Polystyrene (PS) Plastic Parts Materials
When most folks think of polystyrene, they picture that white stuff we see all the time in packaging and for keeping things warm. But did you know there are two main kinds? One is called high-impact polystyrene and the other is general purpose polystyrene. The high-impact kind is super popular because it's really easy to work with when making things by injection molding—that's like using a fancy machine to shape plastic.
Here's why it's so awesome:
- It doesn't wear out easily and can take a beating
- Keeps things nice and cozy, great for insulation
- You can paint it or glue it without much fuss
- It's pretty cheap, which saves money
- And it's strong, really tough against bumps and knocks
This type of plastic isn't just for show; it's used in lots of different areas, especially for making electronics and medical stuff. Like those little Petri dishes doctors use, the bins that hold our trash, the cases around TVs and computers, toolboxes that last forever, and even the outside of fridges and freezers.
Just take a peek at your toolbox next time—it's probably made from high-impact polystyrene, shaped perfectly by injection molding. That's what makes it so solid, compact, and long-lasting.
Polystyrene (PS) Plastic Parts Making Service
Be good at product structure optimization and greatly reduce the cost of Plastic Parts Materials
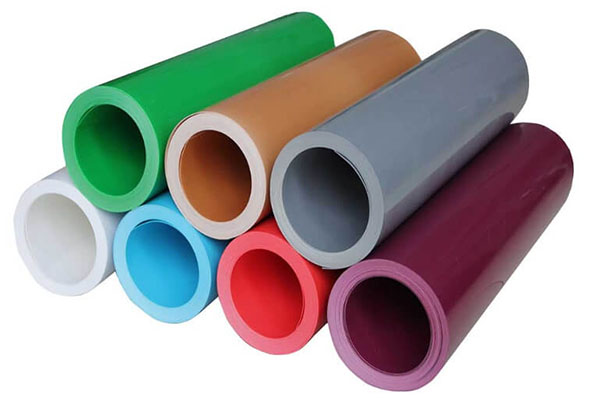
Part Design
Appearance and structural design
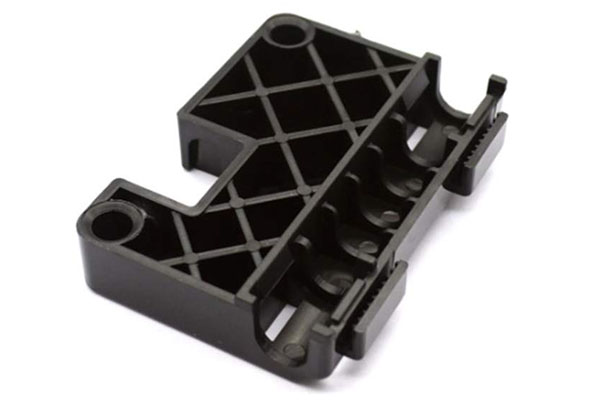
Mold Making
Design, DFM confirmation
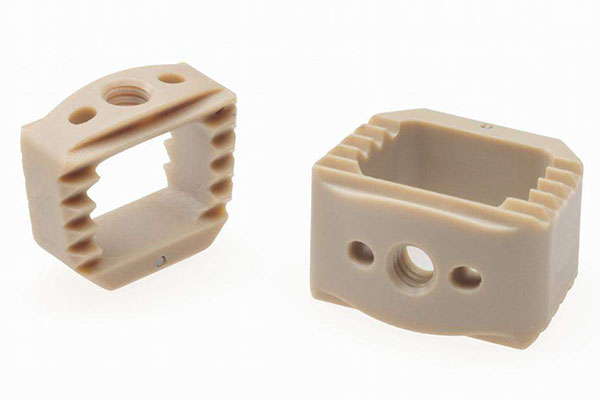
Product Production
Imported, high-speed equipment
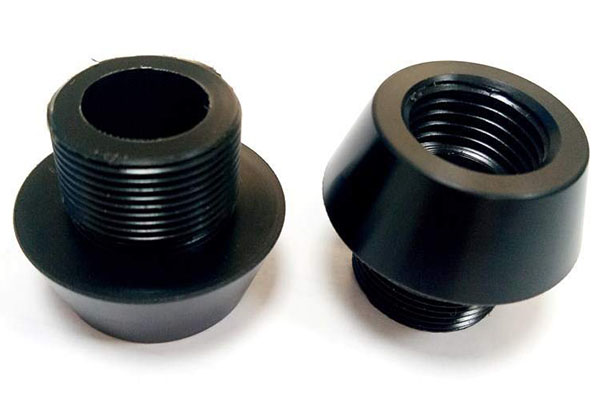
Product Assembly
Incoming materials, inspection and assembly
The Ins and Outs of Polystyrene PS Plastic Parts Materials: Properties, Applications, and Benefits
Polystyrene (PS) is a common thermoplastic polymer that's often picked for plastic parts because of its great properties. PS materials are light, strong, and easy to customize for specific needs. In this article, we'll look at the properties, uses, and advantages of PS in making plastic parts.
Properties of PS Materials PS is made from styrene monomers and has several useful features:
Lightweight: PS is light, making it perfect for things where weight matters.
Strong: PS can handle heavy impact without breaking or cracking.
Stable shape: PS keeps its shape even when it gets hot or wet.
Good insulator: PS is great at stopping electricity, which makes it good for electronic stuff.
Uses of PS Materials PS is used in many industries like packaging, consumer goods, and electronics. Here are some common uses:
Packaging: PS is often used for disposable cups, trays, and food containers.
Consumer goods: PS is used to make toys, appliances, and kitchen items.
Electronics: PS is used in computers, printer cartridges, and other electronic parts.
Advantages of PS Materials PS has several benefits, including:
Customizable: PS can be changed to fit specific needs like color, texture, and hardness.
Cheap: PS is affordable, making it a good choice for manufacturing.
Recyclable: PS can be recycled, making it an eco-friendly option.
Versatile: PS can be used in many different ways, making it very adaptable.
PS is a popular choice for plastic parts because it's light, strong, and stable. It's widely used in packaging, consumer goods, and electronics. If you're thinking about using PS for your plastic parts, talk to a trusted manufacturer to make sure you get the right material for your needs.
FAQ About Polystyrene PS Plastic Parts
What are polystyrene PS plastic parts used for?
Polystyrene PS plastic parts are widely used in various industries due to their versatility and durability. They are commonly found in packaging materials, disposable cutlery, insulation, and even some electronic housings. Their lightweight nature makes them ideal for applications where weight is a concern. Moreover, they can be easily molded into different shapes and sizes, making them suitable for custom designs.
Are polystyrene PS plastic parts recyclable?
Yes, polystyrene PS plastic parts are recyclable, but the process can be more challenging compared to other plastics. It's essential to check with your local recycling program as not all facilities accept polystyrene. When recycled properly, it can be transformed back into useful products, reducing environmental impact. Proper sorting at the source is crucial for effective recycling.
How do polystyrene PS plastic parts compare to other plastics?
Compared to other plastics like polyethylene or polypropylene, polystyrene has a higher clarity and rigidity, making it perfect for applications requiring transparent components or structural integrity. However, it's generally less flexible and more brittle. Each type of plastic has its unique set of properties, so the choice depends on the specific requirements of the application.
Can polystyrene PS plastic parts be used in food packaging?
Absolutely, polystyrene PS plastic parts are extensively used in food packaging, especially for items like yogurt cups, salad containers, and takeout boxes. They are favored for their ability to maintain product freshness and their lightweight nature. However, it's important to ensure that they meet food safety standards to avoid any health risks.
What are the environmental concerns associated with polystyrene PS plastic parts?
One major concern is that polystyrene is not biodegradable and can persist in the environment for a long time if not properly managed. Additionally, its production and disposal processes can contribute to environmental pollution. Efforts are being made to improve recycling rates and develop more sustainable alternatives to mitigate these issues.
How durable are polystyrene PS plastic parts?
Polystyrene PS plastic parts are quite durable under normal conditions but can become brittle over time when exposed to extreme temperatures or UV light. They are resistant to impact and can withstand moderate stress, making them suitable for a variety of uses. However, their longevity can vary based on the specific formulation and intended use.
Are there any health risks associated with using polystyrene PS plastic parts?
Generally, polystyrene PS plastic parts are considered safe for their intended uses. However, there have been concerns about the potential release of styrene monomer, a precursor to polystyrene, under certain conditions. It's always advisable to follow safety guidelines and regulations to minimize any potential health risks.
How can I identify polystyrene PS plastic parts?
Polystyrene PS plastic parts often have a clear or translucent appearance and are usually marked with the recycling symbol #6. They also tend to be lighter than many other types of plastic. If you're unsure, a material data sheet or consulting with the manufacturer can provide definitive identification.
What is the cost of producing polystyrene PS plastic parts?
The cost of producing polystyrene PS plastic parts can vary depending on factors like raw material prices, manufacturing processes, and scale of production. Generally, it's a cost-effective material, especially for high-volume production runs. However, it's always best to get quotes from multiple suppliers to find the most economical option.
Can polystyrene PS plastic parts be customized?
Yes, polystyrene PS plastic parts can be highly customized to meet specific needs. This includes variations in color, shape, size, and even adding special features like textures or coatings. Working with an experienced manufacturer can help you achieve the desired specifications while ensuring quality and functionality.