Surface Finish post-treatment Service
After production, plastic and metal products often need to undergo a series of post-treatment processes to ensure that their performance, appearance, and functionality are closer to the design requirements.
For metal parts, common post-treatment processes include heat treatment, polishing, painting, and electroplating. Heat treatment can change the physical properties of metals, such as hardness, toughness, and wear resistance; Polishing is used to improve surface smoothness and enhance aesthetics; Painting and electroplating can form a protective layer on the metal surface, preventing corrosion and increasing decorative effects.
For non-metallic parts, especially plastic parts, post-processing may involve steps such as deburring, polishing, painting, screen printing, or transfer printing. These processes help improve the feel, appearance, and clarity of identification of parts.
Through such one-stop services, we can not only shorten the product development cycle, but also effectively control costs and improve product quality. More importantly, we can help you solve various technical problems encountered during production and post-processing, so that you have no worries.
surface treatment effect
In order to remove various foreign objects attached to the surface of an object (such as oil stains, rust, dust, old paint films, etc.) and provide a good substrate suitable for painting requirements, to ensure that the coating film has good anti-corrosion performance, decorative performance, and certain special functions, it is necessary to pre-treat the surface of the object before painting. People refer to the work done for this type of treatment as pre coating (surface) treatment or (surface) pre-treatment.
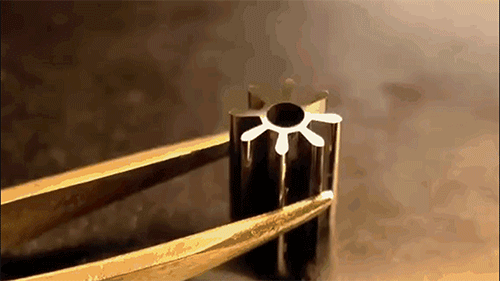
During the processing, transportation, storage, and other processes of workpieces, the surface often contains oxide skin, rust mold residue, molding sand, welding slag, dust, oil, and other dirt. To ensure that the coating can firmly adhere to the surface of the workpiece, it is necessary to clean the surface of the workpiece before coating. Otherwise, it not only affects the adhesion and corrosion resistance between the coating and the metal, but also allows the base metal to continue to corrode even with coating protection, causing the coating to peel off, affecting the mechanical properties and service life of the workpiece. Therefore, surface treatment before painting the workpiece is an important guarantee and measure to obtain a high-quality protective layer and extend the service life of the product.
Surface treatment process type
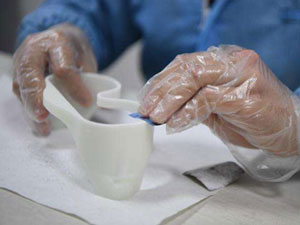
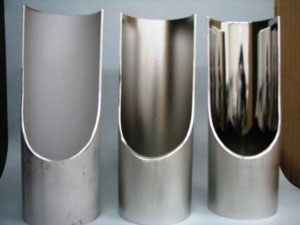
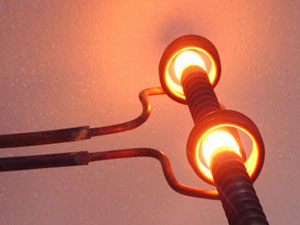
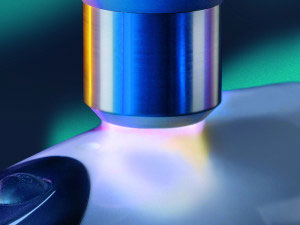
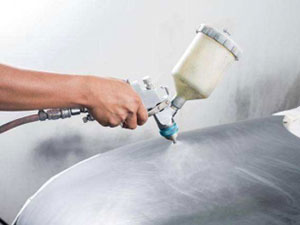
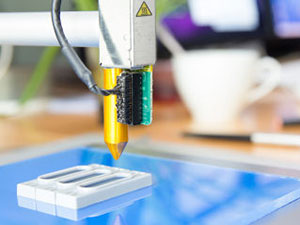
Grinding and polishing - Surface Finish Post-Treatment
In order to better solve the surface smoothness problem of printed products, The working principle of 3D printing layer by layer stacking results in a step effect on the surface of the printed piece. Although the layer thickness can be minimized during the printing process, there are still multi-level steps with a certain thickness at the micro size. The surface quality of the printed piece is related to the quality of 3D data, data slicing parameters, printing materials, machine accuracy, printing speed, printing temperature, etc, In order to better solve the surface quality problem of printed materials, it is necessary to put in effort in the post-processing process after printing is completed.
Grinding
Polishing is a type of surface modification technology that generally refers to a processing method that uses rough objects (such as sandpaper with higher hardness particles) to change the physical properties of the material surface through friction, with the main purpose of obtaining specific surface roughness.
The objects printed by FDM and SLA processes generally have obvious layer patterns. If there are requirements for the surface of the objects, polishing, soil filling, coloring, and other treatments are required.
Sandpaper polishing
The types of sandpaper are mainly divided by the thickness of surface particles, commonly including 180 mesh, 400 mesh, 600 mesh, 800 mesh, 1000 mesh, 1200 mesh, 1500 mesh, 2000 mesh, 2500 mesh, 3000 mesh, and 5000 mesh. The lower the label, the larger the sandpaper particles and the rougher the surface.
The polishing sequence starts from the low grade, starts with 180 mesh, passes through 400 mesh, 600 mesh, 800 mesh, 1000 mesh, 1200 mesh, 1500 mesh, and finally grinds to over 2000 mesh before painting.
sand blast
Sandblasting is the process of cleaning and roughening the surface of the substrate using the impact of high-speed sand flow. Using compressed air as the power, a high-speed spray beam is formed to spray materials (copper ore, quartz sand, diamond sand, iron sand, etc.) onto the surface of the workpiece to be treated at high speed, making the surface of the workpiece smooth and having a uniform matte effect. Due to the impact and cutting effects of abrasives on the surface of the workpiece, it achieves a certain degree of cleanliness and different roughness, which improves the mechanical properties of the workpiece surface. As a result, the fatigue resistance of the workpiece is improved, the adhesion between it and the coating is increased, the durability of the coating is extended, and it is also conducive to the leveling and decoration of the coating.
Sandblasting application:
(1) Workpiece coating and pre-treatment before workpiece bonding: sandblasting can remove rust and other dirt on the surface of the workpiece, making the bonding of the bonded parts more firm.
(2) Cleaning of rough surfaces and heat treated workpieces in casting: Use polishing and sandblasting to make the appearance of the workpiece more beautiful and attractive.
(3) Burr cleaning and beautification of machined parts: sandblasting can clean small burrs on the workpiece, making the surface of the workpiece appear more precise.
(4) Improving the mechanical performance of parts: After sandblasting, the mechanical parts reduce noise and improve the service life of the machinery.
(5) Decoration function: For certain special purpose workpieces, sandblasting can achieve different reflections or matte at will.
Shot peening
(1) Shot Peening:
Shot peening is a widely used surface strengthening process in factories, which has simple equipment, low cost, and is not limited by the shape and position of the workpiece. It is easy to operate, but the working environment is poor. Shot peening is widely used to improve the mechanical strength, wear resistance, fatigue resistance, and corrosion resistance of parts. It can also be used for surface smoothing, removing oxide skin, and eliminating residual stress in cast, forged, and welded parts.
(2) The difference between shot peening and sandblasting:
Both shot peening and sandblasting use high-pressure air or compressed air as power to blow out the medium at high speed and impact the surface of the workpiece to achieve cleaning effect. However, the effect varies depending on the medium chosen.
After sandblasting treatment, the dirt on the surface of the workpiece is removed, and the surface of the workpiece is slightly damaged, resulting in a significant increase in surface area, thereby increasing the bonding strength between the workpiece and the coating/coating.
The surface of the workpiece after sandblasting treatment is metallic in its natural color, but due to its rough surface, light is refracted off, resulting in no metallic luster and a dark surface.
polishing
Polishing refers to the process of using mechanical equipment, chemical or electrochemical processes to reduce the surface roughness of a workpiece, in order to obtain a bright and flat surface. It is a decorative production process that uses polishing tools to remove abrasive particles or other polishing substances from the surface of workpieces. Polishing cannot improve the machining accuracy or geometric shape accuracy of the workpiece, but is primarily used to obtain a smooth surface or mirror glass glossiness, sometimes also used to remove glossiness (polishing). Generally, polishing wheels are used as special polishing tools. The polishing wheel is generally made of double-layer white canvas, felt, or leather products stacked together, with alloy circular plates clamped on both sides, and its edges coated with a polishing agent composed of a uniform mixture of micro powder abrasive and vegetable oil. During polishing, a high-speed polishing wheel (with a circumferential speed of over 20 meters/second) presses against the workpiece, causing wear-resistant materials to extrude and slightly drill the surface of the workpiece, resulting in a bright production and processing surface. The surface roughness can generally reach Ra0.63-0.01 μ M; When using non greasy polishing agents, bright surfaces will be polished to improve appearance. For different polishing processes: rough polishing (basic polishing process), intermediate polishing (deep machining process), and precision polishing (polishing process), using suitable polishing wheels can achieve the best polishing actual effect while improving polishing efficiency.
metal surface treatment - Surface Finish Post-Treatment
By physical or chemical methods, a surface layer with certain special properties is formed on the surface of a metal. Surface treatment is the process of forming a surface layer with certain or multiple special properties on the surface of a material through physical or chemical methods. Surface treatment can improve the appearance, texture, functionality, and other aspects of product performance.
Appearance: color, pattern, logo, gloss/lines (3D, 2D);
Texture: Hand feel, roughness, lifespan (quality), streamline, etc;
Function: Hardening, anti fingerprint, anti scratch;
Below is a detailed introduction to various surface treatment processes for metal 3D printed parts:
Anodization
Anodic oxidation, electrochemical oxidation of metals or alloys. Using metal or alloy parts as anodes, an oxide film is formed on their surface by electrolysis. Metal oxide films change the surface state and properties, such as surface coloring, improving corrosion resistance, enhancing wear resistance and hardness, and protecting metal surfaces. For example, aluminum anodizing involves placing aluminum and its alloys in corresponding electrolytes (such as sulfuric acid, chromic acid, oxalic acid, etc.) as anodes for electrolysis under specific conditions and external current. Anodized aluminum or its alloys are oxidized, forming a thin layer of aluminum oxide on the surface, with a thickness of 5-20 microns. The hard anodized film can reach 60-200 microns. The anodized aluminum or its alloy improves its hardness and wear resistance, reaching 250-500 kilograms per square millimeter. It has good heat resistance, a hard anodized film with a melting point of up to 2320K, excellent insulation, and a breakdown voltage of up to 2000V, enhancing its corrosion resistance ω= 0.03NaCl salt spray does not corrode after thousands of hours. The thin oxide film contains a large number of micropores that can adsorb various lubricants, making it suitable for manufacturing engine cylinders or other wear-resistant parts; The membrane has strong microporous adsorption ability and can be colored into various beautiful and beautiful colors.
Benefits of anodizing:
1. Anti static. 2. Surface gloss. 3. Wear resistance.
Many small aluminum parts on semiconductor devices require anodizing treatment in order to increase hardness and reduce wear.
Phosphating treatment
Phosphating is a commonly used pre-treatment technology that belongs to chemical conversion film treatment in principle. It is mainly applied to the surface of steel for phosphating, and non-ferrous metal (such as aluminum, zinc) parts can also be phosphatized.
Phosphating is a process of chemical and electrochemical reactions to form a phosphate chemical conversion film, which is called a phosphating film. The main purpose of phosphating is to provide protection for the base metal and to some extent prevent metal corrosion; Used for priming before painting to improve the adhesion and corrosion resistance of the paint film layer; It plays a role in reducing friction and lubrication in metal cold working processes.
Phosphatization
1. Enhance the adhesion between the coating layer (such as paint coating) and the workpiece.
2. Improve the corrosion resistance of the surface coating of the workpiece after coating.
3. Improve decorative properties.
Blackening treatment
Blackening is a common method of chemical surface treatment, which involves producing an oxide film on the metal surface to isolate air and achieve rust prevention.
There are two commonly used methods for blackening treatment: traditional alkaline heating blackening and later room temperature blackening. But the room temperature blackening process is not very effective for low-carbon steel. Alkaline blackening is subdivided, and there is a difference between once blackening and twice blackening. The main components of black liquor are sodium hydroxide and sodium nitrite. The temperature tolerance required for blackening is relatively high, and a good surface can be obtained between 135-155 ℃, but the required time is only a bit short.
Passivation treatment
The phenomenon of significant decrease in corrosion rate of metals after being treated with oxidizing media compared to before is called metal passivation. The passivation mechanism can mainly be explained by the thin film theory, which suggests that passivation is due to the interaction between metals and oxidizing media, generating a very thin, dense, well covered passivation film on the metal surface that can firmly adhere to the metal surface. This layer of film exists as an independent phase, usually a compound of oxygen and metal. It plays a role in completely separating the metal from the corrosive medium, preventing direct contact between the metal and the corrosive medium, thereby basically stopping the dissolution of the metal and forming a passive state, achieving the effect of preventing corrosion.
Passivation treatment is the last and crucial step in chemical cleaning, aimed at preventing corrosion of materials. After acid washing, water flushing, and rinsing, the metal surface of the boiler is very clean, highly activated, and prone to corrosion. Therefore, it is necessary to immediately undergo passivation treatment to generate a protective film on the cleaned metal surface and slow down corrosion.
laser marking
Laser engraving, also known as laser engraving or laser marking, is a surface treatment process using optical principles. Laser engraving is a marking method that uses high-energy density laser to locally irradiate the workpiece, causing instantaneous vaporization or color change of the surface material, thereby leaving a permanent mark. Laser engraving can create various characters, symbols, and patterns, with character sizes ranging from millimeters to micrometers. The characters carved by this technology have no scratches, the surface of the object is still smooth, and the handwriting will not wear out.
Process (implementation method):
Laser engraving refers to laser engraving, which involves the use of the light energy of a laser beam to cause chemical and physical changes in the surface material, resulting in the carving of marks. Alternatively, the use of light energy to burn off some of the material and display the desired etched graphics and text; According to different carving methods, it can be divided into lattice carving and vector cutting.
The process of laser engraving is very simple, just like using a computer and printer to print on paper; It can be designed in various graphic processing software such as CorelDraw, and scanned graphics, vectorized graphics, and various CAD files can be easily "printed" into the engraving machine. The only difference is that printing involves applying toner to paper, while laser engraving involves shooting laser light onto almost all materials such as wood, acrylic, plastic, metal, and stone.
Electrophoretic paint
Electrophoresis process is divided into anodic electrophoresis and cathodic electrophoresis. If the coating particles are negatively charged, the workpiece is an anode, and the coating particles deposit into a film on the workpiece under the action of electric field force, which is called anodic electrophoresis; On the contrary, if the coating particles are positively charged and the workpiece is a cathode, the deposition of coating particles onto the workpiece is called cathodic electrophoresis.
Electrophoretic application:
It can be divided into anodic electrophoretic paint and cathodic electrophoretic paint.
Among them, anodic electrophoretic paint includes anodic acrylic acid, which is mainly used in aluminum products. After aluminum oxidation, it is protected with anodic electrophoretic paint, with a glossiness between 50-90 degrees and a thin paint film. It is widely used in the aluminum profile industry. Cathodic electrophoretic paint can also be divided into epoxy electrophoretic paint, acrylic electrophoretic paint, and polyurethane electrophoretic paint.
wire drawing
Wire drawing process is a metal processing process. In metal pressure processing. The technical processing method of metal wire drawing is to force metal through the mold under external forces, compress the cross-sectional area of the metal, and obtain the required cross-sectional area shape and size. Change its shape. The tool of size is called a wire drawing die. For example, in the cable industry, 8mm copper rods are pulled into copper wire using a copper wire drawing machine, using a set of 5-8 wire drawing molds from large to small, such as 3.5mm, 2.0mm, etc.
Wire drawing is a method of improving the surface smoothness of a workpiece by using the reciprocating motion of the wire drawing cloth and rubbing it back and forth on the surface. The surface texture is linear. It can improve surface quality and mask slight scratches on the surface.
The function of wire drawing:
The surface of the metal plate has characteristics such as rust prevention, oxidation resistance, scratch resistance, chemical reagent resistance, and smoke resistance. In terms of appearance, due to the unique and bright surface of the product itself, it is recommended to apply it to horizontal surfaces with less friction or general vertical surfaces to avoid losing its luster due to friction. In addition, it is recommended to use in dry or non wet areas where moisture is not too heavy to maintain the stability of the product. Metal surface wire drawing can effectively cover up mechanical lines and mold defects in production
CD pattern
CD pattern is an effect similar to the pattern on a CD disc obtained by removing materials on a metal surface using a precision CD pattern machine. The spacing between the patterns is determined by the appearance and size of the product. CD pattern is widely recognized as a high-end surface treatment process for metal surfaces in the industry.
High quality CD pattern processing must have the following five key elements:
1. High precision CD pattern machine.
2. Scientific product processing fixtures.
3. Trained process operators.
4. Choose a reasonable machining tool.
5. Correct cooling plan.
Metal heat treatment - Surface Finish Post-Treatment
Imagine that you have just printed a metal part with a body full of "powder armor". Do you need to remove this layer of "armor" before proceeding to the next step? That's right, this is the preparation work before heat treatment.
Firstly, why clean up these powders? Firstly, it is to save material costs, after all, powder is also money; Secondly, if there are small flow channels inside the component, and these channels are as narrow as needle holes, if they are not cleaned thoroughly, the powder may get stuck in the channels, causing the component to suffocate. So, we need to carefully remove these 'powder obstacles'.
Next, it's the highlight of heat treatment. Heat treatment, in fact, is to give metal or alloy a "three warmth" - heating, insulation, and cooling. None of these three steps can be omitted, and the temperature, time, and cooling rate of each step must be precisely controlled. Just like baking bread, if the heat is not enough or too high, the bread will become burnt or undercooked.
Speaking of which, you may be asking, 'What will the parts look like after heat treatment?' Good question! The characteristic of heat treatment is that it does not change the external dimensions of metal parts, but can penetrate deep into the "inner" and change the internal structure and properties of materials. It's like giving a 'spiritual massage' to a component, making it look brand new!
Common heat treatment methods include annealing, normalizing, quenching, and tempering. Let's take steel as an example to talk about the wonderful uses of these heat treatments. The purpose of steel heat treatment is like giving steel a "physical examination" to identify and eliminate small problems in the material structure. More importantly, it can also enhance the performance of steel, allowing it to unleash greater potential. This is simply too important for improving product quality and extending service life!
Overall, heat treatment after metal printing is an essential process. It not only makes the parts more flawless, but also safeguards product quality and service life. So, next time you see those sparkling metal parts, don't forget that they have undergone countless "tempering" and "baptism" behind them!
Metal annealing
Annealing is a heat treatment process that heats metal or alloy workpieces to an appropriate temperature (above or below the critical temperature, even if the material undergoes structural transformation), maintains it for a certain period of time, and then slowly cools (i.e., cools down with the furnace or embeds it in a medium with poor thermal conductivity). The characteristics of annealing process are long insulation time, slow cooling, and the ability to obtain a balanced state of microstructure.
The main purpose of steel annealing is to refine the structure, improve performance, reduce hardness, and facilitate cutting processing; Eliminate internal stress; Improve toughness and stabilize size. Unify the structure and composition of steel; It can also prepare the structure for future heat treatment processes. Depending on the purpose of annealing, there are several types of annealing, including complete annealing, spheroidizing annealing, and stress relief annealing.
Annealing is often performed on castings, forgings, and weldments during the manufacturing process of parts, in order to facilitate subsequent machining or prepare for quenching.
Metal normalization
The heat treatment process of heating steel parts to a critical temperature above 30-50 ℃, holding them for an appropriate period of time, and cooling them in still air is called normalizing. The main purpose of normalizing is to refine the microstructure, improve the properties of steel, and obtain a microstructure close to equilibrium state.
The main difference between normalizing and annealing processes is that the cooling speed of normalizing is slightly faster, so the production cycle of normalizing heat treatment is shorter. Therefore, when annealing and normalizing can also meet the performance requirements of parts, normalizing should be chosen as much as possible. Most of the billets of medium and low carbon steel are generally subjected to normalizing heat treatment. Annealing is commonly used for alloy steel billets. If normalizing is used, due to the fast cooling rate, the hardness after normalizing is higher, which is not conducive to cutting processing.
Metal quenching
The heat treatment process of heating steel components to a certain temperature above the critical point (quenching temperature of 45 # steel is 840-860 ℃, and quenching temperature of carbon tool steel is 760-780 ℃), holding for a certain time, and then cooling at an appropriate rate to obtain martensite or bainite structure is called quenching.
The main difference in process between quenching, annealing, and normalizing is the fast cooling rate, aimed at obtaining martensitic structure. That is to say, in order to obtain martensitic structure, the cooling rate of the steel must be greater than the critical speed of the steel. The so-called critical speed is the minimum cooling rate for obtaining martensitic structure. The types of steel vary, and the critical cooling rate varies. Generally, the critical cooling rate of carbon steel is higher than that of alloy steel. So carbon steel needs to be cooled in water after heating, while alloy steel needs to be cooled in oil. If the cooling rate is less than the critical cooling rate, martensitic structure cannot be obtained, but if the cooling rate is too fast, it will increase the internal stress in the steel, causing deformation and even cracking of the steel parts.
Metal tempering
The heat treatment process of hardening steel parts, heating them to a temperature below the critical temperature, holding them for a certain period of time, and then cooling them to room temperature is called tempering.
Quenched steel parts generally cannot be used directly and must be tempered before use. Due to the high hardness and brittleness of quenched steel, direct use often leads to brittle fracture. Tempering can eliminate or reduce internal stress, reduce brittleness, and improve toughness; On the other hand, the mechanical properties of quenched steel can be adjusted to achieve its serviceability. According to the different tempering temperatures, tempering can be divided into three types: low temperature tempering, medium temperature tempering, and high temperature tempering.
(1) Low temperature tempering
Tempering of quenched steel parts below 250 ℃ is called low-temperature tempering. Low temperature tempering is mainly used to eliminate internal stress and reduce the brittleness of steel.
(2) Medium temperature tempering
The tempering of quenched steel parts between 250 ℃ and 500 ℃ is called medium temperature tempering, which can achieve good elasticity.
(3) High temperature tempering
Tempering of quenched steel parts above 500 ℃ is called high-temperature tempering. Quenched steel parts have good comprehensive mechanical properties after high-temperature quenching. Quenching+high-temperature tempering is called quenching and tempering treatment.
Plastic surface treatment - Surface Finish Post-Treatment
By physical or chemical methods, a surface layer with a specific property is formed on the surface of a material
Surface treatment refers to the formation of a surface layer with one or more special properties on the surface of a material through physical or chemical methods. Surface treatment can improve the appearance, texture, functionality, and other aspects of product performance.
Appearance: color, pattern, logo, gloss/lines (3D, 2D);
Texture: Hand feel, roughness, lifespan (quality), streamline, etc;
Function: Hardening, anti fingerprint, anti scratch;
Silk screen printing
Silk screen printing generally refers to screen printing, which refers to using silk screen as the substrate and using photosensitive plate making methods to produce a screen printing plate with graphics and text.
Silk screen printing is not suitable for overall coloring of 3D printed parts, and is more suitable for printing patterns. For example, printing text, logos, or other creative patterns on the outer side of the shell.
Process characteristics:
The characteristics of screen printing can be summarized as follows:
1. Screen printing can use various types of inks. That is, various types of inks such as oil-based, water-based, synthetic resin emulsion type, powder, etc.
2. The layout is soft. The screen printing layout is soft and has a certain degree of elasticity, which is not only suitable for printing on soft objects such as paper and fabric, but also suitable for printing on hard objects such as glass and ceramics.
3. Screen printing has low imprinting force. Due to the low pressure used during printing, it is also suitable for printing on fragile objects.
4. The ink layer is thick and has strong coverage.
5. Not limited by the surface shape and size of the substrate. As can be seen from the above, screen printing can not only be printed on flat surfaces, but also on curved or spherical surfaces; It is not only suitable for printing on small objects, but also suitable for printing on larger objects. This printing method has great flexibility and wide applicability.
Application scope:
Screen printing has advantages such as large batch size, low price, bright colors, long shelf life, and fast delivery, which are increasingly recognized by the industry and widely used.
On the circuit boards of household appliances, patterns on textiles, patterns on T-shirts, cultural shirts, and shoes, text on the panels of refrigerators, televisions, and washing machines, and decorations on ceramics, glass, and wall tiles; Various commercial advertising platforms such as appliances, packaging, outdoor, fixed, mobile, etc; In the packaging and decoration industry, screen printing is widely used for high-end packaging boxes, bottles, cigarette packs, and wine packs, especially for large-sized outer packaging and product appearance decoration. Screen printing is closely related to our daily lives, and its technology is mainly controlled by many printing factories. However, small-scale personalized screen printing technology is rarely taught in China, and the market is exceptionally broad!
Pad printing
Transfer printing is one of the special printing methods. It can print text, graphics, and images on irregular and irregular surfaces, and is now becoming an important specialty printing. For example, the text and patterns on the surface of mobile phones are printed using this method, and many electronic products such as computer keyboards, instruments, and meters are printed using transfer printing. The transfer printing process is very simple, using steel (or copper, thermoplastic) intaglio plates and a curved transfer printing head made of silicone rubber material. The ink on the intaglio plate is dipped into the surface of the transfer printing head, and then the desired object surface is pressed to print text, patterns, etc.
Transfer printing is a printing technique that indirectly transfers the patterns and text on the gravure transfer plate to the product through a concave adhesive head. It has now become an important printing technique. Transfer printing technology first etches the patterns and text on the design or product onto the printing plate, making the transfer plate. The etched transfer plate is coated with specialized transfer printing ink using a transfer printing machine, and the excess ink is scraped off by the transfer printing machine with a steel knife, The remaining ink with patterns and text is then lowered from the transfer printing machine head to the steel plate to pick up the ink inside the patterns. Then, the transfer printing adhesive head is shifted and lowered to the product where the images and text are printed on the product to complete the transfer printing process.
water transfer printing
Water transfer printing technology is the latest digital imaging technology that surpasses any printing technology. It uses specialized paper and special environmentally friendly ink made of nanomaterials to print images on any solid medium. Its biggest technical advantage is that it does not require specialized equipment, is not limited by the medium, does not require specialized consumables, does not require high-temperature heating, and can print any image on any solid object or surface at will, The image has bright colors and absolute photo quality.
Process (implementation method):
Water transfer printing uses a specially chemically treated film, which is printed with the desired color patterns and then sent flat to the surface of water. By using water pressure, the color patterns are evenly transferred onto the product surface, and the film is automatically dissolved in water. After cleaning and drying, a transparent protective coating is applied. At this time, the product has presented a completely different visual effect.
UV paint
UV paint is the abbreviation for Ultraviolet Curing Paint, also known as UV initiated paint or UV cured paint. Its characteristics include long activation period, excellent yellowing resistance, good hardness, and high transparency.
Process (implementation method):
UV varnish is a transparent coating, also known as UV varnish. Its function is to spray or roll coat on the surface of the substrate, and after being irradiated by a UV lamp, convert it from a liquid state to a solid state, thereby achieving surface hardening. It has a scratch and scratch resistant effect, and the surface looks bright, beautiful, and has a rounded texture
Etching
Generally speaking, etching, also known as photochemical etching, refers to the removal of the protective film in the etching area after exposure to printing, plate making, and imaging. During etching, the chemical solution is touched to achieve the effect of melting and etching, establishing the actual effect of convex, concave, or hollow carving formation.
Production process:
Exposure method: The engineering project provides material preparation specifications based on the pattern - preparation materials - raw material cleaning - drying treatment - glass film or adhesive application - blow drying - exposure - fixing - drying treatment - etching - film removal - OK
Screen printing method: cutting → cleaning the plate (stainless steel plate and other metal composite materials) → screen printing → etching process → delamination → OK
Painting and coloring - Surface Finish Post-Treatment
Process the color of the object's spatial appearance to obtain a visual effect on the surface of the object,
At present, 3D printing technology has been applied in many fields. Most 3D printed products are monochrome, which is the natural color of the material. If there is an additional requirement for the surface color of the printed part at this time, we can use a post color treatment method to solve it. The following are four common methods for coloring 3D prints.
Hand drawn
Handdrawn coloring is a relatively simple and commonly used coloring method. Generally, a light colored paint primer (light gray or white) is applied first, followed by the main color to prevent uneven or reversed colors.
The main coloring technique is the cross coating method. First apply the first layer of paint, with each stroke in the same direction (such as from left to right). When the first layer of paint is dry to 70% or 80%, start the second layer of paint and perpendicular to the brush direction of the first layer of paint (such as from top to bottom).
The pigments used mainly include water-based paints (acrylic pigments) and oil-based paints. Water-based paint is affordable and can be diluted with water, making it easy to operate. However, its adhesion and color performance are slightly inferior to those of oil-based paint (especially in terms of color performance), making it suitable for 3D printing with low color requirements; Oily paints require specialized diluents, which generally have a certain pungent odor and require specialized personnel to operate under special protective conditions. Oily paints have better adhesion and are more uniform than water-based paints, but good techniques are required. Once failed, 3D printed parts are easily scrapped (water-based paints can be repeatedly repaired)
Painting
Painting is currently the main coloring process for 3D printed parts. Spray painting refers to the use of a spray gun to evenly spray artificial paint made from nitrocellulose, resin, pigments, solvents, etc. on the surface of an object. There are also spray cans that can be directly sprayed onto the surface of 3D printed parts without the use of a spray gun.
Spray cans are mostly oily paint with high adhesion, a wide range of applications, and excellent color and gloss. However, the color is relatively single, and multi color spraying is more difficult due to the influence of spraying technology and paint dryness.
After spraying, it takes 3-4 hours to air dry and fine tune the details. In terms of product effectiveness, it is also influenced by various factors such as manual proficiency, mastery of secondary coloring, and connection of spray points, resulting in a strong technical demand. In terms of color glossiness, influenced by the original mirror surface of the product, glossiness is second only to electroplating and nano spray coating effects.
2、 Painting and coloring, with moderate cost and widest applicability, are often used in conjunction with hand painting in the same work.
plating
Electroplating is the process of plating a thin layer of other metals or alloys on certain metal surfaces using the principle of electrolysis. It is the process of using electrolysis to attach a metal film to the surface of metal or other material products, thereby preventing metal oxidation (such as rust), improving wear resistance, conductivity, reflectivity, corrosion resistance (such as copper sulfate), and enhancing aesthetics.
Electroplating has fewer colors, but its high gloss color mirror and excellent appearance cannot be achieved by pure manual, spray painting, and dip dyeing. Electroplating can be applied to metal 3D printed parts.
Impregnation
Mainly used for coloring nylon materials. The cost is higher than that of pure manual coloring and painting processes. Generally, it is a single color, and colors can be selected and prepared according to needs. The final product presents a relatively dark color and low glossiness, which can achieve simultaneous coloring in small batches.
secondary processing - Surface Finish Post-Treatment
The process of reprocessing metal printed parts using CNC machine tools as needed after printing and forming,
Secondary processing refers to the process of using CNC machine tools to reprocess metal printed parts after printing and forming, including welding, boring, reaming, closing tolerance holes, or tapping tolerance holes that require threads. Depending on the material, various inserts can be inserted using hot piles or adhesive.
welding
Welding, also known as fusion welding, is a manufacturing process and technique that involves joining metals or other thermoplastic materials such as plastics by heating, high temperature, or high pressure.
There are many sources of energy for modern welding, including gas flames, arcs, lasers, electron beams, friction, and ultrasound. In addition to being used in factories, welding can also be carried out in various environments, such as outdoors, underwater, and space. No matter where, welding can pose a danger to the operator, so appropriate protective measures must be taken when welding. Welding may cause harm to the human body, including burns, electric shock, visual impairment, inhalation of toxic gases, excessive ultraviolet radiation, etc.
Due to the size limitations of SLM process metal printing, for some large-sized workpieces and molds, it is often necessary to use welding technology to complete the final cost of manufacturing.
Boring
Boring refers to the further processing of reserved holes on printed parts. Boring can expand the aperture, improve accuracy, reduce surface roughness, and also effectively correct the deviation of the original hole axis.
Boring can be divided into coarse boring, semi precision boring, and precision boring. The dimensional accuracy of precision boring can reach IT8 to IT7, and the surface roughness Ra value is 1.6 to 0.8 μ M.
Boring can be divided into general boring and deep boring. Generally, boring can be done on a regular lathe, and the boring tool can be fixed on the lathe tailstock or on a small tool holder. Deep hole boring requires a dedicated deep hole drilling and boring machine, with a boring cutter and a boring stem, as well as a hydraulic pump station that uses coolant to remove iron filings.
reaming
Reaming is a method of cutting a small amount of metal layer from the hole wall of a printed piece with a reamer to improve its dimensional accuracy and hole surface quality. Reaming is one of the precision machining methods for holes and is widely used in production. For smaller holes, reaming is a more economical and practical machining method compared to internal grinding and precision boring.
Commonly used are: integral cylindrical machine reamers and hand reamers, adjustable hand reamers, and spiral groove hand reamers.