Servizi di estrusione di metalli: precisione, versatilità
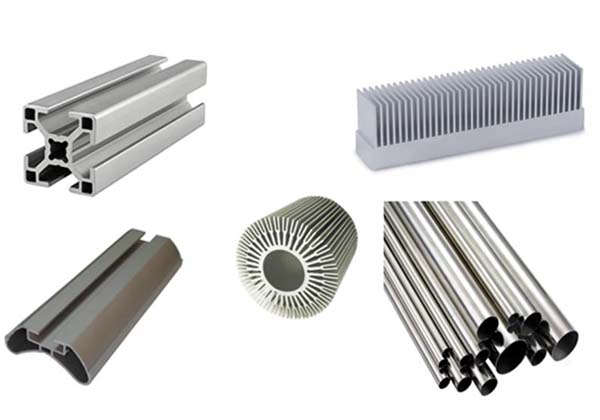
What is Metal Extrusion?
Definition: Metal extrusion is a high - precision manufacturing process where a heated or cold metal billet is forced through a die with a specific cross - sectional profile, shaping it into continuous lengths of uniform geometry. This process leverages compressive forces to achieve intricate shapes, tight tolerances, and enhanced mechanical properties, making it ideal for both simple and complex components.
Core Principles: Plastic Deformation: The metal undergoes permanent shape change under controlled pressure. When the metal billet is forced through the die, the atoms within the metal re - arrange themselves, resulting in a new shape that remains even after the external force is removed.
Die Design: Custom dies determine the final product’s cross - section, enabling precise replication of profiles. A well - designed die can produce complex cross - sectional shapes such as hollow tubes, multi - chambered profiles, and intricate architectural components. For example, a die for producing a window frame extrusion will have a very specific shape that includes channels for seals and slots for attaching other parts.
Types of Metal Extrusion Processes
By Temperature
Process | Temperature Range | Material State | Advantages | Applicazioni |
Hot Extrusion | Above recrystallization | Soft, ductile | Large-scale components, structural parts | |
Cold Extrusion | Room temperature | Work-hardened | Excellent surface finish, tight tolerances | Small, high-precision parts (e.g., gears, fasteners) |
Warm Extrusion | Between room temp and recrystallization | Reduced work hardening | Balances formability and surface quality | Medium-complexity parts (e.g., aluminum alloys) |
- Hot Extrusion:
- Explanation: When the metal is heated above its recrystallization temperature, it becomes more malleable. This allows for the extrusion of high - strength metals like steel e titanium into large - scale components. For example, the large - diameter pipes used in oil and gas transportation are often produced through hot extrusion. The heat reduces the force required for extrusion, making it suitable for materials that are otherwise difficult to shape at room temperature.
- Key Benefits: High formability, which is crucial for creating large and complex shapes from hard - to - work metals. It also reduces the risk of cracking during the extrusion process due to the increased ductility of the metal at high temperatures.
- Cold Extrusion:
- Explanation: Cold extrusion is carried out at room temperature. The process work - hardens the metal, which can improve its mechanical properties. However, it requires higher forces compared to hot extrusion. Small - scale components such as precision gears and fasteners are often cold - extruded. The lack of heat allows for better control over the final dimensions and surface finish, resulting in parts with tight tolerances.
- Key Benefits: Produces parts with excellent surface finish and tight dimensional tolerances. The work - hardening effect can also enhance the strength and wear - resistance of the final product.
- Warm Extrusion:
- Explanation: Warm extrusion strikes a balance between hot and cold extrusion. The metal is heated to a temperature between room temperature and its recrystallization temperature. This reduces work hardening compared to cold extrusion while still maintaining better dimensional control than hot extrusion. Aluminum alloy parts with medium complexity, such as some automotive components, are often produced using warm extrusion.
- Key Benefits: Combines the advantages of both hot and cold extrusion, offering good formability and surface quality. It also requires less force than cold extrusion and better dimensional accuracy than hot extrusion for certain applications.
By Material Flow Direction
- Direct Extrusion: In direct extrusion, the material flows in the same direction as the applied force. This is the most common method for producing simple profiles. For example, when extruding a basic aluminum rod, the billet is pushed through a die, and the extruded rod emerges in the same direction as the force applied. It is straightforward and suitable for a wide range of materials and cross - sectional shapes. However, the friction between the billet and the container wall can be high, which may limit the length of the extruded product and increase the energy required for extrusion.
- Indirect Extrusion: Here, the material flows opposite to the applied force. A ram pushes a dummy block, which in turn moves the billet through the die. This method reduces friction and die wear significantly. It is particularly suitable for soft metals like copper. Since there is less friction, the quality of the extruded product can be higher, and the process can be more energy - efficient for these soft materials. However, the equipment for indirect extrusion is more complex and expensive compared to direct extrusion.
- Composite Extrusion: Composite extrusion combines both direct and indirect flow for producing complex, multi - section parts. For instance, parts with varying cross - sectional areas or those made from multiple materials can be created using this method. It offers greater design flexibility but requires more precise control over the extrusion process and more advanced tooling.
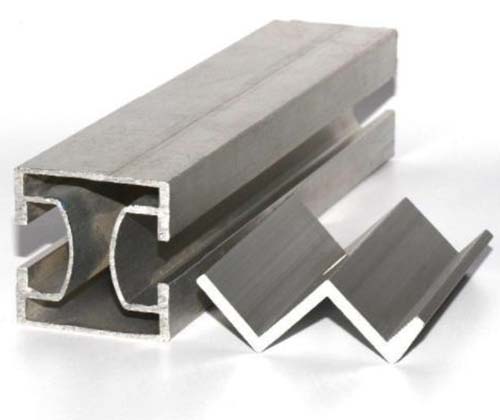
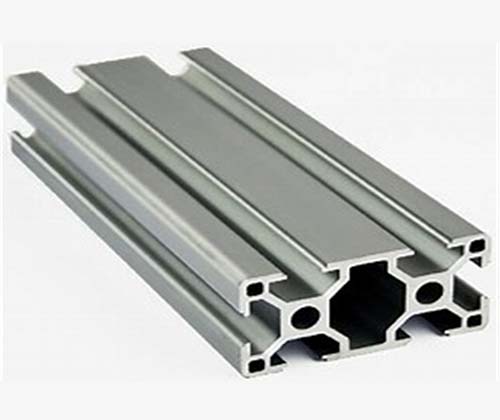
Materials for Metal Extrusion
Common Extrudable Metals
Material | Key Properties | Typical Applications |
Aluminum Alloys | Lightweight, corrosion-resistant, high thermal conductivity | Aerospace components, automotive parts, heat sinks |
Rame Alloys | Excellent electrical conductivity, ductility | Electrical connectors, plumbing fixtures |
High strength, corrosion resistance | Medical devices, industrial equipment, architectural elements | |
Titanium Alloys | High strength-to-weight ratio, heat resistance | Aerospace structures, marine components |
Nichel Alloys | Exceptional heat and corrosion resistance | Turbine parts, chemical processing equipment |
- Aluminum Alloys: Aluminum alloys are popular due to their low density, which is about one - third that of steel. They are highly corrosion - resistant, thanks to the formation of a thin oxide layer on their surface when exposed to air. Their high thermal conductivity makes them ideal for heat sinks in electronics and cooling systems in automotive applications. For example, the 6061 aluminum alloy, containing magnesium and silicon, is widely used in the aerospace industry for its good strength - to - weight ratio and excellent formability during extrusion.
- Copper Alloys: Copper alloys are renowned for their outstanding electrical conductivity, second only to silver among common metals. This property makes them indispensable in the electrical and electronics industries. They are also highly ductile, allowing for complex shapes to be extruded. Brass, an alloy of copper and zinc, is often used for plumbing fixtures due to its corrosion resistance and ease of machining.
- Acciaio inossidabile: Stainless steel contains a minimum of 10.5% chromium, which provides it with excellent corrosion - resistant properties. It also has high strength, making it suitable for applications that require durability and resistance to harsh environments. In the medical device industry, stainless steel is used to make surgical instruments and implants because of its biocompatibility and corrosion resistance. In architecture, it is used for decorative elements and structural components in buildings.
- Titanium Alloys: Titanium alloys offer an impressive strength - to - weight ratio, which is crucial in applications where weight reduction is essential without sacrificing strength, such as in aerospace. They also have excellent heat resistance, allowing them to maintain their mechanical properties at high temperatures. Titanium alloys are used in the construction of aircraft frames, engine components, and in marine applications where corrosion resistance in seawater is vital.
- Nichel Alloys: Nickel alloys are prized for their exceptional heat and corrosion resistance. They can withstand extreme temperatures and corrosive chemicals, making them suitable for use in turbine parts in power generation and chemical processing equipment. In a chemical plant, nickel - based alloys are used in reactors and pipelines that handle corrosive substances.
Material Selection Tips
- Strength Requirements: For applications that involve high - stress conditions, such as in the construction of heavy - duty machinery or high - performance aircraft components, materials like steel or titanium alloys are preferred. Steel offers high strength and is cost - effective for large - scale industrial applications. Titanium alloys, on the other hand, provide a high strength - to - weight ratio, making them suitable for applications where weight reduction is crucial without compromising on strength.
- Corrosion Needs: In harsh environments, such as marine or chemical processing settings, materials with good corrosion resistance are essential. Aluminum alloys are a good choice for applications where light weight and moderate corrosion resistance are required, like in boat hulls. Stainless steel is an excellent option when high - level corrosion resistance is needed, such as in chemical storage tanks or medical equipment that may be exposed to disinfectants and body fluids.
Surface Finishing Options
Enhanced Durability and Aesthetics
- Anodizing: Forms a protective oxide layer on aluminum, improving corrosion resistance and enabling vibrant colors. Anodizing is an electrochemical process. For aluminum extrusion products, it can create an oxide layer ranging from 5 - 30 microns in thickness for general applications, and up to 25 - 150 microns for hard - anodized coatings. This not only makes the aluminum more resistant to corrosion but also allows for various coloring options, making it suitable for both industrial and decorative applications like architectural facades and consumer electronics casings.
- Electroplating: Deposits metals like nickel or chrome for wear resistance and decorative finishes. The thickness of nickel plating can vary based on the application. For light - duty decorative purposes, a thickness of 0.01 - 0.02mm might be sufficient, while for applications requiring higher wear resistance, such as in the automotive or machinery industries, the nickel plating thickness can be increased to 0.05 - 1.0mm. Chrome plating, on the other hand, is often used for its shiny, decorative appearance as well as its ability to enhance corrosion resistance, especially on parts like bathroom fixtures and automotive trim.
- Powder Coating: Provides a durable, uniform finish with excellent chemical resistance. Powder coating is a dry finishing process where a powder (usually a mixture of resins, pigments, and additives) is electrostatically applied to the metal surface and then cured under heat. This results in a tough, uniform coating that can withstand harsh chemical environments. It is commonly used in applications such as outdoor furniture, industrial equipment, and building components where long - term durability and weather resistance are crucial.
- Lucidatura: Achieves a mirror - like surface for aesthetic or functional purposes (e.g., reflectors). Polishing can be done through mechanical or chemical means. Mechanical polishing uses abrasives to gradually smooth the metal surface, while chemical polishing uses chemical solutions to dissolve the surface layer evenly. For applications like reflectors in lighting fixtures, a high - quality mirror - like finish is essential, and polishing can ensure that the extruded metal parts meet these strict requirements.
Applications Across Industries
Diverse Industrial Solutions
- Aerospaziale: In the aerospace industry, weight reduction is crucial for fuel efficiency and performance. Aluminum and titanium components produced by extrusion are lightweight yet strong, making them ideal for aircraft frames and engine parts. For example, the fuselage of many modern aircraft contains extruded aluminum alloy sections that contribute to its structural integrity while keeping the overall weight down. Titanium extrusions are used in high - temperature areas such as engine components due to their heat - resistant properties.
- Automotive: The automotive industry benefits from metal extrusion for producing complex - shaped parts. Steel and aluminum are commonly extruded into transmission components, chassis parts, and exhaust systems. Extruded aluminum alloy chassis components can reduce the vehicle's weight, improving fuel economy. The complex cross - sectional shapes required for transmission gears and shafts can be efficiently produced through extrusion, ensuring high precision and strength.
- Construction: Aluminum profiles are extensively used in construction for windows, doors, and building frameworks. Their corrosion resistance, light weight, and ability to be extruded into various shapes make them a popular choice. For instance, the frames of modern office buildings often feature extruded aluminum profiles that provide both structural support and an aesthetically pleasing appearance. These profiles can be easily customized with different finishes, such as anodizing or powder coating, to match the building's design.
- Electronics: High - conductivity copper is extruded into heat sinks to dissipate heat from electronic components, ensuring their proper functioning. Precision stainless steel connectors are also produced through extrusion. In a computer's central processing unit (CPU), a copper heat sink extruded with fins can effectively transfer heat away from the CPU, preventing overheating. The small, intricate shapes of stainless - steel connectors for high - speed data transfer are achievable through extrusion, maintaining high - quality electrical connections.
- Medical: Corrosion - resistant stainless steel and titanium are used to manufacture implants and surgical instruments. These materials' biocompatibility and durability are essential in medical applications. For example, titanium hip implants, often produced through extrusion, can withstand the mechanical stresses in the human body over long periods. Stainless - steel surgical instruments, with their sharp edges and precise shapes achieved through extrusion, are crucial for accurate surgical procedures.
Case Study: Automotive Chassis Component
- Riduzione del peso: The cold - extrusion process allowed for the production of high - strength aluminum alloy brackets with a complex internal structure designed for optimal strength - to - weight ratio. As a result, the part weight was reduced by 30% compared to the previous design, contributing to the overall weight reduction of the vehicle. This, in turn, improved the vehicle's energy efficiency and extended its driving range.
- Production Time: Cold extrusion is a high - speed process. By implementing it, the manufacturer reduced the production time of the chassis brackets by 25%. This increase in production efficiency enabled them to meet the growing market demand for their EVs more effectively.
- Quality Assurance: The cold - extruded brackets achieved ISO 20285 automotive quality certification. This certification ensured that the parts met strict quality standards in terms of dimensional accuracy, material properties, and surface finish. The tight tolerances achievable through cold extrusion guaranteed proper fitment within the vehicle's chassis, enhancing the overall safety and performance of the vehicle.
Advantages of Our Metal Extrusion Services
Technical Excellence
- Design Freedom: Our state - of - the - art extrusion technology allows for the creation of intricate profiles that are simply impossible to achieve with traditional machining methods. Whether it's a hollow, thin - walled component for a high - tech device or a multi - lumen profile for a medical application, we can bring your complex designs to life. For example, we've successfully produced hollow aluminum heat sink extrusions with extremely thin walls for the electronics industry. These heat sinks are designed to maximize surface area for efficient heat dissipation while keeping the weight and size to a minimum.
- Cost Efficiency: We are committed to minimizing waste in the manufacturing process. Our extrusion techniques can achieve up to 95% material utilization, which means less raw material is wasted compared to other manufacturing methods. Additionally, our high - speed production capabilities significantly reduce labor costs. High - volume production runs can be completed in a shorter time frame, making our services cost - effective for both small - and large - scale projects.
- Mechanical Performance: The metal extrusion process results in parts with a uniform grain structure. During extrusion, the metal undergoes directional solidification, which aligns the grains in a favorable direction. This alignment improves the strength and mechanical properties of the final product. For instance, extruded aluminum alloy parts used in automotive suspensions can withstand higher stress levels due to their enhanced grain structure, leading to better - performing and more durable components.
Process Benefits
Metric | Performance |
Tolerance Accuracy | ±0.05mm for cold extrusion |
Production Speed | Up to 10 meters/minute for simple profiles |
Minimum Wall Thickness | 0.8mm for aluminum alloys |
- Tolerance Accuracy: In cold extrusion, we can achieve a tolerance accuracy of ±0.05mm. This high level of precision ensures that the extruded parts fit perfectly into their intended assemblies. For applications such as aerospace and medical devices, where tight tolerances are crucial for proper functioning, our cold - extrusion process can meet these exacting standards.
- Production Speed: For simple profiles, our extrusion process can reach speeds of up to 10 meters/minute. This high - speed production allows us to meet tight deadlines and high - volume demands. For example, in the production of standard aluminum window frames, our fast extrusion speed enables us to produce a large number of units in a short time, reducing lead times for our customers in the construction industry.
- Minimum Wall Thickness: We can produce aluminum alloy parts with a minimum wall thickness of 0.8mm. This capability is especially valuable for applications where weight reduction is important without sacrificing structural integrity. In the production of lightweight components for the automotive or aerospace industries, our ability to achieve such thin walls while maintaining strength is a significant advantage.
Why Choose Yigu Technology for Metal Extrusion?
When it comes to metal extrusion, Yigu Technology stands out as a premier choice. Our commitment to excellence, advanced capabilities, and customer - centric approach make us the ideal partner for all your metal extrusion needs.
Our Competitive Edge
- 20+ Years of Expertise: With over 20 years in the industry, we have a proven track record of delivering high - quality custom extrusions. We've successfully completed 50,000+ projects for global industrial clients across various sectors, from aerospace to automotive. This wealth of experience allows us to handle even the most complex extrusion challenges with ease.
- Advanced Equipment: Our state - of - the - art facilities are equipped with CNC extrusion presses ranging from 500 - 5,000 tons, ensuring we can handle projects of all sizes. Additionally, our in - house die design capabilities enable us to create custom dies quickly and efficiently, reducing lead times and ensuring the highest quality products.
- Quality Assurance: We are ISO 9001:2015 certified, demonstrating our commitment to quality management systems. Every extrusion undergoes 100% dimensional inspection using 3D coordinate measuring machines (CMM). This rigorous inspection process ensures that our products meet or exceed industry standards, providing you with peace of mind.
- Sustainability Focus: We are committed to environmental responsibility. We offer 100% recycled material options for our extrusions, and our energy - efficient processes have reduced our carbon footprint by 40%. By choosing Yigu Technology, you're not only getting high - quality products but also contributing to a more sustainable future.
Client Testimonial
FAQs Metal Extrusion
There is no strict minimum order quantity. We can accommodate both small - scale prototyping and large - volume production runs.
For standard orders, the production time can range from 2 - 4 weeks, depending on the complexity of the design, material type, and order quantity.
Yes, we have experience working with a wide range of standard and non - standard metal alloys. Please provide us with the specific alloy composition and requirements, and we can determine the feasibility.
Our equipment can produce extruded products up to 12 meters in length. For longer lengths, we may be able to provide solutions through additional processing or splicing methods.
Yes, our experienced engineering team can provide design assistance. We can help optimize your designs for manufacturability, ensuring the best possible results in terms of quality, cost, and production time.
We source raw materials from reliable suppliers and conduct thorough quality checks upon receipt. We also maintain strict inventory management to ensure the integrity of the materials.
The cost can vary depending on factors like material type, product complexity, and production volume. Generally, cold extrusion may be more expensive for high - strength materials due to the higher forces required, while hot extrusion can be more cost - effective for large - scale production of certain metals. Warm extrusion often offers a balance in cost and performance.
Yes, we can provide samples for you to evaluate the quality, dimensions, and finish of the extruded product before proceeding with mass production.
We offer a range of post - extrusion services, including cutting, drilling, tapping, and surface finishing such as anodizing, electroplating, powder coating, and polishing.
We can arrange for transportation through our trusted logistics partners. We ensure that the products are properly packaged to prevent damage during transit and can deliver them to your specified location, whether it's locally or internationally.