Servicio de postratamiento de acabado superficial
After production, plastic y metal products often need to undergo a series of post-treatment processes to ensure that their performance, appearance, and functionality are closer to the design requirements.
For metal parts, common post-treatment processes include heat treatment, polishing, painting, and electroplating. Heat treatment can change the physical properties of metals, such as hardness, toughness, and wear resistance; Polishing is used to improve surface smoothness and enhance aesthetics; Painting and electroplating can form a protective layer on the metal surface, preventing corrosion and increasing decorative effects.
For non-metallic parts, especially plastic parts, post-processing may involve steps such as deburring, polishing, painting, screen printing, or transfer printing. These processes help improve the feel, appearance, and clarity of identification of parts.
Through such one-stop services, we can not only shorten the product development cycle, but also effectively control costs and improve product quality. More importantly, we can help you solve various technical problems encountered during production and post-processing, so that you have no worries.
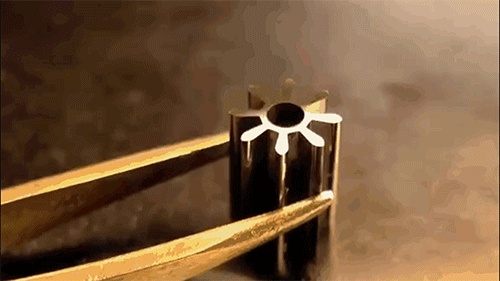
surface treatment effect
In order to remove various foreign objects attached to the surface of an object (such as oil stains, rust, dust, old paint films, etc.) and provide a good substrate suitable for painting requirements, to ensure that the coating film has good anti-corrosion performance, decorative performance, and certain special functions, it is necessary to pre-treat the surface of the object before painting. People refer to the work done for this type of treatment as pre coating (surface) treatment or (surface) pre-treatment.
During the processing, transportation, storage, and other processes of workpieces, the surface often contains oxide skin, rust mold residue, molding sand, welding slag, dust, oil, and other dirt. To ensure that the coating can firmly adhere to the surface of the workpiece, it is necessary to clean the surface of the workpiece before coating. Otherwise, it not only affects the adhesion and corrosion resistance between the coating and the metal, but also allows the base metal to continue to corrode even with coating protection, causing the coating to peel off, affecting the mechanical properties and service life of the workpiece. Therefore, surface treatment before painting the workpiece is an important guarantee and measure to obtain a high-quality protective layer and extend the service life of the product.
Surface treatment process type
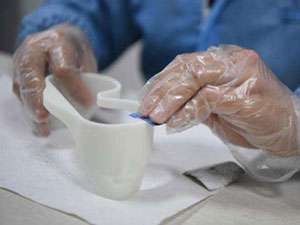
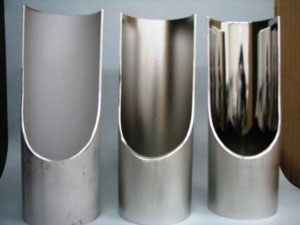

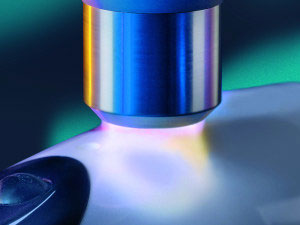
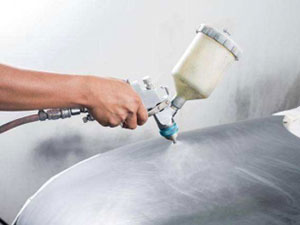
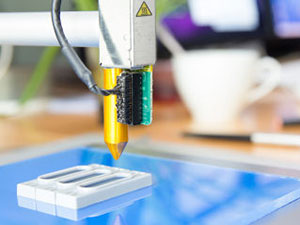
Grinding and polishing - Surface Finish Post-Treatment
In order to better solve the surface smoothness problem of printed products, The working principle of 3D printing layer by layer stacking results in a step effect on the surface of the printed piece. Although the layer thickness can be minimized during the printing process, there are still multi-level steps with a certain thickness at the micro size. The surface quality of the printed piece is related to the quality of 3D data, data slicing parameters, printing materials, machine accuracy, printing speed, printing temperature, etc, In order to better solve the surface quality problem of printed materials, it is necessary to put in effort in the post-processing process after printing is completed.
Polishing is a type of surface modification technology that generally refers to a processing method that uses rough objects (such as sandpaper with higher hardness particles) to change the physical properties of the material surface through friction, with the main purpose of obtaining specific surface roughness.
The objects printed by FDM and SLA processes generally have obvious layer patterns. If there are requirements for the surface of the objects, polishing, soil filling, coloring, and other treatments are required.
Sandpaper polishing
The types of sandpaper are mainly divided by the thickness of surface particles, commonly including 180 mesh, 400 mesh, 600 mesh, 800 mesh, 1000 mesh, 1200 mesh, 1500 mesh, 2000 mesh, 2500 mesh, 3000 mesh, and 5000 mesh. The lower the label, the larger the sandpaper particles and the rougher the surface.
The polishing sequence starts from the low grade, starts with 180 mesh, passes through 400 mesh, 600 mesh, 800 mesh, 1000 mesh, 1200 mesh, 1500 mesh, and finally grinds to over 2000 mesh before painting.
Sandblasting is the process of cleaning and roughening the surface of the substrate using the impact of high-speed sand flow. Using compressed air as the power, a high-speed spray beam is formed to spray materials (copper ore, quartz sand, diamond sand, iron sand, etc.) onto the surface of the workpiece to be treated at high speed, making the surface of the workpiece smooth and having a uniform matte effect. Due to the impact and cutting effects of abrasives on the surface of the workpiece, it achieves a certain degree of cleanliness and different roughness, which improves the mechanical properties of the workpiece surface. As a result, the fatigue resistance of the workpiece is improved, the adhesion between it and the coating is increased, the durability of the coating is extended, and it is also conducive to the leveling and decoration of the coating.
Sandblasting application:
(1) Workpiece coating and pre-treatment before workpiece bonding: sandblasting can remove rust and other dirt on the surface of the workpiece, making the bonding of the bonded parts more firm.
(2) Cleaning of rough surfaces and heat treated workpieces in casting: Use polishing and sandblasting to make the appearance of the workpiece more beautiful and attractive.
(3) Burr cleaning and beautification of machined parts: sandblasting can clean small burrs on the workpiece, making the surface of the workpiece appear more precise.
(4) Improving the mechanical performance of parts: After sandblasting, the mechanical parts reduce noise and improve the service life of the machinery.
(5) Decoration function: For certain special purpose workpieces, sandblasting can achieve different reflections or matte at will.
(1) Shot Peening:
Shot peening is a widely used surface strengthening process in factories, which has simple equipment, low cost, and is not limited by the shape and position of the workpiece. It is easy to operate, but the working environment is poor. Shot peening is widely used to improve the mechanical strength, wear resistance, fatigue resistance, and corrosion resistance of parts. It can also be used for surface smoothing, removing oxide skin, and eliminating residual stress in cast, forged, and welded parts.
(2) The difference between shot peening and sandblasting:
Both shot peening and sandblasting use high-pressure air or compressed air as power to blow out the medium at high speed and impact the surface of the workpiece to achieve cleaning effect. However, the effect varies depending on the medium chosen.
After sandblasting treatment, the dirt on the surface of the workpiece is removed, and the surface of the workpiece is slightly damaged, resulting in a significant increase in surface area, thereby increasing the bonding strength between the workpiece and the coating/coating.
The surface of the workpiece after sandblasting treatment is metallic in its natural color, but due to its rough surface, light is refracted off, resulting in no metallic luster and a dark surface.
Polishing refers to the process of using mechanical equipment, chemical or electrochemical processes to reduce the surface roughness of a workpiece, in order to obtain a bright and flat surface. It is a decorative production process that uses polishing tools to remove abrasive particles or other polishing substances from the surface of workpieces. Polishing cannot improve the machining accuracy or geometric shape accuracy of the workpiece, but is primarily used to obtain a smooth surface or mirror glass glossiness, sometimes also used to remove glossiness (polishing). Generally, polishing wheels are used as special polishing tools. The polishing wheel is generally made of double-layer white canvas, felt, or leather products stacked together, with alloy circular plates clamped on both sides, and its edges coated with a polishing agent composed of a uniform mixture of micro powder abrasive and vegetable oil. During polishing, a high-speed polishing wheel (with a circumferential speed of over 20 meters/second) presses against the workpiece, causing wear-resistant materials to extrude and slightly drill the surface of the workpiece, resulting in a bright production and processing surface. The surface roughness can generally reach Ra0.63-0.01 μ M; When using non greasy polishing agents, bright surfaces will be polished to improve appearance. For different polishing processes: rough polishing (basic polishing process), intermediate polishing (deep machining process), and precision polishing (polishing process), using suitable polishing wheels can achieve the best polishing actual effect while improving polishing efficiency.
metal surface treatment - Surface Finish Post-Treatment
By physical or chemical methods, a surface layer with certain special properties is formed on the surface of a metal. Surface treatment is the process of forming a surface layer with certain or multiple special properties on the surface of a material through physical or chemical methods. Surface treatment can improve the appearance, texture, functionality, and other aspects of product performance.
Appearance: color, pattern, logo, gloss/lines (3D, 2D);
Texture: Hand feel, roughness, lifespan (quality), streamline, etc;
Function: Hardening, anti fingerprint, anti scratch;
Below is a detailed introduction to various surface treatment processes for metal 3D printed parts:
Metal heat treatment - Surface Finish Post-Treatment
Imagine that you have just printed a metal part with a body full of "powder armor". Do you need to remove this layer of "armor" before proceeding to the next step? That's right, this is the preparation work before heat treatment.
Firstly, why clean up these powders? Firstly, it is to save material costs, after all, powder is also money; Secondly, if there are small flow channels inside the component, and these channels are as narrow as needle holes, if they are not cleaned thoroughly, the powder may get stuck in the channels, causing the component to suffocate. So, we need to carefully remove these 'powder obstacles'.
Next, it's the highlight of heat treatment. Heat treatment, in fact, is to give metal or alloy a "three warmth" - heating, insulation, and cooling. None of these three steps can be omitted, and the temperature, time, and cooling rate of each step must be precisely controlled. Just like baking bread, if the heat is not enough or too high, the bread will become burnt or undercooked.
Speaking of which, you may be asking, 'What will the parts look like after heat treatment?' Good question! The characteristic of heat treatment is that it does not change the external dimensions of metal parts, but can penetrate deep into the "inner" and change the internal structure and properties of materials. It's like giving a 'spiritual massage' to a component, making it look brand new!
Common heat treatment methods include annealing, normalizing, quenching, and tempering. Let's take steel as an example to talk about the wonderful uses of these heat treatments. The purpose of steel heat treatment is like giving steel a "physical examination" to identify and eliminate small problems in the material structure. More importantly, it can also enhance the performance of steel, allowing it to unleash greater potential. This is simply too important for improving product quality and extending service life!
Overall, heat treatment after metal printing is an essential process. It not only makes the parts more flawless, but also safeguards product quality and service life. So, next time you see those sparkling metal parts, don't forget that they have undergone countless "tempering" and "baptism" behind them!
Plastic surface treatment - Surface Finish Post-Treatment
Painting and coloring - Surface Finish Post-Treatment
secondary processing - Surface Finish Post-Treatment
The process of reprocessing metal printed parts using CNC machine tools as needed after printing and forming,
Secondary processing refers to the process of using CNC machine tools to reprocess metal printed parts after printing and forming, including welding, boring, reaming, closing tolerance holes, or tapping tolerance holes that require threads. Depending on the material, various inserts can be inserted using hot piles or adhesive.