Materiais de peças metálicas de aço
Aço is an alloy made of iron and carbon, with a carbon content ranging from 0.0218% to 2.11%. It also contains small amounts of silicon, manganese, sulfur, and phosphorus. To keep it flexible and plastic, the carbon content is usually kept below 1.7%. Adding these elements not only boosts steel's strength and hardness but also improves its workability and resistance to corrosion. For instance, silicon enhances the strength and heat resistance of steel, while manganese increases its toughness and wear resistance. Sulfur and phosphorus are impurities in steel that need to be carefully controlled to prevent brittleness and cold shortness.
Steel is widely used in many areas because of its high strength, wear resistance, heat resistance, and corrosion resistance. It's found in buildings, bridges, cars, ships, power equipment, chemical equipment, and medical devices. In construction, steel is used for beams, floors, roofs, and reinforcement in concrete structures. In bridge building, it's used for piers, decks, and cables to ensure strength and stability. In car manufacturing, steel is used for bodies, chassis, and engines, providing safety and durability. In shipbuilding, it's used for hulls, decks, and bulkheads to maintain structural strength and buoyancy. In power equipment, steel is used for transformers, motors, and transmission towers to ensure stable and safe electricity transmission. In chemical equipment, it's used for reactors, tanks, and pipes to meet high temperature, pressure, and corrosion requirements. In medical devices, steel is used for surgical instruments and implants to ensure accuracy and safety in medical procedures.
Peças de metal de aço que fazem o serviço
Be good at product structure optimization and greatly reduce the cost of Steel Metal Parts Materials
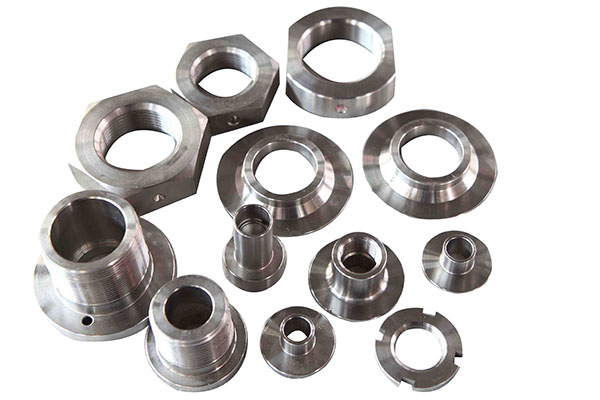
Design da peça
Design Estético e Estrutural
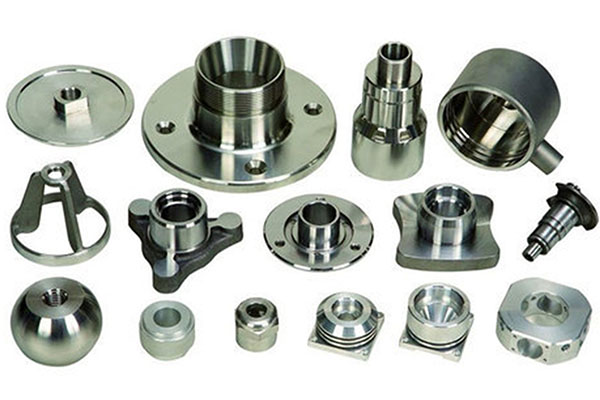
Fabricação de moldes
Design, Confirmação de Facilidade de Manufatura
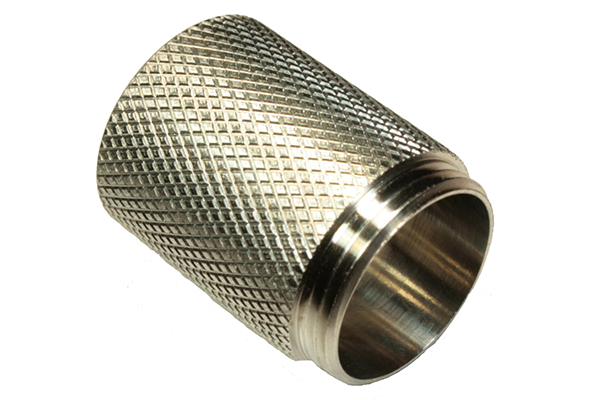
Produção de Produto
Equipamento de Alta Velocidade Importado
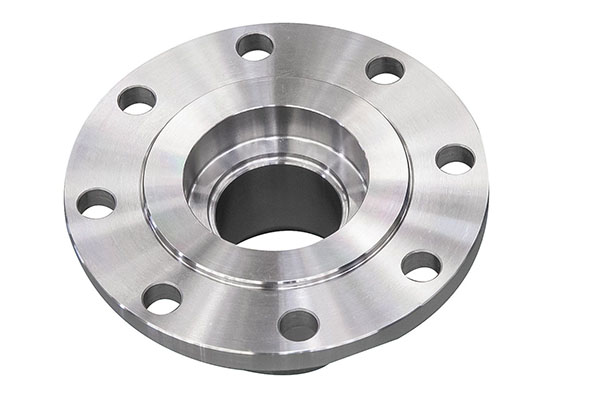
Montagem do Produto
Matéria-Prima, Inspeção e Montagem
Model classification of Steel Metal Parts Materials
Including low carbon steel (C ≤ 0.25%), medium carbon steel (0.25% ≤ C ≤ 0.60%), and high carbon steel (C ≥ 0.60%). Low carbon steel has good plasticity and weldability, and is commonly used in the manufacture of cold-rolled steel plates, cold drawn steel wires, and other products; Medium carbon steel has high strength and hardness, and is commonly used in the manufacturing of mechanical parts, axles, etc; High carbon steel has high strength and wear resistance, and is commonly used in the manufacture of cutting tools, springs, etc. Specific models such as Q235, 45 #, etc. Q235 is a commonly used low-carbon steel with excellent comprehensive performance, widely used in building structures and mechanical manufacturing. 45 # steel is a medium carbon steel with high strength and hardness, suitable for manufacturing mechanical parts and tools.
Adding one or several alloying elements, such as chromium, nickel, molybdenum, titanium, etc., to carbon steel to improve its mechanical and special properties. Alloy steel can be divided into low-alloy steel (≤ 5%), medium alloy steel (5%~10%), and high alloy steel (>10%) based on the total content of alloying elements. Specific models such as 40Cr, 30CrMo, etc. 40Cr is a low-alloy steel with good strength and toughness, suitable for manufacturing mechanical parts such as gears and bearings. 30CrMo is a medium alloy steel with excellent wear resistance and fatigue resistance, suitable for manufacturing high-strength bolts, nuts and other fasteners.
The chromium content is at least 10.5%, which has good corrosion resistance and is commonly used in the manufacture of kitchenware, chemical containers, etc. Specific models such as 304, 316L, etc. 304 stainless steel is a universal stainless steel with good corrosion resistance and processing performance, widely used in food processing equipment and medical devices. 316L stainless steel is an ultra-low carbon stainless steel with excellent corrosion resistance and welding performance, suitable for marine environments and chemical industries.
Including carbon tool steel, alloy tool steel, and high-speed tool steel, mainly used for manufacturing cutting tools, molds, etc. Specific models such as T10A, W18Cr4V, etc. T10A is a carbon tool steel with good hardness and wear resistance, suitable for manufacturing hand tools and small cutting tools. W18Cr4V is a high-speed tool steel with extremely high hardness and red hardness, suitable for manufacturing high-speed cutting tools and stamping dies.
Including engineering steel, carburizing steel, cold plastic forming steel, etc., mainly used for building structures and mechanical manufacturing. Specific models such as 16Mn, 20CrMnTi, etc. 16Mn is an engineering steel with high strength and toughness, suitable for large-scale building structures and bridge construction. 20CrMnTi is a carburizing steel with good surface hardness and core toughness, suitable for manufacturing gears and bearings.
Machining Process of Steel Metal Parts
Forging is a process that changes the shape and internal structure of steel by heating it and making it malleable. This allows the steel to be shaped into the desired form through hammering or pressing. Forging makes the steel stronger and more flexible by refining its grain structure and removing any internal faults or stress points. It's used in industries like aerospace and automotive manufacturing for creating important mechanical parts and structures.
Rolling involves shaping steel by passing it between rotating rollers, which flattens it and changes its cross-section shape. There are two main types: hot rolling and cold rolling. Hot rolling happens at high temperatures, making the steel easier to shape. It's good for producing items like beams, plates, and pipes in large quantities. Cold rolling occurs at room temperature, which makes the steel harder to shape but results in better precision and surface quality. Rolling is widely used in metalworking, construction, and shipbuilding to make various steel products.
Casting is a method where molten metal is poured into molds and left to cool and solidify, forming steel products of the desired shape. There are several types of casting, including sand casting, which is traditional and great for complex shapes; metal casting, which uses metal molds for higher precision; and precision casting, which can create detailed small-batch components. Casting is ideal for making intricate steel parts like automotive components and machinery parts.
Welding joins pieces of metal together by heating them until they melt and fuse, then cooling to form a strong bond. Common welding methods include electric arc welding, which uses an electric arc to generate heat; gas welding, which uses burning gas as a heat source and is suitable for thin sheets and small diameter pipes; and laser welding, which uses a high-energy laser beam for precise welding. Welding is essential in constructing steel structures, pipelines, and containers, connecting various metal components securely.
Cutting shapes steel into needed sizes using methods like shearing, flame cutting, and plasma cutting. Shearing with scissors or guillotine machines is best for thinner sheets. Flame cutting uses hot flames from oxygen and fuel to cut thicker materials. Plasma cutting employs high-temperature plasma arcs for various thicknesses. Cutting is crucial in metalworking, construction, and shipbuilding for preparing steel parts of all shapes and sizes.
In summary, steel materials have become an indispensable and important material in modern society due to their excellent comprehensive performance and wide application fields. With the advancement of technology and the development of industry, the types and properties of steel continue to enrich and improve, providing more diverse and high-quality choices for various industries.
FAQ About Steel Metal Parts
When it comes to making parts, there's a variety of steel we often turn to. For starters, carbon steel is a go-to because it's strong and affordable. Then you've got alloy steels, which mix in other metals to boost things like strength or corrosion resistance. Stainless steel is another popular choice, especially when you need something that won't rust. And don't forget about tool steels for things that need to stay sharp or withstand high temperatures. Each type has its own superpowers, so we pick based on what the part needs to do.
Picking the right steel grade might seem tricky, but it's all about matching the material to your project's needs. First off, consider what the part will be used for—is it for construction, machinery, or something else? The application will guide you towards the right properties, like strength, hardness, or resistance to wear and tear. Also, think about the environment it'll be in, such as exposure to moisture or chemicals, which could affect your choice. And don't forget about any special requirements, like needing it to be magnetic or non-magnetic. By considering these factors, you'll zero in on the perfect steel grade for your job.
To keep steel parts in top shape and extend their lifespan, we use several tricks of the trade. One popular method is painting or coating them, which not only protects against rust but also gives them a nice finish. Another option is galvanizing, which involves dipping the steel in molten zinc for a durable, rust-resistant layer. For parts that need extra toughness, we might use heat treatment processes like hardening or tempering. And if you're looking for a sleek, modern look, anodizing or electroplating can add both style and protection. These treatments help ensure our steel parts perform well and look good doing it.
Keeping corrosion at bay is crucial for maintaining the integrity of steel parts. A big step in prevention is choosing the right type of steel from the get-go, like stainless steel, which is less prone to rusting. But even with the best materials, you still need to take precautions. Regular cleaning and maintenance go a long way; removing dirt, grime, and moisture can stop corrosion before it starts. Applying protective coatings, like paint or specialized sealants, creates a barrier against the elements. And in environments where salt or chemicals are present, more robust measures like cathodic protection or using corrosion-resistant alloys might be necessary. By staying proactive, you can keep your steel parts corrosion-free and functioning flawlessly.
Opting for stainless steel instead of regular steel brings a bunch of advantages to the table. Firstly, it's corrosion-resistant, meaning it won't rust easily, even in harsh environments. This makes it perfect for outdoor or marine applications. Plus, it looks sleek and modern, adding a touch of elegance to any product. Stainless steel is also hygienic, making it ideal for food processing and medical equipment. While it might cost a bit more upfront, its durability and low maintenance requirements often make it a cost-effective choice in the long run. So, if you want a material that combines performance with good looks, stainless steel is hard to beat.
Absolutely, steel parts can be recycled, and the process is pretty straightforward yet impressive. When steel products reach the end of their lifecycle, they're collected and sorted by type and grade. Then, they're shredded into small pieces using powerful machinery. These shreds are melted down in a furnace at really high temperatures, turning them back into raw steel. Any impurities are removed during this melting process, ensuring the recycled steel is just as good as new. Finally, the molten steel is poured into molds to create new products. Recycling steel not only saves natural resources but also reduces energy consumption and greenhouse gas emissions. It's a win-win for both the environment and industry.