Polyethylene (PE) Plastic Parts Materials
Let's talk about plastic parts, specifically those made from polyethylene. This type of plastic is super handy for making various items because it has some really cool features.
Firstly, polyethylene is great at keeping things safe from moisture and gases. It's like using an airtight container to keep your snacks fresh—polyethylene does the same thing but for a lot more stuff. It keeps the good stuff inside and the bad stuff out.
Another awesome thing about polyethylene is how light it is. It's so light that you barely feel it, which makes it perfect for things like aerospace or sports equipment. You won't even notice it's there, but you'll definitely feel the difference when you lift it.
Polyethylene is also really tough. It's like the marathon runner of the plastic world—it can handle a lot without breaking down. Whether it's exposed to harsh weather or heavy use, this material stands strong.
And let's not forget about its flexibility and rigidity. Polyethylene can be stiff for structural support or flexible for packaging. It adapts to whatever you need, making it a star player in various industries.
When used in food and drink containers, high-density polyethylene is also safe. Some common items made from polyethylene include containers, pallets, crates, packaging, bottle tops, automotive components, toys, and drainpipes.
So, there you have it—a quick look at why polyethylene is such a versatile material for making plastic parts.
Polyethylene (PE) Plastic Parts Making Service
Be good at product structure optimization and greatly reduce the cost of Plastic Parts Materials
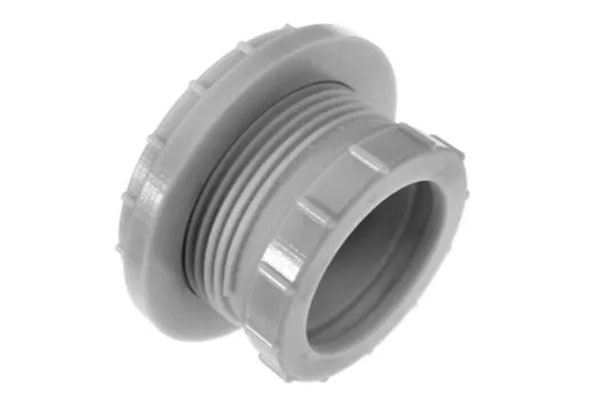
Part Design
Appearance and structural design
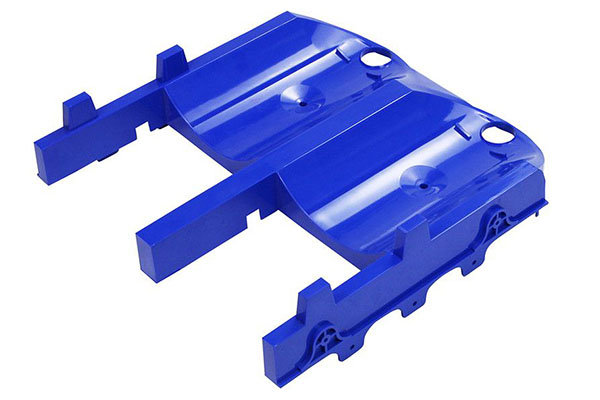
Mold Making
Design, DFM confirmation
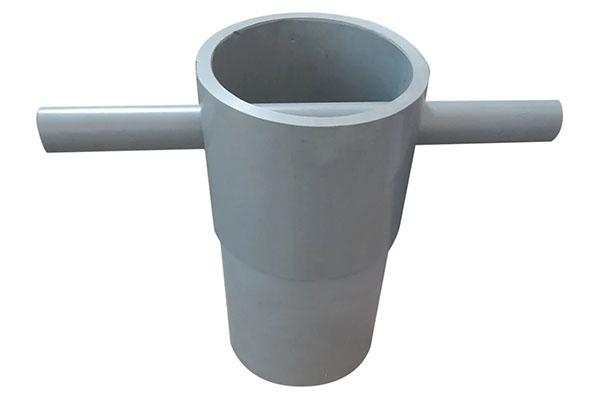
Product Production
Imported, high-speed equipment
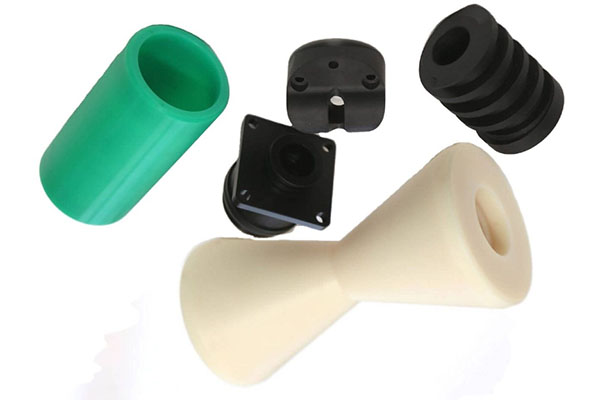
Product Assembly
Incoming materials, inspection and assembly
An Overview of Polyethylene (PE) Plastic Parts Materials
Cost-Effectiveness and Processability Polyethylene (PE) really shines when it comes to cost-effectiveness. It's a great choice for mass production because it keeps material costs low. Plus, it's super easy to work with, so manufacturers can quickly ramp up production. This is perfect for hitting tight deadlines and meeting high-volume demands.
Types of Polyethylene High-Density Polyethylene (HDPE): HDPE is known for being stiff and strong, making it ideal for things that need to be rigid like containers and industrial parts. Low-Density Polyethylene (LDPE): LDPE is more flexible and often used in products like plastic bags and film wraps. Linear Low-Density Polyethylene (LLDPE): LLDPE sits between HDPE and LDPE in terms of properties. It's tough yet flexible, making it great for grocery sacks and agricultural films. Environmental Benefits One big plus of PE is that it can be recycled. In today's world, where environmental concerns are huge, being able to recycle PE helps reduce waste and lower the carbon footprint of production. This fits well with many companies' sustainability goals and what consumers expect from eco-friendly products.
Customization PE can easily be colored or tinted, which is great for branding. This is especially useful in packaging where brand recognition matters. Different colors can help differentiate product lines or just make the product look better.
Key Considerations When choosing PE for manufacturing, it's important to think about factors like what the part will be used for, how durable it needs to be, its chemical resistance, and the specific mechanical properties needed. For example, an automotive part might need different properties than a packaging solution. Working with experienced suppliers can help fine-tune these aspects to make sure the final product meets all necessary specifications.
Applications Galore From household items like toys and storage bins to critical components in the automotive and aerospace industries, PE's versatility knows no bounds. Its ability to withstand harsh conditions and maintain performance over time makes it a go-to material for various industries.
In summary, PE materials offer a great mix of affordability, ease of processing, and adaptability, making them a top choice for manufacturers across diverse sectors. Whether it’s about achieving high performance or maintaining sustainability, PE has got you covered.
FAQ About Polyethylene PE Plastic Parts
What are Polyethylene PE Plastic Parts?
Polyethylene (PE) plastic parts are components made from a versatile thermoplastic polymer known for its durability, flexibility, and resistance to chemicals. These parts can take various forms, including films, sheets, containers, pipes, and more. They're widely used in industries like packaging, automotive, construction, and consumer goods because of their lightweight nature and ease of fabrication.
Are Polyethylene PE Plastic Parts Recyclable?
Yes, polyethylene PE plastic parts are indeed recyclable. In fact, they fall under the category of one of the most commonly recycled plastics. When it comes to recycling PE, it’s essential to sort them correctly based on their type, typically marked with recycling codes #2 (HDPE) or #4 (LDPE). Proper sorting ensures they can be efficiently processed and reused in manufacturing new products, reducing environmental impact.
How Durable are Polyethylene PE Plastic Parts?
Polyethylene PE plastic parts are quite durable. They have excellent resistance to moisture, making them ideal for outdoor applications. Additionally, they can withstand a wide range of temperatures without becoming brittle or losing shape. This makes them suitable for long-term use in various environments, from harsh industrial settings to everyday household items.
Can Polyethylene PE Plastic Parts Be Used in Food Packaging?
Absolutely! Polyethylene PE plastic is commonly used in food packaging due to its non-toxic properties and ability to act as a barrier against moisture and contaminants. High-density polyethylene (HDPE), for example, is often found in grocery bags and margarine tubs, while low-density polyethylene (LDPE) is used in food wraps and squeeze bottles. It's safe for food contact and helps extend the shelf life of products.
What Makes Polyethylene PE Plastic Parts Suitable for Outdoor Use?
The suitability of polyethylene PE plastic parts for outdoor use stems from their remarkable resistance to UV radiation, moisture, and temperature fluctuations. They don’t degrade easily when exposed to sunlight or extreme weather conditions, making them perfect for outdoor furniture, playground equipment, garden tools, and even in construction materials like roofing membranes.
Are There Different Types of Polyethylene PE Plastic Parts?
Yes, there are several types of polyethylene PE plastic parts, mainly categorized into high-density polyethylene (HDPE) and low-density polyethylene (LDPE). HDPE is stiffer and more resistant to wear and tear, often used in products like milk jugs and piping. LDPE, on the other hand, is flexible and used in applications requiring toughness and stretch, such as plastic bags and flexible containers.
Can Polyethylene PE Plastic Parts Be Customized?
Indeed, polyethylene PE plastic parts can be customized extensively. Through processes like injection molding, blow molding, and roto-molding, manufacturers can create parts of specific shapes, sizes, and colors to meet particular needs. Additives can also be mixed into the material to enhance properties such as UV resistance, flame retardancy, or antimicrobial features.
What Industries Commonly Use Polyethylene PE Plastic Parts?
Polyethylene PE plastic parts find applications across numerous industries. In the automotive sector, they're used for fuel tanks and interior components. The construction industry utilizes them in pipes, fittings, and roofing membranes. Packaging is another significant user, employing PE for everything from shopping bags to protective wrappings. Even in healthcare, PE is valued for its use in medical devices and packaging due to its sterility and safety.
How Do Polyethylene PE Plastic Parts Contribute to Sustainability?
Polyethylene PE plastic parts play a role in sustainability through their recyclability and the potential for using recycled content in manufacturing new products. By reducing the need for virgin materials, this practice conserves natural resources and reduces environmental footprint. Moreover, their longevity and resistance to degradation mean fewer replacements are needed over time, further supporting sustainable practices.
Are Polyethylene PE Plastic Parts Safe for Children?
Yes, polyethylene PE plastic parts are generally considered safe for children. They are non-toxic and free from harmful chemicals like BPA and phthalates, which are often concerns with other plastics. Products made from PE, such as children’s toys and baby bottles, are widely regarded as safe. However, it's always wise to check for certifications and ensure the product complies with safety standards specific to children’s products.