Professional 3D Printing Service
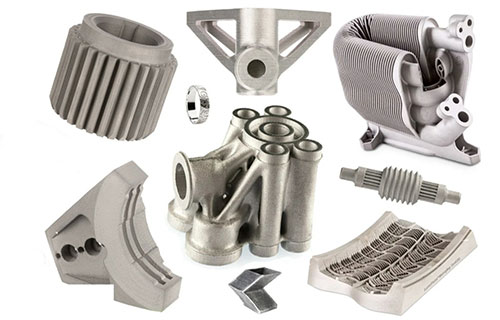
3D Printing: High-Quality Rapid Prototyping and Production Parts
Experience the industry-leading 3D printing solutions provided by our experts! As a full-service additive manufacturing provider, we are able to quickly turn around prototypes and produce complex custom parts quickly and accurately. Within a week, we can turn the design in the CAD file into a finished 3D printed object. Whether you need a single model or mass production, our multifunctional printers can produce components with precise dimensions, fine details, strict tolerances, and excellent surface smoothness. As your trusted manufacturing partner, we provide affordable and customized solutions based on your application, as well as early quotes and fast delivery times. Let our engineers optimize the design for your printing and mass production. Contact us immediately to discuss how we can take your product to the next level using advanced 3D printing technology!
Custom Personal 3D Printing Additive Manufacturing Service
By utilizing cutting-edge additive technology, we manufacture cost-effective components with unparalleled functionality and quality. As an industry leader in providing the most diverse materials, our well-trained team utilizes 8 advanced plastic and over 60 metal 3D printing processes. This includes selective laser sintering, melt deposition modeling, stereolithography, direct metal laser sintering, PolyJet, Carbon DLS, Nexa3D LSPc, and powder bed melting methods. By utilizing industrial grade equipment such as high-performance Stratasys Fortus 900mc and Fortus 450 FDM platforms, as well as top-notch powder bed fusion solutions from EOS, Concept Laser, and SLM solutions, we design precision parts with unparalleled resolution, strength, and surface quality. As a comprehensive service provider, our inclusive solutions drive the forefront of technology and transform innovative designs into final products. Contact us immediately to explore how we can maximize your application potential through cutting-edge additive manufacturing.
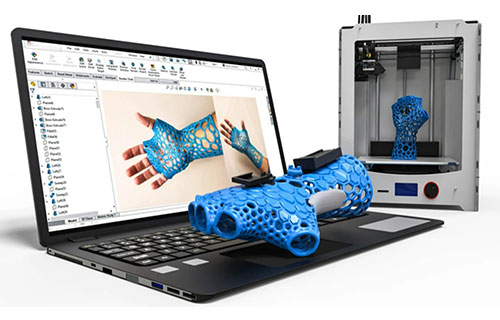
Thermoplastic 3D Printing
Selective Laser Sintering (SLS) 3D Printing Service
Selective Laser Sintering (SLS) 3D printing service is a technology that uses lasers to melt nylon powder into solid parts. SLS 3D printing services provide high precision, durability, and functionality for various applications such as prototyping, small batch production, and end use parts. SLS 3D printing services do not require supporting structures, reducing material waste and post-processing time. SLS 3D printing services can produce parts with complex geometric shapes, fine details, and smooth surfaces. SLS 3D printing services can also use different materials, such as glass filling, carbon filling, or flame-retardant nylon, to achieve specific performance and capabilities.
HP Multi Jet Fusion (MJF) 3D Printing Service
HP Multi Jet Fusion (MJF) 3D printing service is a cutting-edge technology that produces complex and functional parts quickly, accurately, and cost-effectively.MJF uses fine-grained materials for high resolution and smooth surface finishes.MJF also supports full-color printing and post-processing options such as dyeing, penetrating, and coating. With MJF, you can create prototypes, end-use products, or customized parts with high performance and durability.
Fused Deposition Modeling (FDM) 3D Printing Service
Fused deposition modeling (FDM) 3D printing services is an additive manufacturing technology that uses thermoplastic filaments to create solid objects. The filament is heated and extruded layer-by-layer through a nozzle onto a build platform.FDM 3D printing services are ideally suited for rapid prototyping, functional testing, and low-volume production of complex parts.FDM 3D printing services are available in a wide range of materials, colors, and finishes, as well as high precision and durability.
Thermoset 3D Printing
Stereolithography (SLA) 3D Printing Service
Stereolithography (SLA) 3D printing service is a type of additive manufacturing that uses liquid resin and ultraviolet light to create solid objects.SLA 3D printing produces high-quality parts with smooth surfaces, intricate details, and complex geometries.SLA 3D printing is suitable for applications such as prototyping, jewelry making, dental implants, etc.SLA 3D printing works by curing the resin layer by layer until the final object is complete. The thickness of each layer can vary from 10µm to 50µm, depending on the desired resolution and print time.SLA 3D printing requires support structures, resin cleaning, support removal, and post-curing to ensure stability and durability of the part.
PolyJet 3D Printing Service
PolyJet 3D Printing Services is a technology that allows you to create high-resolution, multi-material and full-colour models in a fast and cost-effective way.PolyJet 3D Printing Services uses a jetting process that deposits tiny liquid photopolymer droplets onto a build tray, where they are cured with UV light. The result is a smooth, detailed surface that mimics the look and feel of the final product.PolyJet 3D printing services are ideal for prototyping, design verification and testing applications that require complex geometries, intricate detail and realistic textures.
Production Photopolymer 3D Printing
Nexa3D LSPc® Resin 3D Printing Service
The Nexa3D LSPc® Resin 3D Printing Service is a fast and reliable way to produce high-quality parts with complex geometries and fine details.LSPc® stands for Lubricant Sublayer Light Curing, a patented technology that uses a transparent film to reduce the adhesion between the resin and the build platform, resulting in faster layer changeovers and higher print speeds. With Nexa3D LSPc® resin 3D printing services, you get a range of materials with different properties such as toughness, flexibility, heat resistance, and biocompatibility. Whether you need prototypes, functional parts, or dental models, Nexa3D LSPc®Resin 3D printing services can be delivered within hours.
Carbon Digital Light Synthesis™ (DLS™) 3D Printing Service
The Carbon Digital Light Synthesis™ (DLS™) 3D printing service is a revolutionary technology that uses light and oxygen to create high quality, durable and functional parts from a wide range of materials. Unlike traditional 3D printing methods, DLS™ produces complex geometries, smooth surface finishes and fine details quickly and accurately. Whether you need a prototype, end-use product or custom solution, Carbon DLS™ 3D printing services can help you achieve your goals quickly and efficiently.
Metal 3D Printing
Selective Laser Melting (SLM) 3D Printing Service
SLM selective laser melting is a metal additive manufacturing or 3D printing technology that uses a high-powered laser to melt and fuse metal powders into dense parts.SLM can produce parts with complex geometries, fine features, and high strengths for a variety of applications such as medical, aerospace, and automotive.SLM is one of the fastest and most accurate metal 3D printing technologies available today, and can be used with a a range of metal alloys such as stainless steel, aluminium and nickel-based alloys.
Direct Metal Laser Sintering (DMLS) 3D Printing Service
Direct metal laser sintering (DMLS) is a 3D printing technology that uses lasers to melt metal powders into solid parts.DMLS can produce complex and functional metal parts in a variety of alloys, such as titanium, aluminium, steel, and nickel.DMLS is used in a wide range of applications for prototyping and production in industries such as aerospace, defence, medical, automotive, and energy.DMLS offers high strength, durability, corrosion resistance and heat resistance.
Metal Binder Jetting 3D Printing Service
Metal binder jet 3D printing service is a process that uses an adhesive to bond metal powder particles together layer by layer. The adhesive acts as a glue, holding the metal parts together until they are sintered in a furnace. The service allows the creation of complex and detailed metal parts with high precision and resolution. The metal binder jet 3D printing service is suitable for applications such as prototyping, moulds, jewellery and medical devices.
3D printing plastic and metal materials
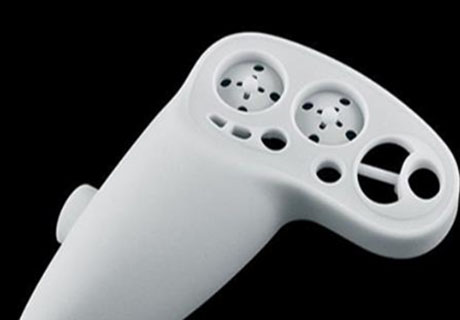
3D printing materials - photosensitive resin
Introduction: The resin is a thermosetting photopolymer that cures when exposed to light, producing highly detailed areas and providing a smooth surface finish on injection moulds.
Accuracy: Tolerance ± 0.5%. (Minimum value: ± 0.05 mm)
Forming: maximum component size 3850mm x 2400mm x 1600mm
Strength: tensile strength 42-50 MPa
Temperature resistance: 40-60 degrees Celsius
Delivery time: up to 12 hours
Applicable: Exhibition models, sculpture decorations, non functional prototype verification of hand boards
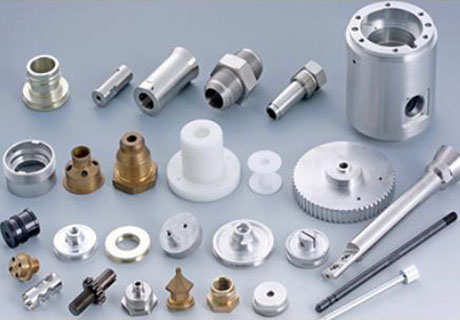
3D printing material - stainless steel 316
Introduction: Stainless steel (DMLS/SLM) has high ductility and excellent corrosion resistance. It produces fully dense components for industrial applications.
Accuracy: tolerance ± 0.1 mm
Forming: The maximum component size is 80 x 50 x 50 centimeters
Strength: tensile strength 42-50 MPa
Temperature resistance: 40-60 degrees Celsius
Delivery time: up to 12 hours
Applicable to: direct manufacturing of components, functional verification, temperature resistance of 850 degrees, military manufacturing
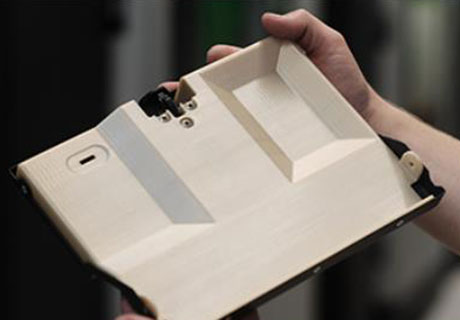
3D printing materials - PLA plastic
Introduction: PLA is a biodegradable thermoplastic for low-cost, non-functional prototyping. It is more detailed than ABS, but more brittle and not suitable for high temperatures.
Accuracy: tolerance ± 0.5% (minimum value: ± 0.05 mm)
Forming: Maximum component size 100 x 100 x 100 centimeters
Strength: tensile strength 42-50 MPa
Temperature resistance: 40-60 degrees Celsius
Delivery time: up to 12 hours
Applicable: educational models, sculpture decorations, material advantages, environmental protection
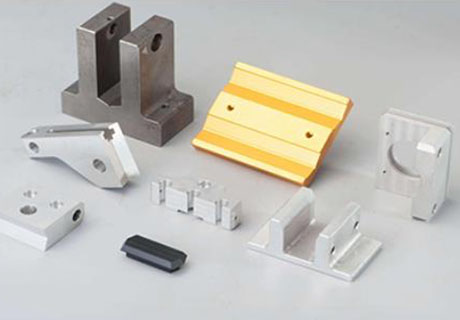
3D Printing Material - Aluminum
Introduction: Aluminum (DMLS/SLM) is a low-density metal with excellent mechanical and thermal properties as well as good conductivity.
Accuracy: tolerance ± 0.1 mm
Forming: The maximum component size is 80 x 50 x 50 centimeters
Strength: tensile strength 42-50 MPa
Temperature resistance: 40-60 degrees Celsius
Delivery time: up to 12 hours
Applicable: structural function verification, small batch metal component manufacturing, temperature resistance of 420 degrees, military manufacturing
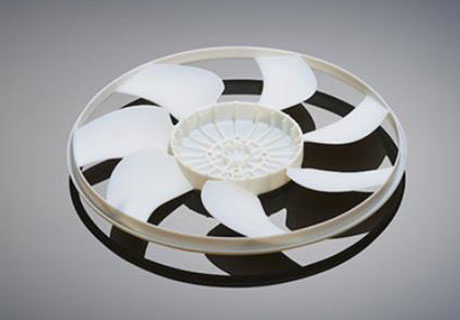
3D printing materials - ABS materials
Introduction: FDM in ABS material is the most widely used 3D printing process, mainly for low-cost prototyping and design verification with very fast turnaround times.
Accuracy: tolerance ± 0.5% (minimum value: ± 0.05 mm)
Forming: Maximum component size 100 x 100 x 100 centimeters
Strength: tensile strength 42-50 MPa
Temperature resistance: 40-60 degrees Celsius
Delivery time: up to 12 hours
Applicable: verification of hand board model, functional verification, material advantages, good smoothness, and temperature resistance of 70 degrees
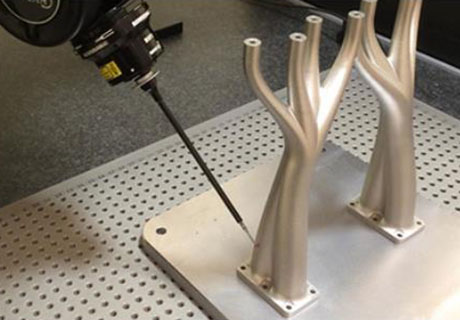
3D Printing Material - Titanium
Introduction: Titanium (DMLS/SLM) has excellent mechanical properties, corrosion resistance, and strength to weight ratio. It has disinfectability and biocompatibility
Accuracy: tolerance ± 0.1 mm
Forming: The maximum component size is 80 x 50 x 50 centimeters
Strength: tensile strength 42-50 MPa
Temperature resistance: 40-60 degrees Celsius
Delivery time: up to 12 hours
Applicable: special verification, functional verification, high-strength component manufacturing, temperature resistance of 1600 degrees Celsius
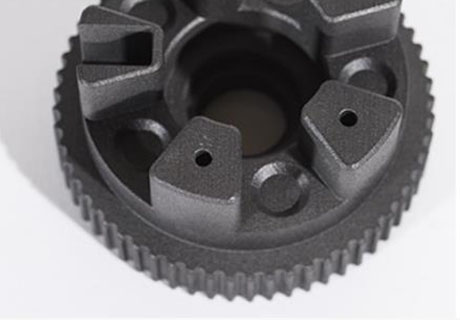
3D printing material - nylon material
Introduction: Nylon or polyamide (PA) is a thermoplastic with excellent mechanical properties, high chemical resistance, and wear resistance. Very suitable for functional applications.
Accuracy: tolerance ± 0.1% (minimum value: ± 0.1 mm)
Forming: Maximum part size 75 x 55 x 55 cm
Strength: tensile strength 42-50 MPa
Temperature resistance: 40-60 degrees Celsius
Delivery time: up to 12 hours
Applicable: verification of hand board model, functional verification, material advantages, good smoothness, temperature resistance of 170 degrees
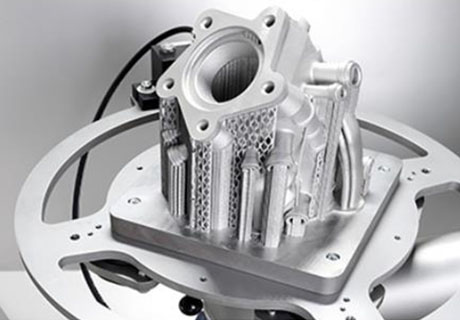
3D printing material - cobalt chromium alloy
Introduction: Cobalt chromium alloy (DMLS/SLM) is a high corrosion and wear resistant material with excellent temperature resistance. Suitable for biomedical applications.
Accuracy: tolerance ± 0.1 mm
Forming: The maximum component size is 80 x 50 x 50 centimeters
Strength: tensile strength 42-50 MPa
Temperature resistance: 40-60 degrees Celsius
Delivery time: up to 12 hours
Applicable: special verification, functional verification, high-strength component manufacturing, military manufacturing
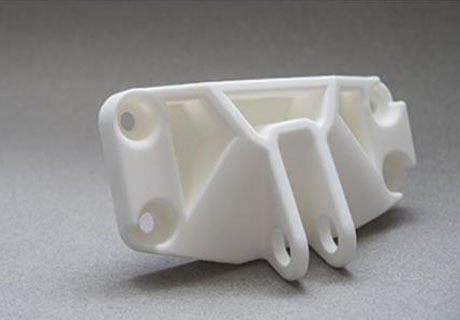
3D printing material - ULTEM plastic
Introduction: ULTEM (FDM) is an engineering plastic with good mechanical properties, excellent heat resistance, chemical resistance, and flame retardancy. Suitable for high-end applications.
Accuracy: tolerance ± 0.5% (minimum value: ± 0.05 mm)
Forming: Maximum component size 100 x 100 x 100 centimeters
Strength: tensile strength 42-50 MPa
Temperature resistance: 40-60 degrees Celsius
Delivery time: up to 12 hours
Applicable: verification of hand board model, functional verification, material advantages, good smoothness, and temperature resistance of 70 degrees
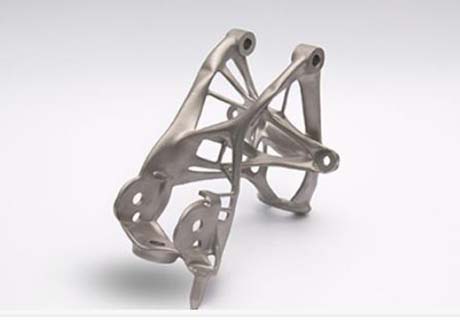
3D Printing Materials - Chromium Nickel Iron Alloy
Introduction: Inconel (DMLS/SLM) is a metal superalloy with excellent tensile, fatigue, creep, and fracture strength, making it an ideal choice for high-temperature applications.
Accuracy: tolerance ± 0.1 mm
Forming: The maximum component size is 80 x 50 x 50 centimeters
Strength: tensile strength 42-50 MPa
Temperature resistance: 40-60 degrees Celsius
Delivery time: up to 12 hours
Applicable: special verification, functional verification, high-strength component manufacturing, military manufacturing
3D printing equipment and capabilities
As a professional 3D printing company, we have 50 SLA resin 3D printers, as well as 6 SLS nylon 3D printers and metal 3D printers. We have a wide range of 3D printing materials to choose from, as well as a variety of post-processing techniques and complete outsourced machining capabilities. We provide 3D printing, replication and colouring services, and have established a dedicated model making business team with excellent display analysis and design capabilities. We have strict quality management system certification. We have rich experience in automotive, household appliances, office equipment, architectural models, medical and dental, jewellery, sculpture, ceramics and other industries.
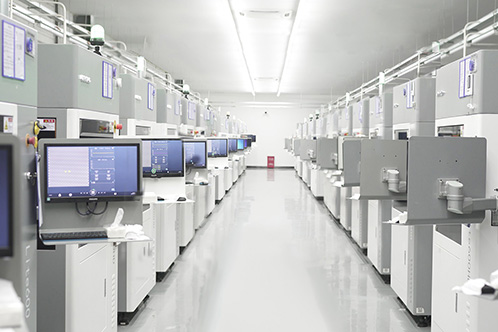
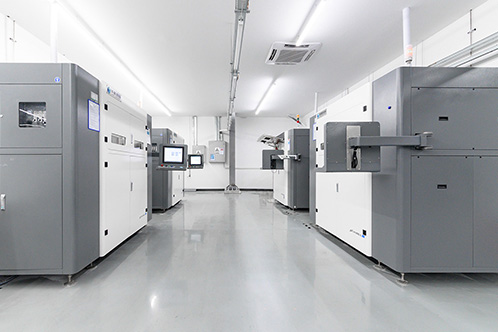
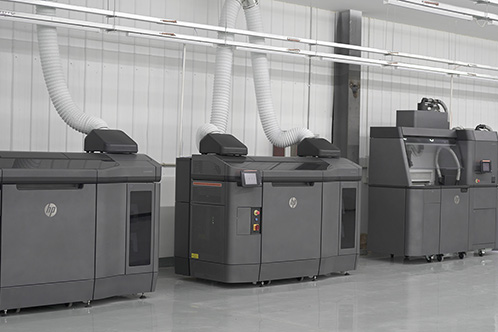
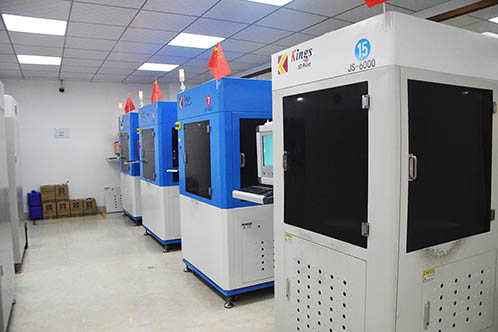
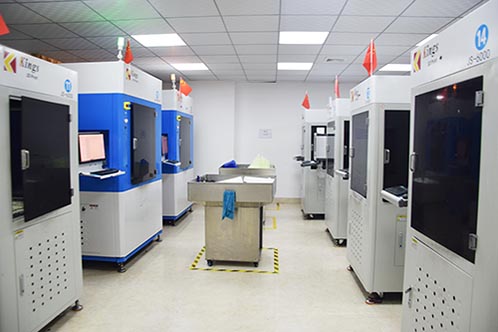
Part 3D printing Frequently Asked Questions
What is 3D printing service?
3D printing services is a professional service that offers the ability to convert digital designs into physical objects using 3D printing technology. It provides individuals, businesses and organisations with the means to bring their ideas to life using specialist equipment and expertise in the field of additive manufacturing. Customers can submit their digital models or designs to a service provider, who then uses 3D printers to create physical objects layer-by-layer according to the specifications provided.3D printing services can offer a range of materials, finishes and printing techniques to suit a variety of needs and applications. This service is commonly used for prototyping, product development, customisation and small-scale production. It offers benefits such as fast turnaround times, design flexibility, cost-effectiveness in small-volume production, and the ability to create complex geometries that would be difficult to achieve with traditional manufacturing methods.3D printing services have revolutionised the manufacturing landscape, enabling innovation, customisation and rapid product development across a wide range of industries.
How does 3D printing work?
3D printing, also known as additive manufacturing, is a process that builds physical objects layer by layer using computer-controlled machines. Here is a professional explanation of how 3D printing works:
- Design: The process begins with a digital 3D model of the object created using computer-aided design (CAD) software or obtained from a 3D model repository.
- Slicing: The 3D model is then sliced into thin layers using specialized software. Each layer is a thin cross-section of the object, typically ranging from fractions of a millimeter to a few millimeters thick.
- Preparation: The sliced model is prepared for printing by specifying the printing parameters such as layer thickness, infill density, and support structures if required.
- Printing: The prepared model is sent to a 3D printer, which interprets the instructions and begins the printing process. The printer typically uses one of several additive manufacturing technologies, such as fused deposition modeling (FDM), stereolithography (SLA), or selective laser sintering (SLS).
- Layer-by-Layer Building: The 3D printer starts building the object by depositing or solidifying material layer by layer. The specific method depends on the technology used. For example, in FDM, a thermoplastic filament is heated and extruded through a nozzle, while in SLA, a liquid resin is cured layer by layer using a UV laser.
- Support Structures: If the design requires overhangs or complex geometries, temporary support structures may be added during printing to ensure stability. These supports can be removed after printing is complete.
- Finishing: Once the object is fully printed, it may require post-processing steps such as removing support structures, sanding, polishing, or applying surface treatments to achieve the desired final appearance and smoothness.
The key advantage of 3D printing is its ability to create complex shapes and intricate details with high precision. The process offers design freedom, enabling the production of customized and unique objects. It is used in various industries, including aerospace, automotive, healthcare, and consumer goods, for prototyping, product development, and small-scale manufacturing.
Overall, 3D printing is a transformative manufacturing technology that allows for the efficient and precise creation of objects by building them layer by layer using digital designs and additive processes.
What are the advantages of using a 3D printing service?
Using a 3D printing service offers several advantages for individuals and businesses. Here is a professional explanation of the benefits:
- Design Freedom: 3D printing allows for intricate and complex designs that are difficult or impossible to achieve with traditional manufacturing methods. It offers greater design freedom and flexibility, enabling the production of geometrically complex and customized objects.
- Rapid Prototyping: 3D printing enables the quick and cost-effective production of prototypes. It allows designers and engineers to iterate designs rapidly, test functionality, and identify improvements before committing to expensive tooling and production processes.
- Customization and Personalization: With 3D printing, it is possible to create highly customized objects tailored to specific needs or preferences. This level of customization can range from individualized product variations to personalized medical devices or consumer goods.
- Cost-Effective for Small Production Runs: 3D printing eliminates the need for expensive molds, tooling, and setup costs associated with traditional manufacturing. It is particularly cost-effective for small-batch or low-volume production, reducing upfront investment and enabling on-demand manufacturing.
- Reduced Time-to-Market: 3D printing significantly reduces the time required to bring a product from concept to market. The ability to quickly produce prototypes and iterate designs accelerates the product development process, enabling faster market entry and competitive advantage.
- Complexity at No Extra Cost: Unlike traditional manufacturing methods, 3D printing does not incur additional costs for complex designs. The cost remains consistent regardless of the complexity, allowing for intricate and detailed objects without added expenses.
- On-Demand Manufacturing: 3D printing enables on-demand production, allowing businesses to manufacture products as needed. This reduces inventory costs, enables just-in-time manufacturing, and facilitates product customization or personalization for individual customers.
- Reduced Material Waste: Additive manufacturing is an inherently more sustainable process compared to subtractive manufacturing. It only uses the required amount of material, minimizing waste and reducing environmental impact.
- Geographical Flexibility: 3D printing services can be accessed remotely, providing geographical flexibility. Customers can upload their designs online and have them printed by a service provider located anywhere in the world, expanding access to specialized manufacturing capabilities.
- Innovation and Prototyping Accessibility: 3D printing services democratize innovation by making advanced manufacturing technologies accessible to a wider audience. Startups, entrepreneurs, and individuals can leverage 3D printing services to bring their ideas to life without significant upfront investment or extensive manufacturing expertise.
These advantages make 3D printing services a valuable tool for product development, customization, small-scale manufacturing, and driving innovation across various industries.
What types of materials can be used in 3D printing?
3D printing technology offers a wide range of materials that can be used to create objects with varying properties and characteristics. Here is a professional overview of the types of materials commonly used in 3D printing:
- Thermoplastics: The most commonly used material in 3D printing is thermoplastics, which can be melted and solidified repeatedly. Examples include PLA (Polylactic Acid) and ABS (Acrylonitrile Butadiene Styrene), known for their versatility, strength, and ease of use.
- Photopolymers: These are liquid resins that solidify when exposed to specific wavelengths of light, commonly used in Stereolithography (SLA) and Digital Light Processing (DLP) printers. Photopolymers offer high detail and smooth finishes, making them suitable for applications requiring intricate designs or visual aesthetics.
- Metals: Metal 3D printing utilizes metal powders, such as titanium, stainless steel, aluminum, copper, or nickel alloys. The process, known as Direct Metal Laser Sintering (DMLS) or Selective Laser Melting (SLM), selectively melts and fuses the metal powders layer by layer, resulting in strong and durable metal parts.
- Ceramics: Ceramic materials, such as alumina, zirconia, or porcelain, can be used in 3D printing for applications like dental restorations, jewelry, or customized ceramic components. Ceramic 3D printing involves a process called binder jetting or powder bed fusion.
- Composites: Composite materials combine multiple components to achieve specific properties. For instance, carbon fiber-reinforced polymers can be 3D printed, resulting in lightweight, high-strength parts used in aerospace, automotive, and sporting goods industries.
- Elastomers: Flexible and rubber-like materials, known as elastomers or TPE (Thermoplastic Elastomers), are used when flexibility, impact resistance, or cushioning properties are required. These materials are suitable for creating gaskets, seals, and soft-touch applications.
- Bioinks and Biomaterials: 3D bioprinting utilizes specialized bioinks and biomaterials to create living tissues and organs. These materials are often composed of living cells, hydrogels, and other biocompatible substances, enabling advancements in regenerative medicine and tissue engineering.
- Others: There are various other materials used in 3D printing, including gypsum-based powders for full-color 3D printing, wax for investment casting, and food-grade materials for creating edible objects or customized confectionery.
It's important to note that the availability of materials may vary depending on the specific 3D printing technology and the capabilities of the 3D printing service provider. Each material has its own unique properties, such as strength, flexibility, heat resistance, or transparency, allowing for a wide range of applications across industries.
Can I print functional and durable parts with 3D printing?
Yes, 3D printing is capable of producing functional and durable parts, although the specific performance characteristics may vary depending on the printing technology, material used, and design considerations. Here is a professional explanation:
- Material Selection: Choosing the right material is crucial for producing functional and durable parts. There are many options available, including various thermoplastics, metals, and composite materials, each with their own strengths and properties. For example, engineering-grade thermoplastics like ABS or nylon offer good mechanical strength, while metal 3D printing can produce parts with high strength and heat resistance.
- Design Considerations: Design plays a significant role in the functionality and durability of 3D-printed parts. Proper engineering practices, such as optimizing wall thickness, incorporating structural supports, and designing for load distribution, can enhance the strength and performance of the printed parts. Reinforcing features like ribs, fillets, or lattice structures can improve the structural integrity of the parts.
- Post-Processing Techniques: Post-processing techniques can further enhance the functional and durable properties of 3D-printed parts. For example, heat treatment or annealing of metal parts can improve their mechanical properties, while post-curing of photopolymer resin parts can enhance their strength and stability. Surface finishing techniques like sanding, polishing, or coating can improve aesthetics and resistance to wear or corrosion.
- Iterative Design and Testing: 3D printing offers the advantage of rapid prototyping, allowing for iterative design and testing. By producing multiple iterations of a part, testing them, and making design modifications based on the results, it is possible to optimize the functionality and durability of the final printed part.
- Material Testing and Validation: Material manufacturers and 3D printing service providers often provide data on the mechanical properties of their materials. These data can help in selecting the appropriate material for specific applications and ensure that the desired functional and durable requirements are met.
While 3D printing has made significant advancements in producing functional and durable parts, it's worth noting that the properties of 3D-printed parts may differ from those manufactured using traditional methods. Factors such as layer adhesion, anisotropy, and surface finish may impact the overall performance. Therefore, it is important to consider the specific requirements of the application and conduct testing and validation to ensure the suitability of 3D-printed parts for their intended use.
What is the typical turnaround time for a 3D printing project?
The turnaround time for a 3D printing project can vary depending on several factors, including the complexity of the design, the size of the object, the chosen 3D printing technology, the materials used, and the capacity and workload of the 3D printing service provider. Here is a professional explanation of the typical turnaround time:
- Small and Simple Objects: For small and relatively simple objects, such as small prototypes or basic shapes, the turnaround time can be relatively quick. It may range from a few hours to a couple of days. These objects require less printing time and minimal post-processing, resulting in faster completion.
- Medium-Sized and Complex Objects: As the size and complexity of the object increase, the turnaround time generally extends. Objects with intricate designs, moving parts, or higher levels of detail may require longer printing times. Depending on the size and complexity, the turnaround time can range from a few days to a couple of weeks.
- Large-Scale Objects: Printing large-scale objects can significantly impact the turnaround time. Printing larger objects takes more time due to the increased number of layers and printing volume. Additionally, larger objects may require additional considerations, such as print bed size limitations or the need to divide the object into multiple parts for assembly. Turnaround time for large-scale objects can range from several days to several weeks.
- Material Considerations: Different materials have varying printing requirements and characteristics. Some materials may require additional post-processing steps, such as curing, annealing, or support removal, which can extend the overall turnaround time. The availability of specific materials and their associated processing times can also affect the project timeline.
- Service Provider Capacity: The workload and capacity of the 3D printing service provider can influence the turnaround time. Providers with high demand or limited resources may have longer lead times. It is advisable to check with the service provider regarding their current workload and estimated project completion time.
It's important to note that these turnaround times are general guidelines and can vary significantly depending on the specific project and circumstances. For time-sensitive projects, it is recommended to communicate your requirements and deadlines with the 3D printing service provider to determine the feasibility of meeting your timeline.
How accurate and precise are the prints from a 3D printing service?
The accuracy and precision of prints from a 3D printing service can vary depending on several factors, including the chosen 3D printing technology, the capabilities of the printer, the quality of the design file, and the expertise of the service provider. Here is a professional explanation of the accuracy and precision in 3D printing:
- Layer Resolution: The layer resolution refers to the thickness of each layer deposited during the printing process. Smaller layer thickness allows for finer details and smoother surfaces, resulting in higher accuracy and precision. However, it's important to note that achieving very fine layer resolutions may increase printing time and cost.
- Printing Technology: Different 3D printing technologies have varying levels of accuracy and precision. For example, technologies like Stereolithography (SLA) or Digital Light Processing (DLP) offer high-resolution prints with excellent detail and surface finish. On the other hand, Fused Deposition Modeling (FDM) or Selective Laser Sintering (SLS) may have slightly lower accuracy due to the nature of layer-by-layer deposition.
- Printer Calibration and Maintenance: Proper calibration and maintenance of the 3D printer are crucial for achieving accurate and precise prints. Regular calibration ensures that the printer's motion system, extrusion system, and other components are in optimal condition, minimizing errors and deviations.
- Design Considerations: The design file's quality and suitability for 3D printing can affect the accuracy and precision of the prints. Design files should be properly prepared, taking into account factors such as wall thickness, tolerances, support structures, and considerations for the specific 3D printing technology being used. Well-designed files can help achieve better accuracy and minimize issues like warping or distortion.
- Expertise of the Service Provider: The expertise and experience of the 3D printing service provider play a significant role in achieving accurate and precise prints. Providers with a deep understanding of the printing technology, materials, and design considerations are more likely to produce high-quality prints. They can offer guidance on optimizing designs, selecting appropriate materials, and fine-tuning print settings for optimal results.
It's important to note that while 3D printing technology has made significant advancements, achieving absolute accuracy and precision comparable to traditional manufacturing methods may have limitations. Factors such as layer adhesion, thermal expansion, or post-processing steps can introduce slight deviations. Therefore, it's advisable to discuss your specific accuracy requirements with the 3D printing service provider and consider conducting test prints or prototypes to verify the desired level of accuracy and precision before proceeding with full-scale production.
How do I choose the right 3D printing service for my project?
Choosing the right 3D printing service for your project requires careful consideration of several factors. Here are some professional tips to help you make an informed decision:
- Project Requirements: Clearly define your project requirements, including the desired object specifications, material needs, required accuracy, quantity, budget, and timeline. Having a clear understanding of your project goals will help you evaluate whether a particular 3D printing service can meet your needs.
- Technology and Materials: Understand the 3D printing technologies and materials offered by the service providers. Different technologies have varying capabilities and material options. Ensure that the service provider offers the specific technology and materials suitable for your project. Consider factors such as strength, flexibility, heat resistance, and surface finish requirements when evaluating material options.
- Quality and Capabilities: Assess the quality and capabilities of the 3D printing service provider. Look for their expertise in the specific printing technology you require. Check their portfolio, reviews, and testimonials to gauge the quality of their previous work. Inquire about their equipment, maintenance practices, and quality control measures to ensure consistent and reliable results.
- Additional Services: Consider whether the service provider offers additional services that may be relevant to your project. These could include design assistance, prototyping, post-processing (such as sanding, polishing, or painting), and finishing services. Having these additional services available can streamline your project workflow and ensure a more comprehensive solution.
- Pricing and Cost Transparency: Request quotes from multiple service providers and compare their pricing structures. Evaluate the pricing based on factors such as material usage, machine time, post-processing, and any additional services required. Ensure that the service provider is transparent about their pricing and any potential additional costs to avoid surprises later.
- Communication and Support: Evaluate the responsiveness and communication of the service provider. Prompt and clear communication throughout the project is crucial for addressing any queries, concerns, or design iterations. A responsive and supportive service provider can provide guidance, technical expertise, and assistance during the entire process.
- Confidentiality and Intellectual Property: If your project involves sensitive or proprietary information, ensure that the service provider has appropriate confidentiality measures in place. Discuss and sign a non-disclosure agreement (NDA) if necessary to protect your intellectual property rights.
- Location and Logistics: Consider the location of the service provider and the logistics involved in shipping and receiving the printed parts. Local providers may offer faster turnaround times and easier communication, while international providers may offer cost advantages. Evaluate the shipping costs, transit times, and any potential customs or import/export considerations.
- Reviews and Recommendations: Seek recommendations from colleagues, industry professionals, or online communities to gather insights about reputable 3D printing service providers. Read reviews and testimonials to gauge the experiences of past clients.
By carefully considering these factors and evaluating multiple options, you can select a 3D printing service provider that aligns with your project requirements, delivers high-quality results, and provides the necessary support throughout the process.
Are there any limitations to what can be 3D printed?
Yes, there are limitations to what can be 3D printed. While 3D printing technology has advanced significantly, it still has certain constraints and limitations that should be considered. Here are some key limitations:
- Size and Scale: 3D printers have limitations on the maximum size of objects they can print. The build volume of the printer determines the maximum dimensions of the object. Large-scale objects may require specialized or industrial-grade printers, and printing them can be time-consuming and expensive.
- Geometry and Complexity: Certain geometries and complex designs may pose challenges for 3D printing. Overhangs, unsupported structures, or intricate details may require the use of support structures, which may need to be manually removed or may leave marks on the final print. Design files need to be carefully prepared to ensure printability and avoid issues like warping or collapsing during the printing process.
- Material Selection: While there is a wide range of materials available for 3D printing, not all materials can be used for all types of 3D printing technologies. Each printer and technology has specific material compatibility requirements. Some materials may have limitations in terms of strength, temperature resistance, or other mechanical properties. Additionally, specialized materials like certain metals or ceramics may require advanced or specialized equipment.
- Surface Finish and Texture: The surface finish of 3D-printed objects may not be as smooth or refined as those produced by traditional manufacturing methods. Layer lines or surface imperfections may be visible, especially in FDM or SLS prints. Additional post-processing steps such as sanding, polishing, or coating may be required to achieve the desired surface finish.
- Material Properties and Performance: While 3D-printed parts can exhibit strength and durability, they may have different material properties compared to parts manufactured using traditional methods. Anisotropic properties, lower heat resistance, or reduced mechanical strength in specific directions are some factors to consider. Material selection and design optimization are important to ensure the printed parts meet the required performance criteria.
- Cost and Time: 3D printing can be cost-effective for certain applications, but it may not always be the most economical choice for large-scale production or when traditional manufacturing methods are better suited. Printing large or complex objects can be time-consuming, and the cost can increase with factors like size, material usage, and post-processing requirements.
It's important to consider these limitations when evaluating the feasibility of a 3D printing project. Collaboration with experienced professionals and understanding the capabilities and constraints of the chosen 3D printing technology and materials can help overcome these limitations and achieve successful outcomes.
FAQs List of Additive manufacturing Services
What is additive manufacturing?
Additive manufacturing, also known as 3D printing, is a manufacturing process that creates three-dimensional objects by adding material layer by layer. It is a transformative technology that has gained a great deal of attention and adoption in various industries. Here is a professional explanation of additive manufacturing:
Additive manufacturing begins with a digital 3D model of the object to be produced. The model can be created using computer-aided design (CAD) software or obtained through 3D scanning technology. The digital model is then sliced into thin cross-sectional layers that serve as instructions to the 3D printer.
The 3D printer builds the object layer by layer as instructed by the sliced model. Each layer is typically a thin cross-section of the final object, ranging in thickness from a fraction of a millimetre to a few millimetres, depending on the chosen printing technology.
There are various additive manufacturing technologies available, each with its own specific process and materials. Some common 3D printing technologies include:
- Fused Deposition Modeling (FDM) or Fused Filament Fabrication (FFF): This technology melts and extrudes thermoplastic filament through a nozzle, which moves in a controlled manner to deposit the material layer by layer.
- Stereolithography (SLA): SLA uses a liquid photopolymer resin that is hardened by a light source, such as a laser or UV projector. The object is built by selectively curing the resin layer by layer.
- Selective Laser Sintering (SLS): SLS employs a high-powered laser to selectively fuse powder materials, typically polymers or metals, layer by layer, creating solid objects.
- Direct Metal Laser Sintering (DMLS) or Selective Laser Melting (SLM): These technologies use a high-powered laser to selectively fuse metal powder particles, layer by layer, to create metal objects with high precision.
- Digital Light Processing (DLP): Similar to SLA, DLP uses a digital light projector to cure a liquid photopolymer resin into solid layers.
Additive manufacturing offers several advantages over traditional manufacturing methods. It allows for complex geometries, customisation, rapid prototyping and on-demand production. It reduces material waste as it adds material only where it is needed and produces lightweight and optimised structures. In addition, additive manufacturing has been used in several industries, including aerospace, automotive, healthcare, consumer goods, and construction.
While additive manufacturing has made significant progress, it has limitations. These include limitations on object size, material properties, surface finish, and production speed. However, ongoing research and development in the field continues to expand the capabilities of additive manufacturing, making it an increasingly valuable tool in modern manufacturing processes.
What are the benefits of using an additive manufacturing service?
Using an additive manufacturing service offers several benefits for individuals and businesses. Here are the key advantages of utilizing an additive manufacturing service:
- Access to Advanced Technology: Additive manufacturing services typically invest in state-of-the-art 3D printing equipment and technologies. By utilizing their services, you gain access to advanced printing capabilities that may be cost-prohibitive for individual purchase. This allows you to leverage cutting-edge technology without the need for significant upfront investment.
- Expertise and Experience: Additive manufacturing service providers have specialized knowledge and expertise in 3D printing. They understand the intricacies of different printing technologies, materials, and design considerations. By working with such professionals, you can tap into their experience, receive guidance on design optimization, and ensure the best possible outcomes for your project.
- Cost Savings: Engaging an additive manufacturing service can result in cost savings, particularly for small-scale or one-off production. Instead of investing in expensive 3D printers, materials, and maintenance, you can outsource the printing to a service provider, paying only for the specific parts or objects you need. This eliminates the need for capital investment, ongoing equipment maintenance, and material inventory management.
- Scalability and Flexibility: Additive manufacturing services offer scalability and flexibility. Whether you need a single prototype or a batch production run, the service provider can accommodate your requirements. They can quickly adjust their production capacity to meet your needs, allowing for easy scalability as your project evolves.
- Faster Turnaround Times: Additive manufacturing services often have multiple printers and efficient production workflows, enabling faster turnaround times compared to in-house printing. By leveraging their resources and optimized processes, you can shorten the production lead time and accelerate your project timelines.
- Quality Assurance: Reputable additive manufacturing services prioritize quality control and assurance. They employ rigorous inspection processes and quality checks to ensure that the printed parts meet your specifications and requirements. This helps minimize the risk of errors, defects, or inconsistencies in the final products.
- Material Selection and Accessibility: Additive manufacturing services offer a wide range of materials suitable for different applications. They can provide access to a variety of plastics, metals, resins, and other specialized materials, allowing you to select the most suitable option for your project. Additionally, they may have partnerships or sourcing capabilities to procure materials that may be challenging to obtain individually.
- Post-Processing and Finishing: Many additive manufacturing services offer post-processing and finishing services as part of their offerings. This includes sanding, polishing, painting, dyeing, or applying protective coatings to enhance the aesthetics and functionality of the printed parts. By leveraging these additional services, you can achieve a professional, finished look for your products.
- Intellectual Property Protection: When working with a reputable additive manufacturing service, you can establish confidentiality agreements and protect your intellectual property. This is particularly important for sensitive or proprietary designs or projects where confidentiality is critical.
By utilizing an additive manufacturing service, you can leverage their expertise, advanced technology, cost-effectiveness, and streamlined processes to bring your ideas to life more efficiently and effectively. It allows you to focus on design, innovation, and product development while leaving the manufacturing process in the hands of experienced professionals.
What types of technologies are used in additive manufacturing?
Additive manufacturing, commonly known as 3D printing, encompasses a range of technologies that enable the creation of three-dimensional objects by adding material layer by layer. Here are some of the key technologies used in additive manufacturing:
- Fused Deposition Modeling (FDM) or Fused Filament Fabrication (FFF): FDM/FFF is one of the most widely used additive manufacturing technologies. It involves extruding a thermoplastic filament through a heated nozzle, which moves in a controlled manner to deposit the material layer by layer. The material solidifies rapidly after deposition, forming the object.
- Stereolithography (SLA): SLA utilizes a liquid photopolymer resin that is selectively cured using a light source, typically a laser or UV projector. The resin is contained in a vat, and a platform is gradually lowered into the resin, with the light source tracing each layer's cross-section to solidify the resin and build the object.
- Selective Laser Sintering (SLS): SLS employs a high-powered laser to selectively fuse powdered materials, such as plastics or metals, layer by layer. The powdered material is spread on a build platform, and the laser scans the cross-section of the object, melting and fusing the particles together. Unfused powder acts as support during the printing process.
- Digital Light Processing (DLP): DLP technology is similar to SLA but uses a digital light projector instead of a laser to cure a liquid photopolymer resin. The projector projects an entire layer's image onto the resin, solidifying it all at once. The build platform is then incrementally lifted, and the process is repeated for subsequent layers.
- Direct Metal Laser Sintering (DMLS) or Selective Laser Melting (SLM): DMLS/SLM technologies utilize a high-powered laser to selectively fuse metal powder particles, layer by layer, to create fully dense metal objects. The laser melts the metal powder particles, which solidify upon cooling. These technologies are commonly used for metal parts production in industries such as aerospace and medical.
- Electron Beam Melting (EBM): EBM is a similar process to DMLS/SLM but uses an electron beam instead of a laser to selectively melt and fuse metal powder particles. EBM is known for its ability to produce large and complex metal parts, often used in aerospace and orthopedic applications.
- Binder Jetting: Binder Jetting is an additive manufacturing process that involves selectively depositing a liquid binding material onto a powdered bed. The binder binds the particles together, layer by layer, to create the desired object. After printing, the object is typically post-processed to remove excess powder and undergoes additional treatments for strength and durability.
These are just a few examples of the technologies used in additive manufacturing. Other notable technologies include PolyJet, Laminated Object Manufacturing (LOM), and Digital Beam Melting (DBM). Each technology has its own advantages, limitations, and applications, making additive manufacturing a versatile and rapidly evolving field.
Can additive manufacturing be used for large-scale production?
Yes, additive manufacturing can be used for large-scale production, although there are certain factors to consider when applying it to high-volume manufacturing. While additive manufacturing was initially developed for rapid prototyping and low-volume production, advancements in technology and materials have made it increasingly viable for larger-scale production. Here are some points to consider regarding the use of additive manufacturing for large-scale production:
- Cost Considerations: Additive manufacturing can be cost-effective for small production runs or highly customized products. However, when it comes to large-scale production, traditional manufacturing methods such as injection molding or casting may still offer cost advantages. The cost per unit in additive manufacturing can be higher due to factors such as longer production times, material costs, and equipment maintenance.
- Production Time: Additive manufacturing can have longer production times compared to traditional manufacturing methods, especially for complex or larger objects. Printing each layer sequentially can be time-consuming, which may limit the throughput for large-scale production. However, advancements in technology, such as faster printers and improved printing strategies, are reducing these time constraints.
- Scalability and Production Capacity: Additive manufacturing technology is becoming more scalable, allowing for larger production volumes. Industrial-grade 3D printers with larger build volumes and higher throughput are being developed. Multiple printers can be operated simultaneously, increasing the production capacity. These advancements enable additive manufacturing to handle larger-scale production requirements.
- Material Availability and Quality: The range of materials available for additive manufacturing has expanded, including various plastics, metals, ceramics, and composites. However, the availability and suitability of materials for large-scale production may still be a limitation. Material properties, consistency, and quality control become crucial factors when aiming for high-volume production.
- Process Automation: To achieve large-scale production with additive manufacturing, automation becomes essential. Automated systems can handle tasks such as material loading, part removal, post-processing, and quality control. Integrating robotics, conveyor systems, and computerized workflows can improve efficiency and reduce labor-intensive processes.
- Design Optimization for Additive Manufacturing: Large-scale production using additive manufacturing often requires design optimization to maximize efficiency and reduce costs. Design for Additive Manufacturing (DfAM) principles focus on utilizing the advantages of additive manufacturing, such as lightweight structures, consolidated assemblies, and reduced material usage. Optimized designs can improve production speed, reduce material waste, and enhance the performance of the printed parts.
- Supply Chain Considerations: Adopting additive manufacturing for large-scale production may require reevaluating the supply chain. Traditional manufacturing methods often rely on established supply chains for raw materials, tooling, and post-processing. Additive manufacturing may require alternative suppliers, specialized materials, and different logistical considerations.
Although additive manufacturing is increasingly being adopted for large-scale production, it is important to assess the specific requirements of each project. Factors such as cost, production time, scalability, material availability, and supply chain considerations should be carefully evaluated to determine the feasibility and viability of using additive manufacturing for large-scale production.
What materials can be used in additive manufacturing?
Additive manufacturing, or 3D printing, offers a wide range of materials for use in the manufacturing process. The materials used in additive manufacturing can vary depending on the specific technology, application, and desired properties of the printed object. Here are some commonly used materials in additive manufacturing:
- Polymers and Plastics: Various polymers and plastics are widely used in additive manufacturing. These include thermoplastics such as ABS (Acrylonitrile Butadiene Styrene), PLA (Polylactic Acid), PETG (Polyethylene Terephthalate Glycol), Nylon, TPU (Thermoplastic Polyurethane), and PEEK (Polyether Ether Ketone). Each material has different characteristics, such as strength, flexibility, temperature resistance, and chemical resistance, making them suitable for different applications.
- Metals: Additive manufacturing has made significant advancements in the production of metal parts. Common metals used in additive manufacturing include stainless steel, titanium, aluminum, nickel alloys, cobalt-chrome alloys, and copper. Metal additive manufacturing technologies like Selective Laser Melting (SLM), Electron Beam Melting (EBM), and Directed Energy Deposition (DED) enable the production of complex metal components with excellent mechanical properties.
- Ceramics: Ceramic materials are used in additive manufacturing for applications where high-temperature resistance, electrical insulation, or biocompatibility is required. Ceramic additive manufacturing methods, such as ceramic stereolithography and binder jetting, enable the production of ceramic objects with intricate geometries. Examples of ceramic materials used in additive manufacturing include alumina, zirconia, and hydroxyapatite.
- Composites: Composites combine different materials to achieve specific properties. In additive manufacturing, composite materials are used to enhance strength, stiffness, or other performance characteristics. Fiber-reinforced composites, such as carbon fiber or glass fiber reinforced polymers, can be 3D printed to create lightweight and strong parts.
- Biomaterials: Additive manufacturing has found applications in the medical and dental fields, where biocompatible materials are necessary. Biomaterials used in additive manufacturing include bioresorbable polymers like polylactic acid (PLA) and poly(lactic-co-glycolic acid) (PLGA), as well as hydrogels and bioink for creating tissue scaffolds or 3D bioprinting.
- Other Materials: Additive manufacturing also allows for the use of materials like wax, sand, silicone, and even food-grade materials. Wax is commonly used for investment casting patterns, sand is used for sand casting molds, and silicone is used for creating molds or prototypes. Food-grade materials are used in the 3D printing of edible objects, such as chocolates or confectionery.
It's important to note that the range of materials available for additive manufacturing continues to expand as research and development efforts progress. New materials and material combinations are constantly being explored to meet specific application requirements. Each material has its own unique properties, and the selection depends on factors such as mechanical properties, temperature resistance, chemical compatibility, biocompatibility, and cost-effectiveness for the intended application.
How does the cost of additive manufacturing compare to traditional manufacturing?
The cost of additive manufacturing, also known as 3D printing, compared to traditional manufacturing methods can vary depending on several factors. While additive manufacturing offers unique advantages, it may not always be the most cost-effective option for every application. Here's a breakdown of the cost considerations when comparing additive manufacturing to traditional manufacturing:
- Initial Investment: The initial investment for additive manufacturing can be higher than traditional manufacturing methods. The cost of acquiring 3D printers, software, and necessary equipment can be significant, especially for industrial-grade systems. In contrast, traditional manufacturing methods may require less capital investment, especially for processes like casting or machining that utilize existing equipment.
- Production Volume: Additive manufacturing is generally more cost-effective for low-volume or customized production, where the flexibility and design freedom provided by 3D printing outweigh the higher per-unit costs. However, as the production volume increases, traditional manufacturing methods like injection molding or casting can offer economies of scale, reducing the cost per unit.
- Material Costs: Material costs can vary between additive manufacturing and traditional manufacturing methods. Additive manufacturing often requires specialized materials in the form of filaments, powders, or resins, which can be more expensive compared to raw materials used in traditional manufacturing. However, additive manufacturing's ability to minimize material waste and optimize designs can offset some of these costs.
- Labor Costs: The labor costs associated with additive manufacturing are typically lower compared to traditional manufacturing methods. Additive manufacturing processes can be automated, requiring less manual labor for operation and supervision. Traditional manufacturing methods, on the other hand, may involve more labor-intensive processes, such as machining or assembly, which can increase labor costs.
- Design Complexity: Additive manufacturing can offer cost advantages when it comes to complex designs. Traditional manufacturing methods may require additional production steps, tooling, or fixtures to achieve intricate geometries, resulting in higher costs. Additive manufacturing's layer-by-layer approach allows for the creation of complex designs without the need for additional tooling, reducing costs in certain cases.
- Post-Processing and Finishing: Additive manufacturing often requires post-processing and finishing steps to achieve the desired surface finish or functional properties. These additional steps can add to the overall cost and time required for additive manufacturing. In traditional manufacturing, processes like machining or polishing may already be integrated into the main production process, potentially reducing the need for additional post-processing.
- Time-to-Market: Additive manufacturing can significantly reduce the time-to-market for certain products, enabling rapid prototyping and iterative design improvements. This advantage can offset higher per-unit costs in scenarios where speed and flexibility are critical. Traditional manufacturing methods may have longer lead times due to tooling and setup processes, which can impact time-to-market and overall costs.
It's important to evaluate the specific requirements of each production scenario to determine the cost-effectiveness of additive manufacturing compared to traditional manufacturing methods. Factors such as production volume, material costs, labor costs, design complexity, post-processing requirements, and time-to-market considerations should be taken into account to make an informed decision. Additive manufacturing is often favored for its design flexibility, customization capabilities, and rapid prototyping benefits, but cost considerations need to be carefully assessed based on the specific use case.
What factors should I consider when choosing an additive manufacturing service provider?
When selecting an additive manufacturing service provider, several factors should be considered to ensure a successful partnership and desired outcome. The following are key factors to consider when selecting an additive manufacturing service provider:
Expertise and experience: Assess the service provider's expertise and experience in additive manufacturing. Consider their track record, industry reputation, and the range of industries they serve. Look for a provider that has a clear understanding of your specific application or industry, as this expertise can have a significant impact on the quality and suitability of manufactured parts.
Technology and capabilities: Assess the range of additive manufacturing technologies and capabilities offered by the service provider. Different technologies, such as FDM, SLA, SLS or metal 3D printing, have different strengths and limitations. Ensure the provider has the right equipment, materials and expertise to meet your project requirements in terms of part size, material selection, accuracy and surface finish.
Material selection: Consider the range of materials offered by the service provider. Verify that they have the right materials for your specific application, including polymers, metals, ceramics or composites. It is important to ensure that the provider has the expertise to handle the materials you need and provide guidance on material selection when needed.
Quality control: Evaluate the service provider's quality control processes and certifications. Ask about their inspection and testing procedures, their adherence to industry standards (e.g., ISO certification) and their commitment to quality assurance. Reliable providers should have strong quality control measures in place to ensure consistent and high-quality parts are produced.
Design and engineering support: Consider the level of design and engineering support offered by the service provider. Determine if they offer design optimisation services, design for additive manufacturing (DFAM) expertise, and assistance in optimising your design in terms of cost, functionality or performance. A capable provider should be able to provide guidance throughout the design process to maximise the benefits of additive manufacturing.
Scalability and Capacity: Evaluate the service provider's scalability and capacity. If you have varying production volumes or anticipate expanding in the future, make sure the provider can meet your requirements. Consider factors such as lead times, production flexibility, and the ability to handle larger production runs if necessary.
Reprocessing and finishing: Evaluate the service provider's reprocessing capabilities. Determine whether they offer services such as surface treatment, painting, dyeing, or other secondary processes that may be required to achieve the desired end product. In addition, ask about any additional costs or lead times associated with post-treatment and finishing services.
Cost and Pricing Structure: Compare the pricing structures of different service providers. Ask for a detailed quote that includes material costs, machine time, reprocessing and any other associated costs. Consider the overall value offered by the provider, taking into account factors such as quality, expertise and customer service in addition to cost.
Customer support and communication: Evaluate the service provider's level of customer support and communication. A responsive and collaborative provider that communicates effectively with you and keeps you updated on the progress of your project can significantly enhance the overall experience and ensure that your requirements are met.
Testimonials and reviews: seek out testimonials and reviews from clients or industry peers who have worked with the service provider before. Feedback from others can provide valuable insight into their reliability, professionalism and quality of output.
By considering these factors and conducting thorough research, you can make an informed decision when choosing an additive manufacturing service provider that meets your specific needs and supports the success of your project.
How does additive manufacturing differ from traditional manufacturing methods?
Additive manufacturing, also known as 3D printing, differs from traditional manufacturing methods in several key aspects. Here is a professional explanation of the differences between additive manufacturing and traditional manufacturing:
- Process: Additive manufacturing builds objects layer by layer, adding material to create the final product. Traditional manufacturing, on the other hand, typically involves subtractive processes, such as cutting, machining, or drilling, where material is removed from a solid block to obtain the desired shape.
- Design Freedom: Additive manufacturing offers greater design freedom and flexibility compared to traditional manufacturing methods. With additive manufacturing, complex geometries, intricate details, and internal cavities can be easily produced, allowing for innovation and customization. Traditional manufacturing methods often have limitations in achieving such complex designs.
- Prototyping and Rapid Iteration: Additive manufacturing excels in rapid prototyping and iterative design processes. It enables quick and cost-effective production of prototypes, allowing for design validation, testing, and refinement before committing to mass production. Traditional manufacturing methods may involve longer lead times and higher costs for prototyping iterations.
- Material Usage and Waste: Additive manufacturing is more material-efficient compared to traditional manufacturing. It adds material only where needed, reducing waste and optimizing material usage. In contrast, traditional manufacturing often involves substantial material waste due to subtractive processes that remove excess material.
- Tooling and Setup: Traditional manufacturing methods often require the creation of molds, dies, or specialized tooling to shape or form the final product. This tooling process can be time-consuming and expensive, especially for small production runs. Additive manufacturing eliminates the need for many custom tools, as the digital design can be directly translated into the printed object, reducing setup costs and time.
- Scalability and Production Volume: Traditional manufacturing methods are typically more suitable for large-scale production runs due to their efficiency and economies of scale. Additive manufacturing is often more advantageous for smaller production quantities or personalized/customized production where each item can be unique. However, with advancements in additive manufacturing, the scalability and production volume are improving, enabling larger production runs.
- Material Options: Traditional manufacturing methods offer a wide range of materials, including metals, plastics, ceramics, and composites. Additive manufacturing also provides a variety of material options, but the range may be more limited depending on the specific technology. However, ongoing research and development in additive manufacturing are expanding the range of printable materials.
- Surface Finish and Post-processing: Traditional manufacturing methods often produce smoother and more refined surface finishes compared to additive manufacturing. Post-processing steps such as sanding, polishing, or coating are commonly required to achieve desired aesthetics and surface quality in additive manufacturing. Traditional methods may have more inherent control over surface finish during the manufacturing process.
It's worth noting that both additive manufacturing and traditional manufacturing have their strengths and limitations. Depending on the specific requirements of a project, a combination of both methods may be used, leveraging the advantages of each to achieve the desired outcome.
Can complex geometries and intricate designs be achieved with additive manufacturing?
Yes, additive manufacturing excels at producing complex geometries and intricate designs that may be challenging or even impossible to achieve with traditional manufacturing methods. One of the key advantages of additive manufacturing, also known as 3D printing, is its ability to create highly intricate and complex shapes layer by layer. Here's why additive manufacturing is well-suited for complex geometries and intricate designs:
- Layer-by-Layer Fabrication: Additive manufacturing builds objects by adding material layer by layer, allowing for precise control over the geometry of each layer. This layer-by-layer approach enables the creation of intricate internal structures, overhangs, undercuts, and complex surface features that would be difficult to achieve using traditional subtractive manufacturing methods.
- Design Freedom: Additive manufacturing offers design freedom that is not constrained by traditional manufacturing limitations. Designers can create complex geometries with organic shapes, intricate lattice structures, and internal channels that optimize performance and functionality. This freedom allows for innovative designs that push the boundaries of traditional manufacturing constraints.
- Support Structures: Additive manufacturing allows for the creation of temporary support structures that provide stability during the printing process. These support structures can be automatically generated and easily removed once the printing is complete. They enable the fabrication of complex overhangs, undercuts, and intricate structures without the need for additional assembly or complex tooling.
- Multi-material Printing: Some additive manufacturing technologies support multi-material printing, allowing for the simultaneous use of different materials within a single print. This capability enables the creation of complex assemblies, hybrid structures, or objects with varying material properties in different regions. It opens up possibilities for functional integration and customized designs.
- Design Optimization: Additive manufacturing encourages the use of design optimization techniques to maximize performance and efficiency. Topology optimization, generative design, and lattice structures are often employed to create lightweight yet structurally sound components. These techniques leverage the inherent advantages of additive manufacturing to reduce material usage, improve strength-to-weight ratios, and enhance overall performance.
- Iterative Prototyping: Additive manufacturing facilitates rapid iteration and prototyping. Design revisions can be implemented quickly and cost-effectively, allowing designers to experiment with different geometries, features, and sizes. Iterative prototyping, coupled with the ability to create complex designs, accelerates the product development process and facilitates innovation.
- Customization and Personalization: Additive manufacturing enables customization and personalization at scale. Complex geometries can be easily tailored to specific requirements, allowing for individualized products or mass customization. This capability is particularly valuable in industries such as healthcare, consumer products, and aerospace, where personalized or bespoke designs are desired.
Overall, additive manufacturing offers significant advantages when it comes to achieving complex geometries and intricate designs. Its layer-by-layer fabrication process, design freedom, support structures, multi-material capabilities, design optimization techniques, and rapid prototyping capabilities make it a powerful tool for creating objects with highly intricate and complex features.