Introduction
What is Molding Process?
The Molding Process is a fundamental manufacturing technique that involves shaping materials by heating them and injecting or pressing them into a mold. Once the material cools and solidifies within the mold, it takes on the desired shape, which can range from simple geometric forms to highly complex and detailed structures. This process is widely used across various industries due to its versatility and efficiency in producing large quantities of identical parts with consistent quality. For example, in plastic manufacturing, molten plastic is injected into molds to create everything from small toy components to large automotive interior parts. The molding process can work with a variety of materials, including plastics, metals, ceramics, and composites, making it an essential part of modern manufacturing.
Importance in Manufacturing
The molding process plays a pivotal role in the manufacturing industry, serving as the backbone for the production of countless products we use in our daily lives.
- Automotive Industry: In car manufacturing, molding is used to create a wide range of components. For instance, bumpers, dashboards, and interior trim pieces are often made through injection molding of plastics. These parts not only need to be lightweight to improve fuel efficiency but also durable enough to withstand the rigors of daily use. According to industry reports, around 50% of the total volume of a modern vehicle consists of plastic components made through molding processes, highlighting its significance in this sector.
- Electronics Industry: Molding is crucial for producing electronic device housings, circuit board components, and connectors. For example, the sleek casings of smartphones and tablets are typically made through precision injection molding, ensuring a perfect fit for internal components while providing protection. In the production of integrated circuits, plastic molding encapsulates the delicate electronic components, safeguarding them from environmental factors like moisture and dust.
- Medical Industry: The medical field relies on molding for manufacturing various devices such as syringes, prosthetics, and diagnostic equipment components. High - precision molding techniques are used to create medical implants that must meet strict biocompatibility and dimensional accuracy standards. For example, 3D printing, which is a type of additive molding process, is increasingly being used to create patient - specific prosthetics, offering a more customized and comfortable fit for patients.
Types of Molding Process
There are several types of molding processes, each with its own characteristics, advantages, and ideal applications. Understanding these different methods is crucial for manufacturers to select the most suitable process for their specific product requirements.
Injection Molding
- Working Principle: Injection molding is a widely used manufacturing process. First, plastic pellets are fed into a heated barrel. As the pellets move through the barrel, they are melted by the heat and the mechanical action of a screw. Once fully molten, the plastic is injected at high pressure into a closed mold cavity. The mold is typically made of two halves, which are clamped tightly together during the injection process. After the mold is filled, the plastic is cooled and solidified, taking on the shape of the mold cavity. Finally, the mold is opened, and the finished part is ejected.
- Applicable Materials: This process is highly suitable for a wide range of thermoplastic materials such as polyethylene (PE), polypropylene (PP), polystyrene (PS), and polycarbonate (PC). These materials can be easily melted and reshaped, making them perfect for injection molding. For example, in the production of water bottles, high - density polyethylene (HDPE) is commonly used due to its strength and chemical resistance.
- Advantages: Injection molding offers high precision, with the ability to produce parts with tight tolerances, often within ±0.001 inches. It also has a high production efficiency, capable of producing large quantities of parts in a short time. For instance, a modern injection molding machine can produce hundreds or even thousands of parts per hour, depending on the complexity of the part.
- Typical Applications: It is extensively used in the production of plastic toys, where the high precision allows for the creation of detailed and intricate designs. Electronics housings, such as those for smartphones and tablets, are also commonly made through injection molding. These housings need to be precisely shaped to fit all the internal components while providing protection and a sleek appearance.
Compression Molding
- Operating Process: In compression molding, a pre - measured amount of raw material, usually in the form of a solid or semi - solid, is placed directly into a heated mold cavity. The mold is then closed, and pressure is applied. As the material is compressed and heated, it softens and flows to fill the entire mold cavity. After a certain period of time, the material cures and hardens, taking the shape of the mold. Finally, the mold is opened, and the finished product is removed.
- Suitable Materials: Compression molding is well - suited for thermosetting plastics like phenolic, epoxy, and urea - formaldehyde resins, as well as rubber. These materials, once cured under heat and pressure, cannot be remelted or reshaped. For example, phenolic resins are often used in the production of electrical insulators due to their excellent heat and electrical resistance properties.
- Strengths: This process is cost - effective, especially for large - scale production runs, as it requires less complex equipment compared to some other molding methods. It is also ideal for manufacturing large - sized products, such as automotive interior components like dashboards and seat backs, which can be produced in one piece with relative ease.
- Common Applications: In the automotive industry, it is used for manufacturing various interior parts, where cost - effectiveness and large - scale production are important factors. In the electrical industry, compression molding is used to make electrical enclosures and switch components, taking advantage of the heat and electrical resistance properties of the materials.
Blow Molding
- Steps: Blow molding starts with creating a parison, which is a tube - like piece of molten plastic. This parison is then placed inside a mold cavity. Compressed air is blown into the parison, causing it to expand and conform to the shape of the mold cavity. As the plastic cools and solidifies, the final product, which is typically a hollow object, is formed. The mold is opened, and the finished product is removed.
- Applicable Materials: The process mainly uses thermoplastic materials such as polyethylene (PE), polyvinyl chloride (PVC), and polypropylene (PP). These materials can be easily blown into various shapes while maintaining their structural integrity. For example, low - density polyethylene (LDPE) is commonly used for making plastic bags and flexible containers due to its flexibility and ease of processing.
- Advantages: Its main advantage is the ability to produce hollow products efficiently, such as plastic bottles and containers. The process allows for a high production rate, and the products can be made with a relatively thin wall thickness, reducing material usage and cost.
- Typical Applications: Plastic bottles for beverages, household chemicals, and personal care products are the most common examples. Fuel tanks for vehicles are also often made through blow molding, as it can create the complex shapes required while ensuring the necessary strength and durability.
Comparison Table
The following table provides a comparison of the three molding processes in terms of cost, precision, production efficiency, applicable materials, and product types:
Molding Process | Cost | Precision | Production Efficiency | Applicable Materials | Product Types |
Injection Molding | Moderate to high initial tooling cost, low per - unit cost for high - volume production | High (±0.001 inches) | High (hundreds - thousands of parts per hour) | Thermoplastics (PE, PP, PS, PC, etc.) | Small to medium - sized, complex - shaped parts like plastic toys, electronics housings |
Compression Molding | Low initial tooling cost, low per - unit cost for large - scale production | Moderate (±0.01 - 0.05 inches) | Moderate (dependent on curing time) | Thermosetting plastics (phenolic, epoxy, urea - formaldehyde), rubber | Large - sized parts like automotive interior components, electrical enclosures |
Blow Molding | Moderate tooling cost, low per - unit cost for high - volume production | Moderate (±0.01 - 0.03 inches) | High (high production rate for hollow products) | Thermoplastics (PE, PVC, PP) | Hollow products like plastic bottles, fuel tanks |
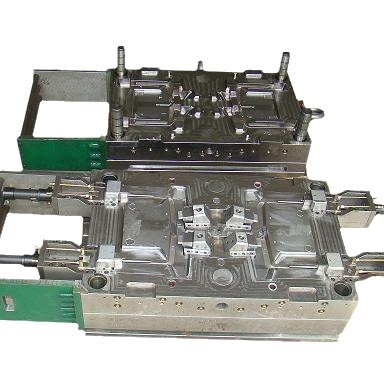
Key Factors in Molding Process
Material Selection
- Common Molding Materials: There is a wide variety of materials used in the molding process. In plastic molding, common thermoplastics include polyethylene (PE), polypropylene (PP), polyvinyl chloride (PVC), and polycarbonate (PC). For example, PE is known for its excellent chemical resistance and low cost, making it suitable for applications like packaging and household items. PP has good heat resistance and is often used in automotive parts and food containers. PVC is commonly used in construction for pipes and fittings due to its durability and low cost. In metal molding, aluminum, copper, and steel are frequently utilized. Aluminum is favored for its lightweight nature and good thermal conductivity, often used in aerospace and automotive components where weight reduction is crucial.
- Impact of Material Properties: Material properties such as fluidity and shrinkage rate have a significant impact on the molding process and product quality. Fluidity affects how easily the material can fill the mold cavity. For instance, materials with high fluidity like some grades of low - density polyethylene can quickly and evenly fill complex mold cavities, reducing the risk of incomplete filling. However, if the fluidity is too high, it may lead to issues such as flash (excess material squeezing out between the mold halves). On the other hand, materials with low fluidity require higher injection pressures or longer compression times to ensure proper filling. Shrinkage rate is another critical factor. Different materials have different shrinkage rates; for example, crystalline plastics like polyethylene and polypropylene generally have higher shrinkage rates compared to amorphous plastics such as polystyrene. A high - shrinkage - rate material can cause dimensional inaccuracies in the final product if not properly accounted for. If the shrinkage is uneven within the product, it can lead to warping or internal stresses, affecting the product's performance and appearance.
- Material Selection Advice: When selecting a material for a molding process, several factors need to be considered. First, the product's functional requirements should be determined. If the product needs to be heat - resistant, materials like polycarbonate or certain grades of engineering plastics should be considered. For products that require high strength, metals such as steel or reinforced plastics can be chosen. Second, the manufacturing process also influences material selection. Some materials are more suitable for injection molding, while others are better for compression or blow molding. Cost is another crucial aspect. If the product is for mass - market consumption and cost - sensitive, materials like polyethylene or polypropylene may be preferred due to their relatively low cost. Additionally, environmental considerations such as recyclability and biodegradability are becoming increasingly important, and materials like biodegradable plastics can be selected for eco - friendly applications.
Mold Design
- Key Points of Mold Design:
- Cavity Design: The cavity design of the mold is the core part that determines the shape of the final product. It must accurately replicate the desired product shape with high precision. For complex - shaped products, the cavity may require intricate details and undercuts. For example, in the production of a plastic toy with multiple small protrusions and cavities, the mold cavity needs to be designed with extreme precision to ensure that these details are accurately reproduced in the final product.
- Cooling System: An efficient cooling system is essential for the molding process. It helps to reduce the cooling time of the material in the mold, thereby increasing the production efficiency. Cooling channels are usually incorporated into the mold structure. These channels are designed to circulate a cooling medium, such as water, around the mold cavity. The layout of the cooling channels should be carefully planned to ensure uniform cooling of the product. Uneven cooling can lead to warping and internal stress in the product. For example, in the injection molding of a large - sized plastic panel, if the cooling system is not designed properly, one side of the panel may cool faster than the other, causing the panel to warp.
- Demolding Mechanism: The demolding mechanism is responsible for removing the finished product from the mold after the molding process is complete. There are various types of demolding mechanisms, such as ejector pins, ejector sleeves, and stripper plates. Ejector pins are the most commonly used. They are small pins that are placed at strategic locations in the mold. When the mold opens, the ejector pins push the product out of the mold cavity. The design of the demolding mechanism should consider factors such as the shape and size of the product, as well as the material properties. For products with complex shapes or thin - walled structures, a more sophisticated demolding mechanism may be required to prevent damage to the product during demolding.
- Importance of Design for Molding Efficiency and Product Quality: A well - designed mold can significantly improve the molding efficiency and product quality. A properly designed cavity ensures that the material fills the mold evenly and accurately, reducing the occurrence of defects such as voids and short - shots (incomplete filling). An efficient cooling system shortens the cycle time of the molding process, allowing for higher production volumes. For example, in a high - volume production of plastic bottle caps, an optimized cooling system can reduce the cooling time of each cap from 10 seconds to 5 seconds, doubling the production output per hour. The demolding mechanism, when designed correctly, ensures that the product can be removed from the mold smoothly without any damage. This is crucial for maintaining the integrity of the product and reducing the number of defective products. If the demolding process is not smooth, it can cause scratches, dents, or even breakage of the product, leading to increased waste and production costs.
Process Parameters
- Influence of Process Parameters:
- Temperature: Temperature plays a crucial role in the molding process. In plastic injection molding, for example, the barrel temperature determines the melting state of the plastic pellets. If the temperature is too low, the plastic may not melt completely, resulting in uneven flow and poor filling of the mold cavity. This can lead to products with voids or a rough surface finish. On the other hand, if the temperature is too high, the plastic may degrade, losing its mechanical properties and causing discoloration or charring of the product. In metal casting, the melting temperature of the metal must be precisely controlled to ensure proper fluidity for filling the mold.
- Pressure: Injection pressure in injection molding and compression pressure in compression molding are key factors. In injection molding, the injection pressure is used to force the molten material into the mold cavity. If the pressure is too low, the mold may not be filled completely, resulting in short - shot products. If the pressure is too high, it can cause flash, excessive stress on the mold, and even damage to the product due to over - packing. In compression molding, the right amount of pressure is needed to ensure that the material is evenly distributed in the mold and achieves the desired density and shape.
- Time: The time parameters, including injection time, cooling time, and curing time (for thermosetting materials), are also critical. The injection time should be long enough to fill the mold completely but not too long to avoid over - injection. The cooling time determines how long the product needs to stay in the mold to solidify. If the cooling time is too short, the product may not be fully solidified, leading to deformation during demolding. For thermosetting materials, the curing time is crucial as it determines when the material transforms from a liquid or semi - liquid state to a solid, cross - linked state.
- Principles and Methods of Parameter Adjustment: When adjusting process parameters, the following principles can be followed. First, start with the recommended parameter values provided by the material supplier or based on previous experience with similar materials and products. Then, make small incremental changes to one parameter at a time while keeping other parameters constant. For example, if adjusting the injection pressure in injection molding, increase the pressure by a small percentage, such as 5 - 10%, and observe the effect on the product quality. If the product shows signs of improvement, continue to make small adjustments in the same direction. If there are negative effects, such as increased flash or warping, reverse the adjustment. For temperature adjustment, make changes in small increments, usually around 5 - 10°C, and monitor the product's appearance, dimensional accuracy, and mechanical properties. In terms of time adjustment, increase or decrease the time by a few seconds and evaluate the impact on the product. Additionally, modern molding processes often use sensors and control systems to monitor and adjust parameters in real - time, ensuring more precise control and consistent product quality.
Yigu Technology's Perspective
As a non - standard plastic metal products custom Supplier, Yigu Technology deeply understands the critical role of the molding process in manufacturing. In our experience, the molding process is not just a production method but the cornerstone of creating high - quality, customized products.
When dealing with non - standard products, material selection becomes even more crucial. We carefully assess the unique requirements of each project, considering factors such as the product's end - use environment, mechanical properties needed, and cost - effectiveness. For example, when manufacturing custom - designed plastic components for a high - precision electronic device, we might choose a special grade of polycarbonate with excellent electrical insulation and dimensional stability.
Mold design is also a focus area for us. We invest in advanced CAD/CAM technologies to create molds that are not only precise but also optimized for the specific non - standard shapes. Our team of engineers pays close attention to details like cavity design, cooling system layout, and demolding mechanisms to ensure smooth production and high - quality end - products.
In terms of process parameters, we use a data - driven approach. Through continuous monitoring and analysis, we fine - tune temperature, pressure, and time settings to achieve the best results for each unique molding job. This has allowed us to produce non - standard plastic and metal products with consistent quality and high efficiency, meeting the diverse needs of our customers.
FAQ
What is the most suitable molding process for small - scale production?
For small - scale production, compression molding might be more suitable. The mold cost is relatively low, and the equipment required is less complex. It doesn't need a large - scale investment like injection molding, which often has high initial tooling costs. With compression molding, manufacturers can start production with a smaller budget, making it an ideal choice for small - scale production runs.
How to reduce the cost of the molding process?
- Material Selection: Choose cost - effective materials that meet the product's performance requirements. Consider using recycled or regrind materials when possible, as they are usually cheaper. For example, in some applications, recycled plastics can be used without sacrificing much on quality.
- Mold Design: Optimize the mold design to reduce the number of parts and simplify the structure. A well - designed mold can also improve production efficiency, reducing the overall cost. For instance, proper cooling system design can shorten the cooling time and increase the production rate.
- Production Efficiency: Improve production efficiency by reducing cycle times. This can be achieved by optimizing process parameters, such as adjusting temperature, pressure, and time settings. Using automation in the production process can also reduce labor costs and increase productivity.
Can different materials be used in the same molding process?
In some molding processes, it is possible to use different materials. For example, in injection molding, multi - material injection can be used to combine two or more different plastics in one product. However, it's important to consider the compatibility of the materials. If the materials are not compatible, it can lead to issues such as poor adhesion between the materials. Also, the process parameters may need to be adjusted to accommodate the different material properties.
Conclusion
Mold manufacturing is a manufacturing process that can produce components of various shapes, sizes, and materials. According to different mold manufacturing processes, we need to consider different advantages and disadvantages. Injection molding, blow molding, compression molding, and rotary molding are some of the most common mold manufacturing processes, each with its own applications and characteristics. By understanding the basic knowledge of these processes, you can choose the most suitable mold manufacturing process for your project and optimize your design to accommodate mold manufacturing.