Injection Molding Plastic Parts Product
China Precision reputation witness
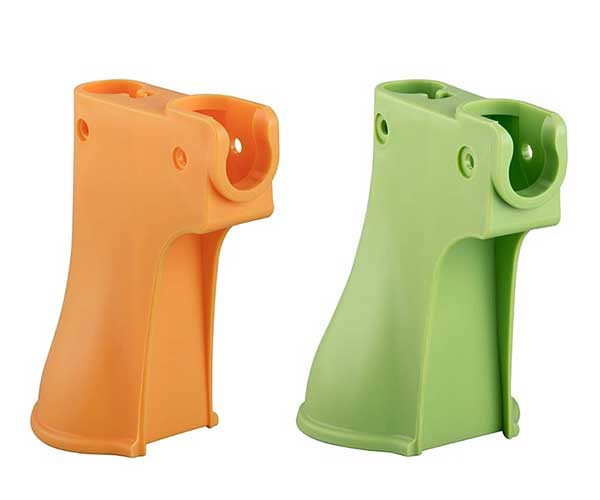
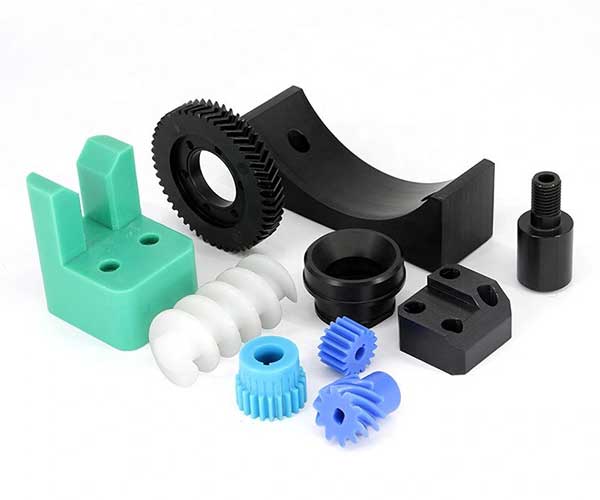
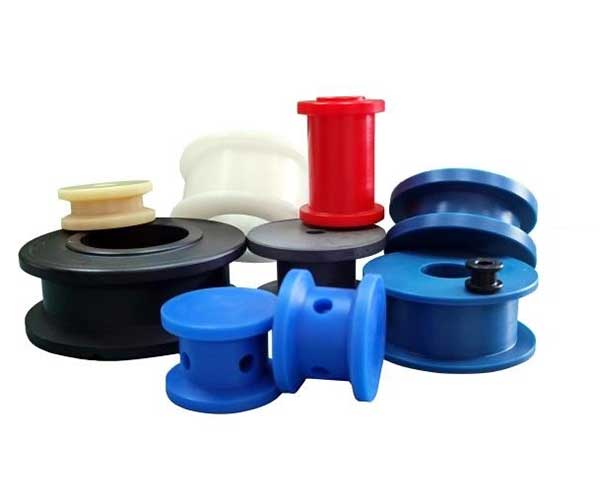
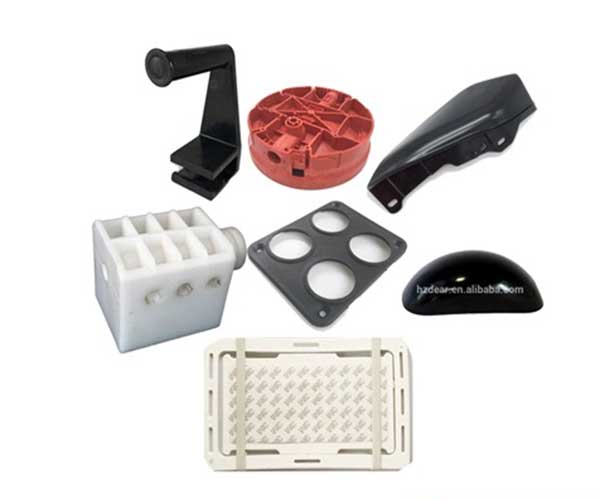
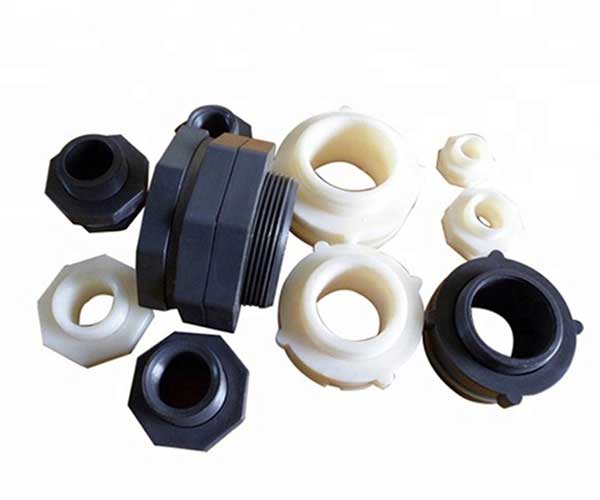
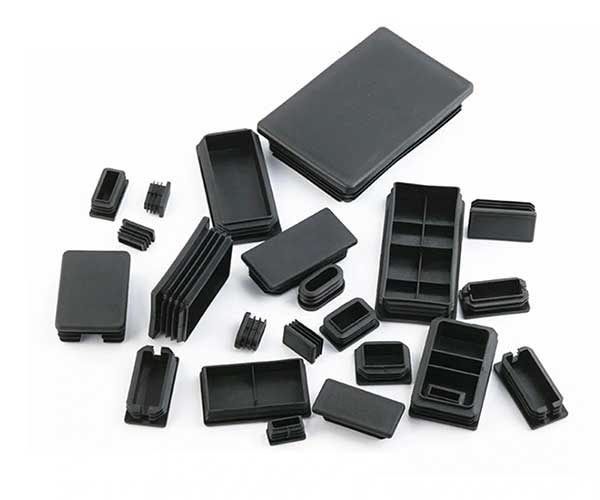
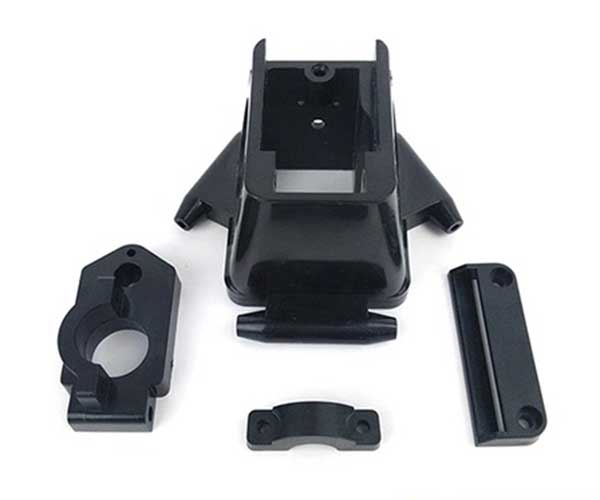
Injection Molding Processing problems
Do you have the following problems when customizing plastic products?
Mold selection
Unable to grasp product features
Mass processing
Unstable injection quality
Finished product spraying
The appearance does not meet the requirements
Slow supply
Failure to supply on time and in quantity
Injection Molding Optimization measures
Not only injection molding, but also optimization measures
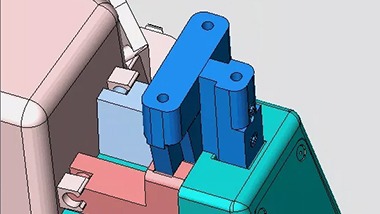
Pretreatment of materials
According to the different water absorption of different materials, some materials need to be dried before processing to remove the moisture in the materials, so as to reduce the proportion of defective products in the injection molding process
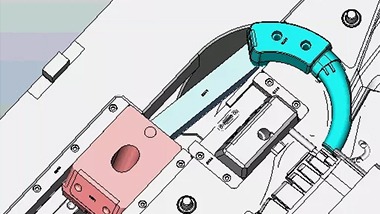
Injection molding equipment status maintenance
Injection molding machine is a high-precision equipment, in which the tacit understanding of the division of labor and cooperation of various systems is very high. Maintaining a good working state can not only operate more efficiently, but also reduce the bad probability in the production process
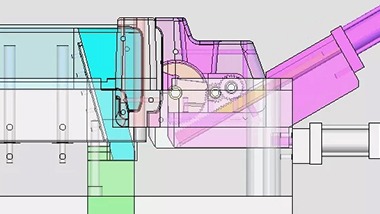
Mold maintenance
Efficient molds are important, but it is also very important to maintain the consistent and efficient operation of molds. Keeping molds in good condition mainly includes: keeping molds clean, avoiding wear and tear, timely replacing worn parts, maintaining lubrication, controlling the influence of temperature difference, timely adjusting the state and so on
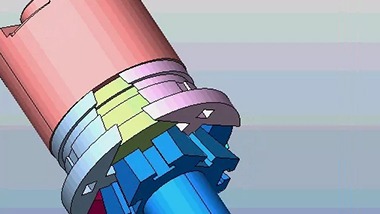
Die design optimization
During the development process, the mold needs to be developed according to the basic properties of the applied raw materials. Designing the flow direction, uniform pressure and gas emission of the melt in the mold cavity is the key component to reduce the difficulty of injection molding and improve the production efficiency. Efficient molding mold is very important
Design, Mold making, production and assembly
What exactly can we do
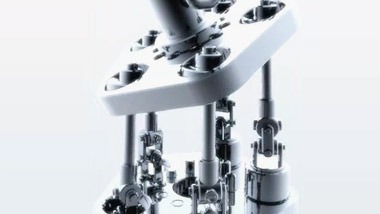
mould design
>Provide samples, drawings and requirements, and provide drawing optimization and design support and efficiency
>Good at optimizing injection mold structure and providing high-efficiency mold development services
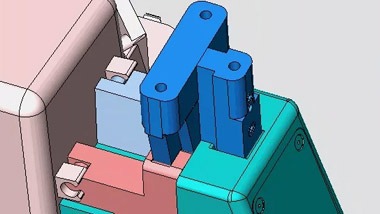
Mold making
>According to the requirements of product structure and product performance, reasonably design the mold structure and cooperate with 3D software for mold flow analysis
>Use 3D laser plate printing to make your samples meet the requirements at one time
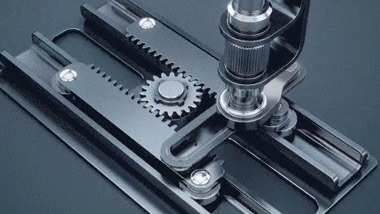
Product production
>With a complete production management team and equipment, it can deliver on time and quickly as soon as one week
>Batch production after sample determination

Product assembly
>Incoming inspection - material preparation - assembly Online - assembly - finished product inspection - shipment
Product production
>Batch production after sample determination
>With a complete production management team and equipment, it can deliver on time and quickly as soon as one week
Injection Molding Equipment display
Accelerate new product development and ensure continuous and stable injection molding production
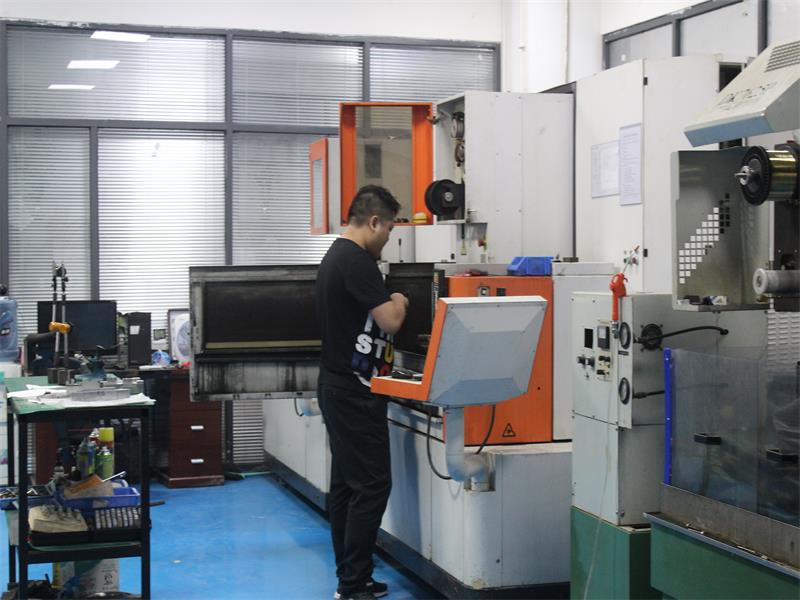
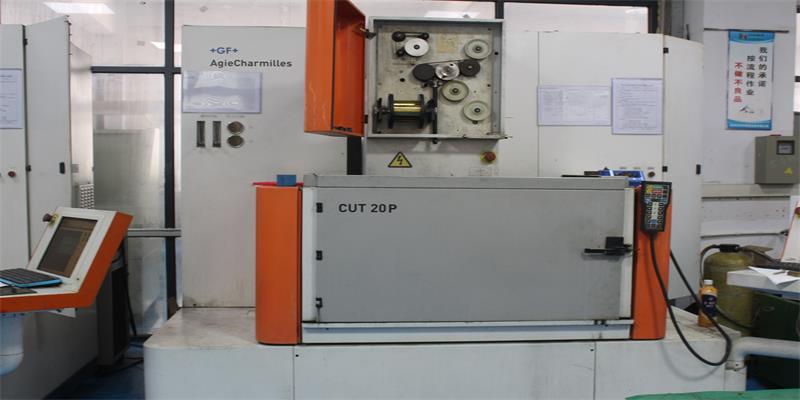
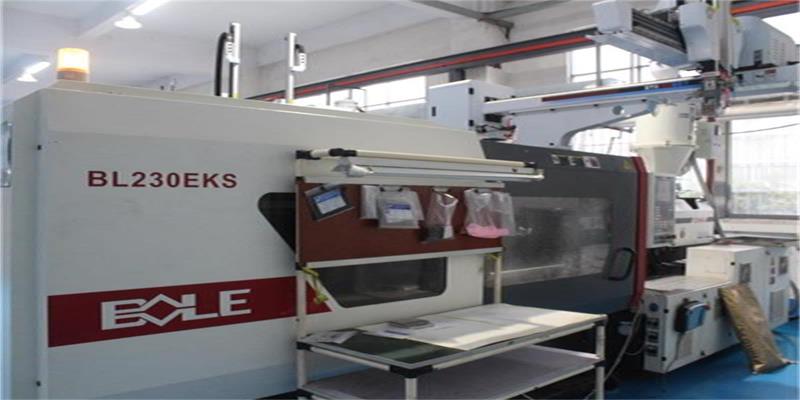
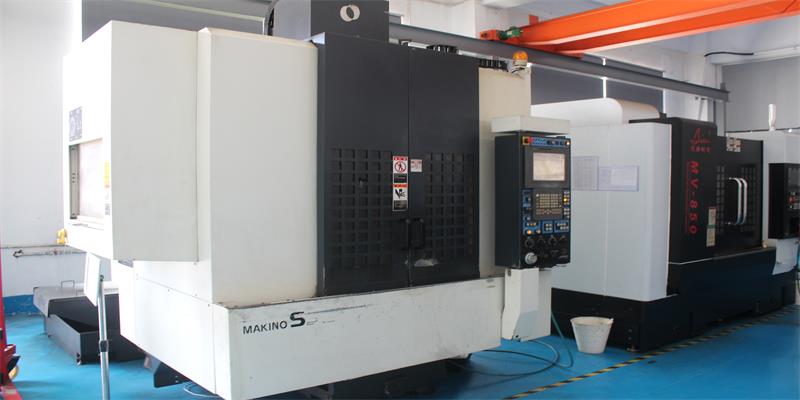
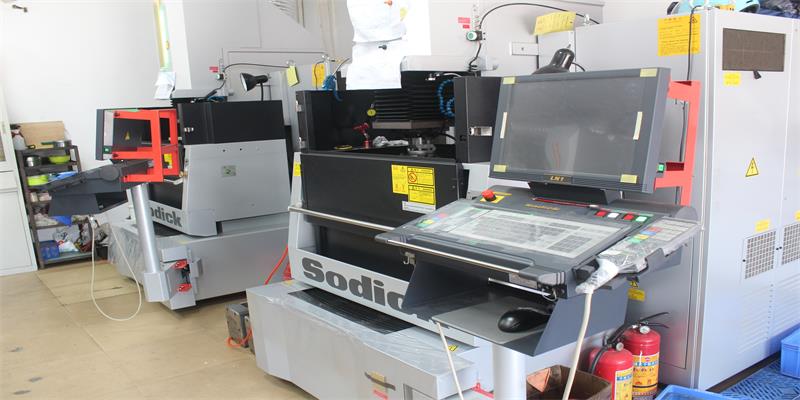
FAQs List of Plastic Injection Molding Services
What is Injection Molding?
Injection molding is a manufacturing process that involves injecting molten plastic into a mold cavity to create a wide range of products with different shapes and sizes.
Injection molding is a manufacturing process used to produce plastic parts and products in large quantities. It is one of the most widely used techniques for mass-producing plastic components due to its efficiency, precision, and repeatability.
The basic principle of injection molding involves injecting molten plastic material into a mold cavity, which is a hollow, usually two-part, metal tool. The mold is designed to have the desired shape of the final product. The molten plastic is forced under high pressure into the mold cavity through a specialized nozzle and runner system.
The key steps in the injection molding process are as follows:
1. Clamping: The two halves of the mold (the "A" side and "B" side) are closed and held together under pressure by a clamping unit. This ensures the mold remains closed during the injection process.
2. Injection: Molten plastic material, typically in the form of small pellets or granules, is fed into a heated barrel where it is melted. Once it reaches the appropriate temperature and consistency, it is injected into the mold cavity at high pressure through the nozzle.
3. Cooling: After the molten plastic fills the mold cavity, it is allowed to cool and solidify within the mold to take the desired shape.
4. Ejection: Once the plastic has cooled sufficiently, the mold opens, and the finished part is ejected from the mold cavity using ejector pins or other mechanisms.
The cycle then repeats for the production of the next part, making injection molding a highly efficient process for large-scale manufacturing.
Injection molding offers numerous advantages, including:
- High production rates: It allows for rapid production of large quantities of parts in a short time.
- Design flexibility: Complex shapes and intricate features can be easily achieved with injection molding.
- Material variety: A wide range of plastic materials can be used in the process, allowing for different properties and characteristics in the final product.
- Minimal post-processing: The parts often require little to no additional finishing or assembly after molding.
Injection molding is commonly used in various industries, including automotive, electronics, consumer goods, medical devices, and more, where high-volume production of plastic components is needed.
What materials can be used for Injection Molding?
A variety of materials can be used for Injection Molding, including thermoplastics, thermosetting polymers, elastomers, and metals.
Injection molding can utilize a wide range of materials, each with its specific properties and characteristics. The choice of material depends on the requirements of the final product, such as strength, flexibility, transparency, chemical resistance, and temperature tolerance. Some of the common materials used for injection molding include:
1. **Polyethylene (PE)**: It is a versatile and widely used thermoplastic with excellent chemical resistance, low cost, and good impact strength. PE is commonly used for containers, toys, and various consumer products.
2. **Polypropylene (PP)**: PP is another versatile thermoplastic with high chemical resistance, toughness, and fatigue resistance. It is commonly used in automotive parts, packaging, and household products.
3. **Polyvinyl Chloride (PVC)**: PVC is known for its excellent chemical resistance and durability. It is used for pipes, fittings, cable insulation, and vinyl records.
4. **Polystyrene (PS)**: PS is a lightweight and rigid material used for packaging, disposable cutlery, CD cases, and various consumer products.
5. **Acrylonitrile Butadiene Styrene (ABS)**: ABS is a tough and impact-resistant thermoplastic often used in automotive parts, electronic housings, and consumer goods.
6. **Polycarbonate (PC)**: PC offers high transparency, impact resistance, and temperature resistance, making it suitable for eyewear, medical devices, and electronic components.
7. **Polyethylene Terephthalate (PET)**: PET is commonly used for beverage bottles, food containers, and other packaging applications.
8. **Nylon (Polyamide)**: Nylon offers high strength, toughness, and abrasion resistance. It is commonly used in engineering applications like gears, bearings, and connectors.
9. **Polyurethane (PU)**: PU can be rigid or flexible, depending on the formulation. It is used for foam cushioning, seals, and various automotive and industrial applications.
10. **Polyethylene Vinyl Acetate (EVA)**: EVA is a flexible and lightweight material often used in footwear, sports equipment, and foam padding.
11. **Polyoxymethylene (POM)**: POM, also known as acetal, offers excellent stiffness, low friction, and high dimensional stability, making it suitable for gears, bushings, and other precision parts.
12. **Polyethylene Chlorotrifluoroethylene (ECTFE)**: ECTFE has excellent chemical resistance and is used in applications requiring high chemical and temperature resistance.
13. **Polyphenylene Sulfide (PPS)**: PPS is a high-performance thermoplastic with excellent chemical resistance and thermal stability, used in electronics, automotive, and aerospace applications.
These are just some of the many materials that can be used for injection molding. Manufacturers often work with material suppliers to select the most appropriate material for a specific application based on the required properties and performance of the final product.
What are the benefits of Injection Molding?
Injection molding offers many benefits, including high production output, precise control over product dimensions and shape, low labor costs, and the ability to produce complex geometries.
Injection molding offers several significant benefits, making it a popular and widely used manufacturing process in various industries. Some of the key advantages of injection molding include:
1. **High Efficiency and Productivity**: Injection molding is a highly efficient process that allows for rapid production of large quantities of parts in a short amount of time. Once the mold is set up, the cycle time for each part is relatively quick, enabling high-volume production.
2. **Design Flexibility**: The process allows for the production of complex shapes and intricate details that may be challenging or even impossible to achieve with other manufacturing methods. This flexibility in design helps meet specific product requirements and can reduce the need for additional assembly steps.
3. **Consistent and Repeatable Results**: Injection molding offers precise control over the molding process, resulting in consistent and repeatable part quality. This is crucial for maintaining uniformity in mass production and meeting tight tolerances.
4. **Material Variety**: A wide range of thermoplastic and thermoset materials can be used for injection molding. Each material has its unique properties, allowing manufacturers to choose the most suitable material for the desired application.
5. **Minimal Material Waste**: Injection molding typically generates minimal material waste compared to other manufacturing processes, as excess material can often be recycled and reused.
6. **Cost-Effective for High-Volume Production**: While the initial tooling and setup costs can be relatively high, the cost per part decreases significantly with higher production volumes. This cost-effectiveness is especially advantageous when producing large quantities of identical parts.
7. **Automation and Labor Savings**: Once the production process is set up, injection molding can be highly automated, reducing the need for extensive manual labor and lowering production costs.
8. **Surface Finish and Texture Options**: Injection molding allows for various surface finishes and textures to be applied to the molded parts, eliminating the need for additional post-processing steps in some cases.
9. **Strength and Durability**: The resulting injection-molded parts often exhibit excellent strength, durability, and resistance to wear, making them suitable for a wide range of applications.
10. **Reduced Assembly Requirements**: Complex parts can often be molded as a single piece, eliminating the need for assembly or reducing the number of components required in the final product.
11. **Quick Prototyping**: Injection molding can also be used for rapid prototyping and iterative product development, helping to validate designs and test functionalities before full-scale production.
Overall, injection molding's benefits make it an attractive choice for high-volume production of plastic parts across various industries, including automotive, consumer goods, electronics, medical devices, and more.
How long does the Injection Molding process take?
The length of the Injection Molding process can vary depending on the complexity and size of the part being produced, but it usually takes seconds to minutes to complete a cycle.
The duration of the injection molding process can vary depending on several factors, including the complexity of the part, the material being used, the size of the mold, the machine's capabilities, and the production volume. Generally, the process can be divided into two main phases: the injection phase and the cooling phase.
1. **Injection Phase**: This phase involves injecting the molten plastic material into the mold cavity. The injection time is influenced by factors like the volume of material to be injected, the injection pressure, and the machine's injection rate. It typically ranges from a few seconds to a minute.
2. **Cooling Phase**: After the molten plastic fills the mold cavity, it needs time to cool and solidify into the desired shape. The cooling time depends on the material's thermal properties, the part's thickness, and the design of the mold. Cooling times can vary significantly, ranging from a few seconds to several minutes.
Overall, the total cycle time for injection molding consists of the injection time and the cooling time. The cycle time is the time it takes to produce one complete part, including both phases. It is an essential factor in determining the production rate and the number of parts that can be manufactured per hour or per day.
For simple and small parts with short cooling times, the entire cycle time could be under a minute. On the other hand, for more complex and larger parts, the cycle time may be several minutes. In high-volume production scenarios, optimizing the cycle time is crucial to achieving efficient production rates.
It's important to note that the cycle time can be affected by process adjustments, such as mold temperature, melt temperature, and cooling system efficiency. Injection molding operators and engineers continually work to optimize these parameters to minimize cycle times while ensuring high-quality parts.
How can I ensure that my Injection Molding project is successful?
To ensure a successful Injection Molding project, it is important to work with a reputable manufacturer with experience in the field. It is also important to provide clear specifications for the part being produced and to consider factors such as material selection, mold design, and production volume.
Ensuring the success of an injection molding project involves careful planning, attention to detail, and collaboration with experienced professionals. Here are some essential steps and considerations to help you achieve a successful injection molding project:
1. **Clear Project Definition**: Start by defining your project goals, objectives, and requirements. Understand the purpose of the molded part, its intended use, performance criteria, and any specific regulatory or industry standards that apply.
2. **Material Selection**: Choose the right material for your application. Work with material suppliers and experienced engineers to select a material that meets your performance, mechanical, chemical, and environmental requirements.
3. **Design for Manufacturability (DFM)**: Design your part with injection molding in mind. Consider wall thickness, draft angles, undercuts, and other design features that can impact moldability. An experienced injection mold designer or engineer can help with DFM guidelines.
4. **Prototype and Testing**: Before committing to full-scale production, create prototypes for testing and validation. This will help identify any design flaws or issues early on and allow you to make necessary improvements.
5. **Selecting the Right Injection Molding Partner**: Choose a reputable and experienced injection molding company or service provider. Look for a partner with a proven track record in producing parts similar to your requirements and one that uses modern equipment and processes.
6. **Mold Design and Tooling**: Collaborate with the mold designer and manufacturer to ensure that the mold design meets your specifications and quality standards. Proper tooling is critical for achieving consistent and high-quality parts.
7. **Process Optimization**: Work closely with the injection molding team to optimize the molding process parameters, such as temperature, pressure, cooling time, and cycle time. Fine-tuning the process can lead to better part quality and reduced production costs.
8. **Quality Control and Inspection**: Implement robust quality control measures to inspect parts during and after production. Ensure that the molded parts meet your dimensional and functional requirements.
9. **Continuous Improvement**: Be open to feedback and learning from each production run. Use the insights gained to continuously improve the design, process, and overall efficiency of the project.
10. **Consider Cost and Timeline**: Have a clear understanding of the project budget and timeline. Be prepared for potential delays or adjustments that may arise during the process.
11. **Communication and Collaboration**: Foster effective communication and collaboration between all stakeholders involved in the project, including designers, engineers, manufacturers, and suppliers.
12. **Regulatory Compliance**: If your project involves parts for specific industries (e.g., medical, aerospace), ensure compliance with relevant regulatory standards and requirements.
By following these steps and working with experienced professionals, you can increase the likelihood of a successful injection molding project that meets your quality, performance, and timeline objectives.
What are some common defects that can occur during Injection Molding?
Some common defects that can occur during Injection Molding include sink marks, warpage, flash, and voids.
During the injection molding process, various defects can occur in the molded parts due to several factors, including material properties, mold design, processing parameters, and machine conditions. Identifying and addressing these defects is essential to ensure the production of high-quality parts. Some common defects in injection molding include:
1. **Short Shot**: A short shot occurs when the molten plastic does not completely fill the mold cavity. It results in an incomplete or undersized part.
2. **Flash**: Flash is excess material that extends beyond the intended part geometry. It occurs when molten plastic escapes between the mold halves during the injection process.
3. **Sink Marks**: Sink marks are depressions or dimples on the surface of the part caused by differential cooling rates within the material. They often appear in thick sections of the part.
4. **Warping**: Warping refers to the deformation or distortion of the part after it has cooled and been ejected from the mold. It occurs due to non-uniform cooling and residual stresses within the material.
5. **Burn Marks**: Burn marks are discolored or blackened areas on the part's surface caused by overheating of the material due to high temperatures or extended residence time.
6. **Jetting**: Jetting happens when the molten plastic shoots out too quickly into the mold, resulting in poor surface finish and reduced part strength.
7. **Splay**: Splay is the appearance of streaks or lines on the surface of the part caused by moisture or other contaminants in the material.
8. **Voids and Air Traps**: Voids are empty spaces or bubbles within the part caused by trapped air. Air traps occur when air is unable to escape from the mold during the injection process.
9. **Knit Lines**: Knit lines are lines or marks on the surface of the part where two or more flow fronts meet during the injection process. They can weaken the part in some cases.
10. **Molding Flash**: Similar to flash, molding flash occurs when excess material escapes through small gaps between the mold components.
11. **Mold Sticking**: Mold sticking occurs when the part adheres to the mold surface and does not eject properly. This defect can damage the part or lead to production delays.
12. **Flow Lines**: Flow lines are visible lines or patterns on the surface of the part caused by the flow of the molten plastic during injection.
Addressing these defects often requires adjustments in processing parameters, mold design modifications, or material changes. Regular inspection and monitoring during the injection molding process can help identify defects early on, allowing for timely corrective actions. Experienced injection molding operators and engineers play a crucial role in minimizing and resolving these defects to produce high-quality parts.
What is the difference between Injection Molding and other manufacturing processes like 3D printing or CNC machining?
Injection Molding is a mass-production manufacturing process that involves injecting molten plastic into a mold cavity, while 3D printing and CNC machining are additive and subtractive processes, respectively, that produce parts one at a time. Injection Molding offers advantages such as faster production rates, higher precision, and lower cost per part.
Injection molding, 3D printing, and CNC machining are all manufacturing processes used to create parts and products, but they differ significantly in their principles, applications, and advantages. Here are the key differences between these three processes:
1. **Injection Molding**:
- Principle: Injection molding involves injecting molten plastic material into a mold cavity to produce a solid part. It is a mass-production process that is highly efficient for creating large quantities of identical parts.
- Materials: Injection molding is primarily used for thermoplastic and thermosetting materials, such as ABS, PE, PP, and more.
- Application: It is commonly used in various industries for high-volume production of plastic components, such as automotive parts, consumer goods, medical devices, and more.
- Advantages: High production rates, design flexibility, cost-effectiveness for large quantities, and the ability to produce complex parts are some of the key advantages of injection molding.
2. **3D Printing (Additive Manufacturing)**:
- Principle: 3D printing, or additive manufacturing, builds up a part layer by layer using computer-controlled machines. It converts digital 3D models into physical objects.
- Materials: A wide range of materials can be used in 3D printing, including plastics, metals, ceramics, and even composites.
- Application: 3D printing is versatile and used in various industries, including rapid prototyping, custom manufacturing, aerospace, medical, and art and design.
- Advantages: Design complexity is virtually unlimited, allowing for rapid prototyping and customization. 3D printing is suitable for low-volume production, and it often eliminates the need for expensive tooling.
3. **CNC Machining**:
- Principle: CNC (Computer Numerical Control) machining involves removing material from a solid block (usually metal or plastic) using computer-controlled cutting tools to create the desired shape.
- Materials: CNC machining can work with a wide range of materials, including metals, plastics, wood, and composites.
- Application: CNC machining is used for precision manufacturing and creating complex parts with high accuracy and tight tolerances.
- Advantages: CNC machining offers excellent accuracy, surface finish, and repeatability. It is well-suited for small to medium production runs and is often used for producing functional prototypes, tooling, and end-use parts.
In summary, injection molding is ideal for mass-producing plastic components with high efficiency and repeatability. 3D printing is suitable for rapid prototyping, custom manufacturing, and creating complex shapes. CNC machining excels in precision manufacturing and is ideal for producing high-quality, functional parts with tight tolerances. The choice between these processes depends on the specific requirements of the project, production volume, material properties, and budget considerations.
What are some common industries that use Injection Molding?
Injection Molding is used in a wide range of industries, including automotive, medical, aerospace, consumer products, and electronics.
Injection molding is a versatile manufacturing process used in a wide range of industries due to its efficiency, ability to produce complex parts, and cost-effectiveness for high-volume production. Some of the common industries that extensively use injection molding include:
1. **Automotive**: Injection molding is widely employed in the automotive industry to produce various components such as interior and exterior trims, dashboard parts, bumpers, door handles, and other critical components.
2. **Consumer Goods**: Many consumer products, such as kitchenware, toys, electronics, and household items, are manufactured using injection molding due to its ability to create intricate designs and high-quality finishes.
3. **Electronics**: Injection molding is used to produce components for electronic devices, including casings, connectors, switches, and other parts used in computers, smartphones, and appliances.
4. **Medical Devices**: Injection molding is crucial in the medical industry for producing a wide range of medical devices and equipment, including syringes, IV components, surgical instruments, and various medical equipment housings.
5. **Packaging**: Injection molding is used in packaging applications to create containers, caps, closures, and other packaging components used in the food and beverage, pharmaceutical, and cosmetics industries.
6. **Aerospace**: The aerospace industry utilizes injection molding for manufacturing parts like aircraft interior components, cabin fittings, and structural elements due to its lightweight and durable properties.
7. **Construction**: Injection molding is employed in the construction industry for producing components such as pipes, fittings, insulation materials, and structural elements.
8. **Sports and Recreation**: Injection molding is used to manufacture sports equipment such as helmets, protective gear, goggles, and various accessories.
9. **Appliances**: Injection molding is commonly used in the appliance industry for producing parts like refrigerator handles, washing machine components, and vacuum cleaner accessories.
10. **Furniture**: Furniture manufacturers use injection molding for producing various components like chair seats, backrests, and other structural elements.
11. **Toys and Games**: Many plastic toys and game components, such as action figures, building blocks, and board game pieces, are manufactured using injection molding.
12. **Electrical and Electronic Enclosures**: Injection molding is commonly used to create enclosures and housings for electrical and electronic devices to provide protection and support.
These are just a few examples, and the use of injection molding spans across numerous other industries due to its versatility and ability to produce high-quality parts at a competitive cost.
How does Injection Molding impact the environment?
Injection Molding can have both positive and negative impacts on the environment. On the positive side, it can reduce waste and energy consumption compared to other manufacturing processes. However, the production of plastic materials used in Injection Molding can have a negative impact on the environment if not properly managed, as plastic waste can accumulate in landfills and oceans.
Injection molding, like any manufacturing process, can have both positive and negative environmental impacts. The extent of these impacts depends on various factors, including the material used, energy consumption, waste generation, and recycling practices. Here are some ways in which injection molding can impact the environment:
**Positive Environmental Impacts:**
1. **Resource Efficiency**: Injection molding is generally efficient in terms of material usage. It produces minimal scrap or waste during the manufacturing process, especially when compared to subtractive processes like CNC machining.
2. **Energy Efficiency**: Injection molding machines are becoming more energy-efficient over time. Manufacturers are investing in technologies to reduce energy consumption during the molding process.
3. **Lightweighting**: Injection molding allows for the production of lightweight parts, which can lead to energy savings during transportation and reduce the overall carbon footprint.
4. **Recycling**: Many injection-molded parts and waste materials can be recycled and reprocessed to produce new products, reducing the demand for virgin materials and reducing landfill waste.
5. **Product Durability**: Injection-molded parts are often durable and long-lasting, leading to less frequent replacements and, thus, lower environmental impact over the product's life cycle.
**Negative Environmental Impacts:**
1. **Energy Consumption**: While injection molding machines are becoming more energy-efficient, the process still requires significant energy input, particularly during the melting and molding phases.
2. **Material Choice**: The choice of materials used in injection molding can impact the environment. Certain plastics, especially those that are difficult to recycle or non-biodegradable, can have long-lasting environmental consequences.
3. **Waste Generation**: Although injection molding generates less waste during production, there may still be waste in the form of defective parts, runners, and sprues. If not properly managed, this waste can contribute to environmental pollution.
4. **Emissions**: Injection molding may emit greenhouse gases and other pollutants during the manufacturing process, especially if the energy sources used are not renewable or clean.
5. **Chemicals and Additives**: The use of certain chemicals, colorants, or additives in the injection molding process can introduce environmental concerns if not managed or disposed of properly.
6. **End-of-Life Management**: Proper end-of-life management of injection-molded products is crucial. If products are not recycled or disposed of responsibly, they can contribute to environmental pollution.
To mitigate the environmental impact of injection molding, manufacturers can implement various strategies, such as using eco-friendly materials, optimizing production processes for energy efficiency, implementing recycling programs, and exploring sustainable end-of-life solutions for their products. Additionally, consumer awareness and responsible waste management play vital roles in reducing the environmental footprint of injection-molded products.
How can Injection Molding be made more sustainable?
Injection Molding can be made more sustainable by using recycled materials, optimizing the design of parts to reduce material usage, and reducing waste through efficient production practices.
Making injection molding more sustainable involves implementing various strategies to reduce its environmental impact throughout the entire life cycle of the products. Here are some ways to make injection molding more sustainable:
1. **Material Selection**: Choose sustainable and eco-friendly materials for injection molding. Opt for biodegradable or recyclable plastics whenever possible, and consider using bio-based or recycled content materials.
2. **Energy Efficiency**: Invest in energy-efficient injection molding machines and optimize process parameters to minimize energy consumption during production.
3. **Waste Reduction**: Implement strategies to reduce waste generation during production. This includes optimizing mold design, runner systems, and using automation to minimize scrap.
4. **Recycling**: Establish recycling programs to collect and reprocess waste materials, defective parts, and runners to reuse in production. Utilize recycled materials whenever feasible.
5. **Closed-Loop Systems**: Implement closed-loop systems that recycle and reuse plastic waste generated during the manufacturing process.
6. **Product Design**: Optimize part design for material efficiency, using less material without compromising performance or functionality. Consider designing for disassembly and recycling.
7. **Life Cycle Assessment (LCA)**: Conduct life cycle assessments to understand the environmental impact of the products and identify areas for improvement in the manufacturing process.
8. **Eco-Friendly Additives**: Choose environmentally friendly additives, colorants, and processing aids that have a lower impact on the environment.
9. **Renewable Energy**: Use renewable energy sources to power the injection molding process, such as solar or wind energy.
10. **Green Certifications**: Obtain green certifications for products that meet specific environmental criteria, demonstrating a commitment to sustainability.
11. **Collaboration with Suppliers**: Work with suppliers and material manufacturers to ensure the sourcing and production of sustainable raw materials.
12. **End-of-Life Solutions**: Develop and promote proper end-of-life solutions for injection-molded products, such as recycling programs and eco-friendly disposal methods.
13. **Education and Awareness**: Educate employees and stakeholders about sustainability practices and the importance of environmental responsibility.
14. **Sustainable Packaging**: Consider the sustainability of packaging materials used for shipping and storing injection-molded products.
15. **Circular Economy Approach**: Adopt a circular economy approach, where products are designed for durability, reuse, and recycling, to minimize waste and resource consumption.
By integrating these sustainable practices into the injection molding process, manufacturers can significantly reduce the environmental impact of their operations and contribute to a more eco-friendly and responsible manufacturing industry. Sustainable injection molding practices benefit not only the environment but also businesses by improving efficiency, reducing costs, and appealing to environmentally conscious customers.
Plastic Injection Molding Frequently Asked Questions
Can Injection Molding be used to produce high-quality parts with tight tolerances?
Yes, Injection Molding can produce high-quality parts with tight tolerances, but it requires careful design, mold construction, and process control to achieve the desired level of precision.
Yes, injection molding can be used to produce high-quality parts with tight tolerances. In fact, injection molding is well-known for its ability to achieve precise and consistent dimensions, making it suitable for manufacturing parts with demanding tolerances. The process involves precise control over various parameters, which enables the production of parts with tight dimensional specifications.
Here are some factors that contribute to achieving high-quality parts with tight tolerances in injection molding:
1. Tool Design and Precision: The mold design plays a critical role in achieving tight tolerances. A well-designed mold with precision machining ensures that the dimensions of the molded part are accurate and consistent.
2. Mold Material and Maintenance: High-quality mold materials, such as hardened steel, are used to maintain dimensional stability over the production life. Regular maintenance of molds ensures that they remain in optimal condition, avoiding wear or distortion that could affect tolerances.
3. Injection Molding Machine Control: Modern injection molding machines have advanced control systems that enable precise regulation of injection pressure, temperature, and cooling rates. This control ensures consistent part quality from shot to shot.
4. Material Selection: Choosing the appropriate material with consistent properties is crucial. Quality materials with low variation help achieve consistent part dimensions.
5. Process Optimization: Careful optimization of the injection molding process, including temperature profiles, injection speed, and cooling time, ensures that parts are formed with minimal variation and within the specified tolerances.
6. Quality Control Measures: Implementing rigorous quality control measures throughout the production process, such as in-process inspections and statistical process control, helps identify and correct any deviations from the desired tolerances.
7. Post-Molding Treatment: Some parts may require post-molding treatments like annealing or stress-relieving to maintain tight tolerances and reduce dimensional variations.
Injection molding is widely used in industries where tight tolerances are essential, such as automotive, aerospace, electronics, medical devices, and precision engineering. However, achieving tight tolerances does require a careful and controlled approach, as variations in any part of the process can affect the final dimensions of the molded parts. Working with experienced injection molding professionals and employing quality control measures ensures the production of high-quality parts with the desired tolerances.
How can I select the right material for my Injection Molding project?
Selecting the right material for an Injection Molding project depends on several factors, such as the part's intended use, operating conditions, and required properties. It is best to consult with an experienced Injection Molding manufacturer to determine the best material for your project.
Selecting the right material for your injection molding project is a crucial step in ensuring the success and performance of your final product. The material choice depends on various factors, including the specific requirements of your application, mechanical properties needed, environmental conditions, regulatory compliance, and cost considerations. Here are the steps to help you select the right material for your injection molding project:
1. **Define Project Requirements**: Clearly outline the functional requirements and specifications of your product. Consider factors like mechanical strength, flexibility, chemical resistance, temperature tolerance, UV stability, and any specific regulatory or industry standards that apply.
2. **Material Property Evaluation**: Understand the material properties required to meet your project's needs. For example, if your product needs high impact resistance, look for materials known for their toughness. If it requires transparency, consider materials with good optical properties.
3. **Material Compatibility with Mold**: Ensure that the selected material is compatible with your mold's design, including its temperature range and surface finish requirements.
4. **Cost Considerations**: Balance performance requirements with cost constraints. Some high-performance materials may be expensive, while others may offer a good compromise between performance and cost.
5. **Material Database and Resources**: Utilize material databases, technical datasheets, and resources from material suppliers. They provide valuable information about material properties, processing guidelines, and potential applications.
6. **Sample Testing and Prototyping**: Conduct sample testing and prototyping with different materials to evaluate their performance in real-world conditions. This helps identify the best material that meets your specific project requirements.
7. **Environmental Impact**: Consider the environmental impact of the materials you are evaluating. Look for eco-friendly options, recycled content, or materials that can be easily recycled after use.
8. **Supplier Reliability**: Work with reputable material suppliers who can provide consistent quality and technical support for your chosen material.
9. **Regulatory Compliance**: Ensure that the material meets any regulatory requirements or certifications necessary for your industry or application.
10. **Future Scalability**: Consider the scalability of the material choice if you plan to expand production or introduce variations of the product in the future.
11. **Consultation with Experts**: Seek advice from experienced injection molding engineers or material specialists who can offer insights based on their expertise and experience.
12. **Material Validation**: Once you have selected a material, conduct thorough validation and testing to verify that it meets all the required specifications and performance criteria.
By carefully considering these factors and conducting proper research and testing, you can select the most appropriate material for your injection molding project, ensuring that your final product performs optimally and meets all the desired requirements.
How can I reduce the cost of Injection Molding?
To reduce the cost of Injection Molding, it is important to optimize the design of the part to minimize material usage, simplify the mold design, and reduce the number of production steps. Additionally, selecting a manufacturer with experience in Injection Molding and a reputation for quality and efficiency can help reduce costs.
Reducing the cost of injection molding requires a strategic approach that considers various aspects of the manufacturing process, material selection, design optimization, and production efficiency. Here are some effective ways to reduce the cost of injection molding:
1. **Material Selection**: Choose cost-effective materials that meet the required performance criteria. Consider using recycled or bio-based materials when feasible to reduce material costs.
2. **Design Optimization**: Design the part with injection molding in mind to minimize material usage and production complexities. Avoid features that add unnecessary complexity and increase production time.
3. **Volume and Tooling**: Assess your production volume needs. For high-volume production, investing in multi-cavity molds can significantly reduce the cost per part.
4. **Mold Material and Maintenance**: Invest in high-quality mold materials for durability and longevity. Regular maintenance of molds ensures they remain in optimal condition, reducing the risk of defects and downtime.
5. **Injection Molding Machine Efficiency**: Use energy-efficient machines that optimize energy consumption during the molding process.
6. **Cycle Time Reduction**: Optimize the injection molding process to reduce cycle times. Minimizing cooling time and optimizing injection parameters can increase production efficiency and reduce costs.
7. **Automation**: Integrate automation wherever possible to reduce manual labor costs and improve overall production efficiency.
8. **Recycling and Waste Reduction**: Implement recycling programs for scrap and waste materials to reuse them in the production process, reducing material costs.
9. **Supplier Relationships**: Build strong relationships with material suppliers and mold manufacturers to negotiate better pricing and terms.
10. **Value Engineering**: Continuously review and evaluate the design and production process to identify areas for cost-saving improvements.
11. **Prototype and Testing**: Conduct thorough prototyping and testing before full-scale production to identify and address any design or manufacturing issues early on, avoiding costly reworks later.
12. **Lean Manufacturing Principles**: Apply lean manufacturing principles to streamline the production process, eliminate waste, and reduce non-value-added activities.
13. **Standardization**: Standardize components and processes where possible to simplify production and reduce the need for custom tooling or modifications.
14. **Quality Control**: Implement stringent quality control measures to minimize defects, rejections, and the need for rework, which can lead to cost overruns.
15. **Volume Commitments**: Consider long-term agreements or volume commitments with suppliers to negotiate more favorable pricing and terms.
By implementing these cost-saving measures and adopting a continuous improvement mindset, you can optimize your injection molding process and reduce overall production costs while maintaining the quality and performance of your products.
Can Injection Molding be used to produce large parts?
Yes, Injection Molding can be used to produce large parts, but it requires specialized equipment and molds designed for large-scale production.
Yes, injection molding can be used to produce large parts, but there are certain limitations and considerations to keep in mind due to the size of the part and the capabilities of the injection molding process.
The primary challenge with producing large parts through injection molding is managing the flow and cooling of the molten plastic material within the mold. As the part size increases, the material flow becomes more challenging to control, and cooling times may lengthen, potentially affecting production cycle times.
Here are some factors to consider when producing large parts through injection molding:
1. **Mold Design**: The mold design must be carefully engineered to accommodate the large part size. It may require thicker and more robust mold walls to withstand the pressures exerted by the molten plastic during injection.
2. **Injection Pressure and Speed**: Higher injection pressures and speeds may be required to ensure proper filling of the large mold cavity. The injection unit of the molding machine should be capable of delivering the necessary pressure and volume.
3. **Cooling**: Cooling becomes more critical for large parts to prevent warping and distortion. Cooling channels within the mold should be strategically designed to facilitate efficient heat transfer.
4. **Cycle Time**: The cooling time is a significant factor in determining the overall cycle time. Longer cooling times for large parts may impact production rates and affect the cost per part.
5. **Material Selection**: The choice of material is important when producing large parts. Materials with good flow properties and low viscosity are preferred to ensure proper filling of the mold and reduce the risk of defects.
6. **Machine Size**: The injection molding machine's clamping force and shot size should be large enough to accommodate the size and weight of the part.
7. **Handling and Ejection**: Large parts may require specialized handling equipment for ejection and post-processing, considering their weight and dimensions.
8. **Warping and Shrinkage**: Large parts are more susceptible to warping and shrinkage during cooling. Design considerations and material selection can help minimize these effects.
While injection molding can be used to produce large parts, it is essential to work with experienced engineers and mold designers who understand the unique challenges associated with large part production. Prototyping and thorough testing are also crucial to validate the design and optimize the process for large-scale production. In some cases, other manufacturing processes like rotational molding or thermoforming may be more suitable for producing very large parts with complex shapes.
What is the difference between a single-cavity mold and a multi-cavity mold?
A single-cavity mold produces one part at a time, while a multi-cavity mold produces multiple parts in a single cycle, resulting in higher production output and lower cost per part.
The difference between a single-cavity mold and a multi-cavity mold lies in the number of identical parts they can produce in a single cycle of the injection molding process. These molds are used in injection molding to shape plastic material into finished parts. Here's a comparison of the two types of molds:
1. **Single-Cavity Mold**:
- Definition: A single-cavity mold, as the name suggests, has only one cavity or impression that shapes the molten plastic into a single part during each molding cycle.
- Production Output: A single-cavity mold produces one part per injection cycle. This means that for every molding cycle, the machine produces only a single unit of the desired part.
- Advantages: Single-cavity molds are straightforward and easy to manufacture. They are typically used for small production runs, prototyping, or when producing large and complex parts that require individual attention.
2. **Multi-Cavity Mold**:
- Definition: A multi-cavity mold contains multiple cavities or impressions that allow the mold to shape multiple identical parts in a single injection cycle.
- Production Output: A multi-cavity mold can produce multiple parts per injection cycle, depending on the number of cavities. For example, a two-cavity mold would produce two parts per cycle, a four-cavity mold would produce four parts, and so on.
- Advantages: Multi-cavity molds significantly increase production efficiency, as they produce more parts in the same amount of time. They are ideal for high-volume production runs when a large quantity of identical parts is required. They help reduce per-part production costs as the mold cost is spread across multiple parts.
**Key Differences Summary**:
- Single-cavity molds produce one part per cycle, while multi-cavity molds produce multiple identical parts per cycle.
- Single-cavity molds are suitable for small production runs, prototyping, or complex parts, while multi-cavity molds are ideal for high-volume production to optimize efficiency and reduce costs.
- Multi-cavity molds require more complex and precise manufacturing processes, making them more expensive than single-cavity molds.
- The choice between single-cavity and multi-cavity molds depends on the production requirements, production volume, part complexity, and cost considerations. For small production runs or specialized parts, a single-cavity mold might be more appropriate. For high-volume production, a multi-cavity mold offers significant benefits in terms of efficiency and cost-effectiveness.
How can I ensure the quality of Injection Molded parts?
To ensure the quality of Injection Molded parts, it is important to implement a comprehensive quality control system that includes testing and inspection of parts throughout the production process. It is also important to work with an experienced Injection Molding manufacturer with a reputation for producing high-quality parts.
Ensuring the quality of injection molded parts requires a comprehensive approach that involves careful planning, process control, and rigorous quality control measures. Here are some essential steps to ensure the quality of injection molded parts:
1. **Design for Manufacturability (DFM)**: Begin with a well-optimized part design that takes into consideration the capabilities and limitations of injection molding. This helps avoid potential molding issues and ensures the manufacturability of the part.
2. **Mold Design and Tooling**: Work with experienced mold designers and manufacturers to create high-quality molds that meet the part specifications and dimensional tolerances. Proper mold construction and precision machining are crucial for part quality.
3. **Material Selection**: Choose the right material that meets the mechanical, thermal, and chemical requirements of the part. Verify the material's properties and quality with reputable suppliers.
4. **Process Optimization**: Carefully control the injection molding process parameters, including temperature, pressure, injection speed, and cooling time. Process optimization helps achieve consistent part quality and minimizes variations.
5. **Validation and Prototyping**: Conduct thorough testing and validation of the part design and mold through prototyping. This step allows for identification and resolution of potential issues before full-scale production.
6. **Quality Control during Production**: Implement in-process quality checks and inspections during production. Regularly monitor the molding process to ensure it remains within specified parameters.
7. **Statistical Process Control (SPC)**: Use SPC techniques to monitor and analyze production data. This helps identify trends, deviations, and potential issues early on, allowing for timely corrective actions.
8. **Inspection and Measurement**: Use accurate measurement tools and inspection equipment to verify part dimensions, tolerances, and surface finish. Inspections should occur at regular intervals during production.
9. **Defect Analysis and Root Cause Investigation**: When defects occur, conduct thorough analysis to identify the root cause. Addressing the root cause prevents recurrence of similar defects in future production runs.
10. **Training and Skill Development**: Ensure that operators and technicians are properly trained and have the necessary skills to operate the injection molding machines and carry out quality control procedures effectively.
11. **Traceability**: Implement a system for tracking and tracing each batch of parts to maintain product traceability and facilitate quick response to any quality issues.
12. **Supplier Quality Management**: Work with reputable suppliers for materials and other components to maintain consistent quality throughout the supply chain.
13. **Certifications and Standards**: Comply with relevant industry standards and obtain necessary certifications to demonstrate product quality and adherence to regulations.
By integrating these quality assurance measures into the injection molding process, you can ensure that the molded parts meet the required specifications, perform as intended, and maintain consistent quality throughout production.
What is the lead time for Injection Molding projects?
The lead time for Injection Molding projects varies depending on several factors, such as the complexity of the part, the size of the production run, and the availability of materials and molds. A reputable Injection Molding manufacturer can provide a more accurate estimate of lead time based on the specific requirements of the project.
The lead time for injection molding projects can vary significantly depending on several factors, including the complexity of the part, the size of the production run, the availability of materials and tooling, the capacity of the injection molding company, and any additional finishing or post-processing requirements. Generally, the lead time for injection molding projects can be broken down into the following stages:
1. **Tooling Design and Manufacturing**: This stage involves designing and manufacturing the injection mold, which is a critical component for the production process. The time required for mold design and fabrication can range from a few weeks to several months, depending on the mold's complexity and the workload of the mold manufacturer.
2. **Prototyping and Validation**: Before full-scale production, it is common to create prototypes of the part to verify its design, fit, and function. The time required for prototyping and validation can vary, but it is typically completed within a few days to a few weeks.
3. **Material Sourcing and Preparation**: The lead time for sourcing the required materials will depend on the availability of the specific material and the supplier's lead time. Materials can typically be sourced within a few days to a couple of weeks.
4. **Production Run**: The actual production of the injection-molded parts will depend on the quantity required. Short production runs with low quantities can be completed in a matter of days or weeks. However, high-volume production runs may take several weeks or even months to complete.
5. **Post-Processing and Finishing**: If any post-processing or finishing steps are required, such as painting, assembly, or packaging, the lead time will be extended accordingly.
6. **Shipping and Delivery**: The time required for shipping and delivery will depend on the location of the injection molding company and the final destination of the parts.
In summary, the total lead time for an injection molding project can range from a few weeks to several months, with the most significant contributing factor being the mold design and manufacturing process. It is essential to work closely with the injection molding company and plan ahead to minimize lead times and ensure that the project timeline aligns with your production schedule and business needs.
What is the difference between hot runner and cold runner molds?
A hot runner mold has a heated runner system that keeps the plastic material in a molten state, while a cold runner mold has a separate runner system that is not heated. Hot runner molds offer faster cycle times and reduced waste, but are more expensive to produce and maintain.
Hot runner and cold runner molds are two different types of injection molding systems used to deliver molten plastic into the mold cavity. The key difference between the two lies in how they manage the flow of plastic and handle the runners (the channels that direct molten plastic from the injection molding machine to the mold cavities). Let's take a closer look at each:
**Hot Runner Mold**:
1. **Definition**: In a hot runner mold, the channels through which molten plastic flows from the injection molding machine to the mold cavities are kept at an elevated temperature (heated). The plastic inside the hot runner system remains molten even during the injection molding cycle, eliminating the need for runners to be solidified and subsequently ejected.
2. **Advantages**:
- Reduced Waste: Hot runner molds eliminate the need for runners, resulting in less material waste and cost savings.
- Faster Cycle Time: As there are no solidified runners to remove, the cycle time is often faster, leading to higher production efficiency.
- Improved Part Quality: Hot runner systems help maintain uniform melt flow, reducing the chances of part defects such as gate marks and knit lines.
3. **Applications**: Hot runner molds are suitable for high-volume production and applications where minimizing material waste and cycle time is critical.
**Cold Runner Mold**:
1. **Definition**: In a cold runner mold, the channels through which molten plastic flows from the injection molding machine to the mold cavities are not heated. The plastic inside the runners cools and solidifies, and the solidified runners are ejected along with the part at the end of each cycle.
2. **Advantages**:
- Simplicity: Cold runner molds are simpler in design and typically more cost-effective for smaller production runs or parts with simple geometries.
- Flexibility: Cold runner molds allow for easy color changes and material swaps since the runners are separate from the part.
3. **Applications**: Cold runner molds are often used for low to medium volume production or when material changes are required between production runs.
**Key Differences Summary**:
- Hot runner molds have heated channels that keep the plastic molten, while cold runner molds have unheated channels that allow the plastic to solidify as runners.
- Hot runner molds reduce material waste, have faster cycle times, and improve part quality, while cold runner molds are simpler and more cost-effective for smaller production runs or when material changes are needed.
- Hot runner molds are commonly used in high-volume production, while cold runner molds are suitable for low to medium volume production or when material flexibility is required.
Can Injection Molding be used to produce parts with high strength and stiffness?
Yes, Injection Molding can be used to produce parts with high strength and stiffness, but it requires careful selection of materials and process parameters to achieve the desired properties.
Yes, injection molding can be used to produce parts with high strength and stiffness, provided that the appropriate material is chosen and the part design is optimized to meet the mechanical requirements. The strength and stiffness of injection-molded parts are influenced by several factors:
1. **Material Selection**: The choice of material is critical in determining the mechanical properties of the final part. There are various high-performance engineering plastics available for injection molding, such as nylon, polycarbonate, polypropylene, and ABS, which offer excellent strength and stiffness.
2. **Fillers and Reinforcements**: Certain materials can be enhanced with fillers and reinforcements, such as glass fibers, carbon fibers, or mineral fillers. These additives can significantly improve the strength and stiffness of the injection-molded parts.
3. **Part Design**: Designing the part with sufficient wall thickness and appropriate ribbing or support structures can enhance its strength and stiffness. Ribs or gussets can distribute loads more effectively, increasing the part's rigidity.
4. **Gate Placement**: Proper gate placement can help optimize the flow of molten plastic into the mold, reducing the risk of weak spots or flow-induced defects that may compromise strength and stiffness.
5. **Mold Design and Manufacturing**: A well-designed and precisely manufactured mold ensures that the part maintains its dimensional accuracy, which is crucial for achieving consistent mechanical properties.
6. **Post-Molding Treatments**: Certain post-molding treatments, such as annealing or stress-relieving, can improve the part's mechanical properties and reduce internal stresses, enhancing strength and stiffness.
7. **Quality Control and Process Optimization**: Implementing rigorous quality control measures and optimizing the injection molding process help ensure that each part meets the desired mechanical specifications.
Injection molding is widely used to produce high-strength and high-stiffness parts for various industries, including automotive, aerospace, electronics, and consumer goods. However, it's essential to work closely with experienced injection molding engineers and material specialists to select the right material and optimize the part design and production process for the desired mechanical properties. Additionally, conducting testing and validation on prototypes helps ensure that the final injection-molded parts meet the required strength and stiffness criteria.
How can I troubleshoot Injection Molding issues?
To troubleshoot Injection Molding issues, it is important to understand the root cause of the problem and to implement corrective actions such as adjusting process parameters, modifying the mold design, or changing materials. An experienced Injection Molding manufacturer can provide valuable insights and expertise in troubleshooting and resolving issues.
Troubleshooting injection molding issues requires a systematic approach to identify and address the root causes of problems. When faced with issues in the injection molding process, follow these steps to effectively troubleshoot and resolve the issues:
1. **Define the Problem**: Clearly define the specific issue you are encountering. It could be related to part defects, dimensional variations, cosmetic imperfections, or any other molding-related problem.
2. **Check Process Parameters**: Review the injection molding machine's process parameters, such as temperature, pressure, injection speed, and cooling time. Ensure they are set correctly and within the recommended range for the material and part design.
3. **Inspect Mold and Tooling**: Examine the mold for any damage, wear, or issues with the cooling system. Check the tooling for proper alignment and cleanliness.
4. **Material Analysis**: Verify the material being used in the injection molding process. Check for contamination, moisture, or variations in material properties that could be contributing to the problem.
5. **Part Design Review**: Evaluate the part design to identify any features that could be causing the issue. Check for thick sections, thin walls, or sharp corners that may lead to defects.
6. **Gate and Runner System**: Analyze the gate design and runner system. Improper gate design or runner configurations can result in flow-related defects.
7. **Machine Settings**: Check the injection pressure, back pressure, screw speed, and other machine settings. Adjust them as needed to improve part quality.
8. **Cooling**: Review the cooling system to ensure it is effectively removing heat from the mold and parts.
9. **Process Monitoring**: Use process monitoring tools like statistical process control (SPC) to analyze production data and identify trends or variations that may be contributing to the issue.
10. **Documentation**: Keep detailed records of the troubleshooting process, including changes made, results, and their impact on part quality.
11. **Testing and Validation**: Conduct testing and validation with different settings and process parameters to identify the optimal conditions for quality production.
12. **Consult Experts**: If you are unable to identify or resolve the issue, consult with experienced injection molding professionals, material experts, or mold designers who can provide insights and solutions.
13. **Implement Solutions**: Based on the analysis and findings, implement the necessary changes to resolve the issue and improve part quality.
14. **Continuous Improvement**: Establish a process for continuous improvement, monitoring, and regular maintenance to prevent similar issues in the future.
Remember that injection molding troubleshooting may require patience and iterative testing to identify the root cause successfully. By following these steps and working systematically, you can effectively troubleshoot injection molding issues and achieve consistent, high-quality part production.