Injection moulding is a manufacturing technique that's super popular in lots of different industries for making complex, high-quality parts in big numbers. It all starts by melting down thermoplastic or thermosetting polymers and then shooting them into a mold. After that, the melted stuff cools down and hardens to become the shape we want.
we're going to dive deep into the injection moulding process. We'll cover everything from its history to the equipment used, the materials involved, the steps it takes, why it's so great, and any limitations it might have. So, let's get started!
History of Injection Moulding Process:
John Wesley Hyatt came up with the idea for injection molding back in 1868, aiming to make billiard balls. But let's be real, those early machines? They were pretty much all manual and not very efficient. Fast forward to the 1940s, and things got a whole lot better. That's when they started using hydraulic systems and automation, making everything smoother and faster. Since then, injection molding has been on a roll, getting better and better. Now, we can whip up tons of high-quality parts with all sorts of intricate designs.
Equipment Used in Injection Moulding:
The injection moulding process involves using several pieces of equipment, like an injection moulding machine, a mould, and some auxiliary gear. The injection moulding machine is pretty big and has a screw, barrel, heater, and hydraulic system inside. The screw helps melt the polymer and pushes it into the mould. The barrel and heater keep everything at the right temperature and pressure. The hydraulic system clamps the mould shut and manages the injection process.
The mould itself is made up of two halves: one with the cavity and the other with the core. Together, they create the shape you want. There are also some extra pieces of equipment, like a material hopper, conveyor belt, and cooling system. These help move the parts around and cool them down after they've been injected.
Types of Polymers Used in Injection Moulding:
There are two main types of polymers used in injection moulding: thermoplastic and thermosetting. Thermoplastic polymers are the most commonly used type and can be melted and reshaped multiple times. Examples of thermoplastic polymers include polyethylene, polypropylene, polystyrene, and polyvinyl chloride. Thermosetting polymers, on the other hand, can only be heated and shaped once and then become rigid and cannot be reshaped. Examples of thermosetting polymers include epoxy, phenolic, and melamine.
Injection Moulding Process Steps:
The injection moulding process involves several steps, including material preparation, mould preparation, injection, cooling, and ejection. The following is a detailed description of each step:
Material Preparation: The polymer is loaded into the material hopper, where it is heated and melted. The material is then transported to the injection moulding machine.
Mould Preparation: The mould is clamped and prepared for injection. The cavity and core are lubricated and cooled, and the mould is preheated to the proper temperature.
Injection: The screw moves forward, forcing the melted polymer into the mould cavity. The polymer fills the cavity and solidifies, forming the desired shape.
Cooling: The mould is cooled to a temperature below the melting point of the polymer, allowing the part to solidify and harden.
Ejection: The mould is opened, and the part is ejected from the mould using ejector pins.
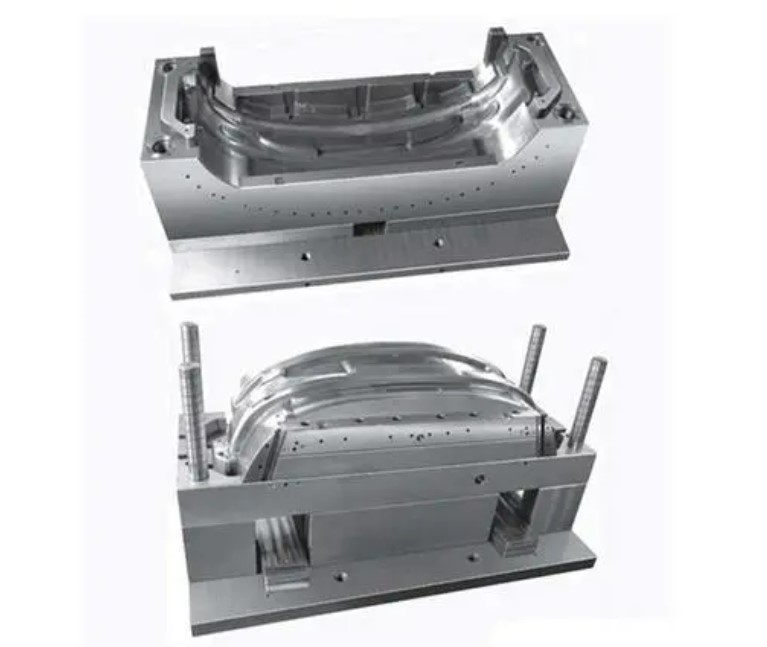
Advantages of Injection Moulding:
Injection moulding offers several advantages over other manufacturing processes, including:
- High Efficiency: Injection moulding is a highly efficient process that can produce high-quality parts in large quantities at a low cost per part. This is because the process is highly automated and can run continuously without much human intervention.
- Design Flexibility: Injection moulding offers design flexibility, allowing for the production of parts with complex geometries, precise details, and tight tolerances. This is because the mould can be designed to match the exact specifications of the desired part.
- Material Versatility: Injection moulding can be used with a wide range of thermoplastic and thermosetting polymers, allowing for the production of parts with a variety of properties, including strength, flexibility, and durability.
- Minimal Waste: Injection moulding generates minimal waste because the excess material can be melted and reused, reducing the overall material costs and environmental impact.
- Consistency and Reproducibility: Injection moulding offers high consistency and reproducibility, ensuring that each part produced is of the same high quality and meets the exact specifications of the design.
Limitations of Injection Moulding:
While injection moulding offers many advantages, there are also some limitations to the process, including:
- High Initial Costs: Injection moulding requires a significant initial investment in equipment and tooling, making it less viable for small-scale production runs.
- Design Constraints: Injection moulding requires careful design considerations to avoid problems such as sink marks, warpage, and air pockets. This can limit the design possibilities and add complexity to the production process.
- Material Selection: Injection moulding requires the use of specific types of polymers that can be melted and injected into the mould. This can limit the selection of materials based on the desired properties of the part.
- Lead Times: The design, manufacturing, and testing of the mould can take several weeks or even months, leading to longer lead times for production runs.
Conclusion:
Injection moulding is a game-changer in manufacturing, making it easier to produce complex and high-quality parts. This process involves melting thermoplastic or thermosetting polymers and injecting them into a mould. Once the material cools and solidifies, it forms the desired shape.
One of the biggest advantages of injection moulding is its design flexibility. You can create almost any shape you need. It also works with a wide variety of materials, giving you plenty of options. Plus, the results are highly consistent, which means each part is pretty much the same as the last one.
However, there are some downsides to consider. For starters, the initial costs can be quite high. There are also some design limitations; not every shape or size is possible. And if you need changes quickly, you might find the lead times a bit long.
Despite these drawbacks, injection moulding has been a huge boon for the manufacturing industry. It's helped make high-quality parts more accessible and efficient to produce. Looking ahead, this process will undoubtedly remain crucial in manufacturing high-quality parts.