Materiais de peças plásticas de resina fenólica de baquelite
We focus on crafting and refining Bakelite phenolic resin plastic components services, providing customized solutions that cater specifically to our clients' needs. Our deep experience in creating tailored Bakelite parts helps us understand designs and specifications precisely, ensuring every product not only meets but often surpasses expectations. By using advanced techniques and equipment, we turn raw materials into durable, high-quality parts perfect for many uses. Whether it's for electrical insulation, automotive parts, furniture, or other applications, our Bakelite products are built to endure tough conditions while maintaining top performance.
Bakelite, a leading type of phenolic resin plastic, is famous for its excellent electrical insulation, heat resistance, and mechanical strength. This makes it a great choice for various uses. At our company, we are dedicated to quality and reliability. We excel in processing Bakelite materials through cutting, molding, and curing, giving us the flexibility to modify material properties to meet specific performance requirements. Our main goal is your satisfaction and dependability, and we are confident that our Bakelite production and processing services will go beyond what you expect.
Peças plásticas da baquelite que fazem o serviço
Be good at product structure optimization and greatly reduce the cost of Bakelite Plastic Parts Materials
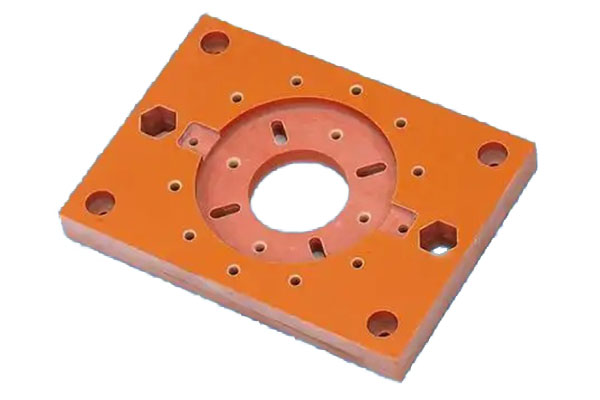
Plastic Design
Design Estético e Estrutural
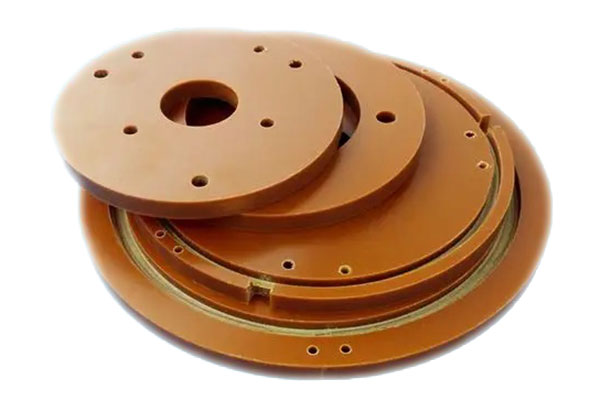
Fabricação de moldes
Design, Confirmação de Facilidade de Manufatura
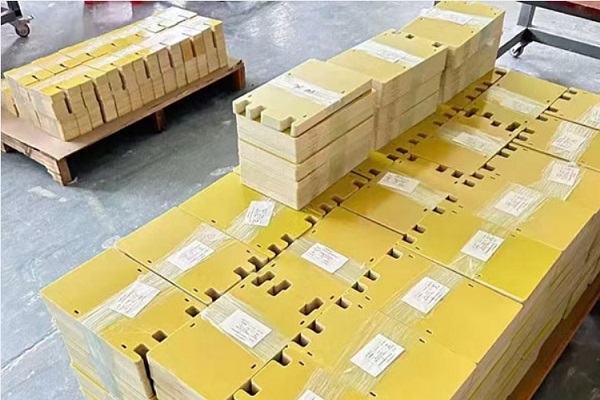
Produção de Produto
Imported, high-speed equipment
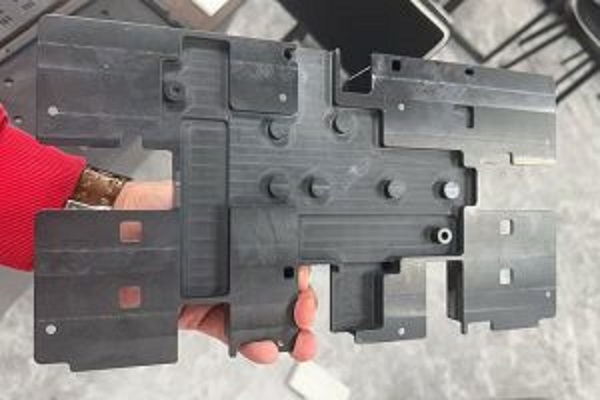
Montagem do Produto
Matéria-Prima, Inspeção e Montagem
Bakelite Manufacturing Process: CNC Machining and Injection Molding
The fabrication of Baquelite, a thermosetting phenolic resin, transcends mere manufacturing; it's a tightly orchestrated interplay of artisanal precision and advanced technological prowess, yielding components of exceptional durability and dimensional fidelity. Our proprietary methodology integrates CNC machining with injection molding, a synergistic approach maximizing both precision and throughput.
CNC machining constitutes a critical juncture in the Bakelite production lifecycle. This process, governed by sophisticated CAM software, allows for the realization of intricately detailed geometries and the attainment of exceptionally tight tolerances, far exceeding the capabilities of traditional methods. The inherent plasticity of the pre-cured Bakelite, while demanding precise control of feed rates and cutting parameters to avoid thermal degradation, allows for the creation of bespoke components tailored to exacting client specifications, encompassing complex curvatures and micro-features previously unattainable. The resultant surface finish, characterized by its inherent smoothness and dimensional accuracy, minimizes the need for post-machining operations.
Injection molding, however, represents the cornerstone of high-volume Bakelite production. Employing a precisely controlled process involving the rheological manipulation of the molten Bakelite resin under high pressure, we achieve consistent part quality and exceptional repeatability. Mold design, a critical factor in this process, necessitates a deep understanding of resin flow dynamics and thermal transfer properties to mitigate issues such as sink marks, weld lines, and residual stresses. Our advanced mold designs, incorporating features such as optimized gating systems and cooling channels, ensure a homogenous final product, free from internal defects and capable of withstanding rigorous performance testing.
The convergence of CNC machining's bespoke capabilities and injection molding's high-volume efficiency establishes a comprehensive Bakelite production paradigm. This integrated approach enables us to deliver a spectrum of solutions, from highly customized, low-volume components requiring intricate detailing to high-throughput manufacturing runs for mass-market applications, consistently exceeding client expectations in terms of quality, precision, and delivery timelines. Our commitment to continuous improvement, driven by ongoing R&D efforts, ensures our position at the forefront of Bakelite fabrication technology.
FAQ About Bakelite Plastic Parts
Bakelite, a type of phenolic resin plastic, was first created in 1907 by Leo Baekeland, a talented Belgian chemist. This unique material is a thermoset plastic, which means it hardens permanently when heated and can't be reshaped after cooling down.
What makes Bakelite stand out is its excellent electrical insulation properties, heat resistance, and strong mechanical strength. These features make it perfect for various uses. For example, it's often used in making electrical components, kitchen utensils, and even some early forms of radio casings.
Bakelite has been a versatile material since its creation. First, it served as an electrical insulator in devices like switches, sockets, and circuit boards. As time went on, it found its way into car parts, furniture, jewelry, and decorative items. Its toughness against heat and chemicals has made Bakelite a top choice for both industry and everyday products.
Bakelite stands out among plastics due to its unique mix of features. It's a thermoset plastic, which means it can resist heat and chemicals, making it perfect for jobs that need longevity and dependability. What's more, Bakelite has an eye-catching look with a smooth, shiny surface. This surface can be clear or opaque, depending on how it's made and processed.
Yes, you can paint or stain Bakelite to get the color or finish you want. But remember, you need to use paints or stains that are compatible with Bakelite to avoid damaging it. Some paints or stains might not stick well to Bakelite and could make it crack or change color. It's a good idea to ask a professional for advice or test a small area first before painting or staining a larger part.
Bakelite stands out for its unique look and characteristics. You'll notice it has a smooth, shiny surface with a special feel and hue. Genuine Bakelite items might carry the Bakelite brand or symbol, making them easier to spot. Besides looks, you can confirm Bakelite through chemical tests. This means taking a tiny piece of the material and seeing how it reacts when exposed to certain chemicals.
Bakelite, a type of phenolic plastic, is a favorite in many industries because of its great physical and chemical properties. You’ll find it in electrical insulation, cookware, cutlery, electronics, toys, and furniture.
One common way to make Bakelite parts is through injection molding. This method lets manufacturers quickly produce lots of parts with the same shape and smooth surfaces.
Here’s how it works: First, the Bakelite material is melted under heat and pressure in an injection molding machine. Then, it’s pushed through the nozzle into the mold cavity. Finally, it cools down to form the needed parts.
As market demands keep changing, more and more people are asking for customized products. For Bakelite items, making them to fit exactly what a customer wants is becoming a big trend.
When we talk about custom production, it includes several steps: designing the mold, picking the right materials, doing the injection molding, and finishing touches afterward. Keeping in close touch with customers is key to make sure the final product matches their expectations.
Not only do we focus on the basics of injection molding, but we also offer extra touches like painting the surface, adding a silicone coat, or even electroplating. These steps help improve how the product looks and works.
Bakelite is a popular material in the electrical industry because it's a great insulator. It's used to make things like insulation boards, tubes, and other insulating components.
When companies make these parts, they have to make sure the Bakelite meets certain standards for both its electrical properties and physical strength. They don't just rely on one method; besides injection molding, they might also use lamination or other molding techniques to get the job done.
Testing and quality control are key steps in making sure these parts perform well.