Servicio de torneado CNC
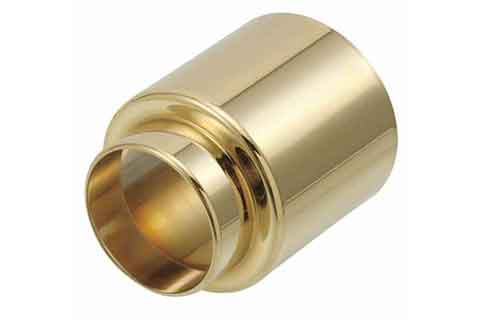
Servicio de torneado CNC de piezas de precisión a medida
Imagine you have a project on hand that requires precision CNC turning of parts, and time is tight with a limited budget. At this moment, Mold7 is like your personal assistant, always on standby. We have a vast network of over 11000 stores, including experts equipped with CNC lathes and turning centers. This means that no matter how specific your needs are, we can quickly match the most suitable resources. When it comes to price and delivery time, we are equally confident. With a wide supplier network and efficient operational model, Mold7 is able to provide the most competitive conditions in the market. From rapid prototyping to mass production, we are able to respond flexibly and ensure high-quality output. Do you want to give it a try? Just tell us your needs, and leave the rest to Mold7. Let's work together to turn your creativity into reality, efficiently and hassle free!
¿Qué es el servicio de torneado CNC?
Fundamentos de los tornos CNC
A CNC lathe machine, also called live tooling lathes, is ideal for cutting any symmetrical cylindrical or spherical parts. Characteristically, a lathe spins a workpiece on a vertical or horizontal axis, while a fixed shaping instrument moves around it on a more or less linear path. The act of cutting a workpiece on a CNC lathe is called turning.
Cómo funciona el torneado CNC
CNC lathes use a subtractive method to create the desired shape. With the G-Code created, a blank bar of stock material is loaded into the chuck of the lathe's spindle. The chuck holds the workpiece in place while the spindle spins. When the spindle is up to speed, a stationary cutting tool is brought into contact with the workpiece to remove material until the desired geometry is achieved.
Hay muchas operaciones que pueden realizarse en un torno de herramientas motorizado, como el refrentado, el roscado, el moleteado, el taladrado, el mandrinado, el escariado y el torneado cónico. Las distintas operaciones requieren cambios de herramienta y pueden aumentar el coste y el tiempo de preparación.
Una vez completadas todas las operaciones de mecanizado, la pieza se corta del material para su posterior procesamiento. A continuación, el torno CNC está listo para repetir la operación sin apenas tiempo de preparación.
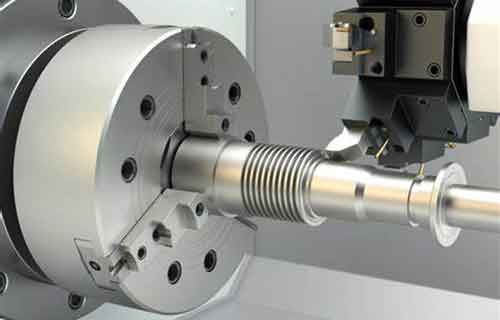
Materiales de torneado CNC
Latón C360,
Latón 260,
C932 M07 Cojinete Bronce
ABS,
Acetal [Delrin],
Acrílico,
G-10 Garolita,
Nylon 6/6,
PEEK,
Policarbonato,
PTFE [Teflón],
Polipropileno,
Polietileno de peso molecular ultra alto
Alloy Acero 4130,
Alloy Acero 4140,
ASTM A36,
Acero inoxidable 15-5,
Acero inoxidable 17-4,
Acero inoxidable 18-8,
Acero inoxidable 303,
Acero inoxidable 304,
Acero inoxidable 316/316L,
Acero inoxidable 416,
Acero inoxidable 420,
Acero 1018,
Acero A36
Cinc Sheet Alloy 500
CNC Turning Tolearances
Acabados superficiales de torneado CNC
The finish option with the quickest turnaround. Parts are left with visible tool marks and potentially sharp edges and burrs, which can be removed upon request. Surface finish is comparable to 125 uin Ra finish.
Se trata de un proceso en el que se pulveriza pintura en polvo sobre una pieza que luego se cuece en un horno. De este modo se crea una capa fuerte y resistente al desgaste y la corrosión que es más duradera que los métodos de pintura estándar. Existe una amplia variedad de colores para crear la estética deseada.
Ventajas del servicio de torneado CNC
CNC lathes, like CNC milling machines, can easily achieve high repeatability settings, which makes them perform well in both rapid prototyping and mass production. Multi axis CNC turning centers and Swiss type lathes can complete multiple machining operations on one machine, which is undoubtedly an economical and efficient choice for complex geometric parts, avoiding the hassle of multiple machines or tool changes that traditional CNC milling machines may require.
CNC turning service is a process of producing precise and complex parts from metal or plastic materials using computer-controlled machines. CNC turning services have many advantages, such as:
-Puede crear piezas de alta precisión y calidad, reduciendo la necesidad de ajustes o correcciones manuales.
-Puede manejar la producción a gran escala, ahorrando tiempo y dinero.
-Se adapta a diferentes tipos de materiales, formas y tamaños, proporcionando más flexibilidad y versatilidad.
-Puede utilizar software y herramientas avanzadas para diseñar y optimizar piezas, mejorar el rendimiento y la funcionalidad.
En nuestra empresa, contamos con la experiencia y los conocimientos necesarios para ofrecer los mejores servicios de torneado CNC. Contamos con un equipo técnico cualificado y bien formado que puede manejar las máquinas y el software CNC más recientes. Nuestro sistema de control de calidad garantiza que cada pieza cumpla sus especificaciones y normas. Nuestro servicio de atención al cliente escucha sus necesidades y le ofrece soluciones personalizadas. Póngase en contacto con nosotros inmediatamente y permítanos mostrarle las ventajas de los servicios de torneado CNC.
Imagine if you need to mass produce a complex metal part, a traditional lathe may require multiple steps and multiple setups to complete. However, with our CNC turning services, all of this can be done on one machine, greatly saving time and costs. And, thanks to our high precision and quality standards, you can rest assured that the final product will fully meet your expectations.
¿Por qué no prueba nuestro servicio de torneado CNC? Tanto si necesita prototipos rápidos como producción en serie, podemos ofrecerle soluciones que satisfagan sus necesidades. Póngase en contacto con nosotros y creemos juntos productos excelentes.
Preguntas frecuentes sobre torneado CNC
La velocidad de corte afecta a la velocidad a la que se elimina el material y puede influir en la calidad y precisión de la pieza acabada.
La velocidad de corte es uno de los parámetros más importantes en el torneado CNC. Afecta a la calidad, la precisión y la eficacia del proceso de mecanizado. La velocidad de corte es la velocidad lineal de la herramienta de corte con respecto a la superficie de la pieza. Suele medirse en metros por minuto (m/min) o pies por minuto (ft/min).
Como proveedor de servicios de torneado CNC con años de experiencia y conocimientos, sabemos elegir la velocidad de corte óptima para diferentes materiales, herramientas y geometrías. Utilizamos software y equipos avanzados para supervisar y controlar la velocidad de corte durante el proceso de mecanizado. También ajustamos la velocidad de corte en función de la información recibida de los sensores, el desgaste de la herramienta y los requisitos de acabado superficial.
Seleccionando la velocidad de corte adecuada, podemos conseguir resultados de torneado CNC de alta calidad con el mínimo desperdicio y coste. También podemos reducir la generación de calor, el desgaste de la herramienta y las vibraciones que pueden afectar al rendimiento y la precisión del mecanizado. La velocidad de corte es un factor clave que determina la calidad y eficacia de nuestro servicio de torneado CNC.
El avance se refiere a la velocidad a la que la herramienta de corte se desplaza por el material y puede influir en la calidad y precisión de la pieza acabada.
El avance es uno de los parámetros más importantes en el torneado CNC, ya que afecta a la calidad, precisión y eficacia del proceso de mecanizado. El avance es la velocidad a la que la herramienta de corte se desplaza a lo largo de la pieza, medida en milímetros por revolución (mm/rev) o pulgadas por revolución (ipr).
Como proveedor de servicios de torneado CNC con años de experiencia y conocimientos, sabemos cómo elegir el avance óptimo para distintos materiales, formas y tamaños de piezas. Utilizamos software y equipos avanzados para calcular y controlar el avance, teniendo en cuenta factores como la geometría de la herramienta, la profundidad de corte, la velocidad del husillo, el acabado superficial y la formación de virutas.
Al seleccionar la velocidad de avance adecuada, podemos garantizar que nuestro servicio de torneado CNC proporcione productos de alta calidad que cumplan o superen las expectativas de nuestros clientes. También podemos reducir el desgaste de las herramientas, minimizar los residuos y los desechos, y mejorar la productividad y la rentabilidad. Siempre estamos dispuestos a compartir nuestros conocimientos y habilidades con nuestros clientes, y a ayudarles a alcanzar sus objetivos con nuestro servicio de torneado CNC.
La velocidad del husillo determina la velocidad de rotación de la pieza y puede influir en la calidad y precisión de la pieza acabada.
En el torneado CNC, la velocidad del husillo desempeña un papel crucial a la hora de determinar el rendimiento de corte, el acabado superficial, la vida útil de la herramienta y la eficacia general del mecanizado. La velocidad del husillo se refiere a la velocidad de rotación del husillo del torno, que sujeta la pieza y la hace girar durante el proceso de torneado. A continuación se explica cómo influye la velocidad del husillo en el torneado CNC:
1. Velocidad de corte: La velocidad del cabezal influye directamente en la velocidad de corte de la herramienta al interactuar con la pieza. La velocidad de corte es la velocidad relativa entre el filo de la herramienta de corte y la superficie de la pieza. Una selección adecuada de la velocidad del cabezal garantiza que la velocidad de corte se encuentre dentro de un rango óptimo, lo que permite una eliminación eficaz del material y reduce el riesgo de desgaste de la herramienta.
2. Acabado superficial: La velocidad del husillo afecta al acabado superficial de la pieza mecanizada. Las velocidades de husillo más altas suelen dar lugar a un acabado superficial más suave porque los filos de corte de la herramienta engranan en la pieza a mayor velocidad, lo que reduce el grosor de la viruta y la rugosidad superficial.
3. Duración de la herramienta: La elección de la velocidad del husillo tiene un impacto significativo en la vida de la herramienta. Utilizar la herramienta a velocidades excesivamente altas puede provocar un desgaste acelerado y reducir su vida útil. Por otro lado, una velocidad de husillo demasiado baja puede hacer que los filos de corte rocen el material en lugar de cortarlo eficazmente, lo que provocaría un fallo prematuro de la herramienta.
4. Control de viruta: La selección adecuada de la velocidad del husillo ayuda a conseguir un mejor control de la viruta durante el torneado. Un proceso equilibrado de formación y evacuación de virutas reduce las posibilidades de atasco de virutas, que pueden causar problemas de mecanizado y dañar la pieza o la herramienta.
5. Velocidad de arranque de material: La velocidad del husillo, en combinación con la velocidad de avance (la velocidad a la que la herramienta de corte avanza en la pieza de trabajo), determina la tasa de eliminación de material. Una selección óptima de la velocidad del husillo garantiza que el material se elimine de forma eficaz sin causar un desgaste excesivo de la herramienta ni comprometer el acabado superficial.
6. Eficiencia de mecanizado: La velocidad correcta del husillo ayuda a conseguir una eficacia de mecanizado óptima. Garantiza que el proceso de corte no sea ni demasiado lento, con la consiguiente pérdida de tiempo, ni demasiado rápido, con el riesgo de dañar la herramienta. Una velocidad de husillo bien elegida contribuye a maximizar la productividad manteniendo la calidad.
7. Selección de la herramienta: Diferentes herramientas de corte y materiales requieren velocidades de husillo específicas para un rendimiento óptimo. Elegir la velocidad de husillo adecuada en función del material y el tipo de herramienta es crucial para lograr los resultados de mecanizado deseados.
Los tornos CNC permiten ajustar fácilmente la velocidad del husillo, ya sea manualmente o mediante comandos programados, en función de los requisitos específicos de cada operación de mecanizado. Los maquinistas y programadores deben considerar cuidadosamente las propiedades del material, las herramientas y los resultados deseados para seleccionar la velocidad de husillo más adecuada para cada tarea de torneado. Una correcta comprensión y utilización de la velocidad del cabezal puede conducir a operaciones de torneado CNC eficientes, precisas y rentables.
El refrigerante ayuda a lubricar y enfriar la herramienta de corte, lo que puede mejorar la calidad y la precisión de la pieza acabada.
El refrigerante desempeña un papel fundamental en el torneado CNC y otros procesos de mecanizado. Se refiere a un fluido lubricante y refrigerante utilizado durante la operación de corte. El refrigerante se aplica normalmente a la zona de corte para mejorar el rendimiento del mecanizado, prolongar la vida útil de la herramienta y mejorar la eficacia general del proceso de torneado CNC. Estas son las funciones clave del refrigerante en el torneado CNC:
1. Disipación del calor: Una de las principales funciones del refrigerante es disipar el calor generado durante el proceso de corte. A medida que la herramienta de corte interactúa con la pieza de trabajo, la fricción y las fuerzas de corte generan calor en la interfaz herramienta-pieza de trabajo. Un calor excesivo puede provocar el desgaste de la herramienta, su rotura prematura y posibles daños en la pieza de trabajo. El refrigerante ayuda a regular la temperatura, manteniéndola dentro de límites aceptables y preservando la integridad de la herramienta de corte.
2. Lubricación: El refrigerante actúa como lubricante entre la herramienta de corte y la pieza. Esto reduce la fricción, minimizando el desgaste de la herramienta de corte. Una lubricación adecuada también mejora el flujo de virutas, lo que ayuda a evacuarlas de la zona de corte, evitando que se atasquen y mejorando la eficacia del mecanizado.
3. Evacuación de virutas: El refrigerante ayuda a evacuar eficazmente las virutas fuera de la zona de corte. Transporta las virutas lejos de la zona de corte y fuera de la máquina, evitando el recorte de virutas y minimizando el riesgo de daños en la pieza o la herramienta.
4. Acabado superficial: El uso de refrigerante puede mejorar el acabado superficial de la pieza mecanizada. Al reducir la fricción y el calor, el refrigerante ayuda a conseguir acabados superficiales más suaves y precisos en la pieza.
5. Extensión de la vida útil de la herramienta: El refrigerante desempeña un papel importante en la prolongación de la vida útil de las herramientas de corte. Al reducir el calor y la fricción, el refrigerante minimiza el desgaste y el astillado de la herramienta, lo que prolonga su vida útil y reduce los costes de sustitución.
6. Precisión de mecanizado: El efecto refrigerante del refrigerante ayuda a mantener la precisión dimensional de la pieza de trabajo. Al controlar la temperatura, se minimizan la expansión y la contracción de la pieza de trabajo, lo que se traduce en un mecanizado más uniforme y preciso.
7. 7. Compatibilidad de materiales: Algunos materiales son propensos a endurecerse por deformación o a generar un calor excesivo durante el mecanizado. La selección del refrigerante puede adaptarse al material que se está mecanizando, lo que ayuda a optimizar el proceso de mecanizado para materiales específicos.
8. Gestión de virutas: El refrigerante ayuda a gestionar las virutas generadas durante el proceso de torneado. Una gestión eficaz de las virutas evita interferencias con el proceso de corte y garantiza un entorno de trabajo más limpio.
9. Rendimiento de la herramienta: Para determinadas operaciones de mecanizado avanzado, como el mecanizado a alta velocidad, el uso de refrigerante se convierte en algo esencial. Ayuda a mejorar el rendimiento general y la productividad del proceso de mecanizado.
El tipo específico de refrigerante utilizado en el torneado CNC (por ejemplo, a base de aceite, a base de agua, emulsiones) puede variar en función del material que se esté mecanizando, el proceso de corte y otras consideraciones. La aplicación, el mantenimiento y la eliminación adecuados del refrigerante son cruciales para lograr resultados óptimos y garantizar una operación de torneado CNC segura y eficaz.
La fijación se refiere al proceso de sujetar la pieza en su sitio para garantizar la precisión y la uniformidad durante el proceso de torneado.
En el torneado CNC, la fijación desempeña un papel fundamental en la sujeción segura de la pieza de trabajo durante el proceso de mecanizado. La fijación se refiere al diseño e implementación de dispositivos de sujeción especializados que sujetan la pieza de trabajo al torno o máquina de torneado CNC. Los principales objetivos y funciones de la fijación en el torneado CNC son los siguientes:
1. Estabilidad de la pieza: La fijación garantiza que la pieza de trabajo permanezca estable y firmemente sujeta en su posición durante toda la operación de torneado. Esta estabilidad es crucial para evitar vibraciones, desplazamientos o movimientos de la pieza, que podrían provocar un mecanizado impreciso y acabados superficiales deficientes.
2. Precisión y exactitud: Una fijación adecuada es esencial para lograr resultados de mecanizado precisos y exactos. Ayuda a alinear la pieza de trabajo con respecto a la herramienta de corte de la máquina y garantiza que se sigan las trayectorias de corte deseadas con una desviación mínima.
3. 3. Seguridad: La fijación aumenta la seguridad durante el torneado CNC. Una pieza fijada de forma segura reduce el riesgo de expulsión de la pieza, lo que minimiza la posibilidad de accidentes y lesiones para el operario de la máquina.
4. Consistencia y reproducibilidad: Mediante el uso de dispositivos consistentes y bien diseñados, los procesos de torneado CNC pueden estandarizarse, lo que permite la producción repetible y reproducible de piezas idénticas con una calidad constante.
5. Accesibilidad para el mecanizado: La fijación debe proporcionar un acceso adecuado a la pieza de trabajo para la herramienta de corte. No debe obstruir el movimiento de la herramienta y debe permitir una evacuación eficaz de la viruta.
6. Eficiencia del material: Unas fijaciones bien diseñadas ayudan a optimizar el uso del material. Al sujetar firmemente la pieza en la orientación correcta, las fijaciones pueden reducir el desperdicio de material durante el proceso de mecanizado.
7. Minimización del tiempo de preparación: Unas fijaciones bien diseñadas pueden reducir el tiempo de preparación, agilizando y facilitando la carga y el posicionamiento precisos de la pieza en el torno CNC.
8. Flexibilidad: En función de los requisitos, los útiles pueden diseñarse para adaptarse a una amplia gama de tamaños, formas y materiales de piezas de trabajo. Esta flexibilidad permite el mecanizado de diversas piezas sin necesidad de grandes reequipamientos.
9. Capacidades de mecanizado mejoradas: Las fijaciones avanzadas pueden equiparse con funciones como la indexación rotativa, lo que permite el mecanizado multieje y la creación de geometrías complejas que serían un reto con las fijaciones estándar.
10. Aumento de la productividad: Una fijación eficiente y fiable contribuye a aumentar la productividad al reducir los tiempos de inactividad por rechazos, minimizar los tiempos de preparación y optimizar los procesos de mecanizado.
Una fijación bien diseñada es crucial para aprovechar todo el potencial de los tornos CNC. Garantiza que la pieza de trabajo esté bien sujeta y orientada, permitiendo que las herramientas de corte produzcan componentes precisos, uniformes y de alta calidad. La elección del método de fijación y las consideraciones de diseño dependen de los requisitos específicos de cada operación de mecanizado, la complejidad de la pieza de trabajo y las capacidades del torno CNC.
Los fabricantes pueden utilizar medidas de control de calidad, como ensayos e inspecciones, para garantizar que sus piezas cumplen las especificaciones exigidas en cuanto a precisión dimensional y acabado superficial.
Garantizar la calidad de las piezas producidas mediante torneado CNC es crucial para que los fabricantes de torneado CNC mantengan la satisfacción del cliente, cumplan las normas del sector y mantengan su reputación. Para lograrlo, los fabricantes pueden aplicar diversas medidas de control de calidad a lo largo del proceso de torneado CNC. A continuación se indican algunos pasos clave para garantizar la calidad de las piezas torneadas mediante CNC:
1. Diseño y programación sólidos: Empiece con una pieza bien diseñada y desarrolle programas CNC precisos. El software CAD/CAM puede utilizarse para crear diseños detallados y generar trayectorias de herramienta precisas para tornos CNC.
2. Inspección de materiales: Verificar la calidad de las materias primas antes del mecanizado. Compruebe las propiedades del material, las dimensiones y cualquier defecto que pueda afectar a la calidad de la pieza final.
3. Calibración y mantenimiento de máquinas: Calibre periódicamente las máquinas de torneado CNC y garantice un mantenimiento adecuado para mantenerlas en condiciones óptimas de funcionamiento. La precisión de las máquinas herramienta es esencial para producir piezas de alta calidad.
4. Fijación adecuada: Utilice fijaciones adecuadas y bien diseñadas para sujetar firmemente la pieza de trabajo durante el mecanizado. Una fijación adecuada garantiza un posicionamiento y una estabilidad precisos, minimizando los errores durante el torneado CNC.
5. Selección y mantenimiento de herramientas: Elija herramientas de corte de alta calidad adecuadas para el material específico y los requisitos de mecanizado. Inspeccione y mantenga regularmente las herramientas para asegurarse de que están afiladas y en buen estado.
6. Inspección en proceso: Implementar inspecciones en proceso para comprobar las dimensiones, tolerancias y acabado superficial de las piezas durante el proceso de torneado CNC. Para ello pueden utilizarse sistemas de medición automatizados o inspecciones manuales.
7. Control Estadístico de Procesos (CEP): Aplicar técnicas de SPC para supervisar y controlar el proceso de torneado CNC. El SPC implica la recopilación y el análisis de datos en varias fases de la producción para identificar y abordar cualquier variación o desviación de la calidad deseada.
8. Inspección posterior al mecanizado: Realice inspecciones minuciosas de las piezas acabadas para validar su precisión dimensional, acabado superficial y otras características críticas. Para ello, utilice herramientas de medición de precisión como calibres, micrómetros y máquinas de medición de coordenadas (MMC).
9. Ensayos no destructivos (END): En determinadas industrias o para piezas críticas, pueden emplearse métodos de ensayo no destructivos, como los rayos X, los ensayos por ultrasonidos o los ensayos por líquidos penetrantes, para detectar defectos ocultos sin dañar la pieza.
10. Procedimientos de calidad documentados: Disponga de procedimientos de calidad e instrucciones de trabajo bien documentados para garantizar la coherencia y la normalización en el proceso de torneado CNC. Esta documentación sirve de referencia para los operarios y el personal de control de calidad.
11. Mejora continua: Fomentar una cultura de mejora continua dentro de la organización. Revisar y analizar periódicamente los datos de calidad para identificar áreas de mejora y aplicar medidas correctoras en caso necesario.
12. Cumplimiento de las normas: Garantizar que el proceso de torneado CNC cumple las normas industriales pertinentes y los requisitos del cliente.
Mediante la aplicación de estas medidas de control de calidad, los fabricantes de torneado CNC pueden producir piezas de alta calidad de forma constante, reducir los rechazos y forjarse una reputación de fiabilidad y precisión. La garantía de calidad es un proceso continuo, y un enfoque proactivo de la gestión de la calidad es esencial para el éxito a largo plazo en la fabricación de torneado CNC.
El utillaje incluye herramientas de corte, portaherramientas y otros componentes que se utilizan para dar forma a la pieza durante el proceso de torneado CNC.
Las herramientas desempeñan un papel crucial en el torneado CNC, ya que afectan directamente al proceso de mecanizado y a la calidad del producto final. El utillaje se refiere a las herramientas de corte y accesorios utilizados en el torno CNC para eliminar el material de la pieza de trabajo y darle la forma deseada. El papel de las herramientas en el torneado CNC puede resumirse como sigue:
1. Eliminación de material: La función principal de las herramientas en el torneado CNC es eliminar material de la pieza de trabajo. La herramienta de corte entra en contacto con la pieza de trabajo y el material se corta para crear la forma y las dimensiones deseadas.
2. Mecanizado de precisión: El torneado CNC se basa en herramientas de corte precisas y exactas para lograr las tolerancias y el acabado superficial deseados. Las herramientas de alta calidad garantizan que el proceso de mecanizado produzca piezas con las dimensiones requeridas y cumpla las tolerancias especificadas.
3. Vida útil y durabilidad de las herramientas: La elección de los materiales y recubrimientos adecuados para las herramientas influye directamente en su vida útil y durabilidad. Las herramientas de alta calidad con revestimientos resistentes al desgaste pueden soportar las tensiones del torneado CNC, lo que se traduce en una mayor vida útil y menores costes de sustitución.
4. Acabado superficial: El utillaje afecta al acabado superficial de la pieza mecanizada. Unas herramientas de corte correctamente seleccionadas y mantenidas pueden dar como resultado un acabado superficial liso y de alta calidad en la pieza.
5. Control de viruta: El diseño y la geometría de la herramienta de corte influyen en el control de la viruta durante el torneado CNC. Un control eficaz de la viruta ayuda a mantener limpia la zona de corte y a evitar problemas de mecanizado relacionados con la viruta.
6. Compatibilidad de materiales: Los diferentes materiales requieren utillajes específicos para garantizar una eliminación eficaz del material y evitar un desgaste excesivo de la herramienta. Las herramientas deben seleccionarse en función de las propiedades del material de la pieza de trabajo para obtener unos resultados de mecanizado óptimos.
7. Selección de herramientas para diferentes operaciones: El torneado CNC implica varias operaciones de corte, como desbaste, acabado, roscado y ranurado. Para cada operación se utilizan diferentes herramientas, y una selección adecuada de las mismas garantiza el proceso de mecanizado más eficiente y preciso.
8. Avances y velocidades: El utillaje, en combinación con la programación del CNC, determina los avances de corte y las velocidades de husillo adecuados para obtener unas tasas de arranque de material y una eficiencia de mecanizado óptimas.
9. 9. Cambio de herramientas y automatización: El torneado CNC a menudo implica múltiples herramientas para diferentes pasos de mecanizado. Los mecanismos eficientes de cambio de herramientas y la automatización garantizan transiciones fluidas entre herramientas, lo que reduce el tiempo de inactividad y aumenta la productividad.
10. Seguridad: El herramental correctamente instalado y asegurado es esencial para la seguridad del operador de la máquina y la integridad del proceso de torneado CNC. Un utillaje mal instalado o dañado puede suponer riesgos para la seguridad y afectar a la calidad del mecanizado.
En resumen, las herramientas son un aspecto fundamental del torneado CNC que influye significativamente en el proceso de mecanizado, la precisión, el acabado superficial y la eficacia general. La selección, el mantenimiento y la gestión de las herramientas de corte son esenciales para lograr una producción constante, de alta calidad y rentable en las operaciones de torneado CNC.
La torreta aloja varias herramientas de corte y puede girarse para seleccionar la herramienta adecuada para el trabajo.
La torreta en el torneado CNC desempeña un papel fundamental en el proceso de mecanizado, concretamente en los tornos CNC con capacidad para múltiples herramientas. La torreta es un mecanismo portaherramientas situado sobre el carro transversal o la bancada del torno CNC, y permite el intercambio rápido y automatizado de las herramientas de corte durante la operación de torneado. Las principales funciones de la torreta en el torneado CNC son las siguientes:
1. Almacenamiento y organización de herramientas: La torreta sirve como sistema de almacenamiento y organización de herramientas. Puede alojar varias herramientas de corte simultáneamente, lo que permite acceder rápidamente a diversas herramientas durante el proceso de mecanizado sin necesidad de cambiarlas manualmente.
2. Cambio automático de herramientas: Con una torreta instalada, los tornos CNC pueden realizar cambios automáticos de herramienta durante el proceso de mecanizado. Esta automatización reduce el tiempo de inactividad entre cambios de herramienta, aumenta la productividad y minimiza la intervención del operario.
3. Capacidad para varias herramientas: La capacidad de la torreta para alojar varias herramientas permite al torno CNC realizar diversas operaciones de mecanizado sin intervención manual. Pueden utilizarse distintas herramientas para desbaste, acabado, roscado, ranurado y otras tareas, lo que permite una mayor versatilidad en el torneado CNC.
4. Indexación de herramientas rápida y repetible: El mecanismo de indexado de la torreta garantiza un posicionamiento preciso y repetible de las herramientas. Esta precisión permite obtener resultados de mecanizado uniformes y la posibilidad de volver a herramientas específicas para diferentes pasos de mecanizado.
5. Increased Efficiency: The turret's rapid tool-changing capabilities enhance the overall efficiency of CNC turning operations. It reduces idle time and enables continuous machining with minimal interruptions.
6. Flexibilidad: El torneado CNC con torreta ofrece flexibilidad en la selección de herramientas, lo que permite a los operarios elegir las herramientas más adecuadas para tareas de mecanizado y materiales específicos.
7. Monitorización y gestión de herramientas: Algunos tornos CNC modernos equipados con torretas pueden tener incorporados sistemas de monitorización de herramientas. Estos sistemas pueden detectar el desgaste y la rotura de la herramienta, alertando al operario para que tome medidas correctivas o inicie la sustitución de la herramienta según sea necesario.
8. Reducción del tiempo de preparación: Al disponer de varias herramientas en la torreta, el tiempo de preparación se reduce considerablemente. Los operarios pueden cambiar rápidamente entre herramientas para diferentes requisitos de mecanizado sin cambiar físicamente las herramientas.
9. Mayor precisión de mecanizado: La capacidad de la torreta para indexar con precisión las herramientas y mantener sus posiciones contribuye a la precisión general y a la exactitud dimensional de las operaciones de torneado CNC.
En resumen, la torreta es un componente fundamental en el torneado CNC, especialmente en los tornos con capacidad para múltiples herramientas. Permite el intercambio automático y eficaz de herramientas de corte, proporcionando versatilidad, mayor productividad y mayor precisión en el proceso de mecanizado. El papel de la torreta en la gestión y el cambio rápido de herramientas es fundamental para optimizar el rendimiento de los tornos CNC.
El torneado CNC puede ser más rápido y eficaz que otros procesos de mecanizado porque permite una mayor precisión y exactitud.
El torneado CNC, como proceso de mecanizado, tiene sus puntos fuertes y débiles en comparación con otros procesos de mecanizado. La velocidad y la eficacia del torneado CNC dependen de varios factores, como el tipo de material que se mecaniza, la complejidad de la pieza, las herramientas de corte utilizadas y las capacidades específicas de la máquina CNC. Comparemos el torneado CNC con otros procesos de mecanizado habituales en términos de velocidad y eficacia:
1. Fresado CNC vs. Torneado CNC:
- Velocidad: El fresado CNC y el torneado CNC pueden tener una velocidad comparable en función de la aplicación específica. El fresado CNC es idóneo para el mecanizado de formas 3D complejas y múltiples superficies simultáneamente, mientras que el torneado CNC destaca en piezas cilíndricas y giratorias.
- Eficacia: El fresado CNC puede tener una ventaja en eficiencia para ciertas piezas intrincadas, ya que puede eliminar material desde múltiples ángulos en una sola configuración. Sin embargo, el torneado CNC suele ser más eficaz para producir piezas giratorias con menos configuraciones y cambios de herramienta.
2. Torneado CNC vs. Rectificado:
- Velocidad: En general, el torneado CNC es más rápido que el rectificado para el mismo volumen de arranque de material. Las máquinas de torneado pueden eliminar material más rápidamente debido a la naturaleza del proceso de corte.
- Eficacia: El torneado CNC es más eficaz para producir piezas con simetría rotacional, como ejes, pasadores y bujes. El rectificado, por su parte, es preferible para conseguir tolerancias estrechas y acabados superficiales excelentes, especialmente en materiales endurecidos.
3. CNC Turning vs. Máquina de corte por hilo EDM (Electrical Discharge Machining):
- Velocidad: En términos de velocidad, el torneado CNC suele ser más rápido que la electroerosión por hilo para la eliminación de grandes cantidades de material. Sin embargo, la electroerosión por hilo puede ser más rápida para cortar formas complejas en materiales duros.
- Eficacia: El torneado CNC es más eficaz para producir piezas giratorias, especialmente cuando el volumen de eliminación de material es significativo. La electroerosión por hilo es muy eficiente para piezas intrincadas y delicadas, sobre todo en materiales duros en los que los procesos de corte convencionales pueden suponer un reto.
4. Torneado CNC vs. Corte por chorro de agua:
- Velocidad: El torneado CNC suele ser más rápido que el corte por chorro de agua, sobre todo para velocidades de arranque de material de moderadas a altas. El corte por chorro de agua es más adecuado para materiales más blandos y formas complejas, pero puede tener velocidades de corte más lentas.
- Eficacia: El torneado CNC es más eficaz para producir piezas giratorias y piezas con mayores tasas de arranque de material. El corte por chorro de agua es muy eficiente para cortar materiales más blandos, materiales compuestos y materiales que pueden ser sensibles a los daños térmicos.
En conclusión, la velocidad y la eficacia del torneado CNC dependen de la aplicación específica y de las características de la pieza mecanizada. El torneado CNC destaca en la producción de piezas giratorias y piezas con velocidades de arranque de material moderadas. Para formas más complejas, tolerancias ajustadas y características intrincadas, otros procesos de mecanizado como el fresado CNC, el rectificado, la electroerosión por hilo o el corte por chorro de agua pueden ofrecer mayor eficacia y precisión. La elección del proceso de mecanizado más adecuado implica tener en cuenta factores como el material, la geometría de la pieza, el volumen de producción y el acabado superficial deseado.
El código G es un lenguaje de programación que se utiliza para controlar máquinas CNC, incluidos los tornos CNC.
El código G desempeña un papel fundamental en el torneado CNC, así como en otros procesos de mecanizado CNC (Control Numérico por Ordenador). El código G, abreviatura de "código geométrico" o "lenguaje de programación G", es un conjunto de instrucciones que se utilizan para controlar los movimientos y las acciones de las máquinas CNC. En el torneado CNC, el código G guía específicamente los movimientos de la herramienta de corte y controla todo el proceso de mecanizado. He aquí la función del código G en el torneado CNC:
1. Control de la trayectoria de la herramienta: El código G indica al torno CNC la trayectoria específica que debe seguir la herramienta de corte durante la operación de mecanizado. Define las coordenadas, la dirección y la profundidad de los cortes necesarios para dar forma a la pieza con precisión.
2. Velocidad del cabezal y velocidad de avance: El código G establece la velocidad del cabezal y el avance durante el torneado CNC. Controla la velocidad de rotación del husillo del torno y la velocidad a la que la herramienta de corte avanza en la pieza de trabajo. Estos parámetros son cruciales para determinar la velocidad de corte y la tasa de eliminación de material.
3. Selección de herramienta: Los comandos de código G especifican qué herramienta de la torreta o del almacén de herramientas debe utilizarse para una operación determinada. Esto permite al torno CNC seleccionar automáticamente la herramienta de corte adecuada para cada parte del proceso de mecanizado.
4. Compensación de herramienta: El código G puede incluir instrucciones de compensación de herramienta, como la compensación del radio o la longitud de la herramienta. Estos comandos ayudan a ajustar la posición de la herramienta para compensar su geometría, garantizando un mecanizado preciso y unas dimensiones exactas de la pieza.
5. 5. Parámetros de mecanizado: El código G incluye parámetros como la dirección del husillo, el encendido y apagado del refrigerante, los comandos de cambio de herramienta, el tiempo de permanencia (pausa en un lugar específico) y el avance rápido (movimiento rápido entre puntos de corte). Estos parámetros controlan el comportamiento de la máquina a lo largo del proceso de torneado.
6. Reproducibilidad: El código G garantiza la reproducibilidad de las operaciones de torneado CNC. Una vez escrito un programa, puede utilizarse repetidamente para fabricar piezas idénticas con una precisión constante.
7. Control de múltiples ejes: Los tornos CNC pueden tener múltiples ejes de movimiento. El código G permite coordinar y controlar estos ejes para realizar operaciones de torneado complejas, como roscado, ranurado y contorneado.
8. 8. Gestión de errores y seguridad: El código G incluye códigos de manejo de errores y de seguridad para hacer frente a situaciones inesperadas, paradas de emergencia y condiciones de fallo durante el torneado CNC.
9. Integración del software CAM: El software CAM (fabricación asistida por ordenador) genera código G basado en el modelo CAD (diseño asistido por ordenador) de la pieza. El software CAM interpreta el diseño de la pieza, crea la trayectoria de la herramienta y genera el código G para accionar el torno CNC.
En resumen, el código G es el lenguaje que comunica las instrucciones al torno CNC. Controla los movimientos, la selección de herramientas y los parámetros de mecanizado necesarios para dar forma a la pieza con precisión y eficacia. Los operarios de torneado CNC utilizan el código G para programar la máquina, y los fabricantes de tornos CNC confían en él para producir piezas precisas y uniformes de acuerdo con las especificaciones deseadas.
El torneado CNC puede utilizarse en una gran variedad de industrias, como la aeroespacial, la automovilística y la fabricación de dispositivos médicos.
El torneado CNC es un proceso de mecanizado versátil que se utiliza en diversas industrias debido a su capacidad para producir una amplia gama de piezas cilíndricas y giratorias. Algunas aplicaciones comunes del torneado CNC incluyen:
1. Componentes aeroespaciales: El torneado CNC se utiliza ampliamente en la industria aeroespacial para producir componentes como ejes de motor, discos de turbina, piezas de tren de aterrizaje y accesorios hidráulicos.
2. Piezas de automoción: El torneado CNC se emplea en el sector de la automoción para fabricar piezas como ejes, árboles de transmisión, pistones, rotores de freno y diversos componentes del motor.
3. Dispositivos médicos: El torneado CNC se utiliza para crear componentes de dispositivos médicos, incluidos instrumentos quirúrgicos, dispositivos implantables y prótesis.
4. Electrónica: El torneado CNC se emplea para producir componentes electrónicos como conectores, terminales y carcasas para dispositivos electrónicos.
5. Componentes hidráulicos y neumáticos: El torneado CNC se utiliza para fabricar válvulas, racores, cilindros y otros componentes utilizados en sistemas hidráulicos y neumáticos.
6. Componentes de manipulación de fluidos: El torneado CNC se aplica para producir diversos componentes utilizados en sistemas de manipulación de fluidos, como bombas, válvulas y boquillas.
7. Artículos deportivos: El torneado CNC se utiliza en la producción de artículos deportivos como ejes de palos de golf, componentes de bicicletas y piezas de carretes de pesca.
8. Componentes de fontanería y HVAC: El torneado CNC se emplea para fabricar accesorios de fontanería, acoplamientos y componentes HVAC.
9. Herramientas y utillajes: El torneado CNC se utiliza para crear utillajes y herramientas necesarios para diversos procesos de mecanizado y fabricación.
10. Aplicaciones militares y de defensa: El torneado CNC se utiliza en las industrias de defensa y militar para producir componentes para armas, municiones, vehículos y sistemas de comunicación.
11. Equipos de construcción: El torneado CNC se emplea en la fabricación de piezas para equipos de construcción como bulldozers, excavadoras y cargadoras.
12. Maquinaria de precisión: El torneado CNC se utiliza para producir piezas para diversas máquinas y equipos de precisión, incluidos robots industriales y máquinas herramienta.
La capacidad del torneado CNC para producir piezas cilíndricas precisas y repetibles con gran eficacia lo convierte en un proceso de mecanizado esencial para una amplia gama de aplicaciones. Es especialmente adecuado para producir componentes con simetría rotacional y diversas características complejas. El torneado CNC sigue desempeñando un papel fundamental en la fabricación moderna, permitiendo la producción de piezas de alta calidad utilizadas en diversas industrias de todo el mundo.
La pinza sujeta la herramienta de corte y puede utilizarse para cambiar las herramientas durante el proceso de torneado.
La pinza desempeña un papel crucial en el torneado CNC, ya que es el principal dispositivo de sujeción de la pieza en el husillo del torno. La pinza es un mandril especializado que se sujeta a la pieza de trabajo, manteniéndola firmemente en su lugar durante el proceso de torneado. Su función en el torneado CNC incluye lo siguiente:
1. Sujeción de la pieza: La pinza sujeta firmemente la pieza de trabajo, garantizando que permanezca fija y estable durante el proceso de mecanizado. Esto es esencial para evitar cualquier movimiento o vibración que pueda provocar imprecisiones en la pieza mecanizada.
2. Exactitud y precisión: Al sujetar firmemente la pieza de trabajo, la pinza ayuda a mantener la exactitud y la precisión en el torneado CNC. La posición y orientación de la pieza son fundamentales para conseguir las dimensiones y tolerancias deseadas en la pieza acabada.
3. Cambios rápidos de pieza: Las pinzas están diseñadas para cambios rápidos de piezas de trabajo. Esto permite una preparación eficiente y minimiza el tiempo de inactividad entre diferentes operaciones de mecanizado, mejorando la productividad general.
4. Consistencia y repetibilidad: La capacidad de la pinza para mantener la pieza en la misma posición garantiza la repetibilidad en el torneado CNC. Esto es especialmente importante en la producción en serie, donde deben fabricarse piezas idénticas con una calidad constante.
5. Mejora del acabado superficial: Una pieza sujeta con seguridad conlleva una mayor estabilidad durante el proceso de corte, lo que se traduce en un mejor acabado superficial de la pieza mecanizada.
6. Reducción del desgaste de la herramienta: Un agarre adecuado de la pinza reduce las posibilidades de deslizamiento o vibración de la pieza de trabajo, lo que puede provocar un mayor desgaste de la herramienta. Una pieza de trabajo estable permite a las herramientas de corte engranar con el material con precisión, prolongando la vida útil de la herramienta.
7. Distorsión minimizada de la pieza de trabajo: La fuerza de sujeción uniforme de la pinza ayuda a minimizar la distorsión de la pieza durante el mecanizado, especialmente cuando se trabaja con componentes delicados o de paredes finas.
8. Gama de tamaños: Las pinzas están disponibles en varios tamaños para adaptarse a diferentes diámetros de pieza. Esta versatilidad permite mecanizar una amplia gama de tamaños de piezas con el mismo torno.
9. Sistemas de carga automática: En las configuraciones automatizadas de torneado CNC, las pinzas se utilizan a menudo con sistemas automáticos de carga y descarga, lo que permite una producción continua con una intervención mínima del operario.
10. Seguridad: La sujeción adecuada de las piezas mejora la seguridad durante el torneado CNC, ya que reduce el riesgo de expulsión de la pieza y los posibles accidentes.
En resumen, la pinza es un componente fundamental en el torneado CNC, ya que proporciona una solución de sujeción segura y eficaz para la pieza de trabajo. Su capacidad para sujetar la pieza con firmeza, al tiempo que permite realizar cambios rápidos y repetibles, contribuye a la precisión, la productividad y el éxito general de las operaciones de torneado CNC.
Las estrategias habituales incluyen el desbaste, el acabado y el refrentado.
En el torneado CNC, se emplean diversas estrategias de corte para lograr diferentes objetivos de mecanizado y optimizar la eficacia y la calidad del proceso. Algunas estrategias de corte comunes utilizadas en el torneado CNC incluyen:
1. El refrentado: El refrentado es una operación básica de torneado que se utiliza para crear una superficie plana en el extremo de la pieza. Consiste en eliminar material del diámetro exterior de la pieza para crear una cara lisa y perpendicular.
2. Torneado: El torneado es la operación fundamental de torneado CNC utilizada para eliminar material del diámetro exterior de la pieza. Crea formas cilíndricas y reduce el diámetro de la pieza al tamaño deseado.
3. Desbaste: El desbaste es la fase inicial de arranque de material del torneado CNC. Consiste en retirar grandes cantidades de material para conformar rápidamente la pieza de trabajo con la forma deseada antes de las operaciones de acabado.
4. Acabado: El acabado es la fase final del torneado CNC, en la que la herramienta de corte elimina pequeñas cantidades de material para conseguir el acabado superficial deseado y unas dimensiones precisas.
5. 5. Ranurado: El ranurado es una operación de torneado CNC utilizada para cortar ranuras estrechas, rectas o contorneadas en la superficie de la pieza de trabajo. Se suele utilizar para crear ranuras de juntas tóricas, ranuras de anillos elásticos y características similares.
6. 6. Roscado: El roscado es el proceso de cortar roscas en la superficie exterior de la pieza. Los tornos CNC pueden realizar operaciones de roscado interior y exterior.
7. Despiece: El tronzado, también conocido como tronzado o corte longitudinal, se utiliza para separar la pieza del material restante. Consiste en cortar el diámetro de la pieza para crear dos partes separadas.
8. Torneado cónico: El torneado cónico es una operación de torneado CNC utilizada para crear superficies cónicas en la pieza de trabajo. La herramienta de corte está programada para moverse en un ángulo relativo al eje de la pieza de trabajo, produciendo la conicidad deseada.
9. Mandrinado: El mandrinado se utiliza para ampliar un agujero existente o crear características internas con gran precisión. Consiste en cortar la superficie interior de la pieza utilizando una herramienta de corte de una sola punta.
10. Torneado de perfiles: El torneado de perfiles consiste en cortar formas y contornos complejos en la superficie exterior de la pieza. Se utiliza para crear características intrincadas y diseños detallados.
11. Torneado de formas: El torneado de formas se utiliza para generar formas geométricas específicas en la pieza de trabajo, como superficies convexas o cóncavas. Utiliza herramientas de corte especializadas con perfiles predeterminados.
12. Moleteado: El moleteado es una operación de torneado CNC utilizada para crear un patrón texturizado en la superficie de la pieza de trabajo para mejorar el agarre o la estética.
Estas son algunas de las estrategias de corte más utilizadas en el torneado CNC. La elección de la estrategia de corte depende del diseño específico de la pieza, el material y los requisitos de mecanizado. Los programadores y maquinistas de CNC utilizan su experiencia para seleccionar las estrategias de corte más adecuadas para lograr los resultados deseados con eficacia y precisión.
El torneado CNC permite una mayor precisión y exactitud, lo que reduce los residuos y aumenta la eficacia del proceso de fabricación.
El torneado CNC ofrece varias formas de reducir los residuos y aumentar la eficacia en los procesos de fabricación. Al combinar tecnología avanzada, automatización y control preciso, el torneado CNC proporciona numerosas ventajas que contribuyen a reducir los residuos y mejorar la eficacia. A continuación se explica cómo ayuda el torneado CNC en estos aspectos:
1. Optimización del material: Los tornos CNC están programados para retirar sólo la cantidad necesaria de material de la pieza. Esto minimiza el desperdicio de material y ayuda a optimizar su uso, reduciendo el coste total de producción.
2. Reproducibilidad y consistencia: El torneado CNC permite crear programas estandarizados que pueden utilizarse para producir piezas idénticas con una calidad constante. Esto reduce el riesgo de errores y repeticiones, ahorrando tiempo y recursos.
3. Puesta a punto más rápida: Los tornos CNC pueden configurarse de forma rápida y eficaz con el uso de trayectorias y bibliotecas de herramientas preprogramadas. Esto reduce el tiempo de inactividad entre series de producción, lo que aumenta la productividad.
4. Reducción de la mano de obra: El torneado CNC está automatizado en gran medida, lo que reduce la necesidad de mano de obra. Esto disminuye las posibilidades de que se produzcan errores humanos o relacionados con la fatiga, lo que se traduce en una mayor precisión y eficacia del mecanizado.
5. Funcionamiento continuo: Los tornos CNC pueden funcionar continuamente, 24 horas al día, 7 días a la semana, con una intervención mínima del operario. Esta capacidad de producción ininterrumpida maximiza la utilización de la máquina y reduce el tiempo de inactividad.
6. Gestión de la vida útil de la herramienta: El torneado CNC permite un control preciso de los parámetros de corte, como la velocidad del husillo y el avance. Esto ayuda a optimizar la vida útil de las herramientas, reducir su desgaste y minimizar la necesidad de cambiarlas con frecuencia.
7. Supervisión y control en tiempo real: Los tornos CNC pueden equiparse con sensores y sistemas de supervisión que proporcionan datos en tiempo real sobre el desgaste de las herramientas, el rendimiento del mecanizado y la calidad de las piezas. Esta información permite a los operarios realizar los ajustes oportunos, mejorando la eficiencia y reduciendo las piezas desechadas.
8. Rapid Prototyping: CNC turning facilitates rapid prototyping by quickly translating CAD designs into tangible parts. This speeds up the product development process and reduces the need for extensive manual prototyping and iterations.
9. Plazos de entrega más cortos: Con configuraciones más rápidas, funcionamiento continuo y menor intervención manual, el torneado CNC ayuda a acortar los plazos de producción, lo que permite a los fabricantes satisfacer las demandas de los clientes de forma más eficiente.
10. Menos operaciones secundarias: Los tornos CNC pueden equiparse con múltiples estaciones de herramientas y capacidades de herramientas vivas, reduciendo la necesidad de operaciones secundarias en otras máquinas. Esto agiliza el proceso de producción y mejora la eficiencia.
11. Reciclaje de residuos: La optimización de materiales y la menor generación de chatarra del torneado CNC también contribuyen a la reducción de residuos y apoyan las prácticas de fabricación respetuosas con el medio ambiente.
En general, la precisión, la automatización y las capacidades avanzadas del torneado CNC contribuyen significativamente a reducir los residuos, mejorar la eficiencia y aumentar la competitividad general de las operaciones de fabricación. Al adoptar la tecnología de torneado CNC, los fabricantes pueden lograr una mayor productividad, reducir los costes de producción y mejorar la sostenibilidad.
El mantenimiento y la calibración periódicos son esenciales para garantizar que los tornos CNC funcionan al máximo rendimiento. Los fabricantes pueden implantar un programa de mantenimiento y calibración para garantizar que sus máquinas estén en condiciones óptimas.
El mantenimiento y la calibración adecuados de los tornos CNC son esenciales para garantizar su rendimiento, precisión y longevidad óptimos. Las prácticas regulares de mantenimiento y calibración ayudan a evitar averías, reducir el tiempo de inactividad y mantener una calidad de mecanizado constante. A continuación se indican algunas medidas que los fabricantes pueden adoptar para garantizar que sus tornos CNC se mantienen y calibran correctamente:
1. Establezca un programa de mantenimiento: Cree un programa de mantenimiento exhaustivo que incluya inspecciones periódicas, limpieza, lubricación y ajustes para los distintos componentes del torno CNC. La frecuencia de las tareas de mantenimiento puede variar en función del uso de la máquina, pero un programa bien definido garantiza un mantenimiento puntual y constante.
2. Siga las directrices del fabricante: Consulte las directrices y recomendaciones de mantenimiento del fabricante de la máquina CNC. Suelen proporcionar instrucciones específicas para el mantenimiento rutinario, procedimientos de calibración y las mejores prácticas para mantener la máquina en las mejores condiciones.
3. Formar a los operarios y al personal de mantenimiento: Asegúrese de que los operarios y el personal de mantenimiento reciben la formación adecuada sobre los procedimientos de mantenimiento y calibración del torno CNC. Un personal bien formado puede identificar posibles problemas y realizar correctamente las tareas de mantenimiento.
4. Supervisar el rendimiento de la máquina: Implemente un sistema para supervisar regularmente el rendimiento del torno CNC. Realice un seguimiento de factores como la vida útil de la herramienta, los parámetros de corte, la precisión y la calidad de la pieza. La supervisión ayuda a identificar cualquier desviación o anomalía que pueda requerir mantenimiento o calibración.
5. Mantenga limpia la máquina: Limpie regularmente la máquina de torneado CNC, incluyendo el área de trabajo, los sistemas de recogida de virutas y los portaherramientas. Una limpieza adecuada reduce el riesgo de contaminación, mejora la precisión y prolonga la vida útil de los componentes de la máquina.
6. Lubricación: Siga el programa de lubricación recomendado y utilice los lubricantes correctos para los distintos componentes. La lubricación evita el desgaste excesivo, reduce la fricción y garantiza un funcionamiento suave de la máquina.
7. Compruebe y sustituya las piezas desgastadas: Inspeccione los componentes de la máquina, como correas, cojinetes y tornillos de bolas, en busca de signos de desgaste. Sustituya rápidamente cualquier pieza desgastada o dañada para mantener el rendimiento de la máquina.
8. Calibrar la máquina: Programe la calibración periódica de los componentes críticos de la máquina, como la excentricidad del husillo, la alineación de los ejes y las compensaciones de las herramientas. La calibración garantiza un mecanizado preciso y evita imprecisiones dimensionales.
9. Utilice sistemas de diagnóstico y supervisión: Muchas máquinas de torneado CNC modernas vienen equipadas con sistemas de diagnóstico y supervisión. Utilice estos sistemas para controlar el estado de la máquina, el estado de la herramienta y las métricas de rendimiento.
10. Documentar los registros de mantenimiento y calibración: Mantenga registros detallados de todas las actividades de mantenimiento y calibración realizadas en el torno CNC. Estos registros proporcionan una visión histórica del historial de mantenimiento de la máquina y pueden ser útiles para la resolución de problemas y la toma de decisiones.
11. Responda a las anomalías: Si la máquina muestra un comportamiento inusual o experimenta problemas, resuélvalos con prontitud. Investigue la causa y adopte medidas correctivas para evitar más problemas.
Siguiendo diligentemente estas prácticas de mantenimiento y calibración, los fabricantes pueden garantizar que sus tornos CNC funcionen de forma óptima, mantengan una alta precisión y ofrezcan resultados de mecanizado uniformes y de alta calidad. Un mantenimiento adecuado de las máquinas también contribuye a crear un entorno de trabajo más seguro y a prolongar la vida útil de la máquina, lo que en última instancia se traduce en una mayor productividad y rentabilidad.
FAQ Lista de servicios de torneado CNC
El torneado CNC es un proceso de fabricación que utiliza máquinas controladas por ordenador para crear piezas cilíndricas eliminando material de una pieza giratoria.
El torneado CNC, también conocido como torneado de control numérico por ordenador, es un proceso de mecanizado utilizado para crear piezas cilíndricas mediante la eliminación de material de una pieza de trabajo giratoria. Es una forma de fabricación sustractiva, en la que el material se retira de la pieza para conseguir la forma y las dimensiones deseadas. El torneado CNC se realiza en un torno CNC, que es una máquina herramienta controlada por ordenador equipada con herramientas de corte que se mueven en una trayectoria lineal a lo largo de la pieza de trabajo para eliminar material.
En el torneado CNC, la pieza se sujeta en un mandril o pinza y la herramienta de corte se monta en un portaherramientas que se desplaza a lo largo del eje de la pieza. El torno CNC sigue instrucciones preprogramadas, denominadas códigos G, para controlar los movimientos y acciones de la herramienta de corte. Estas instrucciones especifican la posición de la herramienta, el avance, la profundidad de corte y otros parámetros para lograr un mecanizado preciso.
Durante el torneado CNC, la pieza gira a una velocidad constante mientras la herramienta de corte se desplaza a lo largo de la pieza. La herramienta de corte elimina material del diámetro exterior de la pieza, creando formas cilíndricas, roscas, ranuras, chaflanes y otras características.
El torneado CNC se utiliza ampliamente en diversas industrias para producir componentes como ejes, pasadores, bujes, bridas y otras piezas giratorias. Ofrece varias ventajas, como alta precisión, repetibilidad y capacidad para producir formas complejas. El torneado CNC también es muy eficaz y adecuado para series de producción de bajo y alto volumen.
El proceso de torneado CNC es versátil y puede utilizarse con una amplia gama de materiales, incluidos metales, plásticos y materiales compuestos. Ofrece a los fabricantes la flexibilidad necesaria para producir piezas personalizadas con tolerancias estrechas y excelentes acabados superficiales, lo que lo convierte en una tecnología esencial en la fabricación moderna.
Los materiales más comunes son los metales (como el aluminio, el latón y el acero), los plásticos y la madera.
El torneado CNC es un proceso de mecanizado versátil que puede utilizarse con una amplia gama de materiales. La elección del material depende de la aplicación específica, los requisitos de la pieza y las capacidades de mecanizado del torno CNC. Algunos tipos comunes de materiales utilizados en el torneado CNC incluyen:
1. Metales:
- Aluminio: Ligero, resistente a la corrosión y ampliamente utilizado en diversas industrias.
- Acero: Ofrece buena resistencia, tenacidad y maquinabilidad para una amplia gama de aplicaciones.
- Acero inoxidable: Proporciona una excelente resistencia a la corrosión y se utiliza habitualmente en las industrias alimentaria, médica y aeroespacial.
- Latón: Conocido por su excelente conductividad eléctrica y térmica, se utiliza a menudo en componentes eléctricos y piezas decorativas.
- Cobre: Ofrece una alta conductividad eléctrica y térmica y se utiliza en aplicaciones eléctricas y de fontanería.
- Titanio: Conocido por su elevada relación resistencia-peso y su resistencia a la corrosión, se utiliza en aplicaciones aeroespaciales y médicas.
- Hierro fundido: Ofrece una buena resistencia al desgaste y amortigua las vibraciones; se utiliza habitualmente para componentes de maquinaria.
2. Plásticos:
- Acrílico (PMMA): Transparente, ligero y de uso común en pantallas, rótulos y componentes ópticos.
- Nylon (poliamida): Material duradero y de baja fricción utilizado en diversas aplicaciones de ingeniería.
- Delrin (Polioximetileno, POM): Material de baja fricción y resistente al desgaste utilizado para engranajes, cojinetes y componentes de precisión.
- Polietileno (PE): Material ligero y resistente a los productos químicos utilizado en diversas aplicaciones.
- Policarbonato (PC): Resistente a los impactos y utilizado en aplicaciones que requieren transparencia y durabilidad.
3. Compuestos:
- Composites reforzados con fibra de carbono: Materiales ligeros y de alta resistencia utilizados en las industrias aeroespacial, automovilística y de artículos deportivos.
- Compuestos reforzados con fibra de vidrio: Ofrecen una buena relación resistencia-peso y se utilizan en diversas aplicaciones.
4. Otros materiales:
- Madera: El torneado CNC puede utilizarse para aplicaciones de torneado de madera para crear componentes de madera artísticos o funcionales.
- Cerámica: CNC turning can be used with certain ceramics for specialized applications.
Es esencial tener en cuenta las propiedades específicas de cada material a la hora de elegir el material adecuado para el torneado CNC. Factores como las propiedades mecánicas, la conductividad térmica, la resistencia química y el coste influirán en la selección del material para una pieza o componente concreto. Los tornos CNC son capaces de trabajar con una amplia variedad de materiales, lo que los convierte en un proceso versátil y adaptable para fabricar diversas piezas en distintos sectores.
El torneado CNC consiste en crear piezas cilíndricas eliminando material de una pieza giratoria, mientras que el fresado CNC consiste en cortar material para crear una forma tridimensional.
El torneado CNC y el fresado CNC son dos procesos de mecanizado distintos, cada uno de los cuales ofrece capacidades y aplicaciones únicas. Aunque ambos son procesos de control numérico por ordenador (CNC), difieren en el tipo de máquina y en la forma en que se retira el material de la pieza de trabajo. Estas son las principales diferencias entre el torneado CNC y el fresado CNC:
1. Tipo de máquina:
- Torneado CNC: En el torneado CNC, el mecanizado se realiza en un torno, también conocido como torno CNC o centro de torneado. La pieza gira mientras la herramienta de corte permanece inmóvil o se desplaza a lo largo del eje de la pieza para eliminar material. El torneado CNC se utiliza principalmente para piezas cilíndricas y giratorias.
- Fresado CNC: En el fresado CNC, el mecanizado se realiza en una fresadora, también conocida como fresadora CNC o centro de mecanizado. La herramienta de corte gira y se mueve a lo largo de varios ejes para eliminar material de la pieza de trabajo en varias direcciones. El fresado CNC es adecuado para el mecanizado de formas y características complejas en 3D, tanto en superficies planas como curvas.
2. Proceso de mecanizado:
- Torneado CNC: El torneado CNC es un proceso de eliminación de material del diámetro exterior de la pieza de trabajo para crear formas cilíndricas, roscas y otras características rotacionales.
- Fresado CNC: El fresado CNC es un proceso de eliminación de material de la pieza de trabajo utilizando herramientas de corte giratorias que pueden moverse a lo largo de los ejes X, Y y Z. Puede producir varias formas, ranuras, agujeros y contornos 3D en la pieza de trabajo. Puede producir diversas formas, ranuras, orificios y contornos 3D en la pieza de trabajo.
3. Geometría de la pieza:
- Torneado CNC: El torneado CNC es el más adecuado para piezas con simetría rotacional, como ejes, pasadores y bujes. Destaca en la producción de piezas con una sección transversal circular uniforme.
- Fresado CNC: El fresado CNC es ideal para piezas con geometrías complejas, características 3D y perfiles de superficie variables. Puede crear cavidades, ranuras, escalones, chaflanes y otras formas complejas.
4. Utillaje:
- Torneado CNC: El torneado CNC utiliza herramientas de corte de un solo punto montadas en el poste de herramientas o torreta del torno. Estas herramientas tienen un único filo de corte y eliminan material a medida que la pieza gira.
- Fresado CNC: El fresado CNC utiliza herramientas de corte multipunto, como fresas o brocas, que tienen múltiples filos de corte. Las herramientas pueden moverse en múltiples direcciones y ángulos para lograr diversas acciones de corte.
5. Fijación de la pieza:
- Torneado CNC: La pieza de trabajo suele sujetarse en un mandril o pinza y gira alrededor de su eje durante el torneado CNC.
- Fresado CNC: La pieza se sujeta firmemente a la mesa o fijación de la fresadora y puede moverse en múltiples direcciones durante el fresado CNC.
En resumen, el torneado CNC y el fresado CNC son procesos de mecanizado diferentes adecuados para aplicaciones específicas. El torneado CNC es ideal para piezas cilíndricas y características rotacionales, mientras que el fresado CNC es preferible para formas 3D complejas y diversos perfiles de superficie. Los fabricantes eligen entre el torneado CNC y el fresado CNC en función del diseño de la pieza, el material y las operaciones de mecanizado necesarias.
El torneado CNC es ideal para crear piezas como ejes, pasadores y conectores.
El torneado CNC es un proceso de mecanizado versátil que puede crear una amplia gama de piezas de distinta complejidad. Es muy adecuado para producir componentes cilíndricos y giratorios, así como piezas con características que pueden mecanizarse a lo largo de la dirección axial de la pieza. Algunos tipos comunes de piezas que pueden crearse utilizando el torneado CNC incluyen:
1. Ejes: El torneado CNC se utiliza comúnmente para producir ejes de varias longitudes y diámetros utilizados en maquinaria, motores y sistemas de transmisión.
2. Pasadores y casquillos: El torneado CNC puede crear pasadores y casquillos precisos utilizados en ensamblajes y enlaces mecánicos.
3. Bridas: Las bridas, utilizadas para unir tuberías, válvulas y otros componentes, se pueden tornear mediante CNC con los orificios y características de montaje necesarios.
4. Conectores y accesorios: El torneado CNC se utiliza para fabricar conectores, acoplamientos y accesorios utilizados en fontanería, hidráulica y neumática.
5. Fijaciones: El torneado CNC puede producir tornillos, pernos, tuercas y otros tipos de elementos de fijación utilizados en diversas aplicaciones.
6. Poleas y engranajes: El torneado CNC se utiliza para crear poleas y engranajes para sistemas mecánicos de transmisión de potencia.
7. Acoplamientos: El torneado CNC puede producir acoplamientos rígidos y flexibles utilizados para conectar ejes giratorios en máquinas.
8. Piezas de automoción: El torneado CNC se utiliza habitualmente en la industria del automóvil para producir diversos componentes de motores y transmisiones, como cigüeñales, árboles de levas y ejes de transmisión.
9. Componentes médicos: El torneado CNC se utiliza para fabricar componentes de dispositivos médicos, incluidos instrumentos quirúrgicos, dispositivos implantables e implantes ortopédicos.
10. Piezas aeroespaciales: El torneado CNC se emplea en la industria aeroespacial para producir componentes como ejes de motores, discos de turbinas y piezas de trenes de aterrizaje.
11. Componentes hidráulicos y neumáticos: El torneado CNC se utiliza para crear componentes hidráulicos y neumáticos, incluyendo válvulas, pistones y cilindros.
12. Piezas eléctricas y electrónicas: El torneado CNC se utiliza para producir conectores eléctricos, terminales y carcasas para dispositivos electrónicos.
13. Aparatos de iluminación: El torneado CNC puede utilizarse para crear diversos componentes para luminarias, como portalámparas y carcasas.
14. Componentes artísticos personalizados: El torneado CNC puede producir componentes artísticos y decorativos, como torneados artísticos de madera y metalistería decorativa.
Estos son sólo algunos ejemplos de los tipos de piezas que pueden crearse utilizando el torneado CNC. El proceso ofrece resultados precisos y uniformes, lo que lo convierte en una tecnología valiosa para fabricar una amplia variedad de componentes utilizados en sectores que van desde la automoción y el aeroespacial hasta el médico, pasando por el electrónico.
El software CAD se utiliza para crear un modelo 3D de la pieza que luego se utiliza para generar las trayectorias de las herramientas para el torno CNC.
El software de diseño asistido por ordenador (CAD) desempeña un papel crucial en el torneado CNC, ya que sirve como punto de partida para crear el modelo digital de la pieza que se va a mecanizar. El software CAD se utiliza para diseñar el modelo 2D o 3D del componente, que luego se utiliza para generar las instrucciones necesarias para el torno CNC. Este es el papel del software CAD en el torneado CNC:
1. Diseño de piezas: El software CAD permite a los ingenieros y diseñadores crear el modelo digital detallado de la pieza que desean fabricar mediante torneado CNC. El software proporciona una interfaz fácil de usar para diseñar geometrías complejas, definir dimensiones y especificar tolerancias.
2. Geometría precisa: El software CAD garantiza que la geometría de la pieza se represente con precisión en el modelo digital. Esta precisión es esencial para conseguir las dimensiones y el ajuste deseados de la pieza acabada.
3. Visualización y simulación: El software de CAD proporciona una visualización en 3D de la pieza, lo que permite a los diseñadores verla desde distintos ángulos y evaluar su estética y funcionalidad. Algunos programas de CAD avanzados también permiten la simulación, lo que puede ayudar a detectar interferencias y posibles problemas de mecanizado.
4. Iteraciones de diseño: El software CAD permite a los diseñadores realizar cambios e iteraciones en el diseño de la pieza con facilidad. Esta flexibilidad tiene un valor incalculable en el proceso de diseño, ya que permite a los ingenieros optimizar el rendimiento y la fabricabilidad de la pieza.
5. 5. Modelado paramétrico: El software CAD suele admitir el modelado paramétrico, que permite a los diseñadores vincular dimensiones y relaciones entre características. Los cambios en un parámetro actualizan automáticamente las características relacionadas, agilizando el proceso de diseño.
6. Exportación de datos CAM: Una vez finalizado el diseño de la pieza, el software CAD puede exportar el modelo al software de fabricación asistida por ordenador (CAM). El software CAM utiliza el modelo CAD para generar sendas e instrucciones de código G para el torno CNC.
7. Generación de sendas: El software CAM utiliza la geometría del modelo CAD para calcular las sendas más eficaces para el torneado CNC. Determina los movimientos, avances y velocidades de la herramienta para lograr el resultado de mecanizado deseado.
8. Postprocesado: El software CAM genera un código G específico de la máquina basado en las capacidades y la configuración del torno CNC. Este código G proporciona las instrucciones necesarias para controlar la máquina durante el proceso de torneado.
9. Reutilización de diseños: El software CAD permite reutilizar los diseños de piezas existentes, ahorrando tiempo y esfuerzo a la hora de fabricar componentes similares o modificados.
In summary, CAD software is an essential tool in CNC turning, as it serves as the foundation for part design and enables seamless integration with CAM software. The CAD-to-CAM workflow streamlines the manufacturing process, ensuring that the part design is accurately translated into the machining instructions for the CNC turning machine. The use of CAD software enhances precision, accelerates design iterations, and facilitates efficient production in CNC turning operations.
El software CAM se utiliza para generar las sendas que indican a la máquina cómo eliminar material de la pieza para crear la forma deseada.
El software de fabricación asistida por ordenador (CAM) desempeña un papel fundamental en el torneado CNC, ya que sirve de puente entre el diseño de la pieza creado en el software CAD y el proceso de mecanizado real. El software CAM toma el modelo digital de la pieza diseñada en CAD y genera las sendas y las instrucciones (código G) necesarias para controlar el torno CNC. Este es el papel del software CAM en el torneado CNC:
1. Generación de trayectorias: La función principal del software CAM es generar sendas que guíen los movimientos de la herramienta de corte durante el torneado CNC. Calcula la trayectoria de herramienta más eficiente basándose en la geometría de la pieza, las características requeridas y los parámetros de mecanizado.
2. Cálculo de avances y velocidades: El software CAM determina los avances (velocidad de corte) y velocidades (velocidad de rotación del husillo) adecuados para el proceso de torneado CNC. Tiene en cuenta factores como el tipo de material, la herramienta, las fuerzas de corte y el acabado superficial deseado para optimizar los parámetros de mecanizado.
3. Simulación de eliminación de material: El software CAM puede simular el proceso de eliminación de material para visualizar cómo interactúa la herramienta de corte con la pieza de trabajo. Esta simulación ayuda a identificar posibles colisiones, interferencias o áreas que necesitan atención adicional en el proceso de mecanizado.
4. Selección y gestión de herramientas: El software CAM permite seleccionar las herramientas de corte adecuadas en función del diseño de la pieza y los requisitos de mecanizado. También gestiona las bibliotecas de herramientas y realiza un seguimiento del desgaste, la vida útil y los cambios de herramienta durante el proceso de producción.
5. Personalización y optimización: El software CAM permite a los maquinistas personalizar el proceso de mecanizado para adaptarlo a requisitos específicos. Pueden ajustar las estrategias de corte, elegir distintas trayectorias y optimizar los movimientos de las herramientas para obtener la máxima eficacia y precisión.
6. Postprocesado: Una vez generadas las sendas, el software CAM las convierte en código G legible por la máquina. El código G contiene instrucciones precisas para el torno CNC, especificando los movimientos de la herramienta, la velocidad del husillo, el avance y otros parámetros necesarios para mecanizar la pieza.
7. Mecanizado multieje: El software CAM avanzado admite el mecanizado multieje, lo que permite a los tornos CNC con ejes adicionales (como herramientas motorizadas o subhusillos) realizar operaciones complejas y crear características intrincadas.
8. Detección y corrección de errores: El software CAM incluye funciones para detectar posibles errores en las trayectorias de las herramientas, como colisiones o sobrecortes. Ofrece opciones para ajustar las trayectorias de las herramientas u optimizar la secuencia de corte para evitar problemas de mecanizado.
9. Procesamiento por lotes: El software CAM puede optimizar las trayectorias de las herramientas y los parámetros de mecanizado para múltiples piezas en un lote, lo que reduce el tiempo de preparación y mejora la eficiencia de la producción.
En resumen, el software CAM es fundamental en el torneado CNC, ya que toma el diseño de la pieza del software CAD y lo convierte en las instrucciones detalladas necesarias para el torno CNC. Al generar trayectorias de herramienta eficaces y gestionar los parámetros de mecanizado, el software CAM optimiza el proceso de fabricación, garantizando resultados precisos y uniformes durante las operaciones de torneado CNC.
Las herramientas de corte más comunes son las brocas, las fresas y las herramientas de mandrinar.
En el torneado CNC, se utilizan diversas herramientas de corte para eliminar el material de la pieza y crear la forma y las características deseadas. Estas herramientas de corte se montan en la torreta o portaherramientas del torno CNC y se seleccionan en función del material que se va a mecanizar, las características requeridas y las condiciones de corte. Algunos tipos comunes de herramientas de corte utilizadas en el torneado CNC incluyen:
1. Insertos de torneado: Son las herramientas de corte más utilizadas en el torneado CNC. Las plaquitas de torneado son herramientas de corte indexables con múltiples filos de corte. Están disponibles en varias geometrías y calidades optimizadas para materiales y condiciones de corte específicos.
2. Barras de mandrinar: Las barras de mandrinar se utilizan para ampliar orificios existentes o crear características internas con gran precisión. Están disponibles en diferentes longitudes y configuraciones para adaptarse a diversos tamaños y profundidades de perforación.
3. Herramientas de ranurado y tronzado: Las herramientas de ranurado se utilizan para cortar ranuras estrechas, rectas o contorneadas en la superficie de la pieza. Las herramientas de tronzado, también conocidas como herramientas de corte, se utilizan para separar la pieza de trabajo del material restante cortando a través del diámetro.
4. Herramientas de roscado: Las herramientas de roscado se utilizan para cortar roscas en la superficie exterior de la pieza. Se presentan en diferentes perfiles para crear distintos tipos de rosca, como roscas internas y externas.
5. Fresas de refrentar: Las fresas de refrentar se utilizan en operaciones de refrentado para crear superficies planas en el extremo de la pieza. Eliminan material del diámetro exterior de la pieza.
6. Brocas: En algunos casos, las brocas se pueden utilizar para taladrar agujeros en la pieza de trabajo en un torno CNC con capacidades de herramientas vivas.
7. Herramienta motorizada: Los tornos CNC equipados con herramientas motorizadas permiten utilizar herramientas de corte giratorias, como fresas o brocas, para realizar operaciones de fresado o taladrado en la superficie exterior de la pieza.
8. Herramientas de moleteado: Las herramientas de moleteado se utilizan para crear patrones de textura en la superficie de la pieza de trabajo para mejorar el agarre o con fines decorativos.
9. Fresas de roscar: Las fresas de roscar se utilizan para operaciones de fresado de roscas, creando roscas internas y externas utilizando un movimiento de corte helicoidal.
10. Taladros centrales: Las brocas centrales se utilizan para crear orificios iniciales precisos para las operaciones de taladrado posteriores.
Es importante seleccionar las herramientas de corte adecuadas en función del material específico, la geometría de la pieza y los requisitos de mecanizado. Los tornos CNC están diseñados para alojar una gran variedad de herramientas de corte y portaherramientas, lo que ofrece flexibilidad para realizar diversas operaciones con eficacia y lograr los resultados deseados.
El torno sujeta y hace girar la pieza mientras la herramienta de corte elimina material para crear la forma deseada.
El torno desempeña un papel fundamental en el torneado CNC, ya que es la máquina principal utilizada para realizar el proceso de torneado. En el torneado CNC, el torno es una máquina herramienta controlada por ordenador que hace girar la pieza mientras una herramienta de corte elimina material del diámetro exterior de la pieza. Las principales funciones y papeles del torno en el torneado CNC son las siguientes:
1. Rotación de la pieza: La función principal del torno es sujetar y hacer girar la pieza de trabajo. La pieza se monta en el husillo del torno y gira a una velocidad controlada. La rotación permite que la herramienta de corte elimine material y dé forma a la pieza.
2. Sujeción y sujeción de la pieza: El torno proporciona un mecanismo de sujeción seguro para sujetar e inmovilizar la pieza de trabajo durante el proceso de mecanizado. Los dispositivos de sujeción de la pieza, como mandriles o pinzas, se utilizan para sujetar la pieza y garantizar que permanezca estable durante el corte.
3. Transporte de la herramienta de corte: El torno está equipado con una torreta o portaherramientas que sujeta y posiciona la herramienta de corte. La torreta de herramientas permite utilizar varias herramientas de corte, cada una con una función específica, que pueden colocarse con rapidez y precisión según sea necesario.
4. 4. Avance y control de la herramienta: La torreta o portaherramientas del torno puede moverse a lo largo del eje de la pieza, controlando la profundidad de corte y el avance de la herramienta de corte. El sistema CNC controla con precisión este movimiento basándose en las trayectorias de herramienta programadas.
5. Generación de sendas: El sistema CNC del torno interpreta el programa de código G generado por el software CAM. Convierte las instrucciones en movimientos específicos de la herramienta y velocidades de avance, generando efectivamente las trayectorias que sigue la herramienta de corte para dar forma a la pieza de trabajo.
6. Supervisión en tiempo real: Muchos tornos CNC modernos vienen con sensores y sistemas de monitorización que proporcionan datos en tiempo real sobre el desgaste de la herramienta, el rendimiento del mecanizado y la calidad de la pieza. Esta información permite a los operarios realizar los ajustes oportunos para mantener un mecanizado eficiente y preciso.
7. Automatización y precisión: El sistema CNC del torno permite automatizar el proceso de mecanizado, lo que se traduce en cortes precisos y uniformes. Los movimientos controlados por ordenador garantizan que cada pieza se mecanice con la misma precisión, lo que reduce la variabilidad y aumenta la productividad.
8. Capacidad multitarea: Algunos tornos CNC están equipados con herramientas vivas y husillos adicionales, lo que permite capacidades multitarea. Estas máquinas pueden realizar fresado, taladrado y otras operaciones además de torneado, lo que aumenta su versatilidad.
En resumen, el torno es la máquina herramienta principal en el torneado CNC. Sujeta y gira la pieza, posiciona y mueve la herramienta de corte e interpreta el programa CNC para ejecutar operaciones de mecanizado precisas. Los tornos CNC han revolucionado el proceso de torneado, ofreciendo alta precisión, eficiencia y automatización en la producción de piezas cilíndricas y giratorias.
El mandril mantiene la pieza en su sitio mientras gira durante el proceso de torneado.
El plato es un componente crucial en el torneado CNC, ya que desempeña un papel fundamental en la sujeción y rotación seguras de la pieza durante el proceso de mecanizado. El plato es un dispositivo de sujeción especializado montado en el husillo del torno, y proporciona los medios para sujetar y posicionar firmemente la pieza de trabajo. Este es el papel del plato en el torneado CNC:
1. Sujeción de la pieza: La función principal del plato es sujetar firmemente la pieza de trabajo. Proporciona un agarre firme de la pieza de trabajo para evitar cualquier movimiento o vibración durante el mecanizado, garantizando la precisión y repetibilidad en las características mecanizadas.
2. Rotación de la pieza: El mandril está montado en el husillo del torno, y permite la rotación de la pieza de trabajo. El husillo, junto con el mandril, hace girar la pieza a una velocidad controlada, permitiendo que la herramienta de corte elimine material y dé forma a la pieza.
3. Adaptación a distintos tamaños de piezas: Los platos vienen en diferentes tamaños y configuraciones para adaptarse a una amplia gama de tamaños y formas de piezas de trabajo. Pueden diseñarse para alojar piezas pequeñas y delicadas o piezas grandes y pesadas, lo que los hace versátiles para diversas aplicaciones de mecanizado.
4. Carga rápida y fácil de la pieza: Los platos están diseñados para permitir una carga y descarga rápida y sencilla de la pieza de trabajo. Esto facilita una preparación eficaz y reduce el tiempo de inactividad entre operaciones de mecanizado.
5. Configuraciones de mordazas múltiples: Algunos platos tienen múltiples mordazas que pueden ajustarse para sujetar diversas formas y diámetros de piezas de trabajo. Las mordazas pueden moverse hacia dentro o hacia fuera para sujetar con seguridad la pieza de trabajo.
6. Precisión y repetibilidad: Los platos se fabrican con gran precisión para garantizar una sujeción constante y repetible de la pieza. Esto es fundamental para mantener la precisión dimensional y la uniformidad en las piezas mecanizadas.
7. Posicionamiento de las mordazas: En el torneado CNC, las mordazas del plato pueden posicionarse con precisión utilizando el sistema de control del torno. Esto permite un centrado rápido y preciso de la pieza, garantizando una alineación adecuada con la herramienta de corte.
8. Expansión y contracción: Algunos platos, conocidos como platos de pinza, pueden expandirse y contraerse para sujetar diferentes diámetros de pieza sin necesidad de ajustar las mordazas. Los mandriles de pinza son especialmente útiles para piezas de pequeño diámetro.
En resumen, la función principal del plato en el torneado CNC es sujetar y girar la pieza de forma segura, proporcionando una configuración estable y precisa para el proceso de mecanizado. Su precisión y flexibilidad contribuyen a la eficacia general y al éxito de la operación de torneado CNC, permitiendo la producción de piezas cilíndricas y giratorias de alta calidad.
El contrapunto proporciona apoyo a la pieza durante el proceso de torneado y puede utilizarse para sujetar herramientas de corte.
El contrapunto es un componente esencial en el torneado CNC, ya que cumple múltiples funciones que contribuyen al proceso de mecanizado global. Está situado en el extremo opuesto del torno respecto al plato y proporciona un soporte adicional a la pieza durante el mecanizado. El contrapunto desempeña las siguientes funciones en el torneado CNC:
1. Apoyo de la pieza: La función principal del contrapunto es proporcionar apoyo adicional a la pieza de trabajo, especialmente cuando se mecanizan piezas largas o esbeltas. Ayuda a minimizar la desviación o flexión de la pieza debido a las fuerzas de corte, garantizando la precisión dimensional y el acabado superficial.
2. Centrado y alineación: El contrapunto está equipado con un centro, conocido como centro del contrapunto o punto muerto, que puede alinearse con precisión con el centro de la pieza de trabajo. Esta alineación asegura que la pieza gire concéntricamente con el husillo del torno, dando como resultado un mecanizado preciso y centrado.
3. Operaciones de taladrado y mandrinado: El contrapunto puede extenderse o retraerse para adaptarse a varias longitudes de pieza de trabajo. Esta característica permite utilizar el contrapunto para operaciones de taladrado y mandrinado, en las que se utiliza una herramienta de corte estacionaria para crear orificios o ampliar orificios existentes en la pieza de trabajo.
4. Contrapeso: En algunas aplicaciones de torneado CNC, las piezas largas pueden provocar un desequilibrio en el husillo de la máquina debido a su peso. El contrapunto puede utilizarse para contrapesar el peso de la pieza, reduciendo las vibraciones y mejorando la estabilidad del mecanizado.
5. Montaje de luneta: El contrapunto puede utilizarse para soportar una luneta, un dispositivo especializado utilizado para estabilizar y soportar piezas de trabajo largas y delgadas durante el mecanizado. La luneta reduce la desviación de la pieza y garantiza unos resultados de mecanizado uniformes.
6. Torneado cónico: El contrapunto se puede ajustar para crear una ligera conicidad en la pieza de trabajo si es necesario para el diseño o la aplicación de la pieza específica.
7. 7. Lubricación: Algunos contrapuntos están equipados con sistemas de lubricación para reducir la fricción entre el centro del contrapunto y la pieza, permitiendo una rotación suave durante el mecanizado.
8. Desbloqueo rápido: Muchos tornos CNC modernos tienen un mecanismo de liberación rápida para el contrapunto, lo que permite posicionarlo y retirarlo rápidamente cuando no se necesita.
El contrapunto es un elemento valioso en el torneado CNC, ya que proporciona soporte, estabilidad y alineación adicionales para la pieza de trabajo durante el mecanizado. Su uso mejora la precisión del mecanizado y permite una gama más amplia de operaciones, lo que lo convierte en una herramienta versátil en el proceso de torneado CNC.
Un torno CNC está controlado por ordenador y puede producir piezas más complejas con mayor precisión que un torno manual.
La principal diferencia entre un torno CNC y un torno manual radica en el método de funcionamiento y el nivel de automatización que ofrecen. Ambas máquinas se utilizan para operaciones de torneado, pero difieren significativamente en términos de control, configuración y capacidades. Estas son las principales diferencias entre un torno CNC y un torno manual:
1. Control y funcionamiento:
- Torno CNC: CNC significa Control Numérico por Ordenador. En un torno CNC, el proceso de mecanizado está automatizado y controlado por ordenador. El operario utiliza software CAD/CAM para crear un modelo digital de la pieza y generar las trayectorias de las herramientas. A continuación, la máquina CNC lee las instrucciones del código G y controla automáticamente los movimientos de la herramienta de corte, el husillo y otras funciones de la máquina.
- Torno manual: Un torno manual, por otro lado, es operado enteramente por el maquinista. El operario ajusta manualmente la posición de la herramienta de corte, controla la velocidad del husillo y desplaza a mano la herramienta de corte a lo largo de la pieza de trabajo mediante diversos controles manuales y volantes.
2. Programación y configuración:
- Torno CNC: La programación de un torno CNC implica la creación de un diseño de pieza mediante software CAD y la generación del programa de código G con software CAM. La configuración también incluye la carga de la pieza de trabajo, las herramientas y las compensaciones de las herramientas, así como la definición de los parámetros de corte. Una vez configurado, el torno CNC puede producir repetidamente piezas idénticas con gran exactitud y precisión.
- Torno manual: En un torno manual, la configuración y el funcionamiento requieren más mano de obra. El operario coloca y fija manualmente la pieza y las herramientas, ajusta los parámetros de corte y maneja manualmente la máquina durante todo el proceso de torneado. El proceso requiere habilidad y experiencia para lograr resultados consistentes.
3. Automatización y productividad:
- Torno CNC: Los tornos CNC están altamente automatizados, lo que permite un funcionamiento desatendido y una mayor productividad. Una vez configurado el programa, la máquina puede funcionar de forma continua, produciendo piezas con una intervención mínima del operario. Los tornos CNC también pueden realizar operaciones de mecanizado complejas y capacidades multitarea.
- Torno manual: Los tornos manuales están menos automatizados y requieren una operación manual continua por parte del maquinista. Esto los hace más lentos y menos productivos en comparación con los tornos CNC, especialmente para producciones de gran volumen.
4. Complejidad de las piezas:
- Torno CNC: Los tornos CNC son capaces de mecanizar piezas complejas con geometrías y características intrincadas. El control CNC permite posicionar y mover la herramienta con precisión, lo que posibilita la creación de formas y diseños más complejos.
- Torno manual: Los tornos manuales son los más adecuados para piezas más sencillas con geometrías simples. La creación de características intrincadas o formas complejas es más difícil y requiere más tiempo en un torno manual.
En resumen, un torno CNC es una máquina más avanzada y automatizada que ofrece mayor productividad, versatilidad y capacidad para producir piezas complejas con mayor precisión. Un torno manual, por el contrario, requiere operarios cualificados, ofrece una automatización limitada y es más adecuado para tareas de torneado más sencillas. La elección entre un torno CNC y un torno manual depende de las necesidades específicas de fabricación, la complejidad de la pieza y el nivel de automatización requerido para el proceso de producción.
El operario es responsable de preparar la máquina, seleccionar las herramientas adecuadas y supervisar el proceso de torneado.
El operario desempeña un papel crucial en el torneado CNC a pesar del alto nivel de automatización que proporciona el sistema CNC. Aunque gran parte del proceso de mecanizado está automatizado, la participación del operario es esencial para garantizar que el torno CNC funcione de forma eficaz, segura y produzca piezas de alta calidad. Estas son algunas de las funciones clave del operario en el torneado CNC:
1. Configuración del programa: El operario es responsable de configurar el torno CNC con el programa correcto. Esto implica cargar el programa de código G adecuado en el sistema de control de la máquina, que define las trayectorias de las herramientas, los parámetros de corte y otras instrucciones para el proceso de mecanizado.
2. Colocación de la pieza: El operario carga la pieza de trabajo en el mandril o pinza y se asegura de que está bien sujeta y alineada con el husillo del torno. La colocación correcta de la pieza de trabajo es fundamental para obtener resultados de mecanizado precisos y uniformes.
3. Colocación de herramientas: El operario instala las herramientas de corte en la torreta o portaherramientas del torno. Esto incluye seleccionar las herramientas de corte adecuadas, instalarlas correctamente y ajustar las compensaciones de las herramientas para garantizar un posicionamiento preciso de las mismas.
4. Calibración de la máquina: El operario puede realizar comprobaciones periódicas de calibración y alineación de la máquina para asegurarse de que funciona dentro de las tolerancias especificadas. Esto ayuda a mantener la precisión y el rendimiento general de la máquina.
5. 5. Supervisión e inspección: El operario supervisa el proceso de torneado CNC, observando el funcionamiento de la máquina y asegurándose de que todo funciona correctamente. También puede inspeccionar las piezas mecanizadas para comprobar su calidad, dimensiones y acabado superficial.
6. Cambios de herramienta y mantenimiento: El operario puede ser responsable de los cambios de herramienta durante el proceso de mecanizado, especialmente en trabajos que requieren múltiples configuraciones de herramienta. Además, puede realizar el mantenimiento rutinario de las herramientas, como la sustitución de herramientas desgastadas o dañadas.
7. 7. Resolución de problemas: En caso de rotura de la herramienta, errores del programa u otros problemas, el operario es responsable de localizar y resolver los problemas para minimizar el tiempo de inactividad y mantener la productividad.
8. Optimización del proceso: El operario puede realizar ajustes en los parámetros de corte, trayectorias y otros ajustes para optimizar el proceso de mecanizado, mejorar la eficiencia y conseguir una mejor calidad de la pieza.
9. Cumplimiento de las normas de seguridad: El operario garantiza el cumplimiento de los protocolos y procedimientos de seguridad durante las operaciones de torneado CNC, promoviendo un entorno de trabajo seguro para sí mismo y para los demás.
10. Gestión de la vida útil de las herramientas y de los materiales: El operario realiza un seguimiento de la vida útil de las herramientas y puede ser responsable de la gestión del inventario de herramientas. También puede gestionar las existencias de material, garantizando un suministro adecuado para la producción continua.
11. Mantenimiento de la máquina: Aunque no todas las tareas de mantenimiento de la máquina son realizadas por el operario, éste puede participar en tareas rutinarias de limpieza, lubricación y mantenimiento sencillo para mantener el torno CNC en buenas condiciones de funcionamiento.
En resumen, el papel del operario en el torneado CNC es fundamental para el éxito general del proceso de mecanizado. Sus responsabilidades incluyen la configuración, la supervisión, la inspección, la resolución de problemas y la optimización del proceso. Con operarios cualificados y bien informados, las operaciones de torneado CNC pueden funcionar de forma eficaz, produciendo piezas de alta calidad con un mínimo de tiempos de inactividad y residuos.
El torneado CNC es ideal para crear piezas pequeñas con gran precisión y exactitud.
El torneado CNC es idóneo para la fabricación de piezas pequeñas debido a su precisión, repetibilidad y capacidad para producir con eficacia grandes volúmenes de componentes pequeños. El proceso se utiliza ampliamente en industrias que requieren la producción de piezas pequeñas e intrincadas con tolerancias estrechas. He aquí algunas formas en que el torneado CNC puede utilizarse eficazmente en la fabricación de piezas pequeñas:
1. Alta precisión: Los tornos CNC ofrecen una precisión excepcional, permitiendo el mecanizado exacto de piezas pequeñas con tolerancias estrechas. Los movimientos controlados por ordenador de la herramienta de corte garantizan resultados uniformes, asegurando que cada pieza pequeña se produzca según las especificaciones exactas.
2. Automatización y eficacia: El torneado CNC está altamente automatizado, lo que lo hace ideal para la producción en masa de piezas pequeñas. Una vez configurado el programa CNC, la máquina puede funcionar de forma continua, produciendo piezas idénticas con una intervención mínima del operario, lo que se traduce en una alta productividad.
3. Capacidad multitarea: Algunos tornos CNC avanzados vienen con capacidades multitarea, lo que significa que pueden realizar múltiples operaciones en una sola configuración. Esto permite la producción de piezas pequeñas con características complejas sin necesidad de máquinas o configuraciones adicionales.
4. Versatilidad de materiales: El torneado CNC puede utilizarse con una amplia gama de materiales, incluidos metales, plásticos y materiales compuestos. Esta versatilidad permite fabricar piezas pequeñas para diversas industrias y aplicaciones.
5. Preparación y cambio rápidos: Los tornos CNC permiten una configuración y un cambio rápidos y sencillos entre diferentes series de piezas. Esta flexibilidad es ventajosa cuando se fabrican lotes pequeños de varias piezas.
6. Consistencia y control de calidad: El torneado CNC asegura resultados consistentes y repetibles, críticos para mantener el control de calidad en la producción de piezas pequeñas. Reduce la variabilidad y la probabilidad de defectos, garantizando que cada pieza cumpla los estándares exigidos.
7. Reducing Waste: CNC turning is a subtractive manufacturing process, meaning it removes material to create the final part. This reduces material waste compared to other manufacturing methods like casting or molding.
8. Opciones de herramientas pequeñas: Los tornos CNC pueden acomodar herramientas de corte pequeñas, lo que permite la creación de características intrincadas y detalles finos en piezas pequeñas.
9. Operaciones secundarias: El torneado CNC puede combinarse con otros procesos de mecanizado como el fresado, taladrado y roscado para realizar operaciones adicionales en piezas pequeñas, mejorando aún más su complejidad y funcionalidad.
10. Escalabilidad: El torneado CNC es escalable, lo que permite a los fabricantes ajustar los volúmenes de producción en función de la demanda. Es igual de eficiente para producir pequeñas cantidades o series de producción a gran escala de piezas pequeñas.
En resumen, el torneado CNC es un método versátil y eficaz para fabricar piezas pequeñas con gran precisión y uniformidad. Su automatización, versatilidad y capacidad para manejar características complejas lo convierten en una opción ideal para una amplia gama de industrias que requieren componentes pequeños e intrincados.
Entre los retos más comunes se encuentran el desgaste de las herramientas, las vibraciones y la eliminación de virutas.
El torneado CNC es un sofisticado proceso de mecanizado que ofrece numerosas ventajas, pero también conlleva algunos retos que los fabricantes deben abordar para garantizar el éxito y la eficacia de las operaciones. Algunos retos comunes en el torneado CNC incluyen:
1. Desgaste y vida útil de la herramienta: Las herramientas de corte utilizadas en el torneado CNC están sujetas a desgaste y degradación debido a las fuerzas de corte de alta velocidad y a la fricción. Gestionar el desgaste y la vida útil de la herramienta es crucial para mantener la precisión de la pieza, el acabado superficial y reducir el tiempo de inactividad por cambio de herramienta.
2. Control de virutas: Las virutas generadas durante el proceso de torneado pueden causar problemas si no se controlan eficazmente. Una evacuación inadecuada de la viruta puede provocar atascos de viruta, daños en la herramienta y afectar al rendimiento del proceso de mecanizado.
3. Desviación de la pieza: Cuando se mecanizan piezas largas o delgadas, la pieza puede sufrir desviaciones debido a las fuerzas de corte, lo que provoca imprecisiones en las dimensiones de la pieza y en el acabado superficial. Es necesario considerar cuidadosamente el soporte de la pieza y el posicionamiento de la herramienta para minimizar la deflexión.
4. Selección del material de la pieza: Los diferentes materiales tienen características de mecanizado distintas, y algunos materiales, como las aleaciones de alta temperatura o los aceros endurecidos, pueden ser difíciles de mecanizar. Seleccionar las herramientas de corte y los parámetros de corte adecuados para materiales específicos es crucial para lograr resultados óptimos.
5. Errores de programación: El torneado CNC depende de una programación precisa del código G. Los errores de programación pueden provocar colisiones de herramientas, trayectorias incorrectas y otros problemas de mecanizado. La verificación exhaustiva del programa de CNC y la realización de simulaciones pueden ayudar a evitar errores costosos.
6. Acabado superficial: Conseguir el acabado superficial deseado puede ser un reto, especialmente cuando se mecanizan geometrías complejas o materiales duros. La selección adecuada de la herramienta, los parámetros de corte y las estrategias de trayectoria de la herramienta son esenciales para lograr la calidad superficial requerida.
7. Gestión del calor: El calor generado durante el proceso de mecanizado puede afectar al rendimiento de la herramienta y provocar la dilatación térmica de la pieza, afectando a la precisión de la pieza. Las estrategias eficaces de gestión del calor, como el uso de refrigerante y las velocidades de corte adecuadas, son cruciales.
8. Mecanizado de formas complejas: El torneado CNC es muy adecuado para piezas giratorias, pero el mecanizado de formas 3D complejas puede requerir operaciones adicionales o métodos de mecanizado alternativos.
9. Tiempo de preparación y cambios: La configuración del torno CNC para una nueva pieza o el cambio de herramientas puede llevar tiempo y puede afectar a la eficiencia de la producción, especialmente cuando se trata de lotes pequeños o cambios de trabajo frecuentes.
10. Complejidades multitarea: Algunos tornos CNC avanzados ofrecen capacidades multitarea, que implican operaciones simultáneas de torneado, fresado y otras. La gestión de estas operaciones complejas requiere conocimientos de programación y experiencia por parte del operario.
11. Sujeción de la pieza y portapiezas: Asegurar y sujetar la pieza durante el mecanizado es crucial para la precisión y estabilidad de la pieza. Es esencial elegir las soluciones de sujeción adecuadas para las distintas geometrías de las piezas.
Al comprender y abordar estos retos, los fabricantes pueden optimizar las operaciones de torneado CNC, mejorar la productividad y lograr resultados de alta calidad en sus procesos de fabricación. El mantenimiento periódico, los operarios cualificados y la mejora continua de los procesos contribuyen a superar estos retos y a garantizar el éxito del torneado CNC.