Polycarbonate (PC) Plastic Parts Materials
Polycarbonate, or PC as it's commonly known, is a type of plastic that's clear, safe, and strong. It's got some great features like being able to handle knocks and bumps really well, standing up to both hot and cold temperatures, not getting easily bent out of shape over time, stopping electricity from passing through, resisting fire, and staying the same size even when the temperature changes. Plus, it doesn't let sunlight damage it quickly, which means it lasts longer.
Right now, when it comes to clear plastics for engineering, PC is top-notch. It lets through more than 90% of daylight, almost like glass. This makes it perfect for things where you need to see through the material.
Because PC is light and easy to work with, it's used in lots of different areas. You'll find it in factories, farms, buildings, electronics, hospitals, airplanes, and more.
When you mold PC parts using injection molding, they come out tough and ready for action. They can take a hit without breaking, stay strong even when it's hot, let light pass through like glass, don't bend much under pressure, and don't soak up water.
There are also special versions of PC mixed with things like glass fibers, minerals, or flame retardants to make them even better for certain jobs. But because PC can be a bit tricky to flow and needs high heat to mold, sometimes you need custom molds for these special types.
You can spot PC parts in lots of everyday items: the casings for gadgets, car parts, lights, brackets, glasses lenses, medical tubes, plugs and sockets, and covers for devices.
Polycarbonate Plastic Parts Making Service
Be good at product structure optimization and greatly reduce the cost of Plastic Parts Materials
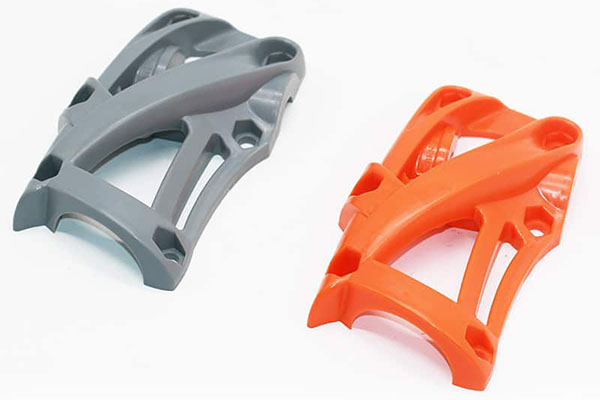
Part Design
Appearance and structural design
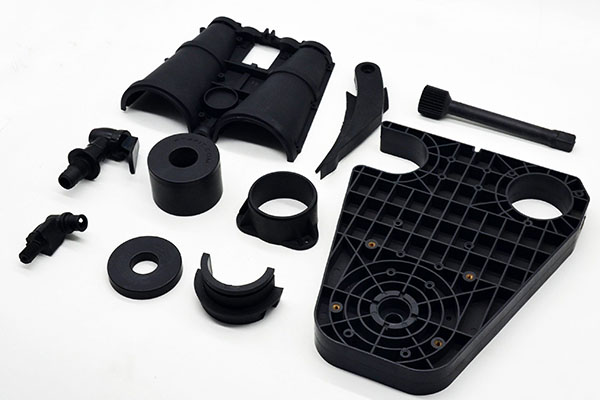
Mold Making
Design, DFM confirmation
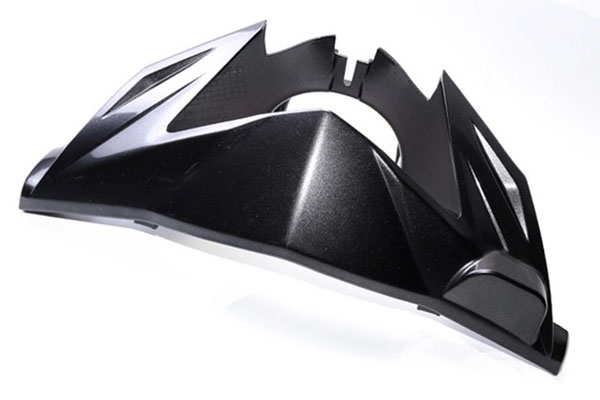
Product Production
Imported, high-speed equipment
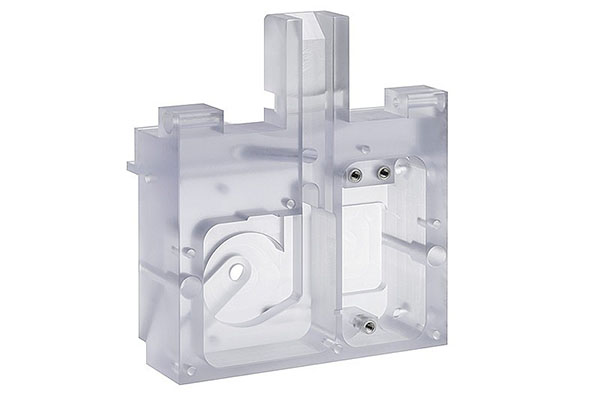
Product Assembly
Incoming materials, inspection and assembly
The Advantages and Applications of PC Plastic Parts Materials
Polycarbonate, or PC, is a really handy thermoplastic material that's often used to make plastic parts. These plastic bits have lots of great features that make them useful in many different fields. In this article, we'll look at the perks and uses of PC plastic parts.
The Good Stuff About PC Plastic Parts PC plastic parts come with several benefits:
- They're tough: PC is known for being able to handle hard knocks, which makes it perfect for things that need to be strong and last long.
- They can take the heat: PC doesn't melt or lose its qualities when it gets hot, so it's great for stuff that needs to withstand high temperatures.
- You can see through them: PC is clear, making it ideal for items where you want to see through or let light pass through.
- They keep their shape: PC stays the same size and shape even under pressure, which is pretty neat.
Where PC Plastic Parts Are Used PC plastic parts are used in a bunch of different areas, like:
- Cars: You'll find PC in car headlights, inside trims, and dashboards because it's durable and clear.
- Electronics: PC is used in computer and phone cases due to its strength and transparency.
- Medical stuff: PC is used in medical equipment like IV connectors and blood filters because it's safe for the body and tough.
- Packaging: PC is used in packaging like water bottles and food containers because it's clear and strong.
Challenges with PC Plastic Parts Even though PC plastic parts are awesome, they do have some downsides:
- They cost more: PC plastic parts are pricier than other types of plastic parts.
- They need special handling: Making PC plastic parts requires special techniques, like higher pressure and longer cooling times.
- They don't like stress: PC can crack or get tiny lines if it's stressed too much.
In short, PC plastic parts are fantastic for many uses but come with some challenges. If you're thinking about using PC plastic parts for your project, talk to a trusted manufacturer to make sure you get the right materials and processes.
FAQ About Polycarbonate Plastic Parts
What are Polycarbonate Plastic Parts?
Polycarbonate plastic parts are components made from a type of thermoplastic known for its strength and transparency. They are often used in applications requiring high impact resistance and clarity. These parts can be molded into various shapes and sizes, making them versatile for many uses.
What makes Polycarbonate Plastic unique compared to other materials?
Polycarbonate stands out due to its balance of toughness, clarity, and heat resistance. Unlike some other plastics, it doesn't become brittle over time and maintains its strength even at higher temperatures. This combination of properties makes it ideal for both indoor and outdoor applications.
Are Polycarbonate Plastic Parts environmentally friendly?
While polycarbonate plastic is durable and long-lasting, it is not biodegradable. However, it can be recycled if proper facilities are available. Recycling helps mitigate environmental impact by reducing waste and conserving resources. Proper disposal and recycling practices are essential for managing the lifecycle of these parts.
Can Polycarbonate Plastic Parts be customized?
Yes, polycarbonate plastic parts can be highly customized. They can be molded into specific shapes, colors, and sizes to meet exact requirements. Additionally, surface treatments such as coatings or texturing can be applied to enhance their appearance or functionality. Customization options make these parts suitable for a wide range of industries.
How do you clean Polycarbonate Plastic Parts?
Cleaning polycarbonate plastic parts is straightforward. Use a mild soap solution and a soft cloth or sponge to gently wipe the surfaces. Avoid using abrasive cleaners or tools that could scratch the material. For more stubborn dirt, a mixture of water and isopropyl alcohol works well without damaging the plastic.
What are common applications for Polycarbonate Plastic Parts?
Polycarbonate plastic parts are used in various industries due to their versatility. Common applications include safety goggles, electronic device casings, automotive parts, and construction materials like windows and roofing. Their durability and optical clarity make them popular in both consumer and industrial products.
How durable are Polycarbonate Plastic Parts?
Polycarbonate plastic parts are highly durable. They have excellent impact resistance, which means they can withstand significant force without breaking. They also resist weathering from UV light and temperature changes, making them suitable for long-term use in harsh environments. This durability ensures a longer lifespan compared to many other plastics.
Do Polycarbonate Plastic Parts have any limitations?
While polycarbonate plastic has many advantages, it does have some limitations. It can scratch more easily than some other plastics, which might affect its appearance over time. Additionally, while it is heat-resistant, prolonged exposure to high temperatures can cause deformation. Proper care and usage are essential to maximize their lifespan.
Are there different types of Polycarbonate Plastic Parts?
Yes, there are several types of polycarbonate plastic parts tailored for specific applications. Some are designed for high impact resistance, others for thermal stability, and some for enhanced optical clarity. The choice depends on the intended use and performance requirements of the part in question.
How can I ensure the quality of Polycarbonate Plastic Parts?
Ensuring the quality of polycarbonate plastic parts involves selecting a reputable manufacturer with stringent quality control processes. Look for certifications and standards compliance such as ISO or ASTM. Additionally, checking for consistent thickness, color, and finish across batches can help maintain quality. Regular inspections and testing during production also play a crucial role in ensuring high-quality parts.