Nickel Metal Parts Materials
Nickel is a shiny, silver-colored metal that falls into the category of transition metals. It's got impressive strength, can stretch without breaking, and has a nice polished look. Plus, it doesn't rust easily, which makes it great for making stainless steel and other rust-resistant alloys. You'll find plenty of nickel in the Earth's crust, mainly in minerals like pentlandite and garnierite. And here's an interesting fact: nickel is magnetic, so it can be attracted by magnets.
Nickel has a wide range of applications, including:
Stainless steel production: As an important alloying element, it improves the strength, corrosion resistance, and heat treatment performance of steel.
Electroplating: Utilizing its corrosion resistance to provide a protective layer for other metals.
Alloy materials: such as nickel based high-temperature alloys, used for key components such as turbine blades in the aerospace industry.
Catalyst: Used as an accelerator for reactions in the chemical industry.
Battery materials: such as nickel hydroxide batteries and nickel cadmium batteries.
Pigments and dyes: used as glazes for ceramic products and for coloring glass.
Special use: such as nickel titanium memory alloy used in medical devices and aviation fields.
Nickel Metal Parts Making Service
Be good at product structure optimization and greatly reduce the cost of Nickel Metal Parts Materials
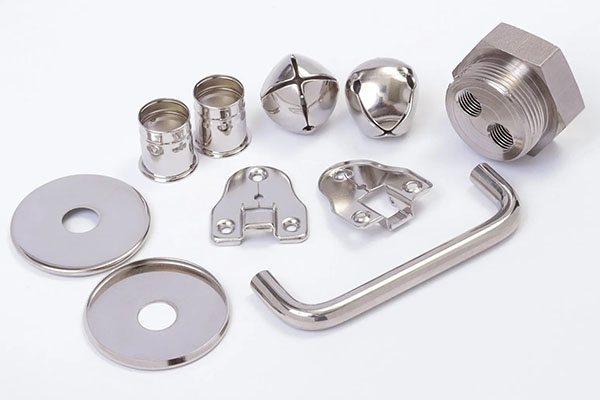
Part Design
Appearance and structural design
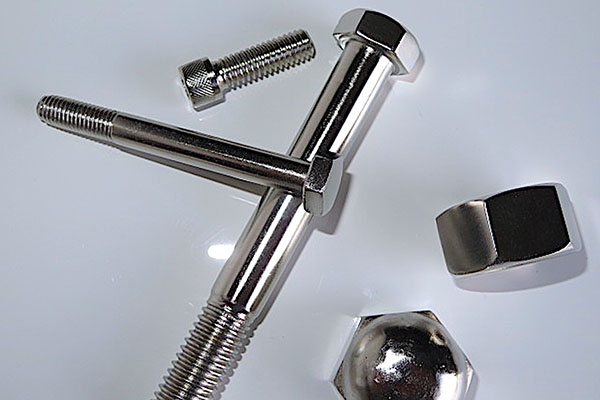
Mold Making
Design, DFM confirmation
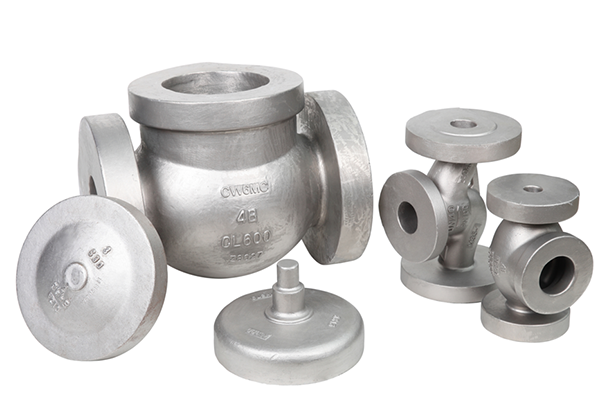
Product Production
Imported, high-speed equipment
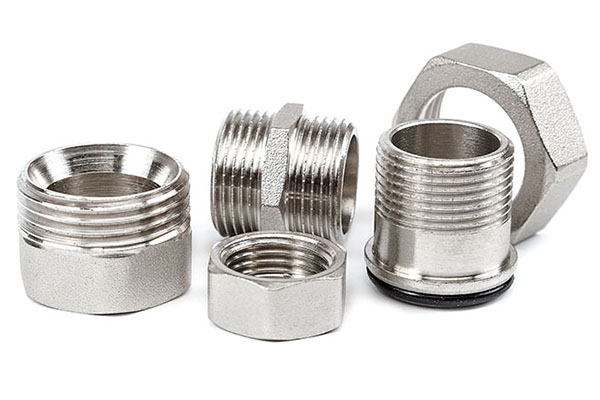
Product Assembly
Incoming materials, inspection and assembly
Model classification of Nickel Metal Parts Materials
Pure nickel series
Ni200/N2: High purity impurity free nickel with excellent corrosion resistance and weldability.
Ni201/N4: A low-carbon version of pure nickel with reduced carbon content to reduce brittleness.
Nickel copper series
NiCu28/NCu28: A nickel alloy containing approximately 28% copper, with oxidation resistance and good mechanical properties.
NiCu44/NCu44: A nickel alloy containing approximately 44% copper, with higher oxidation resistance.
Nickel molybdenum series
NiMo16/N10001: A nickel alloy containing 16% molybdenum, known as "high-temperature sodium", with extremely high oxidation resistance.
Nickel chromium series
NiCr20/N62: Nickel alloy containing 20% chromium, with excellent corrosion resistance and oxidation resistance.
Nickel titanium series
NiTi41/N4113: A nickel alloy containing 41% titanium, with excellent corrosion resistance and high temperature strength.
Machining Process of Nickel Metal Parts
First up, we have cutting. This involves using special tools like high-speed steel, carbide, or ceramic to cut or shape the material. Because nickel alloys are tough and hard, it's crucial to tweak the cutting settings to minimize force and heat during the process.
Next is grinding. For this, we use wheels made from materials like alumina or silicon carbide. During grinding, it's important to pick the right settings—like speed, depth, and pressure—to prevent overheating and damaging the workpiece.
Then there's electric discharge machining (EDM). This method uses electrical sparks to generate heat for processing, perfect for complex shapes that can't be easily handled with traditional methods.
Laser processing is another option. It uses laser beams to heat, melt, or vaporize the material to remove it or change its shape. Laser processing stands out for its precision, efficiency, and minimal heat impact on surrounding areas.
Forging comes into play when we want to reshape and size the material through plastic deformation. Forging not only changes the shape but also boosts the material's strength and improves its microstructure.
Casting involves pouring molten nickel into molds where it cools and solidifies, forming castings.
Lastly, welding joins pieces together by heating or applying pressure until they bond at the atomic level. There are different techniques like arc welding, argon arc welding, and laser welding.
Each of these methods has its own strengths and is used in specific situations. In real production, choosing the right technique and settings is key to ensuring quality and efficiency.
FAQ About Nickel Metal Parts
What are Nickel Parts commonly used for?
Nickel parts are widely used in various industries due to their excellent properties such as high strength, corrosion resistance, and thermal stability. They are often found in electronic connectors, automotive components, aerospace applications, and chemical processing equipment. The ability of nickel to resist tarnishing and maintain its luster makes it ideal for decorative and functional applications alike.
How do you ensure the quality of Nickel Parts during manufacturing?
Ensuring the quality of nickel parts involves several steps, starting with the selection of high-grade raw materials. During the manufacturing process, we employ precise machining techniques and stringent quality control measures. After fabrication, parts undergo rigorous testing for dimensional accuracy, mechanical strength, and surface finish. Additionally, non-destructive testing methods like X-ray inspection and ultrasonic testing are used to detect any internal defects.
Are Nickel Parts resistant to corrosion?
Yes, nickel parts are known for their remarkable corrosion resistance. This is due to the formation of a passive oxide layer on the surface, which protects the metal from further oxidation and environmental factors. Nickel's resistance to corrosion makes it suitable for use in harsh environments, including marine, chemical, and industrial settings. However, the level of resistance can vary depending on the specific alloy composition and the operating conditions.
Can Nickel Parts be customized to specific requirements?
Absolutely! One of the great advantages of nickel parts is their versatility and malleability. We can customize nickel parts to meet specific design requirements, including size, shape, and functionality. Whether you need intricate components for precision engineering or specialized parts for unique applications, our team can work closely with you to develop tailored solutions. This customization capability ensures that the final product meets your exact specifications and performs optimally.
What maintenance is required for Nickel Parts?
Maintenance for nickel parts is relatively straightforward. Regular cleaning with mild soap and water is usually sufficient to keep them in good condition. Avoid using abrasive cleaners or materials that could scratch the surface. For parts exposed to harsh environments, periodic inspection for signs of wear or corrosion is recommended. If any issues are detected, prompt repair or replacement can prevent further damage and ensure continued performance.
Are Nickel Parts cost-effective compared to other metals?
While nickel parts may have a higher upfront cost compared to some other metals, their long-term benefits often make them a cost-effective choice. The durability and resistance to corrosion mean that nickel parts have a longer lifespan, reducing the need for frequent replacements. Additionally, their excellent mechanical properties can enhance the performance and efficiency of the overall system. When considering the total cost of ownership, including maintenance and replacement costs, nickel parts can offer significant savings over time.