1. The Challenge of High-Cost Steel Molds
In the world of product development, especially when it comes to injection molding production for new products, traditional steel molds have long been the standard choice. However, they come with a set of challenges that can be formidable, particularly for those looking to bring new products to market efficiently and cost-effectively.
High Upfront Costs
One of the most significant barriers presented by steel molds is their high upfront cost. For complex designs, the price tag for steel molds often soars beyond $10,000. This substantial investment is a major deterrent, especially for small and medium-sized enterprises and startups with limited budgets. These businesses may have brilliant product ideas but find themselves stymied by the need to allocate a large portion of their capital just to create the molds for production. For instance, a startup in the consumer electronics sector that wants to launch a new, innovative gadget would need to fork out a large sum just for the steel molds, leaving them with less capital for other crucial aspects such as marketing, research, and development.
Long Lead Times
The process of getting a steel mold ready for production is time-consuming. From the initial design phase to fabrication and finally, testing, it typically takes 4 - 8 weeks. This extended lead time can be a critical drawback in today's fast-paced market. Consider a toy company that wants to capitalize on a new, popular trend. By the time their steel molds are ready for production, the trend may have already passed, and they could miss out on significant sales opportunities. The long wait also means that companies have to plan far in advance, which can be difficult when dealing with rapidly changing consumer demands and technological advancements.
Low Flexibility
Steel molds lack flexibility when it comes to making changes. If, during the production process, a company realizes that some modifications are needed to the product design, making changes to the steel mold can be a costly and time-consuming affair. Each modification often requires retooling, which involves additional expenses and further delays. For example, an automotive parts manufacturer may find that a particular component needs a slight design adjustment after initial testing. With a steel mold, this simple change could mean sending the mold back to the manufacturer, incurring high costs for rework, and waiting for an extended period before production can resume. This lack of flexibility can be a major hurdle for companies that need to adapt quickly to market feedback or technological improvements.
In summary, the high costs, long lead times, and low flexibility of traditional steel molds pose significant challenges, especially for SMEs and startups. These barriers can limit innovation and growth, making it essential to explore alternative solutions.
2. Introducing Yigu’s 3D Printed High-Temperature Resin Tooling
Yigu Technology offers a revolutionary solution: 3D printed high-temperature resin rapid tooling for rapid prototyping and small batch production. This innovative approach addresses the challenges posed by traditional steel molds, providing a cost-effective and time-efficient alternative.
2.1 How It Works
- Design Validation: The process begins with the creation of digital prototypes using CAD models. This step allows for thorough design validation, ensuring that the product meets all the required specifications before moving on to the physical production stage. Designers can make adjustments and improvements to the digital model easily, saving both time and resources.
- Stampa 3D: Yigu uses state-of-the-art 3D printing technology to print molds using high-temperature resin. For example, materials like Somos® WaterShed XC 11122 are employed, which can withstand temperatures of up to 200°C. This high - temperature resistance makes the resin molds suitable for a wide range of injection molding processes. The 3D printing process is highly precise, capable of replicating even the most intricate details of the digital design.
- Stampaggio ad iniezione: Once the resin molds are printed, they are ready for injection molding. Each mold can produce 10 - 500 parts, making it an ideal solution for small batch production. This small - batch production approach is perfect for market testing. Companies can produce a limited number of products to gauge market response, gather feedback, and make necessary improvements before committing to large - scale production.
2.2 Key Advantages
Caratteristica | Traditional Steel Molds | Yigu’s Resin Molds |
Cost | \(10k–\)50k | \(500–\)3k |
Lead Time | 4–8 weeks | 3–7 days |
Material Compatibility | Limited to thermoplastics | Supports ABS, PP, PC, and elastomers |
Design Flexibility | Costly retooling | Easy digital adjustments |
3. Why Choose Yigu’s Resin Tooling?
3.1 Risk Reduction
- Market Testing: One of the significant benefits of Yigu's resin rapid tooling is its ability to facilitate market testing. By producing small batches of products, companies can introduce their offerings to the market on a limited scale. This allows them to gauge the market's response, understand customer preferences, and determine the actual demand for the product before making a large - scale investment in production. For example, a new food packaging company can use Yigu's resin - molded products to test the market. They can distribute a few hundred samples to local grocery stores and collect feedback on factors like product usability, design appeal, and functionality. Based on this feedback, they can decide whether to proceed with large - scale production or make adjustments to the product design.
- Design Iteration: With Yigu's resin rapid tooling, design iteration becomes a seamless process. Since the cost and lead time for creating resin rapid molds are relatively low, companies can make changes to the product design based on real - world feedback. They don't have to be burdened by the high costs and long wait times associated with retooling steel molds. A consumer electronics startup that has received feedback that their product's button placement is inconvenient can quickly modify the digital design, 3D print a new resin mold, and produce updated samples for further testing, all within a short period. This iterative approach ensures that the final product meets the highest standards of quality and functionality.
3.2 Performance Meets Affordability
- High - Temperature Resistance: Yigu's high - temperature resin can withstand repeated cycles of molten plastic injection. The resins used, such as those with a heat deflection temperature (HDT) of up to 200°C, ensure that the molds maintain their structural integrity even under extreme heat. This makes them suitable for a wide range of injection molding processes, including those involving high - temperature plastics like polycarbonate (PC). In automotive part production, where components need to endure high - temperature operating conditions, Yigu's high - temperature - resistant resin molds can be used to produce parts such as engine covers and interior components with high - temperature resistance requirements.
- Precision Tolerance: Yigu's 3D printing process offers a precision tolerance of ±0.1mm. This high level of accuracy is crucial for creating functional prototypes. Whether it's a complex mechanical part with interlocking components or a small electronic enclosure, the precise dimensions achieved with Yigu's resin tooling ensure that the parts fit together perfectly. For instance, in the production of a small - scale gear system for a new - generation smartwatch, the tight tolerance of the resin - molded gears guarantees smooth operation and optimal performance.
- Finitura superficiale: The resin - printed molds can achieve a surface finish of Ra 1.6–3.2μm, resulting in smooth part surfaces. This is especially important for products where aesthetics play a significant role, such as consumer goods, electronics, and medical devices. A cosmetic packaging company can use Yigu's resin - molded containers, which have a smooth surface finish, to enhance the visual appeal of their products on the shelves. The smooth surface also reduces the need for extensive post - processing, saving both time and cost.
3.3 Sustainability
- Reduced Waste: 3D printing is inherently a more sustainable manufacturing process compared to traditional subtractive manufacturing methods like CNC machining. Yigu's 3D - printed resin tooling minimizes material usage by up to 90% compared to CNC machining. In CNC machining, large amounts of material are removed from a solid block to create the desired shape, resulting in significant waste. In contrast, 3D printing builds the mold layer by layer, using only the necessary amount of resin. This not only reduces material waste but also decreases the environmental impact associated with the extraction and disposal of excess materials.
- Energy Efficiency: Yigu uses low - power desktop printers for 3D printing the resin molds. These printers consume less energy compared to the large - scale manufacturing equipment used in traditional mold - making processes. The reduced energy consumption contributes to a lower carbon footprint, making Yigu's resin tooling a more environmentally friendly choice. As the world increasingly focuses on sustainable manufacturing practices, choosing Yigu's energy - efficient 3D - printed resin tooling can help companies meet their environmental goals while still achieving high - quality production results.
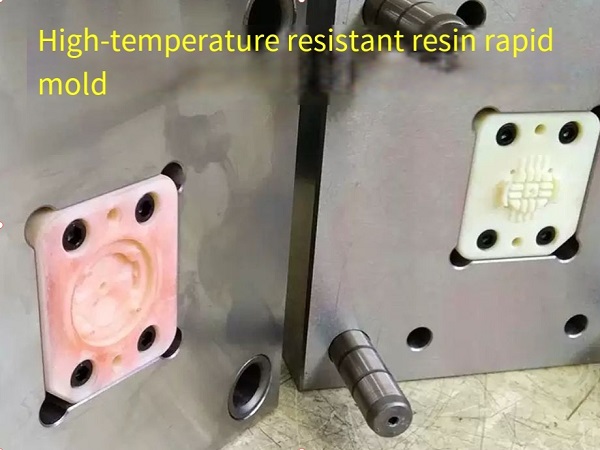
4. Applications Across Industries
Yigu's 3D printed high - temperature resin tooling has found widespread applications across various industries, providing unique solutions to meet the specific needs of each sector.
4.1 Automotive
- Custom Brackets: In the automotive industry, especially with the rise of electric vehicles (EVs), custom brackets are crucial for battery enclosures. Before mass production, companies can use Yigu's resin tooling to test the fitment of these brackets in EV battery enclosures. For example, a new EV startup may need to design a custom - shaped bracket to hold the battery modules securely. With Yigu's 3D printed resin molds, they can quickly produce small batches of these brackets for fitment testing. This allows them to identify any potential issues, such as interference with other components or improper alignment, and make necessary design adjustments before investing in large - scale production.
- Interior Components: The design of automotive interior components requires a high level of ergonomic consideration. Yigu's resin tooling enables automotive manufacturers to validate their ergonomic designs with short lead times. A car manufacturer planning to introduce a new line of luxury cars may want to create a unique, ergonomically - designed center console. Using Yigu's 3D printed resin molds, they can produce samples of the center console in a matter of days. These samples can then be used for user testing, allowing the manufacturer to gather feedback on factors like ease of use, comfort, and accessibility. Based on this feedback, the design can be refined, ensuring that the final product provides a comfortable and user - friendly experience for the end - users.
4.2 Consumer Goods
- Packaging Prototypes: In the consumer goods industry, packaging plays a vital role in product marketing. Yigu's resin tooling allows companies to create retail - ready mockups of packaging prototypes for branding evaluation. A cosmetic company launching a new line of skincare products can use Yigu's 3D printed resin molds to produce sample packaging. These mockups can be used to test different branding elements, such as logo placement, color schemes, and label designs. By getting early feedback on the packaging design, the company can make informed decisions and ensure that the final packaging is visually appealing and aligns with the brand image, ultimately attracting more consumers.
- Small Gadgets: For small gadget manufacturers, producing limited editions can be an effective way to gauge market interest. Yigu's resin tooling makes this process more accessible. A startup that has developed a new, innovative wireless earbud may want to test the market before full - scale production. Using Yigu's 3D printed resin molds, they can produce a limited run of the earbuds. These limited - edition products can be sold through select channels or offered to early adopters. By analyzing the sales data and customer feedback, the company can determine the market demand for their product, identify any areas for improvement, and make strategic decisions regarding further production and marketing efforts.
4.3 Healthcare
- Surgical Guides: In the healthcare industry, precision is of utmost importance, especially in surgical procedures. Yigu's 3D printed high - temperature resin tooling can be used to print patient - specific surgical guides, particularly for orthopedic procedures. For instance, in a total knee replacement surgery, a patient - specific surgical guide can help the surgeon accurately position the implant. Using Yigu's resin molds, medical device companies can produce these guides with high precision. The digital model of the patient's knee, obtained through medical imaging such as CT scans, can be used to design the surgical guide. The 3D printed resin guide then provides a precise template for the surgeon during the operation, reducing the risk of errors and improving the overall success rate of the surgery.
- Medical Device Housings: When it comes to medical device housings, ensuring biocompatibility and functionality is crucial. Yigu's resin tooling can be used to produce medical device housings that meet these requirements. A company developing a new portable insulin pump needs a housing that is not only biocompatible (safe for contact with the patient's skin) but also provides protection for the internal components and allows for easy operation. Yigu's high - temperature resin, which can be sterilized, is suitable for this application. The 3D printed resin housing can be designed to fit the specific components of the insulin pump precisely, and its biocompatible properties ensure the safety of the patient during long - term use.
5. Case Study: Yigu Resin Molds in Action
To illustrate the effectiveness of Yigu's 3D printed high - temperature resin tooling, let's take a look at the real - world experience of a European electronics startup.
The Challenge
This startup had developed a new, innovative portable charger that they believed had great potential in the market. However, like many startups, they were operating on a tight budget. The cost of traditional steel molds, which was estimated to be around $10,000, was simply too high for them to afford. Additionally, they were uncertain about the market reception of their product. They were worried that investing in expensive steel molds for large - scale production without proper market validation could lead to significant losses if the product did not meet customer expectations.
Yigu's Solution
The startup turned to Yigu Technology. Yigu's team of experts worked closely with the startup to understand their product requirements. Using advanced 3D printing technology, Yigu was able to print the resin molds in just 5 days. The total cost for the resin molds was a mere $1,200, a fraction of the cost of traditional steel molds.
Results
- Crowdfunding Success: With the resin - molded portable chargers, the startup was able to produce 100 units for their crowdfunding campaign. These samples were used to showcase the product's features and functionality to potential backers. The crowdfunding campaign was a huge success, generating significant interest and pre - orders for the product.
- Design Optimization: During the crowdfunding process, the startup received valuable feedback from backers. Based on this feedback, they realized that some design adjustments were necessary. Thanks to the low cost and fast turnaround of Yigu's resin molds, they were able to make these adjustments quickly. By making these design changes, they not only improved the product but also saved approximately $8,000 in tooling costs that would have been incurred if they had been using steel molds and needed to retool.
- Enhanced Product Performance: One of the key areas of feedback was related to the thermal management of the portable charger. The startup made improvements to the design, and after producing new samples with the adjusted resin molds, they found that the thermal management of the product had improved by 30%. This improvement was well - received by customers and helped to increase the product's competitiveness in the market.
This case study clearly demonstrates how Yigu's 3D printed high - temperature resin tooling can provide a practical, cost - effective, and flexible solution for companies looking to bring new products to market. It allows them to test the waters, make necessary adjustments, and ultimately reduce the risks associated with new product development.
6. FAQs for Small Batch Injection Molding
Q1: How many injection cycles can Yigu's resin molds support?
A1: Yigu’s high - temperature resins support 50 - 500 cycles, making them ideal for small - batch production. This range provides sufficient capacity for most small - scale production runs, allowing companies to produce a reasonable quantity of products for market testing, initial product launches, or limited - edition runs without the need for frequent mold replacements.
Q2: Can Yigu's resin molds work with different plastic materials?
A2: Yes! Our molds are highly versatile and work well with a variety of materials, including ABS, PP, PC, and flexible elastomers. This wide range of material compatibility ensures that companies can choose the most suitable plastic material for their product based on its specific requirements, such as strength, flexibility, heat resistance, or cost - effectiveness.
Q3: How can I get a quote for Yigu's small batch injection molding service?
A3: It's simple! Just share your CAD file with us, and our team of experts will review it. We are committed to providing a free, detailed quote within 24 hours. This quick turnaround time allows you to plan your project budget and production schedule more efficiently, without having to wait for extended periods to get cost estimates.