Polyoxymethylene (POM) Plastic Parts Materials
Polyoxymethylene, while not a household name, is a superstar in the world of plastic parts. This material's got some serious perks:
First off, it's incredibly strong. It can handle temperatures from a chilly -40°C up to a toasty 140°C without breaking a sweat. Plus, it keeps its shape really well—talk about stable! And let's not forget how tough it is against wear and tear. It also sports a shiny finish that looks great and stays that way. Oh, and it doesn't soak up much moisture, which is always a plus.
Think about all the things that could use these awesome qualities. Gear wheels? Check. Ball bearings? You bet. Fasteners, knife blades, locking systems, even ski bindings—they all benefit from polyoxymethylene's strength and durability. It's almost like having metal without the metal hassle. That's why this stuff is so popular in making all sorts of plastic parts through injection moulding.
Polyoxymethylene (POM) Plastic Parts Making Service
Be good at product structure optimization and greatly reduce the cost of Plastic Parts Materials
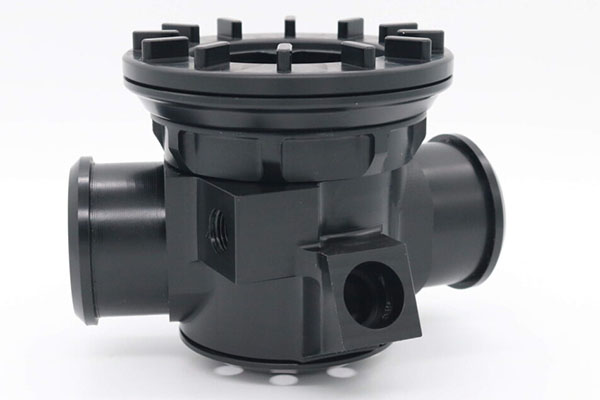
Part Design
Appearance and structural design
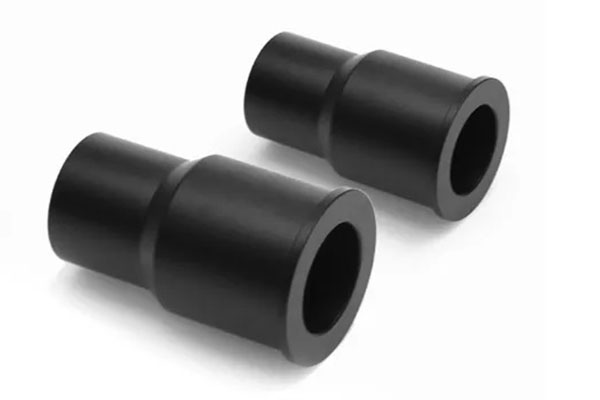
Mold Making
Design, DFM confirmation
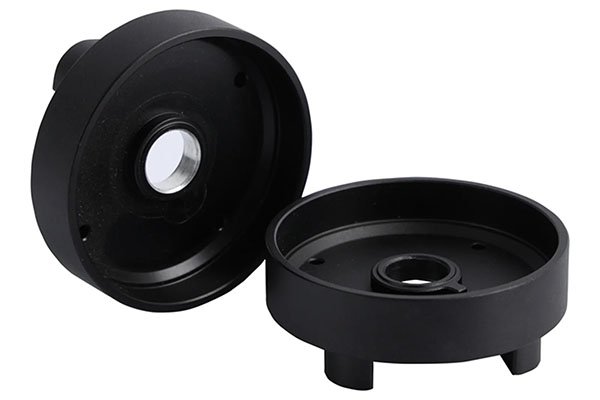
Product Production
Imported, high-speed equipment
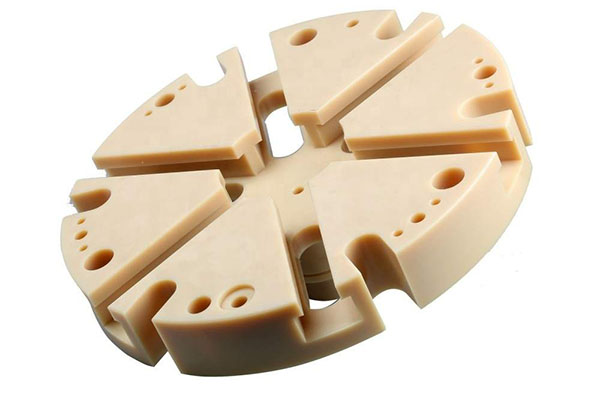
Product Assembly
Incoming materials, inspection and assembly
The Pros and Cons of POM Plastic Parts Materials: Properties, Applications, and Limitations
POM (Polyoxymethylene) is a type of plastic that's really popular because it's strong and stable. It's used in lots of different things because it can handle tough conditions without breaking or changing shape. In this article, we'll take a look at what makes POM special, where it's used, and some of its downsides.
What Makes POM Special
Here are some cool things about POM:
- Strong and Stiff: POM is super strong and doesn't bend easily. That's why it's perfect for things that need to be tough.
- Stays the Same: Even when it gets hot or wet, POM keeps its shape. This means it won't warp or shrink much.
- Smooth Moving: POM is slippery, so it moves easily without sticking. Great for parts that need to glide smoothly.
- Chemical Resistant: POM doesn't get damaged by many chemicals, like acids or alcohols. So it lasts longer in harsh environments.
Where POM is Used
POM is everywhere! Here are a few places you might find it:
- Cars: POM is often used to make car parts like gears and fuel system components.
- Everyday Items: You might not realize it, but POM is in things like zippers and toy parts.
- Electronics: Camera parts and printer bits often use POM because it works well with electronics.
Things to Watch Out For
Even though POM is great, it has some drawbacks:
- Not for High Heat: POM melts at lower temperatures, so it's not good for really hot stuff.
- Sun Sensitive: If left in the sun, POM can break down over time.
- Absorbs Moisture: POM can get swollen if it soaks up too much moisture.
- Limited Colors: It's hard to make POM in bright colors, so choices are limited.
If you're thinking about using POM for your project, talk to a trusted manufacturer to make sure it's the right choice for you.
FAQ About Polyoxymethylene POM Plastic Parts
What is Polyoxymethylene (POM)?
Polyoxymethylene, commonly known as POM, is a high-performance thermoplastic with excellent mechanical properties. It's often referred to by the trade names Delrin or Celcon. POM stands out for its stiffness, strength, and ability to maintain those qualities over a wide range of temperatures. This makes it ideal for parts that need durability and precision.
How are POM plastic parts manufactured?
POM parts can be made through several manufacturing processes including injection molding, extrusion, and machining. Injection molding is the most common method because it allows for high production rates and complex part geometries. The process involves heating the POM pellets until they melt, injecting the molten material into a mold, and then cooling it to solidify.
What are the benefits of using POM plastic parts?
One major benefit of POM plastic parts is their excellent dimensional stability, which ensures that parts maintain their shape and size over time. They also have low moisture absorption, making them suitable for environments where other plastics might swell or warp. Additionally, POM has good resistance to wear and fatigue, which extends the lifespan of the parts.
Are POM plastic parts environmentally friendly?
While POM itself is not biodegradable, it can be recycled. However, recycling facilities need to handle POM separately from other plastics due to its unique properties. Unlike some other plastics, POM does not release toxic substances when properly processed. Always check local recycling guidelines if you plan to recycle POM parts.
Can POM plastic parts be used in food-related applications?
Yes, POM is FDA-approved for food contact, making it safe for use in kitchenware, appliances, and food processing equipment. Its non-toxic nature and low moisture absorption make it an excellent choice for applications where hygiene is critical. Just ensure that the specific grade of POM you use is certified for food contact.
What are the limitations of POM plastic parts?
Despite their many advantages, POM plastic parts do have some limitations. They have relatively poor UV resistance and can become brittle when exposed to prolonged sunlight. Additionally, while they are strong and durable under normal conditions, they can become stressed or crack under extreme impact. Therefore, they may not be the best choice for outdoor or high-impact applications without additional protection.
How do I clean POM plastic parts?
Cleaning POM plastic parts is straightforward. For general cleaning, warm water and mild soap are usually sufficient. Avoid using harsh chemicals or abrasive cleaners as they can damage the surface of the parts. If more intensive cleaning is needed, isopropyl alcohol can be used, but always test on a small area first to ensure it doesn’t affect the material.
Can POM plastic parts be painted or dyed?
Yes, POM plastic parts can be painted or dyed, but special primers and paints designed specifically for plastics are required. Standard paints may not adhere well to the surface of POM, so it’s important to use products formulated for this purpose. Additionally, prepping the surface properly by cleaning and sometimes lightly sanding can improve adhesion.
What industries commonly use POM plastic parts?
POM plastic parts are widely used across various industries including automotive, consumer electronics, industrial machinery, and medical devices. Their durability and precision make them ideal for gears, bearings, fasteners, and structural components. The material’s resistance to chemicals and fatigue also makes it popular in environments requiring long-term reliability.
How do I choose the right grade of POM for my application?
Choosing the right grade of POM depends on your specific application requirements. Some grades are reinforced with glass or other materials to increase strength and stiffness, while others may be optimized for better wear resistance or lower friction. It’s essential to consult with material suppliers or manufacturers to select a grade that meets your mechanical, thermal, and chemical performance needs.