Thermoplastic Polyurethane (TPU) Plastic Parts Materials
When you consider the properties of thermoplastic polyurethane, it's easy to understand why it's a favorite for making plastic parts. The main benefits of using this material include:
- It resists wear and tear.
- It has strong impact resistance.
- It's tough and durable.
- It's flexible and can bend without breaking.
- It has elasticity similar to rubber.
- It protects against oil, grease, and other fluids.
There are countless ways to use thermoplastic polyurethane, but its flexibility while staying rigid makes it particularly useful. Some common applications include:
- Soles of sports shoes
- Car bumpers
- Gaskets
- Bearings
- Mobile phone cases
- Computer parts
- Flotation devices
- Safety goggles
For example, in sports footwear like football boots, where the sole needs both rigidity and flexibility, thermoplastic polyurethane fits the bill perfectly.
Thermoplastic Polyurethane (TPU) Plastic Parts Making Service
Be good at product structure optimization and greatly reduce the cost of Plastic Parts Materials
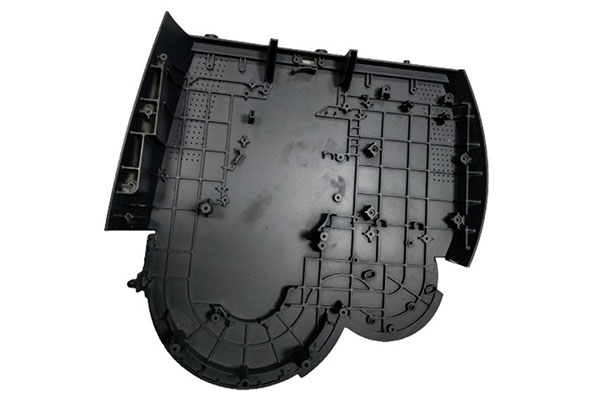
Part Design
Appearance and structural design
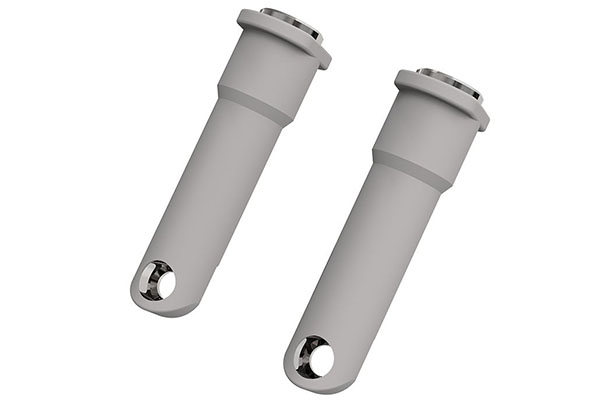
Mold Making
Design, DFM confirmation
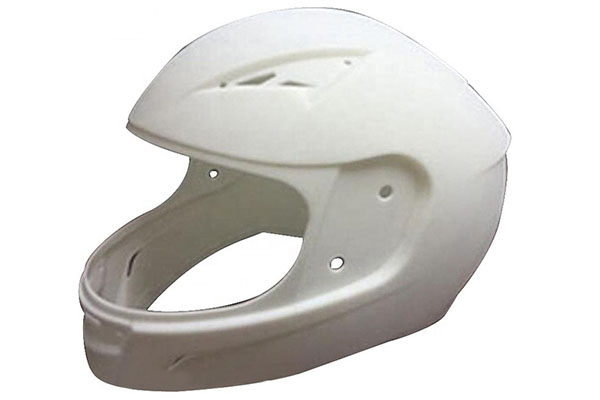
Product Production
Imported, high-speed equipment
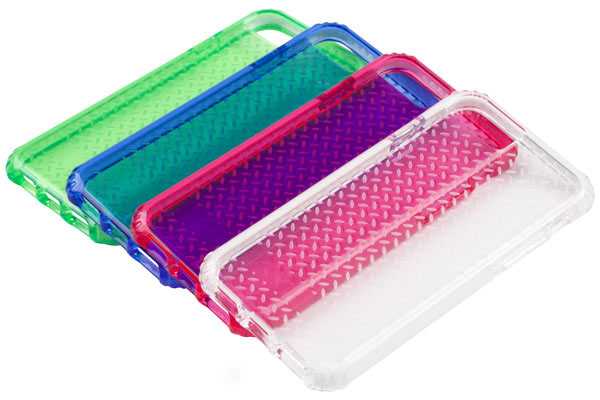
Product Assembly
Incoming materials, inspection and assembly
Understanding Thermoplastic Polyurethane (TPU) Plastic Parts Materials
In the world of manufacturing, plastic parts made fromIn the world of manufacturing, plastic parts made fromthane (TPU) plastic parts made from thermoplastic polyurethane (TPU) are becoming increasingly popular. Whether you're making car parts, sports gear, or medical devices, TPU is a top choice because of its unique qualities. TPU is like a super material that blends the best of both plastic and rubber, giving it amazing benefits during production.
You're designing a new type of sneaker. You need a material that's stretchy enough for comfort but strong enough to hold everything together. That's where TPU shines. It can be molded into any shape or size you need, perfect for creating complex designs. Plus, TPU is tough—it resists wear, chemicals, and UV rays, so your shoes will stay in great shape no matter where you wear them.
One big plus of TPU over other plastics like nylon or polycarbonate is that it doesn't need as high temperatures to mold. This means less shrinking or warping, so your final product comes out just right every time. And if you want to add some color, TPU can be easily dyed, offering endless possibilities for customization and branding.
Of course, when picking TPU for your project, there are a few things to think about. You'll need to know exactly what you're making and what performance features are essential. There are different types of TPU with varying levels of hardness, flexibility, and chemical resistance, so you can find the perfect fit for your needs.
In short, TPU plastic parts are revolutionizing manufacturing with their versatility and excellent properties. Whether you need something rugged enough for harsh conditions or sleek for a premium look, TPU has got you covered. So, next time you're choosing materials, don't overlook TPU—it might just surprise you!
FAQ About Thermoplastic Polyurethane TPU Plastic Parts
What are Thermoplastic Polyurethane (TPU) plastic parts?
TPU plastic parts are components made from thermoplastic polyurethane, a versatile and durable material that combines the benefits of rubber and plastic. It's known for its excellent elasticity, resistance to abrasion, and ability to withstand harsh environmental conditions. These parts are widely used in industries such as automotive, electronics, and consumer goods due to their flexibility and strength.
How do TPU plastic parts compare to other types of plastic parts?
TPU plastic parts stand out because they offer a unique blend of properties. Unlike rigid plastics like ABS or PVC, TPU is highly flexible and can stretch significantly without breaking. It also has better wear and tear resistance compared to rubber, making it ideal for applications requiring durability and longevity. Additionally, TPU is more resistant to oil, grease, and UV light than many other plastics, which enhances its performance in various environments.
Are TPU plastic parts recyclable?
Yes, TPU plastic parts can be recycled, although the process may vary depending on the specific type of TPU and the recycling facilities available. Recycling TPU helps reduce waste and conserve resources. It's essential to check with local recycling programs to see if they accept TPU and follow any specific guidelines they have for processing these materials. Some companies also offer specialized recycling services for TPU products.
Can TPU plastic parts be used in medical applications?
TPU plastic parts are indeed suitable for medical applications due to their biocompatibility and non-toxic nature. They are often used in devices such as catheters, blood bags, and protective covers for medical equipment. Additionally, TPU can be sterilized using various methods, including ethylene oxide and gamma radiation, making it a reliable choice for healthcare settings where hygiene is crucial.
How do you fabricate TPU plastic parts?
Fabricating TPU plastic parts involves several processes, including injection molding, extrusion, and blow molding. Injection molding is the most common method, where molten TPU is injected into a mold cavity under high pressure and then cooled to form the desired shape. Extrusion is used for creating continuous profiles like tubing and sheets, while blow molding is ideal for hollow objects like bottles. Each process requires precise control of temperature and pressure to ensure the quality and consistency of the final product.
What are the advantages of using TPU plastic parts over rubber parts?
TPU plastic parts offer several advantages over traditional rubber parts. Firstly, they are lighter in weight, which can reduce overall product weight and improve fuel efficiency in automotive applications. Secondly, TPU has better resistance to hydrolysis and microbial attack, making it more durable in humid environments. Additionally, TPU can be easily colored and processed into various shapes and textures, providing greater design flexibility compared to rubber.
How do you bond or glue TPU plastic parts together?
Bonding or gluing TPU plastic parts requires special adhesives designed specifically for this material. Cyanoacrylate (super glue) and two-part epoxy resins are commonly used for their strong bonding capabilities. It's important to clean the surfaces thoroughly before applying the adhesive to ensure maximum adhesion. Clamping the parts together during the curing process can also help achieve a stronger bond. Always follow the manufacturer's instructions for the best results.
Can TPU plastic parts be custom-made for specific applications?
Absolutely! TPU plastic parts can be custom-made to fit specific requirements using various manufacturing techniques like injection molding or CNC machining. Customization allows for tailored solutions that meet exact specifications regarding size, shape, color, and functionality. Working with experienced manufacturers can help bring your unique designs to life, ensuring that the parts perform optimally in their intended applications.
What are some common applications of TPU plastic parts?
TPU plastic parts are incredibly versatile and find applications across numerous industries. In the automotive sector, they are used in hoses, gaskets, and interior trim pieces due to their durability and resistance to oils and chemicals. In consumer electronics, TPU protects cables and provides shock absorption for delicate components. They are also prevalent in footwear for their cushioning properties and in sports equipment for impact resistance. The material's flexibility and strength make it an excellent choice for demanding applications.
How do you maintain and care for TPU plastic parts?
Maintaining TPU plastic parts is relatively straightforward. Regular cleaning with mild soap and water is usually sufficient to keep them in good condition. Avoid using harsh chemicals or abrasive cleaners that could damage the surface. For extended lifespan, store TPU parts away from direct sunlight and extreme temperatures, which can cause degradation over time. Periodically inspect the parts for signs of wear or damage, and replace them if necessary to ensure continued performance and safety.