Producto de piezas de plástico de moldeo por inyección
Testigo de reputación de precisión de China
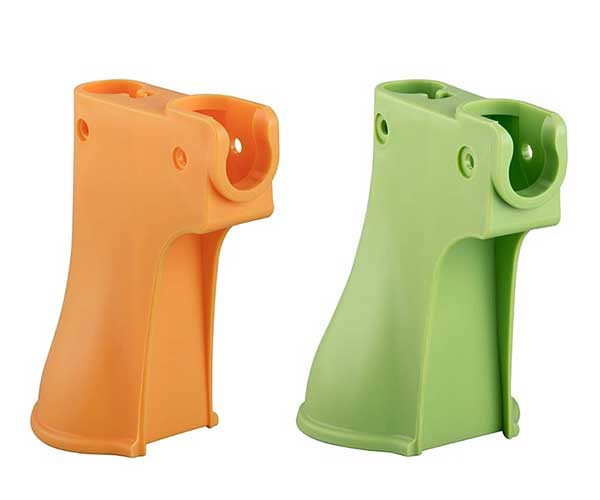
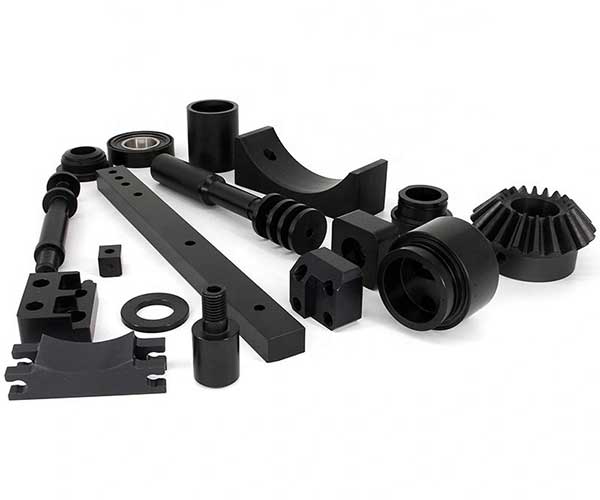
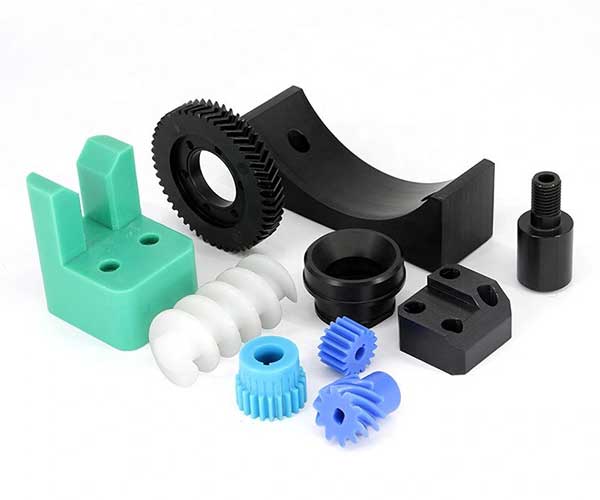
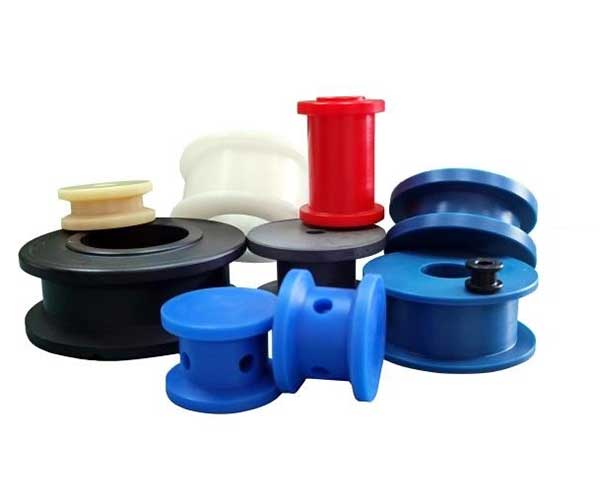
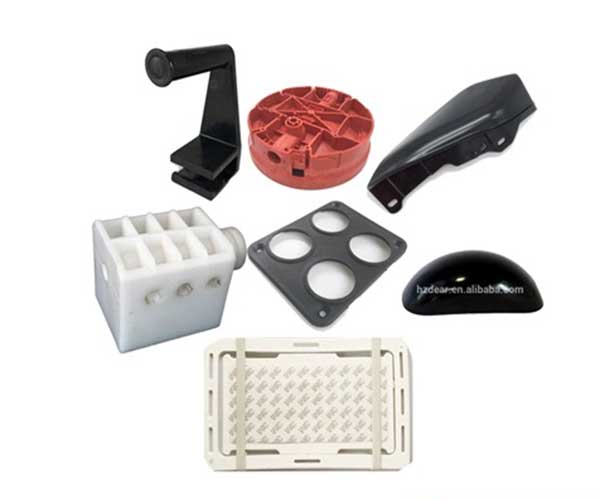
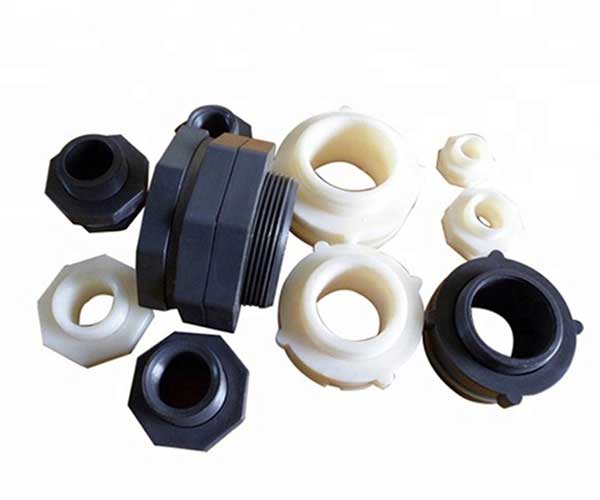
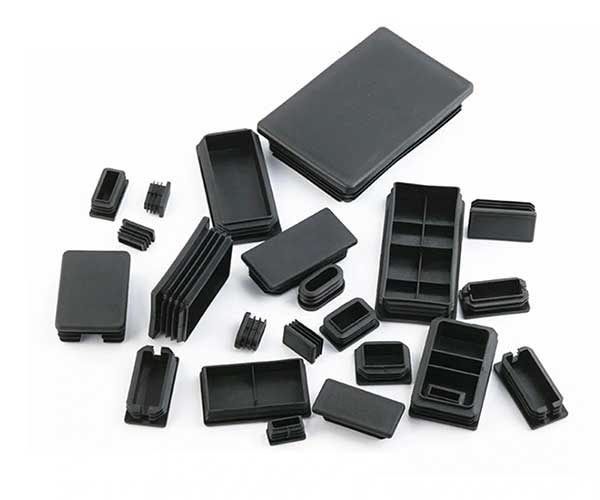
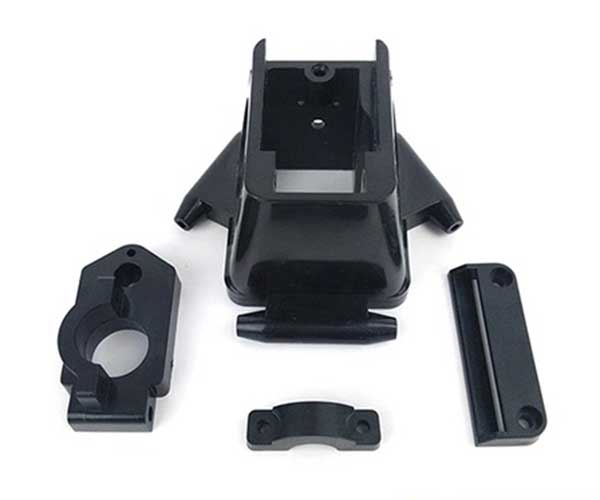
Problemas de procesamiento de moldeo por inyección
Do you have the following problems when customizing plastic products?
Medidas de optimización del moldeo por inyección
Not only injection molding, but also optimization measures
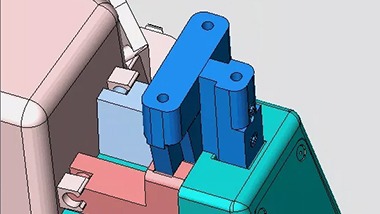
Pretratamiento de materiales
De acuerdo con la diferente absorción de agua de los diferentes materiales, algunos materiales necesitan ser secados antes de su procesamiento para eliminar la humedad en los materiales, con el fin de reducir la proporción de productos defectuosos en el proceso de moldeo por inyección.
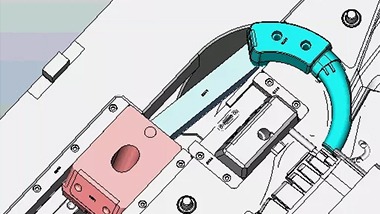
Mantenimiento del estado de los equipos de moldeo por inyección
Moldeo por inyección machine is a high-precision equipment, in which the tacit understanding of the division of labor and cooperation of various systems is very high. Maintaining a good working state can not only operate more efficiently, but also reduce the bad probability in the production process
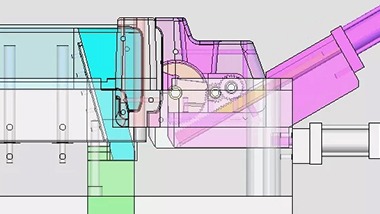
Mantenimiento del moho
Los moldes eficientes son importantes, pero también es muy importante mantener el funcionamiento constante y eficiente de los moldes. Mantener los moldes en buenas condiciones incluye principalmente: mantener los moldes limpios, evitar el desgaste, sustituir a tiempo las piezas desgastadas, mantener la lubricación, controlar la influencia de la diferencia de temperatura, ajustar a tiempo el estado, etc.
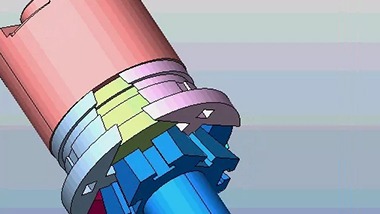
Optimización del diseño de matrices
Durante el proceso de desarrollo, es necesario desarrollar el molde de acuerdo con las propiedades básicas de las materias primas aplicadas. Diseñar la dirección del flujo, la presión uniforme y la emisión de gas de la masa fundida en la cavidad del molde es el componente clave para reducir la dificultad del moldeo por inyección y mejorar la eficiencia de la producción. Un molde de moldeo eficiente es muy importante
Diseño, fabricación de moldes, producción y montaje
¿Qué podemos hacer exactamente?
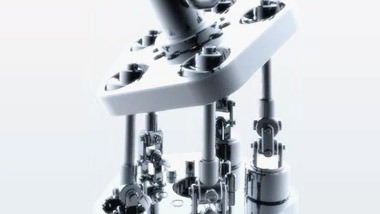
Diseño de moldes
>Proporcionar muestras, dibujos y requisitos, y proporcionar optimización de dibujos y apoyo al diseño y eficiencia.
>Buena optimización de la estructura de moldes de inyección y prestación de servicios de desarrollo de moldes de alta eficacia
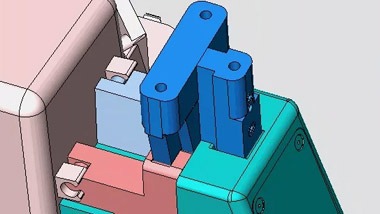
Fabricación de moldes
>De acuerdo con los requisitos de la estructura del producto y el rendimiento del producto, diseñar razonablemente la estructura del molde y cooperar con el software 3D para el análisis del flujo del molde.
>Utilice la impresión de placas láser 3D para que sus muestras cumplan los requisitos de una sola vez
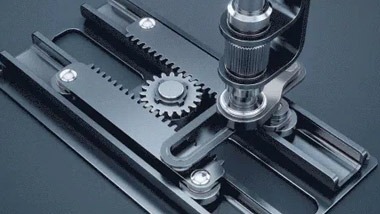
Producción de productos
>Producción de lotes tras la determinación de muestras
>Con un equipo completo de gestión de la producción y equipos, puede realizar entregas puntuales y rápidas de hasta una semana.
Pantalla de equipos de moldeo por inyección
Acelerar el desarrollo de nuevos productos y garantizar una producción de moldeo por inyección continua y estable
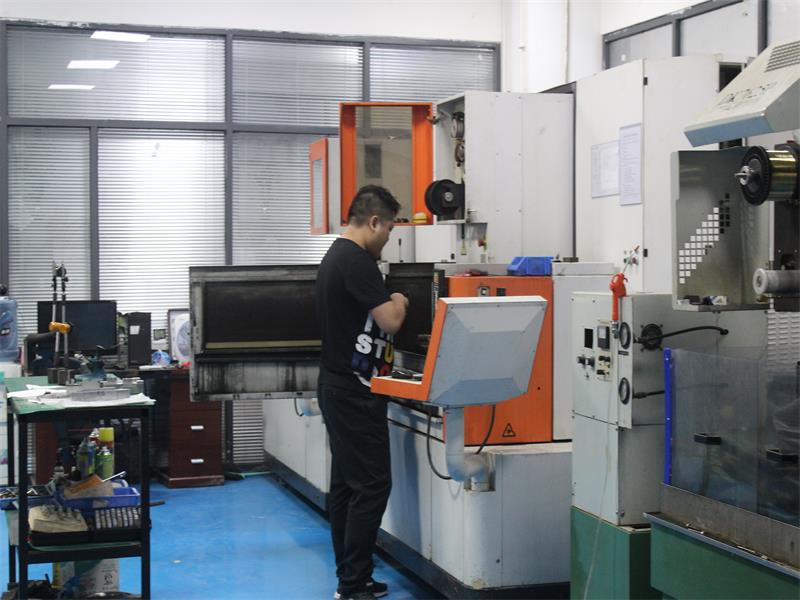
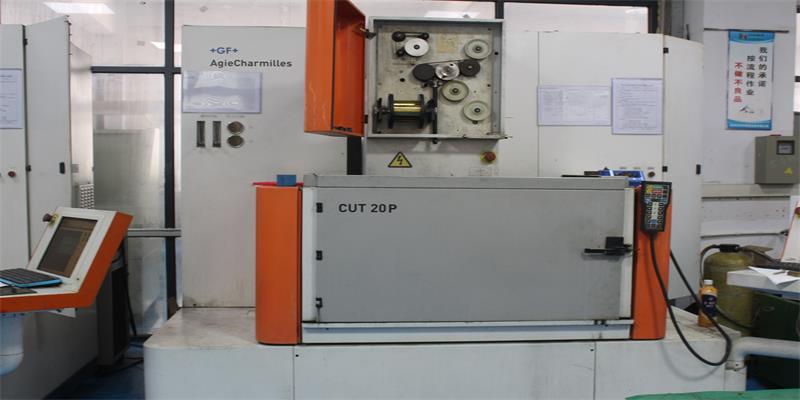
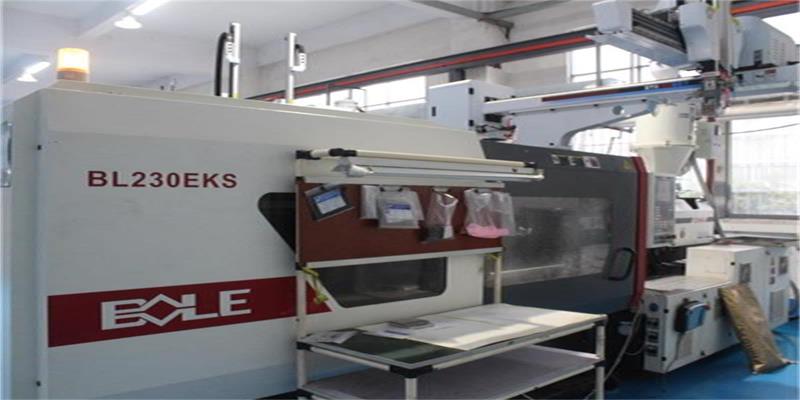
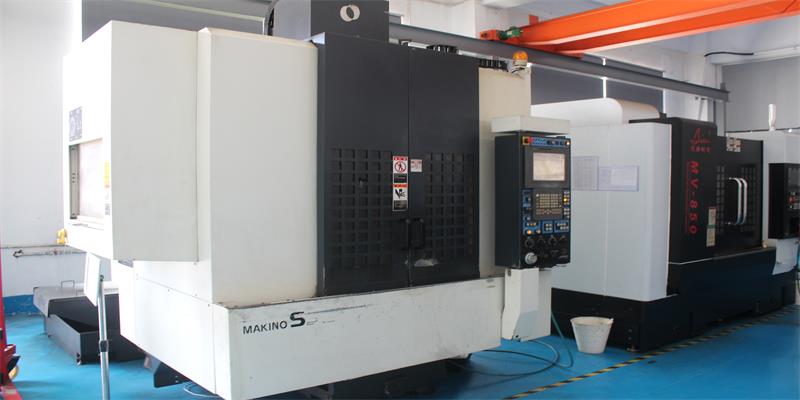
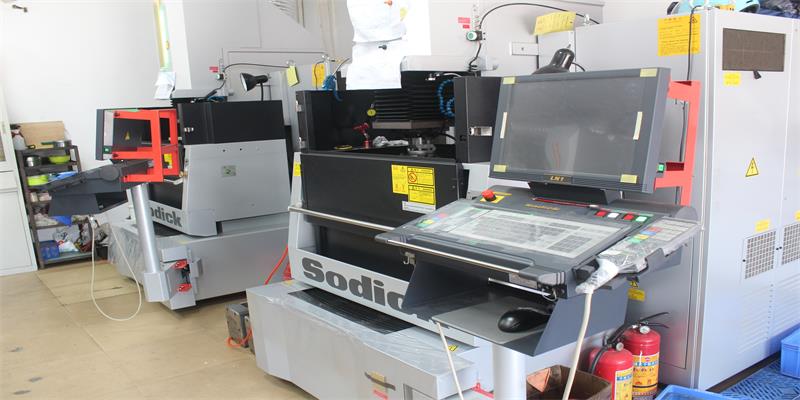
Preguntas frecuentes Lista de servicios de moldeo por inyección de plástico
Moldeo por inyección is a manufacturing process that involves injecting molten plastic into a mold cavity to create a wide range of products with different shapes and sizes.
El moldeo por inyección es un proceso de fabricación utilizado para producir piezas y productos de plástico en grandes cantidades. Es una de las técnicas más utilizadas para producir componentes de plástico en masa debido a su eficacia, precisión y repetibilidad.
The basic principle of injection molding involves injecting molten plastic material into a mold cavity, which is a hollow, usually two-part, metal tool. The mold is designed to have the desired shape of the final product. The molten plastic is forced under high pressure into the mold cavity through a specialized nozzle and runner system.
Las etapas clave del proceso de moldeo por inyección son las siguientes:
1. Sujeción: Las dos mitades del molde (el lado "A" y el lado "B") se cierran y se mantienen unidas bajo presión mediante una unidad de cierre. Esto garantiza que el molde permanezca cerrado durante el proceso de inyección.
2. Inyección: El material plástico fundido, normalmente en forma de pequeñas bolitas o gránulos, se introduce en un barril calentado donde se funde. Una vez que alcanza la temperatura y consistencia adecuadas, se inyecta en la cavidad del molde a alta presión a través de la boquilla.
3. Enfriamiento: Después de que el plástico fundido llena la cavidad del molde, se deja enfriar y solidificar dentro del molde para que adopte la forma deseada.
4. Ejection: Once the plastic has cooled sufficiently, the mold opens, and the finished part is ejected from the mold cavity using ejector pins or other mechanisms.
A continuación, el ciclo se repite para la producción de la siguiente pieza, lo que convierte al moldeo por inyección en un proceso muy eficaz para la fabricación a gran escala.
El moldeo por inyección ofrece numerosas ventajas, entre ellas:
- Altos índices de producción: Permite producir rápidamente grandes cantidades de piezas en poco tiempo.
- Flexibilidad de diseño: Las formas complejas y las características intrincadas pueden lograrse fácilmente con el moldeo por inyección.
- Variedad de materiales: En el proceso puede utilizarse una amplia gama de materiales plásticos, lo que permite obtener diferentes propiedades y características en el producto final.
- Procesamiento posterior mínimo: Las piezas suelen requerir poco o ningún acabado o montaje adicional tras el moldeo.
El moldeo por inyección se utiliza habitualmente en diversos sectores, como el de la automoción, la electrónica, los bienes de consumo y los dispositivos médicos, entre otros, en los que es necesario producir grandes volúmenes de componentes de plástico.
A variety of materials can be used for Injection Molding, including thermoplastics, thermosetting polymers, elastomers, and metals.
El moldeo por inyección puede utilizar una amplia gama de materiales, cada uno con sus propiedades y características específicas. La elección del material depende de los requisitos del producto final, como resistencia, flexibilidad, transparencia, resistencia química y tolerancia a la temperatura. Algunos de los materiales más comunes utilizados para el moldeo por inyección son:
1. **Polyethylene (PE)**: It is a versatile and widely used thermoplastic with excellent chemical resistance, low cost, and good impact strength. PE is commonly used for containers, toys, and various consumer products.
2. **Polipropileno (PP)**: El PP es otro termoplástico versátil con gran resistencia química, tenacidad y resistencia a la fatiga. Se utiliza habitualmente en piezas de automoción, envases y productos domésticos.
3. **Cloruro de polivinilo (PVC)**: El PVC es conocido por su excelente resistencia química y durabilidad. Se utiliza para tuberías, accesorios, aislamiento de cables y discos de vinilo.
4. **Poliestireno (PS)**: El PS es un material ligero y rígido que se utiliza para envases, cubiertos desechables, cajas de CD y diversos productos de consumo.
5. **Acrilonitrilo butadieno estireno (ABS)**: El ABS es un termoplástico duro y resistente a los impactos que suele utilizarse en piezas de automoción, carcasas electrónicas y bienes de consumo.
6. **Policarbonato (PC)**: El PC ofrece una gran transparencia, resistencia al impacto y resistencia a la temperatura, por lo que es adecuado para gafas, dispositivos médicos y componentes electrónicos.
7. **Tereftalato de polietileno (PET)**: El PET se utiliza comúnmente para botellas de bebidas, envases de alimentos y otras aplicaciones de envasado.
8. **Nylon (Poliamida)**: El nailon ofrece gran resistencia, dureza y resistencia a la abrasión. Se utiliza habitualmente en aplicaciones de ingeniería como engranajes, cojinetes y conectores.
9. **Poliuretano (PU)**: El PU puede ser rígido o flexible, dependiendo de la formulación. Se utiliza para acolchado de espuma, juntas y diversas aplicaciones industriales y de automoción.
10. **Acetato de vinilo y polietileno (EVA)**: El EVA es un material flexible y ligero que suele utilizarse en calzado, equipamiento deportivo y acolchado de espuma.
11. **Polioximetileno (POM)**: El POM, también conocido como acetal, ofrece una excelente rigidez, baja fricción y gran estabilidad dimensional, lo que lo hace adecuado para engranajes, bujes y otras piezas de precisión.
12. **12. Polietileno Clorotrifluoroetileno (ECTFE)**: El ECTFE tiene una excelente resistencia química y se utiliza en aplicaciones que requieren una alta resistencia química y a la temperatura.
13. **Sulfuro de polifenileno (PPS)**: El PPS es un termoplástico de alto rendimiento con una excelente resistencia química y estabilidad térmica, utilizado en aplicaciones electrónicas, de automoción y aeroespaciales.
Estos son sólo algunos de los muchos materiales que pueden utilizarse para el moldeo por inyección. Los fabricantes suelen trabajar con proveedores de materiales para seleccionar el más adecuado para una aplicación específica en función de las propiedades requeridas y el rendimiento del producto final.
Injection molding offers many benefits, including high production output, precise control over product dimensions and shape, low labor costs, and the ability to produce complex geometries.
El moldeo por inyección ofrece varias ventajas significativas, lo que lo convierte en un proceso de fabricación popular y ampliamente utilizado en diversas industrias. Algunas de las principales ventajas del moldeo por inyección son:
1. **Alta eficiencia y productividad**: El moldeo por inyección es un proceso muy eficaz que permite la producción rápida de grandes cantidades de piezas en poco tiempo. Una vez configurado el molde, el tiempo de ciclo de cada pieza es relativamente rápido, lo que permite una producción de gran volumen.
2. **Flexibilidad de diseño**: El proceso permite la producción de formas complejas y detalles intrincados que pueden resultar difíciles o incluso imposibles de conseguir con otros métodos de fabricación. Esta flexibilidad en el diseño ayuda a cumplir requisitos específicos del producto y puede reducir la necesidad de pasos de montaje adicionales.
3. **Resultados uniformes y repetibles**: El moldeo por inyección ofrece un control preciso sobre el proceso de moldeo, lo que se traduce en una calidad constante y repetible de las piezas. Esto es crucial para mantener la uniformidad en la producción en masa y cumplir tolerancias estrictas.
4. **Variedad de materiales**: Se puede utilizar una amplia gama de materiales termoplásticos y termoestables para el moldeo por inyección. Cada material tiene sus propiedades únicas, lo que permite a los fabricantes elegir el material más adecuado para la aplicación deseada.
5. **Mínimo desperdicio de material**: El moldeo por inyección suele generar un desperdicio mínimo de material en comparación con otros procesos de fabricación, ya que el material sobrante a menudo puede reciclarse y reutilizarse.
6. **Rentabilidad para grandes volúmenes de producción**: Aunque los costes iniciales de utillaje y preparación pueden ser relativamente elevados, el coste por pieza disminuye significativamente con volúmenes de producción más elevados. Esta rentabilidad es especialmente ventajosa cuando se producen grandes cantidades de piezas idénticas.
7. **Automatización y ahorro de mano de obra**: Una vez configurado el proceso de producción, el moldeo por inyección puede automatizarse en gran medida, lo que reduce la necesidad de una gran cantidad de mano de obra y disminuye los costes de producción.
8. **Opciones de acabado superficial y textura**: El moldeo por inyección permite aplicar diversos acabados superficiales y texturas a las piezas moldeadas, eliminando en algunos casos la necesidad de pasos adicionales de postprocesado.
9. **Fuerza y durabilidad**: Las piezas moldeadas por inyección resultantes suelen presentar una excelente resistencia, durabilidad y resistencia al desgaste, lo que las hace adecuadas para una amplia gama de aplicaciones.
10. **Reducción de los requisitos de montaje**: Las piezas complejas a menudo pueden moldearse como una sola pieza, eliminando la necesidad de ensamblaje o reduciendo el número de componentes necesarios en el producto final.
11. **Quick Prototyping**: Injection molding can also be used for rapid prototyping and iterative product development, helping to validate designs and test functionalities before full-scale production.
En general, las ventajas del moldeo por inyección lo convierten en una opción atractiva para la producción de grandes volúmenes de piezas de plástico en diversos sectores, como la automoción, los bienes de consumo, la electrónica y los dispositivos médicos, entre otros.
La duración del proceso de moldeo por inyección puede variar en función de la complejidad y el tamaño de la pieza fabricada, pero normalmente se tarda entre segundos y minutos en completar un ciclo.
La duración del proceso de moldeo por inyección puede variar en función de varios factores, como la complejidad de la pieza, el material utilizado, el tamaño del molde, las capacidades de la máquina y el volumen de producción. En general, el proceso puede dividirse en dos fases principales: la fase de inyección y la fase de enfriamiento.
1. **Fase de inyección**: Esta fase consiste en inyectar el material plástico fundido en la cavidad del molde. El tiempo de inyección depende de factores como el volumen de material a inyectar, la presión de inyección y la velocidad de inyección de la máquina. Normalmente oscila entre unos segundos y un minuto.
2. **Fase de enfriamiento**: Después de que el plástico fundido llene la cavidad del molde, necesita tiempo para enfriarse y solidificarse en la forma deseada. El tiempo de enfriamiento depende de las propiedades térmicas del material, el grosor de la pieza y el diseño del molde. Los tiempos de enfriamiento pueden variar significativamente, desde unos segundos hasta varios minutos.
En general, el tiempo total del ciclo de moldeo por inyección se compone del tiempo de inyección y del tiempo de enfriamiento. El tiempo de ciclo es el tiempo que se tarda en producir una pieza completa, incluidas ambas fases. Es un factor esencial para determinar la tasa de producción y el número de piezas que pueden fabricarse por hora o por día.
Para piezas sencillas y pequeñas con tiempos de enfriamiento cortos, la duración del ciclo completo podría ser inferior a un minuto. En cambio, para piezas más complejas y grandes, la duración del ciclo puede ser de varios minutos. En escenarios de producción de gran volumen, optimizar el tiempo de ciclo es crucial para lograr índices de producción eficientes.
Es importante tener en cuenta que el tiempo de ciclo puede verse afectado por los ajustes del proceso, como la temperatura del molde, la temperatura de la masa fundida y la eficacia del sistema de refrigeración. Los operarios e ingenieros de moldeo por inyección trabajan continuamente para optimizar estos parámetros con el fin de minimizar los tiempos de ciclo y garantizar al mismo tiempo piezas de alta calidad.
Para garantizar el éxito de un proyecto de moldeo por inyección, es importante trabajar con un fabricante de confianza con experiencia en este campo. También es importante proporcionar especificaciones claras de la pieza que se va a producir y tener en cuenta factores como la selección de materiales, el diseño del molde y el volumen de producción.
Garantizar el éxito de un proyecto de moldeo por inyección implica una planificación cuidadosa, atención a los detalles y colaboración con profesionales experimentados. He aquí algunos pasos y consideraciones esenciales para ayudarle a lograr un proyecto de moldeo por inyección exitoso:
1. **Definición clara del proyecto**: Empiece por definir las metas, los objetivos y los requisitos de su proyecto. Comprenda el propósito de la pieza moldeada, su uso previsto, los criterios de rendimiento y cualquier norma reglamentaria o industrial específica que se aplique.
2. **Selección del material**: Elija el material adecuado para su aplicación. Trabaje con proveedores de materiales e ingenieros experimentados para seleccionar un material que cumpla sus requisitos de rendimiento, mecánicos, químicos y medioambientales.
3. **Diseño para la fabricación (DFM)**: Diseñe su pieza teniendo en cuenta el moldeo por inyección. Tenga en cuenta el grosor de las paredes, los ángulos de desmoldeo, los rebajes y otras características de diseño que pueden afectar a la moldeabilidad. Un diseñador o ingeniero de moldes de inyección con experiencia puede ayudarle con las directrices de DFM.
4. **Prototipos y pruebas**: Antes de comprometerse con la producción a gran escala, cree prototipos para probarlos y validarlos. Esto te ayudará a identificar cualquier fallo o problema de diseño desde el principio y te permitirá realizar las mejoras necesarias.
5. **Selección del socio de moldeo por inyección adecuado**: Elija una empresa de moldeo por inyección o un proveedor de servicios con reputación y experiencia. Busque un socio con una trayectoria demostrada en la producción de piezas similares a sus requisitos y que utilice equipos y procesos modernos.
6. **Diseño de moldes y utillaje**: Colabore con el diseñador y el fabricante del molde para asegurarse de que el diseño del molde cumple sus especificaciones y normas de calidad. Un utillaje adecuado es fundamental para conseguir piezas uniformes y de alta calidad.
7. **Optimización del proceso**: Trabaje en estrecha colaboración con el equipo de moldeo por inyección para optimizar los parámetros del proceso de moldeo, como la temperatura, la presión, el tiempo de enfriamiento y la duración del ciclo. El ajuste del proceso puede mejorar la calidad de las piezas y reducir los costes de producción.
8. **Control de calidad e inspección**: Implemente sólidas medidas de control de calidad para inspeccionar las piezas durante y después de la producción. Asegúrese de que las piezas moldeadas cumplen sus requisitos dimensionales y funcionales.
9. **Mejora continua**: Esté abierto a recibir comentarios y a aprender de cada producción. Utiliza los conocimientos adquiridos para mejorar continuamente el diseño, el proceso y la eficiencia general del proyecto.
10. **Considerar el coste y el calendario**: Comprenda claramente el presupuesto y el calendario del proyecto. Esté preparado para posibles retrasos o ajustes que puedan surgir durante el proceso.
11. **Comunicación y colaboración**: Fomentar la comunicación y la colaboración efectivas entre todas las partes implicadas en el proyecto, incluidos diseñadores, ingenieros, fabricantes y proveedores.
12. **Cumplimiento de la normativa**: Si su proyecto incluye piezas para industrias específicas (por ejemplo, médica, aeroespacial), garantice el cumplimiento de las normas y requisitos reglamentarios pertinentes.
Siguiendo estos pasos y trabajando con profesionales experimentados, puede aumentar la probabilidad de éxito de un proyecto de moldeo por inyección que cumpla sus objetivos de calidad, rendimiento y plazos.
Algunos defectos comunes que pueden producirse durante el moldeo por inyección son marcas de hundimiento, alabeo, rebabas y huecos.
Durante el proceso de moldeo por inyección, pueden producirse diversos defectos en las piezas moldeadas debido a varios factores, como las propiedades del material, el diseño del molde, los parámetros de procesamiento y las condiciones de la máquina. Identificar y tratar estos defectos es esencial para garantizar la producción de piezas de alta calidad. Algunos defectos comunes en el moldeo por inyección incluyen:
1. **Tiro corto**: Un disparo corto se produce cuando el plástico fundido no llena completamente la cavidad del molde. El resultado es una pieza incompleta o de tamaño insuficiente.
2. **Flash**: La rebaba es el exceso de material que se extiende más allá de la geometría prevista de la pieza. Se produce cuando el plástico fundido se escapa entre las mitades del molde durante el proceso de inyección.
3. **Marcas de hundimiento**: Las marcas de hundimiento son depresiones u hoyuelos en la superficie de la pieza causados por velocidades de enfriamiento diferenciales dentro del material. Suelen aparecer en secciones gruesas de la pieza.
4. **Alabeo**: El alabeo se refiere a la deformación o distorsión de la pieza una vez enfriada y expulsada del molde. Se produce debido a un enfriamiento no uniforme y a tensiones residuales dentro del material.
5. **Marcas de quemado**: Las marcas de quemado son áreas decoloradas o ennegrecidas en la superficie de la pieza causadas por el sobrecalentamiento del material debido a altas temperaturas o a un tiempo de permanencia prolongado.
6. **Jetting**: El chorro se produce cuando el plástico fundido sale disparado demasiado rápido hacia el interior del molde, lo que provoca un mal acabado superficial y una menor resistencia de la pieza.
7. **Desplazamiento**: La holgura es la aparición de rayas o líneas en la superficie de la pieza causadas por la humedad u otros contaminantes del material.
8. **Vacíos y trampas de aire**: Los huecos son espacios vacíos o burbujas dentro de la pieza causados por aire atrapado. Las trampas de aire se producen cuando el aire no puede escapar del molde durante el proceso de inyección.
9. **Líneas de punto**: Las líneas de punto son líneas o marcas en la superficie de la pieza donde dos o más frentes de flujo se encuentran durante el proceso de inyección. En algunos casos pueden debilitar la pieza.
10. **Flash de moldeo**: Similar a la rebaba, la rebaba de moldeo se produce cuando el exceso de material se escapa a través de pequeños huecos entre los componentes del molde.
11. **Pegado del molde**: El pegado de molde se produce cuando la pieza se adhiere a la superficie del molde y no se expulsa correctamente. Este defecto puede dañar la pieza o provocar retrasos en la producción.
12. **Líneas de flujo**: Las líneas de flujo son líneas o patrones visibles en la superficie de la pieza causados por el flujo del plástico fundido durante la inyección.
Para solucionar estos defectos, a menudo es necesario ajustar los parámetros de procesamiento, modificar el diseño del molde o cambiar los materiales. La inspección y supervisión periódicas durante el proceso de moldeo por inyección pueden ayudar a identificar los defectos en una fase temprana, lo que permite tomar medidas correctivas a tiempo. Los operarios e ingenieros experimentados en moldeo por inyección desempeñan un papel crucial a la hora de minimizar y resolver estos defectos para producir piezas de alta calidad.
Injection Molding is a mass-production manufacturing process that involves injecting molten plastic into a mold cavity, while 3D printing y CNC machining are additive and subtractive processes, respectively, that produce parts one at a time. Injection Molding offers advantages such as faster production rates, higher precision, and lower cost per part.
El moldeo por inyección, la impresión 3D y el mecanizado CNC son procesos de fabricación utilizados para crear piezas y productos, pero difieren significativamente en sus principios, aplicaciones y ventajas. Estas son las principales diferencias entre estos tres procesos:
1. **Moldeo por inyección**:
- Principio: El moldeo por inyección consiste en inyectar material plástico fundido en la cavidad de un molde para producir una pieza sólida. Se trata de un proceso de producción en serie muy eficaz para crear grandes cantidades de piezas idénticas.
- Materiales: El moldeo por inyección se utiliza principalmente para materiales termoplásticos y termoestables, como ABS, PE, PP, etc.
- Aplicación: Se utiliza comúnmente en diversas industrias para la producción de gran volumen de componentes de plástico, tales como piezas de automóviles, bienes de consumo, dispositivos médicos, y más.
- Ventajas: Los altos índices de producción, la flexibilidad de diseño, la rentabilidad para grandes cantidades y la capacidad de producir piezas complejas son algunas de las principales ventajas del moldeo por inyección.
2. **Impresión 3D (fabricación aditiva)**:
- Principio: La impresión 3D, o fabricación aditiva, construye una pieza capa a capa mediante máquinas controladas por ordenador. Convierte modelos digitales en 3D en objetos físicos.
- Materials: A wide range of materials can be used in 3D printing, including plastics, metals, ceramics, and even composites.
- Aplicaciones: La impresión 3D es versátil y se utiliza en diversos sectores, como la creación rápida de prototipos, la fabricación a medida, la industria aeroespacial, la medicina y el arte y el diseño.
- Ventajas: La complejidad del diseño es prácticamente ilimitada, lo que permite la creación rápida de prototipos y la personalización. La impresión 3D es adecuada para la producción de bajo volumen, y a menudo elimina la necesidad de costosas herramientas.
3. **Mecanizado CNC**:
- Principio: El mecanizado CNC (Control Numérico por Ordenador) consiste en retirar material de un bloque sólido (normalmente metal o plástico) utilizando herramientas de corte controladas por ordenador para crear la forma deseada.
- Materiales: El mecanizado CNC puede trabajar con una amplia gama de materiales, incluidos metales, plásticos, madera y materiales compuestos.
- Aplicación: El mecanizado CNC se utiliza para la fabricación de precisión y la creación de piezas complejas con alta precisión y tolerancias estrechas.
- Ventajas: El mecanizado CNC ofrece una excelente precisión, acabado superficial y repetibilidad. Es idóneo para series pequeñas y medianas y suele utilizarse para fabricar prototipos funcionales, herramientas y piezas de uso final.
En resumen, el moldeo por inyección es ideal para la producción en masa de componentes de plástico con gran eficacia y repetibilidad. La impresión 3D es adecuada para la creación rápida de prototipos, la fabricación a medida y la creación de formas complejas. El mecanizado CNC destaca en la fabricación de precisión y es ideal para producir piezas funcionales de alta calidad con tolerancias estrechas. La elección entre estos procesos depende de los requisitos específicos del proyecto, el volumen de producción, las propiedades del material y las consideraciones presupuestarias.
El moldeo por inyección se utiliza en una amplia gama de industrias, como la automovilística, médica, aeroespacial, de productos de consumo y electrónica.
El moldeo por inyección es un proceso de fabricación versátil utilizado en una amplia gama de industrias debido a su eficacia, capacidad para producir piezas complejas y rentabilidad para la producción de grandes volúmenes. Algunas de las industrias que más utilizan el moldeo por inyección son:
1. **Automoción**: El moldeo por inyección se emplea ampliamente en la industria del automóvil para producir diversos componentes, como embellecedores interiores y exteriores, piezas para el salpicadero, parachoques, tiradores de puertas y otros componentes críticos.
2. **Bienes de consumo**: Muchos productos de consumo, como utensilios de cocina, juguetes, aparatos electrónicos y artículos para el hogar, se fabrican mediante moldeo por inyección debido a su capacidad para crear diseños intrincados y acabados de alta calidad.
3. **Electrónica**: El moldeo por inyección se utiliza para fabricar componentes para dispositivos electrónicos, como carcasas, conectores, interruptores y otras piezas utilizadas en ordenadores, smartphones y electrodomésticos.
4. **Dispositivos médicos**: El moldeo por inyección es crucial en la industria médica para producir una amplia gama de dispositivos y equipos médicos, como jeringuillas, componentes intravenosos, instrumentos quirúrgicos y diversas carcasas de equipos médicos.
5. **Envasado**: El moldeo por inyección se utiliza en aplicaciones de envasado para crear recipientes, tapones, cierres y otros componentes de envasado utilizados en las industrias alimentaria y de bebidas, farmacéutica y cosmética.
6. **Aeroespacial**: La industria aeroespacial utiliza el moldeo por inyección para fabricar piezas como componentes interiores de aviones, accesorios de cabina y elementos estructurales debido a sus propiedades de ligereza y durabilidad.
7. **Construcción**: El moldeo por inyección se emplea en la industria de la construcción para producir componentes como tuberías, accesorios, materiales de aislamiento y elementos estructurales.
8. **Deportes y ocio**: El moldeo por inyección se utiliza para fabricar equipamiento deportivo como cascos, equipos de protección, gafas y diversos accesorios.
9. **Electrodomésticos**: El moldeo por inyección se utiliza habitualmente en la industria de los electrodomésticos para producir piezas como asas de frigoríficos, componentes de lavadoras y accesorios de aspiradoras.
10. **Muebles**: Los fabricantes de muebles utilizan el moldeo por inyección para producir diversos componentes como asientos de sillas, respaldos y otros elementos estructurales.
11. **Juguetes y juegos**: Muchos juguetes de plástico y componentes de juegos, como figuras de acción, bloques de construcción y piezas de juegos de mesa, se fabrican mediante moldeo por inyección.
12. **Cajas eléctricas y electrónicas**: El moldeo por inyección se utiliza comúnmente para crear cajas y carcasas para dispositivos eléctricos y electrónicos con el fin de proporcionar protección y soporte.
Estos son sólo algunos ejemplos, y el uso del moldeo por inyección se extiende a muchas otras industrias debido a su versatilidad y capacidad para producir piezas de alta calidad a un coste competitivo.
El moldeo por inyección puede tener efectos positivos y negativos en el medio ambiente. En el lado positivo, puede reducir los residuos y el consumo de energía en comparación con otros procesos de fabricación. Sin embargo, la producción de los materiales plásticos utilizados en el moldeo por inyección puede tener un impacto negativo en el medio ambiente si no se gestiona adecuadamente, ya que los residuos plásticos pueden acumularse en vertederos y océanos.
El moldeo por inyección, como cualquier otro proceso de fabricación, puede tener un impacto medioambiental tanto positivo como negativo. El alcance de estas repercusiones depende de varios factores, como el material utilizado, el consumo de energía, la generación de residuos y las prácticas de reciclado. Estas son algunas de las formas en que el moldeo por inyección puede afectar al medio ambiente:
**Impactos medioambientales positivos
1. **Eficiencia de recursos**: El moldeo por inyección es generalmente eficiente en términos de uso de materiales. Produce un mínimo de desechos o residuos durante el proceso de fabricación, especialmente si se compara con procesos sustractivos como el mecanizado CNC.
2. **Eficiencia energética**: Las máquinas de moldeo por inyección son cada vez más eficientes desde el punto de vista energético. Los fabricantes invierten en tecnologías para reducir el consumo de energía durante el proceso de moldeo.
3. **Ligereza**: El moldeo por inyección permite fabricar piezas ligeras, lo que puede suponer un ahorro de energía durante el transporte y reducir la huella de carbono global.
4. **Reciclado**: Muchas piezas moldeadas por inyección y materiales de desecho pueden reciclarse y reprocesarse para fabricar nuevos productos, lo que reduce la demanda de materiales vírgenes y disminuye los residuos de los vertederos.
5. **Durabilidad del producto**: Las piezas moldeadas por inyección suelen ser duraderas y de larga duración, lo que conlleva sustituciones menos frecuentes y, por tanto, un menor impacto medioambiental a lo largo del ciclo de vida del producto.
**Impactos medioambientales negativos
1. **Consumo de energía**: Aunque las máquinas de moldeo por inyección son cada vez más eficientes desde el punto de vista energético, el proceso sigue requiriendo un importante aporte de energía, sobre todo durante las fases de fusión y moldeo.
2. **Elección del material**: La elección de los materiales utilizados en el moldeo por inyección puede repercutir en el medio ambiente. Ciertos plásticos, especialmente los difíciles de reciclar o los no biodegradables, pueden tener consecuencias medioambientales duraderas.
3. **Generación de residuos**: Aunque el moldeo por inyección genera menos residuos durante la producción, todavía puede haber residuos en forma de piezas defectuosas, correderas y bebederos. Si no se gestionan adecuadamente, estos residuos pueden contribuir a la contaminación medioambiental.
4. **Emisiones**: El moldeo por inyección puede emitir gases de efecto invernadero y otros contaminantes durante el proceso de fabricación, especialmente si las fuentes de energía utilizadas no son renovables o limpias.
5. **5. Productos químicos y aditivos El uso de ciertos productos químicos, colorantes o aditivos en el proceso de moldeo por inyección puede introducir problemas medioambientales si no se gestionan o eliminan adecuadamente.
6. **Gestión del final de la vida útil**: La gestión adecuada del final de la vida útil de los productos moldeados por inyección es crucial. Si los productos no se reciclan o eliminan de forma responsable, pueden contribuir a la contaminación ambiental.
Para mitigar el impacto medioambiental del moldeo por inyección, los fabricantes pueden aplicar diversas estrategias, como el uso de materiales ecológicos, la optimización de los procesos de producción para aumentar la eficiencia energética, la implantación de programas de reciclaje y la exploración de soluciones sostenibles para el final de la vida útil de sus productos. Además, la concienciación de los consumidores y la gestión responsable de los residuos desempeñan un papel fundamental en la reducción de la huella medioambiental de los productos moldeados por inyección.
El moldeo por inyección puede hacerse más sostenible utilizando materiales reciclados, optimizando el diseño de las piezas para reducir el uso de materiales y reduciendo los residuos mediante prácticas de producción eficientes.
Hacer que el moldeo por inyección sea más sostenible implica aplicar diversas estrategias para reducir su impacto medioambiental a lo largo de todo el ciclo de vida de los productos. He aquí algunas formas de hacer más sostenible el moldeo por inyección:
1. **Selección de materiales**: Elija materiales sostenibles y ecológicos para el moldeo por inyección. Opte por plásticos biodegradables o reciclables siempre que sea posible, y considere el uso de materiales de base biológica o de contenido reciclado.
2. **Eficiencia energética**: Invierta en máquinas de moldeo por inyección energéticamente eficientes y optimice los parámetros del proceso para minimizar el consumo de energía durante la producción.
3. **Reducción de residuos**: Aplicar estrategias para reducir la generación de residuos durante la producción. Esto incluye la optimización del diseño del molde, los sistemas de canalización y el uso de la automatización para minimizar los desechos.
4. **Reciclaje**: Establecer programas de reciclaje para recoger y reprocesar materiales de desecho, piezas defectuosas y corredores para reutilizarlos en la producción. Utilizar materiales reciclados siempre que sea posible.
5. **Sistemas de circuito cerrado**: Implantar sistemas de circuito cerrado que reciclen y reutilicen los residuos plásticos generados durante el proceso de fabricación.
6. **Diseño de productos**: Optimizar el diseño de las piezas para conseguir una mayor eficiencia del material, utilizando menos material sin comprometer el rendimiento o la funcionalidad. Considere el diseño para el desmontaje y el reciclaje.
7. **Evaluación del ciclo de vida (ECV)**: Realizar evaluaciones del ciclo de vida para comprender el impacto medioambiental de los productos e identificar áreas de mejora en el proceso de fabricación.
8. **Aditivos respetuosos con el medio ambiente**: Elija aditivos, colorantes y coadyuvantes tecnológicos respetuosos con el medio ambiente que tengan un menor impacto en el entorno.
9. **Energía renovable**: Utilizar fuentes de energía renovables para alimentar el proceso de moldeo por inyección, como la energía solar o eólica.
10. **Certificaciones verdes**: Obtener certificaciones verdes para productos que cumplan criterios medioambientales específicos, demostrando un compromiso con la sostenibilidad.
11. **Colaboración con proveedores**: Colaborar con los proveedores y fabricantes de materiales para garantizar el abastecimiento y la producción de materias primas sostenibles.
12. **Soluciones al final de la vida útil**: Desarrollar y promover soluciones adecuadas al final de la vida útil de los productos moldeados por inyección, como programas de reciclaje y métodos de eliminación ecológicos.
13. **Educación y sensibilización**: Educar a los empleados y a las partes interesadas sobre las prácticas de sostenibilidad y la importancia de la responsabilidad medioambiental.
14. **Embalaje sostenible**: Considerar la sostenibilidad de los materiales de embalaje utilizados para el envío y almacenamiento de productos moldeados por inyección.
15. **Enfoque de economía circular**: Adoptar un enfoque de economía circular, en el que los productos estén diseñados para durar, reutilizarse y reciclarse, con el fin de minimizar los residuos y el consumo de recursos.
Al integrar estas prácticas sostenibles en el proceso de moldeo por inyección, los fabricantes pueden reducir significativamente el impacto medioambiental de sus operaciones y contribuir a una industria manufacturera más ecológica y responsable. Las prácticas sostenibles de moldeo por inyección no solo benefician al medio ambiente, sino también a las empresas, ya que mejoran la eficiencia, reducen los costes y atraen a clientes concienciados con el medio ambiente.
Preguntas frecuentes sobre el moldeo por inyección de plástico
Sí, Moldeo por inyección puede producir piezas de alta calidad con tolerancias estrechas, pero requiere un diseño cuidadoso, la construcción del molde y el control del proceso para alcanzar el nivel de precisión deseado.
Sí, el moldeo por inyección puede utilizarse para fabricar piezas de alta calidad con tolerancias estrictas. De hecho, el moldeo por inyección es bien conocido por su capacidad para conseguir dimensiones precisas y uniformes, lo que lo hace adecuado para fabricar piezas con tolerancias exigentes. El proceso implica un control preciso de varios parámetros, lo que permite la producción de piezas con especificaciones dimensionales estrictas.
He aquí algunos factores que contribuyen a conseguir piezas de alta calidad con tolerancias ajustadas en el moldeo por inyección:
1. Diseño y precisión de herramientas: El diseño del molde desempeña un papel fundamental en la consecución de tolerancias estrictas. Un molde bien diseñado con mecanizado de precisión garantiza que las dimensiones de la pieza moldeada sean exactas y uniformes.
2. Material y mantenimiento del molde: High-quality mold materials, such as hardened steel, are used to maintain dimensional stability over the production life. Regular maintenance of molds ensures that they remain in optimal condition, avoiding wear or distortion that could affect tolerances.
3. Control de máquinas de moldeo por inyección: Las modernas máquinas de moldeo por inyección disponen de avanzados sistemas de control que permiten regular con precisión la presión de inyección, la temperatura y la velocidad de enfriamiento. Este control garantiza una calidad constante de las piezas de una inyección a otra.
4. Selección de materiales: La elección del material adecuado con propiedades uniformes es crucial. Los materiales de calidad con poca variación ayudan a conseguir unas dimensiones uniformes de las piezas.
5. Optimización de procesos: La cuidadosa optimización del proceso de moldeo por inyección, incluidos los perfiles de temperatura, la velocidad de inyección y el tiempo de enfriamiento, garantiza que las piezas se formen con una variación mínima y dentro de las tolerancias especificadas.
6. Medidas de control de calidad: La aplicación de rigurosas medidas de control de calidad en todo el proceso de producción, como las inspecciones durante el proceso y el control estadístico de procesos, ayuda a identificar y corregir cualquier desviación de las tolerancias deseadas.
7. Tratamiento posterior al moldeo: Algunas piezas pueden requerir tratamientos posteriores al moldeo, como el recocido o el alivio de tensiones, para mantener tolerancias estrictas y reducir las variaciones dimensionales.
El moldeo por inyección se utiliza mucho en sectores en los que las tolerancias estrechas son esenciales, como la automoción, la industria aeroespacial, la electrónica, los dispositivos médicos y la ingeniería de precisión. Sin embargo, conseguir tolerancias estrechas requiere un enfoque cuidadoso y controlado, ya que las variaciones en cualquier parte del proceso pueden afectar a las dimensiones finales de las piezas moldeadas. Trabajar con profesionales experimentados en moldeo por inyección y emplear medidas de control de calidad garantiza la producción de piezas de alta calidad con las tolerancias deseadas.
La selección del material adecuado para un proyecto de moldeo por inyección depende de varios factores, como el uso previsto de la pieza, las condiciones de funcionamiento y las propiedades requeridas. Lo mejor es consultar con un fabricante experimentado en moldeo por inyección para determinar cuál es el mejor material para su proyecto.
Seleccionar el material adecuado para su proyecto de moldeo por inyección es un paso crucial para garantizar el éxito y el rendimiento de su producto final. La elección del material depende de varios factores, como los requisitos específicos de su aplicación, las propiedades mecánicas necesarias, las condiciones medioambientales, el cumplimiento de la normativa y consideraciones de coste. Estos son los pasos que le ayudarán a seleccionar el material adecuado para su proyecto de moldeo por inyección:
1. **Definir los requisitos del proyecto**: Defina claramente los requisitos funcionales y las especificaciones de su producto. Tenga en cuenta factores como la resistencia mecánica, la flexibilidad, la resistencia química, la tolerancia a la temperatura, la estabilidad a los rayos UV y cualquier norma reglamentaria o industrial específica que sea de aplicación.
2. **Evaluación de las propiedades de los materiales**: Comprenda las propiedades de los materiales necesarias para satisfacer las necesidades de su proyecto. Por ejemplo, si su producto necesita una alta resistencia al impacto, busque materiales conocidos por su tenacidad. Si requiere transparencia, considere materiales con buenas propiedades ópticas.
3. **Compatibilidad del material con el molde**: Asegúrese de que el material seleccionado es compatible con el diseño de su molde, incluyendo su rango de temperatura y los requisitos de acabado superficial.
4. **Consideraciones de coste**: Equilibre los requisitos de rendimiento con las limitaciones de coste. Algunos materiales de alto rendimiento pueden ser caros, mientras que otros pueden ofrecer un buen compromiso entre rendimiento y coste.
5. **Base de datos y recursos de materiales**: Utilice las bases de datos de materiales, las fichas técnicas y los recursos de los proveedores de materiales. Proporcionan información valiosa sobre las propiedades de los materiales, directrices de procesamiento y aplicaciones potenciales.
6. **Ensayos de muestras y creación de prototipos**: Realice pruebas de muestras y prototipos con distintos materiales para evaluar su rendimiento en condiciones reales. Esto ayuda a identificar el mejor material que cumpla los requisitos específicos de su proyecto.
7. **Impacto medioambiental**: Considere el impacto medioambiental de los materiales que está evaluando. Busque opciones respetuosas con el medio ambiente, con contenido reciclado o materiales que puedan reciclarse fácilmente después de su uso.
8. **Fiabilidad del proveedor**: Trabaje con proveedores de materiales reputados que puedan ofrecer una calidad constante y asistencia técnica para el material elegido.
9. **Cumplimiento de la normativa**: Asegúrese de que el material cumple todos los requisitos normativos o certificaciones necesarios para su sector o aplicación.
10. **Escalabilidad futura**: Considere la escalabilidad del material elegido si tiene previsto ampliar la producción o introducir variaciones del producto en el futuro.
11. **Consulta con expertos**: Pida consejo a ingenieros experimentados en moldeo por inyección o a especialistas en materiales que puedan ofrecerle ideas basadas en sus conocimientos y experiencia.
12. **Validación del material**: Una vez que haya seleccionado un material, realice una validación y pruebas exhaustivas para verificar que cumple todas las especificaciones y criterios de rendimiento requeridos.
Si considera detenidamente estos factores y realiza las investigaciones y pruebas adecuadas, podrá seleccionar el material más apropiado para su proyecto de moldeo por inyección, garantizando que su producto final tenga un rendimiento óptimo y cumpla todos los requisitos deseados.
Para reducir el coste del moldeo por inyección, es importante optimizar el diseño de la pieza para minimizar el uso de material, simplificar el diseño del molde y reducir el número de pasos de producción. Además, seleccionar un fabricante con experiencia en moldeo por inyección y reputación de calidad y eficiencia puede ayudar a reducir los costes.
Reducir el coste del moldeo por inyección requiere un enfoque estratégico que tenga en cuenta diversos aspectos del proceso de fabricación, la selección de materiales, la optimización del diseño y la eficiencia de la producción. He aquí algunas formas eficaces de reducir el coste del moldeo por inyección:
1. **Selección de materiales**: Elegir materiales rentables que cumplan los criterios de rendimiento exigidos. Considere el uso de materiales reciclados o de origen biológico cuando sea factible para reducir los costes de material.
2. **Optimización del diseño**: Diseñe la pieza pensando en el moldeo por inyección para minimizar el uso de material y las complejidades de producción. Evite características que añadan complejidad innecesaria y aumenten el tiempo de producción.
3. **Volumen y utillaje**: Evalúe sus necesidades de volumen de producción. Para grandes volúmenes de producción, invertir en moldes multicavidad puede reducir significativamente el coste por pieza.
4. **Material del molde y mantenimiento**: Invierta en materiales para moldes de alta calidad para una mayor durabilidad y longevidad. El mantenimiento regular de los moldes garantiza que permanezcan en condiciones óptimas, reduciendo el riesgo de defectos y el tiempo de inactividad.
5. **Eficiencia de la máquina de moldeo por inyección**: Utilizar máquinas energéticamente eficientes que optimicen el consumo de energía durante el proceso de moldeo.
6. **Reducción del tiempo de ciclo**: Optimizar el proceso de moldeo por inyección para reducir los tiempos de ciclo. Minimizar el tiempo de enfriamiento y optimizar los parámetros de inyección puede aumentar la eficiencia de la producción y reducir los costes.
7. **Automatización**: Integrar la automatización siempre que sea posible para reducir los costes de mano de obra y mejorar la eficiencia general de la producción.
8. **Reciclaje y reducción de residuos**: Implantar programas de reciclaje de chatarra y materiales de desecho para reutilizarlos en el proceso de producción, reduciendo los costes de material.
9. **Relaciones con proveedores**: Construir relaciones sólidas con proveedores de materiales y fabricantes de moldes para negociar mejores precios y condiciones.
10. **Ingeniería de valor**: Revisar y evaluar continuamente el proceso de diseño y producción para identificar áreas de mejora que permitan ahorrar costes.
11. **Prototipos y pruebas**: Realice prototipos y pruebas exhaustivos antes de la producción a gran escala para identificar y abordar cualquier problema de diseño o fabricación desde el principio, evitando así costosos retoques posteriores.
12. **Principios de fabricación ajustada**: Aplicar los principios de manufactura esbelta para agilizar el proceso de producción, eliminar desperdicios y reducir actividades sin valor agregado.
13. **Estandarización**: Estandarizar los componentes y procesos siempre que sea posible para simplificar la producción y reducir la necesidad de herramientas personalizadas o modificaciones.
14. **Control de calidad**: Aplicar estrictas medidas de control de calidad para reducir al mínimo los defectos, los rechazos y la necesidad de repeticiones, que pueden dar lugar a sobrecostes.
15. **Compromisos de volumen**: Considere acuerdos a largo plazo o compromisos de volumen con los proveedores para negociar precios y condiciones más favorables.
Aplicando estas medidas de ahorro y adoptando una mentalidad de mejora continua, puede optimizar su proceso de moldeo por inyección y reducir los costes globales de producción, manteniendo al mismo tiempo la calidad y el rendimiento de sus productos.
Sí, el moldeo por inyección puede utilizarse para producir piezas grandes, pero requiere equipos especializados y moldes diseñados para la producción a gran escala.
Sí, el moldeo por inyección puede utilizarse para producir piezas de gran tamaño, pero existen ciertas limitaciones y consideraciones a tener en cuenta debido al tamaño de la pieza y a las capacidades del proceso de moldeo por inyección.
El principal reto a la hora de producir piezas grandes mediante moldeo por inyección es gestionar el flujo y el enfriamiento del material plástico fundido dentro del molde. A medida que aumenta el tamaño de la pieza, resulta más difícil controlar el flujo de material y los tiempos de enfriamiento pueden alargarse, lo que puede afectar a los tiempos del ciclo de producción.
He aquí algunos factores a tener en cuenta a la hora de producir piezas grandes mediante moldeo por inyección:
1. **Diseño del molde**: El diseño del molde debe diseñarse cuidadosamente para adaptarse al gran tamaño de la pieza. Puede requerir paredes de molde más gruesas y robustas para soportar las presiones ejercidas por el plástico fundido durante la inyección.
2. **Presión y velocidad de inyección**: Pueden ser necesarias presiones y velocidades de inyección más elevadas para garantizar un llenado adecuado de la gran cavidad del molde. La unidad de inyección de la máquina de moldeo debe ser capaz de suministrar la presión y el volumen necesarios.
3. **Refrigeración**: La refrigeración es más importante en el caso de piezas grandes para evitar deformaciones. Los canales de refrigeración dentro del molde deben diseñarse estratégicamente para facilitar una transferencia de calor eficaz.
4. **Tiempo de ciclo**: El tiempo de enfriamiento es un factor importante para determinar el tiempo total del ciclo. Los tiempos de enfriamiento más largos para piezas grandes pueden afectar a los índices de producción y al coste por pieza.
5. **Selección del material**: La elección del material es importante cuando se producen piezas de gran tamaño. Se prefieren materiales con buenas propiedades de fluidez y baja viscosidad para garantizar un llenado correcto del molde y reducir el riesgo de defectos.
6. **Tamaño de la máquina**: La fuerza de cierre y el tamaño de inyección de la máquina de moldeo por inyección deben ser lo suficientemente grandes para adaptarse al tamaño y peso de la pieza.
7. **Manipulación y expulsión**: Las piezas de gran tamaño pueden requerir equipos de manipulación especializados para su expulsión y tratamiento posterior, teniendo en cuenta su peso y dimensiones.
8. **Alabeo y contracción**: Las piezas grandes son más susceptibles de alabearse y encogerse durante el enfriamiento. Las consideraciones de diseño y la selección de materiales pueden ayudar a minimizar estos efectos.
Aunque el moldeo por inyección puede utilizarse para producir piezas de gran tamaño, es esencial trabajar con ingenieros y diseñadores de moldes experimentados que comprendan los retos únicos asociados a la producción de piezas grandes. La creación de prototipos y la realización de pruebas exhaustivas también son cruciales para validar el diseño y optimizar el proceso para la producción a gran escala. En algunos casos, otros procesos de fabricación como el rotomoldeo o el termoformado pueden ser más adecuados para producir piezas muy grandes con formas complejas.
Un molde con una sola cavidad produce una pieza cada vez, mientras que un molde con varias cavidades produce varias piezas en un solo ciclo, lo que se traduce en un mayor rendimiento de producción y un menor coste por pieza.
La diferencia entre un molde de una cavidad y un molde de varias cavidades radica en el número de piezas idénticas que pueden producir en un solo ciclo del proceso de moldeo por inyección. Estos moldes se utilizan en el moldeo por inyección para dar forma al material plástico en piezas acabadas. He aquí una comparación de los dos tipos de moldes:
1. **Molde de una sola cavidad**:
- Definición: Un molde de una sola cavidad, como su nombre indica, tiene una sola cavidad o impresión que da forma al plástico fundido en una sola pieza durante cada ciclo de moldeo.
- Producción: Un molde de cavidad única produce una pieza por ciclo de inyección. Esto significa que por cada ciclo de moldeo, la máquina produce una sola unidad de la pieza deseada.
- Ventajas: Los moldes de cavidad única son sencillos y fáciles de fabricar. Suelen utilizarse para pequeñas series de producción, prototipos o cuando se fabrican piezas grandes y complejas que requieren una atención individualizada.
2. **Molde multicavidad**:
- Definición: Un molde multicavidad contiene múltiples cavidades o impresiones que permiten al molde dar forma a múltiples piezas idénticas en un solo ciclo de inyección.
- Producción: Un molde con varias cavidades puede producir varias piezas por ciclo de inyección, en función del número de cavidades. Por ejemplo, un molde de dos cavidades produciría dos piezas por ciclo, un molde de cuatro cavidades produciría cuatro piezas, y así sucesivamente.
- Ventajas: Los moldes multicavidad aumentan significativamente la eficiencia de la producción, ya que producen más piezas en el mismo tiempo. Son ideales para series de producción de gran volumen cuando se requiere una gran cantidad de piezas idénticas. Ayudan a reducir los costes de producción por pieza, ya que el coste del molde se reparte entre varias piezas.
**Resumen de las principales diferencias**:
- Los moldes de una sola cavidad producen una pieza por ciclo, mientras que los moldes de varias cavidades producen varias piezas idénticas por ciclo.
- Los moldes de una sola cavidad son adecuados para pequeñas series de producción, prototipos o piezas complejas, mientras que los moldes de varias cavidades son ideales para la producción de grandes volúmenes con el fin de optimizar la eficacia y reducir los costes.
- Los moldes multicavidad requieren procesos de fabricación más complejos y precisos, por lo que son más caros que los moldes de una sola cavidad.
- La elección entre moldes de una o varias cavidades depende de los requisitos de producción, el volumen de producción, la complejidad de la pieza y los costes. Para pequeñas series de producción o piezas especializadas, un molde de una sola cavidad puede ser más apropiado. Para la producción de grandes volúmenes, un molde de cavidades múltiples ofrece ventajas significativas en términos de eficacia y rentabilidad.
Para garantizar la calidad de las piezas moldeadas por inyección, es importante implantar un sistema de control de calidad exhaustivo que incluya pruebas e inspecciones de las piezas durante todo el proceso de producción. También es importante trabajar con un fabricante de Moldeo por Inyección con experiencia y reputación en la producción de piezas de alta calidad.
Garantizar la calidad de las piezas moldeadas por inyección requiere un enfoque integral que implica una planificación cuidadosa, el control del proceso y rigurosas medidas de control de calidad. Estos son algunos pasos esenciales para garantizar la calidad de las piezas moldeadas por inyección:
1. **Diseño para la fabricación (DFM)**: Comience con un diseño de pieza bien optimizado que tenga en cuenta las capacidades y limitaciones del moldeo por inyección. Esto ayuda a evitar posibles problemas de moldeo y garantiza la fabricabilidad de la pieza.
2. **Diseño de moldes y utillaje**: Trabaje con diseñadores y fabricantes de moldes experimentados para crear moldes de alta calidad que cumplan las especificaciones de la pieza y las tolerancias dimensionales. La construcción adecuada del molde y el mecanizado de precisión son cruciales para la calidad de la pieza.
3. **Selección del material**: Elegir el material adecuado que cumpla los requisitos mecánicos, térmicos y químicos de la pieza. Verifique las propiedades y la calidad del material con proveedores de confianza.
4. **Optimización del proceso**: Controlar cuidadosamente los parámetros del proceso de moldeo por inyección, incluyendo la temperatura, la presión, la velocidad de inyección y el tiempo de enfriamiento. La optimización del proceso ayuda a conseguir una calidad constante de la pieza y minimiza las variaciones.
5. **Validación y creación de prototipos**: Realice pruebas exhaustivas y valide el diseño de la pieza y el molde mediante la creación de prototipos. Este paso permite identificar y resolver posibles problemas antes de la producción a gran escala.
6. **Control de calidad durante la producción**: Implementar controles e inspecciones de calidad durante el proceso de producción. Supervise periódicamente el proceso de moldeo para garantizar que se mantiene dentro de los parámetros especificados.
7. **Control estadístico de procesos (CEP)**: Utilizar técnicas de SPC para supervisar y analizar los datos de producción. Esto ayuda a identificar tendencias, desviaciones y posibles problemas en una fase temprana, lo que permite tomar medidas correctivas a tiempo.
8. **Inspección y medición**: Utilizar herramientas de medición precisas y equipos de inspección para verificar las dimensiones de las piezas, las tolerancias y el acabado superficial. Las inspecciones deben realizarse a intervalos regulares durante la producción.
9. **Análisis de defectos e investigación de la causa raíz**: Cuando se produzcan defectos, realice un análisis exhaustivo para identificar la causa raíz. Al abordar la causa raíz se evita la repetición de defectos similares en futuras series de producción.
10. **Formación y desarrollo de habilidades**: Garantizar que los operarios y técnicos reciben la formación adecuada y disponen de las habilidades necesarias para manejar las máquinas de moldeo por inyección y llevar a cabo los procedimientos de control de calidad de forma eficaz.
11. **Trazabilidad**: Implantar un sistema de seguimiento y localización de cada lote de piezas para mantener la trazabilidad del producto y facilitar una respuesta rápida a cualquier problema de calidad.
12. **Gestión de la calidad de los proveedores**: Trabajar con proveedores reputados de materiales y otros componentes para mantener una calidad constante en toda la cadena de suministro.
13. **Certificaciones y normas**: Cumplir las normas pertinentes del sector y obtener las certificaciones necesarias para demostrar la calidad del producto y el cumplimiento de la normativa.
Al integrar estas medidas de garantía de calidad en el proceso de moldeo por inyección, puede asegurarse de que las piezas moldeadas cumplen las especificaciones requeridas, funcionan según lo previsto y mantienen una calidad constante durante toda la producción.
El plazo de entrega de los proyectos de moldeo por inyección varía en función de varios factores, como la complejidad de la pieza, el tamaño de la tirada de producción y la disponibilidad de materiales y moldes. Un fabricante de Moldeo por Inyección de confianza puede proporcionar una estimación más precisa del plazo de entrega en función de los requisitos específicos del proyecto.
El plazo de entrega de los proyectos de moldeo por inyección puede variar significativamente en función de varios factores, como la complejidad de la pieza, el tamaño de la tirada de producción, la disponibilidad de materiales y herramientas, la capacidad de la empresa de moldeo por inyección y cualquier requisito adicional de acabado o postprocesado. Por lo general, el plazo de entrega de los proyectos de moldeo por inyección puede dividirse en las siguientes etapas:
1. **Diseño y fabricación de herramientas**: Esta etapa consiste en diseñar y fabricar el molde de inyección, que es un componente fundamental para el proceso de producción. El tiempo necesario para el diseño y la fabricación del molde puede oscilar entre unas semanas y varios meses, en función de la complejidad del molde y de la carga de trabajo del fabricante del mismo.
2. **Prototipos y validación**: Antes de la producción a gran escala, es habitual crear prototipos de la pieza para verificar su diseño, ajuste y funcionamiento. El tiempo necesario para la creación de prototipos y la validación puede variar, pero normalmente se completa en unos pocos días o semanas.
3. **Aprovisionamiento y preparación del material**: El plazo de aprovisionamiento de los materiales necesarios dependerá de la disponibilidad del material concreto y del plazo de entrega del proveedor. Normalmente, los materiales pueden obtenerse en un plazo de entre unos días y un par de semanas.
4. **Funcionamiento de la producción**: La producción real de las piezas moldeadas por inyección dependerá de la cantidad requerida. Las series de producción cortas con cantidades reducidas pueden completarse en cuestión de días o semanas. Sin embargo, las series de producción de gran volumen pueden tardar varias semanas o incluso meses en completarse.
5. **Postprocesado y acabado**: Si se requiere algún paso de post-procesamiento o acabado, como pintura, montaje o embalaje, el plazo de entrega se ampliará en consecuencia.
6. **Envío y entrega**: El tiempo requerido para el envío y la entrega dependerá de la ubicación de la empresa de moldeo por inyección y del destino final de las piezas.
En resumen, el plazo total de un proyecto de moldeo por inyección puede oscilar entre unas pocas semanas y varios meses, y el factor que más contribuye a ello es el diseño del molde y el proceso de fabricación. Es esencial trabajar en estrecha colaboración con la empresa de moldeo por inyección y planificar con antelación para minimizar los plazos de entrega y garantizar que el calendario del proyecto se ajuste a su programa de producción y a sus necesidades empresariales.
Un molde de canal caliente tiene un sistema de canal calentado que mantiene el material plástico en estado fundido, mientras que un molde de canal frío tiene un sistema de canal separado que no se calienta. Los moldes de canal caliente ofrecen tiempos de ciclo más rápidos y menos residuos, pero son más caros de producir y mantener.
Los moldes de canal caliente y canal frío son dos tipos diferentes de sistemas de moldeo por inyección que se utilizan para introducir el plástico fundido en la cavidad del molde. La diferencia clave entre los dos radica en cómo gestionan el flujo de plástico y manejan los canales (los canales que dirigen el plástico fundido desde la máquina de moldeo por inyección a las cavidades del molde). Echemos un vistazo más de cerca a cada una:
**Molde de corredor caliente:
1. **Definición**: En un molde de canal caliente, los canales por los que fluye el plástico fundido desde la máquina de moldeo por inyección hasta las cavidades del molde se mantienen a una temperatura elevada (calentados). El plástico dentro del sistema de canal caliente permanece fundido incluso durante el ciclo de moldeo por inyección, eliminando la necesidad de que los canales se solidifiquen y posteriormente sean expulsados.
2. **Ventajas**:
- Reducción de residuos: Los moldes de canal caliente eliminan la necesidad de canales, lo que se traduce en menos desperdicio de material y ahorro de costes.
- Tiempo de ciclo más rápido: Al no haber canales solidificados que retirar, el tiempo de ciclo suele ser más rápido, lo que se traduce en una mayor eficiencia de la producción.
- Mejora de la calidad de las piezas: Los sistemas de canal caliente ayudan a mantener un flujo uniforme de la masa fundida, reduciendo las posibilidades de que se produzcan defectos en las piezas, como marcas de compuerta y líneas de punto.
3. **Aplicaciones**: Los moldes de canal caliente son adecuados para producciones de gran volumen y aplicaciones en las que es fundamental minimizar el desperdicio de material y el tiempo de ciclo.
**Molde de canal frío**:
1. **Definición**: En un molde de canal frío, los canales por los que fluye el plástico fundido desde la máquina de moldeo por inyección hasta las cavidades del molde no se calientan. El plástico del interior de los canales se enfría y solidifica, y los canales solidificados se expulsan junto con la pieza al final de cada ciclo.
2. **Ventajas**:
- Simplicidad: Los moldes de canal frío tienen un diseño más sencillo y suelen ser más rentables para series de producción más pequeñas o piezas con geometrías sencillas.
- Flexibilidad: Los moldes de canal frío permiten cambiar fácilmente de color y material, ya que los canales están separados de la pieza.
3. **Aplicaciones**: Los moldes de canal frío se utilizan a menudo para producciones de volumen bajo a medio o cuando se requieren cambios de material entre series de producción.
**Resumen de las principales diferencias**:
- Los moldes de canal caliente tienen canales calentados que mantienen el plástico fundido, mientras que los moldes de canal frío tienen canales no calentados que permiten que el plástico se solidifique en forma de canales.
- Los moldes de canal caliente reducen el desperdicio de material, tienen tiempos de ciclo más rápidos y mejoran la calidad de las piezas, mientras que los moldes de canal frío son más sencillos y rentables para tiradas de producción más pequeñas o cuando se necesitan cambios de material.
- Los moldes de canal caliente se suelen utilizar en la producción de grandes volúmenes, mientras que los moldes de canal frío son adecuados para la producción de volúmenes bajos y medios o cuando se requiere flexibilidad de material.
Sí, el moldeo por inyección puede utilizarse para fabricar piezas de gran resistencia y rigidez, pero requiere una cuidadosa selección de materiales y parámetros de proceso para conseguir las propiedades deseadas.
Sí, el moldeo por inyección puede utilizarse para fabricar piezas de gran resistencia y rigidez, siempre que se elija el material adecuado y se optimice el diseño de la pieza para cumplir los requisitos mecánicos. La resistencia y la rigidez de las piezas moldeadas por inyección dependen de varios factores:
1. **Selección del material**: La elección del material es fundamental para determinar las propiedades mecánicas de la pieza final. Existen varios plásticos técnicos de alto rendimiento disponibles para el moldeo por inyección, como el nailon, el policarbonato, el polipropileno y el ABS, que ofrecen una resistencia y rigidez excelentes.
2. **Rellenos y refuerzos**: Algunos materiales pueden mejorarse con rellenos y refuerzos, como fibras de vidrio, fibras de carbono o rellenos minerales. Estos aditivos pueden mejorar significativamente la resistencia y rigidez de las piezas moldeadas por inyección.
3. **Diseño de la pieza**: El diseño de la pieza con un grosor de pared suficiente y nervaduras o estructuras de soporte adecuadas puede mejorar su resistencia y rigidez. Las nervaduras o refuerzos pueden distribuir las cargas de forma más eficaz, aumentando la rigidez de la pieza.
4. **Colocación de la compuerta**: La colocación adecuada de las compuertas puede ayudar a optimizar el flujo de plástico fundido en el molde, reduciendo el riesgo de puntos débiles o defectos inducidos por el flujo que pueden comprometer la resistencia y la rigidez.
5. **Diseño y fabricación de moldes**: Un molde bien diseñado y fabricado con precisión garantiza que la pieza mantenga su exactitud dimensional, lo que es crucial para lograr propiedades mecánicas constantes.
6. **Tratamientos posteriores al moldeo**: Determinados tratamientos posteriores al moldeo, como el recocido o el alivio de tensiones, pueden mejorar las propiedades mecánicas de la pieza y reducir las tensiones internas, aumentando la resistencia y la rigidez.
7. **Control de calidad y optimización del proceso**: La aplicación de rigurosas medidas de control de calidad y la optimización del proceso de moldeo por inyección contribuyen a garantizar que cada pieza cumpla las especificaciones mecánicas deseadas.
El moldeo por inyección se utiliza ampliamente para producir piezas de alta resistencia y rigidez para diversas industrias, como la automovilística, aeroespacial, electrónica y de bienes de consumo. Sin embargo, es esencial trabajar en estrecha colaboración con ingenieros expertos en moldeo por inyección y especialistas en materiales para seleccionar el material adecuado y optimizar el diseño de la pieza y el proceso de producción para obtener las propiedades mecánicas deseadas. Además, la realización de pruebas y la validación de prototipos ayudan a garantizar que las piezas finales moldeadas por inyección cumplen los criterios de resistencia y rigidez requeridos.
Para solucionar problemas de moldeo por inyección, es importante comprender la causa raíz del problema y aplicar medidas correctivas, como ajustar los parámetros del proceso, modificar el diseño del molde o cambiar los materiales. Un fabricante con experiencia en moldeo por inyección puede aportar valiosos conocimientos y experiencia en la resolución de problemas.
La solución de problemas de moldeo por inyección requiere un enfoque sistemático para identificar y abordar las causas de los problemas. Cuando se enfrente a problemas en el proceso de moldeo por inyección, siga estos pasos para solucionarlos de forma eficaz:
1. **Defina el problema**: Defina claramente el problema específico que está encontrando. Puede estar relacionado con defectos en las piezas, variaciones dimensionales, imperfecciones estéticas o cualquier otro problema relacionado con el moldeo.
2. **Comprobar los parámetros del proceso**: Revise los parámetros de proceso de la máquina de moldeo por inyección, como la temperatura, la presión, la velocidad de inyección y el tiempo de enfriamiento. Asegúrese de que están ajustados correctamente y dentro del rango recomendado para el material y el diseño de la pieza.
3. **Inspeccione el molde y el utillaje**: Examine el molde para detectar cualquier daño, desgaste o problema con el sistema de refrigeración. Compruebe la correcta alineación y limpieza del utillaje.
4. **Análisis del material**: Verificar el material que se está utilizando en el proceso de moldeo por inyección. Compruebe si hay contaminación, humedad o variaciones en las propiedades del material que puedan estar contribuyendo al problema.
5. **Revisión del diseño de la pieza**: Evalúe el diseño de la pieza para identificar cualquier característica que pueda estar causando el problema. Compruebe si hay secciones gruesas, paredes finas o esquinas afiladas que puedan provocar defectos.
6. **Sistema de compuertas y corredores**: Analizar el diseño de la compuerta y el sistema de canalización. Un diseño inadecuado de las compuertas o de la configuración de los canales puede provocar defectos relacionados con el flujo.
7. **Ajustes de la máquina**: Compruebe la presión de inyección, la contrapresión, la velocidad del husillo y otros ajustes de la máquina. Ajústelos según sea necesario para mejorar la calidad de la pieza.
8. **Refrigeración**: Revisar el sistema de refrigeración para asegurarse de que elimina eficazmente el calor del molde y las piezas.
9. **Seguimiento del proceso**: Utilizar herramientas de monitorización de procesos como el control estadístico de procesos (CEP) para analizar los datos de producción e identificar tendencias o variaciones que puedan estar contribuyendo al problema.
10. **Documentación**: Mantener registros detallados del proceso de solución de problemas, incluyendo los cambios realizados, los resultados y su impacto en la calidad de la pieza.
11. **11. Pruebas y validación Realizar pruebas y validación con diferentes ajustes y parámetros de proceso para identificar las condiciones óptimas para una producción de calidad.
12. **Consulte a expertos**: Si no puede identificar o resolver el problema, consulte con profesionales experimentados en moldeo por inyección, expertos en materiales o diseñadores de moldes que puedan aportar ideas y soluciones.
13. **Aplicar soluciones**: Basándose en el análisis y las conclusiones, aplique los cambios necesarios para resolver el problema y mejorar la calidad de las piezas.
14. **Mejora continua**: Establecer un proceso de mejora continua, supervisión y mantenimiento periódico para evitar problemas similares en el futuro.
Recuerde que la solución de problemas de moldeo por inyección puede requerir paciencia y pruebas iterativas para identificar la causa raíz con éxito. Si sigue estos pasos y trabaja de forma sistemática, podrá solucionar eficazmente los problemas de moldeo por inyección y lograr una producción de piezas uniforme y de alta calidad.