Wire EDM Machining Service

Custom Precision Part Wire EDM Machining Services
Mold7 is capable of producing high-quality wire EDM parts in a matter of days, rather than months. We have a network of stores with hundreds of spare wire cutting and electrical discharge machining capabilities, providing you with almost unlimited production capacity to easily handle both simple and complex parts.
Wire cutting electrical discharge machining (also known as electrical discharge machining) uses a thin single strand wire to transport the workpiece or part together with deionized water. This wire is wound between two guide rollers and guided by the computer that drives the machine. This process uses current to remove conductive material from the component, leaving a smooth surface that does not require further processing. Although the process is complex, we have a highly skilled team capable of handling this task.
What Is Wire Electrical Discharge Machining?
Wire electrical discharge machining (wire EDM) is a process that works by continuously feeding a wire electrode under tension on a vertical axis. Discharge voltage is applied through the wire, crosses via a dielectric liquid, and strikes the grounded workpiece. The workpiece is moved in an X-Y plane to trace a cut pattern through the material. This erosion can commence from the outside edges of the workpiece or by drilling a hole first. EDM is capable of eroding a hole through the billet to be used as a starting point for a contained cut path.
The process is sometimes complicated by the specific pattern to be cut and the need to clear eroded material from the surface. The process takes place in an electrolyte bath of paraffin or deionized water. This bath acts primarily as a coolant and a semiconductor that enables tightly controlled arcing, but it also makes for a convenient way to flush out debris. Wire EDM machines started as a type of arc bandsaw or EDM cutter, built to cut complex 2D shapes. However, they have continuously evolved to the point that modern 5-axis wire EDM machines can perform remarkably complex operations.
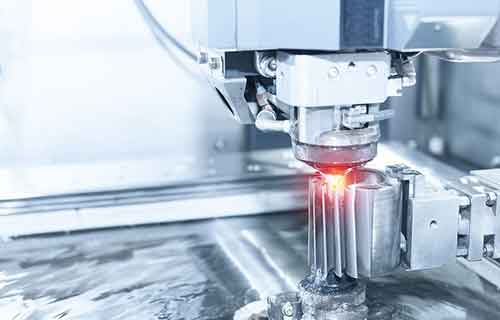
Wire EDM Machining Surface Finishes
Wire EDM Machining Standard Finish (as-milled)
The finish option with the quickest turnaround. Parts are left with visible tool marks and potentially sharp edges and burrs, which can be removed upon request. Surface finish is comparable to 125 uin Ra finish.
Wire EDM Machining Bead Blast
The part surface is left with a smooth, matte appearance.
Wire EDM Machining Tumbled
This is a batch-based process that tumbles vibrating media to remove sharp edges and burrs on machined parts. Tumbling can remove machine marks on exterior surfaces. Parts over 8” may require a manual review.
Wire EDM Machining Anodized (Type II or Type III)
Type II (MIL-A-8625, Type II) creates a corrosion-resistant finish. Parts can be anodized in different colors—clear, black, red, and gold are most common—and is usually associated with aluminum.
Type III (MIL-A-8625, Type III, Class 1/2 "hardcoat") is thicker and creates a wear-resistant layer in addition to the corrosion resistance seen with Type II.
Wire EDM Machining Titanium Anodize
A surface finish for titanium per AMS-2488 Type 2 specification. Also called Tiodize, this finish increases fatigue strength and the wear resistance of a part. Titanium anodized parts are common in aerospace and medical device manufacturing. Non-pigmented titanium anodize finishes will dull shine.
Wire EDM Machining PTFE Impregnated Hard Anodize
A hard coat anodize process that embeds PTFE to create a self-lubricating, dry contact surface with Type 3 hard coat’s protective properties. This finish can be used on aluminum alloys or titanium and increases the service life of the product. This finish conforms to the AMS-2482 Type 1 Hard Coat Anodizing with Teflon (Non-Dyed).
Wire EDM Machining Chem Film
Provides corrosion resistance and good conductivity properties. Can be used as a base for paint. Can leave surface yellow/gold. Adds very little thickness, about 0.00001”-0.00004”. Chem film will conform to MIL-DTL-5541, TYPE I/II.
Wire EDM Machining Passivation
Improves corrosion resistance for 200 and 300 series and precipitation hardened corrosion-resistant steels. Thickness is negligible, about 0.0000001”. Conforms to ASTM A967, AMS-QQ-P-35, MIL-STD-171, ASTM A380, or AMS 2700.
Wire EDM Machining Powder Coat
This is a process where powdered paint is sprayed onto a part that is then baked in an oven. This creates a strong, wear- and corrosion-resistant layer that is more durable than standard painting methods. A wide variety of colors are available to create the desired aesthetic.
Wire EDM Machining Electropolishing
An electrochemical process cleans steel parts to reduce corrosion and improve appearance, by making the metal brighter. Removes about 0.0001”-0.0025” of the metal. Conforms to ASTM B912-02.
Wire EDM Machining Electroless Nickel Plating
Provides uniform nickel coating which offers protection from corrosion, oxidation, and wear on irregular surfaces. The finished part will be brighter. Thickness starts at .0001”. Conforms to MIL-C-26074.
Wire EDM Machining Silver Plating
Silver offers high solderability and electrical conductivity but is susceptible to tarnish. Conforms to AMS QQ-S-365D. Thickness is about 0.00002” - 0.0003.”
Wire EDM Machining Gold Plating
Gold Plating provides good corrosion and tarnish resistance with excellent solderability. Default application specification is MIL-G-45204 and ASTM B488, CLASS 00, 0, OR 1. Thickness is about 0.00002" - 0.00005."
Wire EDM Machining Zinc Plating
Provides uniform zinc coating which offers protection from corrosion, oxidation, and wear on irregular surfaces. Conforms to ASTM B633-15.
Advantages of Wire EDM Machining
Wire EDM Machining Production efficiency
High overall manufacturing efficiency, since few follow-on processes, is needed and extreme surface finish quality is directly achievable.
Wire EDM Machining All metals capability
Unlimited ability to process conductive materials of any hardness or brittleness.
Wire EDM Machining High precision
Extreme tolerances, with feature accuracies approaching 10 millionths of an inch and general tolerances of 40 millionths of an inch being common.
Wire EDM Machining Low distortion
Zero-distortion processing— there is no bulk heating, no tearing or fracture, and no impact, so internal stresses and distortion resulting from processing can be kept close to zero.
Wire EDM Machining Very fine features
Unlimited feature complexity in 2D parts (and limited 3D complexity in 5-axis wire EDM production) as the wire is infinitely maneuverable and cannot misapply force.
Wire EDM Machining Safe operation
Wire EDM is safe, despite high voltages, so unsupervised processing is the norm, reducing costs without increasing risks.
Maybe you know Wire EDM Machining
What Is Wire EDM Machining Used For?
Wire EDM is used for the direct, single-stage processing of hard materials from basic billet form to a finished state. Its single-stage nature reduces costs and improves toolmaking precision for a range of industries, including: extruder, punch, and die tooling, aerospace, medical equipment, automotive, and electronics.
This benefit arises from the process’ ability to directly work with pre-hardened tool steels. The hardening process can introduce serious internal stresses and distortion/inaccuracy in machined parts. The ability to cut pre-hardened materials removes this issue almost entirely. The introduction of 5-axis CNC wire EDM machines has increased the breadth of tasks that the technology can undertake. The additional degrees of freedom in part design make complex three-dimensional products much more feasible.
What is the process of EDM wire cut machine?
The process of Wire EDM involves a thin wire, which conducts an electrical current and forms an electrode. The electrode is positioned precisely next to the workpiece and submerged in a dielectric fluid bath, usually deionized water. The electrical discharge then erodes the material as the electrode and workpiece are charged with a high voltage, resulting in the creation of the desired shape. The process is controlled through computer-aided design (CAD) systems, which allow for a high degree of precision and control.
Which Wire Is Used in an EDM Machine?
The wire used in an EDM machine comes in various grades and purposes. Among the choices are: copper, brass, tungsten, molybdenum, coated (zinc-coated and diffusion-annealed), and steel-core wires. The wire acts as the EDM device’s cutting tool. Each type of wire affects the machining process in different ways.
Whatever the wire type, it can only be used once and has only scrap value after use. The material breaks down during the electrical discharge process. EDM wire is sold by weight and classification. Its handling makes the difference between an optimized setup and one that is disrupted by breakages, poor precision, or other production interruptions.
What materials can be machined by wire EDM?
Wire EDM can cut all metals. In particular, it is used for cutting: pre-hardened die steels, titanium, austenitic stainless steels, tungsten, and molybdenum. Though functional, it is generally not cost-effective to cut soft materials such as: copper, bronze, brass, and non-hardened steel, all of which can be easily machined by cheaper conventional means. However, if the part must be manufactured in a single stage or with no added heat, EDM is the only practical option.
Wire EDM can be used to machine a variety of metals and alloys, such as aluminum, copper, steel, and titanium, and even hard materials like tungsten carbide and hardened tool steels due to its ability to use electrical sparks to erode material instead of physically cutting it. This makes it ideal for creating intricate shapes and difficult-to-machine materials in various industries such as aerospace, automotive, and medical devices.
What Is the Cutting Method Used by Wire EDM?
Electrical discharge as a machining process uses a discharge (spark) between a tool electrode and a material billet to be cut. The spark energy is dissipated as heat at a microscopic point, reaching as high as 12,000°C and vaporizing both parts. However, since the point of contact is so small, the part does not absorb much of that heat. Wire EDM preserves the electrode by moving the wire through the cut area so the cut is always facing fresh wire. The wire is moved across the workpiece – usually in the X-Y plane – following a CNC-controlled path that is programmed in G-code.
How Does Wire-Cut EDM Work?
Arc-eroded material from both the work (the equivalent of cuttings or swarf) and the electrode is flushed out of the cut area by the dielectric liquid. As the arc erodes the workpiece, the table advances the work along a preprogrammed path. This process results in the most precise and fine cutting available from any CNC equipment. The machining process aims to maintain a very small spark gap, across which the arc forms. At no time should the electrode wire actually touch the workpiece.
How Accurate Is Wire EDM?
Typical high-end machines maintain a wire positional accuracy of 40 millionths of an inch (0.000004”). Special high-precision machines can maintain 0.000001” accuracy. It is common for cut parts to maintain tolerances of 0.0001”, or one ten-thousandth of an inch.
Who Manufactures Wire EDM Machines?
CNC equipment manufacturers of both specialist and budget varieties make a range of wire EDM machines. The leading manufacturers are: Agie Charmilles, FANUC, Cincinnati Milacron, Hitachi, Xact Wire EDM Corp, KentUSA, and many other first-tier brands. There is also a very competitive market for less well-known but highly capable machine brands. Research the company and specific machines carefully before choosing one.
What Are the Disadvantages of Wire EDM?
Wire EDM is not suited to all tasks. The disadvantages are listed below:
- Wire EDM is not suitable for plastics, composites, and natural materials. It only functions on conductive materials.
- Cuts relatively slowly. This slow process makes per-part costs higher than other machining processes (when comparing like for like).
- Consumable costs are high, as the wire cannot be reused.
What is wire EDM machine?
Wire EDM (Electrical Discharge Machining) machine is a highly precise and efficient industrial tool used for shaping and cutting materials. It employs electrical sparks to erode the material’s surface, resulting in a very precise cutting, and there is no need for direct physical contact between the cutting material and the machine.
What is wire EDM in manufacturing?
Wire EDM is a favored machining process in the manufacturing industry due to its ability to deal with complex parts that are hard to machine using conventional methods. The machine is controlled through computer-aided design (CAD) systems, which allow a high degree of precision and control over the cutting process. The process can be used to machine a variety of metals, alloys, and hard materials, making it ideal for creating complex shapes and difficult-to-machine parts.
What Is the Difference Between EDM and Wire Cut EDM?
EDM uses a shaped electrode made of copper or carbon to cut intricate partial 3D cavities. The electrodes themselves are machined by conventional processes. Spark electrodes are then used in a pulsating height mode that allows cooling and full flushing of the work face. EDM is only as precise as the electrode machining but allows significant complexity in the shape of the eroded surface. This method is used for complex and precise shapes within molds and die-casting tools. It can operate on pre-hardened material, reducing overall costs and allowing more extreme hardening without tool distortion. Wire EDM, on the other hand, uses a continuously fed wire electrode for essentially 2D cutting. This process is ideal for complex 2D profiles for extrusion tools, punch/die sets, etc., as well as extreme precision processing of hard materials for aerospace and military applications.
FAQ About Wire EDM Machining
- What is wire EDM machining and how does it work?
Wire EDM machining is an electrothermal production process that uses electric discharges to remove material from a workpiece. It is an improvement to the conventional EDM method, compatible with almost all conductive materials, and can create complex designs and shapes .
The process works by continuously feeding a wire electrode under tension on a vertical axis. Discharge voltage is applied through the wire, crosses via a dielectric liquid, and strikes the grounded workpiece. The workpiece is moved in an X-Y plane to trace a cut pattern through the material. This erosion can commence from the outside edges of the workpiece or by drilling a hole first .
Wire EDM machines can also move along five axes, including being inclined, to create tapered effects on the metal and offering more degrees of freedom. The remarkable thing about Wire EDM technology is that using this method, it is possible to create certain geometrical features on your piece that are next to impossible with other types of CNC machine. You can create small slots, square corners, and complex shapes and designs within the metal that are impossible with, for instance, CNC milling .
Wire EDM machining is widely used for prototyping, tooling, die making, aerospace, medical, automotive, and other industries that require high precision and accuracy .
- What are the advantages and disadvantages of wire EDM machining?
Wire EDM machining is a process that uses an electrically charged wire to cut through metal materials with high precision and accuracy. Wire EDM machining has some advantages and disadvantages compared to other machining methods. Some of the advantages are:
- Wire EDM machining can cut complex shapes and intricate details that are difficult or impossible to achieve with conventional tools.
- Wire EDM machining can produce smooth and burr-free surfaces that require little or no finishing operations.
- Wire EDM machining can cut hard and brittle materials that are prone to cracking or chipping with other methods.
- Wire EDM machining can cut very thin and delicate parts without causing distortion or damage.
- Wire EDM machining can cut materials that are not affected by heat, such as ceramics, composites, and superalloys.
Some of the disadvantages are:
- Wire EDM machining is a slow and expensive process that consumes a lot of electricity and wire.
- Wire EDM machining requires a conductive material to work, which limits its applications to metals and some alloys.
- Wire EDM machining generates a lot of waste material and debris that need to be disposed of properly.
- Wire EDM machining can cause thermal stress and micro-cracks on the workpiece due to the high temperature of the spark.
- Wire EDM machining can alter the mechanical and metallurgical properties of the workpiece due to the heat affected zone (HAZ).
- What are the applications and industries that use wire EDM machining?
Wire EDM machining is a process that uses an electrically charged wire to cut through various materials with high precision and accuracy. Wire EDM machining has many applications and industries that use it, such as:
- Aerospace: Wire EDM machining can create complex shapes and patterns on turbine blades, engine components, landing gear parts, and other aerospace parts that require high strength and durability.
- Medical: Wire EDM machining can produce surgical instruments, implants, prosthetics, and other medical devices that need to meet strict quality and hygiene standards.
- Automotive: Wire EDM machining can cut and shape metal parts for engines, transmissions, brakes, steering systems, and other automotive components that require high performance and reliability.
- Mold and die making: Wire EDM machining can create intricate molds and dies for injection molding, stamping, forging, and casting processes that produce various products such as plastic parts, metal parts, jewelry, coins, and more.
- Electronics: Wire EDM machining can cut and etch circuit boards, semiconductors, sensors, switches, and other electronic components that need to have precise dimensions and features.
- What are the types and specifications of wire EDM machines?
Wire EDM machines are a type of electrical discharge machining (EDM) that use a thin wire as an electrode to cut metal with high precision and accuracy. Wire EDM machines can create complex shapes and intricate details that are difficult or impossible to achieve with other machining methods. Wire EDM machines are widely used in industries such as aerospace, medical, automotive, and mold making.
There are two main types of wire EDM machines: conventional and high-speed. Conventional wire EDM machines use a brass wire that is continuously fed from a spool through the workpiece and then collected on another spool. The wire is charged with a high voltage and creates a spark gap between the wire and the workpiece, which erodes the metal. The wire is constantly moving to avoid breaking or short-circuiting. Conventional wire EDM machines can cut any conductive material, but they are relatively slow and consume a lot of wire.
High-speed wire EDM machines use a coated wire that is specially designed to withstand higher temperatures and currents. The wire is also fed from a spool through the workpiece, but it is not collected on another spool. Instead, the wire is cut off after each pass and disposed of. High-speed wire EDM machines can cut faster and more efficiently than conventional ones, but they are more expensive and require more maintenance.
The specifications of wire EDM machines vary depending on the model and manufacturer, but some common parameters are:
- Wire diameter: The thickness of the wire used as an electrode. It can range from 0.02 mm to 0.3 mm, depending on the desired accuracy and surface finish.
- Wire tension: The force applied to the wire to keep it straight and stable. It can range from 3 N to 25 N, depending on the wire diameter and cutting speed.
- Wire speed: The rate at which the wire is fed through the workpiece. It can range from 0.5 m/min to 15 m/min, depending on the material and thickness of the workpiece.
- Spark gap: The distance between the wire and the workpiece where the spark occurs. It can range from 0.005 mm to 0.05 mm, depending on the wire diameter and cutting speed.
- Spark frequency: The number of sparks per second that occur between the wire and the workpiece. It can range from 50 kHz to 500 kHz, depending on the power supply and cutting speed.
- Spark voltage: The potential difference between the wire and the workpiece that generates the spark. It can range from 50 V to 400 V, depending on the material and thickness of the workpiece.
- Spark current: The amount of electric current that flows through the spark gap. It can range from 0.5 A to 25 A, depending on the material and thickness of the workpiece.
Wire EDM machines are a versatile and precise machining tool that can create high-quality parts with complex geometries and fine details. However, they also require careful operation and maintenance to ensure optimal performance and safety.
- What are the materials and thicknesses that can be cut by wire EDM machining?
Wire EDM machining is a process that uses a thin metal wire to cut through various materials with high precision and accuracy. Wire EDM machining can cut through materials that are hard, brittle, or conductive, such as metals, alloys, ceramics, and composites. Wire EDM machining can also create complex shapes and intricate details that are difficult or impossible to achieve with other cutting methods.
One of the factors that determines the capability of wire EDM machining is the thickness of the material to be cut. The thickness of the material affects the speed, accuracy, and quality of the cut. Generally speaking, the thicker the material, the slower the cutting speed, the lower the accuracy, and the rougher the surface finish. However, the thickness of the material also depends on other factors, such as the type of material, the diameter of the wire, the power of the machine, and the settings of the machine.
Different materials have different properties that affect their suitability for wire EDM machining. Some materials are more resistant to heat and wear than others, which means they can withstand higher temperatures and pressures during the cutting process. Some materials are more conductive than others, which means they can transfer electricity more easily and efficiently. Some materials are more ductile than others, which means they can deform more easily without breaking.
The table below shows some examples of materials and their approximate maximum thicknesses that can be cut by wire EDM machining.
| Material | Maximum Thickness |
| -------- | ----------------- |
| Steel | 300 mm |
| Aluminum | 200 mm |
| Copper | 150 mm |
| Titanium | 100 mm |
| Brass | 80 mm |
| Carbide | 50 mm |
| Ceramic | 10 mm |
The diameter of the wire also affects the cutting performance of wire EDM machining. The wire diameter determines the size of the kerf, which is the gap left by the wire after cutting. The smaller the wire diameter, the smaller the kerf, which means higher accuracy and finer details. However, smaller wires also have lower tensile strength and higher resistance, which means they are more prone to breaking and overheating. Therefore, smaller wires require lower cutting speeds and lower power settings.
The power of the machine is another factor that influences the cutting capability of wire EDM machining. The power of the machine determines how much current and voltage are applied to the wire and the material during the cutting process. The higher the power, the faster and deeper the cut, but also the higher the risk of melting or burning the material. Therefore, higher power requires higher cooling and flushing systems to prevent damage to the wire and the material.
The settings of the machine are also important for optimizing the cutting performance of wire EDM machining. The settings include parameters such as pulse frequency, pulse duration, pulse gap, feed rate, tension, and spark gap. These parameters affect how much energy is delivered to the wire and the material during each pulse cycle. By adjusting these parameters, one can control the speed, accuracy, quality, and efficiency of the cut.
Wire EDM machining is a versatile and precise cutting method that can handle various materials and thicknesses. However, one must consider several factors that affect its capability and performance. By choosing the right material, wire diameter, power level, and machine settings, one can achieve optimal results with wire EDM machining.
- What are the factors that affect the accuracy and quality of wire EDM machining?
Wire EDM machining is a process that uses an electrically charged wire to cut through various materials, such as metal, plastic, or wood. Wire EDM machining can produce complex shapes and intricate details with high precision and accuracy. However, there are several factors that can affect the quality and accuracy of wire EDM machining, such as:
- Wire tension: The wire tension is the force that keeps the wire straight and stable during the cutting process. If the wire tension is too low, the wire can bend or vibrate, causing irregularities and errors in the cut. If the wire tension is too high, the wire can break or wear out faster, reducing the lifespan of the wire and increasing the cost of the process. Therefore, it is important to maintain a proper wire tension that is suitable for the material and thickness of the workpiece.
- Wire feed rate: The wire feed rate is the speed at which the wire moves through the workpiece. The wire feed rate affects the cutting speed and the surface finish of the cut. A higher wire feed rate can increase the cutting speed, but it can also cause more heat and sparks, which can damage the workpiece or the wire. A lower wire feed rate can improve the surface finish, but it can also reduce the cutting speed and increase the wear of the wire. Therefore, it is important to adjust the wire feed rate according to the material and shape of the workpiece.
- Dielectric fluid: The dielectric fluid is a liquid that surrounds the wire and the workpiece during the cutting process. The dielectric fluid serves as a coolant, a lubricant, and a conductor for the electrical discharge. The dielectric fluid affects the quality and accuracy of wire EDM machining in several ways, such as:
- Cooling: The dielectric fluid helps to cool down the wire and the workpiece, preventing overheating and thermal distortion. The dielectric fluid also helps to flush away the debris and particles that are generated by the cutting process, preventing them from interfering with the electrical discharge or clogging the gap between the wire and the workpiece.
- Lubrication: The dielectric fluid helps to lubricate the wire and reduce friction, extending the life of the wire and improving its performance. The dielectric fluid also helps to prevent corrosion and oxidation of the wire and the workpiece, preserving their quality and appearance.
- Conduction: The dielectric fluid helps to conduct electricity between the wire and the workpiece, creating a controlled spark that cuts through the material. The dielectric fluid also helps to regulate the intensity and frequency of the spark, affecting the cutting speed and accuracy.
Therefore, it is important to choose a suitable dielectric fluid that has a proper viscosity, conductivity, and purity for wire EDM machining.
These are some of the main factors that affect the accuracy and quality of wire EDM machining. By understanding these factors and optimizing them for each application, one can achieve better results with wire EDM machining.
- What are the costs and benefits of wire EDM machining compared to other methods?
Wire EDM machining is a process that uses an electrically charged wire to cut through metal materials with high precision and accuracy. Wire EDM machining has several advantages and disadvantages compared to other methods of metal cutting, such as laser cutting, plasma cutting, waterjet cutting, etc. In this blog post, we will explore some of the costs and benefits of wire EDM machining and how it compares to other techniques.
One of the main benefits of wire EDM machining is that it can cut complex shapes and intricate details that are difficult or impossible to achieve with other methods. Wire EDM machining can create sharp corners, narrow slots, fine holes, and intricate contours with high accuracy and repeatability. Wire EDM machining can also cut very thin and delicate materials without causing distortion or damage, as well as hard and tough materials that are resistant to other cutting methods.
Another benefit of wire EDM machining is that it does not generate heat or mechanical stress on the workpiece, unlike other methods that use high temperatures or physical force to cut through metal. This means that wire EDM machining does not affect the structural integrity or the surface finish of the metal, and does not create burrs, cracks, or deformations. Wire EDM machining also does not require any secondary operations, such as deburring, polishing, or cleaning, which can save time and money.
However, wire EDM machining also has some drawbacks that limit its applicability and efficiency. One of the main drawbacks of wire EDM machining is that it is a slow and expensive process compared to other methods. Wire EDM machining requires a lot of electricity to generate the sparks that cut through the metal, and also consumes a lot of wire that needs to be constantly replaced. Wire EDM machining also requires a dielectric fluid, such as water or oil, to cool and flush away the debris from the cutting zone. These factors increase the operational costs and maintenance requirements of wire EDM machining.
Another drawback of wire EDM machining is that it can only cut conductive materials, such as metals, alloys, graphite, etc. This means that wire EDM machining cannot cut non-conductive materials, such as plastics, ceramics, glass, wood, etc., which limits its versatility and range of applications. Wire EDM machining also cannot cut very thick or large materials, as the wire can break or lose accuracy when cutting through long distances or deep cuts.
In conclusion, wire EDM machining is a process that has some unique advantages and disadvantages compared to other methods of metal cutting. Wire EDM machining can cut complex shapes and intricate details with high precision and accuracy, without generating heat or mechanical stress on the workpiece. However, wire EDM machining is also a slow and expensive process that consumes a lot of electricity and wire, and can only cut conductive materials. Therefore, wire EDM machining is best suited for applications that require high quality and accuracy, but not speed or low cost.
- How to design and prepare parts for wire EDM machining?
Wire EDM (electrical discharge machining) is a process that uses a thin wire electrode to cut through metal with high precision and accuracy. Wire EDM is ideal for creating complex shapes, intricate details, and fine finishes on metal parts. However, wire EDM also requires careful design and preparation of the parts to ensure optimal results. In this blog post, we will discuss some of the best practices for designing and preparing parts for wire EDM machining.
Design considerations for wire EDM
When designing parts for wire EDM, there are several factors to consider, such as:
- Material selection: Wire EDM can cut through most conductive metals, such as steel, aluminum, copper, brass, titanium, and tungsten. However, some materials are more suitable than others for wire EDM, depending on the desired properties and performance of the part. For example, steel is a common choice for wire EDM because it has high strength, hardness, and wear resistance. Aluminum is another popular option because it has low density, high thermal conductivity, and good machinability. Copper and brass are preferred for electrical applications because they have high electrical conductivity and low electrical resistance. Titanium and tungsten are used for high-temperature and corrosion-resistant applications because they have high melting points and excellent chemical stability.
- Part geometry: Wire EDM can create complex shapes and contours that are difficult or impossible to achieve with other machining methods. However, wire EDM also has some limitations in terms of part geometry, such as:
- Minimum radius: Wire EDM uses a thin wire electrode that can bend around corners and curves, but it cannot cut sharp angles or corners. The minimum radius that wire EDM can cut depends on the diameter of the wire electrode, the material of the part, and the cutting parameters. Typically, the minimum radius ranges from 0.1 mm to 0.5 mm.
- Maximum thickness: Wire EDM can cut through thick materials, but it also takes longer and consumes more power and wire. The maximum thickness that wire EDM can cut depends on the material of the part, the diameter of the wire electrode, and the cutting parameters. Typically, the maximum thickness ranges from 300 mm to 500 mm.
- Taper angle: Wire EDM can create tapered cuts by tilting the wire electrode relative to the workpiece. However, the taper angle that wire EDM can achieve is limited by the geometry of the part and the accuracy of the machine. Typically, the taper angle ranges from 0° to 45°.
- Part tolerance: Wire EDM can produce parts with high dimensional accuracy and surface quality. However, wire EDM also has some sources of error and variation that can affect the part tolerance, such as:
- Thermal expansion: Wire EDM generates heat during the cutting process, which can cause thermal expansion of both the wire electrode and the workpiece. Thermal expansion can result in dimensional changes and distortions of the part. To minimize thermal expansion, it is important to use appropriate cooling systems and cutting parameters.
- Wire wear: Wire EDM uses a consumable wire electrode that wears out gradually during the cutting process. Wire wear can result in changes in the diameter and shape of the wire electrode, which can affect the accuracy and quality of the cut. To minimize wire wear, it is important to use high-quality wire electrodes and replace them regularly.
- Machine alignment: Wire EDM requires precise alignment of the wire electrode and the workpiece to ensure accurate and consistent cuts. However, machine alignment can be affected by various factors, such as vibration, temperature changes, mechanical wear, and human error. To maintain machine alignment, it is important to calibrate and adjust the machine regularly.
Preparation steps for wire EDM
Before sending parts to wire EDM machining, there are some preparation steps that can help improve the efficiency and quality of the process, such as:
- Cleaning: It is essential to clean the parts thoroughly before wire EDM machining to remove any dirt, grease, oil, rust, or other contaminants that could interfere with the electrical discharge or damage the wire electrode or the workpiece. Cleaning can be done by using various methods, such as ultrasonic cleaning, solvent cleaning, or abrasive blasting.
- Marking: It is helpful to mark the parts with identification numbers or labels before wire EDM machining to facilitate tracking and inspection of the parts. Marking can be done by using various methods, such as engraving, stamping, or laser marking.
- Fixturing: It is necessary to fixture the parts securely before wire EDM machining to prevent any movement or displacement of the parts during the cutting process. Fixturing can be done by using various methods, such as clamping, bolting, welding, or gluing.
- Piercing: It is required to pierce holes in the parts before wire EDM machining to allow the insertion of the wire electrode into the part. Piercing can be done by using various methods,
- How to choose the right wire type and diameter for wire EDM machining?
Wire EDM (electrical discharge machining) is a process that uses a thin metal wire to cut complex shapes and patterns from conductive materials. Wire EDM is widely used in industries such as aerospace, medical, automotive, and mold making.
One of the most important factors that affect the quality and efficiency of wire EDM is the choice of wire type and diameter. Different wire types and diameters have different advantages and disadvantages depending on the material, thickness, accuracy, and surface finish required for the workpiece.
In this blog post, we will discuss some of the main considerations and recommendations for choosing the right wire type and diameter for wire EDM machining.
Wire types
There are two main types of wires used for wire EDM: brass and coated. Brass wires are the most common and economical option, as they have good conductivity, tensile strength, and cutting speed. However, brass wires also have some drawbacks, such as lower accuracy, higher wear rate, and more frequent wire breaks.
Coated wires are wires that have a thin layer of metal or alloy applied to the surface of a brass core. The coating can enhance the performance of the wire by improving its conductivity, hardness, durability, or cutting speed. Some of the common coatings are zinc, copper, tungsten, molybdenum, and gamma-phase. Coated wires are more expensive than brass wires, but they can offer higher accuracy, lower wear rate, less wire breaks, and better surface finish.
Wire diameters
The diameter of the wire affects the kerf width, which is the gap left by the wire after cutting. The kerf width determines how much material is removed and how close the wire can get to the desired shape. The smaller the diameter, the smaller the kerf width, and vice versa.
The choice of wire diameter depends on several factors, such as:
- The thickness of the workpiece: thicker materials require larger diameters to avoid excessive resistance and heat generation.
- The accuracy of the workpiece: smaller diameters allow for higher accuracy and finer details, as they can follow tighter radii and corners.
- The surface finish of the workpiece: smaller diameters produce smoother surfaces, as they reduce the roughness and striations caused by the sparks.
- The cutting speed of the workpiece: larger diameters enable faster cutting speeds, as they have more contact area and current flow.
- The cost of the workpiece: smaller diameters consume more wire per unit length, as they have higher wear rate and breakage rate.
As a general rule of thumb, the optimal wire diameter is about 10% to 20% of the workpiece thickness. However, this may vary depending on the specific requirements and preferences of each project.
Conclusion
Choosing the right wire type and diameter for wire EDM machining is a crucial step that can affect the quality, efficiency, and cost of your project. By considering factors such as material, thickness, accuracy, surface finish, cutting speed, and cost, you can select the best wire type and diameter for your needs.
We hope this blog post has been helpful and informative for you. If you have any questions or comments about wire EDM machining or any other machining services we offer at XYZ Inc., please feel free to contact us anytime. We are always happy to assist you with your machining needs.
- How to optimize the cutting parameters and settings for wire EDM machining?
Wire EDM machining is a process that uses a thin wire as an electrode to cut through electrically conductive materials with high precision and accuracy. Wire EDM machining is widely used in industries such as aerospace, medical, automotive, and mold making. However, wire EDM machining also poses some challenges, such as high operating costs, long machining times, and complex process parameters. Therefore, it is important to optimize the cutting parameters and settings for wire EDM machining to achieve the best results.
In this blog post, we will discuss some of the key factors that affect the quality and efficiency of wire EDM machining, and how to optimize them for different applications and materials. We will also provide some tips and best practices for wire EDM machining that can help you improve your productivity and reduce your costs.
Cutting Parameters and Settings for Wire EDM Machining
There are many cutting parameters and settings that influence the performance of wire EDM machining, such as:
- Wire diameter: The wire diameter determines the kerf width, the minimum radius of curvature, and the surface finish of the cut. Generally, smaller wire diameters produce narrower kerfs, smaller radii, and smoother surfaces, but they also require higher tension, lower feed rate, and more frequent wire changes. Larger wire diameters produce wider kerfs, larger radii, and rougher surfaces, but they also require lower tension, higher feed rate, and less frequent wire changes. Therefore, the optimal wire diameter depends on the desired accuracy, geometry, and surface quality of the workpiece.
- Wire material: The wire material affects the electrical conductivity, wear resistance, and tensile strength of the wire. Commonly used wire materials include brass, copper, zinc-coated brass, tungsten, molybdenum, and coated wires. Brass wires are the most widely used due to their high conductivity, low cost, and good machinability. However, they also wear faster and have lower tensile strength than other wires. Copper wires have higher conductivity and tensile strength than brass wires, but they are more expensive and harder to machine. Zinc-coated brass wires have better wear resistance and surface finish than brass wires, but they are also more expensive and prone to zinc build-up on the workpiece. Tungsten and molybdenum wires have high tensile strength and wear resistance, but they are also very expensive and have low conductivity. Coated wires have a core of brass or copper coated with a thin layer of tungsten or molybdenum to combine the advantages of both materials.
- Wire tension: The wire tension affects the straightness, stability, and accuracy of the wire. Too low wire tension can cause wire sagging, vibration, deflection, and deviation from the programmed path. Too high wire tension can cause wire breakage, overheating, excessive wear, and reduced feed rate. Therefore, the optimal wire tension depends on the wire diameter, material, speed, and geometry of the cut.
- Wire feed rate: The wire feed rate determines the speed at which the wire moves through the workpiece. Higher wire feed rates can increase the productivity and efficiency of wire EDM machining by reducing the machining time. However,
- How to find a reliable and experienced wire EDM machining service provider?
Wire EDM machining is a process that uses an electrically charged wire to cut through various materials, such as metal, plastic, or wood. Wire EDM machining can produce complex shapes and intricate details with high precision and accuracy. However, not all wire EDM machining service providers are created equal. If you are looking for a reliable and experienced wire EDM machining service provider, here are some tips to help you find the best one for your needs.
- Check their portfolio and testimonials. A good way to assess the quality and expertise of a wire EDM machining service provider is to look at their previous projects and customer feedback. You can ask for samples of their work, or visit their website and social media pages to see what they have done and what their clients say about them. This will give you an idea of their capabilities, strengths, and areas of improvement.
- Compare their prices and services. Another factor to consider when choosing a wire EDM machining service provider is their pricing and service offerings. You should compare different providers based on the scope, complexity, and duration of your project, as well as the materials, equipment, and technology they use. You should also inquire about any additional services they provide, such as design, engineering, quality control, or delivery. You want to find a provider that can offer you the best value for your money, without compromising on quality or efficiency.
- Ask for references and certifications. A reputable wire EDM machining service provider should be able to provide you with references and certifications that attest to their professionalism and credibility. You can contact their previous or current customers and ask them about their experience working with the provider, such as their communication, timeliness, problem-solving, and satisfaction. You can also check if the provider has any industry-specific certifications or accreditations that demonstrate their competence and compliance with standards and regulations.
- Evaluate their communication and customer service. Finally, you should evaluate how the wire EDM machining service provider communicates and interacts with you as a potential customer. You should look for a provider that is responsive, courteous, and attentive to your needs and expectations. You should also feel comfortable asking them questions, expressing your concerns, or giving feedback. A good provider will listen to you, understand your goals, and offer you solutions that suit your requirements.
Finding a reliable and experienced wire EDM machining service provider can be challenging, but not impossible. By following these tips, you can narrow down your options and select the best one for your project. Remember that wire EDM machining is a complex and delicate process that requires skill and experience, so you should not settle for anything less than the best.