Acrylonitrile Butadiene Styrene (ABS) Plastic Parts Materials
Let's chat about ABS, or Acrylonitrile Butadiene Styrene as it's officially known. It might sound a bit tricky to say, but luckily, everyone just calls it ABS for short. This material is pretty fascinating because it has lots of practical features. For instance:
- It's super rigid
- Great with electricity
- Has a hard surface
- Strong when pulled
- Keeps its shape well
- Doesn't wear down easily
- Can handle knocks and bumps
- Won't break down in chemicals
- Handles heat nicely
Because of all these awesome traits, ABS is used in loads of different things made through injection processes. Think about stuff like:
- Lego bricks
- Sports gear
- Compressors
- Garden tools
- Medical devices
- Parts of car dashboards
- Door trims and handles
- Seatbelt parts
- Car instrument panels
Honestly, we're just barely starting to cover all the cool stuff that can be made with ABS!
Acrylonitrile Butadiene Styrene (ABS) Plastic Parts Making Service
Be good at product structure optimization and greatly reduce the cost of Plastic Parts Materials
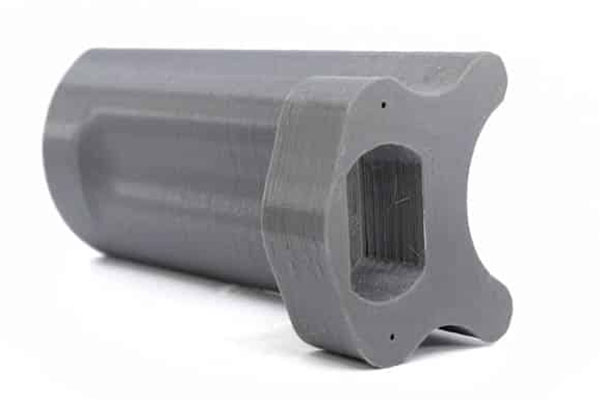
Plastic Design
Appearance and structural design
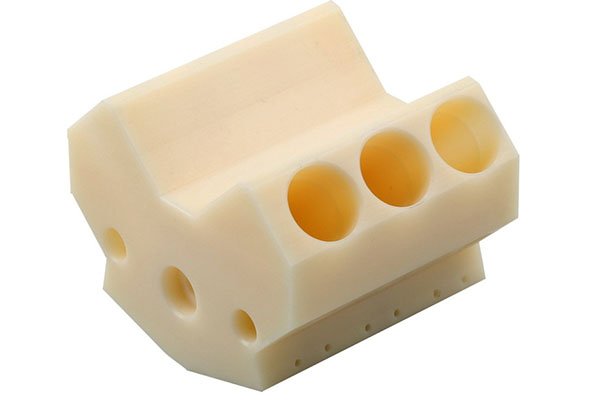
Mold Making
Design, DFM confirmation
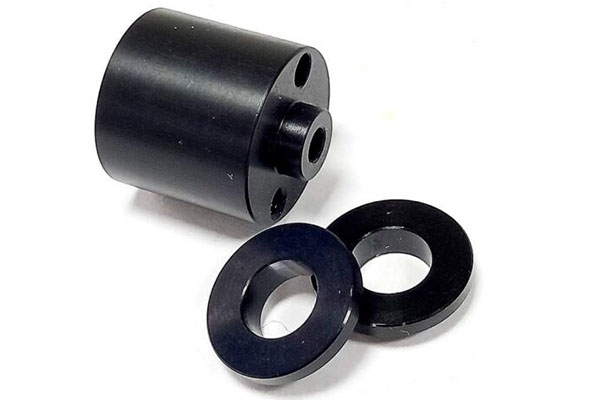
Product Production
Imported, high-speed equipment
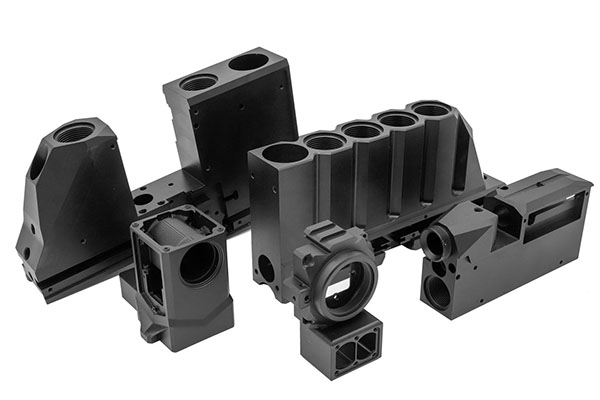
Product Assembly
Incoming materials, inspection and assembly
Understanding ABS Plastic Parts Materials: Properties, Applications, and Advantages
ABS, short for Acrylonitrile Butadiene Styrene, is a super common thermoplastic polymer that's used in loads of different things. It's famous for being tough and resistant to impact, and it doesn't cost an arm and a leg either, which makes it perfect for making plastic parts. In this article, let's dive into what makes ABS so special, where it's used, and why people love it for making plastic bits and bobs.
What Makes ABS Great?
ABS is like the superhero of plastics because it's made from three different types of molecules: acrylonitrile, butadiene, and styrene. The mix of these guys gives ABS its awesome properties:
- Tough and Impact-Resistant: ABS can handle a beating without cracking or breaking. It's like the bodyguard of the plastic world.
- Strong and Stiff: Need something that won't bend easily? ABS has got your back.
- Keeps Its Shape: Even when it gets hot or humid, ABS stays true to form.
- Chemical Resistance: It laughs in the face of acids, alkalis, and alcohols.
Where You’ll Find ABS
You see ABS everywhere, from cars to your kid's toys. Here are some of its most popular spots:
- Car Parts: Think dashboard panels and shiny trims.
- Electronics: Your computer keyboard and mouse housing might be made of ABS.
- Everyday Items: Toys, luggage, and kitchen gadgets often have ABS in them.
Why Choose ABS for Plastic Parts?
Here’s why ABS is a top pick for making plastic parts:
- Cheap and Cheerful: It won't break the bank.
- Easy to Work With: ABS is a favorite in the injection molding game because it's simple to shape.
- Smooth Finish: Want something that looks good? ABS gives a nice, smooth surface.
- Customizable: Whether you need a specific color, texture, or hardness, ABS can be tweaked to fit your needs.
So, if you're on the hunt for a material to make durable, affordable, and versatile plastic parts, ABS should be at the top of your list. Just make sure to chat with a trusted manufacturer to get the best results for your project.
FAQ About Acrylonitrile Butadiene Styrene ABS Plastic Parts
What are ABS plastic parts?
ABS plastic parts are items made from Acrylonitrile Butadiene Styrene, a popular thermoplastic known for its strength, durability, and impact resistance. These parts are often used in applications where toughness and lightweight materials are essential, such as in automotive components, electronic housings, and various types of consumer goods. The versatility of ABS makes it a go-to material in manufacturing due to its ability to be easily molded into different shapes and sizes.
Are ABS plastic parts recyclable?
Yes, ABS plastic parts are indeed recyclable. They can be processed through mechanical recycling methods, which involve grinding the plastic into flakes or pellets that can be reused in manufacturing new products. However, it's important to note that not all local recycling programs accept ABS, so you might need to find specialized facilities. Recycling ABS helps reduce environmental waste and conserves resources by reusing the material rather than creating new plastic from scratch.
How do I clean ABS plastic parts?
Cleaning ABS plastic parts is quite straightforward. For general cleaning, you can use warm water with a mild detergent and a soft cloth or sponge. Avoid using harsh chemicals or abrasive scrubbers as they can scratch or damage the surface of the plastic. If you encounter stubborn stains, a small amount of rubbing alcohol can help remove them without causing harm to the ABS material. Just make sure to rinse thoroughly and dry completely afterward.
Can ABS plastic parts be painted?
Absolutely, ABS plastic parts can be painted, but proper preparation is key to achieving a good finish. First, clean the part thoroughly to remove any dirt or grease. Next, use a fine-grit sandpaper to lightly sand the surface for better paint adhesion. After sanding, wipe off the dust and apply a primer specifically designed for plastic surfaces. Once the primer is dry, you can proceed with your chosen paint. Using spray paint is often the easiest method, but brush painting works too if done carefully.
What are the common uses of ABS plastic parts?
ABS plastic parts are incredibly versatile and find applications in numerous industries. In the automotive sector, they are used for interior trim, bumpers, and other non-structural components. The electronics industry utilizes ABS for making durable yet lightweight casings for devices like remote controls, computer cases, and even some types of medical equipment. Additionally, ABS is commonly found in toys, kitchen appliances, and sporting goods due to its excellent balance of strength and flexibility.
How do I know if a product is made of ABS plastic?
Identifying whether a product is made of ABS plastic can usually be done by checking for markings on the item itself. Many manufacturers stamp an identification code or symbol indicating the type of plastic used. For example, a number "7" inside a triangle often signifies ABS. Additionally, some products may have labels or stickers providing this information. If these aren't present, examining the material characteristics such as its smooth texture, relatively light weight, and ability to withstand impact can also give clues about the material being ABS.
Are there any health concerns associated with ABS plastic?
While ABS plastic is generally considered safe for use in everyday items, there are a few considerations to keep in mind. During its production process, certain chemicals called phthalates may be added as plasticizers to enhance flexibility. Some studies suggest that these substances could potentially leach out over time, especially when exposed to heat or UV light, posing possible health risks. However, many modern ABS products are now phthalate-free or contain very low levels that comply with safety regulations. Always check product specifications if you have specific health concerns.
Can ABS plastic parts be repaired if broken?
Yes, ABS plastic parts can often be repaired if broken, depending on the extent of damage. Small cracks or breaks can sometimes be fixed using ABS-compatible adhesive glues or epoxy resins designed specifically for plastic repairs. For more extensive damage, welding techniques such as ultrasonic welding or hot air welding might be employed by professionals. It's worth noting that while DIY repairs are possible, they may not always restore the original strength or appearance of the part.
How does ABS plastic compare to other types of plastics?
Compared to other plastics like polycarbonate (PC) or polypropylene (PP), ABS stands out due to its combination of toughness, impact resistance, and ease of fabrication. Unlike PC, which tends to be more brittle, ABS offers greater flexibility without sacrificing much strength. When compared to PP, which is lighter but less durable under stress, ABS provides a better balance between weight savings and longevity. Each type of plastic has its own unique set of properties making them suitable for different applications based on specific needs such as temperature resistance, cost-effectiveness, or aesthetic requirements.
Is ABS plastic food-safe?
Yes, ABS plastic can be considered food-safe when it meets certain standards set by regulatory bodies like the FDA (Food and Drug Administration) in the United States. These standards ensure that the plastic does not leach harmful chemicals into food when used under normal conditions. However, it's important to verify that any given ABS product intended for contact with food has been certified as compliant before use. Always look for appropriate labeling indicating food safety approval to avoid potential health hazards associated with non-compliant materials.