Custom CNC Machining Service
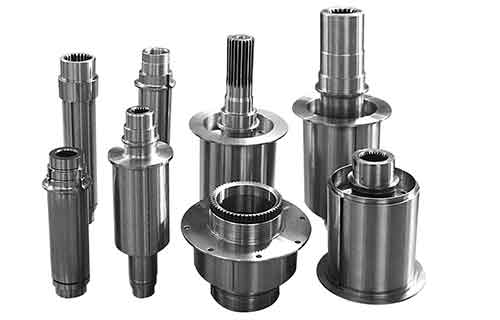
Custom Precision Part CNC Machining Services
In our online CNC machining service, you can easily obtain instant quotes for customized metal and plastic parts. We can quickly produce prototypes and production parts within a few days.
Our facilities have passed ISO 9001:2015, ISO 13485, and AS9100D certifications, ensuring the highest quality standards. We have a high-quality machine workshop with professional knowledge in manufacturing any customized design, whether simple or complex.
We offer a wide range of capabilities, including rapid prototyping, small batch processing, and mass production. Our goal is to provide you with the necessary mechanical components when you need them.
Let's start using our convenient online platform. Submit your design and specifications to receive pricing information immediately. Let us handle your customized processing needs and deliver the parts you need on time, fully meeting your specifications.
What is Plastic Metal Part CNC Machining Service?
CNC, Computer numerical control machining is a widely used manufacturing process. It utilizes automated, high-speed cutting tools to form design patterns from metal or plastic raw materials. Standard CNC machine tools include 3-axis, 4-axis, and 5-axis milling machines, lathes, and routers. Different machine tools may have different cutting methods for CNC parts - the workpiece can remain stationary while the tool moves, or the tool can remain stationary while the workpiece rotates and moves, and even the cutting tool and workpiece can move together.
Skilled mechanics operate CNC machines by programming tool paths based on the geometric shape of the final machined parts. The geometric information of the components is provided by computer-aided design (CAD) models. CNC machine tools are capable of cutting almost all metal alloys and hard plastics with high precision and repeatability, making customized machined parts suitable for almost all industries, including aviation, medical, robotics, electronics, and industry. We provide CNC services and offer customized CNC quotes for over 40 materials, ranging from common aluminum and formaldehyde to advanced titanium and engineering plastics such as PEEK and polytetrafluoroethylene.
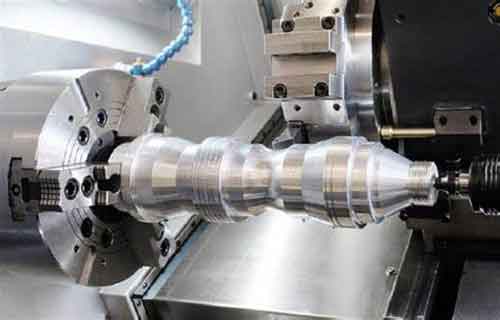
Metal CNC Machining Materials
CNC Machining Aluminum Alloys
Aluminum 6061
Aluminum 5052
Aluminum 2024
Aluminum 6063
Aluminum 7050
Aluminum 7075
Aluminum MIC-6
CNC Machining Bronze Alloys
Copper C932
CNC Machining Stainless Steel Alloys
Nitronic 60 (218 SS)
Stainless Steel 15-5
Stainless Steel 17-4
Stainless Steel 18-8
Stainless Steel 303
Stainless Steel 316/316L
Stainless Steel 416
Stainless Steel 410
Stainless Steel 420
Stainless Steel 440C
CNC Machining Zinc Alloys
Zinc Alloy
Plastic CNC Machining Materials
CNC Machining ABS
High-strength engineering plastic used for many commercial products.
CNC Machining Acrylic
A clear glass-like plastic. Good wear and tear properties. Great for outdoor use.
CNC Machining Delrin (Acetal)
Resin with good moisture resistance, high wear-resistance, and low friction.
CNC Machining Garolite G10
Constructed of an epoxy resin with fiberglass fabric reinforcement, and also called epoxy-grade industrial laminate and phenolic, this material offers high strength and low moisture absorption.
CNC Machining HDPE
High-density polyethylene is a moisture and chemical-resistant plastic with good impact strength. The material is outstanding for outdoor applications as well as watertight containers or seals.
CNC Machining Nylon 6/6
Offers increased mechanical strength, rigidity, good stability under heat and/or chemical resistance.
CNC Machining PC (Polycarbonate)
With almost twice the tensile strength of ABS, polycarbonate has superior mechanical and structural properties. Used widely in automotive, aerospace, and other applications that require durability and stability.
CNC Machining PEEK
Offering excellent tensile strength, PEEK is often used as a lightweight substitute for metal parts in high-temperature, high-stress applications. PEEK resists chemicals, wear, and moisture.
CNC Machining Polypropylene
Has excellent electrical properties and little or no moisture absorption. It carries light loads for a long period in widely varying temperatures. It can be machined into parts requiring chemical or corrosion resistance.
CNC Machining PTFE (Teflon)
This material surpasses most plastics when it comes to chemical resistance and performance in extreme temperatures. It resists most solvents and is an excellent electrical insulator.
CNC Machining UHMW PE
Ultra-high molecular weight polyethylene. A general-purpose material. It offers a unique combination of wear and corrosion resistance, low surface friction, high impact strength, high chemical resistance, and does not absorb moisture.
CNC Machining PVC
Polyvinyl chloride (Type 1) is a highly chemical-resistant synthetic plastic, PVC is commonly in environments exposed to liquids or requires electrical insulation.
CNC Machining Surface Finishes
CNC Machining Standard (As-Milled)
The finish option with the quickest turnaround. Machined parts are left with visible tool marks and potentially sharp edges and burrs, which can be removed upon request. CNC machining surface finish is comparable to 125 uin Ra finish.
CNC Machining Bead Blast
The part surface is left with a smooth, matte appearance.
CNC Machining Tumbled
This is a batch-based process that tumbles vibrating media to remove sharp edges and burrs on CNC parts. Tumbling can remove machine marks on exterior surfaces. Parts over 8” may require a manual review.
CNC Machining Anodized (Type II Or Type III)
Type II (MIL-A-8625, Type II) creates a corrosion-resistant finish. Parts can be anodized in different colors—clear, black, red, and gold are most common—and is usually associated with aluminum.
Type III (MIL-A-8625, Type III, Class 1/2 "hardcoat") is thicker and creates a wear-resistant layer in addition to the corrosion resistance seen with Type II.
CNC Machining Titanium Anodize
A surface finish for titanium per AMS-2488 Type 2 specification. Also called Tiodize, this finish increases fatigue strength and the wear resistance of a part. Titanium anodized parts are common in aerospace and medical device manufacturing. Non-pigmented titanium anodize finishes will dull shine.
CNC Machining PTFE Impregnated Hard Anodize
A hard coat anodize process that embeds PTFE to create a self-lubricating, dry contact surface with Type 3 hard coat’s protective properties. This finish can be used on aluminum alloys or titanium and increases the service life of the product. This finish conforms to the AMS-2482 Type 1 Hard Coat Anodizing with Teflon (Non-Dyed).
CNC Machining Chem Film (Chromate Conversion Coating)
Provides corrosion resistance and good conductivity properties. Can be used as a base for paint. Can leave surface yellow/gold. Adds very little thickness, about 0.00001”-0.00004”. Chem film will conform to MIL-DTL-5541, TYPE I/II.
CNC Machining Passivation
Improves corrosion resistance for 200 and 300 series and precipitation hardened corrosion-resistant steels. Thickness is negligible, about 0.0000001”. Conforms to ASTM A967, AMS-QQ-P-35, MIL-STD-171, ASTM A380, or AMS 2700.
CNC Machining Powder Coat
This is a process where powdered paint is sprayed onto a part that is then baked in an oven. This creates a strong, wear- and corrosion-resistant layer that is more durable than standard painting methods. A wide variety of colors are available to create the desired aesthetic.
CNC Machining Electropolishing
An electrochemical process cleans steel parts to reduce corrosion and improve appearance, by making the metal brighter. Removes about 0.0001”-0.0025” of the metal. Conforms to ASTM B912-02.
CNC Machining Electroless Nickel Plating
Provides uniform nickel coating which offers protection from corrosion, oxidation, and wear on irregular surfaces. The finished part will be brighter. Thickness starts at .0001”. Conforms to MIL-C-26074.
CNC Machining Silver Plating
Silver offers high solderability and electrical conductivity but is susceptible to tarnish. Conforms to AMS QQ-S-365D. Thickness is about 0.00002” - 0.0003.”
CNC Machining Gold Plating
Gold Plating provides good corrosion and tarnish resistance with excellent solderability. Default application specification is MIL-G-45204 and ASTM B488, CLASS 00, 0, OR 1. Thickness is about 0.00002" - 0.00005."
CNC Machining Zinc Plating
Provides uniform zinc coating which offers protection from corrosion, oxidation, and wear on irregular surfaces. Conforms to ASTM B633-15.
CNC Machining Advantages
CNC milling and turning are two extremely precise and repeatable machining processes. According to different specification requirements, we can achieve a tolerance range between ± 0.001 inches and ± 0.005 inches. These machines can be programmed to run reliably for 24 hours, seven days a week, if needed, making CNC milling a good method for producing parts on demand.
Using standard tools, CNC machining services are particularly suitable for manufacturing disposable parts, customizing CNC parts, such as replacing old components or providing customers with professional upgrades. Similarly, expanding the production scale of individual components to over 10000 units is also feasible. Depending on the quantity, size, and complexity of the units, the turnover time for CNC machined parts can be as short as one day. With transportation and delivery, we can meet the deadline within a week.
Another major advantage of CNC technology is its achievable mechanical performance. By cutting from large pieces of material instead of undergoing thermal deformation like injection molding or additive manufacturing, all ideal mechanical properties of the selected metal or plastic are preserved. The materials that can be machined using CNC milling and turning include over 50 industrial grade metals, alloys, and plastics. This option includes aluminum, brass, bronze, titanium, stainless steel, PEEK, ABS, and zinc. For CNC machining, the only material requirement is that the parts have sufficient hardness for fixation and cutting.
Imagine you have an urgent project that requires the completion of thousands of high-precision parts within a week. Traditional machining methods may not be able to meet this urgent need, but CNC technology can. It not only ensures that each part is precise to the micrometer, but also enables mass production in just a few days. That's why many industry leaders rely on CNC machining to meet their most demanding requirements.
In addition, the flexibility of CNC technology means that even the most complex designs can be achieved. Whether you need a simple block shaped part or a part with multiple complex geometric shapes, CNC machines can accurately manufacture it. This provides designers with unlimited creative possibilities and allows them to achieve their vision without sacrificing quality.
In short, CNC milling and turning is not just a manufacturing process, it is an art form. It combines advanced technology and human creativity to create products that are both practical and aesthetically pleasing. Next time you pick up a part made with CNC technology, stop and think about the engineering miracle behind it.
Part CNC Machining Frequently Asked Questions
What is CNC programming?
CNC programming involves writing code that tells the machine how to move and cut the material to create the desired part.
CNC programming stands for Computer Numerical Control programming. It is a process of creating instructions, called G-codes and M-codes, that control the movements of a CNC (Computer Numerical Control) machine. CNC machines are advanced manufacturing tools that can automatically perform precise and complex machining operations on various materials, such as metal, wood, plastic, and composites.
In CNC programming, a programmer or operator uses computer software to generate a set of instructions that guide the CNC machine's movements and operations. These instructions are written in a specific CNC programming language understood by the machine's control system.
Here's how CNC programming works:
1. CAD Design: The first step is to create a detailed 3D model of the part or component to be machined using Computer-Aided Design (CAD) software. The CAD model serves as the blueprint for the CNC program.
2. CAM Software: After designing the part, the CAD model is imported into Computer-Aided Manufacturing (CAM) software. CAM software helps convert the CAD model into CNC machine-readable code.
3. Toolpath Generation: In the CAM software, the programmer defines the toolpaths that the CNC machine will follow to cut and shape the material. Toolpaths determine the tool's movements and cutting directions to achieve the desired shape and finish.
4. G-code Generation: Once the toolpaths are defined, the CAM software generates G-codes and M-codes. G-codes are commands that control the machine's movements, such as positioning, feed rates, and tool changes. M-codes are codes for auxiliary functions, such as tool changes, coolant control, and spindle on/off.
5. CNC Machine Setup: The CNC program is transferred to the CNC machine's control system, typically using a USB drive or network connection. The material to be machined is loaded onto the machine, and the necessary tools are set up.
6. CNC Machining: Once the CNC machine is set up and the program is loaded, the machining process begins. The CNC machine follows the G-codes and M-codes to move the cutting tool precisely and perform the specified operations on the material.
7. Quality Control: Throughout the machining process, operators may perform quality checks and measurements to ensure that the final part meets the required specifications.
CNC programming allows for precise and repeatable manufacturing processes, enabling the production of complex and accurate parts with minimal human intervention. It is widely used in various industries, including aerospace, automotive, electronics, and manufacturing, for tasks such as milling, turning, drilling, and cutting.
What is the role of quality control in CNC machining?
Quality control measures ensure that CNC machined parts meet the required specifications for dimensional accuracy, surface finish, and strength.
Quality control plays a crucial role in CNC machining to ensure that the final products meet the required specifications and quality standards. CNC machining involves precise and automated manufacturing processes, and effective quality control measures are essential to verify that the parts produced are accurate, consistent, and free from defects. Here are the key roles of quality control in CNC machining:
1. **Verification of Design Specifications:** Quality control begins by verifying that the CAD/CAM design specifications match the required dimensions and tolerances. The quality control team ensures that the CNC program accurately reflects the intended design and machining requirements.
2. **Machine Calibration and Setup:** Before starting the machining process, quality control includes verifying that the CNC machine is correctly calibrated and set up. This ensures that the machine's movements and measurements are accurate and aligned with the programmed instructions.
3. **Inspection of Raw Materials:** Quality control personnel inspect the raw materials used for machining to ensure they meet the required quality and composition standards. Material inspection helps prevent potential defects caused by poor material quality.
4. **First Article Inspection:** During the initial production run, a first article inspection is conducted to validate the part's dimensions and features against the design specifications. Any discrepancies or deviations are identified and addressed before proceeding with full-scale production.
5. **In-Process Inspection:** Regular in-process inspections are performed at various stages of the machining process. This helps detect any issues or deviations early on and allows for adjustments to be made to maintain dimensional accuracy.
6. **Surface Finish and Visual Inspection:** Quality control personnel inspect the surface finish of machined parts to ensure they meet the required texture and appearance standards. Visual inspection helps identify surface defects or cosmetic issues that may need to be addressed.
7. **Tolerance Verification:** CNC machining often requires tight tolerances to meet precise requirements. Quality control measures include verifying that the finished parts adhere to the specified tolerances and are within acceptable limits.
8. **Final Inspection:** Once all machining operations are complete, a final inspection is carried out to ensure that the parts meet all the required quality criteria. This inspection verifies that the parts are free from defects and conform to the design specifications.
9. **Non-Destructive Testing (NDT):** In some cases, non-destructive testing techniques, such as ultrasonic testing or X-ray inspection, may be used to detect internal defects or material inconsistencies that may not be visible through visual inspection.
10. **Documentation and Traceability:** Quality control maintains detailed records and documentation of inspection results for traceability and accountability. This documentation aids in identifying and addressing any quality issues that may arise later.
Effective quality control in CNC machining ensures that the final products are of high quality, free from defects, and conform to customer requirements and industry standards. It helps prevent costly rework, reduces waste, and ultimately leads to customer satisfaction and product reliability.
What are some common types of cutting tools used in CNC machining?
Common types include drills, end mills, and taps.
In CNC machining, a variety of cutting tools are used to perform different operations, such as milling, turning, drilling, and cutting. The choice of cutting tool depends on the specific machining operation, the material being machined, and the desired outcome. Some common types of cutting tools used in CNC machining include:
1. **End Mills:** End mills are versatile cutting tools used for milling operations. They have cutting edges on the end and the sides of the tool, allowing them to remove material in various directions. End mills come in various shapes, such as square end, ball nose, and corner radius, for different machining tasks.
2. **Drill Bits:** Drill bits are used for creating holes in the workpiece. They come in different types, such as twist drills for general-purpose drilling and spot drills for precise hole location before drilling.
3. **Turning Inserts:** Turning inserts are used in lathe machines for turning operations. These inserts have cutting edges that remove material as the workpiece rotates, creating cylindrical shapes.
4. **Face Mills:** Face mills have large cutting surfaces and are used for facing operations, where material is removed from the workpiece's surface to achieve a smooth finish.
5. **Taps:** Taps are used for creating internal threads in holes. They come in different thread sizes and types, such as straight flute taps and spiral point taps.
6. **Reamers:** Reamers are precision cutting tools used to enlarge and improve the accuracy of existing holes. They produce smoother and more accurately sized holes than drills.
7. **Chamfer Mills:** Chamfer mills are used to create chamfered edges on the workpiece, providing a beveled or angled finish to the material.
8. **Counterbores:** Counterbores are used to create a flat-bottomed hole with a larger diameter at the opening to accommodate bolts or screws' heads.
9. **Countersinks:** Countersinks are used to create a conical recess in a hole, allowing screw heads to sit flush with the workpiece's surface.
10. **Milling Cutters:** Milling cutters come in various shapes and sizes for specialized milling operations, such as slotting, side milling, and contouring.
11. **Broaches:** Broaches are cutting tools with teeth that gradually increase in size, used for precise and repetitive shaping or finishing operations.
12. **Boring Bars:** Boring bars are used to enlarge existing holes in a workpiece, and they can be adjusted for different diameters.
These are just a few examples of the many cutting tools used in CNC machining. Each cutting tool is designed to perform specific operations efficiently and effectively. CNC operators and programmers select the appropriate cutting tools based on the machining requirements, material properties, and desired surface finish. Proper tool selection and toolpath programming are critical to achieving high-quality results in CNC machining operations.
What is the role of fixturing in CNC machining?
Fixturing refers to the process of holding the material being machined in place to ensure accuracy and consistency.
Fixturing plays a critical role in CNC machining as it is essential for securing and positioning the workpiece during the machining process. Fixturing refers to the use of specialized tools and devices, known as fixtures, to hold the workpiece firmly in place on the CNC machine's table or spindle. The primary role of fixturing in CNC machining is to:
1. **Secure the Workpiece:** Fixturing ensures that the workpiece is securely held in place during machining. It prevents the workpiece from shifting, vibrating, or moving during cutting operations, which could lead to inaccurate results or damaged parts.
2. **Accurate Positioning:** Proper fixturing allows for precise positioning of the workpiece relative to the CNC machine's cutting tool. This accuracy is crucial for achieving the desired dimensions and tolerances in the finished part.
3. **Repeatability:** Fixturing provides repeatability, meaning that the same workpiece can be positioned in the same way for subsequent machining operations or when producing multiple identical parts. This consistency ensures uniformity in the final products.
4. **Multiple Side Machining:** In many CNC machining operations, a single workpiece requires machining on multiple sides. Fixturing allows the workpiece to be repositioned accurately, so each side can be machined without losing alignment.
5. **Reduced Setup Time:** With the use of dedicated fixtures, setup time for each machining operation can be reduced. Once a fixture is properly calibrated, subsequent workpieces can be quickly loaded and positioned for machining.
6. **Safety:** Proper fixturing enhances safety during CNC machining. It prevents the workpiece from coming loose or flying off during high-speed cutting, reducing the risk of accidents and injuries.
7. **Flexibility:** Fixturing provides flexibility to accommodate different shapes and sizes of workpieces. Customized fixtures can be designed for specific parts, making it possible to machine a wide range of components.
8. **Optimized Cutting Conditions:** Properly designed fixtures can allow for optimal cutting conditions, such as the right angle of approach for the cutting tool and access to specific features on the workpiece.
9. **Minimized Material Waste:** Securely fixturing the workpiece helps minimize material waste by reducing the likelihood of workpiece movement leading to machining errors.
10. **Better Surface Finish:** Stable fixturing ensures that the workpiece remains in a fixed position during machining, leading to smoother cuts and improved surface finishes on the final part.
Proper fixturing is a crucial aspect of CNC machining, and skilled machinists pay close attention to selecting or designing the right fixtures for each job. Fixturing techniques may vary depending on the type of CNC machine, the specific machining operations, and the complexity of the workpiece. Effective fixturing contributes to the overall efficiency, accuracy, and quality of CNC machining processes.
How can CNC machining manufacturers ensure the quality of their parts?
Manufacturers can use quality control measures such as testing and inspection to ensure that their parts meet the required specifications.
CNC machining manufacturers can ensure the quality of their parts by implementing a combination of practices and quality control measures throughout the entire manufacturing process. Here are some essential steps and strategies to ensure the quality of CNC-machined parts:
1. **Design Review:** Conduct a thorough design review to ensure that the CAD model and CAM program accurately represent the desired part specifications. Verify tolerances, material requirements, and any special instructions.
2. **Material Inspection:** Inspect the raw materials before machining to ensure they meet the required quality standards and material properties.
3. **CNC Machine Calibration:** Regularly calibrate CNC machines to ensure accurate positioning, movement, and measurements.
4. **Fixture Design and Verification:** Ensure that the fixtures used to hold the workpiece during machining are properly designed, well-suited for the part, and securely fastened.
5. **First Article Inspection:** Perform a first article inspection for the initial production run to verify that the first part matches the design specifications. Address any discrepancies before full-scale production.
6. **In-Process Inspection:** Conduct regular in-process inspections to monitor the machining process and detect any deviations or defects early on. Use precision measuring tools, such as calipers, micrometers, and CMMs (Coordinate Measuring Machines), as needed.
7. **Surface Finish Inspection:** Inspect the surface finish of machined parts to ensure they meet the required texture and appearance standards.
8. **Tolerance Verification:** Verify that the finished parts adhere to the specified tolerances and are within acceptable limits.
9. **Quality Documentation:** Maintain detailed records and documentation of inspection results for each part to ensure traceability and accountability.
10. **Training and Skilled Workforce:** Ensure that CNC machine operators and quality control personnel are properly trained and skilled in operating the machines and conducting inspections.
11. **Statistical Process Control (SPC):** Implement SPC techniques to monitor and control the manufacturing process, identify trends, and prevent defects.
12. **Non-Destructive Testing (NDT):** Use non-destructive testing techniques, such as ultrasonic testing or X-ray inspection, for critical parts to detect internal defects or material inconsistencies.
13. **Continuous Improvement:** Encourage a culture of continuous improvement, where feedback from inspections and customer feedback is used to identify areas for improvement and implement corrective actions.
14. **Quality Certifications:** Obtain quality certifications, such as ISO 9001, to demonstrate compliance with international quality standards.
15. **Customer Feedback and Satisfaction:** Listen to customer feedback and address any quality concerns promptly to ensure customer satisfaction.
By implementing these practices and quality control measures, CNC machining manufacturers can consistently produce high-quality parts that meet customer requirements and industry standards. Quality assurance should be an integral part of the manufacturing process, from design to final inspection, to ensure the successful delivery of reliable and precise CNC-machined components.
What are some common finishing processes for CNC machined parts?
Common finishing processes include polishing, painting, and anodizing.
After the CNC machining process, parts often undergo various finishing processes to improve their appearance, surface quality, and functional characteristics. Some common finishing processes for CNC machined parts include:
1. **Deburring:** Deburring removes sharp edges and burrs left on the part after machining. This process enhances safety, improves aesthetics, and prevents potential injury during handling.
2. **Polishing:** Polishing is done to achieve a smooth and reflective surface finish. It is commonly used for decorative parts or parts requiring a high-quality surface appearance.
3. **Anodizing:** Anodizing is an electrochemical process that adds a protective oxide layer to aluminum parts. It enhances corrosion resistance, improves surface hardness, and allows for coloring options.
4. **Plating:** Plating involves adding a thin layer of metal, such as chrome, nickel, or zinc, onto the surface of the part. Plating improves appearance, corrosion resistance, and wear resistance.
5. **Painting:** Painting provides a wide range of color options and protects the part's surface from environmental factors. It can also be used for identification and branding purposes.
6. **Powder Coating:** Powder coating is a durable and environmentally friendly finishing process that applies a powder coating electrostatically to the part's surface and then cures it through heat.
7. **Electropolishing:** Electropolishing is an electrochemical process that removes surface material, producing a smooth and shiny surface finish. It is often used for stainless steel parts.
8. **Passivation:** Passivation is a chemical treatment that removes free iron and contaminants from stainless steel parts, enhancing corrosion resistance.
9. **Laser Engraving:** Laser engraving is used to add text, logos, or markings to the part's surface. It is precise and provides permanent markings.
10. **Vibratory Finishing:** Vibratory finishing involves placing the parts in a vibrating container with abrasive media, water, and finishing compounds to achieve a smooth and polished surface.
11. **Tumbling:** Tumbling is a mass finishing process where the parts are placed in a rotating drum with abrasive media to remove sharp edges and improve surface finish.
12. **Passive Thermal Control (PTC) Coating:** PTC coatings are used for thermal control in electronic components, providing insulation and heat dissipation.
13. **Chemical Etching:** Chemical etching removes material from the surface of the part to create specific designs or markings.
The selection of the appropriate finishing process depends on the material, design requirements, intended application, and desired aesthetic appearance of the CNC machined part. Finishing processes not only enhance the part's functionality but also add value to the final product and improve customer satisfaction.
What is the role of cutting speed in CNC machining?
Cutting speed affects the rate at which material is removed and can impact the quality and accuracy of the finished part.
Cutting speed plays a critical role in CNC machining and has a significant impact on the efficiency, accuracy, and quality of the machining process. Cutting speed refers to the relative speed at which the cutting tool moves against the workpiece during machining. It is typically measured in surface feet per minute (SFPM) or meters per minute (m/min). The role of cutting speed in CNC machining includes the following aspects:
1. **Material Removal Rate (MRR):** Cutting speed directly affects the material removal rate, which is the amount of material that can be removed from the workpiece in a given period. Higher cutting speeds result in higher MRR, allowing for faster production of parts.
2. **Cycle Time:** Cutting speed affects the overall cycle time of the CNC machining process. Higher cutting speeds reduce the time required to machine a part, leading to shorter production cycles and increased productivity.
3. **Heat Generation:** Cutting speed influences the amount of heat generated during machining. Higher cutting speeds generate more heat due to increased friction between the cutting tool and the workpiece. Controlling heat is crucial to prevent thermal damage to the workpiece and tool.
4. **Tool Wear:** Cutting speed affects tool wear rates. High cutting speeds can lead to faster tool wear, especially in high-speed machining applications. Proper cutting speed selection can extend tool life and reduce tooling costs.
5. **Surface Finish:** The cutting speed directly influences the surface finish of the machined part. Optimal cutting speeds can result in smooth and fine surface finishes, while excessively high speeds may cause surface roughness.
6. **Chip Formation:** Cutting speed influences chip formation during machining. High cutting speeds can lead to better chip control and chip evacuation, reducing the risk of chip clogging and tool damage.
7. **Cutting Forces:** Cutting speed affects cutting forces exerted on the cutting tool and the workpiece. Higher cutting speeds may result in lower cutting forces, which can help reduce machining vibrations and improve dimensional accuracy.
8. **Material Machinability:** Different materials have varying machinability characteristics. Cutting speed needs to be optimized for each material to achieve efficient machining without compromising tool life or surface finish.
9. **Machining Stability:** Cutting speed impacts machining stability. The right cutting speed minimizes vibrations and chatter during machining, enhancing overall process stability.
10. **Power Consumption:** Cutting speed affects the power consumption of the CNC machine. Higher cutting speeds generally require higher spindle motor power.
Balancing cutting speed with other machining parameters, such as feed rate and depth of cut, is essential for successful CNC machining. The choice of cutting speed depends on factors like material type, tool material, part geometry, machine capability, and desired productivity. Properly optimizing cutting speed can lead to efficient machining, reduced production costs, and high-quality finished parts. Machinists and CNC programmers must carefully consider cutting speed to achieve the desired machining results while maintaining safety and precision.
What is the difference between CNC machining and 3D printing?
CNC machining involves removing material to create a part, while 3D printing involves adding material layer by layer to create a part.
CNC machining and 3D printing are both manufacturing processes used to create physical objects, but they differ significantly in terms of their underlying principles, capabilities, materials, and applications. Here are the key differences between CNC machining and 3D printing:
1. **Process and Operation:**
- CNC Machining: CNC machining is a subtractive manufacturing process. It involves cutting away material from a solid block or workpiece using computer-controlled cutting tools such as mills, lathes, drills, and routers. The final part is created by removing material from the original block, leaving behind the desired shape.
- 3D Printing: 3D printing, also known as additive manufacturing, is a process that builds objects layer by layer from a digital 3D model. It adds material, usually in the form of plastic, resin, metal, or other materials, to create the final part.
2. **Materials Used:**
- CNC Machining: CNC machining can work with a wide range of materials, including metals (e.g., aluminum, steel, titanium), plastics, composites, and wood.
- 3D Printing: 3D printing uses various materials depending on the specific 3D printing technology, including thermoplastics, photopolymers, metals, ceramics, and even food-grade materials.
3. **Design Flexibility:**
- CNC Machining: CNC machining offers high design flexibility and can produce parts with intricate shapes and complex geometries. However, certain design features may be limited by the tool access and machining capabilities.
- 3D Printing: 3D printing excels in design freedom, enabling the creation of complex and organic shapes that are difficult or impossible to produce using traditional manufacturing methods.
4. **Prototyping vs. Production:**
- CNC Machining: CNC machining is well-suited for both prototyping and production. It is commonly used for low to medium volume production runs due to its efficiency and precision.
- 3D Printing: While 3D printing is excellent for rapid prototyping, it is also increasingly used for low-volume production of specialized and customized parts.
5. **Speed and Efficiency:**
- CNC Machining: CNC machining is generally faster for producing a single part compared to 3D printing, especially for larger and more complex components.
- 3D Printing: 3D printing is generally slower than CNC machining, particularly for producing large, solid parts.
6. **Post-Processing Requirements:**
- CNC Machining: CNC-machined parts may require additional post-processing, such as deburring, polishing, and coating, to achieve the desired surface finish and appearance.
- 3D Printing: Depending on the 3D printing technology and material used, post-processing may be required to improve surface finish and remove support structures.
7. **Costs:**
- CNC Machining: CNC machining can be cost-effective for medium to large production runs but may have higher upfront costs due to tooling and setup expenses.
- 3D Printing: 3D printing is cost-effective for low-volume production and rapid prototyping, but unit costs may be higher than CNC machining for high-volume production.
Both CNC machining and 3D printing have their strengths and are valuable tools in modern manufacturing. The choice between the two depends on factors like part complexity, material requirements, production volume, design freedom, lead time, and budget considerations. Many industries and applications benefit from using a combination of both processes to leverage their respective advantages.
How can CNC machining manufacturers optimize their processes for cost efficiency?
Manufacturers can use process optimization techniques such as lean manufacturing and just-in-time inventory management to reduce costs and improve efficiency.
CNC machining manufacturers can optimize their processes for cost efficiency by implementing various strategies and best practices that focus on reducing waste, improving productivity, and streamlining operations. Here are some key ways to achieve cost efficiency in CNC machining:
1. **Design for Manufacturability (DFM):** Collaborate closely with customers and design engineers to optimize part designs for CNC machining. By designing parts with CNC machining capabilities and limitations in mind, you can minimize complexity, reduce machining time, and lower material costs.
2. **Material Selection:** Choose materials that are cost-effective and suitable for the application. Consider using standard stock materials to reduce material waste and costs.
3. **Optimize Cutting Parameters:** Fine-tune cutting parameters, such as cutting speed, feed rate, and depth of cut, to achieve the most efficient machining process. Balancing cutting parameters can improve material removal rates and extend tool life.
4. **High-Quality Tooling:** Invest in high-quality cutting tools and toolholders to improve cutting performance, reduce tool wear, and decrease downtime for tool changes.
5. **Automate Setup and Tool Changes:** Implement automation technologies to reduce setup times and tool changeovers. This includes the use of automatic tool changers and pallet changers to increase machine utilization.
6. **Minimize Idle Time:** Aim to minimize machine idle time by optimizing toolpaths and sequencing to keep the machine running continuously.
7. **Implement Lean Manufacturing Principles:** Apply lean manufacturing principles to eliminate waste, reduce inventory levels, and optimize workflow. This can lead to reduced lead times and increased production efficiency.
8. **Preventive Maintenance:** Regularly maintain CNC machines to prevent breakdowns and minimize unplanned downtime. Scheduled maintenance ensures that machines operate at peak performance.
9. **Machine Monitoring Systems:** Implement machine monitoring systems to track machine performance, tool usage, and overall equipment efficiency (OEE). This data helps identify areas for improvement and optimization.
10. **Continuous Improvement:** Foster a culture of continuous improvement within the organization. Encourage feedback from operators and employees to identify opportunities for efficiency gains and cost savings.
11. **Optimal Batch Sizes:** Batch parts strategically to optimize production efficiency while avoiding excessive inventory costs.
12. **Value Engineering:** Continuously review processes and materials to identify opportunities for cost reduction without sacrificing quality or performance.
13. **Supplier Collaboration:** Work closely with material suppliers and tooling vendors to negotiate favorable pricing and ensure timely deliveries.
14. **Standardize Workflows:** Standardize machining processes and workflows to promote consistency and minimize variation in production.
15. **Invest in Training:** Provide training and skill development opportunities for employees to enhance their expertise and efficiency in CNC machining operations.
By implementing these strategies and constantly seeking ways to improve efficiency, CNC machining manufacturers can optimize their processes for cost efficiency, increase competitiveness, and deliver high-quality products to their customers at a competitive price.
FAQs List of CNC Machining Services
What is CNC machining?
CNC machining is a manufacturing process that uses computer-controlled machines to produce precise and complex parts from various materials.
CNC machining, which stands for Computer Numerical Control machining, is a manufacturing process that uses computerized controls and precise cutting tools to remove material from a workpiece to create a final part or product. It is a highly automated and precise method of manufacturing that offers numerous advantages over traditional manual machining.
In CNC machining, the entire process is controlled by computer programs, also known as CNC programs. These programs are created using Computer-Aided Design (CAD) software, which allows designers and engineers to create a digital 3D model of the part to be manufactured. The CAD model serves as the blueprint for the part, specifying its dimensions, geometry, and features.
Once the CAD model is complete, Computer-Aided Manufacturing (CAM) software is used to convert the model into a set of instructions that the CNC machine can understand. These instructions, known as G-codes and M-codes, dictate the movements of the cutting tools and workpiece, as well as the machining parameters such as cutting speed, feed rate, and depth of cut.
The CNC machine uses these instructions to precisely control the movements of the cutting tools, which can include drills, end mills, lathes, routers, and more. The cutting tools rotate or move along multiple axes to remove material from the workpiece, following the programmed toolpaths to create the desired shape and features.
CNC machining is highly versatile and can work with a wide range of materials, including metals, plastics, composites, wood, and more. It is commonly used to produce complex and intricate parts with high precision and tight tolerances, making it essential in various industries, including aerospace, automotive, medical, electronics, and more.
Key advantages of CNC machining include its ability to achieve repeatability, high accuracy, and efficiency, making it a cost-effective solution for both prototyping and production. CNC machining is instrumental in modern manufacturing processes, allowing for the creation of high-quality parts with consistent results and short lead times.
What are your tolerances for machined parts?
- +.005”/-.005” local tolerances across most geometries in metals, +/- 0.010" for plastics. Will vary for large parts, specifically when holding flatness over large parts after heat treatment.
- Finish requirements for “As Milled” finish will have a minimum 125 surface finish for CNC parts.
- All fabricated parts have a 0.010” dimensional and 1° angular tolerance.
- Tapped holes not explicitly called out as Features on the quoted CAD model may be machined to the diameters specified in that model.
- No surface treatments (e.g. anodize, bead blast, iridite, powder coat, etc.) will be applied unless you have paid for them and we have specifically acknowledged them.
CNC milling and CNC turning are two primary machining processes used in CNC (Computer Numerical Control) machining. While both processes involve material removal to create a final part, they differ in their methods of operation, types of tools used, and the types of parts they are best suited for. Here are the key differences between CNC milling and CNC turning:
1. **Operation:**
- CNC Milling: CNC milling is a machining process that uses rotary cutting tools to remove material from a workpiece. The cutting tool moves along multiple axes (typically X, Y, and Z axes) to create various 2D and 3D shapes and features on the workpiece.
- CNC Turning: CNC turning is a machining process that uses a single-point cutting tool to remove material from a rotating workpiece. The cutting tool is fed into the workpiece along the Z-axis, resulting in the creation of cylindrical parts with rotational symmetry.
2. **Tooling:**
- CNC Milling: CNC milling machines use a wide range of cutting tools, such as end mills, face mills, and drills, that rotate at high speeds to cut into the workpiece from various angles. The cutting tools have multiple cutting edges and can remove material in different ways.
- CNC Turning: CNC turning machines use a single-point cutting tool, such as a lathe tool or boring tool, which moves along the length of the workpiece to create the desired shape. The workpiece rotates at high speeds during the cutting process.
3. **Workpiece Geometry:**
- CNC Milling: CNC milling is well-suited for machining flat surfaces, pockets, slots, and complex contours. It is ideal for creating parts with complex 3D shapes and multiple features.
- CNC Turning: CNC turning is primarily used for creating cylindrical parts, such as shafts, pins, and bushings. It is well-suited for producing parts with rotational symmetry.
4. **Part Rotation:**
- CNC Milling: In CNC milling, the workpiece is typically stationary, and the cutting tool moves around it. This allows for greater flexibility in creating intricate shapes and features from different angles.
- CNC Turning: In CNC turning, the workpiece rotates, and the cutting tool moves along the Z-axis. The rotation of the workpiece allows for efficient and consistent machining of cylindrical shapes.
5. **Applications:**
- CNC Milling: CNC milling is commonly used for producing complex components, molds, dies, and parts with intricate shapes, such as those used in aerospace, automotive, and consumer electronics industries.
- CNC Turning: CNC turning is well-suited for manufacturing round or cylindrical parts, such as shafts, bushings, and threaded components used in various industries, including automotive, medical, and industrial equipment.
In summary, CNC milling is used for machining complex shapes and features, while CNC turning is ideal for creating cylindrical parts with rotational symmetry. Both processes are essential in modern CNC machining, and the choice between CNC milling and CNC turning depends on the specific design requirements and characteristics of the part to be manufactured.
How does CNC machining work?
CNC machining uses subtractive processes, which means feedstock is machined to its final form by subtracting and removing material. Holes are drilled, lots and pathways are bored, and metal stock is shaped into new material with varying tapers, diameters, and shapes.
For subtractive manufacturing, shapes are achieved by the subtraction of material. This contrasts with other types such as additive manufacturing — where materials are added, layered, and deformed to a specified shape. It also contrasts with injection molding where the material is injected in a different state of matter, using a mold, and formed to a specified shape.
CNC machining is versatile — and can be used with various materials, including metals, plastics, wood, glass, foam, and other composite materials. This versatility has helped make CNC machining a popular choice across industries, enabling designers and engineers to fabricate products efficiently and precisely.
CNC machining, which stands for Computer Numerical Control machining, is a manufacturing process that uses computerized controls and precise tools to remove material from a workpiece to create a final part or product. The process involves the following steps:
1. **Design and Programming:** The first step in CNC machining is to create a digital 3D model of the part to be manufactured. Computer-Aided Design (CAD) software is used for this purpose. Once the design is complete, Computer-Aided Manufacturing (CAM) software is used to generate a CNC program that contains instructions for the CNC machine.
2. **Machine Setup:** The CNC machine is set up with the necessary cutting tools and workholding devices (fixtures) to securely hold the workpiece in place during machining. The operator loads the CNC program into the machine's computer, which controls the entire machining process.
3. **Workpiece Loading:** The workpiece, which is typically a raw material such as metal or plastic, is loaded onto the CNC machine's table or chuck. The workpiece is positioned accurately according to the coordinates specified in the CNC program.
4. **Tool Selection:** The appropriate cutting tools, such as drills, end mills, or lathes, are selected based on the specific machining operations required to create the part. The CNC program will include instructions for tool changes as needed.
5. **Machining Process:** Once everything is set up, the CNC machine begins the machining process. The computerized controls precisely guide the cutting tools to remove material from the workpiece following the programmed toolpaths. The cutting tools rotate or move along multiple axes to create the desired shape and features on the workpiece.
6. **Coolant and Chip Management:** During the machining process, coolant or cutting fluid may be used to cool the cutting tools and workpiece, reducing heat and lubricating the cutting area. This helps prevent tool wear and improves surface finish. Chips, the material removed during machining, are managed using chip conveyors or chip augers to keep the work area clean and safe.
7. **Toolpath Optimization:** The CNC program ensures that the cutting tool follows optimal toolpaths to efficiently remove material while maintaining dimensional accuracy and surface finish.
8. **Quality Control:** Throughout the machining process, quality control checks are performed to verify dimensions and ensure the final part adheres to the required tolerances and specifications.
9. **Finishing Operations:** After the primary machining process is complete, secondary operations like deburring, polishing, or surface treatments may be applied to achieve the desired final appearance and surface finish.
10. **Unloading the Finished Part:** Once the machining is complete, the finished part is removed from the CNC machine. The CNC operator inspects the part for quality and prepares it for any additional post-processing or assembly if required.
CNC machining offers precision, repeatability, and the ability to produce complex parts with high accuracy. The process is widely used in various industries, including aerospace, automotive, medical, electronics, and more, to manufacture a wide range of components and products.
How does CNC machining differ from traditional machining?
CNC machining and traditional machining are both manufacturing processes used to shape materials into finished parts, but they differ significantly in terms of operation, control, and automation. Here are the key differences between CNC machining and traditional machining:
1. **Control and Automation:**
- CNC Machining: CNC (Computer Numerical Control) machining is a modern, computer-controlled process where the movements of the cutting tools and workpiece are precisely controlled by computer programs (CNC programs). It requires minimal manual intervention, as the CNC machine follows the programmed instructions.
- Traditional Machining: Traditional machining, also known as manual machining or conventional machining, is carried out by skilled machinists who operate the machine tools manually. The machinist controls the cutting tools' movements and feeds based on their experience and expertise.
2. **Programmability:**
- CNC Machining: CNC machines are highly programmable. Part designs are created using CAD (Computer-Aided Design) software, and the corresponding CNC program is generated using CAM (Computer-Aided Manufacturing) software. Changes to the design can be easily accommodated by modifying the CNC program.
- Traditional Machining: In traditional machining, changes to part designs typically require manual adjustments to the machine settings, such as tool positions and feed rates. This process may involve more time and effort compared to CNC machining.
3. **Complexity and Precision:**
- CNC Machining: CNC machining excels at producing complex parts with high precision and tight tolerances. It can accurately follow intricate toolpaths and create repeatable parts with consistent quality.
- Traditional Machining: Traditional machining can achieve high precision, but complex and intricate parts may be challenging to produce consistently. It relies heavily on the operator's skill and experience.
4. **Productivity and Efficiency:**
- CNC Machining: CNC machining is generally more productive and efficient, especially for large production runs. Once the CNC program is set up, the CNC machine can run continuously, reducing human intervention and cycle times.
- Traditional Machining: Traditional machining may require more time for manual setup, tool changes, and adjustments, making it less efficient for high-volume production.
5. **Labor Requirements:**
- CNC Machining: CNC machining requires fewer skilled operators. Once the CNC program is prepared and the machine is set up, a single operator can oversee multiple machines.
- Traditional Machining: Traditional machining typically relies on skilled machinists to operate each machine manually, which may limit the number of machines an operator can manage simultaneously.
6. **Flexibility:**
- CNC Machining: CNC machining offers greater flexibility for design changes and modifications. It allows for rapid prototyping and easy adaptation to new part designs.
- Traditional Machining: Traditional machining may be less flexible, requiring more time and effort for tooling changes and adjustments to accommodate design changes.
Both CNC machining and traditional machining have their advantages and are suitable for various applications. CNC machining is ideal for complex and high-precision parts, while traditional machining may be preferred for smaller production runs, custom jobs, or operations that don't require computerized automation.
What industries use CNC machining?
CNC machining is widely used across industries. It is common in aerospace, automotive, consumer electronics, robotics, agriculture, and other fields that frequently use metal parts. It is also widely used in medical devices, household goods, energy, oil and gas, and other consumer applications. It is one of the most common manufacturing processes in the world.
CNC machining is a versatile and widely used manufacturing process, and it finds applications across various industries that require precision, accuracy, and the ability to create complex parts. Some of the industries that extensively use CNC machining include:
1. **Aerospace:** CNC machining is crucial in aerospace manufacturing for producing aircraft components, such as engine parts, landing gear, airframes, and turbine blades, which require high precision and reliability.
2. **Automotive:** The automotive industry relies on CNC machining to manufacture engine components, transmission parts, chassis components, and other critical automotive parts with tight tolerances.
3. **Medical and Healthcare:** CNC machining is essential in producing medical devices, surgical instruments, implants, prosthetics, and other medical components that demand strict quality control and biocompatibility.
4. **Electronics:** CNC machining is used to manufacture electronic components like printed circuit boards (PCBs), heat sinks, connectors, and enclosures for electronic devices.
5. **Oil and Gas:** The oil and gas industry uses CNC machining to create components for drilling equipment, valves, pumps, and other parts required for exploration and production.
6. **Defense and Military:** CNC machining is crucial in manufacturing military equipment, including weapons, firearm components, armored vehicle parts, and aircraft components used in defense applications.
7. **Energy and Power Generation:** CNC machining is employed in the production of parts for power generation equipment, such as gas turbines, wind turbine components, and hydroelectric equipment.
8. **Industrial Equipment:** CNC machining is used to manufacture parts for various industrial machinery and equipment, including pumps, valves, gears, and hydraulic components.
9. **Consumer Goods:** CNC machining is utilized in the production of consumer goods like kitchen appliances, home tools, electronic gadgets, and decorative items.
10. **Marine and Shipbuilding:** CNC machining is employed in producing ship components, marine equipment, and ship systems for the maritime industry.
11. **Injection Molding and Tooling:** CNC machining is crucial in creating injection molds, dies, and tooling for various industries, including automotive, packaging, and consumer goods.
12. **Precision Engineering:** CNC machining plays a significant role in precision engineering, which involves manufacturing high-precision components for diverse industries.
The versatility and ability of CNC machining to work with various materials, including metals, plastics, composites, and more, make it indispensable in many industries that demand high-quality, custom, and precise parts. As technology continues to advance, CNC machining is likely to play an increasingly important role in modern manufacturing across even more industries.
What are your CNC machining & turning capabilities?
- 5 Axis Machining up to 26″
- 4 Axis Machining up to 36″
- 3 Axis Machining up to 60″
- Dual Spindle Lathes with 32″ Swing, 18″ Max Diameter, and 8″ Chuck
- Wire EDM with a part depth of 18″
As an AI language model, I don't have real-world capabilities, including CNC machining and turning capabilities. However, I can provide general information about CNC machining and turning processes.
CNC Machining:
CNC machining is a computer-controlled manufacturing process used to remove material from a workpiece to create a final part or product. The process involves the use of computer numerical control (CNC) machines, such as CNC mills, lathes, routers, and grinders, which are programmed to precisely control the movements of cutting tools and workpieces. CNC machining offers high precision, repeatability, and the ability to produce complex parts with tight tolerances. Some of the common CNC machining operations include milling, turning, drilling, and tapping.
CNC Turning:
CNC turning is a specific type of CNC machining process that is used to create cylindrical parts. It involves rotating the workpiece while a single-point cutting tool is fed into the rotating workpiece to remove material and create the desired shape. CNC turning is particularly suited for producing parts like shafts, pins, bushings, and other components with rotational symmetry.
Capabilities of CNC Machining & Turning:
The capabilities of CNC machining and turning depend on various factors, including the specific CNC machine being used, the size and material of the workpiece, and the complexity of the part design. Some general capabilities of CNC machining and turning processes include:
1. High precision and accuracy: CNC machining and turning can achieve tight tolerances and consistent part dimensions.
2. Versatility: CNC machines can work with a wide range of materials, including metals, plastics, composites, and more.
3. Complex part geometry: CNC machining and turning can create parts with intricate shapes and features.
4. Reproducibility: Once a CNC program is set up, it can be used repeatedly to produce identical parts.
5. Automation: CNC machines can operate autonomously once the CNC program is loaded, reducing the need for constant manual intervention.
6. Efficiency: CNC machining and turning can be highly efficient for both prototype development and large production runs.
7. Multi-axis machining: Advanced CNC machines can perform multi-axis machining, enabling complex part production in a single setup.
It's important to note that specific CNC machining and turning capabilities may vary depending on the equipment and expertise of the manufacturing facility. Manufacturers often list their specific capabilities, equipment, and materials on their websites or promotional materials to showcase their offerings to potential customers.
Do you offer Quick-Turn CNC Machining?
We offers fast lead times on quick-turn parts, with many parts available in 3-4 days. We offer an expedite option, and our team works closely with you to meet your most urgent deadlines.
As an AI language model, I don’t offer any services, including Quick-Turn CNC Machining. My primary function is to provide information and answer questions to the best of my knowledge and abilities.
Quick-Turn CNC Machining is a service provided by certain manufacturing companies or machining shops. These companies specialize in providing rapid and expedited CNC machining services to meet tight deadlines and quick production requirements. Quick-Turn CNC Machining is particularly useful for rapid prototyping, urgent production needs, and low to medium volume production runs.
If you are looking for Quick-Turn CNC Machining services, I recommend searching for reputable CNC machining shops or manufacturers that explicitly offer quick-turn or rapid machining services. Many manufacturing companies advertise their turnaround times and rapid prototyping capabilities on their websites or through customer inquiries.
Always make sure to consider the company's experience, reputation, quality of work, and customer reviews before choosing a Quick-Turn CNC Machining service provider. Additionally, providing clear and detailed specifications for your project can help ensure that the machining shop can meet your requirements efficiently.
What materials can be used in CNC machining?
Common materials include metals (such as aluminum, steel, and brass), plastics, and wood.
CNC machining is a versatile manufacturing process that can work with a wide range of materials. The choice of material depends on the specific requirements of the part, such as its intended use, mechanical properties, aesthetics, and environmental factors. Some of the common materials used in CNC machining include:
1. **Metals:**
- Aluminum: Lightweight, corrosion-resistant, and has good strength-to-weight ratio. Widely used in aerospace, automotive, and consumer electronics industries.
- Steel: Offers excellent strength and durability, commonly used in various industrial applications.
- Stainless Steel: Resistant to corrosion and high temperatures, suitable for food, medical, and marine applications.
- Brass: Durable and has good electrical and thermal conductivity. Often used in electronics and plumbing.
- Copper: High electrical and thermal conductivity, used in electrical components and heat exchangers.
- Titanium: Lightweight, strong, and corrosion-resistant, commonly used in aerospace and medical applications.
2. **Plastics:**
- ABS (Acrylonitrile Butadiene Styrene): Durable and versatile, used in consumer products, automotive, and electronics.
- Polycarbonate (PC): Transparent and impact-resistant, commonly used in automotive, medical, and safety applications.
- Nylon (Polyamide): High strength and flexibility, used in gears, bearings, and structural components.
- PVC (Polyvinyl Chloride): Rigid and easy to process, used in construction and electrical applications.
- PEEK (Polyether Ether Ketone): High-performance thermoplastic, used in aerospace, medical, and engineering applications.
3. **Composites:**
- Carbon Fiber: Lightweight and strong, used in aerospace, sports equipment, and automotive industries.
- Fiberglass: Resistant to corrosion and used in marine and aerospace applications.
- G10/FR4: Epoxy-based laminate, commonly used in electrical and electronic components.
4. **Wood:**
- Various types of wood can be used in CNC machining for decorative, artistic, and functional purposes.
5. **Other Materials:**
- Ceramics: Used in high-temperature applications, electronics, and cutting tools.
- Foam: Used for prototyping, modeling, and packaging applications.
It's important to note that different CNC machines and cutting tools may have specific capabilities and limitations with certain materials. Additionally, some materials may require special considerations during machining, such as appropriate cutting speeds, feeds, and tooling to achieve the desired results. Manufacturers often provide guidelines for material selection and machining parameters based on their equipment and expertise.
What types of CNC machines are commonly used in manufacturing?
Common types include CNC mills, lathes, and routers.
Various types of CNC machines are commonly used in manufacturing, each specialized for specific machining operations and applications. The choice of CNC machine depends on the type of part to be manufactured, the material used, the required level of precision, and the production volume. Some of the most commonly used CNC machines in manufacturing include:
1. **CNC Milling Machine:** CNC milling machines use rotary cutting tools to remove material from a workpiece to create complex 3D shapes and features. They are widely used for machining flat surfaces, slots, pockets, and contours. CNC milling machines can be vertical or horizontal, and they come in various sizes to accommodate different workpiece sizes and production needs.
2. **CNC Lathe Machine:** CNC lathe machines are used for turning cylindrical workpieces. The workpiece is rotated, and a single-point cutting tool is fed into the workpiece to remove material and create rotational symmetry. CNC lathes are used to produce parts like shafts, rods, and bushings.
3. **CNC Router:** CNC routers are specialized for cutting, shaping, and engraving materials like wood, plastic, and composites. They are commonly used in woodworking, signage, and prototyping applications.
4. **CNC Plasma Cutter:** CNC plasma cutters use a high-velocity jet of ionized gas to cut through materials like steel, stainless steel, and aluminum. They are commonly used in metal fabrication and automotive industries.
5. **CNC Laser Cutter:** CNC laser cutters use a high-powered laser to cut through materials like metal, plastic, and wood. They offer high precision and are used in various industries, including aerospace, electronics, and signage.
6. **CNC EDM (Electrical Discharge Machining) Machine:** CNC EDM machines use electrical discharge sparks to remove material from a workpiece. They are often used for machining complex shapes and hardened materials.
7. **CNC Swiss-type Lathe:** Swiss-type lathes are specialized CNC lathes used for high-precision turning of small, intricate parts. They are commonly used in the medical and watchmaking industries.
8. **CNC Grinding Machine:** CNC grinding machines are used to achieve high-precision surface finishes and tight tolerances on parts. They are commonly used for grinding metal components.
9. **CNC Waterjet Cutter:** CNC waterjet cutters use a high-pressure stream of water mixed with abrasive particles to cut through various materials, including metals, stone, and glass.
10. **CNC 3D Printer:** While not a traditional CNC machine, CNC 3D printers use computer control to additively manufacture parts layer by layer. They are used for rapid prototyping and low-volume production of plastic and metal parts.
These are just a few examples of the many types of CNC machines available. Each type of CNC machine offers specific capabilities to cater to diverse manufacturing needs and plays a vital role in modern manufacturing processes across different industries.
What is the role of CAD software in CNC machining?
CAD software is used to create a 3D model
Computer-Aided Design (CAD) software plays a crucial role in CNC machining as it serves as the starting point for creating the digital model of the part to be manufactured. CAD software is used by engineers and designers to design and model 2D and 3D objects with precise dimensions and geometries. Its role in CNC machining includes the following key aspects:
1. **Part Design and Modeling:** CAD software allows designers to create detailed and accurate 3D models of the part they want to manufacture. The software provides a virtual workspace where users can sketch, extrude, revolve, and apply various operations to create complex shapes and features.
2. **Dimensional Accuracy:** CAD software ensures that the digital model of the part adheres to the desired dimensions, tolerances, and design specifications. Designers can input precise measurements and constraints, ensuring the accuracy of the final part.
3. **Complex Geometry:** CAD software enables the creation of intricate and complex part geometries that may not be feasible with traditional manual drafting methods. It allows designers to visualize and model parts with freeform surfaces, curves, fillets, chamfers, and other features.
4. **Assembly Modeling:** In CNC machining, assemblies may involve multiple parts that need to fit together precisely. CAD software facilitates the modeling and testing of assemblies, ensuring proper fit and functionality.
5. **Rapid Prototyping:** CAD software facilitates rapid prototyping by allowing designers to quickly create digital models of parts. These models can be used to create physical prototypes using 3D printing or other rapid prototyping methods.
6. **Design Validation and Simulation:** Some CAD software offers simulation capabilities, allowing designers to perform finite element analysis (FEA) and other tests to validate the design's structural integrity and performance under different conditions.
7. **CAM Integration:** CAD software often integrates with Computer-Aided Manufacturing (CAM) software. CAM software uses the CAD model to generate CNC toolpaths and instructions (G-codes and M-codes) that the CNC machine can understand and follow during the machining process.
8. **File Export:** CAD software enables the export of the designed model in various file formats, such as STEP, IGES, or STL, which can be imported into CAM software for CNC programming.
By using CAD software, designers can create detailed and precise digital models of parts, allowing for efficient and accurate CNC machining processes. The CAD/CAM integration streamlines the entire manufacturing workflow, reducing manual errors, shortening lead times, and enhancing the overall productivity and quality of CNC machining operations.
What are some common applications of CNC machined parts?
CNC machined parts are used in a wide range of industries such as aerospace, automotive, and medical.
CNC machined parts are widely used in various industries due to their high precision, quality, and versatility. Some of the common applications of CNC machined parts include:
1. **Aerospace:** CNC machined parts are essential in the aerospace industry for manufacturing aircraft components such as engine parts, turbine blades, brackets, and structural components. The high precision and reliability of CNC machining are critical in aerospace engineering.
2. **Automotive:** CNC machined parts are used in the automotive industry for producing engine components, transmission parts, brake calipers, steering components, and other critical automotive parts.
3. **Medical and Healthcare:** CNC machined parts are used in the medical field to manufacture medical devices, surgical instruments, orthopedic implants, dental components, and prosthetics, requiring high precision and biocompatibility.
4. **Electronics:** CNC machined parts are used in electronics for producing intricate components like PCBs (Printed Circuit Boards), connectors, heatsinks, and enclosures for electronic devices.
5. **Oil and Gas:** The oil and gas industry relies on CNC machined parts for manufacturing drilling equipment, valves, fittings, and other components used in exploration and extraction processes.
6. **Industrial Equipment:** CNC machined parts are used in the production of various industrial machinery and equipment, including pumps, valves, gears, and hydraulic components.
7. **Defense and Military:** CNC machined parts are crucial in manufacturing military equipment, including firearms, weapon components, armored vehicle parts, and aircraft components.
8. **Consumer Goods:** CNC machined parts are used in the production of consumer goods like kitchen appliances, home tools, electronic gadgets, and decorative items.
9. **Marine and Shipbuilding:** CNC machined parts are used in manufacturing ship components, marine equipment, and ship systems for the maritime industry.
10. **Packaging Machinery:** CNC machined parts are utilized in the production of packaging machinery components, ensuring precise and reliable packaging processes.
11. **Renewable Energy:** CNC machined parts are used in the renewable energy sector for producing components in wind turbines, solar panels, and hydroelectric power systems.
12. **Robotics:** CNC machined parts are critical in the manufacturing of robotic systems, robotic arms, and automation equipment.
These applications are just a few examples, and CNC machined parts have a wide range of uses in various other industries as well. The ability to produce custom, high-quality, and intricately designed parts with CNC machining makes it a versatile and indispensable technology in modern manufacturing processes.
What is the difference between CNC milling and CNC turning?
CNC milling involves cutting away material to create a 3D shape, while CNC turning involves rotating the material to create cylindrical shapes.
CNC milling and CNC turning are two distinct machining processes used in CNC (Computer Numerical Control) machining. While both processes involve the removal of material from a workpiece to create a final part, they have different methods of operation, tooling, and types of parts they are best suited for. Here are the key differences between CNC milling and CNC turning:
CNC Milling:
1. **Operation:** CNC milling is a machining process that uses rotary cutting tools to remove material from a workpiece. The cutting tool moves along multiple axes (typically X, Y, and Z axes) to create various 2D and 3D shapes and features on the workpiece.
2. **Tooling:** CNC milling machines use a wide range of cutting tools, such as end mills, face mills, and drills, that rotate at high speeds to cut into the workpiece from different angles. The cutting tools have multiple edges and can remove material in various ways.
3. **Workpiece Geometry:** CNC milling is well-suited for machining flat surfaces, pockets, slots, and complex contours. It is ideal for creating parts with complex 3D shapes and multiple features.
4. **Part Rotation:** In CNC milling, the workpiece is typically stationary, and the cutting tool moves around it. This allows for greater flexibility in creating intricate shapes and features from different angles.
CNC Turning:
1. **Operation:** CNC turning is a machining process that uses a single-point cutting tool to remove material from a rotating workpiece. The cutting tool is fed into the workpiece along the Z-axis, resulting in the creation of cylindrical parts with rotational symmetry.
2. **Tooling:** CNC turning machines use a single-point cutting tool, such as a lathe tool or boring tool, which moves along the length of the workpiece to create the desired shape. The workpiece rotates at high speeds during the cutting process.
3. **Workpiece Geometry:** CNC turning is primarily used for creating cylindrical parts, such as shafts, pins, and bushings. It is well-suited for producing parts with rotational symmetry.
4. **Part Rotation:** In CNC turning, the workpiece rotates, and the cutting tool moves along the Z-axis. The rotation of the workpiece allows for efficient and consistent machining of cylindrical shapes.
In summary, CNC milling is used for machining complex shapes, intricate contours, and parts with multiple features, while CNC turning is ideal for producing cylindrical parts with rotational symmetry. Both processes are essential in CNC machining and complement each other to meet a wide range of manufacturing needs. The choice between CNC milling and CNC turning depends on the specific design requirements and characteristics of the part to be manufactured.