Peças plásticas e metálicas para instrumentos.
In the world of making medical and scientific gadgets, plastic metal parts are super important. These parts are used in a lot of different devices like medical tools, lab equipment, and machines that help scientists analyze things.
To make these parts, we use a special process called injection molding. It's kind of like baking a cake. First, we melt down tiny pieces of plastic. Then, we press this melted plastic into a special mold under a lot of pressure. Once it cools down and hardens, we open the mold and take out the finished part. This way, we can make really precise and high-quality plastic parts that are all the same.
One great thing about using plastic metal parts in the instrument industry is that they can have really cool shapes and designs. This is really important in medicine and science because the tools need to work well, be safe, look good, and be easy to use.
These plastic parts can be made from different types of plastic, like strong plastics, flexible plastics, and even special plastics that can resist chemicals or let light through. Being able to make parts with different features makes injection molding perfect for making all sorts of medical and scientific tools.
Another plus is that we can make lots of these parts quickly. This is really helpful when we need to make instruments fast to keep up with demand. Using machines and robots in the process can make it even faster and cheaper.
But there are some problems too. Making the molds can be expensive, especially if the design is complicated. Also, this process can create a lot of waste plastic, which is bad for the environment and costs money to deal with.
Overall, plastic metal parts are key in making medical and scientific instruments. It's important to make high-quality parts quickly and efficiently because these tools need to meet strict standards. As these industries grow, injection molding will keep being an important part of making new and better medical and scientific gadgets.
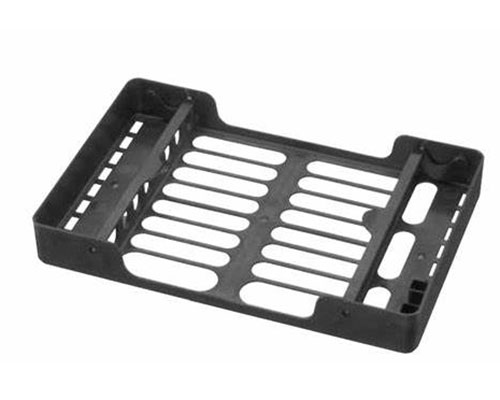
Peças de instrumento.
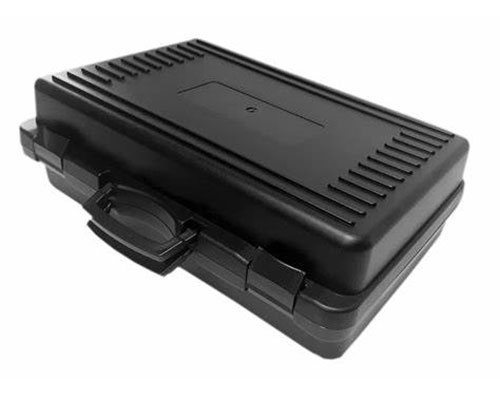
Peças de instrumento.
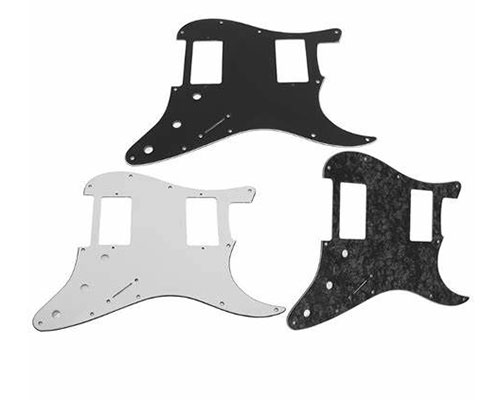
Instrument Products
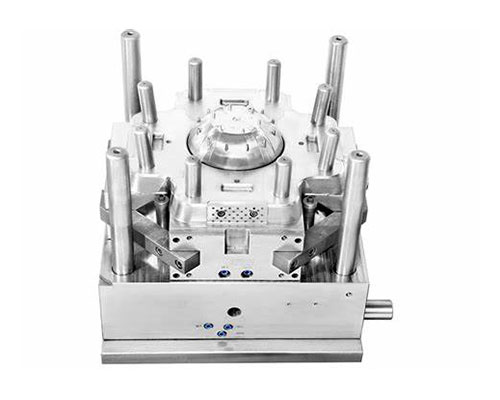
Instrument Parts Mould
Serviço de fabricação de peças plásticas e metálicas para instrumentos.
Be good at product structure optimization and greatly reduce the cost of Plastic Metal Parts custom solutions
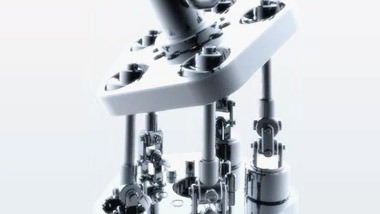
Design da peça
Design Estético e Estrutural
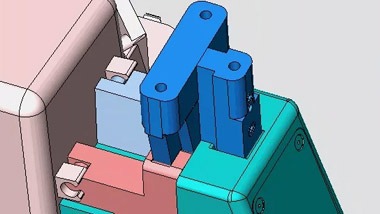
Fabricação de moldes
Design, Confirmação de Facilidade de Manufatura
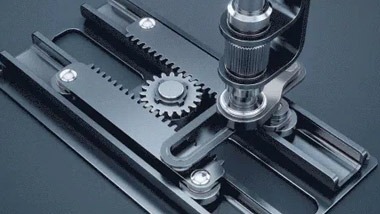
Produção de Produto
Equipamento de Alta Velocidade Importado
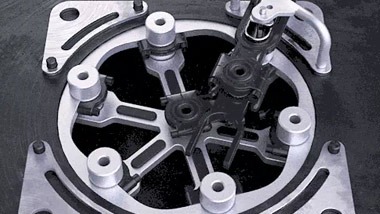
Montagem do Produto
Matéria-Prima, Inspeção e Montagem
São utilizados peças plásticas e metálicas na indústria de instrumentos.
In many industries, plastic metal parts have become an indispensable tool for manufacturing instruments, especially in the medical and scientific instrument sectors. These components have completely changed the production process of instrument parts, making them more efficient and cost-effective. Plastic metal technology enables manufacturers to produce high-quality parts that meet strict industry standards.
One of the main advantages of using plastic metal parts is the ability to produce high-precision and consistent pieces. This is particularly important in the fields of medicine and science, as instruments must be precise and reliable. Plastic metal technology allows manufacturers to create complex and detailed components, facilitating mass production of high-quality parts.
Another benefit of plastic metal parts is the ability to use a wide range of materials to manufacture instrument components. Manufacturers can choose from various options, including thermoplastic plastics, thermoplastic elastomers, and engineering plastics. This flexibility enables manufacturers to select the most ideal materials for each instrument component.
In the medical and scientific fields, it is crucial to be able to produce complex components with high accuracy and consistency, as instruments in these areas must meet strict safety standards. Plastic metal parts enable manufacturers to create components that meet these standards, reduce the risk of failure, and ensure the safety of patients and researchers.
In addition to precision and consistency, plastic metal parts also offer other benefits that make them ideal tools for manufacturing instrument components. One such benefit is the ability to produce parts in high quantities, which reduces production time and costs. Plastic metal parts can quickly and effectively be manufactured, enabling manufacturers to meet the growing demand for instruments in various industries.
Although plastic metal parts have many advantages, some limitations also need to be considered. For more complex designs, the initial cost of creating molds may be high. However, once the molds are created, they can produce components at a lower unit cost. Additionally, this process may generate a large amount of plastic waste, which must be properly handled to minimize environmental impact.
In short, plastic metal parts are key tools in the manufacturing process of instruments across various industries. They enable manufacturers to produce high-quality components with extremely high precision and consistency, which is essential in the medical and scientific fields. With the continuous advancement of plastic metal technology, manufacturers will continue to rely on this process to produce innovative and high-quality instrument components.
FAQ About Instrument Plastic Metal Parts
Instrument plastic metal parts are typically made from a variety of materials, including high-grade polymers like ABS, polycarbonate, and PEEK for the plastic components. Metal parts often use aluminum, stainless steel, or titanium due to their durability and resistance to corrosion. These materials ensure that the parts can withstand harsh environments and maintain their functionality over time.
To choose the right material, consider factors such as mechanical strength, thermal stability, chemical resistance, and weight. For instance, if your instrument is exposed to high temperatures, you might opt for metals like stainless steel. If weight is a concern, aluminum could be a good choice. Plastic materials like ABS are great for their cost-effectiveness and ease of manufacturing.
Yes, many instrument plastic metal parts are designed to be highly resistant to corrosion. Metals like stainless steel and titanium are naturally corrosion-resistant, making them ideal for use in instruments. Plastics such as PEEK also offer excellent chemical resistance, ensuring longevity even in harsh chemical environments.
Absolutely! One of the significant advantages of using plastic and metal parts in instruments is their customizability. Whether it's altering the dimensions, adding specific features, or modifying the material properties, these parts can be tailored to meet precise requirements. This flexibility makes them suitable for a wide range of applications.
Plastic parts are generally lighter and more cost-effective than metal parts, making them ideal for applications where weight and budget are critical. They are also easier to mold into complex shapes and can offer better electrical insulation. On the other hand, metal parts provide superior strength and durability, especially in high-stress or high-temperature environments.
Instrument plastic metal parts are known for their durability. Metals like stainless steel and titanium offer exceptional strength and longevity, while high-performance plastics such as polycarbonate and PEEK provide robustness and resistance to wear and tear. When properly maintained, these parts can last for many years.
While plastic does have some environmental concerns, such as being less biodegradable compared to metal, advancements in materials science have led to the development of more eco-friendly options. Recycled plastics and bioplastics are becoming increasingly popular. Additionally, proper disposal and recycling programs can mitigate some of these concerns.
Generally, instrument plastic metal parts do not require extensive maintenance. Regular cleaning and inspection are usually sufficient to keep them in good condition. For metal parts, occasional polishing or rust-proof coating may be necessary to maintain their appearance and functionality. Plastic parts might need protection from extreme temperatures or chemicals.
Yes, both plastic and metal instrument parts can be recycled. Metals like aluminum and stainless steel are commonly recycled, and there are established recycling programs for various types of plastics. Recycling these materials helps reduce waste and conserve natural resources, contributing to sustainability efforts.
Instrument plastic metal parts are crucial for the overall performance of an instrument. They contribute to its structural integrity, precision, and reliability. Metal parts often handle load-bearing functions and provide durability, while plastic parts can offer additional benefits like weight reduction and improved aesthetics. Together, they ensure that the instrument operates efficiently and effectively.