Polyimide Plastic Parts Materials
Let's talk about plastic parts, shall we? Imagine this: you have a bunch of melted plastic that gets turned into all sorts of cool stuff—like tiny gears, tough bearings, and those important electrical connectors. This isn't just any plastic; it's polyimide, the superhero of thermoplastics. It's super strong, can handle extreme heat, and doesn't mess around with chemicals. That makes it perfect for high-tech jobs in aerospace, cars, and electronics.
Here's how it goes down: First, you heat up the polyimide resin until it's nice and melty. Then, using a special machine, either a screw type or a plunger type, you shoot this gooey stuff into a carefully made mold. Once it cools off and comes out of the mold, you might need to do a little cleanup—trim here, drill there, and maybe smooth out the surface a bit.
This process is pretty amazing. You end up with parts that fit together perfectly or are strong enough to take on the roughest conditions. The magic of making these plastic parts lies in being able to make them very precise and complex without wasting time or materials.
But, like any superhero, polyimide has its weaknesses too. It can be expensive and needs special tools and machines. Some types are so stubborn and sensitive to heat that they can be tricky to work with. That's where the real skill comes in—choosing the right material and tweaking every step to make sure each part is top-notch.
Polyimide Plastic Parts Making Service
Be good at product structure optimization and greatly reduce the cost of Plastic Parts Materials
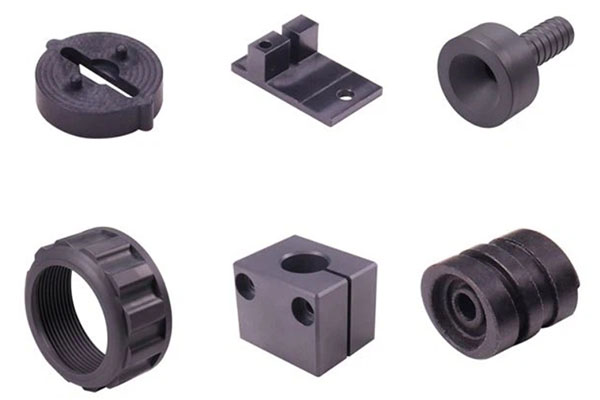
Part Design
Appearance and structural design
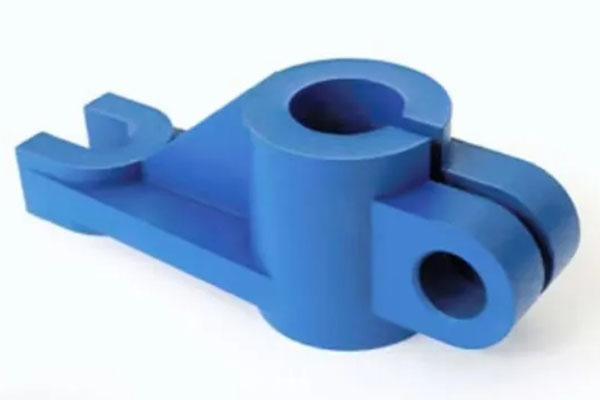
Mold Making
Design, DFM confirmation
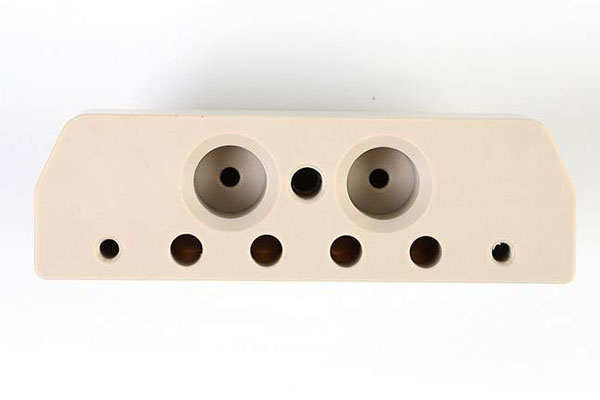
Product Production
Imported, high-speed equipment
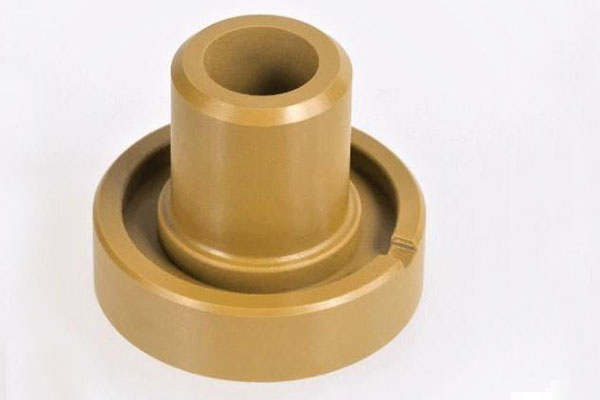
Product Assembly
Incoming materials, inspection and assembly
the World of Polyimide Plastic Parts Materials: Properties, Applications, and Challenges
Plastic parts made from polyimide are super popular because they're strong and can handle extreme conditions. These plastics don't melt easily, even when it gets really hot, which is why you see them in planes and gadgets. They also don't get ruined by chemicals, so they're perfect for tough jobs.
What makes these plastic parts special?
- Heat-resistant: They can take a lot of heat without falling apart. Great for things like jet engines or electronic stuff that gets warm.
- Chemically tough: They won't break down if you spill something harsh on them. Useful for harsh environments.
- Strong and stiff: They keep their shape well and don't wear out quickly.
- Good with electricity: They don't let electricity pass through easily, which is handy for electronic devices.
Where do we use these plastic parts?
- Airplanes: For engine bits, structure pieces, and keeping wires safe.
- Electronics: In connectors, circuit boards, and protecting cables.
- Cars: As bearings, gears, and electrical safety covers.
- Medical stuff: In implants, tubes for doctors, and surgery tools.
But, there are some tricky parts too:
- Pricey: They cost more than other plastics, making production expensive.
- Hard to work with: These plastics are thick and hard to shape into detailed designs.
- Not always the same: Sometimes, the quality can vary between batches, affecting how good the final product is.
In short, while polyimide plastic parts are amazing for many high-tech uses, making them isn't always easy or cheap. But as we need better materials, these plastics will keep getting better and used more widely.
FAQ About Polyimide Plastic Parts
What are polyimide plastic parts?
Polyimide plastic parts are components made from a type of high-performance polymer known for its exceptional thermal stability, mechanical strength, and resistance to wear and chemicals. These parts are used in various industries where durability and reliability under extreme conditions are crucial.
What makes polyimide plastic unique compared to other plastics?
Polyimide stands out due to its high temperature resistance, which can go up to 500°F (260°C), making it suitable for applications that involve exposure to heat. It also has excellent mechanical properties, including high tensile strength and flexibility, and is resistant to many chemicals and radiation. This combination of attributes sets it apart from more common plastics.
In what industries are polyimide plastic parts commonly used?
Polyimide parts find extensive use in aerospace, automotive, electronics, and medical industries. For instance, they are often employed in aircraft and spacecraft for their lightweight yet strong characteristics. In electronics, they're used for printed circuit boards and insulation materials due to their electrical properties and heat resistance. The medical field uses them for surgical tools and implantable devices because of their biocompatibility and strength.
How are polyimide plastic parts manufactured?
The manufacturing process typically involves a chemical reaction called polycondensation, where dianhydrides and diamines react to form polyimide precursors. These precursors are then processed through stages such as curing and molding to achieve the final shape and properties. Advanced techniques like 3D printing are also becoming popular for creating complex geometries with precision.
Can polyimide plastic parts be recycled?
Recycling polyimide plastic parts can be challenging due to their complex chemical structure and high-performance nature. However, some specialized recycling programs and processes do exist. It's essential to consult with experts or manufacturers to understand the best practices and facilities available for recycling these materials.
Are there any health risks associated with handling polyimide plastic parts?
Generally, polyimide plastic parts are safe to handle and do not pose significant health risks. However, like any material, it’s advisable to follow standard safety protocols, such as wearing protective gear and ensuring proper ventilation, especially during cutting or shaping processes to avoid inhaling any fine particles.
How do you maintain and clean polyimide plastic parts?
Maintenance is relatively straightforward. Cleaning can usually be done with mild soap and water or specific solvents recommended by the manufacturer. Avoid using abrasive materials that could scratch the surface. Regular inspections for wear and tear are also important to ensure longevity and performance.
What are the limitations of polyimide plastic parts?
Despite their many advantages, polyimide plastic parts can be expensive to produce and may not be cost-effective for all applications. Additionally, their high melting point can make them difficult to process using conventional methods. They can also be brittle at lower temperatures, which might limit their use in extremely cold environments.
Can polyimide plastic parts be customized for specific applications?
Yes, polyimide plastic parts can often be customized to meet specific requirements. Manufacturers can adjust the formulation and processing techniques to enhance certain properties, such as flexibility, strength, or thermal resistance. Customization options include different shapes, sizes, and even incorporating additional features like embedded components or coatings.
What are the future trends for polyimide plastic parts?
The future of polyimide plastic parts looks promising with ongoing research aimed at improving their properties and reducing costs. Innovations in manufacturing techniques, such as advanced 3D printing, are expected to broaden their application scope. There is also growing interest in developing more sustainable production methods and exploring new composite materials that incorporate polyimide for enhanced performance.