High-Precision Injection Molding Service
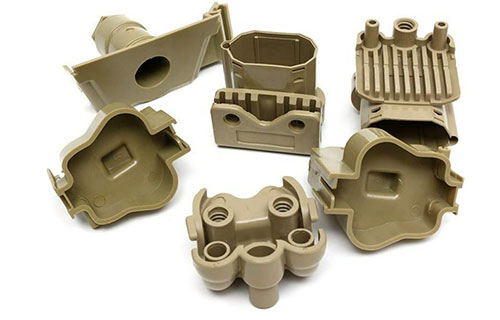
Custom High-Precision Injection Molding Parts
Injection molding is a manufacturing process widely used in various products, whether it is simple parts or complex components, such as those used in the aerospace, medical, and automotive industries. High precision injection molding is a professional technology that can produce fine and precise parts with strict tolerance requirements.
So, what is high-precision injection molding? Simply put, it is a technology that can manufacture plastic parts with precise dimensions, smooth surfaces, and complex shapes. This technology is crucial for applications that require extremely high precision, such as micro gears, optical lenses, or tiny medical device components.
Next, we will delve into the advantages of high-precision injection molding, its application scope, and various factors that affect this process together. Imagine that without this technology, many high-tech products in our lives may not be achievable. This is not just about manufacturing, but also about exploring innovation and possibilities.
What is High-Precision Injection Molding?
High precision injection molding, this is really a technical job! Imagine that we have to use those super precision machines, such as micro injection molding machines, and extremely fine molds, to create components with extremely strict size requirements. The whole process is like a dance under high temperature - molten plastic is injected into the mold cavity under high pressure and high temperature, perfectly filling every corner and forming the precise shape we want.
You know what? This process can bring many benefits. Firstly, the quality has significantly improved, with each component resembling a meticulously crafted work of art. Secondly, waste has been reduced and resource utilization has become more efficient, which is also good news for the environment. Finally, efficiency has also increased, production speed is faster, and meeting market demand is no longer necessary.
So, when you pick up a delicate and flawless product, think about the magic of high-precision injection molding behind it!

Design, High-Precision Injection Mold making, production and assembly
What exactly can we do
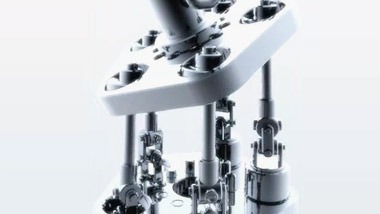
mould design
>Provide samples, drawings and requirements, and provide drawing optimization and design support and efficiency
>Good at optimizing injection mold structure and providing high-efficiency mold development services
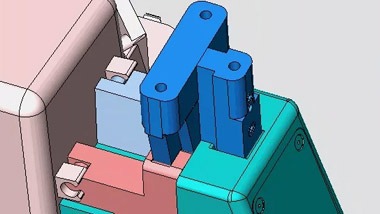
Mold making
>According to the requirements of product structure and product performance, reasonably design the mold structure and cooperate with 3D software for mold flow analysis
>Use 3D laser plate printing to make your samples meet the requirements at one time
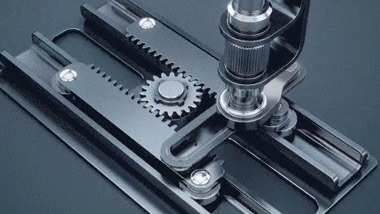
Product production
>With a complete production management team and equipment, it can deliver on time and quickly as soon as one week
>Batch production after sample determination

Product assembly
>Incoming inspection - material preparation - assembly Online - assembly - finished product inspection - shipment
The Benefits of High-Precision Injection Molding
High-precision injection molding offers several benefits, including:
Improved quality: High-precision injection molding produces parts with tight tolerances and precise geometries, resulting in improved quality and consistency.
Reduced waste: The process minimizes waste by producing parts with high accuracy and reducing the need for secondary operations, such as trimming or machining.
Increased efficiency: High-precision injection molding reduces the time and cost associated with manufacturing complex parts by eliminating the need for additional processes.
Cost-effective: High-precision injection molding is cost-effective for producing small and intricate parts in high volumes.
Applications of High-Precision Injection Molding
High-precision injection molding is used in various applications, including:
Medical devices: The process is used to manufacture parts such as surgical instruments, catheter components, and implantable devices.
Aerospace: High-precision injection molding is used to manufacture parts such as sensors, connectors, and electrical components.
Electronics: The process is used to manufacture parts such as micro switches, connectors, and housings for electronic devices.
Automotive: High-precision injection molding is used to manufacture parts such as gears, sensors, and connectors.
Factors Affecting High-Precision Injection Molding
Several factors can affect the quality and consistency of high-precision injection molding, including:
Material selection: The choice of material affects the part's mechanical properties, surface finish, and moldability. Manufacturers must select materials that meet the desired specifications and are compatible with the mold and processing conditions.
Mold design: The mold design must be optimized for high-precision injection molding, with particular attention to minimizing any imperfections that can cause defects such as warping, sink marks, or flow lines.
Processing parameters: The high-precision injection molding process parameters, such as temperature, pressure, and cooling rate, must be carefully controlled to prevent defects and ensure consistency.
Part design: The design of the part affects the ease of molding and the quality of the final product. Manufacturers must consider factors such as gate location, draft angle, and parting line location to ensure a successful high-precision injection molding process.
Custom Plastic Parts By High-Precision Injection Molding
Precision injection molding is truly a treasure in the manufacturing industry, allowing complex components with extremely high precision requirements to be perfectly presented. Imagine that every product is like a carefully crafted work of art, with every detail perfectly matched. There are many secrets hidden behind this!
Firstly, advanced equipment is needed to support it, these machines are like precision surgical knives that can accurately inject plastic raw materials into molds. Of course, the operators of these devices are experienced veterans whose eyes are like rulers, ensuring that every step is precise and error free. Selecting materials, designing molds, adjusting parameters, and planning component structures require repeated scrutiny at every step, striving for perfection.
You know what? The life-saving instruments in the medical field, key components on airplanes, electronic products that we cannot do without in our daily lives, and many precision components in the automotive industry may all be manufactured through precision injection molding technology. As long as these influencing factors are addressed one by one, it is not difficult to produce high-quality parts that meet the requirements. With the increasing demand for personalized and high-performance components in the market, the position of precision injection molding technology will only become more and more stable.
So, next time you see those exquisitely crafted products, why not think about the precision injection molding technology they may contain? Do you think they are even more precious?
FAQ About High-Precision Injection Molding
What is High-Precision Injection Molding, and how does it differ from conventional injection molding?
High-Precision Injection Molding is an advanced and specialized manufacturing process that focuses on producing extremely accurate and intricate plastic parts with tight tolerances. It is a variation of conventional injection molding, but with greater precision and control over the molding parameters and process.
The key differences between High-Precision Injection Molding and conventional injection molding are:
1. Tolerance and Accuracy: High-Precision Injection Molding achieves much tighter tolerances and higher accuracy in the dimensions of the molded parts. The process is capable of producing parts with micron-level precision, making it suitable for applications that demand exacting specifications.
2. Mold and Tooling: In High-Precision Injection Molding, the mold and tooling used are of higher quality and precision compared to those used in conventional injection molding. The molds are often made using advanced manufacturing techniques like CNC machining or electrical discharge machining (EDM) to ensure precise and consistent cavity dimensions.
3. Material Handling: High-Precision Injection Molding typically involves the use of high-grade engineering polymers and specialty materials that offer improved dimensional stability and repeatability. These materials are carefully selected to minimize any potential variations during the molding process.
4. Process Control: High-Precision Injection Molding requires meticulous process control to maintain stable and consistent conditions. Parameters such as temperature, pressure, injection speed, and cooling time are closely monitored and regulated to achieve the desired part quality and accuracy.
5. Machine Precision: Machines used for High-Precision Injection Molding are designed to provide enhanced control over the injection process. They are equipped with advanced controllers and sensors to ensure precise injection and repeatable results.
6. Post-Processing: After molding, High-Precision Injection Molded parts may undergo additional post-processing steps, such as trimming, machining, or assembly, to achieve the final required dimensions and features.
7. Applications: High-Precision Injection Molding is commonly used in industries where stringent tolerances and accuracy are essential, such as medical devices, aerospace components, electronic connectors, optical lenses, microfluidics, and other precision-engineered products.
Overall, the primary distinction between High-Precision Injection Molding and conventional injection molding lies in the level of precision and accuracy achieved in the final parts. High-Precision Injection Molding allows manufacturers to produce intricate and highly accurate components that meet the strict requirements of advanced applications, providing reliable and consistent performance.
What are the advantages of using High-Precision Injection Molding in manufacturing?
High-Precision Injection Molding offers several advantages in manufacturing, making it a preferred choice for applications that demand tight tolerances and high-quality parts. Some of the key advantages of using High-Precision Injection Molding include:
1. Superior Part Accuracy: High-Precision Injection Molding can achieve extremely tight tolerances and precise part dimensions, ensuring that the manufactured parts meet exacting specifications and requirements.
2. Consistency and Repeatability: The process provides excellent part-to-part consistency and repeatability, resulting in uniform product quality and performance throughout the production run.
3. Reduced Material Waste: With its high accuracy and precise control, High-Precision Injection Molding minimizes material waste, leading to cost savings and environmentally friendly manufacturing.
4. Complex Part Geometry: The process can produce intricate and complex part geometries with great accuracy, allowing for innovative designs and advanced functionality.
5. Enhanced Surface Finish: High-Precision Injection Molding can achieve smooth and precise surface finishes, eliminating the need for secondary finishing processes in many cases.
6. Multi-Cavity Molding: The precise control of the molding process allows for multi-cavity molds, enabling the simultaneous production of multiple identical parts in each molding cycle, increasing production efficiency.
7. High-Quality Materials: High-Precision Injection Molding uses high-grade engineering polymers and specialty materials with improved dimensional stability, enhancing the overall performance of the final parts.
8. Improved Product Performance: The precise molding process ensures that the parts have consistent and accurate dimensions, leading to better product performance and reliability.
9. Reduced Assembly Steps: The high accuracy of High-Precision Injection Molded parts often reduces the need for secondary assembly processes, simplifying production and reducing labor costs.
10. Design Flexibility: Manufacturers can achieve intricate and innovative part designs, as High-Precision Injection Molding allows for the production of micro-sized features and complex shapes.
11. Shorter Lead Times: The reduced need for post-processing and secondary operations, along with improved cycle times, can lead to shorter overall lead times for manufacturing.
12. Wide Range of Applications: High-Precision Injection Molding is suitable for a diverse range of industries and applications, including medical devices, electronics, automotive components, optics, microfluidics, and more.
Overall, the advantages of High-Precision Injection Molding make it an ideal choice for producing high-quality, accurate, and complex parts in various industries where precision and consistency are critical requirements.
Can you explain the process of High-Precision Injection Molding step-by-step?
Certainly! The process of High-Precision Injection Molding involves several steps, each meticulously controlled to achieve accurate and intricate plastic parts with tight tolerances. Here's a step-by-step explanation of the process:
Step 1: Mold Design and Preparation
- The first step is to design the mold, considering the desired part geometry, tolerances, and material selection.
- High-Precision Injection Molding requires molds with high-quality materials and precise machining to achieve the desired part accuracy.
- The mold is then prepared, cleaned, and coated with release agents to facilitate easy part ejection after molding.
Step 2: Material Selection
- High-grade engineering polymers and specialty materials are selected based on the specific application and part requirements.
- The material properties, such as flow characteristics, thermal stability, and dimensional stability, are critical for achieving high precision in the final parts.
Step 3: Material Preparation
- The selected materials are dried thoroughly to remove any moisture content that could affect the molding process and part quality.
Step 4: Injection Molding Machine Setup
- The injection molding machine is set up, and the mold is clamped securely into the machine.
- Temperature, pressure, injection speed, and other parameters are carefully set and monitored for precise control during the molding process.
Step 5: Injection
- The material is fed into the injection unit of the machine, where it is melted and homogenized.
- The molten material is then injected into the mold cavity with high pressure and speed, filling the cavity with the exact amount of material required for the part.
Step 6: Packing and Cooling
- After the cavity is filled, a packing phase may be applied to ensure that the mold is completely filled and that any shrinkage is compensated.
- The mold is then cooled to solidify the material, which can take longer than in standard injection molding due to the precision required.
Step 7: Part Ejection
- Once the material has solidified and cooled sufficiently, the mold is opened, and the parts are ejected.
- Careful ejection is crucial to avoid any damage to the precise features of the parts.
Step 8: Post-Processing (Optional)
- Depending on the specific requirements, High-Precision Injection Molded parts may undergo additional post-processing steps, such as trimming, machining, or assembly, to achieve the final required dimensions and features.
Step 9: Quality Inspection
- Each part is inspected for dimensional accuracy and quality using various measuring and testing techniques.
- Parts that meet the required specifications are approved for further use or shipment, while any defects or out-of-tolerance parts are rejected or reworked.
Step 10: Packaging and Shipment
- Finally, the approved High-Precision Injection Molded parts are packaged and prepared for shipment or further assembly, depending on the manufacturing requirements.
The entire process is carried out with strict process control and attention to detail to achieve the high level of precision and accuracy that High-Precision Injection Molding is known for.
What industries commonly utilize High-Precision Injection Molding for their products?
High-Precision Injection Molding is utilized in various industries that require parts with extremely tight tolerances, intricate geometries, and high-quality finishes. The process is favored for applications where precision and consistency are critical. Some of the industries that commonly utilize High-Precision Injection Molding for their products include:
1. Medical and Healthcare: The medical industry often requires small, precise, and complex parts for medical devices, surgical instruments, drug delivery systems, and diagnostic equipment.
2. Electronics and Electrical: The electronics industry utilizes High-Precision Injection Molding for producing intricate components such as connectors, microswitches, sensors, and other electronic parts.
3. Automotive: In the automotive sector, High-Precision Injection Molding is used to manufacture critical components like fuel system parts, sensors, connectors, and interior components with tight tolerances and high-quality finishes.
4. Aerospace: The aerospace industry demands precision and reliability in its components. High-Precision Injection Molding is used to produce parts for aircraft, satellites, and space exploration equipment.
5. Optics and Photonics: For applications in optics, photonics, and imaging devices, High-Precision Injection Molding is employed to produce lenses, optical filters, and microfluidic devices.
6. Microfluidics and Lab-on-a-Chip: High-Precision Injection Molding is crucial for producing microfluidic devices and lab-on-a-chip systems used in biomedical research, diagnostics, and point-of-care testing.
7. Industrial Equipment: Manufacturers of industrial machinery and equipment utilize High-Precision Injection Molding to create precision components with high accuracy and durability.
8. Consumer Electronics: High-Precision Injection Molding is commonly used in consumer electronics for producing precise and intricate parts for smartphones, laptops, cameras, and wearables.
9. Telecommunications: The telecommunications industry uses High-Precision Injection Molding for manufacturing components such as connectors, fiber optics, and communication devices.
10. Defense and Military: High-Precision Injection Molding is applied in the defense sector to produce critical components for military equipment and weaponry.
11. Robotics: The robotics industry uses High-Precision Injection Molding for creating intricate parts for robots and robotic systems.
12. Packaging: High-Precision Injection Molding is employed in the packaging industry for creating precise closures, caps, and other packaging components.
These are just a few examples of industries that benefit from High-Precision Injection Molding. The process is widely used in various sectors where precision, consistency, and high-quality components are essential for meeting the stringent requirements of modern applications.
What types of materials are typically used in High-Precision Injection Molding?
In High-Precision Injection Molding, a wide range of materials is used to meet the specific requirements of the intended applications. The choice of material depends on factors such as the desired part properties, functional requirements, environmental conditions, and industry standards. Some of the commonly used materials in High-Precision Injection Molding include:
1. Engineering Thermoplastics: High-performance engineering thermoplastics, such as PEEK (Polyether Ether Ketone), PEI (Polyetherimide), PPS (Polyphenylene Sulfide), and PPSU (Polyphenylsulfone), are frequently used for their excellent mechanical and thermal properties.
2. Liquid Silicone Rubber (LSR): LSR is a popular choice for producing flexible, durable, and biocompatible parts used in medical devices, baby products, and sealing applications.
3. Thermoplastic Elastomers (TPE): TPEs, also known as thermoplastic rubbers, offer a combination of properties from both rubber and plastic. They are used in applications that require flexibility, elasticity, and chemical resistance.
4. ABS (Acrylonitrile Butadiene Styrene): ABS is a versatile and widely used engineering thermoplastic known for its good impact resistance, toughness, and dimensional stability.
5. PC (Polycarbonate): PC is valued for its high impact strength, optical clarity, and heat resistance, making it suitable for applications in optics and electronics.
6. PMMA (Polymethyl Methacrylate): PMMA, commonly known as acrylic or plexiglass, is used for transparent or translucent parts due to its optical clarity and excellent light transmission.
7. POM (Polyoxymethylene): POM is a high-strength engineering plastic with low friction and good dimensional stability, making it suitable for precision gears and mechanical components.
8. PA (Nylon): Nylon is known for its toughness, wear resistance, and excellent mechanical properties, making it suitable for a wide range of applications.
9. PBT (Polybutylene Terephthalate): PBT is often used for its good electrical properties, dimensional stability, and resistance to chemicals.
10. PSU (Polysulfone): PSU is a high-temperature engineering plastic with excellent chemical resistance and hydrolytic stability, commonly used in medical and aerospace applications.
11. PEEK (Polyether Ether Ketone): PEEK is a high-performance thermoplastic with exceptional mechanical, thermal, and chemical properties, suitable for demanding applications in aerospace, medical, and automotive industries.
12. Liquid Crystal Polymer (LCP): LCP offers excellent strength, chemical resistance, and dimensional stability, making it suitable for high-precision electrical connectors and components.
These are just a few examples of materials commonly used in High-Precision Injection Molding. Manufacturers can choose from a vast selection of materials, each with its unique properties, to achieve the required characteristics for their high-precision components. Material selection is a critical aspect of the process and is based on a thorough understanding of the application's demands and performance requirements.
How does High-Precision Injection Molding contribute to improved product quality and consistency?
High-Precision Injection Molding plays a significant role in improving product quality and consistency by offering a level of accuracy, repeatability, and control that is not easily achievable with conventional molding processes. Here are several ways in which High-Precision Injection Molding contributes to enhanced product quality and consistency:
1. Tighter Tolerances: High-Precision Injection Molding can achieve extremely tight tolerances, sometimes in the micron range. This level of precision ensures that the final parts meet exact specifications and perform consistently within the required limits.
2. Uniform Part Dimensions: The process provides excellent part-to-part consistency and repeatability. Each molded part is produced with precise dimensions, resulting in a more uniform product that functions consistently across the entire production run.
3. Reduced Variability: The high accuracy and process control in High-Precision Injection Molding minimize variations between individual parts, leading to reduced defects and waste.
4. Minimal Warpage and Shrinkage: With precise control over temperature and cooling rates, High-Precision Injection Molding minimizes warpage and shrinkage issues that can negatively impact part quality.
5. Improved Surface Finish: High-Precision Injection Molding can achieve smooth and precise surface finishes, reducing the need for additional post-processing steps like polishing or machining.
6. Elimination of Defects: The accuracy of the molding process and the use of high-quality molds help reduce common defects like sink marks, flash, and gate vestiges, leading to higher-quality parts.
7. Consistent Material Properties: The process uses high-grade engineering polymers and specialty materials with excellent dimensional stability and consistency. This ensures that the material properties remain uniform across all parts.
8. Precise Material Placement: High-Precision Injection Molding allows for precise control over material flow and placement within the mold cavity, ensuring that each feature of the part is accurately formed.
9. Multi-Cavity Molding: The process supports multi-cavity molds, enabling the simultaneous production of multiple identical parts in each molding cycle, ensuring consistency in part quality and performance.
10. Reduced Assembly Requirements: The high accuracy of High-Precision Injection Molded parts often reduces the need for secondary assembly processes, eliminating potential misalignments or defects introduced during assembly.
11. Enhanced Product Performance: The consistent and accurate dimensions of High-Precision Injection Molded parts lead to better product performance and reliability, meeting the stringent requirements of demanding applications.
12. Shorter Lead Times: The reduced need for post-processing and secondary operations, along with improved cycle times, can lead to shorter overall lead times for manufacturing.
Overall, High-Precision Injection Molding offers manufacturers the ability to produce high-quality, accurate, and consistent parts, which are critical for meeting the exacting demands of industries such as medical, aerospace, electronics, and automotive. By delivering reliable and consistent parts, High-Precision Injection Molding helps ensure that the final products meet the highest standards of performance and quality.
What tolerances can be achieved with High-Precision Injection Molding?
High-Precision Injection Molding is capable of achieving exceptionally tight tolerances, which are typically measured in micrometers (µm) or microns (μm). The achievable tolerances depend on various factors, including the complexity of the part design, the selected materials, the precision of the mold and tooling, and the overall process control. In many cases, the tolerances can be held to within a few micrometers, making High-Precision Injection Molding suitable for applications that demand the highest levels of accuracy and consistency.
The specific tolerances that can be achieved with High-Precision Injection Molding can vary based on the following factors:
1. Part Size: Generally, smaller parts can achieve tighter tolerances compared to larger parts due to reduced material shrinkage and thermal variations.
2. Material Properties: Some materials have better dimensional stability and lower coefficients of thermal expansion, making them more suitable for achieving tight tolerances.
3. Mold Design and Quality: The precision and quality of the mold and tooling play a crucial role in achieving tight tolerances. High-quality molds with advanced machining techniques allow for better control over part dimensions.
4. Process Control: Maintaining precise control over the injection molding process parameters, including temperature, pressure, and cooling rates, is essential to achieving consistent and accurate parts.
5. Part Complexity: Highly complex parts with intricate features may have slightly looser tolerances compared to simpler parts due to the increased challenges in molding intricate geometries.
As a general guideline, High-Precision Injection Molding can achieve tolerances in the range of ±0.01 mm (10 µm) to ±0.05 mm (50 µm) for many applications. In some cases, even tighter tolerances down to ±0.002 mm (2 µm) or better can be achieved for critical dimensions.
It's important to note that achieving such high tolerances requires careful planning, precision tooling, skilled process optimization, and thorough quality control measures. The capabilities of High-Precision Injection Molding make it a preferred choice for manufacturing parts with intricate features, tight fits, and precise dimensions required in industries such as medical, electronics, aerospace, and automotive, among others.
How does the cost of High-Precision Injection Molding compare to other molding methods?
The cost of High-Precision Injection Molding can be higher than that of conventional molding methods due to several factors associated with the process. While High-Precision Injection Molding offers numerous advantages, including tight tolerances and improved part quality, it involves additional considerations that influence the overall cost. Some factors that contribute to the cost difference include:
1. High-Quality Tooling: High-Precision Injection Molding requires molds and tooling of superior quality and precision. These molds are often made using advanced machining techniques like CNC milling or electrical discharge machining (EDM) to achieve tight tolerances, which can increase the initial tooling costs.
2. Material Selection: High-Precision Injection Molding often involves the use of high-grade engineering polymers and specialty materials that come at a higher cost than standard materials used in conventional molding.
3. Process Control: The process demands meticulous process control to maintain stable and consistent conditions, which may require more advanced equipment and monitoring systems.
4. Design Complexity: Parts with intricate geometries and tight tolerances may require specialized mold features and precise machining, contributing to the overall cost.
5. Longer Cycle Times: High-Precision Injection Molding may have longer cycle times due to the need for slow and controlled cooling to prevent warpage and distortion. This can affect production throughput and increase manufacturing costs.
6. Post-Processing: Depending on the part requirements, High-Precision Injection Molded parts may undergo additional post-processing steps, such as trimming, machining, or assembly, which can add to the overall cost.
7. Volume of Production: High-Precision Injection Molding is often more cost-effective for low to medium production volumes. For high-volume production, the costs may become more competitive when using conventional molding methods.
It is essential to consider the specific requirements of the project and the benefits of High-Precision Injection Molding when evaluating the cost. While the initial investment and part price may be higher, the advantages of achieving tight tolerances, reduced defects, and enhanced part quality can outweigh the cost difference, especially for critical applications where precision and consistency are paramount.
Manufacturers must carefully analyze the trade-offs and choose the most suitable molding method based on factors like part complexity, volume, required tolerances, material properties, and the overall cost-effectiveness for their specific project.
What are some common challenges or limitations associated with High-Precision Injection Molding?
High-Precision Injection Molding, while offering numerous advantages, also comes with some challenges and limitations that manufacturers should be aware of. Addressing these challenges is crucial to ensure successful implementation of the process. Some common challenges and limitations associated with High-Precision Injection Molding include:
1. High Tooling Costs: High-Precision Injection Molding requires molds and tooling of exceptional quality and precision, which can result in higher initial tooling costs compared to standard injection molding.
2. Longer Cycle Times: Achieving high precision often involves slower injection and cooling cycles, which can lead to longer production times, potentially affecting overall production throughput.
3. Material Selection: The selection of suitable materials with low coefficients of thermal expansion and excellent dimensional stability is critical to achieving tight tolerances. Some high-precision materials may be more expensive and challenging to process.
4. Complexity of Part Design: Parts with intricate geometries and tight tolerances may be more challenging to mold accurately, increasing the complexity of the molding process.
5. Part Warpage and Shrinkage: High-Precision Injection Molding is sensitive to thermal variations, which can lead to part warpage or shrinkage if not carefully managed.
6. Defect Sensitivity: Due to the high precision required, the process can be more sensitive to variations in material quality, process parameters, and mold conditions, making it crucial to have stringent quality control measures.
7. Limited Material Compatibility: High-Precision Injection Molding may have limitations in terms of material compatibility for multi-material or overmolding applications, restricting certain design possibilities.
8. Cost for Small Production Runs: The cost-effectiveness of High-Precision Injection Molding can diminish for very small production runs, as the initial tooling investment may not be justified for limited quantities.
9. Assembly Complexity: Complex part designs with tight tolerances may require careful assembly techniques and tooling, which can add complexity and cost to the manufacturing process.
10. Design Restrictions: Achieving tight tolerances and high precision may impose design constraints, requiring certain features or dimensions to be modified to accommodate the molding process.
11. Surface Imperfections: Despite the high quality achievable with High-Precision Injection Molding, very demanding optical or surface appearance applications may still face challenges in achieving perfection.
12. Part Size Limitations: The process may have limitations in molding very large parts with high precision due to the potential for material cooling and warpage issues.
Despite these challenges and limitations, High-Precision Injection Molding remains an invaluable process for manufacturing parts with the utmost accuracy and quality. Addressing these challenges through careful design, material selection, process optimization, and rigorous quality control measures can lead to successful outcomes in many critical applications across various industries.
Can you provide examples of products that are commonly manufactured using High-Precision Injection Molding?
Certainly! High-Precision Injection Molding is used to manufacture a wide range of products across various industries, especially those that require exacting specifications and tight tolerances. Some examples of products commonly manufactured using High-Precision Injection Molding include:
1. Medical Devices: High-precision components used in medical devices, such as syringe barrels, surgical instruments, drug delivery systems, catheters, and microfluidic devices.
2. Electronics and Electrical Components: Precision connectors, sockets, switches, microchips, and miniature components used in various electronic devices and circuitry.
3. Automotive Components: Precision automotive parts like fuel system components, sensors, connectors, electronic control units (ECUs), and lighting systems.
4. Aerospace Components: High-precision parts for aircraft and aerospace applications, such as fuel system components, airframe structures, and electronic connectors.
5. Optics and Imaging Devices: Optical lenses, lens arrays, camera components, laser optics, and imaging system components.
6. Microfluidics and Lab-on-a-Chip Devices: Microfluidic chips and lab-on-a-chip devices used in biomedical research, diagnostics, and point-of-care testing.
7. Watch Components: High-precision parts for watch movements, such as gears, pinions, and other intricate components.
8. Consumer Electronics: Small, precise components used in smartphones, laptops, cameras, wearables, and other electronic devices.
9. Telecommunications Components: Precision connectors, fiber optic components, and communication devices for the telecommunications industry.
10. Defense and Military Equipment: High-precision components for military equipment, weapons, communication systems, and surveillance devices.
11. Robotics and Automation Components: Precision parts for robotic arms, grippers, and automation systems.
12. Injection Pen Systems: Precision components used in injection pen systems for medical and pharmaceutical applications.
These examples illustrate the versatility of High-Precision Injection Molding and its suitability for manufacturing intricate and high-quality components across a wide range of industries. The process plays a crucial role in meeting the demanding requirements of modern technology, healthcare, transportation, aerospace, and other advanced applications.
What are the key design considerations for High-Precision Injection Molding to achieve accurate and complex parts?
Designing for High-Precision Injection Molding requires careful attention to detail to ensure that accurate and complex parts can be successfully manufactured. Here are some key design considerations to achieve the desired precision and quality:
1. Tolerances and Specifications: Clearly define the required tolerances and specifications for each feature of the part. Communicate these requirements with the molding manufacturer to ensure they can be met.
2. Part Geometry: Design parts with simple and consistent geometries where possible to facilitate the molding process and minimize the risk of defects.
3. Wall Thickness: Maintain uniform wall thickness throughout the part to avoid sink marks, warpage, and uneven cooling.
4. Draft Angles: Incorporate draft angles into the design to facilitate part ejection from the mold and prevent damage to the part during ejection.
5. Gate Placement: Position gates strategically to minimize visible marks on the part surface and ensure proper material flow.
6. Material Selection: Choose materials with low coefficients of thermal expansion and excellent dimensional stability to minimize part warpage and distortion.
7. Material Flow: Design the part to allow for smooth and even material flow during injection to avoid flow marks and other surface imperfections.
8. Undercuts and Overmolding: Minimize undercuts and overmolding features, or include appropriate mechanisms for part ejection and mold release.
9. Ejection Points: Identify suitable ejection points on the part to avoid affecting critical dimensions or features.
10. Critical Dimensions: Identify critical dimensions that require the highest level of precision and ensure they are appropriately located and specified.
11. Mold Design: Work closely with mold designers to ensure that the mold can accommodate the desired precision and complex features.
12. Mold Venting: Ensure proper mold venting to prevent trapped air and gas, which can cause defects like burn marks or voids.
13. Surface Finish: Specify the required surface finish for the part and consider post-processing requirements to achieve the desired appearance and performance.
14. Part Size and Complexity: Be aware of the potential limitations of the molding process in terms of part size and complexity, and design accordingly.
15. Prototyping and Testing: Consider prototyping and testing to validate the design before committing to full-scale production, especially for complex or critical parts.
By taking these design considerations into account during the early stages of product development, engineers and designers can optimize the design for High-Precision Injection Molding, ensuring that accurate and complex parts can be manufactured with the desired level of precision and quality. Collaborating closely with experienced molding manufacturers can further enhance the design process and lead to successful outcomes in high-precision molding projects.
How is the equipment and machinery used in High-Precision Injection Molding different from standard injection molding equipment?
The equipment and machinery used in High-Precision Injection Molding are specialized and designed to meet the stringent requirements of producing accurate and intricate parts with tight tolerances. While there are similarities between standard injection molding equipment and High-Precision Injection Molding equipment, there are some key differences to achieve the higher level of precision. Here are some of the differences:
1. CNC-Machined Molds: High-Precision Injection Molding often uses molds that are CNC-machined or manufactured using advanced machining techniques. This ensures precise cavity dimensions and tight tolerances, reducing part variability.
2. Enhanced Mold Cooling: High-Precision Injection Molding requires precise temperature control during the molding process to minimize warpage and ensure consistent part quality. The machinery may have enhanced cooling systems to achieve this level of control.
3. Precision Injection Units: The injection units of High-Precision Injection Molding machines are designed to provide precise control over material flow and injection speed to achieve accurate part filling.
4. Advanced Process Control: High-Precision Injection Molding machines are equipped with advanced process control systems, sensors, and monitoring capabilities to maintain precise and stable process conditions.
5. High-Resolution Pressure and Temperature Sensors: High-precision machines often incorporate high-resolution pressure and temperature sensors to monitor the injection process with greater accuracy.
6. Precise Shot Control: High-Precision Injection Molding machines have precise shot control to ensure accurate material dosing for each shot.
7. Low-Velocity Injection: The machines can be configured for low-velocity injection to prevent material shear and ensure consistent part quality in delicate or thin-walled components.
8. High-Speed Molding: Some high-precision machines can also operate at high speeds while maintaining accuracy, enabling faster cycle times without compromising quality.
9. Closed-Loop Feedback Systems: High-Precision Injection Molding machines may use closed-loop feedback systems to continuously adjust process parameters based on real-time data, ensuring greater process consistency.
10. Material Handling and Drying: High-precision materials may require special handling and drying processes to eliminate moisture and ensure consistent material properties.
11. Precise Ejection Systems: The ejection systems are designed to gently and accurately eject parts without causing damage to intricate features.
12. Quality Control and Inspection Systems: High-Precision Injection Molding machines may incorporate in-line quality control and inspection systems to ensure that parts meet the specified tolerances and dimensions.
These differences in equipment and machinery allow High-Precision Injection Molding to achieve the level of accuracy and repeatability required for manufacturing parts with tight tolerances and complex geometries. The precise control and monitoring capabilities of these machines ensure consistent and reliable production of high-quality components across various industries.