Serviços de peças de estampagem de metal
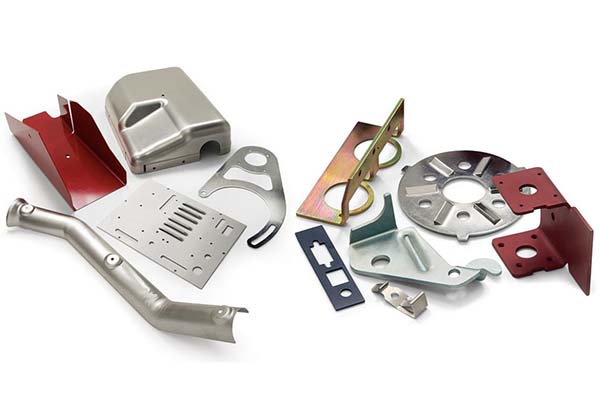
What Is Metal Stamping?
Defining Metal Stamping: Metal stamping is a versatile manufacturing process that uses mechanical presses and custom tools (molds/dies) to shape flat metal sheets into precise components through plastic deformation or material separation. By applying controlled force, we transform raw materials into complex parts with tight tolerances (±0.05mm typical) and consistent quality, ideal for high-volume production across industries.
Types of Metal Stamping Processes
Core Process Categories
Process Category | Process Characteristics | Common Operations | Typical Applications |
Separation | Cut or separate material along defined contours. | Blanking/Punching, Shearing, Trimming | Automotive part blanks, electronic connector terminals |
Forming | Deform material without separation to create 3D shapes. | Bending, Drawing, Flanging, Bulging | Appliance casings, aerospace structural components, medical device brackets |
Advanced Stamping Techniques
- Progressive Die Stamping: This technique automates multi - step processes (such as punching, bending, and embossing) in a single press. With a high production rate of up to 500 parts per minute, it is highly efficient for high - volume production. For example, in the production of small metal components for electronics, progressive die stamping can complete multiple operations in one continuous process, reducing production time and cost.
- Fine Blanking: It produces burr - free, high - precision parts with a tolerance of ±0.02mm and smooth sheared edges. This makes it critical for manufacturing components in the aerospace and medical industries, where precision is of utmost importance. Components like aircraft engine parts and surgical instruments often require the high - precision manufacturing capabilities of fine blanking.
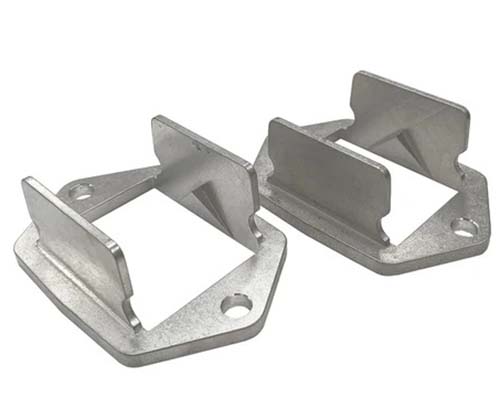
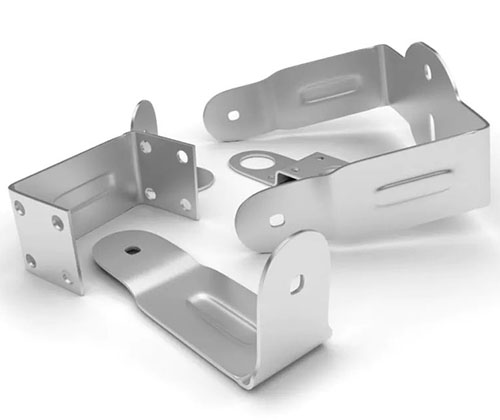
Material Expertise: Selecting the Right Metal
Common Stamping Materials & Properties
Material | Key Mechanical Properties | Key Advantages | Typical Applications |
Cold - Rolled Aço | Tensile strength 300 - 600MPa, good plasticity | Low cost, easy to form | Automotive chassis parts, architectural hardware, mechanical structural parts |
Tensile strength 500 - 1000MPa, corrosion - resistant, high - temperature resistant | Smooth surface, rust - resistant | Kitchen utensils, medical devices, food equipment | |
Aluminum Alloy | Density 2.7g/cm³, good thermal conductivity, tensile strength 150 - 350MPa | Lightweight, easy for surface treatment | Electronic heat sinks, automotive lightweight components, aerospace parts |
Conductivity ≥90% IACS, tensile strength 200 - 400MPa | Excellent electrical conductivity, easy to form | Electrical connectors, heat - dissipating components, decorative parts |
Surface Treatments: Enhancing Function and Aesthetics
Comprehensive Finishing Options
Treatment Method | Process Description | Key Performance Indicators | Typical Applications |
Electroplating | Automotive decorative parts, electronic components, hardware accessories | ||
Powder Coating | Spraying electrostatic powder and then curing at high - temperature to form a wear - resistant and weather - resistant coating. | Coating thickness 60 - 100μm, impact strength ≥50kg·cm | Appliance casings, outdoor equipment, industrial equipment |
Anodizing | Generating an oxide film on the aluminum surface to enhance hardness and corrosion resistance. | Oxide film thickness 5 - 25μm, hardness HV 300+ | Electronic enclosures, aerospace aluminum components, decorative parts |
Electrophoretic Coating | Electrophoretic deposition of water - soluble coatings to achieve a uniform anti - corrosion coating. | Film thickness 15 - 25μm, salt spray resistance ≥1200 hours | Automotive chassis parts, metal furniture, construction machinery components |
Diverse Applications Across Industries
Industry-Leading Solutions
Industry | Typical Components | Material & Performance Highlights |
Automóvel | Body structural parts, engine brackets, battery trays | Body parts: High - strength steel with tensile strength ≥350MPa for safety. Battery trays: Aluminum alloy for lightweight design, achieving over 30% weight reduction |
Electronics & Appliances | Smartphone casings, refrigerator liners, heat dissipation modules | Smartphone casings: Stainless steel or aluminum alloy with surface roughness Ra ≤0.8μm for a sleek look. Heat dissipation modules: Copper or aluminum alloys for excellent thermal conductivity |
Aerospace | Titânio alloy wing ribs, carbon fiber - metal composite sandwich structures | Titânio alloy wing ribs: High fatigue strength (≥150MPa) for long - term reliability. Carbon fiber - metal composite sandwich structures: Precision blanking for high - precision forming, with dimensional accuracy of ±0.03mm |
Medical Devices | Stainless steel surgical instruments, aluminum medical trays | Stainless steel surgical instruments: Passivated to meet ISO 13485 standards for biocompatibility. Aluminum medical trays: Anodized with biocompatibility certification |
Why Yigu Technology for Metal Stamping?
When choosing a metal stamping partner, Yigu Technology stands out for our technical prowess and customer - centric approach. Here's why we are the ideal choice for your metal stamping needs.
Unmatched Technical Advantages
- Precision Tooling: Our team of engineers, with over 20 years of combined experience, uses advanced CAD/CAM software like AutoCAD and UG to design and develop custom - made stamping dies. Our dies are built to last, with a lifespan of over 500,000 cycles and a defect rate of less than 0.5%, ensuring long - term cost - effectiveness.
- State - of - the - Art Equipment: Equipped with a range of stamping presses from 50 to 2000 tons, fully - automated progressive die production lines (capable of producing up to 300 parts per minute), and 3D vision inspection systems (with an accuracy of ±0.01mm), we can handle projects of any scale and complexity.
- End - to - End Quality Control: Certified to ISO 9001:2015, we conduct over 10 quality checks on each production batch. Our quality control measures include CMM (Coordinate Measuring Machine) dimensional inspections, tensile strength tests, and salt - spray corrosion tests, providing you with a detailed and traceable quality control report.
Customer - Centric Benefits
Benefits | Details | Impact on Your Project |
Fast Prototyping & Low MOQ | 7 - 15 days for sample delivery, with a minimum order quantity (MOQ) of 500 pieces | Significantly reduces product development time and trial - and - error costs |
Cost - Efficiency | 20% lower die costs than the industry average and a 95% material utilization rate (through optimized nesting) | Results in a 15% - 25% cost reduction per unit during mass production |
Flexibilidade de conceção | Accommodates sheet thickness from 0.2mm - 6mm and complex surface forming (minimum bending radius of R0.5mm) | Meets diverse design requirements without the need for secondary processing |
Metal Stamping FAQs: Your Questions Answered
We accept MOQs as low as 500 pieces for prototyping and scale to 1,000,000+ pieces for mass production. This flexibility allows startups and large - scale manufacturers alike to benefit from our services. Whether you're testing a new product concept or ramping up production for a high - demand item, we've got you covered.
Standard lead time is 25 - 35 days for simple dies, with expedited options (15 days) available for urgent projects. Our experienced die - making team uses advanced CAD/CAM technology to streamline the design and manufacturing process, ensuring you get your die as quickly as possible without sacrificing quality.
Our expertise focuses on metal sheets (steel, aluminum, copper, etc.), but we can advise on composite material solutions. While our core strength lies in metal stamping, we understand the growing need for composite materials in some applications. Our engineers can provide guidance on how to incorporate non - metal elements into your design, such as using metal - reinforced plastics or other composite structures.
We achieve ±0.05mm for most parts and ±0.02mm for precision components using fine blanking. Our state - of - the - art equipment, including high - precision stamping presses and 3D vision inspection systems, enables us to maintain tight tolerances. This level of accuracy ensures that your parts fit together perfectly, reducing the need for costly rework and ensuring the overall quality of your product.
Yes, every order includes a mill certificate and QC report verifying material composition and mechanical properties. We source our materials from trusted suppliers and conduct rigorous in - house testing. This ensures that the metal used in your stamping project meets all the required standards, giving you peace of mind about the quality and integrity of your components.
We maintain a 20% production buffer and use real - time order tracking, achieving a 98% on - time delivery rate in 2024. Our efficient production planning and advanced tracking systems allow us to closely monitor the progress of your order. In the rare event of unforeseen delays, we'll communicate with you promptly and proactively find solutions to minimize the impact on your project timeline.
Our engineers provide DFM (Design for Manufacturing) feedback to reduce costs and improve manufacturability at no extra charge. We believe in collaborating with our clients from the early design stages. By leveraging our expertise in metal stamping, we can suggest design changes that will make your product easier and more cost - effective to manufacture, without compromising on functionality or aesthetics.
Powder coating and electrophoretic coating are ideal, offering salt spray resistance exceeding 1,000 hours. These coatings provide excellent protection against corrosion and weathering, making them perfect for outdoor applications such as automotive exteriors, outdoor furniture, and industrial equipment.
Yes, we are IATF 16949 certified, ensuring traceability and quality for automotive - grade components. This certification demonstrates our commitment to meeting the strict quality and safety requirements of the automotive industry. From design to production, every step of our process is carefully monitored and documented to ensure that your automotive parts meet or exceed industry standards.
We manage global logistics, including export packaging (fumigated wooden crates), customs documentation, and DDP/DAP Incoterms. Whether your project requires shipping to a neighboring country or across the globe, we have the expertise and resources to handle all aspects of international shipping. Our team will work with you to ensure that your parts are delivered safely and on time, no matter where in the world they need to go.
Contact Yigu Technology today to discuss how our metal stamping expertise can elevate your project—from prototype to mass production, we deliver precision, reliability, and innovation at every step.