Serviço de usinagem CNC M1TP7 personalizado
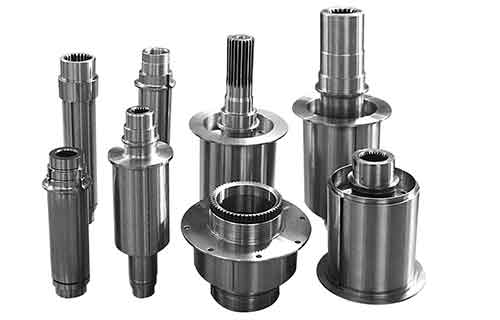
Serviços personalizados de usinagem de precisão Part CNC Machining
In our online CNC machining service, you can easily obtain instant quotes for customized metal and plastic parts. We can quickly produce prototypes and production parts within a few days. Our facilities have passed ISO 9001:2015, ISO 13485, and AS9100D certifications, ensuring the highest quality standards. We have a high-quality machine workshop with professional knowledge in manufacturing any customized design, whether simple or complex. We offer a wide range of capabilities, including rapid prototyping, small batch processing, and mass production. Our goal is to provide you with the necessary mechanical components when you need them. Let's start using our convenient online platform. Submit your design and specifications to receive pricing information immediately. Let us handle your customized processing needs and deliver the parts you need on time, fully meeting your specifications.
O que é o serviço de maquinagem CNC Plastic Metal Part?
CNC, Computer numerical control machining is a widely used manufacturing process. It utilizes automated, high-speed cutting tools to form design patterns from metal or plastic raw materials. Standard CNC machine tools include 3-axis, 4-axis, and 5-axis milling machines, lathes, and routers. Different machine tools may have different cutting methods for CNC parts - the workpiece can remain stationary while the tool moves, or the tool can remain stationary while the workpiece rotates and moves, and even the cutting tool and workpiece can move together.
Skilled mechanics operate CNC machines by programming tool paths based on the geometric shape of the final machined parts. The geometric information of the components is provided by computer-aided design (CAD) models. CNC machine tools are capable of cutting almost all metal alloys and hard plastics with high precision and repeatability, making customized machined parts suitable for almost all industries, including aviation, medical, robotics, electronics, and industry. We provide CNC services and offer customized CNC quotes for over 40 materials, ranging from common aluminum and formaldehyde to advanced titanium and engineering plastics such as PEEK and polytetrafluoroethylene.
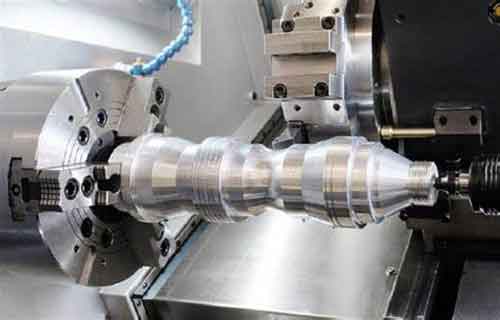
Metal CNC Machining Materials
Cobre C932
Cobre 260
Cobre 360
Nitronic 60 (218 SS)
Aço inoxidável 15-5
Aço inoxidável 17-4
St1TP7Aço inoxidável 18-8
St1TP7Aço inoxidável 303
St1TP7Aço inoxidável 316/316L
St1TP7Aço inoxidável 416
St1TP7Aço inoxidável 410
St1TP7Aço inoxidável 420
St1TP7Aço inoxidável 440C
Aço 1018
Aço 1215
Aço 4130
Aço 4140
Aço 4140PH
Aço 4340
Aço A36
Titânio (Grade 2)
Titanium (Grade 5)
Plastic CNC Machining Materials
Plástico de engenharia de alta resistência utilizado para muitos produtos comerciais.
Um plar glass semelhante ao cleastic. Boas propriedades de resistência ao calor e ao calor. Ideal para utilização no exterior.
Resina com boa resistência à humidadeance, alta resistência ao desgasteance, and baixa fricção.
Construído em resina epóxi an com reforço de fibra de vidro ass fabric, and also called epoxy-grade industrial laminate and fenólico, este material oferece alta resistência and baixa absorção de humidade absorption.
O polietileno de alta densidade é a resistente à humidade ae à química ant plastico com boa resistência impact. O material é adequado para aplicações no exterior a bem como a com containers ou seals estanques.
Oferece maior resistência mecânica, rigidez e boa resistência ao calor e/ou resistência química.
Com quase o dobro da resistência à tração do ABS, o policarbonato tem propriedades mecânicas e estruturais anicas al superiores. Amplamente utilizado na indústria automotiva, aerospace, ae outras applications thatat require durability and stability.
Com uma excelente resistência à tração, o PEEK é frequentemente utilizado como substituto a leve do metal em aplicações ar de alta temperatura e tensão. O PEEK resiste à química, ao desgaste e à humidade.
Haem excelentes propriedades eléctricasal ae pouca ou nenhuma absorção de humidade absorção. Pode suportar cargas leves durante um longo período de tempo em temperaturas muito variáveis. Pode ser transformado em produtos que exijam resistência química ou à corrosão.
Este material supera a maioria dos plasticos no que diz respeito resistncia qumicaal ance ance e desempenhoance em temperaturas extremasance. Resiste à maioria dos solventes e é um excelente isolante elétrico.
Ultra-high molecular weight polyethylene. A general-purpose material. It offers a unique combination of wear and corrosion resistance, low surface friction, high impact strength, high chemical resistance, and does not absorb moisture.
O cloreto de polivinilo (Tipo 1) é um plástico sintético altamente resistente a al, o PVC é normalmente utilizado em ambientes expostos a líquidos ou que requerem isolamento elétrico.
CNC Machining Surface Acabamentos
Tipo II (MIL-A-8625, Tipo II) creates a acabamento resistente à corrosãoant. As peças podem ser anodizadas em diferentes cores - amarelo, preto, vermelho e dourado -, sendo a mais comum a and normalmente associada ao alumínio.
O Tipo III (MIL-A-8625, Tipo III, Class 1/2 "hardcoat") é mais espesso and creates a wear-resistant layer em addicionado à resistência à corrosãoance observada com o Tipo II.
Um acabamento de surface para titanium de acordo com a especificação AMS-2488 Tipo 2ation. Também chamado de Tiodize, este acabamento aumenta a resistência à fadiga e a resistência ao desgaste da peça de titânio. Os parts anodizados de titânio arts are são comuns em aerospace and dispositivos médicos al manufacturing. Os acabamentos não pigmentados de titanium anodize esbatem o brilho.
Um processo de coard coat anodize que incorpora PTFE para criar ate a autolubrificante, superfície de contact seca com propriedades protectoras do Tipo 3 hard coat. Este acabamento pode ser utilizado em ligas de alumínio ou titânio e aumenta a vida útil do produto. Este acabamento está em conformidade com a norma AMS-2482 Tipo 1 Hard Coat Anodização com Teflon (não tingido).
Melhora a resistência à corrosãoance para os aços de 200 and 300 series and precipitation hardened corrosion-resistant. A espessura é insignificante, cerca de 0,0000001". Em conformidade com as normas ASTM A967, AMS-QQ-P-35, MIL-STD-171, ASTM A380 ou AMS 2700.
A prata oferece uma elevada condutibilidade de soldadura e condutividade eléctrica, mas é suscetível de se deteriorar. Está em conformidade com a norma AMS QQ-S-365D. A espessura é de cerca de 0,00002" - 0,0003".
Provides uniform zinc coating which offers protection from corrosion, oxidation, and wear on irregular surfaces. Conforms to ASTM B633-15.
CNC Machining Advantages
CNC milling and turning are two extremely precise and repeatable machining processes. According to different specification requirements, we can achieve a tolerance range between ± 0.001 inches and ± 0.005 inches. These machines can be programmed to run reliably for 24 hours, seven days a week, if needed, making CNC milling a good method for producing parts on demand.
Utilizando ferramentas de última geração, os serviços de maquinagem CNC are são particularmente adequados para a produção de peças de reposição, personalização de peças CNC, tais como a substituição de componentes antigos ou o fornecimento de actualizações profissionais aos clientes. Do mesmo modo, é igualmente possível aumentar o nível de produção de componentes individuais para mais de 10000 unidades. Dependendo da quantidade, tamanho e complexidade das unidades, o tempo de rotação de peças maquinadas por CNC pode ser tão curto quanto um dia. Com a entrega de ansportation and, podemos cumprir o prazo de adline dentro de a semana.
Another major advantage of CNC technology is its achievable mechanical performance. By cutting from large pieces of material instead of undergoing thermal deformation like injection molding or additive manufacturing, all ideal mechanical properties of the selected metal or plastic are preserved. The materials that can be machined using CNC milling and turning include over 50 industrial grade metals, alloys, and plastics. This option includes aluminum, brass, bronze, titanium, stainless steel, PEEK, ABS, and zinc. For CNC machining, the only material requirement is that the parts have sufficient hardness for fixation and cutting.
Imagine que tem um projeto urgente que requer a realização de milhares de peças de alta precisão no prazo de uma semana. Além disso, os métodos de maquinagem não podem ser capazes de satisfazer esta necessidade urgente, mas a tecnologia CNC pode. Não só garante que a peça de trabalho seja precisa ao micrómetro, como também permite a produção em apenas alguns dias. É por isso que muitos líderes da indústria confiam na maquinagem CNC para satisfazer os seus requisitos mais exigentes.
Além disso, a flexibilidade da tecnologia CNC significa que até os projectos mais complexos podem ser realizados. Quer se trate de a de um simples bloco de peças moldadas ou de a de peças com múltiplos tipos geométricos complexos, as máquinas CNC podem an accurately manufacture it. Isto proporciona aos designers possibilidades criativas ilimitadas e permite-lhes concretizar a sua visão sem sacrificar a qualidade.
Em suma, a fresagem CNC ae o torneamento não é apenas a manufa processo de fabrico, é an art forma. Combina advanced tecnologia and human creativity para criar ate produtos que at are ambos practical and aesthetically pleasing. Da próxima vez que pegar em a part made com tecnologia CNC, pare ae pense asobre o milagre de engenharia por detrás dele.
Part CNC Machining Perguntas mais frequentes
A programação CNC envolve a escrita de código que indica à máquina como mover e cortar o material para criar a peça desejada.
O programa de controlo CNC significa programa de controlo numérico computorizado. Trata-se de um processo de criação de instruções, denominadas códigos G e códigos M, que controlam os movimentos de uma máquina CNC (Computer Numerical Control). As máquinas CNC are advanced manufacturing tools thatat can automatically perform precise and complex machining operations on various materials, tais como metal, madeira, plastico, and compósitos.
Na programação CNC, o programador ou operador utiliza um software informático para gerar um conjunto de instruções que orientam os movimentos e as acções da máquina CNC. Estas instruções são escritas num programa específico da CNC, que é compreendido pelo sistema de controlo da máquina.
Eis como funciona o programa CNCamming:
1. Desenho CAD: O primeiro passo é criar um modelo 3D detate ate da peça ou componente a ser maquinado utilizando um software de desenho assistido por computador (CAD). O modelo CAD serve como projeto para o programa CNC.
2. CAM Software: Após a conceção da peça, o modelo CAD é importado para o software CAM (Computer-Aided Manufacturing). O software CAM ajuda a converter o modelo CAD em código de máquina CNC.
3. Geração de ferramentasath: No software CAM, o programador define as pontas das ferramentas que a máquina CNC seguirá para cortar e moldar o material. As pontas das ferramentas determinam os movimentos da ferramenta e as direcções de corte para obter o acabamento e a forma desejados.
4. Geração de código Gation: Uma vez definidas as ferramentas, o software CAM gera os códigos G e os códigos M. Os códigos G são comandos que controlam os movimentos da máquina, tais como o posicionamento, os avanços e as mudanças de ferramenta. Os códigos M são códigos para as funções de auxiliary, tais como as mudanças de ferramenta, controlo de ant de refrigeração, and ligar/desligar o fuso.
5. CNC M1TP7Configuração da máquina: O programa CNC é transferido para o sistema de controlo da máquina CNC, normalmente através de uma unidade USB ou de uma ligação em rede. A máquina a ser maquinada é instalada na máquina, e as ferramentas necessárias são instaladas.
6. Usinagem CNC: Depois de a máquina CNC estar configurada e o programa estar carregado, inicia-se o processo de maquinagem. A máquina CNC segue os códigos G e os códigos M para deslocar a ferramenta de corte com precisão e efetuar as operações especificadas no material.
7. Quality Controlo: Ao longo do processo de maquinação, os operadores realizam controlos de qualidade e medidas para garantir que o produto final cumpre as especificações exigidas.
A maquinagem CNC permite processos de maquinagem and repeatable manufacturing precisos, permitindo a produção de produtos and accurate complexos com um mínimo de intervenção al human. É amplamente utilizado em várias indústrias, incluindo aerospace, automotiva, eletrónica, and manufacturing, para tarefas como as fresagem, torneamento, perfuração, and corte.
As medidas de controlo de qualidade garantem que as peças maquinadas por CNC cumprem as especificações exigidas em termos de precisão dimensional, acabamento de superfície e resistência.
O controlo de qualidade desempenha um papel crucial na maquinagem CNC para garantir que os produtos finais cumprem as especificações e as normas de qualidade exigidas. A maquinagem CNC envolve processos de fabrico precisos e automatizados, e são essenciais medidas de controlo de qualidade eficazes para verificar se as peças produzidas são precisas, consistentes e isentas de defeitos. Eis as principais funções do controlo de qualidade na maquinagem CNC:
1. **Verificação das especificações do projeto:** O controlo de qualidade começa por verificar se as especificações do projeto CAD/CAM correspondem às dimensões e tolerâncias exigidas. A equipa de controlo de qualidade assegura que o programa CNC reflecte com precisão o desenho pretendido e os requisitos de maquinação.
2. **Calibragem e configuração da máquina:** Antes de iniciar o processo de maquinagem, o controlo de qualidade inclui a verificação de que a máquina CNC está corretamente calibrada e configurada. Isto assegura que os movimentos e as medições da máquina são exactos e estão alinhados com as instruções programadas.
3. **Inspeção das matérias-primas:** O pessoal do controlo de qualidade inspecciona as matérias-primas utilizadas na maquinagem para garantir que cumprem as normas de qualidade e composição exigidas. A inspeção de materiais ajuda a evitar potenciais defeitos causados pela má qualidade dos materiais.
4. **Inspeção do primeiro artigo:** Durante a produção inicial, é realizada uma inspeção do primeiro artigo para validar as dimensões e caraterísticas da peça em relação às especificações do projeto. Quaisquer discrepâncias ou desvios são identificados e tratados antes de se avançar para a produção em grande escala.
5. **Inspeção durante o processo:** São realizadas inspecções regulares durante o processo em várias fases do processo de maquinagem. Isto ajuda a detetar quaisquer problemas ou desvios numa fase inicial e permite que sejam feitos ajustes para manter a precisão dimensional.
6. **Acabamento da superfície e inspeção visual:** O pessoal do controlo de qualidade inspecciona o acabamento da superfície das peças maquinadas para garantir que cumprem as normas de textura e aspeto exigidas. A inspeção visual ajuda a identificar defeitos de superfície ou problemas cosméticos que possam ter de ser resolvidos.
7. **Verificação de tolerâncias:** A maquinagem CNC exige frequentemente tolerâncias apertadas para satisfazer requisitos precisos. As medidas de controlo de qualidade incluem a verificação de que as peças acabadas cumprem as tolerâncias especificadas e estão dentro dos limites aceitáveis.
8. **Inspeção final:** Uma vez concluídas todas as operações de maquinagem, é efectuada uma inspeção final para garantir que as peças cumprem todos os critérios de qualidade exigidos. Esta inspeção verifica se as peças estão isentas de defeitos e se estão em conformidade com as especificações do projeto.
9. **Ensaios não destrutivos (END):** Em alguns casos, podem ser utilizadas técnicas de ensaio não destrutivas, como o ensaio ultrassónico ou a inspeção por raios X, para detetar defeitos internos ou inconsistências materiais que podem não ser visíveis através de inspeção visual.
10. **Documentação e rastreabilidade:** O controlo de qualidade mantém registos e documentação pormenorizados dos resultados da inspeção para efeitos de rastreabilidade e responsabilidade. Esta documentação ajuda a identificar e a resolver quaisquer problemas de qualidade que possam surgir posteriormente.
Um controlo de qualidade eficaz na maquinagem CNC garante que os produtos finais são de alta qualidade, sem defeitos e em conformidade com os requisitos do cliente e as normas da indústria. Ajuda a evitar retrabalho dispendioso, reduz o desperdício e, em última análise, conduz à satisfação do cliente e à fiabilidade do produto.
Os tipos mais comuns incluem brocas, fresas de topo e machos.
Na maquinagem CNC, é utilizada uma variedade de ferramentas de corte para efetuar diferentes operações, tais como fresagem, torneamento, perfuração e corte. A escolha da ferramenta de corte depende da operação de maquinagem específica, do material a ser maquinado e do resultado pretendido. Alguns tipos comuns de ferramentas de corte utilizadas na maquinagem CNC incluem:
1. **Fresas de topo:** As fresas de topo são ferramentas de corte versáteis utilizadas para operações de fresagem. Têm arestas de corte na extremidade e nos lados da ferramenta, o que lhes permite remover material em várias direcções. As fresas de topo têm várias formas, tais como ponta quadrada, ponta esférica e raio de canto, para diferentes tarefas de maquinagem.
2. **Brocas:** As brocas são utilizadas para fazer furos na peça de trabalho. Existem diferentes tipos de brocas, tais como brocas helicoidais para perfuração de uso geral e brocas de ponto para localização precisa do furo antes da perfuração.
3. **Insertos para tornear:** Os insertos para tornear são utilizados em máquinas de torno para operações de torneamento. Estas pastilhas têm arestas de corte que removem material à medida que a peça roda, criando formas cilíndricas.
4. **Fresas de facear:** As fresas de facear têm grandes superfícies de corte e são utilizadas para operações de facear, onde o material é removido da superfície da peça de trabalho para obter um acabamento suave.
5. **Machos:** Os machos são utilizados para criar roscas internas nos furos. Existem em diferentes tamanhos e tipos de rosca, como os machos de canelura reta e os machos de ponta espiral.
6. **Alargadores:** Os alargadores são ferramentas de corte de precisão utilizadas para alargar e melhorar a precisão dos furos existentes. Produzem orifícios mais suaves e de dimensão mais exacta do que as brocas.
7. **Fresas de chanfrar:** As fresas de chanfrar são utilizadas para criar arestas chanfradas na peça de trabalho, proporcionando um acabamento biselado ou angular ao material.
8. **Contrafuros:** Os contrafuros são utilizados para criar um furo de fundo plano com um diâmetro maior na abertura para acomodar as cabeças dos parafusos.
9. **Escareadores:** Os escareadores são utilizados para criar um recesso cónico num furo, permitindo que as cabeças dos parafusos fiquem niveladas com a superfície da peça de trabalho.
10. **Fresas:** As fresas são fornecidas em várias formas e tamanhos para operações de fresagem especializadas, tais como abertura de ranhuras, fresagem lateral e contorno.
11. **Brochas:** As brochas são ferramentas de corte com dentes que aumentam gradualmente de tamanho, utilizadas para operações precisas e repetitivas de moldagem ou acabamento.
12. **Barras de mandrilar:** As barras de mandrilar são utilizadas para alargar furos existentes numa peça de trabalho e podem ser ajustadas para diferentes diâmetros.
Estes são apenas alguns exemplos das muitas ferramentas de corte utilizadas na maquinagem CNC. Cada ferramenta de corte foi concebida para efetuar operações específicas de forma eficiente e eficaz. Os operadores e programadores de CNC selecionam as ferramentas de corte adequadas com base nos requisitos de maquinação, nas propriedades do material e no acabamento de superfície pretendido. A seleção adequada das ferramentas e a programação do percurso da ferramenta são fundamentais para obter resultados de alta qualidade nas operações de maquinagem CNC.
A fixação refere-se ao processo de manter o material a ser maquinado no lugar para garantir precisão e consistência.
A fixação desempenha um papel crítico na maquinagem CNC, uma vez que é essencial para fixar e posicionar a peça de trabalho durante o processo de maquinagem. A fixação refere-se à utilização de ferramentas e dispositivos especializados, conhecidos como dispositivos de fixação, para manter a peça de trabalho firmemente no lugar na mesa ou no eixo da máquina CNC. O principal papel da fixação na maquinagem CNC é:
1. **Fixação da peça de trabalho:** A fixação garante que a peça de trabalho é mantida firmemente no lugar durante a maquinagem. Evita que a peça de trabalho se desloque, vibre ou se mova durante as operações de corte, o que poderia levar a resultados imprecisos ou a peças danificadas.
2. **Posicionamento exato:** A fixação adequada permite um posicionamento exato da peça de trabalho em relação à ferramenta de corte da máquina CNC. Esta precisão é crucial para alcançar as dimensões e tolerâncias desejadas na peça acabada.
3. **Repetibilidade:** A fixação permite a repetibilidade, o que significa que a mesma peça de trabalho pode ser posicionada da mesma forma em operações de maquinagem subsequentes ou na produção de várias peças idênticas. Esta consistência garante a uniformidade dos produtos finais.
4. **Maquinação de múltiplos lados:** Em muitas operações de maquinação CNC, uma única peça de trabalho requer maquinação em múltiplos lados. A fixação permite que a peça de trabalho seja reposicionada com precisão, para que cada lado possa ser maquinado sem perder o alinhamento.
5. **Redução do tempo de preparação:** Com a utilização de dispositivos de fixação dedicados, o tempo de preparação para cada operação de maquinagem pode ser reduzido. Assim que uma fixação estiver corretamente calibrada, as peças subsequentes podem ser rapidamente carregadas e posicionadas para maquinagem.
6. **Segurança:** A fixação correta aumenta a segurança durante a maquinagem CNC. Evita que a peça de trabalho se solte ou voe durante o corte a alta velocidade, reduzindo o risco de acidentes e ferimentos.
7. **Flexibilidade:** A fixação proporciona flexibilidade para acomodar diferentes formas e tamanhos de peças de trabalho. Podem ser concebidas fixações personalizadas para peças específicas, tornando possível a maquinação de uma vasta gama de componentes.
8. **Condições de corte optimizadas:** Os dispositivos de fixação corretamente concebidos podem permitir condições de corte optimizadas, tais como o ângulo de aproximação correto para a ferramenta de corte e o acesso a caraterísticas específicas da peça de trabalho.
9. **Minimização do desperdício de material:** A fixação segura da peça de trabalho ajuda a minimizar o desperdício de material, reduzindo a probabilidade de o movimento da peça de trabalho conduzir a erros de maquinagem.
10. **Melhor acabamento superficial:** A fixação estável assegura que a peça de trabalho permanece numa posição fixa durante a maquinagem, conduzindo a cortes mais suaves e a melhores acabamentos superficiais na peça final.
A fixação adequada é um aspeto crucial da maquinagem CNC, e os maquinistas especializados prestam muita atenção à seleção ou conceção das fixações corretas para cada trabalho. As técnicas de fixação podem variar consoante o tipo de máquina CNC, as operações de maquinagem específicas e a complexidade da peça de trabalho. A fixação eficaz contribui para a eficiência global, precisão e qualidade dos processos de maquinagem CNC.
Os fabricantes podem utilizar medidas de controlo de qualidade, como testes e inspecções, para garantir que as suas peças cumprem as especificações exigidas.
Os fabricantes de maquinagem CNC podem garantir a qualidade das suas peças através da implementação de uma combinação de práticas e medidas de controlo de qualidade ao longo de todo o processo de fabrico. Aqui estão alguns passos e estratégias essenciais para garantir a qualidade das peças maquinadas em CNC:
1. **Revisão do projeto:** Realizar uma revisão completa do projeto para garantir que o modelo CAD e o programa CAM representam com precisão as especificações da peça pretendida. Verificar tolerâncias, requisitos de material e quaisquer instruções especiais.
2. **Inspeção de materiais:** Inspecionar as matérias-primas antes da maquinagem para garantir que cumprem as normas de qualidade e as propriedades dos materiais exigidas.
3. **Calibração de máquinas CNC:** Calibrar regularmente máquinas CNC para assegurar um posicionamento, movimento e medições exactos.
4. **Conceção e verificação de fixações:** Assegurar que as fixações utilizadas para segurar a peça de trabalho durante a maquinagem são corretamente concebidas, bem adaptadas à peça e firmemente fixadas.
5. **Inspeção do primeiro artigo:** Efetuar uma inspeção do primeiro artigo para a produção inicial, a fim de verificar se a primeira peça corresponde às especificações do projeto. Resolver quaisquer discrepâncias antes da produção em grande escala.
6. **Inspeção durante o processo:** Realizar inspecções regulares durante o processo para monitorizar o processo de maquinagem e detetar quaisquer desvios ou defeitos numa fase inicial. Utilizar ferramentas de medição de precisão, tais como paquímetros, micrómetros e CMM (máquinas de medição por coordenadas), conforme necessário.
7. **Inspeção do acabamento superficial:** Inspecionar o acabamento superficial das peças maquinadas para garantir que cumprem as normas de textura e aspeto exigidas.
8. **Verificação das tolerâncias:** Verificar se as peças acabadas respeitam as tolerâncias especificadas e se encontram dentro dos limites aceitáveis.
9. **Documentação de qualidade:** Manter registos detalhados e documentação dos resultados da inspeção de cada peça para garantir a rastreabilidade e a responsabilidade.
10. **Formação e mão de obra qualificada:** Assegurar que os operadores de máquinas CNC e o pessoal de controlo de qualidade tenham a formação e as competências adequadas para operar as máquinas e realizar inspecções.
11. **Controlo estatístico do processo (SPC):** Aplicar técnicas de SPC para monitorizar e controlar o processo de fabrico, identificar tendências e prevenir defeitos.
12. **Ensaios não destrutivos (NDT):** Utilizar técnicas de ensaio não destrutivas, como o ensaio ultrassónico ou a inspeção por raios X, para peças críticas, a fim de detetar defeitos internos ou inconsistências materiais.
13. **Melhoria contínua:** Incentivar uma cultura de melhoria contínua, em que o feedback das inspecções e o feedback dos clientes são utilizados para identificar áreas de melhoria e implementar acções corretivas.
14. **Certificações de qualidade:** Obter certificações de qualidade, como a ISO 9001, para demonstrar a conformidade com as normas internacionais de qualidade.
15. **Feedback e satisfação do cliente:** Ouvir o feedback do cliente e resolver prontamente quaisquer problemas de qualidade para garantir a satisfação do cliente.
Ao implementar estas práticas e medidas de controlo de qualidade, os fabricantes de maquinagem CNC podem produzir consistentemente peças de alta qualidade que satisfazem os requisitos dos clientes e as normas da indústria. A garantia de qualidade deve ser uma parte integrante do processo de fabrico, desde a conceção até à inspeção final, para assegurar a entrega bem sucedida de componentes maquinados por CNC fiáveis e precisos.
Os processos de acabamento mais comuns incluem o polimento, a pintura e a anodização.
Após o processo de maquinagem CNC, as peças são frequentemente submetidas a vários processos de acabamento para melhorar o seu aspeto, a qualidade da superfície e as caraterísticas funcionais. Alguns processos de acabamento comuns para peças maquinadas em CNC incluem:
1. **Rebarbação:** A rebarbação remove arestas vivas e rebarbas deixadas na peça após a maquinagem. Este processo aumenta a segurança, melhora a estética e evita possíveis ferimentos durante o manuseamento.
2. **Polimento:** O polimento é feito para obter um acabamento de superfície liso e refletor. É normalmente utilizado para peças decorativas ou peças que requerem um aspeto superficial de alta qualidade.
3. **Anodização:** A anodização é um processo eletroquímico que adiciona uma camada protetora de óxido às peças de alumínio. Aumenta a resistência à corrosão, melhora a dureza da superfície e permite opções de coloração.
4. **Plating:** Plating involves adding a thin layer of metal, such as chrome, nickel, or zinc, onto the surface of the part. Plating improves appearance, corrosion resistance, and wear resistance.
5. **Pintura:** A pintura oferece uma vasta gama de opções de cores e protege a superfície da peça contra factores ambientais. Pode também ser utilizada para efeitos de identificação e de marca.
6. **Revestimento a pó:** O revestimento a pó é um processo de acabamento durável e amigo do ambiente que aplica um revestimento a pó electrostaticamente à superfície da peça e depois cura-o através do calor.
7. **Electropolimento:** O electropolimento é um processo eletroquímico que remove o material da superfície, produzindo um acabamento superficial liso e brilhante. É frequentemente utilizado para peças de aço inoxidável.
8. **Passivação:** A passivação é um tratamento químico que remove o ferro livre e os contaminantes das peças de aço inoxidável, aumentando a resistência à corrosão.
9. **Gravação a laser:** A gravação a laser é utilizada para acrescentar texto, logótipos ou marcações à superfície da peça. É precisa e proporciona marcações permanentes.
10. **Acabamento vibratório:** O acabamento vibratório consiste em colocar as peças num recipiente vibratório com meios abrasivos, água e compostos de acabamento para obter uma superfície lisa e polida.
11. **Tumbling:** O Tumbling é um processo de acabamento em massa em que as peças são colocadas num tambor rotativo com meios abrasivos para remover arestas vivas e melhorar o acabamento da superfície.
12. **Revestimento de controlo térmico passivo (PTC):** Os revestimentos PTC são utilizados para o controlo térmico de componentes electrónicos, proporcionando isolamento e dissipação de calor.
13. **Gravura química:** A gravura química remove material da superfície da peça para criar desenhos ou marcações específicos.
A seleção do processo de acabamento adequado depende do material, dos requisitos de design, da aplicação pretendida e do aspeto estético desejado da peça maquinada por CNC. Os processos de acabamento não só melhoram a funcionalidade da peça, como também acrescentam valor ao produto final e melhoram a satisfação do cliente.
A velocidade de corte afecta a taxa a que o material é removido e pode ter impacto na qualidade e precisão da peça acabada.
A velocidade de corte desempenha um papel fundamental na maquinagem CNC e tem um impacto significativo na eficiência, precisão e qualidade do processo de maquinagem. A velocidade de corte refere-se à velocidade relativa à qual a ferramenta de corte se move contra a peça de trabalho durante a maquinagem. É normalmente medida em pés de superfície por minuto (SFPM) ou metros por minuto (m/min). O papel da velocidade de corte na maquinagem CNC inclui os seguintes aspectos:
1. **Taxa de remoção de material (MRR):** A velocidade de corte afecta diretamente a taxa de remoção de material, que é a quantidade de material que pode ser removida da peça num determinado período. Velocidades de corte mais elevadas resultam numa MRR mais elevada, permitindo uma produção mais rápida de peças.
2. **Tempo de ciclo:** A velocidade de corte afecta o tempo de ciclo global do processo de maquinagem CNC. Velocidades de corte mais elevadas reduzem o tempo necessário para maquinar uma peça, conduzindo a ciclos de produção mais curtos e a um aumento da produtividade.
3. **Geração de calor:** A velocidade de corte influencia a quantidade de calor gerado durante a maquinagem. Velocidades de corte mais elevadas geram mais calor devido ao aumento do atrito entre a ferramenta de corte e a peça de trabalho. O controlo do calor é crucial para evitar danos térmicos na peça de trabalho e na ferramenta.
4. **Desgaste da ferramenta:** A velocidade de corte afecta as taxas de desgaste da ferramenta. Velocidades de corte elevadas podem levar a um desgaste mais rápido da ferramenta, especialmente em aplicações de maquinagem de alta velocidade. A seleção adequada da velocidade de corte pode prolongar a vida útil da ferramenta e reduzir os custos com ferramentas.
5. **Acabamento da superfície:** A velocidade de corte influencia diretamente o acabamento da superfície da peça maquinada. Velocidades de corte óptimas podem resultar em acabamentos de superfície suaves e finos, enquanto velocidades excessivamente altas podem causar rugosidade na superfície.
6. **Formação de aparas:** A velocidade de corte influencia a formação de aparas durante a maquinagem. Velocidades de corte elevadas podem levar a um melhor controlo e evacuação da apara, reduzindo o risco de entupimento da apara e de danos na ferramenta.
7. **Forças de corte:** A velocidade de corte afecta as forças de corte exercidas sobre a ferramenta de corte e a peça de trabalho. Velocidades de corte mais elevadas podem resultar em forças de corte mais baixas, o que pode ajudar a reduzir as vibrações de maquinagem e melhorar a precisão dimensional.
8. **Maquinabilidade do material:** Diferentes materiais têm caraterísticas de maquinabilidade variáveis. A velocidade de corte deve ser optimizada para cada material, de modo a obter uma maquinação eficiente sem comprometer a vida útil da ferramenta ou o acabamento da superfície.
9. **Estabilidade da maquinagem:** A velocidade de corte tem impacto na estabilidade da maquinagem. A velocidade de corte correta minimiza as vibrações e a vibração durante a maquinagem, melhorando a estabilidade geral do processo.
10. **Consumo de energia:** A velocidade de corte afecta o consumo de energia da máquina CNC. Velocidades de corte mais elevadas requerem geralmente maior potência do motor do fuso.
Equilibrar a velocidade de corte com outros parâmetros de maquinagem, como a velocidade de avanço e a profundidade de corte, é essencial para uma maquinagem CNC bem sucedida. A escolha da velocidade de corte depende de factores como o tipo de material, o material da ferramenta, a geometria da peça, a capacidade da máquina e a produtividade pretendida. A otimização adequada da velocidade de corte pode conduzir a uma maquinagem eficiente, a custos de produção reduzidos e a peças acabadas de elevada qualidade. Os maquinistas e programadores CNC devem considerar cuidadosamente a velocidade de corte para obter os resultados de maquinagem desejados, mantendo a segurança e a precisão.
CNC machining involves removing material to create a part, while 3D printing involves adding material layer by layer to create a part.
A maquinagem CNC e a impressão 3D são ambos processos de fabrico utilizados para criar objectos físicos, mas diferem significativamente em termos dos seus princípios subjacentes, capacidades, materiais e aplicações. Eis as principais diferenças entre a maquinagem CNC e a impressão 3D:
1. **Processo e funcionamento
- Maquinação CNC: A maquinagem CNC é um processo de fabrico subtrativo. Envolve o corte de material de um bloco sólido ou peça de trabalho utilizando ferramentas de corte controladas por computador, tais como fresas, tornos, brocas e routers. A peça final é criada através da remoção de material do bloco original, deixando para trás a forma desejada.
- Impressão 3D: A impressão 3D, também conhecida como fabrico aditivo, é um processo que constrói objectos camada a camada a partir de um modelo 3D digital. Adiciona material, normalmente sob a forma de plástico, resina, metal ou outros materiais, para criar a peça final.
2. **Materiais utilizados:**
- Maquinação CNC: A maquinagem CNC pode trabalhar com uma vasta gama de materiais, incluindo metais (por exemplo, alumínio, aço, titânio), plásticos, compósitos e madeira.
- 3D Printing: 3D printing uses various materials depending on the specific 3D printing technology, including thermoplastics, photopolymers, metals, ceramics, and even food-grade materials.
3. **Flexibilidade de conceção:**
- Maquinação CNC: A maquinagem CNC oferece uma elevada flexibilidade de conceção e pode produzir peças com formas intrincadas e geometrias complexas. No entanto, certas caraterísticas do desenho podem ser limitadas pelo acesso à ferramenta e pelas capacidades de maquinagem.
- Impressão 3D: A impressão 3D destaca-se pela liberdade de design, permitindo a criação de formas complexas e orgânicas que são difíceis ou impossíveis de produzir utilizando métodos de fabrico tradicionais.
4. **Prototipagem vs. Produção
- Maquinação CNC: A maquinagem CNC é adequada tanto para a criação de protótipos como para a produção. É normalmente utilizada para produções de baixo a médio volume devido à sua eficiência e precisão.
- Impressão 3D: Embora a impressão 3D seja excelente para a criação rápida de protótipos, também é cada vez mais utilizada para a produção de baixo volume de peças especializadas e personalizadas.
5. **Velocidade e eficácia
- Maquinação CNC: A maquinagem CNC é geralmente mais rápida para produzir uma única peça em comparação com a impressão 3D, especialmente para componentes maiores e mais complexos.
- Impressão 3D: A impressão 3D é geralmente mais lenta do que a maquinagem CNC, especialmente para a produção de peças grandes e sólidas.
6. **Requisitos de pós-processamento
- Maquinação CNC: As peças maquinadas em CNC podem necessitar de pós-processamento adicional, como rebarbação, polimento e revestimento, para obter o acabamento e o aspeto da superfície pretendidos.
- Impressão 3D: Dependendo da tecnologia de impressão 3D e do material utilizado, o pós-processamento pode ser necessário para melhorar o acabamento da superfície e remover estruturas de suporte.
7. **Custos
- Maquinação CNC: A maquinagem CNC pode ser rentável para médias e grandes séries de produção, mas pode ter custos iniciais mais elevados devido às despesas com ferramentas e configuração.
- Impressão 3D: A impressão 3D é rentável para produção de baixo volume e prototipagem rápida, mas os custos unitários podem ser mais elevados do que a maquinagem CNC para produção de alto volume.
Tanto a maquinagem CNC como a impressão 3D têm os seus pontos fortes e são ferramentas valiosas no fabrico moderno. A escolha entre os dois depende de factores como a complexidade da peça, os requisitos de material, o volume de produção, a liberdade de conceção, o prazo de entrega e as considerações orçamentais. Muitas indústrias e aplicações beneficiam da utilização de uma combinação de ambos os processos para potenciar as respectivas vantagens.
Os fabricantes podem utilizar técnicas de otimização de processos, tais como o lean manufacturing e a gestão de stocks just-in-time, para reduzir os custos e melhorar a eficiência.
Os fabricantes de maquinagem CNC podem otimizar os seus processos para obterem eficiência de custos através da implementação de várias estratégias e melhores práticas que se centram na redução de desperdícios, na melhoria da produtividade e na racionalização das operações. Eis algumas das principais formas de obter eficiência de custos na maquinagem CNC:
1. **Design for Manufacturability (DFM):** Colaborar estreitamente com clientes e engenheiros de design para otimizar os designs de peças para maquinagem CNC. Ao conceber peças tendo em conta as capacidades e limitações da maquinagem CNC, é possível minimizar a complexidade, reduzir o tempo de maquinagem e diminuir os custos de material.
2. **Seleção de materiais:** Escolher materiais que sejam rentáveis e adequados para a aplicação. Considere a utilização de materiais de stock padrão para reduzir o desperdício de material e os custos.
3. **Otimizar os parâmetros de corte:** Afinar os parâmetros de corte, como a velocidade de corte, o avanço e a profundidade de corte, para obter o processo de maquinagem mais eficiente. O equilíbrio dos parâmetros de corte pode melhorar as taxas de remoção de material e prolongar a vida útil da ferramenta.
4. **Ferramentas de alta qualidade:** Investir em ferramentas de corte e porta-ferramentas de alta qualidade para melhorar o desempenho do corte, reduzir o desgaste das ferramentas e diminuir o tempo de paragem para substituição de ferramentas.
5. **Automatizar a preparação e as mudanças de ferramentas:** Implementar tecnologias de automatização para reduzir os tempos de preparação e as mudanças de ferramentas. Isto inclui a utilização de trocadores automáticos de ferramentas e trocadores de paletes para aumentar a utilização da máquina.
6. **Minimizar o tempo de inatividade:** Procurar minimizar o tempo de inatividade da máquina, optimizando os percursos das ferramentas e a sequenciação para manter a máquina em funcionamento contínuo.
7. **Aplicar os princípios da produção enxuta:** Aplicar os princípios da produção enxuta para eliminar o desperdício, reduzir os níveis de inventário e otimizar o fluxo de trabalho. Isto pode levar à redução dos prazos de entrega e ao aumento da eficiência da produção.
8. **Manutenção preventiva:** Manutenção regular das máquinas CNC para evitar avarias e minimizar o tempo de inatividade não planeado. A manutenção programada garante que as máquinas funcionem com o máximo desempenho.
9. **Sistemas de monitorização de máquinas:** Implementar sistemas de monitorização de máquinas para acompanhar o desempenho das máquinas, a utilização de ferramentas e a eficiência global do equipamento (OEE). Estes dados ajudam a identificar áreas de melhoria e otimização.
10. **Melhoria contínua:** Promover uma cultura de melhoria contínua na organização. Incentivar o feedback dos operadores e dos trabalhadores para identificar oportunidades de ganhos de eficiência e de redução de custos.
11. **Tamanhos óptimos de lotes:** Peças de lotes estrategicamente para otimizar a eficiência da produção, evitando custos de inventário excessivos.
12. **Engenharia de valor:** Rever continuamente os processos e materiais para identificar oportunidades de redução de custos sem sacrificar a qualidade ou o desempenho.
13. **Colaboração com fornecedores:** Trabalhar em estreita colaboração com fornecedores de materiais e de ferramentas para negociar preços favoráveis e garantir entregas atempadas.
14. **Normalizar os fluxos de trabalho:** Normalizar os processos de maquinagem e os fluxos de trabalho para promover a consistência e minimizar a variação na produção.
15. **Investir na formação:** Proporcionar oportunidades de formação e desenvolvimento de competências aos trabalhadores, a fim de melhorar a sua especialização e eficiência nas operações de maquinagem CNC.
Ao implementar estas estratégias e ao procurar constantemente formas de melhorar a eficiência, os fabricantes de maquinagem CNC podem otimizar os seus processos para obter eficiência de custos, aumentar a competitividade e fornecer produtos de alta qualidade aos seus clientes a um preço competitivo.
FAQs Lista de serviços de usinagem CNC
A maquinagem CNC é um processo de fabrico que utiliza máquinas controladas por computador para produzir peças precisas e complexas a partir de vários materiais.
A maquinagem CNC, que significa maquinagem de controlo numérico computorizado, é um processo de fabrico que utiliza controlos computorizados e ferramentas de corte precisas para remover material de uma peça de trabalho e criar uma peça ou produto final. Trata-se de um método de fabrico altamente automatizado e preciso que oferece inúmeras vantagens em relação à maquinagem manual tradicional.
Na maquinagem CNC, todo o processo é controlado por programas de computador, também conhecidos como programas CNC. Estes programas são criados utilizando software de desenho assistido por computador (CAD), que permite aos projectistas e engenheiros criar um modelo digital 3D da peça a fabricar. O modelo CAD serve de projeto para a peça, especificando as suas dimensões, geometria e caraterísticas.
Quando o modelo CAD está completo, o software de fabrico assistido por computador (CAM) é utilizado para converter o modelo num conjunto de instruções que a máquina CNC pode compreender. Estas instruções, conhecidas como códigos G e códigos M, ditam os movimentos das ferramentas de corte e da peça de trabalho, bem como os parâmetros de maquinação, como a velocidade de corte, a taxa de avanço e a profundidade de corte.
A máquina CNC utiliza estas instruções para controlar com precisão os movimentos das ferramentas de corte, que podem incluir berbequins, fresas de topo, tornos, tupias e muito mais. As ferramentas de corte rodam ou movem-se ao longo de múltiplos eixos para remover material da peça de trabalho, seguindo os percursos de ferramenta programados para criar a forma e as caraterísticas pretendidas.
A maquinagem CNC é altamente versátil e pode trabalhar com uma vasta gama de materiais, incluindo metais, plásticos, compósitos, madeira e muito mais. É normalmente utilizada para produzir peças complexas e intrincadas com elevada precisão e tolerâncias apertadas, o que a torna essencial em várias indústrias, incluindo a aeroespacial, automóvel, médica, eletrónica e outras.
As principais vantagens da maquinagem CNC incluem a sua capacidade de obter repetibilidade, elevada precisão e eficiência, o que a torna uma solução económica tanto para a criação de protótipos como para a produção. A maquinagem CNC é fundamental nos processos de fabrico modernos, permitindo a criação de peças de alta qualidade com resultados consistentes e prazos de entrega curtos.
- Tolerâncias locais de +.005"/-.005" na maioria das geometrias em metais, +/- 0.010" para plásticos. Varia no caso de peças grandes, especificamente quando se trata de manter a planicidade sobre peças grandes após o tratamento térmico.
- Os requisitos de acabamento para o acabamento "As Milled" terão um acabamento superficial mínimo de 125 para peças CNC.
- Todas as peças fabricadas têm uma tolerância dimensional de 0,010" e uma tolerância angular de 1°.
- Os furos roscados que não estejam explicitamente indicados como caraterísticas no modelo CAD indicado podem ser maquinados com os diâmetros especificados nesse modelo.
- Não serão aplicados quaisquer tratamentos de superfície (por exemplo, anodização, jato de areia, iridite, revestimento em pó, etc.), exceto se tiverem sido pagos e se tiverem sido especificamente reconhecidos.
A fresagem CNC e o torneamento CNC são dois processos de maquinação primários utilizados na maquinação CNC (Controlo Numérico Computadorizado). Embora ambos os processos envolvam a remoção de material para criar uma peça final, diferem nos seus métodos de funcionamento, tipos de ferramentas utilizadas e tipos de peças para as quais são mais adequados. Eis as principais diferenças entre a fresagem CNC e o torneamento CNC:
1. **Funcionamento
- Fresagem CNC: A fresagem CNC é um processo de maquinagem que utiliza ferramentas de corte rotativas para remover material de uma peça de trabalho. A ferramenta de corte move-se ao longo de vários eixos (normalmente os eixos X, Y e Z) para criar várias formas e caraterísticas 2D e 3D na peça de trabalho.
- Torneamento CNC: O torneamento CNC é um processo de maquinação que utiliza uma ferramenta de corte de ponto único para remover material de uma peça de trabalho em rotação. A ferramenta de corte é introduzida na peça de trabalho ao longo do eixo Z, resultando na criação de peças cilíndricas com simetria rotacional.
2. **Ferramentas:**
- Fresagem CNC: As fresadoras CNC utilizam uma vasta gama de ferramentas de corte, tais como fresas de topo, fresas de facear e brocas, que rodam a alta velocidade para cortar a peça de trabalho a partir de vários ângulos. As ferramentas de corte têm várias arestas de corte e podem remover material de diferentes formas.
- Torneamento CNC: Os tornos CNC utilizam uma ferramenta de corte de ponto único, como uma ferramenta de torno ou uma ferramenta de perfuração, que se move ao longo do comprimento da peça de trabalho para criar a forma desejada. A peça de trabalho roda a alta velocidade durante o processo de corte.
3. **Geometria da peça:**
- Fresagem CNC: A fresagem CNC é adequada para maquinar superfícies planas, bolsas, ranhuras e contornos complexos. É ideal para criar peças com formas 3D complexas e múltiplas caraterísticas.
- Torneamento CNC: O torneamento CNC é utilizado principalmente para criar peças cilíndricas, como veios, pinos e casquilhos. É adequado para a produção de peças com simetria rotacional.
4. **Rotação parcial:**
- Fresagem CNC: Na fresagem CNC, a peça de trabalho é tipicamente estacionária e a ferramenta de corte move-se à sua volta. Isto permite uma maior flexibilidade na criação de formas e caraterísticas complexas a partir de diferentes ângulos.
- Torneamento CNC: No torneamento CNC, a peça de trabalho roda e a ferramenta de corte desloca-se ao longo do eixo Z. A rotação da peça de trabalho permite uma maquinação eficiente e consistente de formas cilíndricas.
5. **Aplicações
- Fresagem CNC: A fresagem CNC é normalmente utilizada para produzir componentes complexos, moldes, matrizes e peças com formas complexas, como as utilizadas nas indústrias aeroespacial, automóvel e eletrónica de consumo.
- Torneamento CNC: O torneamento CNC é adequado para o fabrico de peças redondas ou cilíndricas, tais como veios, casquilhos e componentes roscados utilizados em várias indústrias, incluindo a automóvel, a médica e o equipamento industrial.
Em resumo, a fresagem CNC é utilizada para maquinar formas e caraterísticas complexas, enquanto o torneamento CNC é ideal para criar peças cilíndricas com simetria rotacional. Ambos os processos são essenciais na maquinagem CNC moderna, e a escolha entre fresagem CNC e torneamento CNC depende dos requisitos específicos do projeto e das caraterísticas da peça a fabricar.
A maquinagem CNC utiliza processos subtractivos, o que significa que a matéria-prima é maquinada até à sua forma final através da subtração e remoção de material. Os furos são efectuados, os lotes e os caminhos são perfurados e o material metálico é moldado num novo material com diferentes cones, diâmetros e formas.
No fabrico subtrativo, as formas são obtidas através da subtração de material. Isto contrasta com outros tipos de fabrico, como o fabrico aditivo, em que os materiais são adicionados, colocados em camadas e deformados de acordo com uma forma específica. Também contrasta com a moldagem por injeção, em que o material é injetado num estado diferente da matéria, utilizando um molde, e moldado numa forma específica.
A maquinagem CNC é versátil - e pode ser utilizada com vários materiais, incluindo metais, plásticos, madeira, vidro, espuma e outros materiais compostos. Esta versatilidade ajudou a tornar a maquinagem CNC uma escolha popular em todas as indústrias, permitindo aos designers e engenheiros fabricar produtos de forma eficiente e precisa.
A maquinação CNC, que significa maquinação por controlo numérico computorizado, é um processo de fabrico que utiliza controlos computorizados e ferramentas precisas para remover material de uma peça de trabalho para criar uma peça ou produto final. O processo envolve os seguintes passos:
1. **Conceção e programação:** A primeira etapa da maquinagem CNC consiste em criar um modelo digital 3D da peça a fabricar. Para o efeito, é utilizado um software de desenho assistido por computador (CAD). Uma vez concluído o projeto, o software de fabrico assistido por computador (CAM) é utilizado para gerar um programa CNC que contém instruções para a máquina CNC.
2. **Preparação da máquina:** A máquina CNC é preparada com as ferramentas de corte e os dispositivos de fixação necessários para manter a peça em segurança durante a maquinagem. O operador carrega o programa CNC no computador da máquina, que controla todo o processo de maquinagem.
3. **Carregamento da peça de trabalho:** A peça de trabalho, que é normalmente uma matéria-prima como o metal ou o plástico, é carregada na mesa ou no mandril da máquina CNC. A peça de trabalho é posicionada com exatidão de acordo com as coordenadas especificadas no programa CNC.
4. **Seleção de ferramentas:** As ferramentas de corte adequadas, tais como brocas, fresas de topo ou tornos, são selecionadas com base nas operações de maquinagem específicas necessárias para criar a peça. O programa CNC incluirá instruções para a troca de ferramentas, conforme necessário.
5. **Processo de maquinagem:** Depois de tudo estar preparado, a máquina CNC inicia o processo de maquinagem. Os controlos computorizados guiam com precisão as ferramentas de corte para remover material da peça de trabalho seguindo os percursos de ferramentas programados. As ferramentas de corte rodam ou movem-se ao longo de múltiplos eixos para criar a forma e as caraterísticas desejadas na peça.
6. **Durante o processo de maquinagem, pode ser utilizado líquido de refrigeração ou fluido de corte para arrefecer as ferramentas de corte e a peça de trabalho, reduzindo o calor e lubrificando a área de corte. Isto ajuda a evitar o desgaste da ferramenta e melhora o acabamento da superfície. As aparas, o material removido durante a maquinagem, são geridas utilizando transportadores de aparas ou sem-fins de aparas para manter a área de trabalho limpa e segura.
7. **Otimização do percurso da ferramenta:** O programa CNC assegura que a ferramenta de corte segue percursos de ferramenta óptimos para remover material de forma eficiente, mantendo a precisão dimensional e o acabamento da superfície.
8. **Controlo de qualidade:** Ao longo do processo de maquinagem, são efectuados controlos de qualidade para verificar as dimensões e assegurar que a peça final respeita as tolerâncias e especificações exigidas.
9. **Operações de acabamento:** Após a conclusão do processo de maquinagem primária, podem ser aplicadas operações secundárias, como rebarbação, polimento ou tratamentos de superfície, para obter o aspeto final e o acabamento superficial desejados.
10. **Descarga da peça acabada:** Uma vez concluída a maquinagem, a peça acabada é retirada da máquina CNC. O operador CNC inspecciona a qualidade da peça e prepara-a para qualquer pós-processamento ou montagem adicional, se necessário.
A maquinagem CNC oferece precisão, repetibilidade e a capacidade de produzir peças complexas com elevada exatidão. O processo é amplamente utilizado em várias indústrias, incluindo a aeroespacial, automóvel, médica, eletrónica e outras, para fabricar uma vasta gama de componentes e produtos.
A maquinagem CNC e a maquinagem tradicional são ambos processos de fabrico utilizados para moldar materiais em peças acabadas, mas diferem significativamente em termos de funcionamento, controlo e automação. Eis as principais diferenças entre a maquinagem CNC e a maquinagem tradicional:
1. **Controlo e automatização:**
- Maquinação CNC: A maquinação CNC (Controlo Numérico Computadorizado) é um processo moderno, controlado por computador, em que os movimentos das ferramentas de corte e da peça de trabalho são controlados com precisão por programas de computador (programas CNC). Requer uma intervenção manual mínima, uma vez que a máquina CNC segue as instruções programadas.
- Maquinação tradicional: A maquinação tradicional, também conhecida como maquinação manual ou maquinação convencional, é efectuada por maquinistas qualificados que operam as máquinas-ferramentas manualmente. O maquinista controla os movimentos e os avanços das ferramentas de corte com base na sua experiência e conhecimentos.
2. **Programabilidade
- Maquinação CNC: As máquinas CNC são altamente programáveis. Os desenhos das peças são criados utilizando software CAD (desenho assistido por computador) e o programa CNC correspondente é gerado utilizando software CAM (fabrico assistido por computador). As alterações ao projeto podem ser facilmente acomodadas através da modificação do programa CNC.
- Maquinação tradicional: Na maquinagem tradicional, as alterações aos desenhos das peças requerem normalmente ajustes manuais às definições da máquina, tais como as posições das ferramentas e as taxas de avanço. Este processo pode envolver mais tempo e esforço em comparação com a maquinagem CNC.
3. **Complexidade e precisão
- Maquinação CNC: A maquinagem CNC é excelente na produção de peças complexas com elevada precisão e tolerâncias apertadas. Pode seguir com precisão percursos de ferramentas complexos e criar peças repetíveis com qualidade consistente.
- Maquinação tradicional: A maquinagem tradicional pode atingir uma elevada precisão, mas pode ser difícil produzir peças complexas e intrincadas de forma consistente. Depende muito da capacidade e experiência do operador.
4. **Produtividade e eficiência
- Maquinação CNC: A maquinagem CNC é geralmente mais produtiva e eficiente, especialmente para grandes séries de produção. Uma vez configurado o programa CNC, a máquina CNC pode funcionar continuamente, reduzindo a intervenção humana e os tempos de ciclo.
- Maquinação tradicional: A maquinagem tradicional pode exigir mais tempo para a configuração manual, mudanças de ferramentas e ajustes, tornando-a menos eficiente para a produção de grandes volumes.
5. **Requisitos de mão de obra
- Maquinação CNC: A maquinagem CNC requer menos operadores qualificados. Uma vez preparado o programa CNC e configurada a máquina, um único operador pode supervisionar várias máquinas.
- Maquinação tradicional: A maquinação tradicional depende normalmente de maquinistas qualificados para operar cada máquina manualmente, o que pode limitar o número de máquinas que um operador pode gerir em simultâneo.
6. **Flexibilidade
- Maquinação CNC: A maquinagem CNC oferece uma maior flexibilidade para alterações e modificações de design. Permite a criação rápida de protótipos e a fácil adaptação a novos designs de peças.
- Maquinação tradicional: A maquinagem tradicional pode ser menos flexível, exigindo mais tempo e esforço para mudanças de ferramentas e ajustes para acomodar alterações de design.
Tanto a maquinação CNC como a maquinação tradicional têm as suas vantagens e são adequadas para várias aplicações. A maquinação CNC é ideal para peças complexas e de alta precisão, enquanto a maquinação tradicional pode ser preferida para produções mais pequenas, trabalhos personalizados ou operações que não requerem automação computorizada.
A maquinagem CNC é amplamente utilizada em todos os sectores. É comum na indústria aeroespacial, automóvel, eletrónica de consumo, robótica, agricultura e outros campos que utilizam frequentemente peças metálicas. É também muito utilizada em dispositivos médicos, bens domésticos, energia, petróleo e gás e outras aplicações de consumo. É um dos processos de fabrico mais comuns no mundo.
A maquinagem CNC é um processo de fabrico versátil e amplamente utilizado, que encontra aplicações em várias indústrias que exigem precisão, exatidão e capacidade de criar peças complexas. Algumas das indústrias que utilizam extensivamente a maquinagem CNC incluem:
1. **Aeroespacial:** A maquinagem CNC é crucial no fabrico aeroespacial para a produção de componentes de aeronaves, tais como peças de motores, trens de aterragem, estruturas e pás de turbinas, que exigem elevada precisão e fiabilidade.
2. **Automóvel:** A indústria automóvel depende da maquinagem CNC para fabricar componentes de motores, peças de transmissão, componentes de chassis e outras peças automóveis críticas com tolerâncias apertadas.
3. **Medicina e saúde:** A maquinagem CNC é essencial na produção de dispositivos médicos, instrumentos cirúrgicos, implantes, próteses e outros componentes médicos que exigem um controlo de qualidade rigoroso e biocompatibilidade.
4. **Eletrónica:** A maquinagem CNC é utilizada para fabricar componentes electrónicos como placas de circuitos impressos (PCB), dissipadores de calor, conectores e caixas para dispositivos electrónicos.
5. **Petróleo e gás:** A indústria do petróleo e do gás utiliza a maquinagem CNC para criar componentes para equipamento de perfuração, válvulas, bombas e outras peças necessárias para a exploração e produção.
6. **Defesa e militar:** A maquinagem CNC é crucial no fabrico de equipamento militar, incluindo armas, componentes de armas de fogo, peças de veículos blindados e componentes de aeronaves utilizados em aplicações de defesa.
7. **Energia e produção de energia:** A maquinagem CNC é utilizada na produção de peças para equipamento de produção de energia, como turbinas a gás, componentes de turbinas eólicas e equipamento hidroelétrico.
8. **Equipamento industrial:** A maquinagem CNC é utilizada para fabricar peças para várias máquinas e equipamentos industriais, incluindo bombas, válvulas, engrenagens e componentes hidráulicos.
9. **Bens de consumo:** A maquinagem CNC é utilizada na produção de bens de consumo, como aparelhos de cozinha, ferramentas domésticas, aparelhos electrónicos e artigos decorativos.
10. **Construção naval e marítima:** A maquinagem CNC é utilizada na produção de componentes de navios, equipamento marítimo e sistemas de navios para a indústria marítima.
11. **Moldes de injeção e ferramentas:** A maquinagem CNC é crucial na criação de moldes de injeção, matrizes e ferramentas para várias indústrias, incluindo a automóvel, a de embalagens e a de bens de consumo.
12. **Engenharia de precisão:** A maquinagem CNC desempenha um papel significativo na engenharia de precisão, que envolve o fabrico de componentes de alta precisão para diversas indústrias.
A versatilidade e a capacidade da maquinagem CNC para trabalhar com vários materiais, incluindo metais, plásticos, compósitos e outros, tornam-na indispensável em muitas indústrias que exigem peças de alta qualidade, personalizadas e precisas. À medida que a tecnologia continua a avançar, é provável que a maquinagem CNC venha a desempenhar um papel cada vez mais importante no fabrico moderno em cada vez mais indústrias.
- Usinagem de 5 eixos up to 26″
- Maquinação de 4 eixos até 36
- Maquinação de 3 eixos até 60″
- Tornos de eixo duplo com giro de 32 ″, diâmetro máximo de 18 ″ e mandril de 8 ″
- Máquina de corte a fio EDM with a part depth of 18″
Enquanto modelo de linguagem de IA, não tenho capacidades do mundo real, incluindo capacidades de maquinagem e torneamento CNC. No entanto, posso fornecer informações gerais sobre os processos de maquinagem e torneamento CNC.
Maquinação CNC:
A maquinagem CNC é um processo de fabrico controlado por computador utilizado para remover material de uma peça de trabalho para criar uma peça ou produto final. O processo envolve a utilização de máquinas de controlo numérico computorizado (CNC), tais como fresadoras, tornos, fresadoras e rebarbadoras CNC, que são programadas para controlar com precisão os movimentos das ferramentas de corte e das peças de trabalho. A maquinagem CNC oferece elevada precisão, repetibilidade e a capacidade de produzir peças complexas com tolerâncias apertadas. Algumas das operações comuns de maquinagem CNC incluem a fresagem, o torneamento, a perfuração e a abertura de roscas.
Torneamento CNC:
O torneamento CNC é um tipo específico de processo de maquinagem CNC que é utilizado para criar peças cilíndricas. Envolve a rotação da peça de trabalho enquanto uma ferramenta de corte de ponto único é introduzida na peça de trabalho rotativa para remover material e criar a forma desejada. O torneamento CNC é particularmente adequado para a produção de peças como veios, pinos, casquilhos e outros componentes com simetria rotacional.
Capacidades de maquinagem e torneamento CNC:
As capacidades da maquinagem e do torneamento CNC dependem de vários factores, incluindo a máquina CNC específica que está a ser utilizada, o tamanho e o material da peça de trabalho e a complexidade do design da peça. Algumas capacidades gerais dos processos de maquinagem e torneamento CNC incluem:
1. Alta precisão e exatidão: A maquinagem e o torneamento CNC permitem obter tolerâncias apertadas e dimensões consistentes das peças.
2. Versatilidade: As máquinas CNC podem trabalhar com uma vasta gama de materiais, incluindo metais, plásticos, compósitos e muito mais.
3. Geometria complexa das peças: A maquinagem e o torneamento CNC podem criar peças com formas e caraterísticas complexas.
4. Reprodutibilidade: Uma vez configurado um programa CNC, este pode ser utilizado repetidamente para produzir peças idênticas.
5. Automatização: As máquinas CNC podem funcionar de forma autónoma uma vez carregado o programa CNC, reduzindo a necessidade de intervenção manual constante.
6. Eficiência: A maquinagem e o torneamento CNC podem ser altamente eficientes tanto para o desenvolvimento de protótipos como para grandes séries de produção.
7. Maquinação multieixos: As máquinas CNC avançadas podem executar maquinação multieixos, permitindo a produção de peças complexas numa única configuração.
É importante notar que as capacidades específicas de maquinagem e torneamento CNC podem variar consoante o equipamento e a experiência das instalações de fabrico. Os fabricantes listam frequentemente as suas capacidades, equipamentos e materiais específicos nos seus sítios Web ou materiais promocionais para apresentar as suas ofertas a potenciais clientes.
Oferecemos prazos de entrega rápidos para peças de fabrico rápido, com muitas peças disponíveis em 3-4 dias. Oferecemos uma opção de expedição e a nossa equipa trabalha em estreita colaboração consigo para cumprir os seus prazos mais urgentes.
Como modelo de linguagem de IA, não ofereço quaisquer serviços, incluindo maquinagem CNC de torneamento rápido. A minha principal função é fornecer informações e responder a perguntas com o melhor dos meus conhecimentos e capacidades.
A maquinagem CNC de rotação rápida é um serviço prestado por certas empresas de fabrico ou oficinas de maquinagem. Estas empresas são especializadas em fornecer serviços de maquinagem CNC rápidos e expeditos para cumprir prazos apertados e requisitos de produção rápidos. A maquinagem CNC de torneamento rápido é particularmente útil para a criação rápida de protótipos, necessidades urgentes de produção e tiragens de produção de baixo a médio volume.
Se procura serviços de maquinagem CNC de torneamento rápido, recomendo que procure oficinas de maquinagem CNC de renome ou fabricantes que ofereçam explicitamente serviços de torneamento rápido ou de maquinagem rápida. Muitas empresas de fabrico anunciam os seus tempos de execução e capacidades de prototipagem rápida nos seus sítios Web ou através de pedidos de informação dos clientes.
Certifique-se sempre de que tem em conta a experiência, a reputação, a qualidade do trabalho e as opiniões dos clientes da empresa antes de escolher um fornecedor de serviços de maquinagem CNC de torneamento rápido. Além disso, o fornecimento de especificações claras e detalhadas para o seu projeto pode ajudar a garantir que a oficina de maquinagem pode satisfazer os seus requisitos de forma eficiente.
Os materiais mais comuns incluem metais (como o alumínio, o aço e o latão), plásticos e madeira.
A maquinagem CNC é um processo de fabrico versátil que pode trabalhar com uma vasta gama de materiais. A escolha do material depende dos requisitos específicos da peça, tais como a utilização pretendida, as propriedades mecânicas, a estética e os factores ambientais. Alguns dos materiais mais comuns utilizados na maquinagem CNC incluem:
1. **Metais
- Alumínio: Leve, resistente à corrosão e com uma boa relação resistência/peso. Amplamente utilizado nas indústrias aeroespacial, automóvel e eletrónica de consumo.
- Aço: Oferece uma excelente resistência e durabilidade, sendo normalmente utilizado em várias aplicações industriais.
- Aço inoxidável: Resistente à corrosão e a temperaturas elevadas, adequado para aplicações alimentares, médicas e marítimas.
- Latão: Durável e com boa condutividade eléctrica e térmica. É frequentemente utilizado em eletrónica e canalizações.
- Cobre: Elevada condutividade eléctrica e térmica, utilizado em componentes eléctricos e permutadores de calor.
- Titânio: Leve, forte e resistente à corrosão, normalmente utilizado em aplicações aeroespaciais e médicas.
2. **Plásticos:**
- ABS (Acrilonitrilo Butadieno Estireno): Durável e versátil, utilizado em produtos de consumo, automóveis e eletrónica.
- Policarbonato (PC): Transparente e resistente ao impacto, normalmente utilizado em aplicações automóveis, médicas e de segurança.
- Nylon (poliamida): Alta resistência e flexibilidade, utilizado em engrenagens, rolamentos e componentes estruturais.
- PVC (cloreto de polivinilo): Rígido e fácil de processar, utilizado na construção e em aplicações eléctricas.
- PEEK (Poliéter Éter Cetona): Termoplástico de elevado desempenho, utilizado em aplicações aeroespaciais, médicas e de engenharia.
3. **Compostos:**
- Fibra de carbono: Leve e resistente, utilizada nas indústrias aeroespacial, de equipamento desportivo e automóvel.
- Fibra de vidro: Resistente à corrosão e utilizada em aplicações marítimas e aeroespaciais.
- G10/FR4: Laminado à base de epóxi, normalmente utilizado em componentes eléctricos e electrónicos.
4. **Madeira:**
- Vários tipos de madeira podem ser utilizados na maquinagem CNC para fins decorativos, artísticos e funcionais.
5. **Outros materiais
- Cerâmica: Used in high-temperature applications, electronics, and cutting tools.
- Espuma: Utilizada para aplicações de prototipagem, modelação e embalagem.
É importante notar que diferentes máquinas CNC e ferramentas de corte podem ter capacidades e limitações específicas com determinados materiais. Além disso, alguns materiais podem exigir considerações especiais durante a maquinagem, tais como velocidades de corte, avanços e ferramentas adequados para obter os resultados desejados. Os fabricantes fornecem frequentemente diretrizes para a seleção de materiais e parâmetros de maquinagem com base no seu equipamento e experiência.
Os tipos mais comuns incluem moinhos CNC, tornos e routers.
Na indústria transformadora são normalmente utilizados vários tipos de máquinas CNC, cada uma especializada em operações e aplicações de maquinagem específicas. A escolha da máquina CNC depende do tipo de peça a ser fabricada, do material utilizado, do nível de precisão exigido e do volume de produção. Algumas das máquinas CNC mais utilizadas na indústria transformadora incluem:
1. **Fresadora CNC:** As fresadoras CNC utilizam ferramentas de corte rotativas para remover material de uma peça de trabalho e criar formas e caraterísticas 3D complexas. São amplamente utilizadas para maquinar superfícies planas, ranhuras, bolsas e contornos. As fresadoras CNC podem ser verticais ou horizontais e estão disponíveis em vários tamanhos para se adaptarem a diferentes tamanhos de peças e necessidades de produção.
2. **Torno CNC:** Os tornos CNC são utilizados para tornear peças cilíndricas. A peça de trabalho é rodada e uma ferramenta de corte de ponto único é introduzida na peça de trabalho para remover material e criar simetria rotacional. Os tornos CNC são usados para produzir peças como eixos, hastes e buchas.
3. **Router CNC:** Os routers CNC são especializados no corte, modelação e gravação de materiais como a madeira, o plástico e os materiais compósitos. São normalmente utilizadas em aplicações de trabalho da madeira, sinalização e prototipagem.
4. **Cortador de plasma CNC:** Os cortadores de plasma CNC utilizam um jato de gás ionizado de alta velocidade para cortar materiais como o aço, o aço inoxidável e o alumínio. São normalmente utilizados no fabrico de metais e na indústria automóvel.
5. **Cortador a laser CNC:** Os cortadores a laser CNC utilizam um laser de alta potência para cortar materiais como metal, plástico e madeira. Oferecem uma elevada precisão e são utilizados em várias indústrias, incluindo a aeroespacial, a eletrónica e a sinalização.
6. **Máquina CNC EDM (Electrical Discharge Machining):** As máquinas CNC EDM utilizam faíscas de descarga eléctrica para remover material de uma peça de trabalho. São frequentemente utilizadas para maquinar formas complexas e materiais endurecidos.
7. **Torno CNC de tipo suíço:** Os tornos de tipo suíço são tornos CNC especializados, utilizados para o torneamento de alta precisão de peças pequenas e complexas. São normalmente utilizados nas indústrias médica e relojoeira.
8. **Rectificadoras CNC:** As rectificadoras CNC são utilizadas para obter acabamentos de superfície de alta precisão e tolerâncias apertadas nas peças. São normalmente utilizadas para retificar componentes metálicos.
9. **Cortador de jato de água CNC:** Os cortadores de jato de água CNC utilizam um fluxo de água a alta pressão misturado com partículas abrasivas para cortar vários materiais, incluindo metais, pedra e vidro.
10. **Impressora CNC 3D:** Embora não sejam uma máquina CNC tradicional, as impressoras CNC 3D utilizam o controlo por computador para fabricar aditivamente peças camada a camada. São utilizadas para prototipagem rápida e produção de baixo volume de peças de plástico e metal.
Estes são apenas alguns exemplos dos muitos tipos de máquinas CNC disponíveis. Cada tipo de máquina CNC oferece capacidades específicas para responder a diversas necessidades de fabrico e desempenha um papel vital nos processos de fabrico modernos em diferentes indústrias.
O software CAD é utilizado para criar um modelo 3D
O software de desenho assistido por computador (CAD) desempenha um papel crucial na maquinagem CNC, uma vez que serve de ponto de partida para a criação do modelo digital da peça a fabricar. O software CAD é utilizado por engenheiros e designers para conceber e modelar objectos 2D e 3D com dimensões e geometrias precisas. O seu papel na maquinagem CNC inclui os seguintes aspectos fundamentais:
1. **Conceção e modelação de peças:** O software CAD permite aos projectistas criar modelos 3D detalhados e precisos da peça que pretendem fabricar. O software fornece um espaço de trabalho virtual onde os utilizadores podem esboçar, extrudir, revolver e aplicar várias operações para criar formas e caraterísticas complexas.
2. **Precisão dimensional:** O software CAD garante que o modelo digital da peça respeita as dimensões, as tolerâncias e as especificações de conceção pretendidas. Os projectistas podem introduzir medidas e restrições precisas, garantindo a precisão da peça final.
3. **Geometria complexa:** O software CAD permite a criação de geometrias de peças intrincadas e complexas que podem não ser viáveis com os métodos tradicionais de desenho manual. Permite aos projectistas visualizar e modelar peças com superfícies de forma livre, curvas, filetes, chanfros e outras caraterísticas.
4. **Modelação de conjuntos:** Na maquinagem CNC, os conjuntos podem envolver várias peças que têm de se encaixar com precisão. O software CAD facilita a modelação e o teste de montagens, garantindo o ajuste e a funcionalidade corretos.
5. **Prototipagem rápida:** O software CAD facilita a prototipagem rápida, permitindo aos projectistas criar rapidamente modelos digitais de peças. Estes modelos podem ser utilizados para criar protótipos físicos utilizando a impressão 3D ou outros métodos de prototipagem rápida.
6. **Validação e simulação do projeto:** Alguns programas CAD oferecem capacidades de simulação, permitindo aos projectistas efetuar análises de elementos finitos (FEA) e outros testes para validar a integridade estrutural e o desempenho do projeto em diferentes condições.
7. **Integração CAM:** O software CAD integra-se frequentemente com o software de fabrico assistido por computador (CAM). O software CAM utiliza o modelo CAD para gerar percursos de ferramentas CNC e instruções (códigos G e códigos M) que a máquina CNC pode compreender e seguir durante o processo de maquinagem.
8. **Exportação de ficheiros:** O software CAD permite a exportação do modelo concebido em vários formatos de ficheiros, como STEP, IGES ou STL, que podem ser importados para o software CAM para programação CNC.
Utilizando software CAD, os projectistas podem criar modelos digitais detalhados e precisos de peças, permitindo processos de maquinagem CNC eficientes e precisos. A integração CAD/CAM simplifica todo o fluxo de trabalho de fabrico, reduzindo os erros manuais, encurtando os prazos de entrega e melhorando a produtividade e a qualidade globais das operações de maquinagem CNC.
As peças maquinadas CNC são utilizadas numa vasta gama de indústrias, como a aeroespacial, a automóvel e a médica.
As peças maquinadas CNC são amplamente utilizadas em várias indústrias devido à sua elevada precisão, qualidade e versatilidade. Algumas das aplicações comuns das peças maquinadas CNC incluem:
1. **Aeroespacial:** As peças maquinadas por CNC são essenciais na indústria aeroespacial para o fabrico de componentes de aeronaves, tais como peças de motores, pás de turbinas, suportes e componentes estruturais. A elevada precisão e fiabilidade da maquinagem CNC são fundamentais na engenharia aeroespacial.
2. **Automóvel:** As peças maquinadas por CNC são utilizadas na indústria automóvel para produzir componentes de motores, peças de transmissão, pinças de travão, componentes de direção e outras peças automóveis críticas.
3. **Medicina e saúde:** As peças maquinadas por CNC são utilizadas no domínio médico para o fabrico de dispositivos médicos, instrumentos cirúrgicos, implantes ortopédicos, componentes dentários e próteses, que exigem elevada precisão e biocompatibilidade.
4. **Eletrónica:** As peças maquinadas por CNC são utilizadas na eletrónica para produzir componentes complexos como PCB (placas de circuitos impressos), conectores, dissipadores de calor e caixas para dispositivos electrónicos.
5. **Petróleo e gás:** A indústria do petróleo e do gás depende de peças maquinadas por CNC para o fabrico de equipamento de perfuração, válvulas, acessórios e outros componentes utilizados nos processos de exploração e extração.
6. **Equipamento industrial:** As peças maquinadas por CNC são utilizadas na produção de várias máquinas e equipamentos industriais, incluindo bombas, válvulas, engrenagens e componentes hidráulicos.
7. **Defesa e exército:** As peças maquinadas por CNC são cruciais no fabrico de equipamento militar, incluindo armas de fogo, componentes de armas, peças de veículos blindados e componentes de aeronaves.
8. **Bens de consumo:** As peças maquinadas por CNC são utilizadas na produção de bens de consumo, como aparelhos de cozinha, ferramentas domésticas, aparelhos electrónicos e artigos decorativos.
9. **Construção naval e marítima:** As peças maquinadas por CNC são utilizadas no fabrico de componentes de navios, equipamento marítimo e sistemas de navios para a indústria marítima.
10. **Máquinas de embalagem:** As peças maquinadas em CNC são utilizadas na produção de componentes de máquinas de embalagem, garantindo processos de embalagem precisos e fiáveis.
11. **Energias renováveis:** As peças maquinadas por CNC são utilizadas no sector das energias renováveis para a produção de componentes de turbinas eólicas, painéis solares e sistemas de energia hidroelétrica.
12. **Robótica:** As peças maquinadas por CNC são essenciais para o fabrico de sistemas robóticos, braços robóticos e equipamento de automatização.
Estas aplicações são apenas alguns exemplos, e as peças maquinadas em CNC também têm uma vasta gama de utilizações em várias outras indústrias. A capacidade de produzir peças personalizadas, de alta qualidade e de conceção complexa com a maquinagem CNC torna-a uma tecnologia versátil e indispensável nos processos de fabrico modernos.
A fresagem CNC envolve o corte de material para criar uma forma 3D, enquanto o torneamento CNC envolve a rotação do material para criar formas cilíndricas.
A fresagem CNC e o torneamento CNC são dois processos de maquinação distintos utilizados na maquinação CNC (Controlo Numérico Computadorizado). Embora ambos os processos envolvam a remoção de material de uma peça de trabalho para criar uma peça final, têm diferentes métodos de operação, ferramentas e tipos de peças para os quais são mais adequados. Eis as principais diferenças entre a fresagem CNC e o torneamento CNC:
Fresagem CNC:
1. **Operação:** A fresagem CNC é um processo de maquinagem que utiliza ferramentas de corte rotativas para remover material de uma peça de trabalho. A ferramenta de corte move-se ao longo de vários eixos (normalmente os eixos X, Y e Z) para criar várias formas e caraterísticas 2D e 3D na peça de trabalho.
2. **Ferramentas:** As fresadoras CNC utilizam uma vasta gama de ferramentas de corte, tais como fresas de topo, fresas de facear e brocas, que rodam a alta velocidade para cortar a peça de trabalho a partir de diferentes ângulos. As ferramentas de corte têm várias arestas e podem remover material de várias formas.
3. **Geometria da peça:** A fresagem CNC é adequada para maquinar superfícies planas, bolsas, ranhuras e contornos complexos. É ideal para criar peças com formas 3D complexas e múltiplas caraterísticas.
4. **Rotação da peça:** Na fresagem CNC, a peça de trabalho é normalmente estacionária e a ferramenta de corte move-se à sua volta. Isto permite uma maior flexibilidade na criação de formas e caraterísticas complexas a partir de diferentes ângulos.
Torneamento CNC:
1. **Funcionamento:** O torneamento CNC é um processo de maquinagem que utiliza uma ferramenta de corte de ponto único para remover material de uma peça de trabalho em rotação. A ferramenta de corte é introduzida na peça de trabalho ao longo do eixo Z, resultando na criação de peças cilíndricas com simetria rotacional.
2. **Ferramentas:** Os tornos CNC utilizam uma ferramenta de corte de ponto único, como uma ferramenta de torno ou uma ferramenta de perfuração, que se move ao longo do comprimento da peça de trabalho para criar a forma desejada. A peça roda a alta velocidade durante o processo de corte.
3. **Geometria da peça:** O torneamento CNC é utilizado principalmente para criar peças cilíndricas, tais como veios, pinos e casquilhos. É adequado para a produção de peças com simetria rotacional.
4. **Rotação da peça:** No torneamento CNC, a peça roda e a ferramenta de corte desloca-se ao longo do eixo Z. A rotação da peça permite uma maquinação eficiente e consistente de formas cilíndricas.
Em resumo, a fresagem CNC é utilizada para maquinar formas complexas, contornos intrincados e peças com múltiplas caraterísticas, enquanto o torneamento CNC é ideal para produzir peças cilíndricas com simetria rotacional. Ambos os processos são essenciais na maquinagem CNC e complementam-se mutuamente para satisfazer uma vasta gama de necessidades de fabrico. A escolha entre a fresagem CNC e o torneamento CNC depende dos requisitos específicos do projeto e das caraterísticas da peça a ser fabricada.