Acrylic (AA) Plastic Parts Materials
Did you know that acrylic first came out in 1928 and is still super popular today? That just goes to show how important it is in making plastic parts. Nowadays, people use acrylic a lot for many reasons:
- It doesn't get damaged by different chemicals.
- It's tougher than regular glass when something hits it.
- It can handle big changes in temperature.
- It's really clear and transparent.
- It's light and easy to carry.
Because it's so clear, light, and can deal with temperature changes, acrylic is used in lots of things. These things include:
- Windows
- Lighting stuff
- Replacing glass
- Fridges
- Food storage containers
One cool thing about acrylic is that it's great for making and storing food because it doesn't have BPA. BPA is a controversial chemical that some people say can cause health problems, even though others disagree.
Acrylic (AA) Plastic Parts Making Service
Be good at product structure optimization and greatly reduce the cost of Plastic Parts Materials
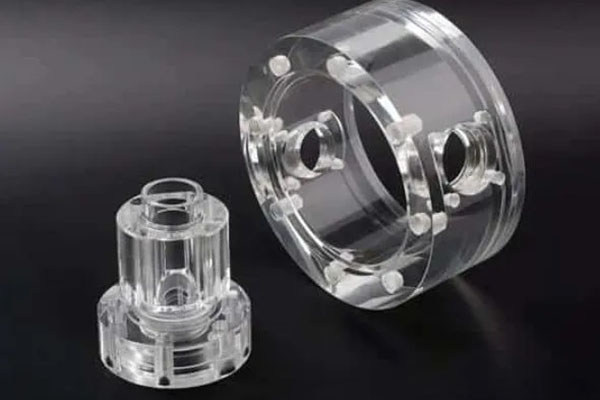
Part Design
Appearance and structural design
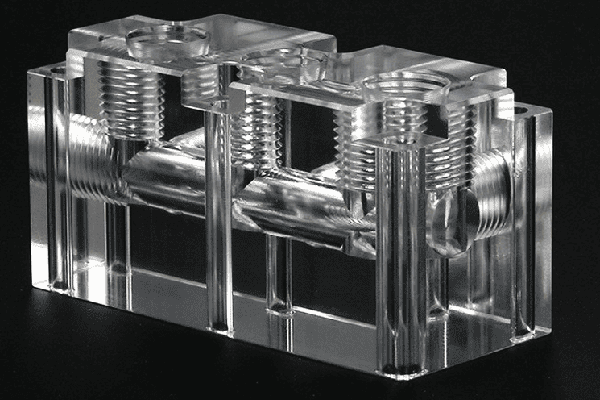
Mold Making
Design, DFM confirmation
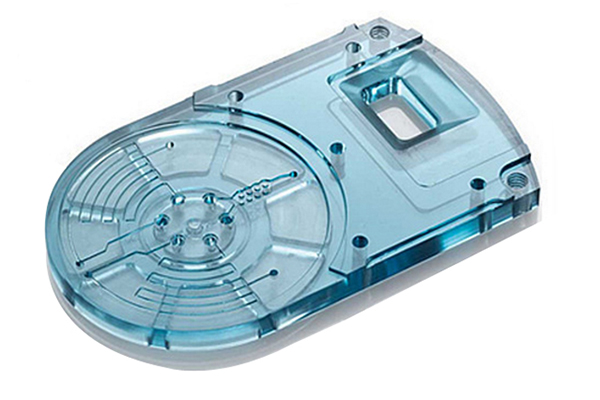
Product Production
Imported, high-speed equipment
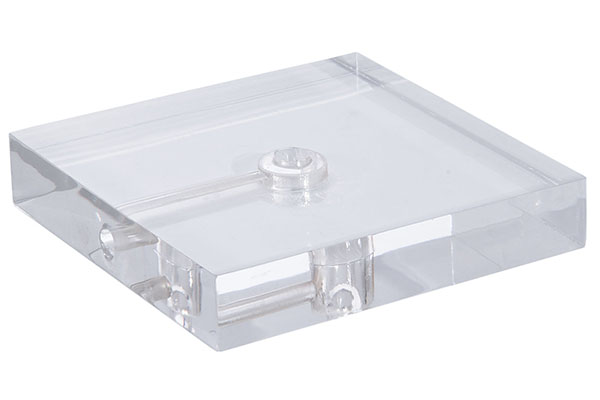
Product Assembly
Incoming materials, inspection and assembly
Understanding the Benefits and Applications of Acrylic AA Plastic Parts Materials: Properties and Advantages
Acrylic (AA) is a popular choice for making plastic parts because it has some great features. It's a clear, strong material that doesn't easily get damaged by sunlight or bad weather. We will dive into what makes acrylic AA so special, why it's a good pick, and where you can find it used.
What Makes Acrylic AA Great? Here are some cool things about acrylic AA:
- Clear as Glass: It's super clear, which is perfect when you need see-through stuff.
- Sun Protection: It can take a lot of sun without getting ruined, great for outside use.
- Weatherproof: It stands up well against rain, wind, and other tough conditions.
- Scratch Resistant: It's tough on the surface, so it doesn't easily get scratched up.
Why Choose Acrylic AA? There are several reasons to go with acrylic AA for your plastic parts:
- See-Through Quality: Just like glass, but lighter and stronger.
- UV Safe: Keeps its looks even after lots of sun exposure.
- Durable Outdoors: Stays in shape even when Mother Nature throws her worst at it.
- Chemical Proof: Doesn't easily get damaged by acids, bases, or solvents.
Where You'll See Acrylic AA You can find acrylic AA in many places thanks to its versatility:
- Cars: Headlights, tail lights, and dashboard screens often use acrylic.
- Lighting: Lamps, light covers, and lenses benefit from its clear nature.
- Everyday Items: From makeup containers to furniture, it's everywhere.
- Gadgets: Screens and protective covers in electronics are commonly made from acrylic.
In short, acrylic AA is a fantastic option for creating durable, clear plastic parts that last. If you're thinking about using it for your project, make sure to talk to a trusted supplier to get the best results.
FAQ About Acrylic (AA) Plastic Parts
What is acrylic plastic used for?
Acrylic plastic, often referred to as AA plastic, is a versatile material that's widely used in various applications. You’ll find it in windows and skylights due to its excellent light transmission properties. It's also popular in the automotive industry for headlight lenses and tail lights because of its durability and impact resistance. In addition, acrylic plastic is commonly used in medical devices, such as surgical tools and equipment, due to its biocompatibility and ease of sterilization. Its clear nature makes it ideal for display cases, signage, and even in some consumer electronics.
How durable are acrylic parts compared to other plastics?
Acrylic plastic parts are quite durable. They have good impact resistance, which means they can withstand knocks and bumps without breaking easily. This makes them suitable for use in environments where they might be subjected to physical stress. However, while they are tough, they aren't as strong as some other plastics like polycarbonate. So, while they can handle everyday wear and tear, they may not be the best choice for applications requiring the highest strength and durability.
Are acrylic plastic parts weather-resistant?
Yes, acrylic plastic parts are generally weather-resistant. They have good UV resistance, which means they won’t yellow or degrade quickly under sunlight. They also perform well in varying temperatures, making them suitable for both indoor and outdoor use. However, prolonged exposure to harsh environmental conditions, like extreme heat or cold, can affect their performance over time. For example, in very cold climates, acrylic can become more brittle. So, while they are weather-resistant, it’s important to consider the specific conditions they will be exposed to.
Can acrylic plastic parts be recycled?
Yes, acrylic plastic parts can be recycled, but the process is a bit more complex compared to other plastics. There are specialized recycling programs that accept acrylic waste, and these programs can reclaim the material and turn it into new products. However, not all municipal recycling programs accept acrylic, so you may need to find a specialized facility. Recycling acrylic helps reduce waste and conserve resources, so it’s a great practice if you can manage it.
How do I clean acrylic plastic parts?
Cleaning acrylic plastic parts is pretty straightforward. Use a soft cloth and mild soap with water to gently wipe down the surface. Avoid using abrasive cleaners or materials as they can scratch the plastic. For tougher stains, a mixture of water and isopropyl alcohol works well. Always dry the part thoroughly after cleaning to prevent water spots or streaks. If you take care of it, your acrylic parts will stay clear and shiny for a long time.
Are acrylic plastic parts safe for food contact?
Yes, acrylic plastic parts are generally considered safe for food contact. They are non-toxic and do not leach harmful chemicals into food. This makes them suitable for use in kitchenware, food storage containers, and even some types of cutlery. However, it's always a good idea to check the specific product’s certifications to ensure it meets food safety standards.
Can acrylic plastic parts be repaired if they get damaged?
Yes, acrylic plastic parts can often be repaired if they get damaged. Small scratches can be polished out using fine sandpaper or a specialized plastic polish. For cracks or breaks, you can use an acrylic adhesive or solvent cement to mend the parts. These products are designed specifically for bonding acrylic and can create a strong, nearly invisible repair. Just make sure the surfaces are clean and dry before applying any adhesive.
Do acrylic plastic parts have UV protection?
Acrylic plastic parts do have some level of UV protection, but it varies depending on the specific type and formulation of the acrylic. While they resist yellowing and degradation better than many other plastics, prolonged exposure to direct sunlight can still cause some changes over time. For applications that require high UV resistance, look for acrylic products that are specifically labeled as UV-resistant. These will offer better protection against the harmful effects of sunlight.
Are there any special considerations when cutting acrylic plastic?
When cutting acrylic plastic, it’s important to use the right tools and techniques to avoid cracking or melting the material. A fine-toothed saw or a table saw with a fine blade works well for straight cuts. For curved shapes, a jigsaw with a fine blade is effective. Always clamp the acrylic securely to prevent it from moving while you cut. Additionally, using a sharp blade and making slow, steady cuts will help achieve clean edges. After cutting, smooth any rough edges with sandpaper or a deburring tool.
How does the cost of acrylic plastic compare to other plastics?
Acrylic plastic tends to be more expensive than some other types of plastics, such as polyethylene or polypropylene. This higher cost is due to its superior optical clarity, impact resistance, and overall quality. However, the extra expense is often justified by its performance and aesthetic qualities. For applications where these features are crucial, like in high-end displays or architectural elements, the cost is usually worth it. But if budget is a major concern, there are other plastics that might be more economical choices.