Equipamento de produção e processamento de peças de metal plástico





The production of Plastic Metal Parts is a complex process that requires specialized equipment to produce high-quality molds. The equipment used for injection mold production can be roughly divided into three categories: design and CAD software, processing equipment, and testing equipment.
Design and CAD software are crucial for the production of plastic and metal parts. For example, design software such as SolidWorks is used to create 3D models of the parts that the mold will produce. This 3D model is then imported into CAD software such as AutoCAD to create mold designs. CAD software is used to create detailed plastic metal parts designs, including the shape and size of the part, the location of parts points, and the placement of parts.
Processing equipment is used to manufacture the plastic metal parts itself. This type of equipment includes various machines such as CNC milling machines, lathes, EDM machines, 3D printer, and grinders. CNC milling machines are used to cut plastic metal parts from steel blocks, while lathes are used to process the cylindrical parts of molds. EDM machines use electrical discharge to cut complex shapes in steel, while grinding machines are used to polish the surface of plastic metal parts to achieve the desired smoothness.
Testing equipment is used to ensure that the plastic metal parts meet the expected specifications. These devices include a range of measuring tools such as micrometers, calipers, and altimeters. Coordinate measuring machines (CMM) are also used to measure plastic metal components to ensure they meet the required tolerances.
Overall, the equipment used for plastic metal parts production is specialized and requires a high level of professional knowledge to operate. The combination of design software, processing equipment, and testing equipment is essential for producing high-quality plastic metal parts that meet strict customer specifications. Manufacturers must invest in the right equipment and expertise to ensure they can produce plastic metal parts efficiently and economically.
Equipamento de moldagem por injeção de peças plásticas
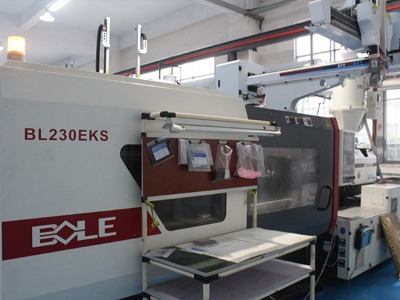
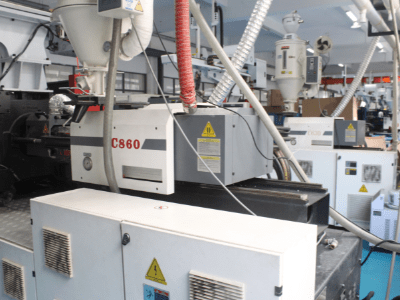
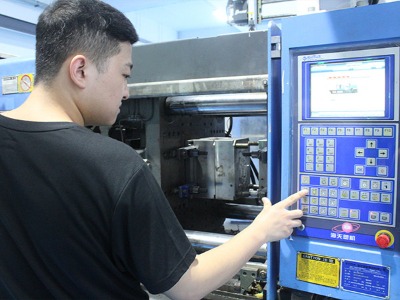
Plastic injection molding is a manufacturing process that involves melting plastic particles and injecting them into a mold to create specific shapes or parts. To achieve the expected results, plastic injection molding services require several pieces of equipment.
The main equipment required for plastic injection molding is an injection molding machine. This machine is responsible for melting and injecting plastic particles into the mold to manufacture the desired shape or part. According to the specific needs of the manufacturer, injection molding machines come in different sizes and shapes.
To ensure that plastic pellets are correctly fed into the injection molding machine, auxiliary equipment such as hoppers, dryers, and conveyors are also required. The hopper is a place to store plastic pellets, and the dryer ensures that the pellets are dry and free of any moisture. The conveyor belt moves the particles from the hopper to the injection molding machine.
Mold is another key equipment required for plastic injection molding services. A mold is a place where melted plastic is injected to manufacture the desired shape or part. The mold consists of two halves, namely the cavity side and the core side. The cavity side is where the plastic flows, while the core side shapes the interior of the part. Molds can be made of various materials, such as steel, aluminum, or copper alloys.
Cooling equipment is also necessary for plastic injection molding services. These devices are responsible for cooling the plastic after it is injected into the mold to prevent deformation and ensure that the parts maintain their shape. Cooling equipment can take various forms, including water-cooled systems or air-cooled systems.
Quality control equipment is crucial for ensuring that the produced plastic parts meet the expected specifications. These devices include measuring tools such as calipers, gauges, and microscopes. These tools are used to verify the dimensions and tolerances of parts and ensure they meet customer requirements.
In short, plastic injection molding services require several pieces of equipment to consistently produce high-quality parts. These devices include injection molding machines, auxiliary equipment, molds, cooling equipment, and quality control equipment. With the right equipment and professional knowledge, plastic injection molding can be an efficient and economical way to produce plastic parts.
Plastic Metal Parts production and assembly Workshop
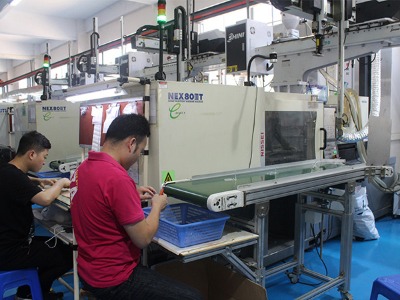
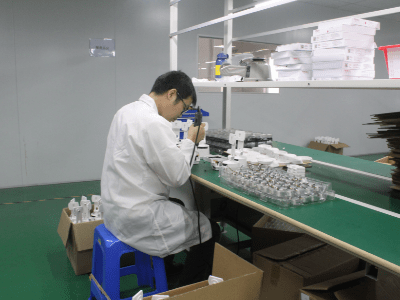
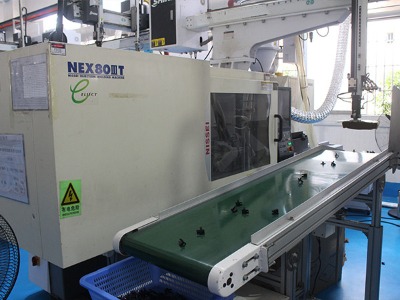
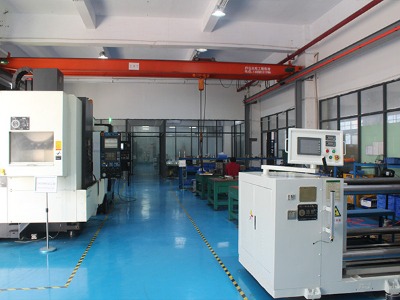
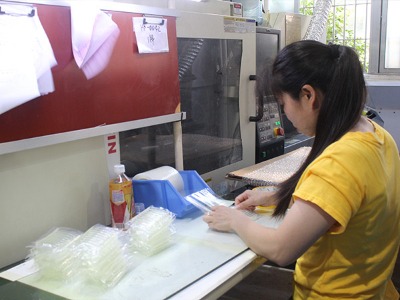
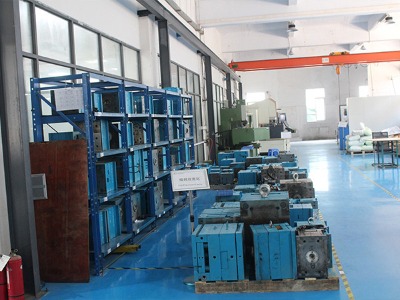