Titanium Metal Parts Materials
Titanium is a metal with great features like being lightweight, strong, and resistant to corrosion. It's widely used in areas like aerospace, cars, and medical devices. Depending on its purity and added elements, titanium comes in two main types: pure industrial titanium and titanium alloys.
Pure industrial titanium includes grades TA1, TA2, and TA3. As the content of impurities increases from TA1 to TA3, both the strength and hardness go up too. However, this also means that the material becomes less flexible and tough. Despite this, pure titanium still performs well at very low temperatures, making it perfect for structures that need to withstand cold down to -253°C.
On the other hand, titanium alloys are categorized into three types based on their structure: alpha, beta, and alpha-beta. Alpha titanium alloys contain elements that stabilize the alpha phase, such as aluminum, carbon, oxygen, and nitrogen. They are known for their resistance to creep and ability to stay tough at low temperatures. Beta titanium alloys include elements like molybdenum, niobium, vanadium, and chromium, which stabilize the beta phase. These alloys are strong and can be shaped easily. Alpha-beta titanium alloys have a mix of elements that stabilize both the alpha and beta phases, giving them both high strength and good flexibility.
Titanium Metal Parts Making Service
Be good at product structure optimization and greatly reduce the cost of Titanium Metal Parts Materials
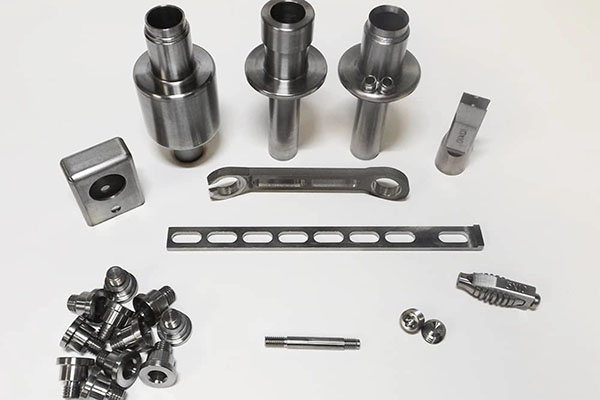
Part Design
Appearance and structural design
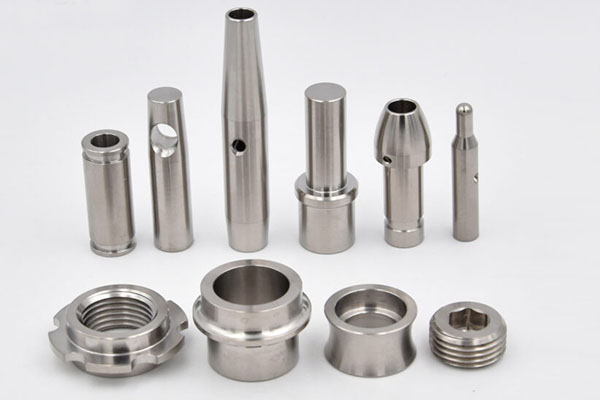
Mold Making
Design, DFM confirmation
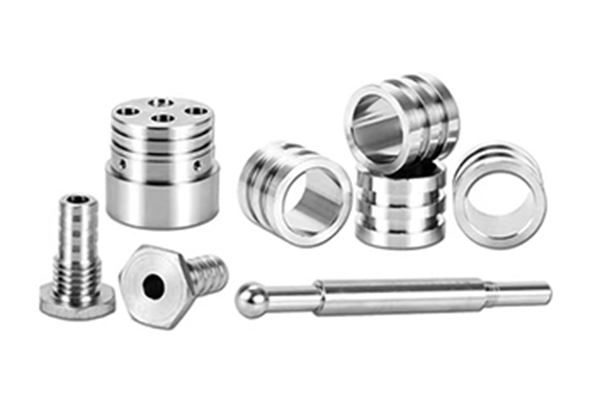
Product Production
Imported, high-speed equipment
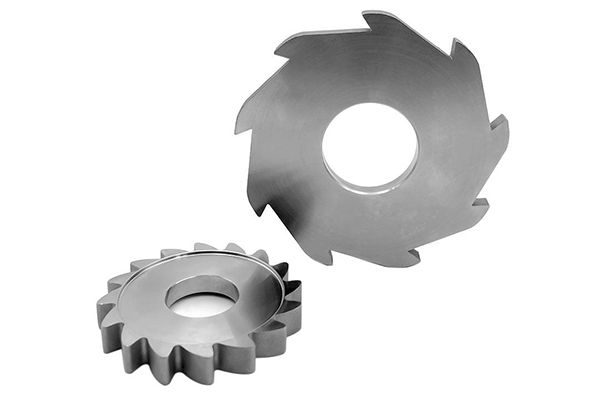
Product Assembly
Incoming materials, inspection and assembly
Model classification of Titanium Metal Parts Materials
A titanium alloy
TA7 (Ti-5Al-2.5Sn): It has good comprehensive mechanical properties and thermal processing performance, mainly used for manufacturing aircraft skins, wall panels, and other aviation compressor discs, blades, and body structural components.
TA9 (Ti-6Al-2Zr-1Mo-1V): With a working temperature of up to 500 ℃ and good thermal stability, it can be used to manufacture parts such as compressor discs and blades for aircraft engines.
TA10 (Ti-6Al-2.5Zr-1Mo-1V): With a working temperature of up to 500 ℃ and good thermal stability, it can be used to manufacture parts such as compressor discs and blades for aircraft engines.
β titanium alloy
TB2 (Ti-10V-2Fe-3Al): It has excellent cold and hot processing properties and can be used for cold forming of sheet metal. It is mainly used for manufacturing fasteners.
TB3 (Ti-10V-8Cr-1Fe-3.5Al): It has excellent resistance to seawater corrosion and high strength, mainly used for manufacturing compressor blades and discs.
α+β titanium alloy
TC4 (Ti-6Al-4V): It is one of the most widely used titanium alloys, accounting for over 50% of the total production of titanium alloys. This alloy has good comprehensive properties and can be used to produce large-sized aviation forgings and parts.
TC6 (Ti-6Al-2Sn-4Zr-2Mo): It has high strength and good toughness, and is commonly used in the manufacturing of aerospace structural components.
TC9 (Ti-3Al-2.5V): It has good weldability and plasticity, and is widely used in the aerospace industry.
TC10 (Ti-6Al-3Sn-2Zr-1Mo-1Nd): It has excellent high-temperature performance and corrosion resistance, and is suitable for manufacturing aviation engine components.
Machining Process of Titanium Metal Parts
Let's break down the various ways titanium materials can be processed into simpler terms:
First off, there's casting. Imagine melting metal in a special way to pour it into molds and make strong shapes. Techniques like vacuum melting or electron beam melting are used here. They help create top-notch parts for many uses.
Next up is forging. This step is about hammering the metal to make it denser and stronger. It's crucial to get the temperature and how much we stretch the metal just right for quality results.
Rolling comes after that. Think of it as flattening a piece of metal through rollers to get it thinner or wider. We have to be careful with how much pressure we use and how fast we go to avoid cracks.
Extruding is another method, where we push the metal through a die to shape it. Controlling the speed and pressure is key to getting the perfect form.
Drawing is similar but focuses on pulling the metal through a die to make wires or tubes. Lubrication and pull strength are important here to prevent breaks.
Then there's stamping, which involves pressing metal sheets into molds to cut or shape them. The force applied and mold gap need careful attention for precise parts.
Machining covers cutting, shaping, and drilling the metal. Since titanium is tough and doesn't conduct heat well, choosing the right tools and settings is vital.
Heat treatment changes the metal's inner structure by heating and cooling it. Methods like annealing or hardening improve strength and durability.
Surface treatment protects the metal from corrosion and wear, making it look good too. Anodizing, plating, or coating are common techniques.
Lastly, 3D printing builds things layer by layer using digital designs. It's great for detailed designs and saves time and money. Special printers handle titanium due to its high melting point and reactivity. This tech even allows for making parts with hollow spaces and complex structures, ideal for aerospace and medical fields.
In summary, titanium's unique traits make it valuable across different industries. As technology advances, its uses will only grow more diverse and widespread.
FAQ About Titanium Metal Parts
What are the primary benefits of using titanium parts?
Titanium parts have gained massive popularity in various industries due to their exceptional properties. First off, they're incredibly strong for their weight, making them ideal for applications where weight savings are crucial but durability is a must. This strength-to-weight ratio is particularly beneficial in aerospace and automotive industries. Plus, titanium boasts fantastic corrosion resistance. It can withstand harsh environments, including seawater, chlorine, and many chemicals, without rusting or deteriorating. This makes titanium perfect for marine applications and chemical processing plants. Lastly, titanium has a high melting point and can handle extreme temperatures, which is why it's often used in jet engines and other high-heat environments.
How are titanium parts typically manufactured?
Manufacturing titanium parts involves several steps, starting with the extraction and refining of titanium from its ore, usually ilmenite or rutile. Once refined, titanium sponge is produced, which is then melted into ingots. These ingots can be further processed into different shapes using methods like forging, rolling, or extrusion. For more complex parts, computer numerical control (CNC) machining is often employed. This process allows for precise shaping and sizing according to detailed specifications. Titanium can also be cast, although this method is less common due to the metal's reactivity at high temperatures.
Are there different grades of titanium, and what do they mean?
Yes, indeed! Titanium comes in several grades, each tailored for specific applications based on their mechanical properties and composition. The most common commercially pure grades are Grade 1 (CP Ti), Grade 2 (CP Ti), Grade 3 (CP Ti), and Grade 4 (CP Ti). These grades differ mainly in their oxygen and iron content; lower levels generally result in better ductility and formability. For instance, Grade 2 is widely used for cryogenic applications and in situations requiring high toughness and formability. On the other hand, Grade 4 offers a balance of strength and workability, making it suitable for a variety of structural components.
What industries commonly use titanium parts?
Titanium parts are highly valued across numerous industries due to their unique combination of properties. The aerospace industry is one of the biggest consumers of titanium because of its high strength-to-weight ratio and ability to withstand extreme temperatures. Aircraft frames, engines, and landing gear frequently incorporate titanium components to improve performance and fuel efficiency. The automotive industry also utilizes titanium for high-performance sports cars and luxury vehicles, seeking to reduce weight and increase horsepower. Even everyday cars benefit from titanium in exhaust systems and engine parts for better durability and performance.
Can titanium parts be recycled, and how is the recycling process done?
Yes, titanium parts can indeed be recycled, and the recycling process is both environmentally friendly and cost-effective. Recycling titanium requires collecting scrap titanium from manufacturing processes or end-of-life products. This scrap is then cleaned to remove any contaminants such as paint, coatings, or other materials. Once clean, the titanium is melted down in a furnace at very high temperatures to produce titanium ingots or sponge. This recycled material retains all the desirable properties of new titanium, making it just as valuable for manufacturing new parts.
How do you maintain and care for titanium parts to ensure longevity?
Maintaining titanium parts involves regular cleaning and inspection to prevent dirt buildup and identify any potential issues early on. For general cleaning, simply use mild soap and water. Avoid abrasive cleaners or materials that could scratch the surface. Inspecting the parts periodically for signs of wear or damage is crucial, especially in high-stress applications. If you notice any surface scratches or minor damages, it’s advisable to address them promptly to prevent further deterioration.