Polyester Plastic Parts Materials
Polyester plastic parts are a versatile and efficient manufacturing choice for many applications. Let's take a closer look at how they're made and their benefits.
How It's Made
Heating and Melting: First, polyester pellets are heated until they melt. This usually happens at temperatures between 220-260°C (428-500°F).
Injection: The melted polyester is then pushed into a mold under high pressure. This step makes sure the material fills all the tiny details of the mold, allowing for complex shapes.
Cooling and Solidification: Once the mold is filled, the melted polyester cools down and solidifies. Cooling channels in the mold help speed up this process, making it faster and more productive.
Ejection: After cooling, the mold opens, and the finished part pops out. Now it's ready for any final touches or to be used right away.
Advantages of Polyester Plastic Parts
- Precision and Complexity: These parts can be very detailed and precise, perfect for things that need to fit just right.
- Cost-Effectiveness: Making lots of them at once lowers the cost per piece, great for mass production.
- Durability: Polyester parts are strong and long-lasting, ideal for tough jobs.
- Versatility: They can be colored and textured in many ways, which is handy for looks-important items like car parts or gadgets.
Common Uses
- Automotive Parts: Things like mirror covers, trim pieces, and some functional parts.
- Electrical Components: Housings for switches and connectors because they don't let electricity pass through easily.
- Household Appliances: Parts for toasters, blenders, and vacuum cleaners.
- Toys and Houseware: Lightweight but durable toys, kitchen tools, and storage containers.
Key Considerations
- Material Selection: Different polyesters have different strengths, like heat resistance and chemical resistance. Pick the right one for your needs.
- Mold Design: A well-made mold is key for precision and quick production. Working with skilled toolmakers helps here.
- Process Control: Keeping injection speed, pressure, and cooling time just right ensures quality and reduces mistakes.
Environmental Impact
Polyester, especially PET, can be recycled, which is good for the environment. Proper recycling turns old stuff into new products, cutting down on waste and saving resources.
In short, polyester plastic parts are a fantastic option for making high-quality, complex items efficiently and affordably. Whether you need tough automotive parts or pretty household items, polyester has got you covered.
Polyester Plastic Parts Making Service
Be good at product structure optimization and greatly reduce the cost of Plastic Parts Materials
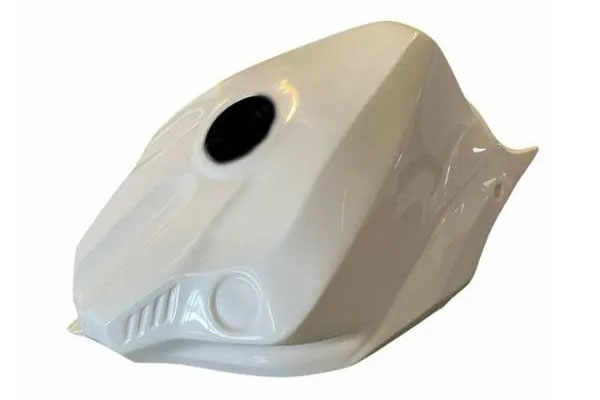
Part Design
Appearance and structural design
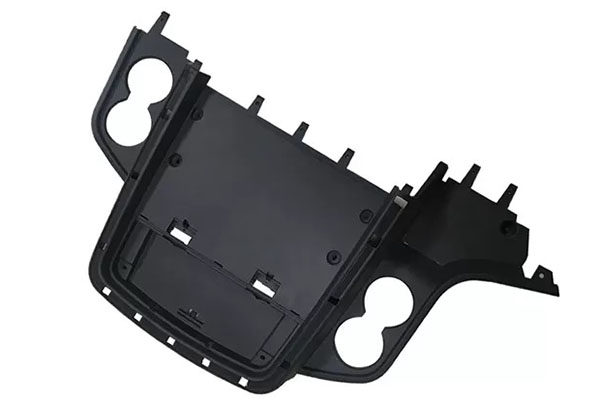
Mold Making
Design, DFM confirmation
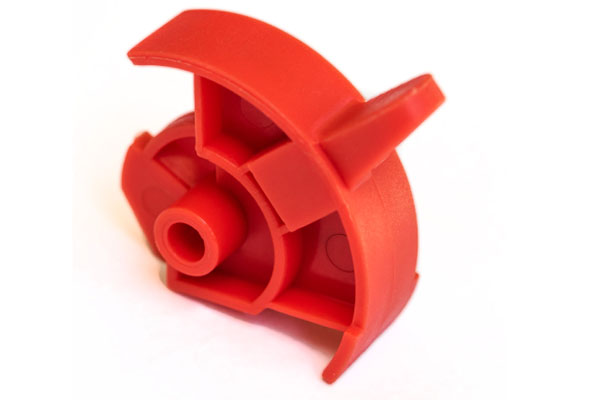
Product Production
Imported, high-speed equipment
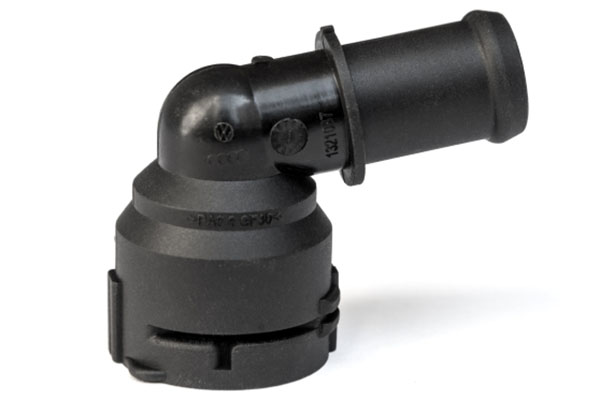
Product Assembly
Incoming materials, inspection and assembly
Exploring the Materials Used in Polyester Plastic Parts Materials
Understanding the materials used in creating plastic parts is super important for making high-quality products. Let's break down each part and its role:
Polyester Resins These are the main ingredients in making plastic parts. They turn hard and strong through a special process called curing. Here's what they bring to the table:
- Strong and Stiff: Polyester resins are really tough, which makes them perfect for things that need to hold up under pressure.
- Heat Resistant: They can handle high temperatures, so they're great for many industrial uses.
- Shrinkage Issues: One tricky part is that they can shrink and twist as they cool. This means you have to be careful with how you make them to avoid problems.
Fillers Fillers are added to make the plastic parts even better and cheaper. Common ones include:
- Glass Fibers: These make the parts stronger and stiffer, which is why you see them in cars and electronics.
- Calcium Carbonate: It helps cut costs while keeping the parts strong enough. It also makes the surface smoother.
- Talc: Like calcium carbonate, it reduces costs and improves how easy it is to mold the parts. However, it might slightly weaken the material compared to not using any filler.
Pigments Pigments are what give color to the final product. Here’s what you need to know:
- Color Options: You can get pigments in lots of colors, so you can make your product look just right.
- Type Matters: Organic pigments are brighter but might not stand up to heat as well as inorganic ones. The choice depends on what you need the part to do.
- Impact on Strength: Adding pigments can change how strong the material is. Sometimes, you might need to tweak the process a bit to keep everything balanced.
By picking the right mix of polyester resins, fillers, and pigments, manufacturers can make parts that perform well, look good, and don't cost too much. Knowing how these materials work together is key to making awesome plastic parts efficiently.
In short:
- Polyester Resins form the base but need careful handling to prevent shrinking and warping.
- Fillers boost strength and save money but can make the process a bit harder.
- Pigments add color and customization but need to be used smartly to keep the parts strong.
Mastering these materials helps manufacturers create top-notch plastic parts that meet high standards without breaking the bank.
FAQ About Polyester Plastic Parts
What are Polyester Plastic Parts and how are they used?
Polyester plastic parts are components made from polyester materials, which are types of polymers with ester groups in their chemical structure. They're known for their strength and durability, making them perfect for a variety of applications. You'll often find them in the automotive industry, where they're used for parts like car bodies and bumpers, because of their resistance to wear and tear. They're also popular in electronics for casings due to their insulating properties.
How do Polyester Plastic Parts compare to other types of plastics?
Well, when it comes to comparing polyester plastic parts to others, it really depends on what you need. For instance, polyester parts tend to be stronger and more durable than some plastics, like polyethylene or PVC. They also have better resistance to heat and chemicals, which makes them great for tough environments. However, they might not be as flexible as some other plastics, so if you need something that can bend easily, you might want to look elsewhere. It's all about picking the right material for the job!
Are Polyester Plastic Parts environmentally friendly?
That's a good question! Polyester plastic parts themselves aren't biodegradable, which means they won't break down easily in the environment. This can be a concern if they end up in landfills or oceans. However, many manufacturers are working on making these parts more eco-friendly. Some are using recycled materials to make new parts, which helps reduce waste. Plus, because these parts last longer and are more durable, you don't need to replace them as often, which can be better for the environment in the long run. It's all about finding a balance!
Can Polyester Plastic Parts be recycled?
Yes, they can be recycled, but there are some challenges. The recycling process for polyester plastic parts is a bit more complicated compared to other materials. It usually involves breaking down the polymer chains and then reforming them into new products. This process requires specialized equipment and facilities, which aren't as widespread. However, advancements in recycling technology are making it easier and more cost-effective. So, while it might not be as simple as throwing them in a curbside bin, it is possible to recycle polyester plastic parts with the right setup.
How durable are Polyester Plastic Parts?
Oh, they're pretty tough! Polyester plastic parts are known for their strength and durability. They can withstand a lot of wear and tear, which is why they're often used in applications where other materials might fail. For example, in the automotive industry, they're used for parts that need to be both strong and lightweight. They also resist impacts well, so they're great for things that might get knocked around a bit. Overall, if you're looking for something that will last, polyester plastic parts are a good bet.
What are the manufacturing processes involved in creating Polyester Plastic Parts?
There are a few different ways to make polyester plastic parts, depending on what you need. One common method is injection molding, where the melted plastic is injected into a mold to form the part. This is great for making complex shapes and large quantities. Another method is extrusion, where the plastic is forced through a die to create continuous shapes like tubes or sheets. And then there's blow molding, which is used to make hollow objects like bottles. Each method has its own advantages, so the choice depends on the specific requirements of the part being made.
How do you maintain Polyester Plastic Parts?
Maintaining polyester plastic parts is pretty straightforward. First off, keep them clean by wiping them down regularly with a damp cloth. Avoid using harsh chemicals or abrasive materials, as these can damage the surface. If the parts are exposed to sunlight, try to keep them out of direct UV rays, as prolonged exposure can cause them to fade or become brittle over time. Lubricate moving parts as needed to ensure smooth operation. And if you notice any cracks or damage, address it promptly to prevent further deterioration. With a bit of care, these parts can last a long time!
Are there any safety concerns associated with Polyester Plastic Parts?
Generally speaking, polyester plastic parts are considered safe for most uses. However, there are a few things to keep in mind. For instance, if these parts are exposed to high temperatures, they can release fumes that might not be safe to inhale. It's also important to handle them properly during manufacturing and installation to avoid any injuries. And if the parts are used in food-related applications, make sure they meet all regulatory standards for safety. As long as you follow basic safety guidelines, everything should be fine.
Can Polyester Plastic Parts be customized for specific applications?
Absolutely! One of the great things about polyester plastic parts is that they can be easily customized to fit almost any application. Whether you need a specific shape, size, or color, manufacturers can adjust the production process to meet your needs. This flexibility makes them ideal for a wide range of industries, from automotive to consumer goods. Just provide the specifications, and they can tailor the parts accordingly. It's this adaptability that keeps polyester plastic parts relevant in so many fields.
What are the cost considerations for using Polyester Plastic Parts?
When it comes to cost, polyester plastic parts can vary quite a bit depending on several factors. The complexity of the part, the volume of production, and any special requirements all play a role in determining the final price. While they might be more expensive upfront compared to some other materials, they often provide better value in the long run due to their durability and low maintenance needs. Additionally, bulk orders or long-term contracts can sometimes lead to discounts. So, while the initial investment might be higher, the overall cost benefit can be quite favorable.