Moldagem por injeção para peças de eletrodomésticos.
Injection molds for household appliances are essential professional tools for producing various types of household appliances. These mold designs are used to manufacture high-quality and precise components, which are crucial for the normal operation of household appliances. By using injection molding technology, manufacturers can quickly and efficiently mass produce parts, making it an ideal process for producing home appliance components.
Many household appliances such as refrigerators, washing machines, dishwashers, and air conditioners use injection molded components. Through this process, various components can be produced, including compressor parts, water pumps, fan blades, and door handles.
One major advantage of using injection molds in the production of household appliances is the ability to produce parts of consistent and precise quality. Using computer-aided design (CAD) and computer-aided manufacturing (CAM) software to ensure the precise production of molds, thereby producing parts that meet specification requirements. This precision also ensures that each component can be assembled correctly, allowing the equipment to operate normally.
Another advantage is that injection molds can produce parts quickly and efficiently. The injection molding process is highly automated and can produce a large number of parts in a short amount of time. In the home appliance industry, this speed is particularly crucial as manufacturers need to meet high demand while maintaining low production costs.
In addition, injection molds are highly suitable for manufacturing parts with complex geometric shapes, and the flexibility of this design allows manufacturers to produce innovative home appliance designs that are both aesthetically pleasing and practical.
Finally, household appliance parts produced using injection molds are durable and long-lasting. The materials selected for injection molding are chosen for their strength, durability, and wear resistance, ensuring that household appliance components can withstand the test of daily use.
In short, injection molds for household appliances are key tools for producing various household appliances. With the help of injection molding technology, manufacturers can quickly and efficiently produce high-quality, precise, and durable parts, making them an ideal choice for the home appliance industry. With the continuous advancement of injection molding technology, manufacturers will continue to rely on this process to produce more innovative and high-quality home appliance components.
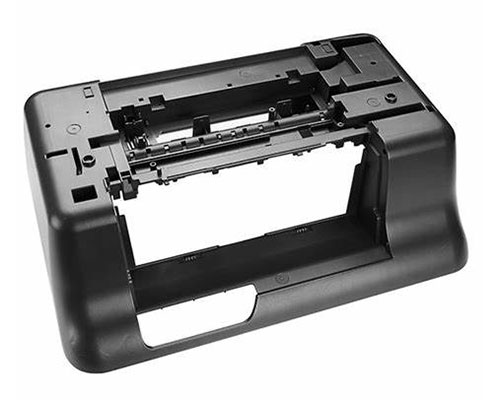
Molde para Peças de Eletrodomésticos
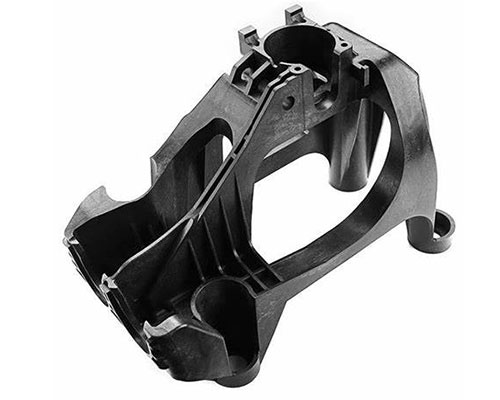
Molde para Peças de Eletrodomésticos
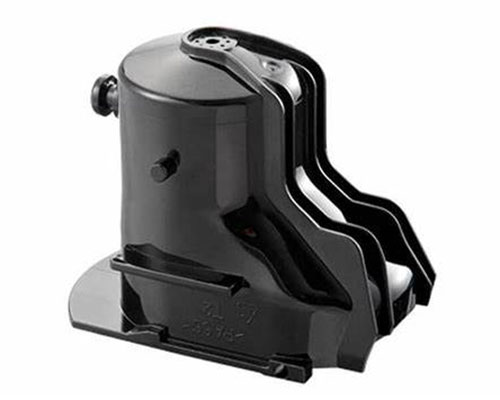
Molde para Peças de Eletrodomésticos
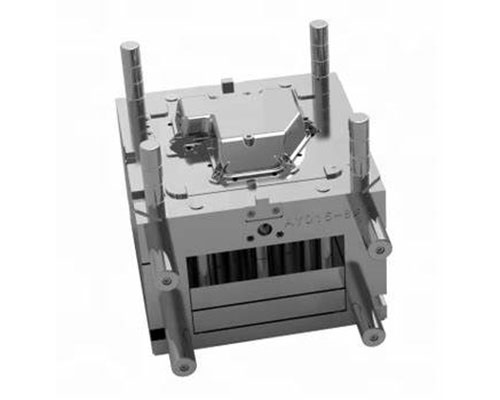
Molde para Peças de Eletrodomésticos
Fabricação de moldes para peças de eletrodomésticos, serviço de moldagem por injeção de plástico.
Be good at product structure optimization and greatly reduce the cost of mold making injection molding
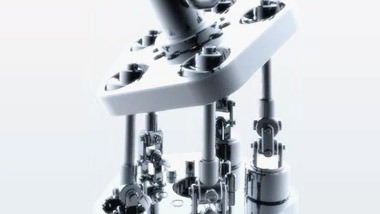
Mould Design
Design Estético e Estrutural
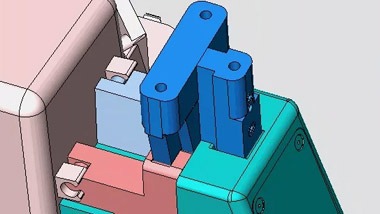
Fabricação de moldes
Design, Confirmação de Facilidade de Manufatura
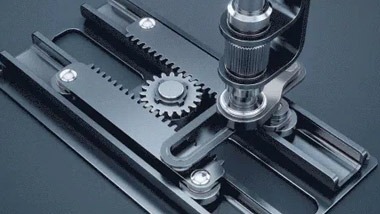
Produção de Produto
Equipamento de Alta Velocidade Importado
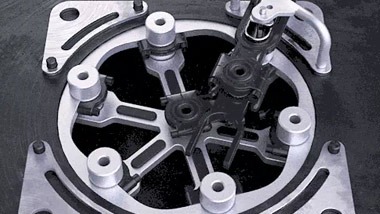
Montagem do Produto
Matéria-Prima, Inspeção e Montagem
São utilizados moldes de injeção na indústria de eletrodomésticos.
Injection molding technology has completely changed the manufacturing industry, especially in the household appliance industry, and its impact is particularly significant. Injection molds are widely used in the production of various household appliances, from refrigerators and washing machines to air conditioners and vacuum cleaners. This article will explore the role of injection molds in the household appliance industry and why they are crucial for producing high-quality household appliances.
Injection molding is a manufacturing process that involves injecting melted plastic into a mold to create specific shapes or components. The injection mold is a crucial component in the injection molding process, as it determines the shape and size of the final product. Injection molds used in the household appliance industry are designed to produce complex and precise components that meet specific requirements.
One of the main advantages of using injection molds in the household appliance industry is the ability to produce high-precision and consistent parts. The use of computer-aided design (CAD) and computer-aided manufacturing (CAM) software ensures that the design and manufacturing of molds can produce parts that meet precise specifications. This precision and consistency are crucial for producing high-quality household appliances that are functionally correct and efficient.
Another advantage of using injection molds is the ability to produce parts quickly and efficiently. The injection molding process is highly automated and can produce a large number of parts in a short amount of time. This production speed is essential for the household appliance industry, as manufacturers need to meet high demand while maintaining low production costs.
Injection molds are also highly suitable for creating complex and intricate components with precise geometric shapes. This design flexibility enables manufacturers to produce innovative home appliance designs that are both aesthetically pleasing and practical. For example, injection molds are used to create complex components such as compressor parts, water pumps, fan blades, and door handles.
The use of injection molds in the household appliance industry also ensures the durability and longevity of the final product. The materials chosen for injection molding are renowned for their strength, durability, and wear resistance, ensuring that household appliance components can withstand the test of daily use. In the household appliance industry, durability is crucial as appliances need to be able to withstand frequent use without experiencing malfunctions or rapid wear and tear.
In short, injection molds are crucial for producing high-quality household appliances. The use of injection molding technology enables manufacturers to produce parts quickly and efficiently, while ensuring high precision and consistency. The flexibility of design also allows for the creation of innovative home appliance designs that are both aesthetically pleasing and practical. With the continuous advancement of injection molding technology, manufacturers will continue to rely on this process to produce high-quality household appliance components.
FAQ About Household Appliance Injection Mold
A Household Appliance Injection Mold is a specialized tool used in the manufacturing process of household appliances through a technique called injection molding. Injection molding is a widely used manufacturing process in which molten plastic or other materials are injected into a mold cavity under high pressure. The mold is designed to have the shape and features of the desired household appliance.
Here's an overview of how the process works:
1. Mold Design: A skilled engineer or designer creates the mold's design, taking into consideration the specific requirements of the household appliance. The mold design includes details such as the dimensions, surface finishes, and features of the final product.
2. Mold Fabrication: The mold is then fabricated using high-precision machinery, typically made from metal (e.g., steel or aluminum). The fabrication process involves CNC machining or other techniques to ensure the mold's accuracy and durability.
3. Injection Molding Process: Once the mold is ready, the injection molding process begins. Plastic pellets or other raw materials are heated until they become molten. The molten material is then injected into the mold cavity under high pressure using an injection molding machine.
4. Cooling and Solidification: The molten material rapidly cools and solidifies inside the mold, taking the shape of the mold cavity. Cooling channels within the mold help regulate the temperature and speed up the solidification process.
5. Ejection: After the material has solidified and cooled sufficiently, the mold opens, and the newly formed household appliance is ejected from the mold using ejector pins.
6. Finishing: Some additional finishing processes, such as trimming, deburring, or surface texturing, may be required to achieve the desired final appearance and functionality of the household appliance.
Household Appliance Injection Molds enable manufacturers to produce large quantities of household appliances with consistent quality, precise details, and intricate shapes. This efficient and cost-effective manufacturing method is widely used in the production of various household appliances, including but not limited to vacuum cleaners, blenders, toasters, coffee makers, microwave ovens, and many others.
Household Appliance Injection Molding is a highly efficient and widely used manufacturing process for producing a wide range of household appliances made from plastic or other materials. The process involves several steps, from designing the mold to the final product's ejection. Here's a detailed overview of how household appliance injection molding works:
1. Mold Design: The process begins with the design of the injection mold. Skilled engineers or designers create a 3D CAD model of the mold, taking into account the specific requirements of the household appliance being manufactured. The mold design includes details such as the dimensions, features, surface finishes, and any additional components needed for the final product.
2. Mold Fabrication: Once the mold design is finalized, the mold is fabricated using precision machining techniques. Commonly, molds are made from high-quality metals such as steel or aluminum, which can withstand the high temperatures and pressures involved in the injection molding process. The fabrication process ensures the mold's accuracy and durability, as any imperfections can negatively impact the final product.
3. Injection Molding Process:
a. Material Preparation: Plastic resin pellets or other raw materials are selected based on the desired characteristics of the final product. These pellets are then fed into a hopper, where they are heated and melted into a molten state.
b. Injection: The molten material is injected into the mold cavity under high pressure using an injection molding machine. The machine consists of a barrel where the plastic is melted, a screw that transports the molten material, and an injection nozzle that delivers the material into the mold.
c. Cooling and Solidification: Once the molten material is injected into the mold, it rapidly cools and solidifies inside the mold cavity. The mold contains cooling channels that help regulate the temperature and speed up the solidification process. This cooling phase ensures that the material takes on the shape and details of the mold cavity.
4. Ejection: After the material has solidified and cooled sufficiently, the mold opens, and the newly formed household appliance is ejected from the mold using ejector pins. The appliance retains the shape and features of the mold.
5. Finishing: Some additional finishing processes may be required after ejection. These may include trimming off excess material, removing any rough edges, adding surface textures, or assembling multiple parts to create the final household appliance.
6. Quality Control: Throughout the entire injection molding process, quality control measures are implemented to ensure that each appliance meets the required specifications and standards. Defective products are identified and removed from the production line.
Household Appliance Injection Molding offers various benefits, including high production efficiency, precise and consistent product quality, cost-effectiveness for large-scale production, and the ability to manufacture complex and intricate designs. This process is widely used in the production of household appliances such as vacuum cleaners, blenders, refrigerators, and many others.
Injection molding is a versatile manufacturing process used to produce a wide range of household appliances made from plastic and other materials. Many common household appliances are manufactured using injection molds due to the process's efficiency, cost-effectiveness, and ability to create complex designs. Some of the commonly produced household appliances include:
1. **Vacuum Cleaners:** The outer shells, internal components, and accessories of vacuum cleaners are often produced using injection molds.
2. **Blenders and Food Processors:** The containers, lids, blades, and other components of blenders and food processors are typically made through injection molding.
3. **Coffee Makers:** The carafes, filter baskets, and other parts of coffee makers are commonly manufactured using injection molds.
4. **Microwave Ovens:** Various components such as control panels, door frames, and interior parts of microwave ovens are often produced using injection molding.
5. **Toasters and Toaster Ovens:** The outer casings and control panels of toasters and toaster ovens are frequently made through injection molding.
6. **Refrigerators and Freezers:** Some interior components, such as shelves and door compartments, in refrigerators and freezers are manufactured using injection molds.
7. **Washing Machines and Dryers:** Certain parts, like control panels and door handles, in washing machines and dryers are commonly produced using injection molding.
8. **Dishwashers:** Some dishwasher components, such as cutlery baskets and detergent dispensers, are often made through injection molding.
9. **Air Conditioners:** Various parts of air conditioners, including fan blades and covers, are commonly produced using injection molds.
10. **Electric Fans:** The blades, casings, and stands of electric fans are frequently manufactured using injection molding.
11. **Irons:** The handles, plates, and other components of irons are often produced through injection molding.
12. **Electric Kettles:** The bodies, handles, and spouts of electric kettles are commonly made using injection molds.
13. **Rice Cookers:** Certain components like the inner pots and lids of rice cookers are manufactured through injection molding.
14. **Handheld Appliances:** Handheld appliances like hairdryers, electric shavers, and electric toothbrushes often use injection-molded parts.
15. **Electric Juicers:** The juicer bodies, pulp containers, and other parts are commonly produced using injection molding.
These are just a few examples, and many other household appliances use injection molding for various components. The ability to produce complex shapes, consistent quality, and cost-effective mass production make injection molding a preferred method for manufacturing numerous household appliances.
Household Appliance Injection Molding utilizes a variety of materials depending on the specific requirements and properties of the household appliance being manufactured. The choice of material is crucial as it directly impacts the appliance's performance, durability, appearance, and cost. Some of the key materials commonly used in household appliance injection molding are:
1. **ABS (Acrylonitrile Butadiene Styrene):** ABS is a widely used thermoplastic known for its excellent impact resistance, rigidity, and toughness. It is commonly used for manufacturing outer shells, covers, and structural components of household appliances.
2. **PP (Polypropylene):** PP is a lightweight and flexible thermoplastic with good chemical resistance. It is often used for producing parts such as containers, lids, and hinges in household appliances.
3. **PS (Polystyrene):** PS is a versatile and cost-effective material used for items like disposable cutlery, food containers, and packaging for household appliances.
4. **PC (Polycarbonate):** PC is a transparent thermoplastic with high impact resistance, making it suitable for applications such as blender jars, oven windows, and other transparent or translucent parts.
5. **PET (Polyethylene Terephthalate):** PET is commonly used for beverage bottles and containers in appliances like water dispensers and juicers.
6. **PA (Nylon):** Nylon offers excellent strength and durability, making it suitable for components that require toughness and wear resistance, such as gears and moving parts.
7. **POM (Polyoxymethylene or Acetal):** POM is a low-friction and high-strength material commonly used for producing components like gears, bearings, and handles in household appliances.
8. **PBT (Polybutylene Terephthalate):** PBT is known for its electrical insulating properties, making it suitable for electrical components in household appliances.
9. **PE (Polyethylene):** PE is a widely used thermoplastic known for its flexibility and chemical resistance. It is used for items such as seals and gaskets in appliances.
10. **PMMA (Polymethyl Methacrylate):** PMMA, commonly known as acrylic, is used for transparent or clear parts like display panels and windows.
11. **TPU (Thermoplastic Polyurethane):** TPU is a flexible and elastic material used for soft-touch handles and grips on household appliances.
12. **TPE (Thermoplastic Elastomer):** TPE is a versatile material that combines the properties of rubber and plastic. It is used for items like seals, gaskets, and flexible components.
The choice of material depends on factors such as the appliance's function, desired appearance, environmental conditions, regulatory requirements, and cost considerations. Manufacturers carefully select the appropriate material to ensure the final product meets the necessary performance and safety standards while remaining cost-effective for mass production.
Designing a Household Appliance Injection Mold is a crucial and intricate process that requires expertise in mold engineering and a deep understanding of the specific requirements of the household appliance being manufactured. Here's an overview of the steps involved in designing a household appliance injection mold:
1. **Product Requirements Analysis:** The first step is to thoroughly understand the requirements of the household appliance. This includes examining the 3D CAD model or physical prototype of the product, understanding its functionality, dimensions, material, desired surface finish, and any specific features or inserts required.
2. **Material Selection:** Based on the product requirements and the properties needed for the final appliance, the appropriate material is selected. Factors like strength, rigidity, transparency, temperature resistance, and cost are considered during material selection.
3. **Mold Type Selection:** Depending on the complexity of the household appliance and its parts, the type of mold is chosen. Common mold types include single-cavity, multi-cavity, hot runner, cold runner, and stack molds.
4. **Mold Layout Design:** The mold layout is designed to accommodate the number of cavities needed and the parting line. The layout includes the placement of cooling channels to regulate temperature during the injection process.
5. **Gate and Runner Design:** The gates and runners are critical components that control the flow of molten material into the mold cavity. Their design is optimized to ensure smooth filling, minimize material waste, and reduce cycle time.
6. **Draft Analysis:** Draft angles are incorporated into the mold design to allow for easy ejection of the molded parts. A draft analysis ensures that the angles are appropriate for the type of material and the specific shape of the appliance.
7. **Cooling System Design:** Cooling channels are strategically placed within the mold to ensure efficient and uniform cooling of the molten material. Proper cooling is essential to avoid defects and achieve consistent part quality.
8. **Ejection System Design:** The ejection system, including ejector pins and plates, is designed to safely remove the molded part from the mold cavity after it solidifies.
9. **Venting:** Proper venting is essential to allow air and gases to escape from the mold during the injection process, preventing defects like air traps or burns on the final part.
10. **Mold Steel Selection:** The appropriate mold steel is chosen based on factors such as part volume, material properties, expected production volume, and budget constraints.
11. **Tooling Design:** The tooling design includes details like mold base, cavities, inserts, slides, and lifters. The tooling is carefully designed to ensure precision, durability, and ease of maintenance.
12. **Mold Flow Analysis:** Before finalizing the mold design, a mold flow analysis is often performed using specialized software to simulate the injection molding process. This analysis helps identify potential issues and optimize the mold design for better performance.
13. **Prototyping and Testing:** Once the mold design is completed, a prototype mold may be created to test and verify the design. Test runs are performed to check for any issues and validate the functionality and quality of the molded parts.
14. **Finalizing the Design:** After the necessary adjustments and testing, the mold design is finalized, and detailed engineering drawings are created to guide the mold fabrication process.
The entire mold design process requires collaboration between product designers, mold engineers, and manufacturers to ensure the mold meets the product's requirements and facilitates efficient and cost-effective production of the household appliance.
Injection molding offers numerous advantages for the production of household appliances. It has become a preferred manufacturing method for a wide range of household appliances due to the following key benefits:
1. **Cost-Effective Mass Production:** Injection molding allows for high-volume production of identical parts, making it cost-effective for large-scale manufacturing. The ability to produce multiple parts in a single cycle reduces labor and material costs per unit.
2. **Complex and Intricate Designs:** Injection molding enables the creation of intricate and complex shapes with precision and consistency. This is particularly useful for designing stylish and ergonomic household appliances with smooth surfaces and fine details.
3. **High Productivity and Efficiency:** The injection molding process is highly automated, leading to faster production cycles and increased productivity. Minimal human intervention ensures a consistent output and reduces the chances of errors during production.
4. **Wide Range of Materials:** Injection molding can utilize a broad selection of materials, including various plastics and thermoplastics, which can be chosen based on the appliance's specific requirements, performance, and aesthetics.
5. **Consistent Part Quality:** Injection molding results in parts with uniform quality and dimensional accuracy. The mold design, cooling system, and process controls ensure consistent and repeatable part production.
6. **Reduced Post-Processing:** Injection-molded parts typically require minimal post-processing, reducing the need for additional finishing steps and lowering overall production time and costs.
7. **Shorter Lead Times:** Once the injection mold is designed and fabricated, it can be quickly put into production, resulting in shorter lead times for the manufacturing of household appliances.
8. **Design Flexibility:** The flexibility of injection molding allows for easy modification of the mold design, making it possible to adapt to design changes or introduce product improvements without significant retooling costs.
9. **Material Efficiency:** Injection molding generates little material waste, as excess material from one part can be used in the production of the next part.
10. **Environmental Considerations:** The efficiency and material-saving nature of injection molding contribute to reduced waste generation and a lower environmental impact compared to other manufacturing processes.
11. **Part Integration:** Injection molding allows for the integration of multiple parts or components into a single piece, reducing assembly steps and enhancing the appliance's structural integrity.
12. **High Surface Finish Quality:** Injection-molded parts often have smooth and polished surfaces, eliminating the need for additional surface treatments and enhancing the final appearance of the household appliance.
Overall, injection molding offers manufacturers of household appliances a highly efficient, reliable, and cost-effective method to produce high-quality products that meet consumer demands for performance, aesthetics, and functionality.
Yes, designing household appliance injection molds comes with specific challenges and considerations that mold engineers need to address to ensure successful and efficient production. Some of the key challenges and considerations include:
1. **Part Complexity:** Many household appliances have complex designs with intricate details. Designing molds for such parts requires careful consideration of gating and venting to ensure even material flow and proper filling of all features.
2. **Material Selection:** Choosing the right material is crucial as different household appliances may require specific material properties such as heat resistance, chemical resistance, or transparency. The material's shrinkage and flow characteristics must also be taken into account during mold design.
3. **Draft Angles:** Proper draft angles are essential to ensure smooth part ejection from the mold. Complex parts may require different draft angles for different sections, adding complexity to the mold design.
4. **Wall Thickness Variation:** Household appliances may have varying wall thicknesses to meet structural and design requirements. Mold designers must account for these variations to prevent defects like sink marks and warping.
5. **Cooling System Design:** Efficient cooling is critical to maintain cycle times and achieve consistent part quality. Proper placement and design of cooling channels are essential to avoid hot spots and reduce cooling time.
6. **Parting Line Selection:** Choosing the parting line (the line where the two halves of the mold meet) affects the part's appearance and functionality. It should be carefully selected to minimize visible parting line marks and ensure proper part assembly.
7. **Ejection System:** Household appliance parts may have complex shapes that require precise ejection. The ejection system design must avoid damage to the parts during ejection and ensure smooth removal from the mold.
8. **Undercuts and Side Actions:** Some household appliance designs may have undercuts or side actions that complicate the ejection process. Mold designers must incorporate appropriate mechanisms to release such features.
9. **Mold Cost and Complexity:** Complex household appliance designs may result in more intricate molds, leading to increased manufacturing costs and longer lead times. Balancing the benefits of the design against production costs is crucial.
10. **Regulatory Compliance:** Depending on the appliance's purpose and location of sale, there may be regulatory standards and safety requirements that the mold design must adhere to.
11. **Tool Maintenance and Repair:** Regular maintenance and occasional repair of the molds are essential to ensure consistent part quality and prolong the mold's lifespan.
12. **Production Volume and Lead Time:** The expected production volume and lead time for producing household appliances must be considered during mold design to ensure the mold's efficiency aligns with the production requirements.
By addressing these challenges and considerations during the mold design phase, mold engineers can create molds that deliver high-quality parts, efficient production, and cost-effectiveness for household appliance manufacturers. Collaboration between product designers and mold engineers is crucial to ensure that the final mold design meets the appliance's specific requirements and market demands.
The costs associated with producing household appliance injection molds can vary significantly depending on various factors, including the complexity of the mold design, the type of household appliance being manufactured, the material used, the number of cavities in the mold, and the production volume required. Here are some typical costs and factors to consider:
1. **Mold Design and Engineering:** The initial design and engineering of the mold involve skilled labor, design software, and prototyping costs to ensure the mold meets the appliance's specific requirements. This cost can range from a few thousand to tens of thousands of dollars, depending on the complexity of the mold.
2. **Mold Material:** The type of material used for the mold impacts its durability and lifespan. High-quality mold steel can be expensive, and the cost may increase for molds with more complex features.
3. **Mold Fabrication:** The actual manufacturing of the mold requires precision machining and tooling. The cost of mold fabrication can range from thousands to tens of thousands of dollars, depending on the mold's size and complexity.
4. **Number of Cavities:** The number of cavities in the mold directly affects the production output per cycle. Molds with more cavities can produce more parts in a single cycle, reducing production time and costs per part.
5. **Mold Maintenance and Repair:** Regular maintenance and occasional repairs are necessary to ensure the mold's longevity and consistent part quality. These costs should be factored into the overall mold production expenses.
6. **Material Costs:** The cost of the raw material used for injection molding is a significant factor, especially for large-scale production. The material's price per kilogram or pound can impact the overall production cost.
7. **Labor Costs:** Labor costs, including machine operators and technicians, need to be considered as part of the overall production expenses.
8. **Prototyping and Testing:** Before full-scale production, prototype molds may be used to test and validate the mold design. While prototype molds are generally less expensive than production molds, they still contribute to the overall costs.
9. **Regulatory Compliance:** If the household appliance must meet specific regulatory standards or certifications, additional testing and compliance expenses may be incurred.
10. **Production Volume:** The expected production volume influences the cost-effectiveness of the mold. Higher production volumes can spread the initial mold investment across more units, reducing the per-unit cost.
Overall, the cost of producing household appliance injection molds can range from a few thousand dollars for simpler molds to several hundred thousand dollars for large, complex molds used in high-volume production. It's essential for manufacturers to carefully consider these costs and find the right balance between quality, efficiency, and cost-effectiveness for their specific appliance production requirements.
The quality of an injection mold has a significant impact on the final product's performance and durability. A well-designed and well-manufactured mold ensures that the molded parts meet the desired specifications, resulting in a high-quality product with consistent performance and longevity. Here are some ways in which the quality of an injection mold affects the final product:
1. **Dimensional Accuracy:** A high-quality mold ensures precise replication of the part's dimensions and features. Any inaccuracies in the mold design or fabrication can lead to variations in the part's dimensions, potentially causing fitment issues and affecting the appliance's overall functionality.
2. **Surface Finish:** The mold's surface finish directly influences the appearance and feel of the molded parts. A smooth and well-finished mold surface produces parts with an attractive and professional appearance.
3. **Strength and Durability:** The material and construction of the mold determine its durability. A high-quality mold made from robust materials can withstand the rigors of repeated molding cycles, reducing the risk of mold damage and prolonging its lifespan.
4. **Part Consistency:** A well-designed mold, combined with proper process controls, ensures consistent material flow and filling throughout the part. This results in molded parts with uniform properties and performance characteristics.
5. **Minimized Defects:** A quality mold design helps reduce the occurrence of common defects like sink marks, warping, voids, and flash in the final molded parts. Fewer defects lead to improved product reliability and reduced waste.
6. **Longevity of the Product:** When the molded parts are made using a high-quality mold, they are less likely to suffer from premature wear and failure. The appliance, as a whole, benefits from increased durability and extended lifespan.
7. **Functionality and Fitment:** A precise mold design ensures that parts fit together as intended, enabling smooth assembly and proper functionality of the household appliance.
8. **Consistent Performance:** The consistent quality of the molded parts, achieved through a quality mold, ensures that each household appliance performs reliably, meeting customer expectations and minimizing product returns or warranty claims.
9. **Optimized Material Usage:** A well-engineered mold design minimizes material wastage during the injection molding process. This optimization leads to cost savings, reduced material expenses, and a more sustainable production process.
10. **Regulatory Compliance:** High-quality molds can help meet regulatory requirements and standards, ensuring that the final product meets safety and performance guidelines.
In summary, the quality of an injection mold directly impacts the final product's performance and durability. A high-quality mold design and construction lead to precise, consistent, and reliable molded parts, resulting in household appliances that function as intended, have an appealing appearance, and last longer in service. Manufacturers should prioritize investing in quality molds to achieve these benefits and deliver products that satisfy customer needs and expectations.
Yes, there are several eco-friendly and sustainable practices that can be implemented in household appliance injection molding to reduce the environmental impact of the manufacturing process. These practices aim to minimize waste, conserve resources, and promote more sustainable production methods. Here are some eco-friendly practices in household appliance injection molding:
1. **Material Selection:** Choosing eco-friendly and sustainable materials for injection molding can significantly impact the environmental footprint of the process. Opting for biodegradable or recyclable plastics, as well as using recycled materials, helps reduce the reliance on virgin resources and minimizes waste.
2. **Recycling and Reusing Materials:** Implementing recycling programs within the injection molding facility allows for the collection and reuse of excess materials, production scrap, and defective parts. Recycling minimizes material waste and conserves resources.
3. **Energy Efficiency:** Using energy-efficient machinery and optimizing production processes can reduce energy consumption during injection molding. Energy-efficient equipment and practices contribute to lower greenhouse gas emissions and overall energy usage.
4. **Reducing Water Usage:** Water is often used for cooling during the injection molding process. Implementing water-saving technologies and recycling water can help reduce the facility's water consumption.
5. **Lean Manufacturing:** Adopting lean manufacturing principles aims to eliminate waste, including excess inventory, overproduction, and unnecessary transportation. Reducing waste streamlines the production process and minimizes the environmental impact.
6. **Mold Design Optimization:** Designing molds for efficient material usage and shorter cycle times can reduce material waste and energy consumption during the molding process.
7. **Post-Processing Waste Reduction:** Implementing measures to reduce post-processing waste, such as trimming and finishing, contributes to a more sustainable manufacturing process.
8. **Sustainable Packaging:** Using eco-friendly and recyclable packaging materials for the final household appliances reduces the environmental impact of the product's life cycle.
9. **Lifecycle Analysis:** Conducting a lifecycle analysis of the household appliance, from raw material extraction to end-of-life disposal, can identify areas for improvement and guide more sustainable design and production decisions.
10. **Circular Economy Practices:** Adopting circular economy principles involves designing products with materials that can be easily recycled or repurposed at the end of their life, contributing to a closed-loop system that reduces waste.
11. **Eco-friendly Additives:** Some molders use eco-friendly additives and processing aids to enhance material performance and reduce the need for harmful substances.
12. **Environmental Certifications:** Seeking and achieving environmental certifications, such as ISO 14001, demonstrates a commitment to environmental responsibility and sustainable practices.
By incorporating these eco-friendly practices into household appliance injection molding processes, manufacturers can contribute to more sustainable production and help reduce the environmental impact of their products. Embracing sustainability in the manufacturing industry is crucial for promoting a greener future and meeting the growing demand for environmentally conscious products.
Certainly! Injection molding is widely used in the manufacturing of various popular household appliances. Here are some examples of household appliances that are commonly produced using injection molds:
1. **Coffee Makers:** The housing, water reservoir, and drip tray of coffee makers are often manufactured using injection molds.
2. **Blenders and Food Processors:** The blending jars, lids, and various components of blenders and food processors are typically made through injection molding.
3. **Toasters and Toaster Ovens:** The outer casings, control panels, and crumb trays of toasters and toaster ovens are commonly produced using injection molds.
4. **Microwave Ovens:** The control panels, door handles, and interior components of microwave ovens are often manufactured using injection molding.
5. **Refrigerators and Freezers:** Certain interior components like shelves, door bins, and crispers in refrigerators and freezers are commonly made through injection molding.
6. **Dishwashers:** The cutlery baskets, detergent dispensers, and interior components of dishwashers are often produced using injection molds.
7. **Washing Machines and Dryers:** Various parts, including control panels, detergent drawers, and door handles, in washing machines and dryers are commonly made through injection molding.
8. **Vacuum Cleaners:** The outer casings, dustbins, and accessories of vacuum cleaners are typically manufactured using injection molds.
9. **Electric Fans:** The fan blades, casings, and stands of electric fans are frequently made through injection molding.
10. **Irons:** The handles, soleplates, and other components of irons are often produced using injection molds.
11. **Electric Kettles:** The bodies, handles, and spouts of electric kettles are commonly made using injection molds.
12. **Rice Cookers:** Certain components like the inner pots, lids, and control panels of rice cookers are manufactured through injection molding.
13. **Hair Dryers and Electric Shavers:** Many handheld appliances like hair dryers and electric shavers utilize injection-molded parts.
14. **Electric Juicers:** The juicer bodies, pulp containers, and other parts are commonly produced using injection molding.
These examples represent only a portion of the numerous household appliances that benefit from the efficiency, versatility, and cost-effectiveness of injection molding. The process's ability to produce complex shapes, precise details, and consistent quality makes it a popular choice for manufacturing a wide range of household appliances.