. Sus ventajas la convierten en una tecnología importante para industrias como la aeroespacial, la automovilística, la médica y la de fabricación de moldes, que requieren componentes complejos y precisos.