Peek Plastic Parts Materials
Polyether ether ketone, or PEEK, injection molding is a pretty amazing way to make high-quality plastic parts. This method lets us create parts that are super strong and durable.
PEEK is a special type of plastic known for its incredible strength, stiffness, and ability to withstand heat, chemicals, and wear and tear. It's like the ultimate all-rounder in the world of materials.
Here’s how it works: First, we melt down the raw PEEK material in a heated barrel. Once it's melted, we inject it under high pressure into a carefully designed mold. The molten PEEK fills the mold and then cools down, taking on the exact shape we want. It's like magic, but backed by science!
This process is incredibly precise, allowing us to make complex shapes with very tight tolerances. It’s like having a Swiss watchmaker’s precision for every part we produce. That’s why it’s perfect for industries like aerospace, automotive, medical, and oil and gas. These sectors need really complex parts, and PEEK injection molding delivers.
And there’s more! PEEK injection molding is also used to make components for high-performance applications such as pumps, valves, and electrical connectors. These parts are the unsung heroes of our daily lives, working tirelessly behind the scenes to keep everything running smoothly.
So, the next time you use a product that relies on these high-performance plastic parts, remember the incredible process that made it possible. PEEK injection molding isn’t just a manufacturing technique; it’s a testament to human ingenuity and innovation.
Peek Plastic Parts Making Service
Be good at product structure optimization and greatly reduce the cost of Plastic Parts Materials
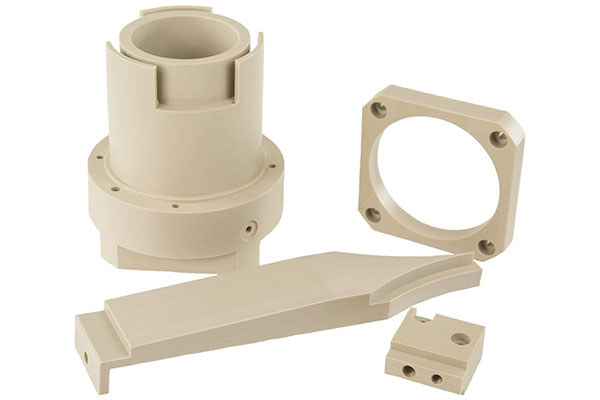
Part Design
Appearance and structural design
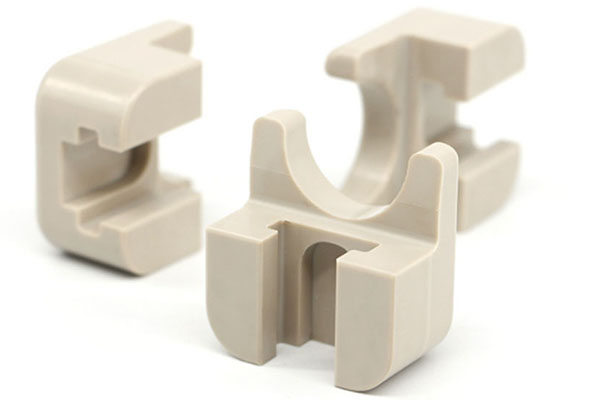
Mold Making
Design, DFM confirmation
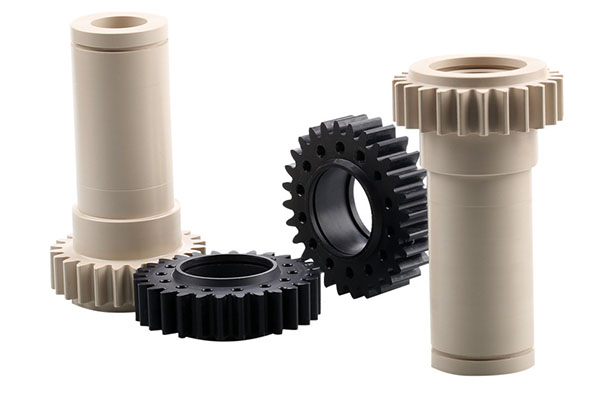
Product Production
Imported, high-speed equipment
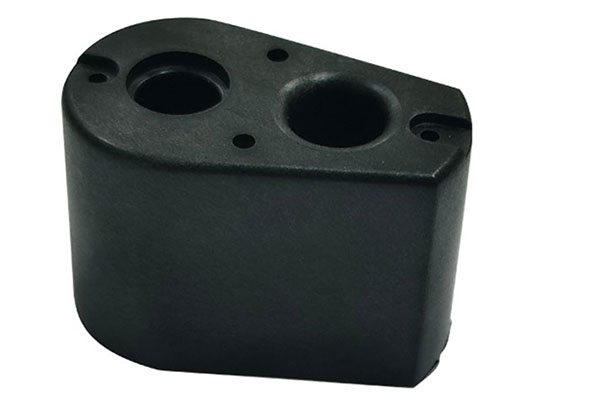
Product Assembly
Incoming materials, inspection and assembly
Exploring the Benefits and Applications of PEEK Plastic Parts Materials
Polyether ether ketone, or PEEK for short, is a superstar in the world of plastic parts. It's tough, stands up to heat, and doesn't mess around with chemicals, making it perfect for all kinds of heavy-duty jobs. Whether you're in the business of building machines that can take a beating or crafting medical gear that needs to be sterilized but still strong, PEEK has got your back.
Let's break down why PEEK is so awesome:
Toughness: This material can handle serious stress without breaking a sweat. It's like the superhero of plastics when it comes to taking on weight and wear.
Heat Resistance: Up to 260°C (500°F), no problemo! PEEK stays cool under pressure, making it great for things that get hot, like engines or cooking appliances.
Chemical Resistance: Strong acids? Harsh bases? No biggie. PEEK laughs in the face of corrosive stuff, which means it lasts longer in rough conditions.
Lightweight & Smooth: Light as a feather but strong as an ox, PEEK also glides smoothly, reducing friction and wear. This means parts move better and last longer.
Easy to Work With: You can shape PEEK into almost anything using injection molding or other methods. It's like Play-Doh for engineers, but way stronger.
Where does PEEK shine? Well, just about everywhere:
- Sky High: In aerospace, PEEK makes parts that keep planes and rockets flying safely.
- Health Hero: Medical devices benefit from PEEK's strength and biocompatibility.
- Oil Country: Down in the oil fields, PEEK components withstand extreme conditions.
- Road Warriors: Automotive applications love PEEK for its strength and resistance to car chemicals.
In short, PEEK injection molding materials are like the Swiss Army knife of the manufacturing world. They're versatile, durable, and make life easier for engineers and designers alike. By choosing PEEK, you're not just getting a part; you're getting peace of mind knowing it'll perform well and last a long time.
FAQ About Peek Plastic Parts
What are PEEK plastic parts?
Peek plastic parts are components made from Polyether Ether Ketone (PEEK), a high-performance thermoplastic known for its excellent mechanical properties, chemical resistance, and ability to withstand extreme temperatures. These parts are widely used in demanding applications where durability and reliability are crucial.
Why choose PEEK over other plastics?
Choosing PEEK over other plastics comes down to its superior performance characteristics. PEEK offers exceptional thermal stability, high mechanical strength, and outstanding chemical resistance. It can handle continuous use at higher temperatures compared to many other plastics, making it ideal for challenging environments.
How durable are PEEK plastic parts?
PEEK plastic parts are incredibly durable. They maintain their mechanical properties even at elevated temperatures and harsh chemical exposures. This makes them suitable for long-term use in demanding industrial applications without significant wear or degradation.
Can PEEK parts withstand high temperatures?
Absolutely! PEEK is renowned for its ability to withstand high temperatures. It has a continuous service temperature of up to 480°F (250°C) and can handle short-term exposures to even higher temperatures. This makes PEEK parts perfect for applications involving heat and thermal cycling.
Are PEEK plastic parts resistant to chemicals?
Yes, PEEK plastic parts are highly resistant to a wide range of chemicals, including acids, bases, and solvents. This resistance ensures that PEEK parts remain stable and functional even in corrosive environments, which is why they are often used in the chemical processing industry.
What industries commonly use PEEK plastic parts?
PEEK plastic parts are utilized across various industries due to their robust performance. Common applications include the aerospace, automotive, medical, semiconductor, and oil & gas sectors. In these fields, reliability and performance under extreme conditions are critical, and PEEK meets those demands effectively.
How are PEEK plastic parts manufactured?
Manufacturing PEEK plastic parts involves several steps, including injection molding, extrusion, and machining. The process begins with raw PEEK pellets, which are melted and then shaped into the desired form. Post-processing techniques like CNC machining can further refine the parts to meet specific requirements.
Do PEEK parts require special handling or maintenance?
While PEEK parts are quite resilient, they do benefit from proper handling and maintenance to ensure longevity. Regular cleaning and inspection can help detect any potential issues early on. Additionally, avoiding prolonged exposure to extremely high temperatures beyond their limits can prevent material degradation.
Are there any limitations of using PEEK plastic parts?
Despite their numerous advantages, PEEK plastic parts do have some limitations. They tend to be more expensive than other plastics, which can be a consideration for budget-sensitive projects. Additionally, while PEEK is highly resistant to many chemicals, it may not be suitable for use with strong oxidizing acids or certain halogenated compounds.
How can I get custom PEEK plastic parts made?
Getting custom PEEK plastic parts made involves working with a manufacturer that specializes in high-performance materials. Provide detailed specifications, including dimensions, tolerances, and any special requirements you might have. Many manufacturers offer design assistance to ensure the parts meet your exact needs before proceeding with production.