PLA Plastic Parts Materials
Whether you're working with PLA plastic parts that are already in the making or still developing your PLA product, our process will make every stage of your product lifecycle smoother.
Benefits of PLA Plastic Parts:
- Long-lasting and safe to use
- Many treatment options available
- Quick delivery
- Custom-made PLA plastic parts
- One-stop service from quotation to delivery, including design, manufacturing, and samples
Designing PLA Plastic Parts Our molds are always optimized for certain polymers and fine-tuned to produce the best parts. To prevent degradation of the PLA material, you need a hot runner system with low shear and no dead spots in the manifold or nozzle. Use an externally heated nozzle with an open channel to stop PLA from getting stuck and causing flow lines on the product. This can happen with an internally heated nozzle.
Unlike a hot runner, a sprue needs a draft angle of more than 6° during the injection process to avoid sticking when the mold opens. This reduces the maximum height of the sprue. If not, the sprue becomes too thick, cools or crystallizes too quickly, and extends the process time. Sprue walls should be thinner than the product walls. PLA should crystallize in the mold when used with high heat materials. Amorphous materials can only be formed by polymers, leaving others in a semi-crystalline state.
As a result, the product is slightly flexible when ejected from the mold.
When the product draft angle is increased, enough ejector pins are installed, and the ejector surface is sufficient, the product won't warp during ejection.
The injection of PLA into the mold happens under high pressure. PLA is very viscous. A faulty venting system might cause minor flashes on the product. Start with minimal venting and open the machine (remove steel) as needed. Molds that aren't filled or areas where PLA material burns near venting points show insufficient venting and need more.
A stiff material like PLA can cause sharp flashes. Ventilation should be close to where it's needed but not where flashing is banned. Heat-resistant PLA products need more crystallization in the mold, so they shrink more than standard PLA products.
For PLA products with tight dimensional specifications, designers should consider this when developing molds. Create a mold so steel can be removed anywhere it's needed after the first reproducible injection molding trial.
Injection molding of PLA offers several benefits:
- Degradable by microorganisms, minimal environmental impact after use.
- Excellent mechanical and physicochemical properties.
- Easily processed, useful, and suitable for blow molding, melt processing, and various other processes.
- Glamorous and transparent.
- Compatible and degradable.
- Superior tensile and ductile strength.
- Permeance to air and oxygen.
Applications of Injection Molded PLA:
- Food packaging
- Fast food lunch boxes
- Nonwoven fabrics
- Industrial fabrics
- Healthcare fabrics
- Dishcloths
- Sanitary products
- Outdoor UV resistant fabrics
- Tent cloths
- Floor mats, etc.
PLA Plastic Parts Making Service
Be good at product structure optimization and greatly reduce the cost of Plastic Parts Materials
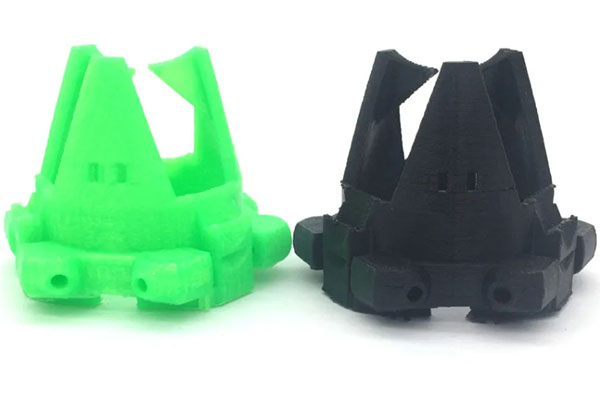
Parts Design
Appearance and structural design
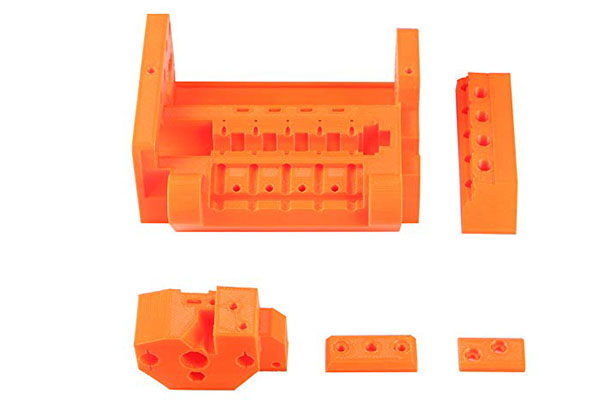
Mold Making
Design, DFM confirmation
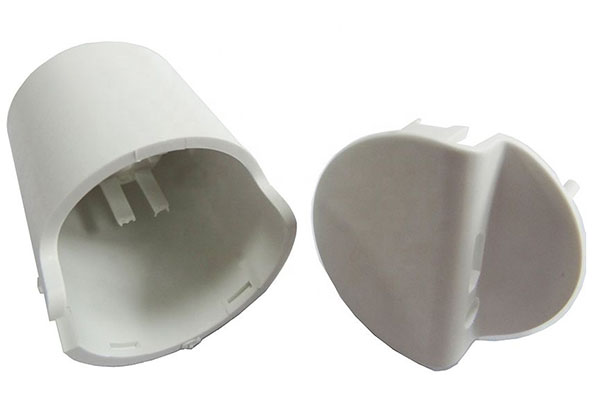
Product Production
Imported, high-speed equipment
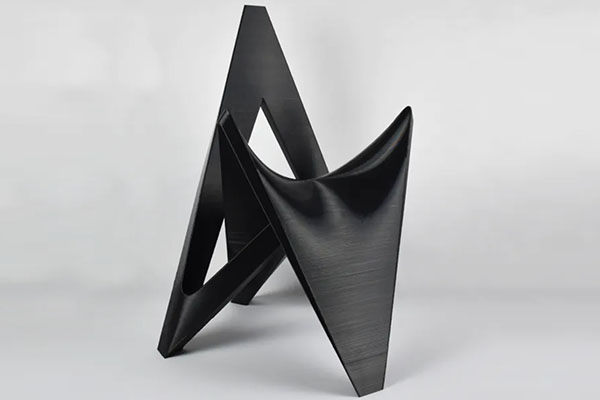
Product Assembly
Incoming materials, inspection and assembly
The Advantages of PLA Plastic Parts Materials
Polyactic acid, or PLA, is a type of plastic that breaks down naturally and can be made again. It's getting really popular for making all sorts of things because it's better for the environment. Let's talk about why PLA plastic parts are so great and where they can be used.
Here's what makes PLA plastic parts stand out:
- Eco-friendly: PLA breaks down into natural stuff over time. This means it's better for the planet compared to regular plastics made from oil.
- Safe: It's not toxic, so it's safe to use with food and in medical stuff. Plus, it doesn’t have any nasty chemicals like BPA or phthalates.
- Easy to work with: PLA melts at a low temperature, so it's simple to shape into different forms using injection molding machines. It flows well, which means it can easily fill complex molds.
- Strong and durable: PLA is pretty strong and stiff, which makes it perfect for lots of different uses. It also stands up well to moisture and heat.
- Versatile: You can use PLA plastic parts to make packaging, everyday items, and even medical devices.
- Affordable: Compared to other eco-friendly materials, PLA is quite cheap, making it a budget-friendly choice for many products.
In short, PLA plastic parts are a fantastic option for makers who want to create products that are good for the environment and safe to use.
FAQ About PLA Plastic Parts
What are PLA plastic parts?
PLA, or polylactic acid, is a type of biodegradable plastic commonly used to make various parts and products. It's derived from renewable resources like corn starch or sugar cane, making it an eco-friendly choice compared to traditional plastics. PLA parts are often used in 3D printing and packaging due to their ease of processing and relatively low environmental impact. Plus, they have a good strength-to-weight ratio and can be easily colored or modified for different applications.
How are PLA plastic parts made?
The production of PLA plastic parts starts with the fermentation of natural materials like corn or sugarcane. This process breaks down the starches into lactic acid. Then, through a chemical reaction called polycondensation, lactic acid molecules link together to form long chains of polylactic acid. These chains are then melted and molded into the desired shapes. The entire process is more sustainable than producing conventional plastics because it relies on renewable resources and produces fewer greenhouse gases.
Are PLA plastic parts eco-friendly?
Yes, PLA plastic parts are considered eco-friendly for several reasons. Firstly, they are made from renewable resources, reducing our reliance on fossil fuels. Secondly, they are biodegradable under industrial composting conditions, which means they can break down more quickly than traditional plastics. However, it's important to note that PLA doesn't degrade easily in home compost bins or natural environments, so proper disposal in industrial composting facilities is essential.
Can PLA plastic parts be recycled?
Recycling PLA plastic parts can be a bit tricky because not all recycling facilities accept PLA. While it’s technically recyclable, the infrastructure to handle it isn't as widespread as for other plastics like PET or HDPE. That said, some specialized programs do exist. If you want to recycle PLA, you should check with local recycling centers to see if they accept it or if there are drop-off locations available. Otherwise, ensuring these parts are sent to industrial composting facilities is the next best option.
What are the advantages of using PLA plastic parts?
One major advantage of PLA plastic parts is their biodegradability, which makes them more environmentally friendly than many other plastics. They also have good mechanical properties, including decent strength and flexibility, making them suitable for a variety of applications. Additionally, PLA is easier to print than some other materials, making it popular in 3D printing. Its ability to be colored and its clarity add to its versatility for different uses, from packaging to medical devices.
What are the disadvantages of using PLA plastic parts?
Despite their benefits, PLA plastic parts do have some drawbacks. For one, they aren’t as durable as some other plastics, especially under high heat or prolonged exposure to moisture. This can limit their use in certain applications where longevity and robustness are crucial. Another issue is that while PLA is biodegradable, it requires specific conditions to break down properly, usually found only in industrial composting settings. Also, the raw materials for PLA, such as corn, can compete with food supplies, potentially driving up prices for both.
How do PLA plastic parts compare to other types of plastic parts?
Compared to traditional plastics like ABS or PETG, PLA has the edge in terms of being more eco-friendly and easier to print, especially in 3D printing applications. However, it falls short in durability and heat resistance. For instance, ABS is much stronger and more heat-resistant but is not biodegradable. On the other hand, PETG offers a good balance between strength and ease of printing but again lacks the biodegradable quality of PLA. So, the choice depends on whether sustainability or performance is more critical for your needs.
Can PLA plastic parts be used in food packaging?
Yes, PLA plastic parts are often used in food packaging because they are non-toxic and can be safely used in contact with food. Their biodegradable nature also makes them an attractive option for reducing waste in the food industry. However, it’s worth noting that while PLA is generally safe, it may not be suitable for all types of food packaging, especially those requiring high heat resistance or long shelf life. Always check compatibility with specific food products and storage conditions.
What happens to PLA plastic parts when they are buried in landfill?
When PLA plastic parts are buried in a landfill, they don’t decompose as quickly as they would in an industrial composting facility. Landfills lack the necessary conditions—like temperature, oxygen levels, and microbial activity—that facilitate the breakdown of PLA. As a result, PLA parts can take a long time to decompose in a landfill, similar to many other types of plastics. Therefore, it’s better to dispose of PLA in an industrial composting setting if possible.
Are there any special considerations when designing with PLA plastic parts?
When designing with PLA plastic parts, there are a few things to keep in mind. First, because PLA isn’t as strong or heat-resistant as some other plastics, it might not be suitable for applications requiring high durability or exposure to high temperatures. You’ll need to consider the mechanical properties carefully. Additionally, PLA can absorb moisture from the environment, which can affect its performance over time. Designing with these factors in mind will help ensure that your PLA parts function well throughout their intended lifespan.