Plastic PVC Plastic Parts Materials
PVC, or Polyvinyl Chloride, is a super common material in the world of plastic parts. It's the third most made synthetic plastic polymer and is loved by many because it's strong, doesn't attract static, and is easy to shape. Plus, it's cheap but gives you a lot back in return. Both the tough and flexible types of PVC are used in lots of places like building stuff, making chemicals, packaging, health care gadgets, and home items.
Here's why PVC parts are great:
- They don't cost much and are easy to find.
- You can easily shape them into whatever you need.
- They're really hard and strong (especially the rigid kind).
- If you add something called a heat stabilizer, they can handle high heat.
- They don't break when hit much compared to other plastics.
- Good for certain electrical jobs because they stop electricity from going through.
- They last long outside and don't get ruined by chemicals or alkali.
- Being a thermoplastic, PVC can be molded and recycled easily. This makes it a top pick for making things like building materials, electronic bits, and all sorts of shapes and tubes. We've been offering top-notch PVC part making for over 13 years now, helping businesses in many fields with our reliable service.
Our PVC part making service has some clear wins:
- We use only the best PVC for molding, with strict checks on quality.
- We help you make things faster and cheaper.
- Our plans save money and fit your needs perfectly.
- We tailor our service just for you, from start to finish.
- Our expert engineers design perfect PVC parts just for you.
- We give quick support before and after you buy, free samples, and always deliver on time.
PVC Injection Plastic Parts Making Service
Be good at product structure optimization and greatly reduce the cost of Plastic Parts Materials
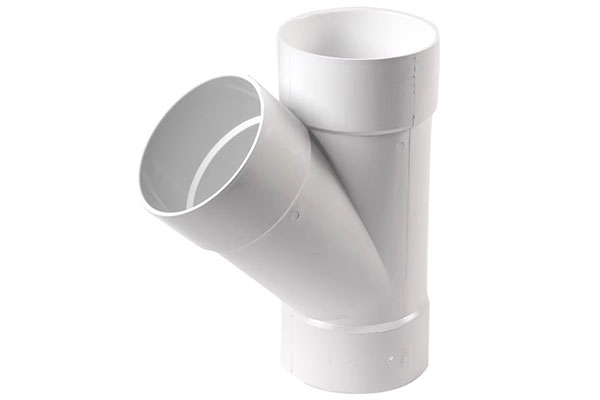
Part Design
Appearance and structural design
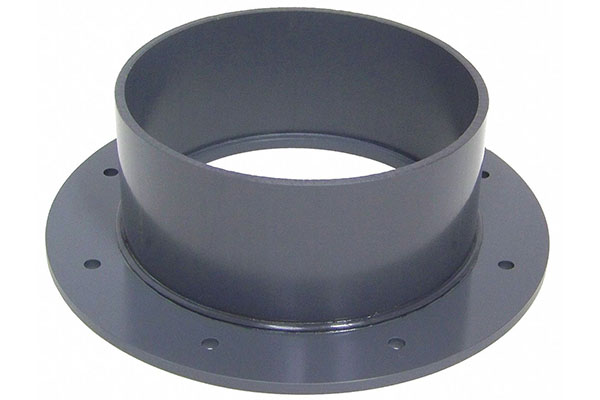
Mold Making
Design, DFM confirmation
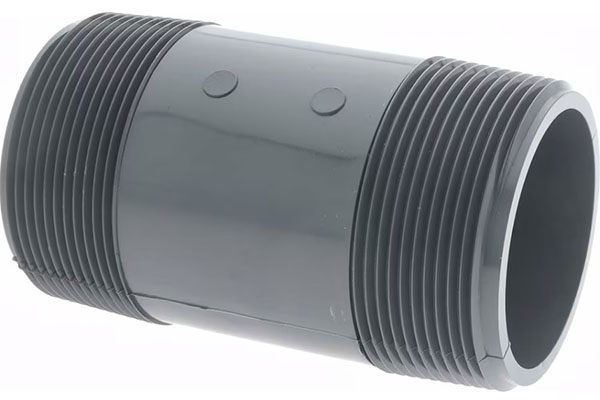
Product Production
Imported, high-speed equipment
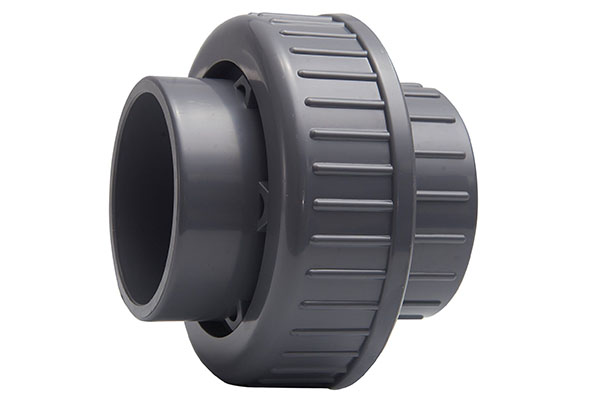
Product Assembly
Incoming materials, inspection and assembly
The Benefits and Applications of PVC Plastic Parts Materials
Polyvinyl chloride, or PVC, is a super common thermoplastic material that's widely used in making plastic parts. These PVC parts have a bunch of benefits that make them perfect for lots of different industries. Let's take a look at why PVC parts are so great and where they're used.
Why PVC Parts Are Awesome:
- Durable: PVC can handle all sorts of tough conditions like sunlight, heat, and chemicals without falling apart.
- Flexible: It’s easy to shape PVC into whatever form you need, which makes it super versatile for many uses.
- Cheap: Compared to other plastic materials, PVC is pretty affordable.
- Versatile: You can tweak PVC to be rigid, flexible, clear, or opaque, fitting a wide range of needs.
Where PVC Parts Shine:
- Construction: You'll find PVC in things like window frames, pipes, and vinyl siding because it’s strong and long-lasting.
- Consumer Goods: PVC is used in toys, inflatable items, and shower curtains thanks to its flexibility and durability.
- Medical Devices: PVC is great for medical stuff like blood bags and tubing because it’s safe, flexible, and resistant to chemicals.
- Packaging: PVC is often used in packaging like blister packs and clamshell cases because it’s clear and tough.
Challenges with PVC Parts:
Even though PVC has a lot of pros, it does come with some cons:
- Not Green Friendly: PVC isn’t the best for the environment and can release harmful chemicals when made and thrown away.
- Flammable: PVC burns easily and gives off toxic fumes if it catches fire.
- Heat Sensitive: PVC doesn’t do well in high temperatures, which can limit its use in certain applications.
In short, PVC parts are fantastic for many uses due to their durability, flexibility, and cost-effectiveness. However, they do have some downsides, especially regarding the environment and safety. If you're thinking about using PVC parts for your project, it’s a good idea to chat with a reliable manufacturer to make sure you get the right material and processing for your needs.
FAQ About PVC Plastic Parts
What are PVC plastic parts used for?
PVC plastic parts are incredibly versatile and find applications in a wide range of industries. They're commonly used in the construction industry for pipes, fittings, and window frames due to their durability and resistance to chemicals. In the automotive sector, they're utilized for interior components like door panels and trims. Additionally, PVC is prevalent in medical devices, packaging materials, and even in making toys, thanks to its cost-effectiveness and ease of molding into various shapes.
How are PVC plastic parts manufactured?
The manufacturing process of PVC plastic parts begins with the polymerization of vinyl chloride monomer to create polyvinyl chloride resin. This resin is then mixed with various additives such as stabilizers, lubricants, and plasticizers to enhance its properties. The mixture is heated until it melts, forming a homogeneous substance that can be shaped using techniques like injection molding, extrusion, or blow molding. Once formed, the parts are cooled and cured to achieve their final shape and hardness.
Are PVC plastic parts environmentally friendly?
While PVC itself is durable and long-lasting, its environmental impact has been a concern. The production process releases harmful chemicals, including dioxins, which can persist in the environment. However, advancements have been made to minimize these emissions. Additionally, PVC is recyclable, but the recycling process can be complex due to the presence of various additives. Efforts are ongoing to improve recycling methods and promote the use of recycled PVC in new products.
Can PVC plastic parts be recycled?
Yes, PVC plastic parts can be recycled, but the process is more challenging compared to other plastics. Due to the different types of additives used in PVC products, they need to be sorted and processed separately. Specialized facilities are required to handle PVC recycling, where the material is ground into small pieces, melted, and reformed into new products. Encouraging consumers to recycle PVC items properly and supporting infrastructure development for efficient recycling can significantly reduce waste.
What are the advantages of using PVC plastic parts?
PVC plastic parts offer several advantages that make them a popular choice across various industries. They are lightweight yet strong, providing excellent durability without adding much weight. Their resistance to chemicals, weather, and wear makes them ideal for outdoor applications. Moreover, PVC is cost-effective, both in terms of initial material cost and maintenance over time. Its ability to be easily molded into complex shapes also adds to its versatility.
Are there any health concerns associated with PVC plastic parts?
There have been concerns about the potential health risks associated with PVC, particularly due to the presence of phthalates and bisphenol A (BPA), which are sometimes used as plasticizers and stabilizers. These chemicals can leach out of the plastic and potentially cause health issues. However, regulatory bodies closely monitor these substances, and many manufacturers now produce phthalate-free and BPA-free PVC products. It's always advisable to check product specifications and choose certified safe options when possible.
How do I care for and maintain PVC plastic parts?
Maintaining PVC plastic parts is relatively simple. Regular cleaning with mild soap and water is usually sufficient to keep them looking new. Avoid using harsh chemicals or abrasive cleaners, as they can damage the surface. For outdoor applications, PVC parts may require occasional treatments with UV protectants to prevent fading or brittleness over time. Inspecting the parts periodically for any signs of wear or damage can help extend their lifespan.
What is the difference between rigid and flexible PVC plastic parts?
The primary difference between rigid and flexible PVC plastic parts lies in the amount of plasticizers added during manufacturing. Rigid PVC contains very little to no plasticizers, making it hard and brittle, suitable for structural components like pipes and profiles. On the other hand, flexible PVC, also known as vinyl, incorporates higher levels of plasticizers, resulting in a softer, more pliable material ideal for applications like hoses, cables, and seals.
Can PVC plastic parts be painted or printed on?
Yes, PVC plastic parts can be painted or printed on, but proper surface preparation is crucial. Before painting, the surface should be cleaned thoroughly to remove any dirt, grease, or contaminants. A primer specifically designed for plastic surfaces may also be necessary to ensure good adhesion. For printing, techniques like screen printing, pad printing, or digital printing can be used depending on the complexity and quantity of the design. Post-processing treatments might be applied to enhance durability and finish.
Are there alternatives to PVC plastic parts?
Yes, several alternatives exist for PVC plastic parts, especially for those concerned about environmental impact or health risks. Materials like polyethylene (PE), polypropylene (PP), and thermoplastic elastomers (TPE) offer similar properties with potentially lower environmental footprints. Biodegradable options such as polylactic acid (PLA) derived from renewable resources are also gaining popularity. However, it's important to consider the specific requirements of the application when choosing an alternative, as each material has its unique set of characteristics and limitations.