Servicios personalizados de fundición a presión de metal
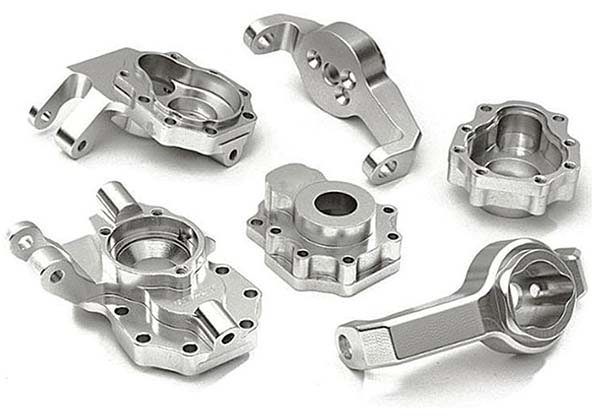
What Is Die Casting?
Definition & Core Principles: Die casting is a high-pressure manufacturing process where molten metal alloys are injected into reusable metal molds (dies) to form precise, complex components. Using pressures ranging from 10 to 175 MPa, this method ensures tight tolerances (±0.05mm typical) and intricate details, making it ideal for high-volume production. At Yigu Technology, we leverage 20+ years of expertise to deliver defect-free parts, from prototype to mass production.
Types of Die Casting: Choosing the Right Process
Hot Chamber vs. Cold Chamber Die Casting
Process Type | How It Works | Ideal Materials | Advantages | Typical Applications |
Hot Chamber Die Casting | Melting pot integrated with the machine; molten metal is directly injected via a piston. | Cinc, Tin, Lead Alloys | Faster cycle times (5 - 15 seconds), lower cost for small parts. | Electronics housings, hardware |
Cold Chamber Die Casting | Separate melting unit; molten metal is transferred to the injection chamber before casting. | Handles higher melting points, suitable for large/heavy components. | Automotive engine parts, aerospace components |
Specialty Techniques
- Vacuum Die Casting: This technique is a game - changer for applications demanding high - strength components. By evacuating air from the die cavity before injection, it can reduce gas porosity by up to 90%. In the aerospace industry, where component integrity is non - negotiable, vacuum die - cast parts are used in critical structures to ensure maximum strength - to - weight ratios.
- Thixomolding: Exclusive to magnesium alloys, thixomolding uses semi - solid metal. This allows for the creation of ultra - thin walls (less than 1mm), which is a boon for the 3C product industry. Devices like smartphones benefit from thixomolded magnesium alloy frames, which are both lightweight and offer enhanced ductility, improving the overall durability of the product.
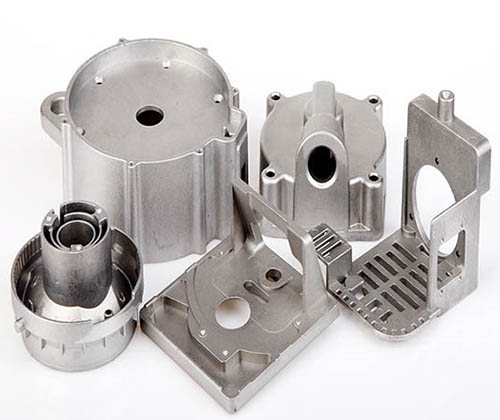
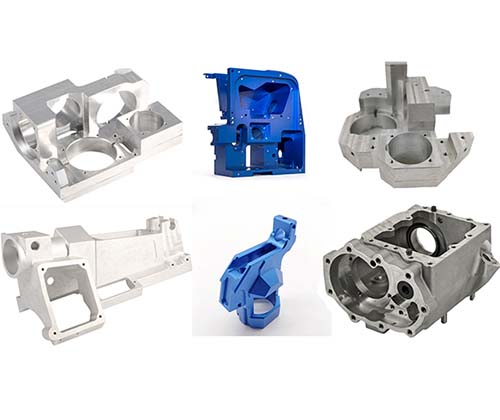
Material Selection: Matching Alloys to Your Needs
Common Die Casting Alloys & Their Strengths
Alloy | Key Properties | Aplicaciones | Yigu’s Material Standards |
Aluminum Alloys | Lightweight (density: 2.7g/cm³), excellent thermal conductivity, corrosion resistance. | Automotive brackets, heat sinks, consumer electronics. | ISO 6722 - certified alloys (e.g., ADC12, A380), tested for tensile strength (≥260MPa). |
Cinc Alloys | High dimensional stability (shrinkage: 0.3 - 0.4%), cost - effective, easy to plate. | Door handles, electrical connectors, automotive interiors. | Zamak 3/5 alloys with <0.005% impurity content, salt spray test resistance (500+ hours). |
Magnesium Alloys | Ultra - lightweight (density: 1.8g/cm³), highest strength - to - weight ratio (UTS: 240 - 300MPa). | Aerospace brackets, EV battery casings, sports equipment. | AZ91D alloy with tight impurity control (Fe <0.004%, Ni <0.001%). |
Surface Treatments: Enhancing Function & Aesthetics
Comprehensive Post-Processing Solutions
Treatment Type | Purpose | Finish Options | Performance Metrics |
Anodizing | Corrosion resistance, surface hardening (HV 300+), dielectric protection. | Clear, colored (anodic oxide thickness: 5-25μm). | Salt spray test: 1,000+ hours for aluminum parts. |
Electroplating | Decorative finishes, improved wear resistance (e.g., nickel, chrome, gold plating). | Glossy, matte, textured. | Adhesion tested via cross-cut (ISO 2409: Grade 0). |
Powder Coating | Durable, uniform coating for outdoor applications. | 100+ color options, thickness: 60-100μm. | Impact resistance: 50kg·cm, UV resistance (ASTM G154: 1,000 hours). |
Chromate Conversion | Rust prevention for zinc/magnesium alloys. | Clear or yellow chromate conversion. | Neutral salt spray: 200+ hours for zinc parts. |
Applications: Where Die Casting Shines
Industry-Leading Solutions
- Automoción: In the automotive industry, die casting is used for a variety of components. Engine components such as cylinder heads require high - temperature resistance and good heat dissipation properties. Die - cast cylinder heads can meet these requirements with their excellent thermal conductivity. Transmission cases need to withstand high mechanical stress, and die - cast ones, made from high - strength alloys, can handle the torque and forces involved. Structural brackets, with a tensile strength of ≥280MPa, are essential for vehicle safety and stability. They support various parts of the vehicle and are designed to be lightweight yet strong. In the era of electric vehicles (EVs), die - cast lightweight parts are used to reduce the vehicle's overall weight, which in turn improves battery efficiency and driving range.
- Aerospace: The aerospace industry demands components with the highest quality and reliability. Wing brackets, often made from magnesium alloys, are critical for aircraft structural integrity. These brackets have a fatigue strength of ≥120MPa, ensuring they can withstand the repeated stress during flight. Avionics housings, which protect sensitive electronic equipment, are often vacuum - cast to achieve a density of 99.9%. This high - density casting reduces the risk of porosity, which could compromise the performance of the electronics in harsh aerospace environments.
- Electrónica: Heat dissipation is a major concern in electronics. Laptop frames made from aluminum alloys, with a thermal conductivity of 180W/m·K, are designed to efficiently transfer heat away from the internal components, ensuring stable operation. Waterproof connectors are crucial for devices used in wet or humid environments. With IP67 - rated surface treatments, these die - cast connectors can prevent water ingress and protect the electrical connections.
- Medical Devices: Surgical instrument handles require a high - quality surface finish for easy cleaning and a comfortable grip. Biocompatible anodizing, with a surface roughness of Ra ≤0.8μm, provides a smooth, non - reactive surface. Components used in MRI machines need to be MRI - compatible, and die - casting can produce parts made from non - ferromagnetic materials that do not interfere with the magnetic field, ensuring accurate imaging.
Why Choose Yigu Technology for Your Die Casting Needs?
Unmatched Expertise & Technical Excellence
- Design - to - Production Prowess: Our team consists of over 50 certified engineers, 15 of whom have more than 20 years of experience in the die - casting industry. We utilize advanced CAD/CAM software such as SolidWorks and AutoCAD to optimize mold flow. This not only ensures the highest quality of the final product but also reduces scrap rates to less than 1.5%. Our engineers work closely with clients from the initial design stage, providing valuable insights and suggestions to improve product functionality and manufacturability.
- State - of - the - Art Facilities: Equipped with 30+ die - casting machines, ranging from 80 - 1,200 tons in clamping force, we can handle projects of various sizes and complexities. Our 24/7 automated CNC machining centers offer a positioning accuracy of ±0.01mm, ensuring the tightest tolerances. Additionally, our in - house mold fabrication capabilities mean we can produce complex molds in just 25 - 35 days, significantly reducing lead times.
- Rigorous Quality Assurance: We hold ISO 9001:2015, IATF 16949 certifications, demonstrating our commitment to quality. Every part undergoes more than 10 inspections, including X - ray flaw detection and CMM dimensional analysis. We maintain a 5 - year retention period for inspection reports, providing our clients with complete traceability and peace of mind.
Customer - Centric Advantages
Benefit | How We Deliver | Data Backing |
Fast Turnaround | We can produce prototypes in just 15 days. For mass production of 100,000+ parts, the lead time is 4 - 6 weeks. Our efficient production processes and streamlined supply chain management enable us to achieve a 98% on - time delivery rate (Year - to - Date 2024). | 98% on - time delivery rate (2024 YTD). |
Cost - Efficiency | Through modular mold design, we can reduce tooling costs by 20%. Our LED - lit, automated production lines also result in 15% energy savings. Overall, clients can expect an average project cost savings of 12 - 18%. | Average project cost savings: 12 - 18%. |
Sustainability | We are committed to environmental responsibility. We recycle 95% of scrap metal and reduce water usage by 30% through the use of closed - loop cooling systems. Our facilities are RoHS/REACH compliant and ISO 14001 - certified, reflecting our dedication to sustainable manufacturing. | RoHS/REACH compliant, ISO 14001 - certified facilities. |
Die Casting FAQs: Your Questions Answered
We accept MOQs as low as 500 pieces for prototyping, with scalable pricing for volumes over 10,000 units. This flexibility allows both small - scale startups and large - scale manufacturers to benefit from our die - casting services. Whether you're in the initial stages of product development or ramping up for mass production, we've got you covered.
Yes, using thixomolding for magnesium or vacuum die casting for aluminum, achieving uniform filling and structural integrity. Thixomolding, exclusive to magnesium alloys, enables the creation of ultra - thin walls by using semi - solid metal. Vacuum die casting for aluminum also ensures that even with a wall thickness of less than 1mm, the component can be filled uniformly and maintain its structural integrity.
Our molds are precision - machined to ±0.01mm, and we use 3D scanning (CMM) to verify 100% of critical dimensions post - casting. Our state - of - the - art mold - making facilities allow us to machine molds with extremely tight tolerances. After casting, we use 3D scanning technology, also known as Coordinate Measuring Machine (CMM) inspection, to verify the dimensions of every critical feature on the part, ensuring that it meets your exact specifications.
Aluminum - silicon (Al - Si) alloys with 12 - 14% silicon content, offering thermal stability and creep resistance. These alloys are specifically designed to withstand high - temperature applications. The silicon content in the alloy provides thermal stability, preventing the material from deforming or losing its mechanical properties at elevated temperatures. The creep resistance ensures that the part can maintain its shape and integrity even under long - term exposure to high - temperature and stress conditions.
Yes, electropolished finishes and PTFE coatings compliant with FDA 21 CFR Part 177.2600 for medical/consumer applications. Our electropolished finishes remove surface impurities, creating a smooth, non - porous surface that is easy to clean and resistant to bacterial growth. The PTFE coatings offer additional non - stick and chemical - resistant properties, making them suitable for applications where contact with food or medical substances is involved. Both treatments are compliant with the strict FDA regulations, ensuring the safety and quality of your products.
Our Six Sigma - driven processes achieve a defect rate of 0.36%, well below the industry average of 1.2%. We have implemented Six Sigma methodologies across our entire production process, from design to delivery. This includes rigorous process control, employee training, and continuous improvement initiatives. By closely monitoring and analyzing every step of the production process, we are able to identify and eliminate potential sources of defects, resulting in a defect rate that is significantly lower than the industry standard.
Every order includes a detailed QC report with material composition, mechanical properties, and inspection results. Our quality control reports are comprehensive and provide all the necessary information about the materials used in your order. The material composition section details the exact chemical makeup of the alloy, while the mechanical properties section includes data on tensile strength, hardness, and other key characteristics. The inspection results section outlines the findings of our various quality control checks, giving you complete transparency and confidence in the quality of your products.
We offer full transparency via design reviews, 3D mold simulations, and sample approval before production. Our team of experienced engineers welcomes your input throughout the mold - design process. We conduct regular design reviews where you can provide feedback and suggestions. Our 3D mold simulations allow you to visualize the casting process and identify any potential issues before production begins. And we always obtain your sample approval before moving forward with mass production, ensuring that the final product meets your expectations.
DDP/DAP Incoterms, with expedited shipping (3 - 5 days via air) and sea freight for large volumes (20 - 30 days). We offer a range of shipping options to meet your specific needs. For urgent orders, we provide expedited air freight services that can deliver your products in just 3 - 5 days. For larger volume orders where cost - effectiveness is a priority, we offer sea freight options with a transit time of 20 - 30 days. We also work with DDP (Delivered Duty Paid) and DAP (Delivered at Place) Incoterms, which means we take care of all the customs clearance and delivery arrangements, making the shipping process as seamless as possible for you.
Yes, the integration of inserts, sub - components, and final packaging, reducing your supply chain complexity. Our post - production assembly services are designed to simplify your supply chain. We can integrate inserts, such as threaded inserts or bushings, into your die - cast parts. We can also assemble sub - components, such as attaching brackets or connectors, and provide final packaging services. This one - stop solution saves you time and resources, allowing you to focus on your core business activities.
Contact Yigu Technology today to transform your design into high - precision die - cast components—where engineering expertise meets manufacturing excellence.