Servizi di fabbricazione di lamiere
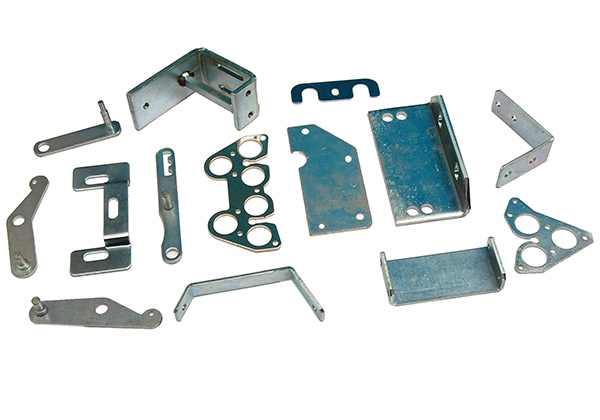
What Is Sheet Metal Fabrication?
Defining the Process: Sheet metal fabrication is a versatile manufacturing technique that transforms flat metal sheets into custom components through cutting, bending, forming, and assembling. Using advanced machinery like laser cutters, CNC presses, and robotic welders, we shape materials into precise parts with tight tolerances (typically ±0.05mm), catering to both prototyping and high-volume production across industries.
Types of Sheet Metal Fabrication Processes
Core Fabrication Methods
Process | Description | Advantages | Common Applications |
Laser Cutting | Utilizes a high - energy laser beam to precisely cut sheet metal. Minimum aperture 可达 0.5mm, and edge roughness Ra≤1.6μm. | Electronic components, medical device housings | |
Bending | High - precision angle control (±1°), supports multi - step forming | Equipment enclosures, structural brackets | |
Uses dies on a press to punch, draw, or emboss. Enables mass production with die life exceeding 500,000 cycles. | Efficient mass production, complex 3D structure forming | Automotive body panels, home appliance facades | |
Welding | Connects components using TIG/MIG/laser welding. Supports precision welding of stainless steel/aluminum alloy, with weld strength ≥ 85% of the base material. | Structural integration, manufacturing of load - bearing components | Machinery frames, aerospace components |
Specialty Techniques
- Precision Forming: For sheet metal with a thickness of 0.2mm - 6mm, progressive dies are used to achieve multi - process continuous processing, increasing efficiency by 30%.
- Bend Relief: CAD simulation is used to account for bending springback, ensuring dimensional accuracy of complex structural parts (±0.03mm for critical features).
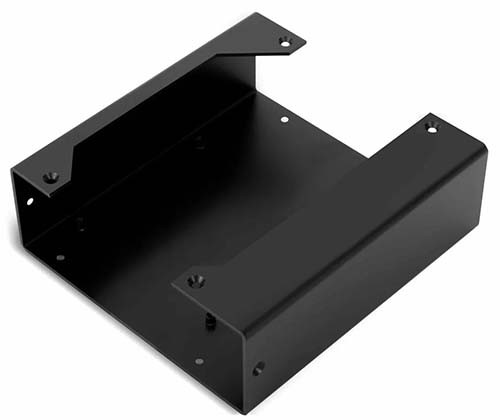
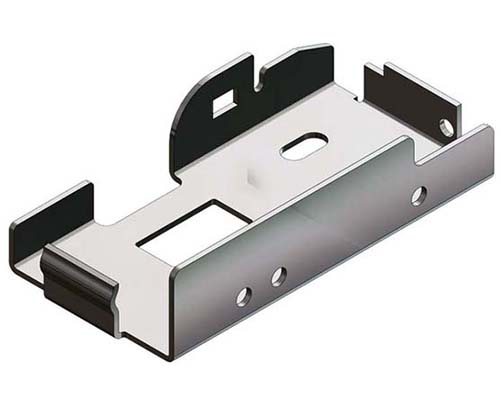
Sizes and Tolerances: Meeting Your Precision Requirements
Material Size Capabilities
Process | Size Range |
Sheet Thickness | 0.1mm (aluminum foil) - 12mm (carbon steel) |
Laser Cutting | Maximum 2000mm×4000mm |
Bending | Maximum length 3000mm, minimum bending edge 5mm |
Tolerance Control Methods
- First Article Inspection, FAI: We use Coordinate Measuring Machines (CMM) to conduct a comprehensive inspection of the first - produced part. This allows us to verify critical dimensions and make any necessary adjustments before full - scale production.
- n - Process Monitoring: During production, we conduct regular sampling (every 50 pieces) and use laser scanners for full - size verification. This real - time monitoring enables us to maintain tight tolerances and promptly address any potential issues.
Tolerance Level | Tolerance Range |
Standard | ±0.05mm (length ≤ 100mm) |
Precision | ±0.02mm (achieved through secondary processing and calibration) |
Material Selection: Durable and Versatile Options
Common Sheet Metal Materials
Material | Key Mechanical Properties | Advantages | Typical Applications |
Carbon Steel | Tensile strength 300 - 600MPa, elongation ≥20% | Low cost, easy to weld | Automotive chassis parts, construction steel structures |
Tensile strength 500 - 1000MPa, salt spray test ≥1000 hours | Corrosion - resistant, smooth surface | Medical equipment, food processing machinery | |
Aluminum Alloy | Density 2.7g/cm³, thermal conductivity ≥180W/m·K, tensile strength 150 - 350MPa | Lightweight, easy to form | Electronic heat sinks, aerospace structural parts |
Electrical conductivity ≥90% IACS, elongation ≥30% | Excellent electrical conductivity, easy to electroplate | Electrical connectors, decorative components |
Material Certification
Surface Treatments: Enhancing Function and Appearance
5.1 Comprehensive Finishing Solutions
Treatment | Process Description | Performance Highlights | Common Applications |
Powder Coating | After electrostatically adsorbing the powder, it is cured at high - temperature, with a coating thickness of 60 - 100μm. | Impact resistance ≥ 50kg·cm, weather resistance ≥ 10 years | Outdoor equipment, home appliance housings |
Electroplating | Surface hardness HV ≥ 200, glossiness ≥ 90% | Automotive decorative parts, electronic components | |
Anodizing | Forms an oxide film on the aluminum surface, with a thickness of 5 - 25μm and a hardness of HV 300 +. | Insulation ≥ 10MΩ, resistant to UV aging | Electronic enclosures, aerospace aluminum components |
Electrophoretic Coating | Water - soluble paint is electrophoretically deposited, with a film thickness of 15 - 25μm. | Salt spray resistance ≥ 1200 hours, adhesion grade 0 | Automotive chassis parts, metal furniture |
Applications Across Industries
Sheet metal fabrication is a cornerstone technology that finds diverse applications across multiple industries. Our expertise in this field allows us to provide tailored solutions that meet the unique demands of each sector.
Industry-Specific Solutions
- Automotive: In the automotive industry, the demand for high performance and lightweight is of vital importance. The aluminum alloy body structural components we provide adopt advanced extrusion e stamping processes. Compared with traditional steel, they can achieve a weight reduction of over 20%, effectively improving fuel efficiency and handling performance. The stainless steel battery trays we manufacture feature outstanding fire resistance and corrosion resistance, and have passed the IP67 water and dust resistance test, providing reliable guarantees for the safe operation of new energy vehicles.
- Electronics & Telecom: In the field of electronics and communications, our carbon steel server racks, meticulously designed and manufactured, have a load-bearing capacity of ≥500kg and are equipped with EMI shielding design to ensure the stable operation of electronic equipment. Our aluminum alloy 5G device casing adopts a precise heat dissipation fin design, which improves the heat dissipation efficiency by 15% compared to traditional materials, meeting the heat dissipation requirements for high-power operation of 5G devices.
- Aerospaziale: The aerospace field has extremely high requirements for the performance and precision of materials. The titanium alloy wing ribs we produce have a tensile strength of ≥900MPa and strictly comply with the AS9100D aerospace quality management system standard, providing crucial support for the safe flight of aircraft. The satellite antenna brackets we manufacture adopt a high-precision bending process with an Angle deviation of no more than 0.5°, ensuring the accurate reception and transmission of satellite signals.
- Construction & Industrial: In the fields of architecture and industry, our stainless steel curtain wall frames have passed the weather resistance certification and can be used for a long time in harsh environments such as high-salt coastal areas, maintaining their appearance and structural stability. Our carbon steel powder-coated mechanical protective covers have an impact resistance grade of IK10, effectively protecting mechanical equipment and extending its service life.
Why Choose Yigu Technology for Sheet Metal Fabrication?
Technical Excellence
- Advanced equipment cluster: Our state - of - the - art manufacturing facility is equipped with over 10 high - precision laser cutters with an accuracy of ±0.02mm, ensuring intricate and precise cuts. Complemented by more than 20 CNC bending machines with a maximum pressure of 400 tons, we can handle complex bending tasks with ease. Our fully automated spraying line, with a daily processing capacity of 5000㎡, provides consistent and high - quality surface finishes.
- Senior team: Our team of over 50 professional engineers, with more than 30 years of collective industry experience, including technicians with over 10 years of expertise, is committed to providing Design for Manufacturability (DFM) optimization suggestions. These suggestions not only enhance the quality of the final product but also help reduce production costs by 10% - 15%.
Quality & Compliance
- Certification system: We are ISO 9001:2015 certified, demonstrating our commitment to quality management systems. Additionally, our compliance with IATF 16949 for the automotive industry and RoHS/REACH regulations for environmental protection ensures that our products are suitable for a wide range of applications.
- Detection capability: Our in - house quality control laboratory is equipped with a Coordinate Measuring Machine (CMM) with a detection range of 1000×1500×600mm, enabling us to conduct precise dimensional inspections. We also have a salt - spray test chamber that supports the ASTM B117 standard, with a maximum test duration of 1000 hours, to evaluate the corrosion resistance of our products.
Customer-Centric Services
Service Aspect | Service Details | Benefits to Customers |
The sample delivery cycle is 7 to 15 days, and we support small-batch trial production (MOQ 10 pieces). | We offer a quick sample delivery cycle of 7 - 15 days and support low - volume trial production with a minimum order quantity (MOQ) of 10 pieces. | This allows you to quickly test the waters and validate your product concepts, reducing the cost of trial - and - error. |
The monthly production capacity of sheet materials is 500 tons, and the delivery time for bulk orders is 4 to 6 weeks | With a monthly production capacity of 500 tons of sheet metal, we can handle large - scale orders. Our delivery time for bulk orders is 4 - 6 weeks, and we can also achieve a price reduction of over 20% for high - volume purchases. | We ensure that you can meet market demands on time while enjoying cost - effective solutions for large - scale procurement. |
Covering the entire process from design, processing, surface treatment to assembly | Our one - stop service covers every aspect of the manufacturing process, from design and processing to surface treatment and assembly. | This simplifies your supply chain management and shortens the overall project cycle, saving you time and resources. |
Sheet Metal Fabrication FAQs
We accept MOQs as low as 10 pieces for prototyping and scale to 100,000+ pieces for mass production.
Yes, using precision laser cutting and forming techniques, ensuring minimal material deformation.
Our engineers use 3D modeling and simulation software to optimize bend sequences, ensuring 98% first - pass 合格率 for complex parts.
All materials come with mill certificates and comply with international standards (ASTM, EN, JIS), available upon request.
We use laser alignment systems during bending and 3D scanning for final inspection, achieving ±0.1mm accuracy for parts up to 3000mm.
Powder coating and electrophoretic coating are ideal, offering superior weather and corrosion resistance (salt spray test ≥1000 hours).
Yes, we offer full assembly, including welding, fastener installation, and functional testing, delivering ready - to - use components.
Our DFM team provides free design feedback to optimize material usage, bend angles, and finishing choices, typically saving 10 - 20% on production costs.
Lead times range from 4 - 6 weeks for standard orders, with expedited options (2 - 3 weeks) available for urgent projects.
Yes, we handle global logistics, including export packaging (fumigated wooden crates), customs documentation, and DDP/DAP Incoterms.
Contact Yigu Technology today to discuss how our sheet metal fabrication expertise can transform your designs into high - precision, cost - effective solutions—from concept to completion, we deliver excellence at every step.