Carbon Fiber Plastic Parts Materials
Plastic parts made with carbon fiber are gaining popularity for their impressive strength and light weight. These parts resist corrosion, handle fatigue well, and don't expand much when they heat up. Plus, they're great at conducting heat. You can shape them using injection molding, which fits products that need both strong and flexible materials.
When making these parts, the process starts by preparing a super smooth mold surface. Then, resin is brushed on, followed by laying down carbon fiber sheets which harden into the desired shape. A special spray ensures the part slides out easily after molding. The mold itself might be made from different materials like fiberglass, aluminum, or even wood, depending on what works best for low-pressure shaping. But if you need really precise details, stainless steel molds are the top choice.
For injecting resin into these molds, they need special openings for letting the resin in and air out. This sealing is crucial, especially when using vacuum techniques, to make sure the final product is top-notch. The molds have to be exactly right in size, with perfect matches between the top and bottom parts, and a very smooth finish. They also come with guides to help line everything up perfectly, locks to keep it all together during molding, and mechanisms to easily remove the finished part.
Our carbon fiber plastic parts boast several advantages:
- They're incredibly strong, able to withstand heavy use.
- They stay stable at high temperatures without softening.
- Their dimensions remain consistent, ensuring a perfect fit every time.
- We use pure materials, so there's no harm to the environment.
In short, if you're looking for durable, precise, and eco-friendly plastic parts, carbon fiber injection molding is the way to go.
Carbon Fiber Plastic Parts Making Service
Be good at product structure optimization and greatly reduce the cost of Plastic Parts Materials
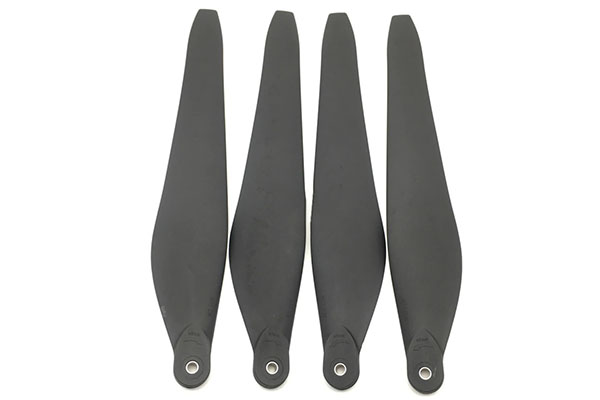
Plastic Design
Appearance and structural design
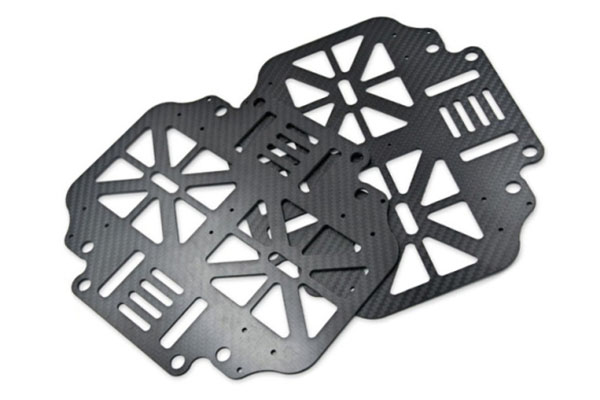
Mold Making
Design, DFM confirmation
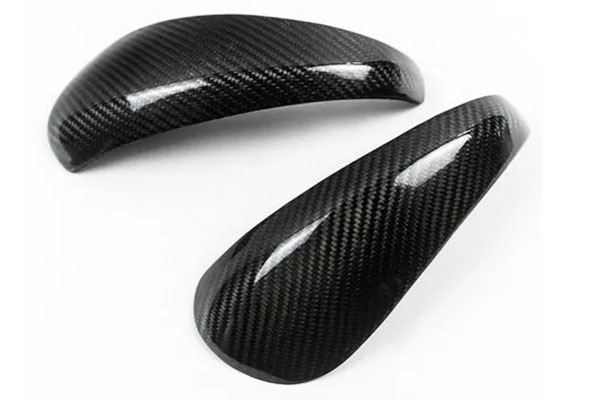
Product Production
Imported, high-speed equipment
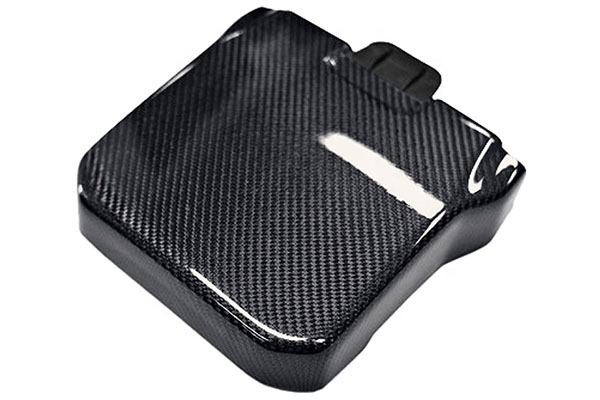
Product Assembly
Incoming materials, inspection and assembly
The Benefits and Challenges of Carbon Fiber Plastic Parts Materials: Properties, Applications, and Considerations
In recent years, carbon fiber materials for manufacturing plastic parts have gained popularity due to their unique properties and benefits. Carbon fiber is a lightweight and strong material that offers excellent mechanical properties. we will explore the properties, advantages, and challenges of carbon fiber materials used in plastic parts manufacturing.
Properties of Carbon Fiber Materials for Plastic Parts
Carbon fiber materials exhibit the following properties:
- High strength and stiffness: Carbon fiber is stronger and stiffer than most metals and other composite materials.
- Lightweight: Carbon fiber is a lightweight material that offers a high strength-to-weight ratio.
- Corrosion resistance: Carbon fiber is resistant to corrosion, making it suitable for applications that require exposure to harsh environments.
- Low thermal expansion: Carbon fiber has a low coefficient of thermal expansion, meaning it does not expand or contract significantly when exposed to temperature changes.
Advantages of Carbon Fiber Materials for Plastic Parts
Carbon fiber materials offer several advantages, including:
- High strength and stiffness: Carbon fiber provides excellent strength and stiffness, making it suitable for applications that require high performance.
- Lightweight: Carbon fiber is lightweight, making it ideal for applications that require weight reduction.
- Corrosion resistance: Carbon fiber's resistance to corrosion makes it suitable for applications that require exposure to harsh environments.
- Design flexibility: Carbon fiber allows for the production of complex and intricate shapes, making it suitable for applications that require customized parts.
Applications of Carbon Fiber Materials for Plastic Parts
Carbon fiber materials have a wide range of applications in various industries, including:
- Aerospace: Carbon fiber is commonly used in the aerospace industry for structural components, such as aircraft wings and fuselage.
- Automotive: Carbon fiber is used to make automotive parts, such as body panels, chassis, and suspension components.
- Sporting goods: Carbon fiber is used to make sporting goods, such as bicycles, golf clubs, and tennis rackets.
- Medical devices: Carbon fiber is used in medical devices, such as prosthetics and implants.
Challenges of Carbon Fiber Materials for Plastic Parts
While carbon fiber materials offer several advantages, they also have some challenges, including:
- Cost: Carbon fiber materials are more expensive than other traditional materials used in plastic part manufacturing.
- Processing challenges: Manufacturing with carbon fiber requires specialized equipment and processing techniques, making it more challenging than traditional methods.
- Brittleness: Carbon fiber can be brittle, meaning it may crack or break when subjected to high stress or impact.
Carbon fiber materials offer excellent mechanical properties and are suitable for various applications. They are commonly used in the aerospace, automotive, sporting goods, and medical industries. However, carbon fiber materials also present some challenges, including cost, processing difficulties, and potential brittleness. If you are considering using carbon fiber materials for your plastic parts application, consult with a reputable manufacturer to ensure that you get the right material and processing for your needs.
FAQ About Carbon Fiber Plastic Parts
What are carbon fiber plastic parts?
Carbon fiber plastic parts are components made from a composite material that combines carbon fibers with a plastic or polymer matrix. The carbon fibers add strength and rigidity, while the plastic provides a lightweight and moldable form. These parts are known for their high strength-to-weight ratio, making them popular in industries like aerospace, automotive, and sports equipment.
Why choose carbon fiber plastic parts over other materials?
Choosing carbon fiber plastic parts can be advantageous due to their superior strength, lightweight nature, and durability. They offer excellent resistance to fatigue and corrosion, which is crucial for long-term use. Moreover, they can be designed to meet specific engineering requirements, providing both functionality and efficiency.
How are carbon fiber plastic parts manufactured?
The manufacturing process typically involves laying out carbon fiber sheets in a predetermined pattern and then bonding them together using a resin matrix, usually through a process called curing. This can be done through methods such as compression molding, vacuum bagging, or autoclave curing. Each method ensures that the fibers are evenly distributed and the part maintains its structural integrity.
Are carbon fiber plastic parts expensive?
Yes, carbon fiber plastic parts tend to be more expensive than parts made from traditional materials like steel or aluminum. However, their enhanced performance characteristics often justify the higher cost, especially in applications where weight savings and strength are critical. Over time, advancements in manufacturing technology may help reduce costs.
Can carbon fiber plastic parts be recycled?
Recycling carbon fiber plastic parts can be challenging due to the complexity of separating the carbon fibers from the resin matrix. However, some specialized recycling processes do exist, and research is ongoing to improve these methods. Proper disposal and recycling can help mitigate environmental impact.
Do carbon fiber plastic parts require special maintenance?
While carbon fiber plastic parts are generally low-maintenance, it's important to keep them clean and free from abrasive materials that could damage the surface. Regular inspections for cracks or wear are advisable, especially in high-stress applications. In case of damage, professional repair services are available.
Are carbon fiber plastic parts suitable for all types of environments?
Carbon fiber plastic parts perform exceptionally well in a variety of environments, including high temperatures and harsh weather conditions. However, prolonged exposure to ultraviolet (UV) light can degrade certain types of plastic matrices, so protective coatings may be necessary for outdoor use.
How do carbon fiber plastic parts compare to metal parts in terms of performance?
Carbon fiber plastic parts often outperform metal parts in terms of weight and strength. They can handle higher stress levels without adding significant weight, which is particularly beneficial in industries like aerospace and motorsports. Additionally, they have better fatigue resistance and are less likely to corrode.
What are common applications for carbon fiber plastic parts?
These parts are commonly used in aerospace components, automotive parts, sporting goods (like bicycles and golf clubs), and even in medical devices. Their ability to provide high strength and low weight makes them ideal for applications requiring performance and efficiency.
Can custom carbon fiber plastic parts be made?
Yes, custom carbon fiber plastic parts can be fabricated to meet specific design and performance criteria. This involves detailed engineering and precise manufacturing processes to ensure that the part fits perfectly and functions as intended. Customization allows for optimization in various industrial and consumer applications.